設備停止は”作業者ごとのバラつき”が要因だった。
スピーディな要因分析の方法とは
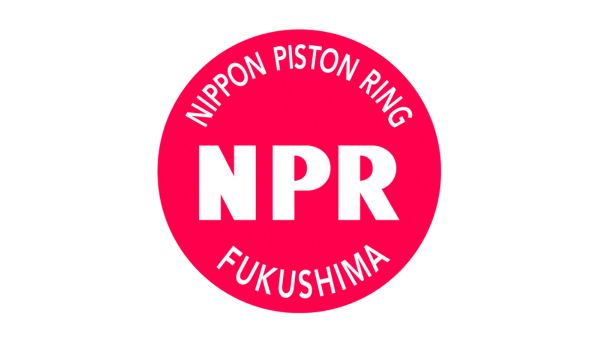
株式会社日ピス福島製造所
- 業種 : 製造
- 従業員数 : 101-500名
お話を伺った方:佐野様:取締役社長 兼 工場長
小林様:製造第三課 工作第三係 係長
斎藤様:製造第三課 工作第三係 班長 (動画内)
-
課題
- 記録を可視化するまでのスキルや時間が不足していた
- 監督者が帳票を確認しにいく手間も発生していた
- 異常の発見がしづらく、タイミングが遅れていた
-
効果
- 設備停止要因を分析し、対策できるようになった
- 記録入力と同時に可視化でき、工数削減した
- リアルタイムデータで進捗管理ができるようになった
高品質・高性能なエンジン部品メーカー
貴社の事業内容を教えてください
佐野様:当社はリケンNPRのグループ企業として1982年に操業開始し、主に自動車のエンジン部品を製造しています。 日ピス福島では特に鋳造製品であるシリンダライナと、焼結製品のバルブシートの製造を行っています。
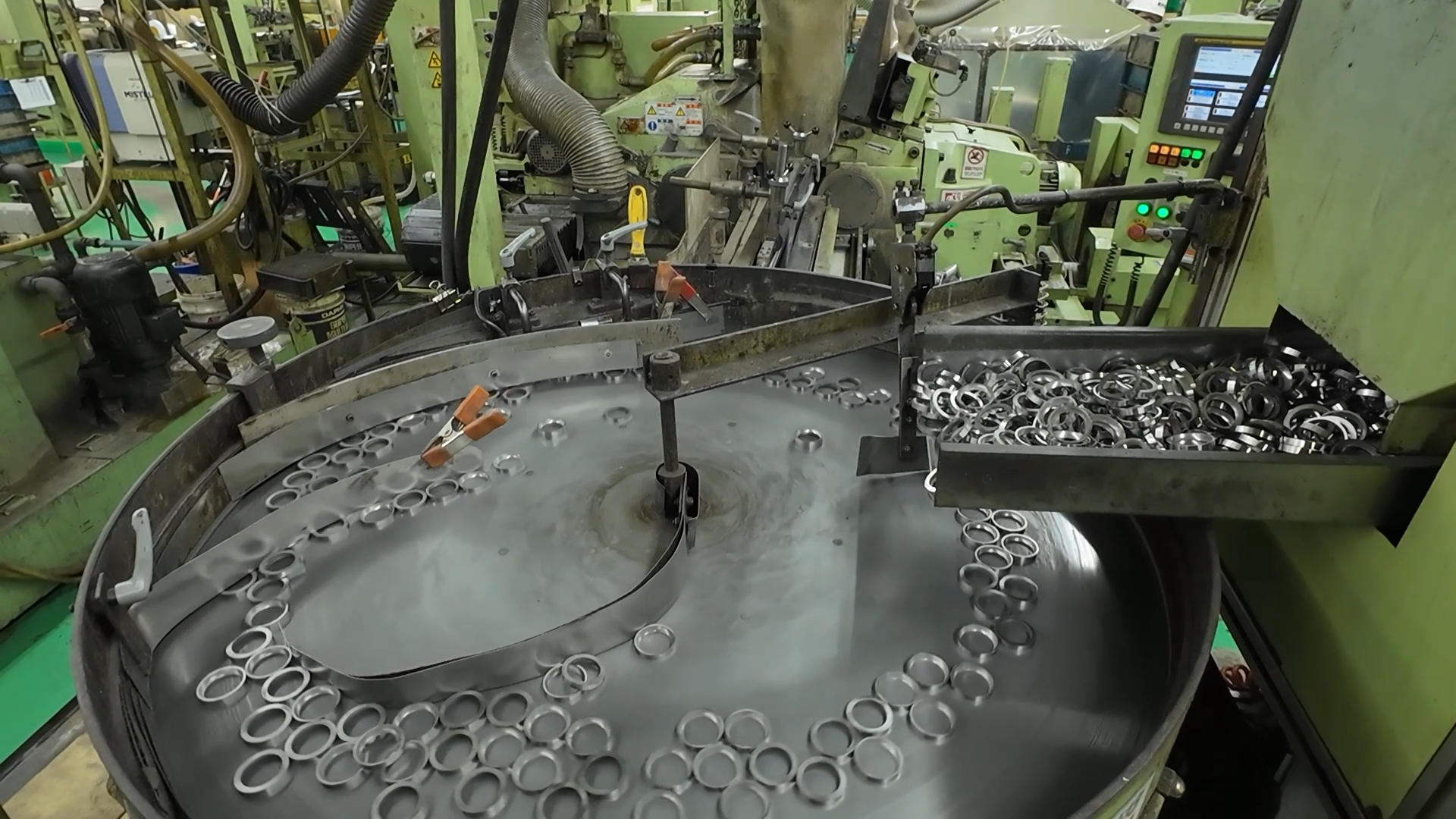
シリンダライナは鉄屑などを溶かし砂型に鋳込む「砂型鋳造」という工法を使い生産しています。製造した粗材を加工し完成形状にした後、表面処理等を行い製品を完成させます。 鋳鉄製品としては非常に大きなものを肉薄に加工するため高い加工精度が要求される製品です。
バルブシートは原材料となる粉を配合・混合し、成形機にて圧縮成形し形を作ります。そのままでは粉を押し固めただけで壊れやすいため、固めた材料を焼結炉へ投入し粉同士を結合させる「焼結」という処理を行います。その後、お客様の指定寸法に合わせて加工し、検査を行いお客様へと出荷しています。
今回デジタル化した現場帳票について教えてください
佐野様:tebiki現場分析を用いて、主に3種類の帳票のデジタル化に取り組んでいます。一つ目は「出来高管理」で、これはいわゆる生産実績で、各工程で日々記録し、最終的にその日の予実の差異を確認したりするために記録している帳票です。二つ目は「品質記録」です。製品の検査時に寸法や材料特性などを記録する帳票ですね。最後に「製造条件記録」で、切削液の濃度や投入量の管理など、重要管理項目の帳票になります。現状はこれらの品質や実績に関わる帳票からデジタル化にトライしています。
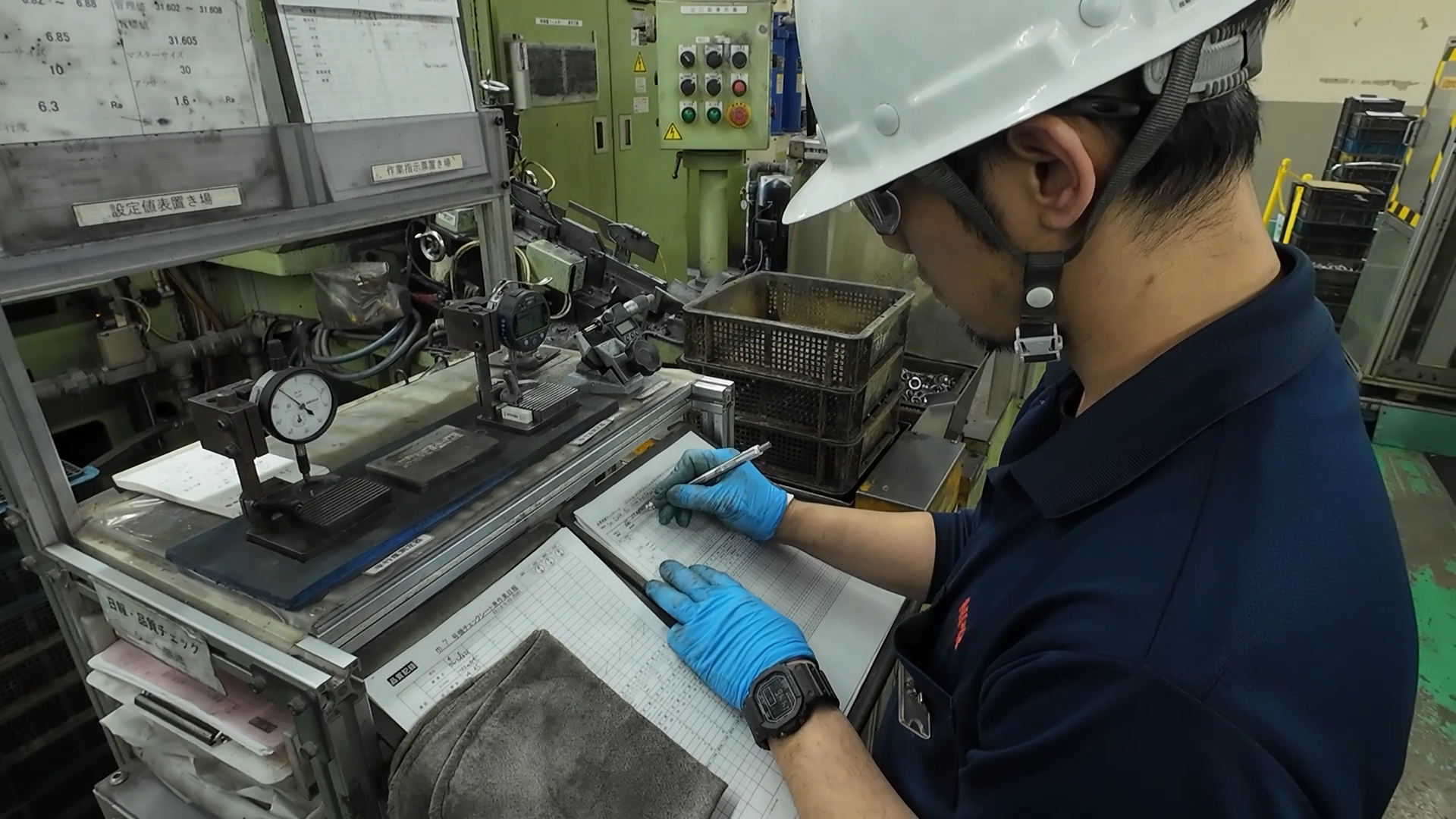
異常把握の遅れから、生きたデータ活用ができていない課題感
tebiki現場分析導入前の課題を教えてください
佐野様:”生きたデータ活用ができていない”という課題がありました。例えば、製造管理項目において、毎日の定時チェックで測定値を記録していたものの、その数値が徐々に上昇していることに気付くのが遅れていました。前月と比較すると1.4倍程度まで上がっており、異常があったにもかかわらず、迅速な対応ができませんでした。 数値データも紙で記録しているとバラツキを把握するのが難しいため、グラフ化すれば視覚的に把握しやすくなるものの、データを転記するための工数や、グラフ化するための力量も必要で中々取り組めていませんでした。
効率化はもちろん、要因と対策へのスピードアップを実現
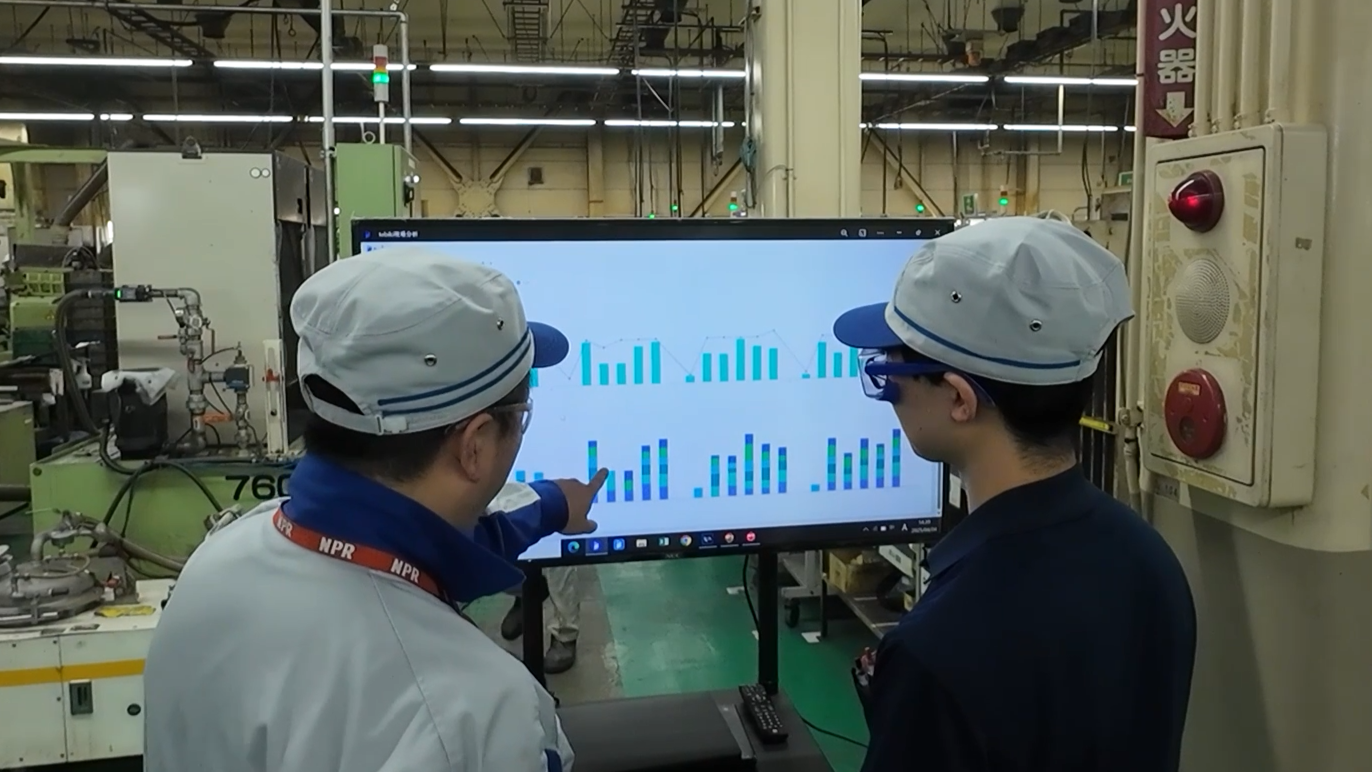
導入後の具体的な変化を教えてください
小林様:作業者がtebiki現場分析でデータを記録してくれるだけで、グラフがリアルタイムに更新されるので、管理者としては一目で変化が見えるようになりました。今までだと監督者が掲示されている帳票のところまで状況を見に行って、デスクに戻るまでの時間というものもかかっていましたが、こういった時間は大きく短縮されましたね。
また、ノーコードで帳票やダッシュボードを手軽に作ることができるため、今まで取り組めていなかった色々な視点での分析ができるようになりました。
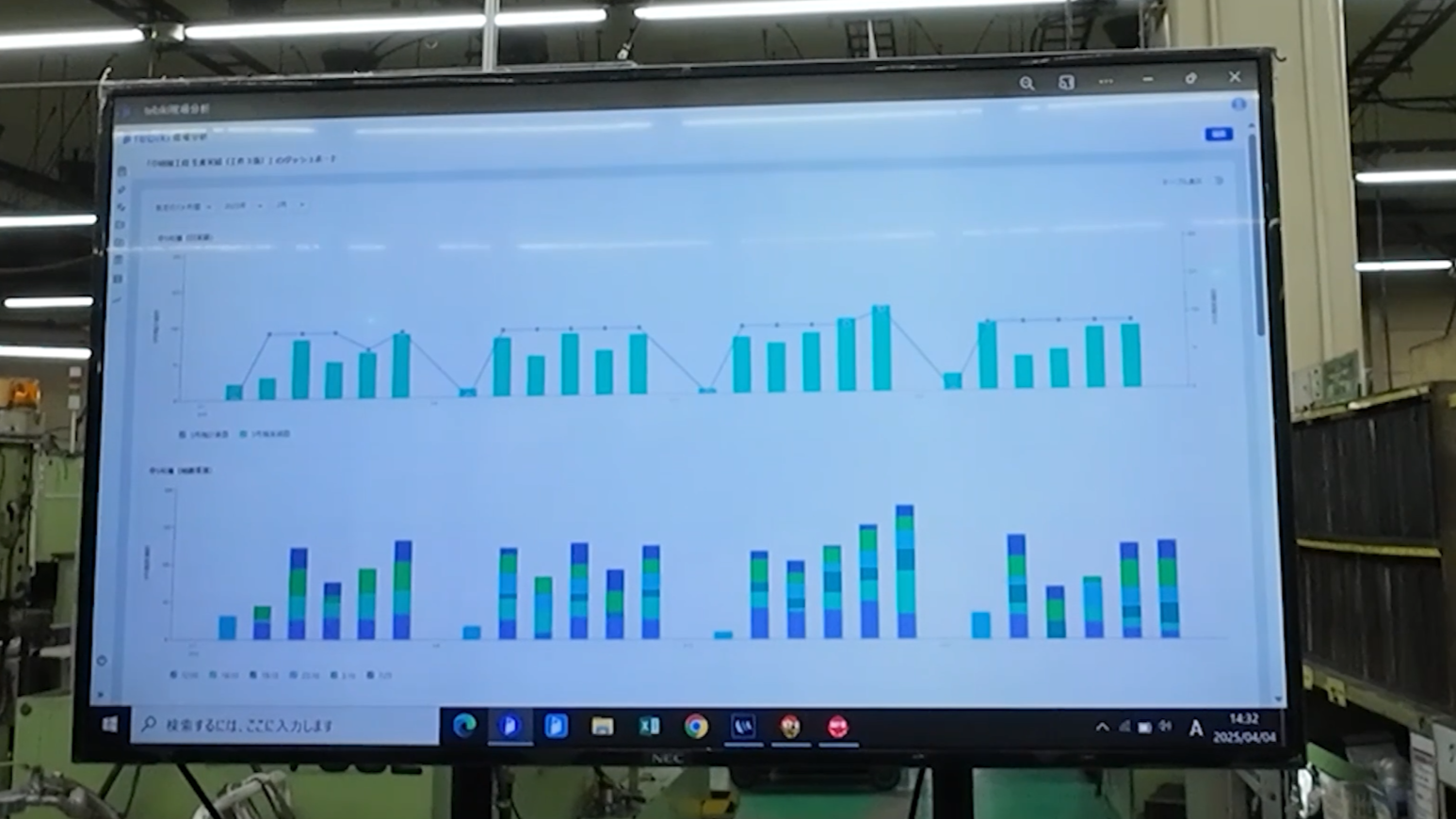
例えば、「品質記録」においては、生産計画数と実績数に加え、停止時間と停止理由をtebiki現場分析の生産実績帳票に記録し、予実差異分析に役立てています。集計結果をグラフで可視化した結果、設備のトラブルよりも、作業者の作業効率に起因する停止が多いことが明確になりました。この停止時間は概ね、次の製造の準備にかかる「段取り」のための停止時間にあたるのですが、この停止時間のバラつきが、人によって差があることがわかりました。停止時間がかかってしまっている人に対しては、標準化のための教育を行い、効率的に設備が稼働するように、といった対策ができるようになりました。 こういったデータがリアルタイムに、またグラフを作成する手間もなくパッと見れるのは非常にありがたいですね。
佐野様:他に、シリンダライナの製造工程の検査では、手直しの不良率を記録し、その推移をグラフで表示し確認することに取り組んでいます。まだ取り組みはじめではありますが、不良の推移を確認している中で、不良が連続した際にその要因をチェックすると、これも作業者毎のバラつきがあるね、だとか材料のバラつきがあるね、といった要因を断定することができ、それらへの対策のスピード感は格段に上がったなと感じています。
現場の方の反応はどうでしたか?
小林様:今まで紙で管理していたことも合って、作業者の中で拒否反応みたいなのがでるかな、と思ったのですが、入力画面もそうですし、グラフもシンプルで扱いやすいのですぐ定着しました。 また、作業者の意識というものも変わったなと感じております。 計画対比がグラフで明示されていることにより、意識の変化も生まれたのかなぁと考えております。今までよりも時間当たり生産数というのを意識して、作業していただけるようになったのかなと感じています。
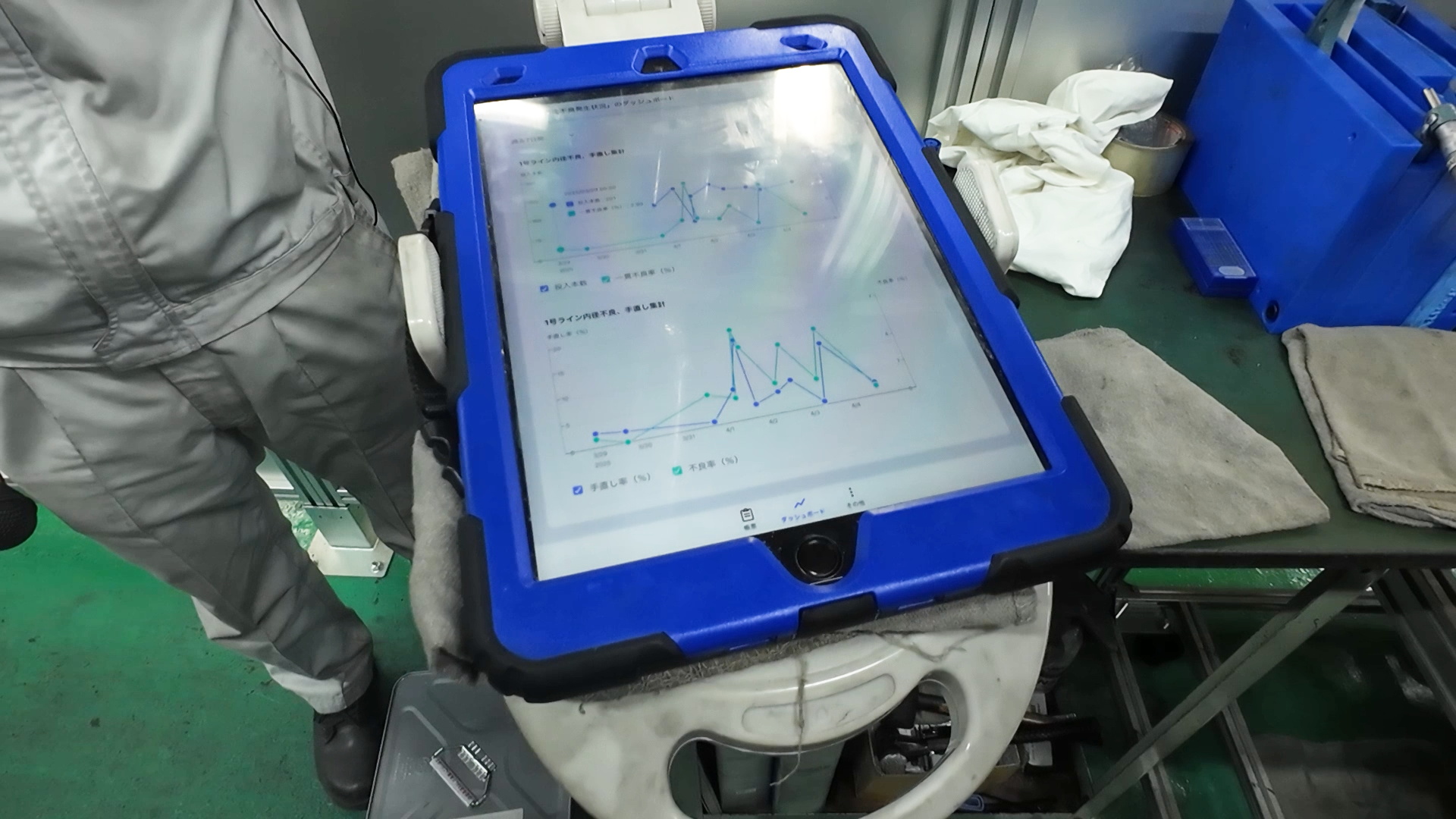
面白みを持って取り組みをどんどん拡大していきたい
今後の展望を教えてください
小林様:まだまだスタート地点かなというところです。現在帳票をデジタル化している工程の使用状況を見ても、スムーズに作業ができていると感じられますので、他の帳票類についても、スピード感を持って電子化を進めて、さらに効率よく作業ができる現場づくりをしていきたいなと考えております。
佐野様:さらに広めていくためには、現場の監督者の推進力というのが必要になってくるかな、というふうに思っています。 現場の監督者がデジタル化に面白みを持って取り組み、便利さを現場の作業者に感じてもらえるか、というのが大事になってくるかと思っています。
同席した小林の現場でも、試行錯誤しつつ帳票を作り込んでいてですね。多種多様な帳票を管理者が作業者を巻き込み、楽しみながら帳票を電子化する取り組みが広がっています。この取り組みが工場全体に広がれば、デジタル化を推進力として、生産性が大きく向上することに期待したいです。
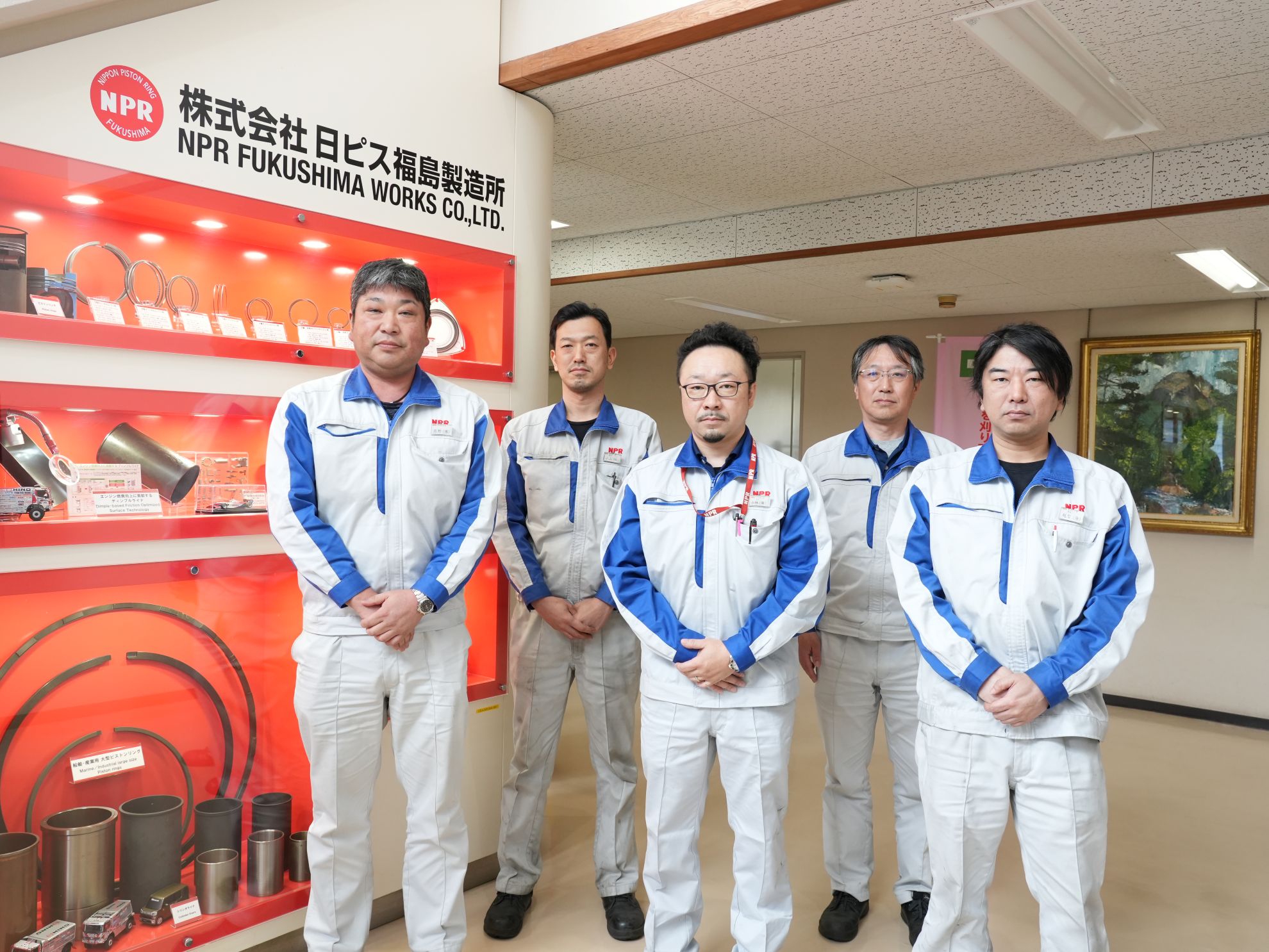