1日2時間の集計作業が約1分に。
スチール製家具製造の共栄工業のデジタル改革
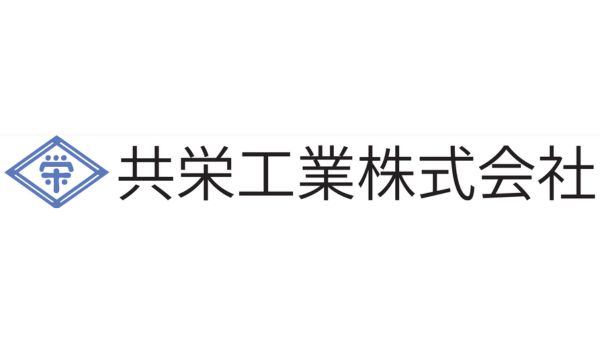
共栄工業株式会社
- 業種 : 製造
- 従業員数 : 101-500名
お話を伺った方:川上様:京都工場長
竹村様:品質管理部長
竹添様:実際の操作 (現場リーダー)
-
課題
- 紙帳票からExcelに転記・集計する作業に1日あたり2時間以上かかっていた
- 記録したものの分析が十分にできていなかった
- 現場まで見に行かないと作業進捗が把握できない
-
効果
- 集計作業が約1分にまで削減できた
- 記録情報が即ダッシュボード化され、翌日朝礼時点で改善施策に繋げられた
- リアルタイムに作業状況を把握でき、意思決定のスピードや作業効率が改善した
上流工程からtebiki現場分析を導入
貴社の事業内容を教えてください
川上様:共栄工業株式会社は、スチール製家具の生産・販売を主な事業として1948年に創業しました。昨今、紙の削減などの世の流れもあり、現在は事業範囲を「再生可能なスチールを活用し、社会課題の解決に貢献できる製品を提供する」と定義しています。例えば、核家族化によるお墓の問題を解決する「納骨壇の生産・販売」や宅配の再配達の問題を解決する「宅配ボックスの生産・販売」などの活動をおこなっています。
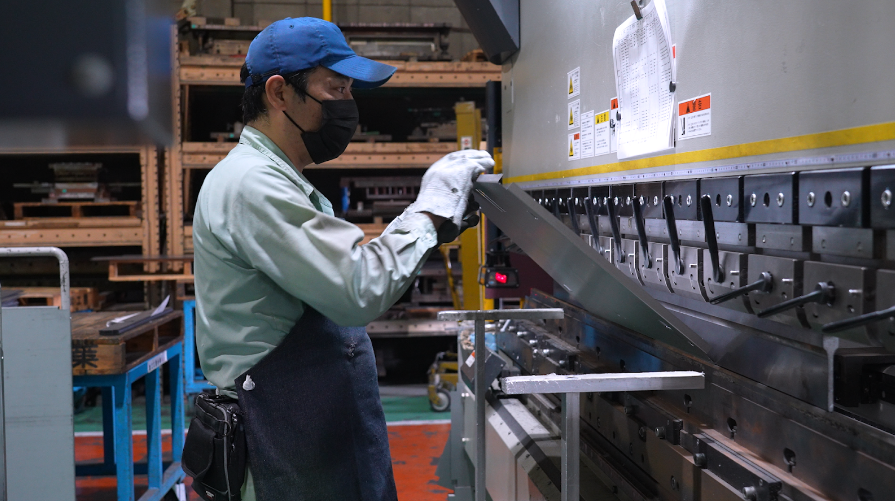
tebiki現場分析でデジタル化している帳票を教えてください
竹村様:現在(2024年8月時点)は、「作業日報」と「前処理管理表(日常点検表)」の2つをtebiki現場分析で運用しています。もともと弊社の現場には、何種類もの帳票が存在しており、ISO(ISO9001認証、ISO14001認証を取得)関連で管理するための帳票に加えて、個人でまとめているものや設備ごとに作られているものなど様々です。主軸事業であるスチール家具の工程には、「加工」「溶接」「塗装」「組立」の4つの工程があり、まずは上流工程にあたる加工工程の帳票からtebiki現場分析に置き換えています。
生命線である記録を、見える化したい
どのような課題があったのでしょうか?
竹村様:「前処理管理表」は、製品を塗装する前に行う工程で管理している表になります。塗料の密着を良くするために下地処理を行う際、最初にお湯で鉄板の油分を洗い流す、いわゆる湯洗が必要になります。湯洗にはお湯の温度が重要になるので、温度が必ず40〜50度の範囲に入っているかをチェックしています。他にも、化成処理で素材の表面に化成の被膜をつけることになり、処理液のpH、A値といった薬品の濃度などをチェックします。この辺りが適正範囲に入っていないと、塗装の剥がれなどに繋がりますので、重点的に検査・管理をしています。
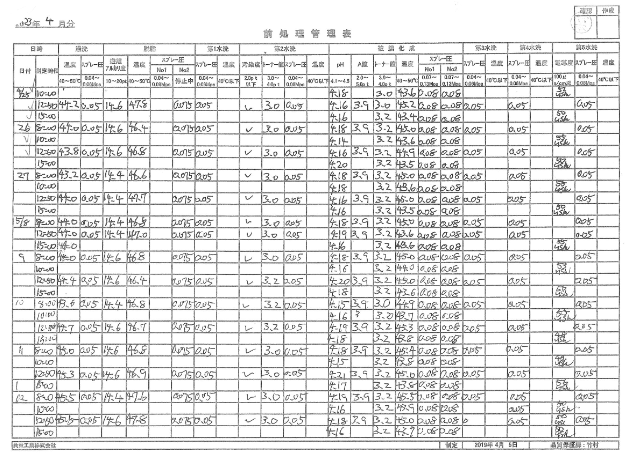
このように、ISO9001の運用も含め、高品質の保証とお客様の信頼をいただくために、製造工程の各プロセスの検査・点検を記録に残すことは、非常に重要な意味を持っており、当社の生命線といえます。
ただ、業務を進める中で記録すること自体が目的となってしまい、記録から改善点を見出したり、品質向上のための分析を行うといったPDCAのC(チェック)A(アクション)に結びつけるのがどうしても後手になっていました。紙に記録した帳票を一度自分の席に戻って、Excelに転記して、転記をしたものから分析を行う必要があるのですが、当社の現場を監督している課長はほとんどがプレイングマネージャーなので、日常の生産管理・進捗管理をしながらだとどうしても分析が後回しになることが多くなっていました。
1日2時間の集計作業が、約1分に
tebiki現場分析導入の経緯を教えて下さい
竹村様:先ほどお話ししたように、当社にとって記録は生命線です。品質保証部として、これらの記録をより効果的に現場で活用する方法を日々模索しています。 以前、全工程の作業の流れを可視化するプロジェクトに着手しました。その一環として、一部の工程で社内システムを用いて帳票のデジタル化を行い、大型モニターに表示することを試みました。しかし、自社内のシステム改修でさえ多大な負荷がかかり、製造工程全体をこの方式に移行することは非常に困難でした。結果として、このプロジェクトは頓挫してしまいました。 そんな中、既に動画マニュアルを導入していたTebiki社との会話の中で、「tebiki現場分析」のリリース情報をいただきました。当社では記録データの活用に苦心しており、また大規模な改革の困難さを身をもって経験していたため、この「tebiki現場分析」の導入をすぐに決定しました。
tebiki現場分析導入後の成果を教えて下さい
川上様:当初の目的通り、作業に時間を取られていたExcelへの転記作業が不要になりました。従来の紙帳票による運用では、10名ほどいる課員が紙の書類に記録したものを、課長が翌日の朝礼までにExcelへ転記しており、その作業に1日2時間ほどかかっていました。しかし「tebiki現場分析」を導入して以降、担当者が直接入力したデータがあり、既に集計されている状態なので、課長の作業は約1分になりました。週次・月次でも同様の集計作業は行っていますが、こちらも全体で5,6時間かかっていたものが30分程度で集計でき、工数削減の効果が如実に表れています。ダッシュボードにも反映されるので、翌日の朝礼で課員といっしょに確認して業務改善に繋げるなど、記録・集計・分析の全てで効率改善に繋がっています。
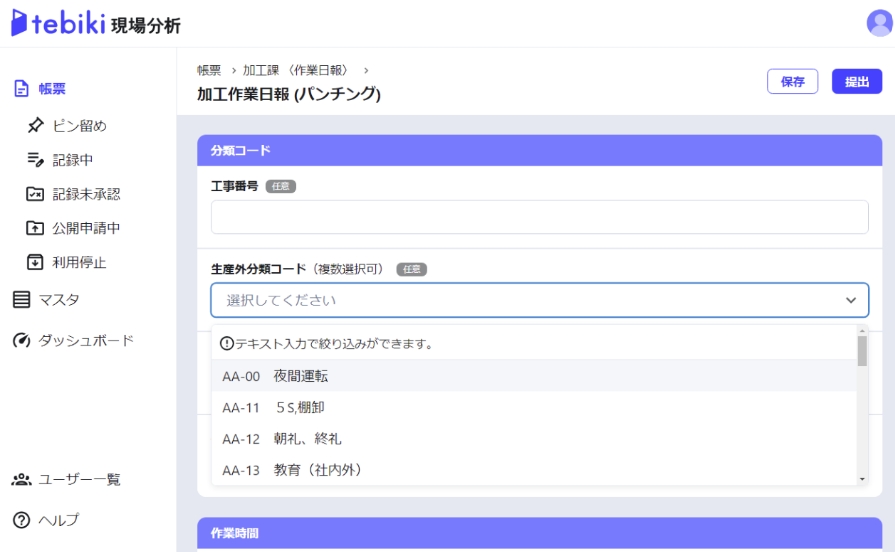
竹村様:たとえば先ほどお話ししたように、湯洗の温度が40~50度の範囲に収まっているかどうかを確認しています。しかし、冬の寒い時期には、朝の生産開始時に40度に達するまでにかかる時間が長くなることがあります。この問題について、担当者は経験から把握していますが、管理者や工場全体ではその事象が十分に理解できておらず、その結果、製造ラインが徐々に遅れることが発生していました。「tebiki現場分析」を導入してからは、ダッシュボードによってこの課題を可視化できるようになり、少し早めの時間に正常な温度に達するよう調整することが可能になりました。
川上様:また、デジタル化による恩恵も表れてきています。設備にトラブルが発生したときに記録を取るようにしているのですが、その記入データをもとに予防処置ができるようになりました。「記録されたデータから○○のような傾向が出ているから、1週間に1回この部分を点検し予防していこう」といった実際の業務改善に繋がっています。
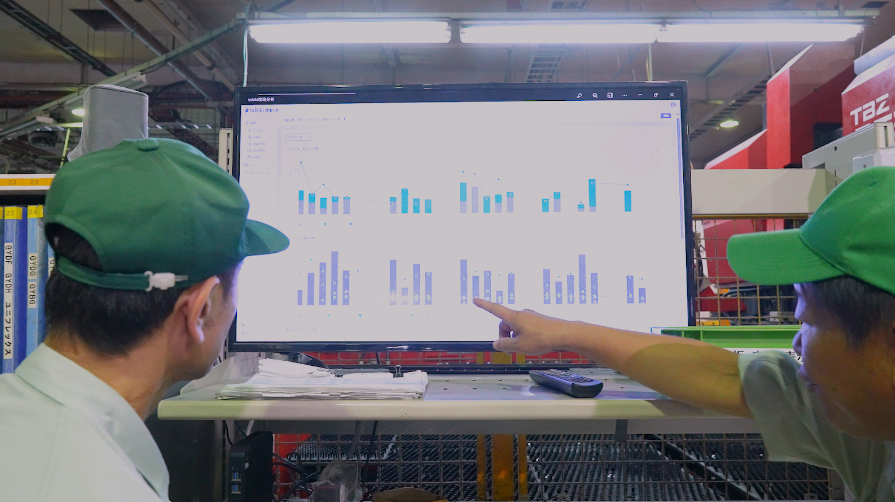
あとは、作業実績がリアルタイムに可視化されることで、他部門の進捗がわかるというメリットもあります。具体的には、データの入力時刻を見れば、何分前にどこまでやっているかといった工程の進捗が把握できます。また、1人で作業している設備では、設備が停止していた場合、怪我などしてはいないかといったことを把握できますね。他にも、上流工程の作業進捗を可視化できるようになったので、下流工程が「tebiki現場分析」を確認することで、次の作業をスムーズに準備できるようになったこともポジティブな点でした。
実際にtebikiを使用して記録してみた感想を教えてください
竹添様:使用前は、紙にペンで記入していた作業がスマホに代わっただけで作業が本当に楽になるのか疑問でした。しかし、実際に使ってみると、紙に記入していたときよりも圧倒的に入力作業が楽になりました。作業開始・終了時間をボタンで簡単に設定できたり、マスタ連携で製品番号が自動的に表示されたりするため、記録時には作業件数を入力するだけでとても簡単です。
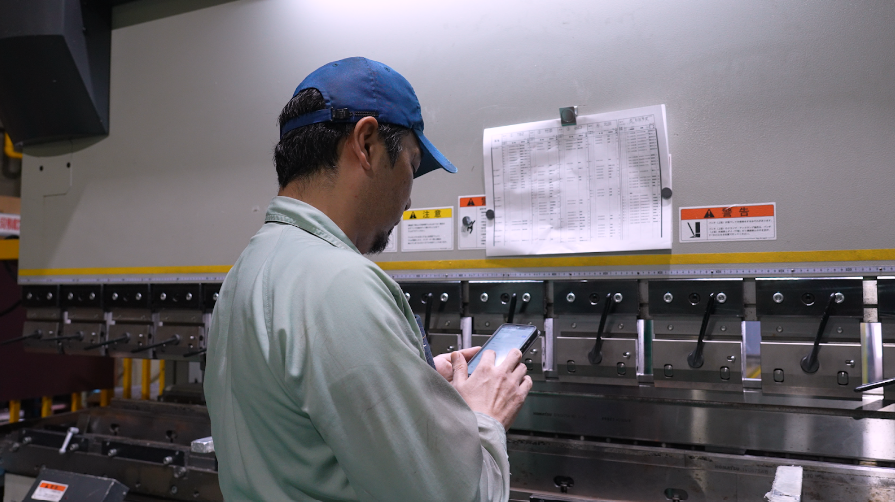
リアルタイムな作業状況の可視化で、意思決定がスムーズに
tebiki現場分析のおすすめポイントはどこですか?
竹村様:改めてになりますが、記録を行うと、ダッシュボードが自動で更新されていくところです。パソコン作業が苦手な人にとっては紙帳票からExcelへの転記だけでも大変ですし、測定値の入力やグラフの更新となるとさらに負担が大きくなっていました。tebiki現場分析では、データの入力さえ行えばダッシュボードが更新されるので、それをもとに分析もしっかり行えて、迅速に改善アクションができるようになり、さまざまな業務で大幅に時間が短縮されました。
川上様:記録から分析まで、一貫してリアルタイムである、というところです。例えば、紙帳票で管理している場合、作業進捗を確認するために現場に直接出向く必要があったのですが、弊社工場の敷地もかなり広いため、なかなか大変でした。今では、tebiki現場分析を通じてほぼリアルタイムで作業進捗を把握することができるので、意思決定がとてもスムーズになりました。
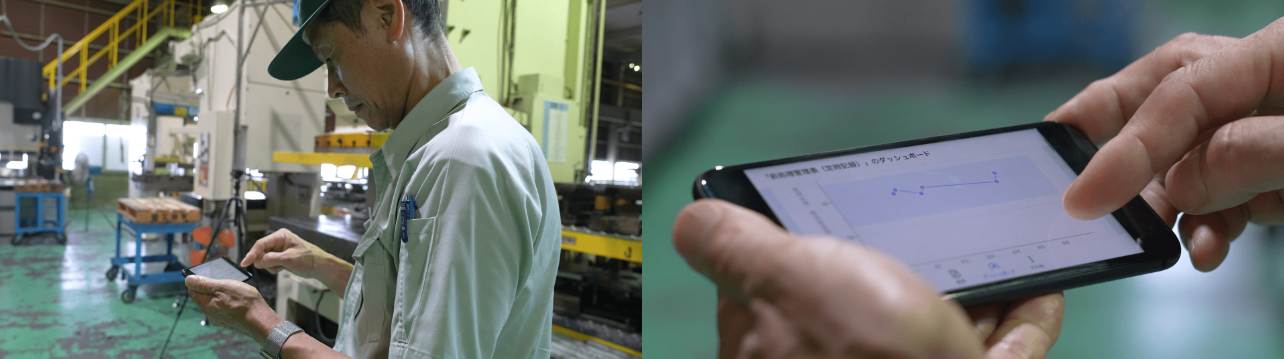
最後に、今後のtebiki活用の展望を教えて下さい!
竹村様:社内のあらゆる帳票を電子化していきたいですね。当初想定していた通り、現場帳票のデジタル化ができたことはもちろんですが、それによる成果も予想以上でした。これからは、製造工程だけではなく、間接業務でも見える化していくことで、新たな課題を見つけ改善し、工場全体のパフォーマンスを上げていきたいと思います。