前回の記事「サプライチェーンマネジメント(SCM)とは?基本概念と仕組みをわかりやすく解説」では、SCMの定義、歴史や目的そしてSCMと勘違いしやすい物流についても触れました。
今回のテーマでは「失敗事例から紐解く、SCM最適化の成功に必要な条件」をSCMコンサルタントの視点で解説しようと思います。
各企業が、それこそ必死にSCMの思想を理解し、その仕組みを取り組もうとした結果、残念ながら失敗した例はたくさんあるものの、ブランディング等の観点から企業はSCMの失敗に対する反省コメントを自ら出さないものです。ただビジネススクールでは実際にあった企業の失敗例を学ぶ機会を提供してくれます。そこでは教授と学生とで、様々なディスカッションが繰り広げられ、チームを組んで原因を分析し、どうすべきだったかまで議論します。
そこで今回は、にわかMBA授業っぽくなりますが、いくつかすでにパブリックになっているSCMの失敗事例を紹介しながら、私なりの視点でコメントを入れつつ、失敗の根本的原因を見出せればと思います。そこから、SCMの最適化を実現するには何が必要なのか?少しでもヒントが見えてくる内容になっていますので、どうぞご覧ください。
※当メディア「現場改善ラボ」にてSCMの実践ヒントや事例に関する連載記事を執筆しております。本記事は「2記事目」です。
▼執筆者
リソース・グローバル・プロフェッショナル・ジャパン株式会社
RGPコンサルタント 木内 祥二
大学卒業後、住友電気工業に入社。海外部にて子会社の拡販支援を担当。その後オーストラリアに留学しMBAを取得。コスト削減のケーススタディでSCMと出会う。帰国後は様々な業種の外資系企業でSCMの実務を経験。現在はRGPのSCMコンサルタントとして活動中。
目次
SCM失敗例(1):トイザらスの破綻(2017)
みなさんよくご存知の方も多いトイザらス(Toys “R” Us)ですが、2017年9月に米国で破産申請を行い、2018年には全米の735店舗を閉鎖しました。(ただ、トイザらス日本は本社が経営破綻した影響を受けたものの、現在も約160店舗運営をしております。)かつて世界最大の玩具小売業者だった同社は、なぜ破綻してしまったのか?たしかに破綻に至るいろいろな要素(財務戦略の失敗、マーケットにおける競争の激化など)があったと言われてますが、一つの破綻要因として「サプライチェーンの問題(物流の遅れ・高コスト構造)」が指摘されます。以下3つの主な原因があると、すでに公に言われてますので紹介します。
原因1. EC(E-Commerce電子商取引)対応の遅れ
- Amazon、ウォルマートと比較して オンライン注文・配送のスピードが遅かった。
- 消費者がオンラインで購入する傾向が強まる中、トイザらスのECシステムは時代遅れだった。
原因2. 店舗過多による固定費の増大
- 2017年時点で、 全世界で1600店舗以上を展開 しており、多くの不採算店舗を抱えていた。
- ECシフトが進む中、リアル店舗の維持コストが重荷となった。
原因3. 物流コストの高さ
- 大規模な倉庫・物流網を持っていたが、Amazonのような効率的なシステムを持っていなかった。
学びのポイント:消費者視点を無視した結果が招いた経営の失敗
一見すると、店舗過多による運営コストの増大とオンライン配送の遅延が発生し、顧客離れを招いたと言えるでしょう。しかしここで、私のSCM視点を入れるとするならば、「サプライチェーンはデマンドチェーンとも言われるように、つねに消費者視点にたっていないと、意味をなさないということ」です。
どんなに優秀なシステムを導入しようが、立派な倉庫や物流網を持っていようが、マーケットの動向、同業他社の動きなどを的確に早く察知し、究極的には消費者が何を期待しているのか、それを認識できていることが、SCM成功へのはじめの一歩なんです。
調達・購買の業務が長かった私は、いつもイライラさせるサプライヤーがありました。品質は超一級、価格もまあまあでしたが、いつも約束納期から遅延する、さらにこちらから督促しないと納期回答をしてこない。そこで、サプライヤーのパフォーマンスを数値化しようと試みQ(品質)、C(価格)、D(納期)、S(サービス)の4つの切り口で、主要なサプライヤーにだけに絞りましたが総合点をつけ毎年、通信簿として改善要求をしてました。ただ、買い手側(客先)から売り手側(サプライヤー)に、不満や改善をつねに口にださないことも多いのです。本来なら、その客先の不満情報を入手し、後方部隊にも連絡し、必要な手だてを即時にうっていくことが必要です。
ロジスティクスが兵站の意味と前回も申しましたが、ある意味マーケットは戦場で、兵站(=在庫センター)に、必要な武器弾薬(=商品)であったとして、戦線(=マーケット)で欲しい時にタイムリーに届けることができなければ、そこで戦いに負けてしまうことになる例です。トイザらスの場合、お客が欲しがっている商品は在庫にあったのだと思いますが、タイムリーにそれを客が欲しい時に届けることができなかった。代わりに、間隙を縫って台頭してきたアマゾンは、注文後翌日配送するようなクイックデリバリーを実現し、負けてしまった。
SCMの思想は、単にモノだけでなく、客先が欲しいときにタイムリーにデリバリできるサービスも実は大事であることを知らしめた一例です。
SCM失敗例(2):東日本大震災(2011年)によるサプライチェーン寸断による教訓とトヨタの対策
2011年3月11日の東日本大震災は、日本の製造業全体に深刻な影響を与えました。多くのグローバル企業は、東北に集中するTier1からTier3までのサプライヤー(半導体や電子部品メーカーなど)の影響で、生産停止に追い込まれました。トヨタの場合だけでも推定20万台の機会損失といわれてます。
実は、この前にも2004年、2007年に新潟県で比較的大きな地震がありました。私もちょうど2007年の中越沖地震のときに、柏崎市の化学プラントや発電プラント向け制御バルブのメーカーでSCM責任者として勤務しておりましたが、当工場では精密切削の加工設備が多数ありましたが、当地震により設備が大きくずれてしまいました。さらにはコンクリートの床面の多くが損壊し、ひびが深く入っていたため、段差がいたるところに発生しました。
土台からやり直すことになり、さらに加工するための機械の芯だし調整まで含めると、復旧まで数か月かかるとの報告を受け、当時の注残分のお客様が運悪く納期のかかる海外向けで、しかも延滞ペナルティ契約条項のあるお客様でしたので絶望的になった記憶があります。幸い、多くの業者の皆さま、協力取引先の皆さまの昼夜問わずの懸命な復旧作業のご協力の甲斐あって、1か月もかからず復旧することになりました。
【中越地震(2004年)の被害状況】
- 2004年(平成16年)10月23日(土)17時56分、新潟県中越地方を震源とするマグニチュード(M)6.8の大地震が発生。
- この地震により、新潟県の川口町で震度7、小千谷市と長岡市で震度6強、魚沼市と刈羽村で震度6弱を観測したほか、東北地方から近畿地方にかけての広い範囲で震度を観測。
- 中山間地のインフラを大きく損壊。
- 67人が死亡、4805人が負傷、12万棟を越える住宅被害が発生。
【中越沖地震(2007年)の被害状況】
- 2007年(平成19年)7月16日(月)10時13分,新潟県上中越沖の深さ17kmでマグニチュード6.8の地震が発生。
- 新潟県柏崎市,長岡市,刈羽村,長野県飯綱町で震度6強,新潟県上越市,小千谷市,出雲崎町で震度6弱を観測。
- 新潟県三条市,十日町市,南魚沼市,燕市,長野県中野市,飯山市,信濃町で震度5強を観測。
- 北陸地方を中心に東北地方から近畿・中国地方にかけて震度1以上を観測。
- 地方の中堅都市の個人宅や商店街など生活を直撃。
- 柏崎刈羽原子力発電所も被災。
- 14人が死亡、2000人以上が負傷、約4万棟の住宅に被害があった
これらの出来事から、自然災害を想定する重要性を肌で感じた次第です。ちょうど同じタイミングでしたが、たまたま同じ柏崎市にあった世界的にも有名な「リケン」というメーカーのエピソードも、紹介したいと思います。同社はミクロン単位の超精密な薄さのピストンリング(エンジンのピストンに取り付ける金属製の輪)を量産できる唯一のメーカーですが、私どもの工場と同様、地震により、生産加工設備が数メートルも横ズレして使えない、床面もガタガタな状態であることは容易に想像できました。
ただ国内シェア50%をもつこのピストンリングの生産が停止になっては、当時全12社に納品されていた各自動車メーカーはラインストップを招き、莫大な損失につながるということで、いっせいにトヨタからは330人、日産から100人、三菱40人、ホンダ30人、設備機器メーカーの社員も終結し、総勢650名という援軍が、一刻も早く復旧へという願いで駆け付けたのです。そのおかげで7月16日(月)に被災しましたが、なんと、その週の7月20日(金)からは徐々に生産開始にこぎつけることができ、翌週までにはフル操業まで復活を果たしたという、死中に活を見出すとはこのことだと思いました。
このように地震災害でサプライチェーンが寸断されたときの対策を、トヨタの例でおさらいしてみますと、
トヨタは3つの主要対策を立て、サプライチェーンの強靭化を図っております。
代替サプライヤーの確保
- 震災直後、トヨタは影響を受けたサプライヤーの生産再開を支援すると同時に、代替サプライヤーを緊急に確保。
- 特に半導体や塗料などのボトルネック部品は、国内外のサプライヤーを迅速に探し、調達ルートを確保。
- 重要部品については 「マルチソース調達」 を進め、特定のサプライヤーに依存しない体制を強化。
サプライチェーン全体の可視化
- トヨタは震災後、新たに迅速な供給確保のためのシステムを導入。
- これにより、部品メーカーの階層構造を可視化し、どの部品がどのサプライヤーから供給されているかを即座に把握できるようにした。
- 以前は Tier1(一次サプライヤー)までしか把握していなかったが、Tier2(部品メーカー)、Tier3(素材メーカー)までデータを共有し、供給リスクを分散することが可能にした。
重要部品の「適正在庫」確保
- 従来の「ジャスト・イン・タイム(JIT)」方式の弱点を補完するために、特定の重要部品については「適正な在庫」を確保する方針に変更。
- 特に調達が困難な部品(半導体、特殊素材)については、3〜6か月分の在庫を持つことを推奨。
- これにより、今後同様の災害が発生しても、即座に生産が停止しない体制を構築。
学びのポイント:BCPの準備不足でサプライチェーンの脆弱性が露呈したケース
トヨタは、カンバンで有名なジャスト・イン・タイム生産方式を採用しており、部品在庫を最小限に抑え、サプライヤーから必要な部品を必要なタイミングで調達していました。これを誇らしげに世間にも協力関連会社にも教育しておりましたが、キャッシュフロー経営で在庫を薄くもっていたことが、裏目に出てしまった例となります。その結果、一時生産停止に追い込まれ、トヨタのグローバルな生産ラインに深刻な影響が出ました。トヨタだけでなく、他の自動車メーカーも同様の影響を受け、日本の自動車産業全体が大きな打撃を受けました。
今回の例は、SCMの失敗例としていいたくはないのですが、日本は天災(地震、津波、台風、洪水、山火事、土砂くずれなど)という不可抗力の災害が発生するリスクが高い国である、という認識を改めて持つべきであり、そのためには災害に備えておくべきだったという観点では、猛省すべき失敗例です。今後の大きな教訓として、サプライチェーンにおけるBCP(Business Contingency Plan)対策を各社で怠らないようにすることがまず肝心です。
また、一方でこのようなBCPを発動するような緊急事態においては、すべての取引協力会社者、Tier1~3までのサプライヤーとの関係、またお客様との関係も非常に重要であることを痛感した出来事でもありました。とくにサプライヤーとの関係は、なんでも無理難題をおしつけるような一方的交渉が前時代にはありましたが、リケンのようにいざという時にサプライヤーだけではなく、納品先のお客様からも650人もの援軍が瞬時にかけつけてくれる、そういった協力関係を日頃から築いていたことに、深く敬意を表す次第です。
SCM失敗例(3):ウォルマートの「オンタイム・インフル」施策の混乱(2017年)
次のケースは、上記の例とは真逆となる例を紹介します。ウォルマートのケースです。ご存知の方も多いと思いますが、当企業は米国アーカンソー州に本部を置く同族経営の世界最大のスーパーマーケットチェーンです。
まずその圧倒的な過去10年の売上高推移を見てみましょう。先週20日に発表が昨年通期の発表があったばかりです。こちらもトップの座をキープしております。
▼ウォルマートの売上推移
2025年:6809億85百万ドル(約102兆円 1ドル=150円換算)
2024年:6481億25百万ドル(約 97兆円 1ドル=150円換算)
▼2023年以降の売上推移
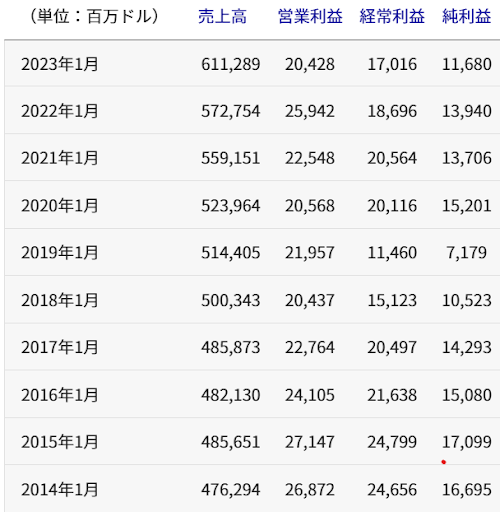
出典:Google
ただ当会社を調べるといろいろ経営面の批判記事もあり、ネガティブな情報も、たくさんヒットしてくるのですが、私は彼らのSCM戦略に特に注目してます。その戦略が効を奏して、やはり売上や利益につながっている会社の一つではないかと見ており、たとえ読者のみなさんの業界が違う場合でもあっても、是非彼らのSCMを実践で学ぶポイントがたくさんある会社です。
ただ、すみません!今回のケースは、NegativeなウォルマートSCM失敗例を学ばせていただくことになります。
ウォルマートのOTIF施策は何故、失敗したのか?
ウォルマート(Walmart)は2017年、「On-Time In-Full(OTIF)」という新しい物流基準を導入しました。この施策の目的は、サプライチェーンの効率化と在庫最適化でした。具体的には、ウォルマートの店舗や物流センターに納品される商品が、決められた時間通り(オンタイム)に、必要な量が揃った状態(インフル)で届くようにすることを目指しました。トヨタのJIT思想を取り入れたんでしょうか。
OTIFの具体的なルール
ウォルマートは、サプライヤー(メーカー・卸業者)に対し、より厳格な納品基準を課しました。
- 納品期限(オンタイム)
- フルトラック便(Full Truck Load, FTL): 75% → 85% まで基準を引き上げ(2017年8月)。
- 少量配送便(Less than Truck Load, LTL): 33% → 50% まで基準を引き上げ(2018年4月)。
- 納品量(インフル)
- 納品された商品が注文された数量と完全に一致していることが求められた。
- 不足や過剰納品があった場合は罰則対象とされた。
- 罰則(ペナルティ)
- 納品遅れ・不足・過剰が発生すると、サプライヤーは納品額の3%の罰金を課された。
この施策により、ウォルマートの物流精度を向上させ、棚在庫を最適化することが目的でした。
混乱を招いた主な原因
OTIF施策の導入は、ウォルマートのサプライチェーン全体に混乱をもたらしました。概略の原因は想像つくかと思いますが、以下の4つにまとめられています。
サプライヤーの準備期間が短すぎた
- ウォルマートはこの施策を2017年初めに発表し、同年8月には新基準を適用した。
- しかし、多くのサプライヤーにとって、新基準を満たすための調整期間が不足していた。
- 物流管理システムの改良、供給計画の見直し、トラック運転手の確保などが間に合わず、混乱が発生。
米国内のトラック運転手不足
- 2017年当時、米国内ではトラック運転手の人手不足が深刻化していた。
- OTIF施策によって配送スケジュールが厳格になったため、適切なタイミングでトラックを手配できないサプライヤーが増加。
- 配送の遅延や不足納品が頻発し、多くのサプライヤーが罰金を課される事態になった。
過剰なペナルティ制度
- OTIFの厳格なペナルティ制度により、サプライヤー側のリスクが急増。
- 例えば、倉庫や物流センターの都合でウォルマート側が受け入れできなかった場合でも、サプライヤーに罰則が適用されることがあった。
- 不公平な罰則と受け取られ、サプライヤー側の不満が高まった。
サプライヤー側の在庫負担増加
- OTIF施策の影響で、サプライヤーは納品遅れを防ぐために、余分な在庫を持つ必要が生じた。
- しかし、ウォルマートの別の施策(「リーン在庫管理」)では過剰在庫を減らすよう求められており、サプライヤーは矛盾する要求に直面した。
学びのポイント:本来、大事にすべき協力外注先(サプライヤー)をないがしろにしたツケが招いた混乱
OTIF施策導入後、多くのサプライヤーから強いクレームがウォルマートに寄せられました。ウォルマートは急遽、柔軟な対応策を迫られ、あらためて当制度の見直しをせざるを得ないことになりました。その結果、2019年にはOTIF基準の遵守率が90%を超え、物流の安定化に成功。サプライヤーの在庫管理の精度も向上し、ウォルマートの在庫回転率が改善。店舗の棚在庫が最適化され、欠品率の低下に貢献することになったのです。
この例は、世界的に売上トップの座に君臨した企業がさらに売上アップ、利潤アップを早急に目指した結果、サプライヤーに過剰負荷をかけてしまった失敗例といえます。トップの座を継続してきた実績が、傲慢さとエゴが先走り、一人勝ちになりやすい状況だったのかとは思いますが、客先が大企業だからという格差がうまれる考えではなく、調達側(買い手)と供給側(売り手)の論理からも、示唆している教訓となるケースと思います。
米国独禁法と日本の独禁法には違いがあるのですが、もし日本で今回のウオルマートのOTIF施策を実施してしまっていたら独禁法違反にあたる可能性が大と思われます。以下、専門的な見方を紹介しておきます。
米国(Sherman Act, FTC Act)
- 米国では「独占禁止法(Sherman Act)」や「連邦取引委員会法(FTC Act)」が存在し、市場支配力を持つ企業が不当に取引条件を押し付ける行為は違法とされる。
- ただし、米国の独禁法は競争者間の制約を重視しており、ウォルマートとサプライヤーの取引は「市場競争の阻害」とまでは言いにくいため、米国では直接違法とはなりにくい。
日本(独占禁止法)
- 日本の独占禁止法では「優越的地位の濫用」(第2条・第19条)を禁止。
- 公正取引委員会(公取委)は、特定の小売業が取引先に過剰な負担を強いる行為を「優越的地位の濫用」と判断することがある。
- ウォルマートが日本市場で同様のOTIFを実施し、サプライヤーに過度な負担を課した場合、規制対象となる可能性がある。
補足:お客様だけでなく、サプライヤーも神様です⁉
最近はサプライヤーという呼び方がいかにも上から目線だという反省までされており、最近の傾向として、企業によっては「パートナー」「協力企業」「共創パートナー」といった表現を使うケースが増えてきています。
製造業では「協力会社」「協力外注先」という表現が一般的。
▼例
トヨタ:「サプライヤー」ではなく「仕入れ先」「協力会社」を使用することが多い。
パナソニック:「グローバルパートナー」と呼び、調達先を協力関係の視点で捉えている。
小売・流通業では「取引先」「パートナー」がよく使われる。
▼例
ユニクロ(ファーストリテイリング):「パートナー工場」という呼び方を使い、単なる発注者-受注者の関係ではなく、共に品質向上に取り組む姿勢を強調。
IT業界では「ベンダー(vendor)」や「開発パートナー」という表現が多い。
「サプライヤー」という言葉が完全になくなったわけではありませんが、対等な関係を重視する企業では「協力企業」「パートナー」「協力外注先」などの呼び方に変える傾向が強まっているのは確かです。特に日本企業では、「協力会社」や「協力外注先」といった表現が好まれることが多くなっています。
まとめ
3つのSCM失敗のケースを一緒に見ていきましたが、いかがでしたでしょうか?これらの失敗例から逆に、SCMの成功に必要なものは何か、少しは見えてきませんか?そこで次の記事で、SCMの成功例にも目をむけてみましょう。成功例から見出せるSCM最適化のヒントについて言及できればと思います。
▼参考文献
・米トイザラス破たん、日本の店はどう生き残る?:日経ビジネス電子版
・日本のトイザらスが米国と違い大健闘のワケ 米国はアマゾン効果よりもLBOの負担で自滅 | 百貨店量販店・総合スーパー | 東洋経済オンライン
・asahi.com:復旧急げ、自動車業界650人集結 柏崎の部品工場へ – 新潟県中越沖地震
・東日本大震災から10年、企業のサプライチェーンはどう変わったか?(坂口孝則) – エキスパート – Yahoo!ニュース
・大震災がサプライチェーンにもたらしたもの ~より強い日本のモノ作りに向けて~|経営研レポート 2011 | NTTデータ経営研究所
・第2章 第1節 生産の立て直しとサプライチェーンの再編成 – 内閣府
・トヨタのBCP 供給網DB「レスキュー」の威力|記事一覧|企業・自治体向け防災情報メディア「防災ニッポン+」読売新聞
・「ウォルマート」、2000/5/26、ボブ オルテガ (著), Bob Ortega (原名), 長谷川 真実 (翻訳)
・「ウォルマートはなぜ、世界最強企業になれたのか (グローバル企業の前衛)」 2014/9/2、ネルソン・リクテンスタイン (著), 佐々木 洋 (翻訳)
▼会社、参考団体、組織、KeyWord:
・企業情報|日本トイザらス株式会社
・企業情報 | 株式会社リケン
・Walmart | Save Money. Live better.
・トヨタ自動車WEBサイト