食品工場におけるリスクアセスメントは、2021年6月からスタートしたHACCPの完全義務化に伴い、ますます重要視されています。しかし、現場で活かせる知識はまだ十分に普及していないのが現状です。
本記事では、食品工場でのリスクアセスメントの基礎から導入方法、実際の導入事例までわかりやすく解説します。トラブルを未然に防ぐための知識を、この記事で押さえていきましょう。
リスクアセスメントについての詳しい解説にご興味のある方は、無料セミナーをご覧ください。専門家の視点から見た「危険を見極めるポイント」についてご紹介しています。
目次
リスクアセスメントとは?簡単に解説!
まずリスクについておさらいしましょう。リスクは「危険性・有害性」と言葉が似ていますが、異なる概念であるため、分けて考える必要があります。たとえば、ライオンそのものは危険ですが、人が関わらなければ襲われることはありません。しかし、人が近づけば襲われる可能性が出てきます。この「襲われる可能性」がリスクです。

引用元:厚生労働省「食品加工作業におけるリスクアセスメント」
一方、リスクアセスメントとは、工場内に潜む危険性・有害性を可能な限り見つけ出し、それぞれのリスクが発生した場合の被害の大きさを順位付けして、その順位に基づき対策を講じる方法です。
簡単に言えばリスクアセスメントとは、工場内に潜むライオンを探し出して、その大きさや凶暴度を順位付けし、上位から出会わないような対策や出会ってしまった場合の対応を考えることです。
リスクアセスメント実施は、労働安全衛生法にて事業者の責務として規定されています。
第二十八条の二
事業者は、厚生労働省令で定めるところにより、建設物、設備、原材料、ガス、蒸気、粉じん等による、又は作業行動その他業務に起因する危険性又は有害性等(第五十七条第一項の政令で定める物及び第五十七条の二第一項に規定する通知対象物による危険性又は有害性等を除く。)を調査し、その結果に基づいて、この法律又はこれに基づく命令の規定による措置を講ずるほか、労働者の危険又は健康障害を防止するため必要な措置を講ずるように努めなければならない。
このシステムを実施するタイミングについては、労働安全衛生規則第24条の11で以下のように定められています。
- 建設物の設置・移転・変更・解体時
- 設備や原材料などの新規採用や変更時
- 作業方法の新規採用や変更時
- 建設物、設備、原材料、ガス、蒸気、粉じんなどにより環境に変化が生じた時
リスクアセスメントを実施する目的について詳しく知りたい方は、以下の関連記事をご覧ください。
関連記事:リスクアセスメントの目的とは?実施に向けた進め方のポイントや企業事例も解説
リスクアセスメントは安全対策の根幹になる
食品工場は、労働災害が非常に多い現場です。農林水産省の『食品産業の安全な職場づくりハンドブック』によると、全産業および製造業の平均と比べて2倍以上にのぼります。
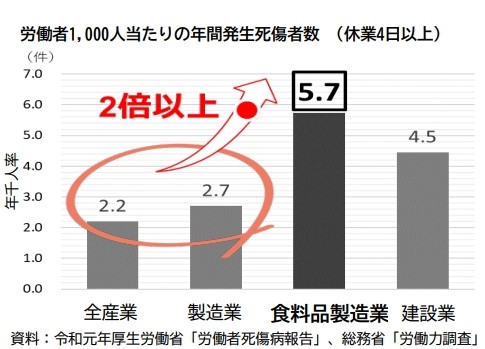
引用元:農林水産省「食品産業の安全な職場づくりハンドブック」
リスクアセスメント導入により、労働災害が発生する前に予防策を講じられるため、安全対策の基盤を築きます。また、手順に沿って実施することで、費用対効果の高い対策が優先的に行われ、予算の効率化も可能です。
リスクアセスメントシステム実施のメリットや導入効果は?
リスクアセスメントで得られるメリットは、以下の通りです。
自社工場で活かせるかどうか、イメージしながらご覧ください。
職場に潜むリスクが明確になる
リスクアセスメントを通じて、作業内容や作業環境を細かく分析でき、これまで見過ごされていたリスクや、経験だけでは気づけなかったリスクを特定できます。
これにより工場内の安全性が向上し、事故やケガの未然防止が可能です。また、各工程ごとの危険度が明確になるため、従業員の安全意識向上にも役立ちます。
衛生管理の徹底
リスクアセスメントシステムは、従業員の健康を守るだけでなく、消費者への食品衛生を確保します。衛生管理上の問題や食品汚染のリスクも明らかにするため、誰にとっても安全・安心な食品を提供できます。
リスクアセスメントは、HACCPの導入手順「手順6 (原則1) 危害要因の分析」にも役立てることが可能です。HACCPの「手順6 (原則1) 危害要因の分析」について詳細に知りたい方は、以下の記事をご覧ください。
関連記事:【例あり】HACCPの危害分析とは?やり方を解説!(分析表エクセル配布)
的確な安全対策を実施できる
リスクの優先順位に基づき、最も効果的な対策が行えるため、時間とコストを最適化したムダのない安全対策が実施できます。また、人的対策から機械・設備への対策まで幅広い対策を検討し、各リスクに合った対策が可能です。
ルールの運用がスムーズになる
対策を打ち出しても、技術的・時間的・経済的な理由からすぐに対処できないリスクもあります。そうしたリスクに対しては、従業員にリスクをリスクと認識させる教育が必要です。
その際に、このシステムによって伝えるべき内容や守るべき理由が明らかになっているため、ルールを教育しやすくなるでしょう。
食品製造現場におけるリスクアセスメントの導入方法
それでは、食品製造現場で導入する手順について解説します。実際の導入シーンを想像しながらご覧ください。
リスクアセスメントの進め方を動画でわかりやすく学びたい方は、以下のリンクから元労基署長による解説動画をぜひご覧ください。現場のキケンを見極める術が身に付きます。
① 実施体制の確立
まず、責任と役割を明らかにします。具体的には、実施の担当者やチームを決め、メンバーに実際の流れや目的を理解させます。以下の手順で行うとスムーズです。
▼体制を作る基本的な順番▼
- 経営トップ(経営者、工場長)による導入宣言
- 担当者・チーム決め
- 実施手順の作成
- リスクアセスメントの試行
- 従業員への教育・トレーニング
② 実施時期と対象の選定
実施時期・対象を明確化することで、現場の状況に適した策定が可能になります。次のうち当てはまるのはどれか考えて、対象を決定しましょう。
時期 | 対象 |
---|---|
初めての実施 | このとき、対象にする設備や作業の選定が必要です。 その上で、対象へのリスクをモレなく見つけ出せる方法を考えます。 |
法令で定められた時期での実施 | 法令に基づき、新規採用・変更した設備や作業を対象とします。 |
定期的な実施 | 一定期間ごとに実施することで、作業内容の見直しが可能です。 |
③ 情報収集
以下の情報を整理・収集しておきましょう。この情報が、⑤で具体的な被害を予測する際に役立ちます。
- 作業手順書
- 取扱説明書
- 普段の5S活動の成果
- KY活動で出された危険箇所
- 安全衛生パトロール
- 突発的な作業に関わる資料
「5S活動」「KY活動」についておさらいしたい方は、以下の関連記事をご覧ください。
▼関連記事▼
・業務改善につなげる「5S活動」の進め方!目的や事例、アイデアも解説
・KY活動(危険予知活動)とは?進め方や記入例文を解説【エクセルテンプレ有】
④ 危険性・有害性の特定
該当する機械設備や原材料、作業工程、環境の危険性・有害性を見つけ出し、そのリスクがどのようなものかを特定します。
次に示す図は、危険性・有害性に対して発生するおそれのある労働災害をまとめたものです。危険性・有害性を特定する際に参考にしてください。
.jpeg)
引用元:厚生労働省「食品加工作業におけるリスクアセスメント」
また、⑤を実施する準備として「誰が」「何によって」「何をして」「どうなったか」を整理しておきます。
.jpeg)
引用元:厚生労働省「食品加工作業におけるリスクアセスメント」
⑤ リスクの見積もり
④をもとに、以下の項目を明確にしてリスクの大きさをランク付けします。
これからご紹介する方法はすべて、厚生労働省が公開している「食品加工作業におけるリスクアセスメント」を参照/引用しております。
危険性・有害性に接触する頻度
頻度を決める際のポイントは、その作業を行う回数ではなく、実際に危険性・有害性と出会った回数を基に考えることです。
点数 | 頻度(例) |
---|---|
4 | 1日あたり1回以上 |
3 | 3日あたり1回以上 |
2 | 週1回以上 |
1 | 月1回以上 |
ケガ・疾病が起こる可能性
次に、作業者が危険性・有害性に接触した時に、ケガや疾病が起こる可能性を検討します。考え方としては、安全のためのカバーがついているか、足を滑らせない床構造になっているか、保護具などの着用があるか、教育しているかどうかなどを基に点数を付けます。
▼点数のつけ方の例▼
点数 | 可能性 | 目安(例) |
---|---|---|
6 | 極めて高い | ①危険領域に体の一部が入る(届く) ②防護カバーなどの工学的対策がない ③非常停止装置がない ④表示や標識がない ⑤保護具がない ⑥マニュアルがない |
5 | 高い | ・①が〇 ・②~⑥で〇が4つ |
4 | 比較的高い | ①~⑥で〇が3、4つ |
3 | 比較的低い | ・①~⑥で〇が3つ ・安全教育で基準や保護具について教育している |
2 | 低い | ・①~⑥で〇が1、2つ ・安全教育で基準や保護具について教育している |
1 | 極めて低い | ・①~⑥で〇がない ・安全教育で基準や保護具について教育している |
ケガ・疾病の重篤度
厚生労働省「食品加工作業におけるリスクアセスメント」によると、重篤度は低く見積もられがちなため、最大の大きさを想定して考えましょう。
点数 | 頻度(例) |
---|---|
10 | 死亡や永久的労働不良につながるケガ |
6 | 長期療養を要するケガおよび障害の残るケガ |
3 | 休業災害および不休災害(いずれも完治可能なケガ) |
1 | 手当後、直ちに基の作業に戻れる軽微なケガ |
リスクを評価する
3つの項目の点数を加算して、リスクのレベルを評価します。点数が高いほど、リスクレベルも高く、優先して取り組む必要があります。
点数 | リスクレベル | 優先度 |
---|---|---|
12以上 | Ⅳ | 直ちに中止または改善する |
9~11 | Ⅲ | 優先的に改善する |
6~8 | Ⅱ | 計画的に改善する |
5以下 | Ⅰ | リスクに応じて教育や人材配置をする |
練習として、以下のソーセージを製造する食品工場の例を考えてみましょう。
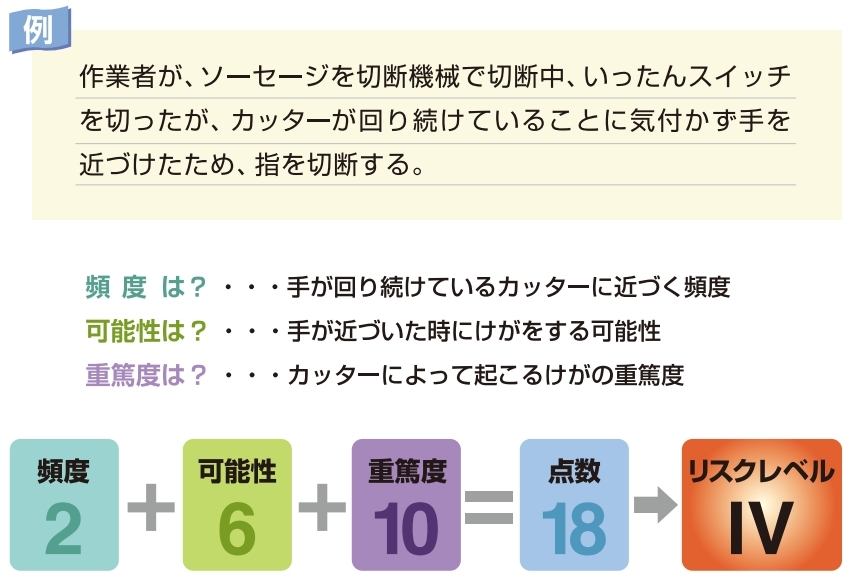
⑥ リスク低減措置の検討及び実施
⑤で見積もりをしたリスクに対し、適切な対策を検討・実施します。この際、以下の図の流れに沿って優先順位の高いものから順に対策を行います。ただし、法令で定められた事項については必ず実施しましょう。
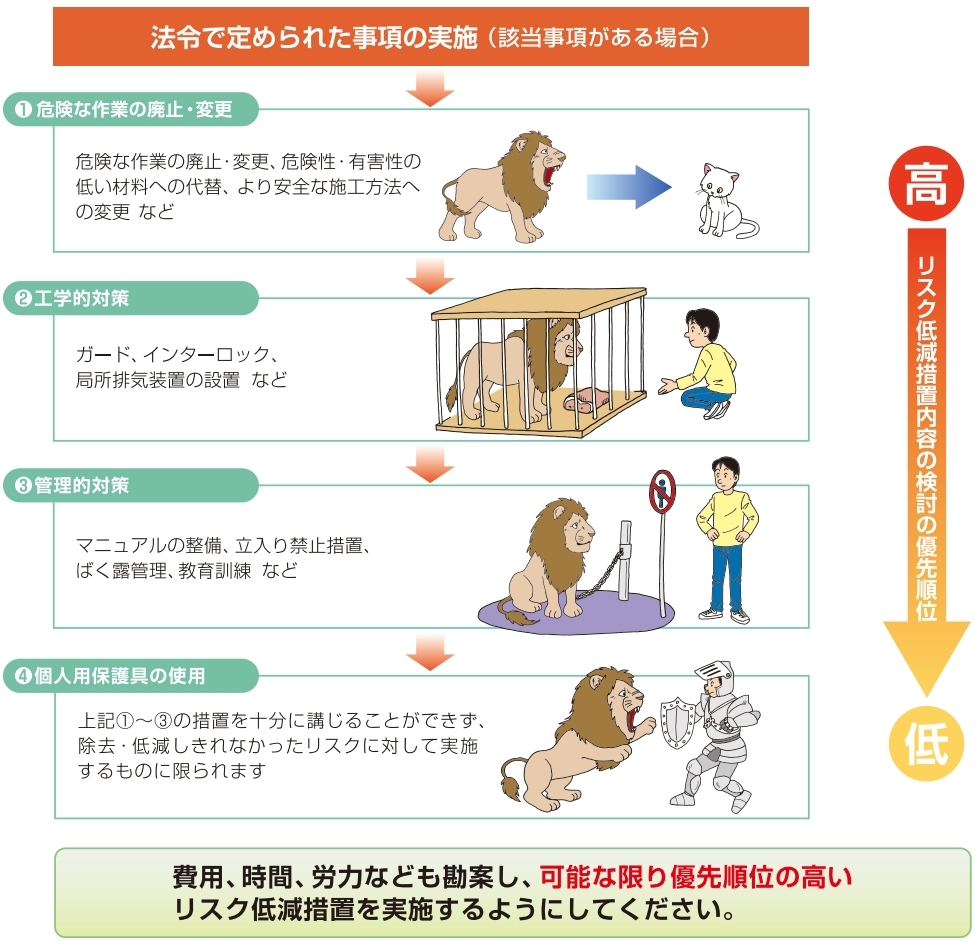
引用元:厚生労働省「食品加工作業におけるリスクアセスメント」
⑦ 実施状況の記録と見直し
リスクアセスメントは「実施して終わり」ではありません。実施後も適切な対策か、さらなる改善が必要かを検討します。
▼見直しのポイント▼
具体的な見直しの方法 | |
---|---|
リスクに変わりはないか | 手順の更新や変更により、新たなリスクが発生していないか確認 |
リスクの見積もりは適切だったか | 当初の見積もりが現状に合っているか再評価 |
実施した対策の効果 | 対策がどのような効果を生み出したかや、事故防止に繋がっているかをチェック |
従業員からのフィードバック | 現場で働く従業員からの意見を取り入れ、見直し・改善 |
リスクアセスメントの各段階で実施した内容や対策の状況を記録することは、リスク管理の有効性を確認するうえで重要です。記録を管理することで、進捗や改善状況がわかりやすくなり、次回以降のリスクアセスメントに役立ちます。
食品製造現場におけるリスクアセスメント実施事例
食品製造現場におけるリスクアセスメント例をご紹介します。
機械へのリスクアセスメント事例
まずご紹介するのは、おにぎり成型機械により作られた「おにぎりのくぼみに具材を入れる工程」の事例です。右の作業者は、おにぎりを直そうとして安全カバーを外しています。
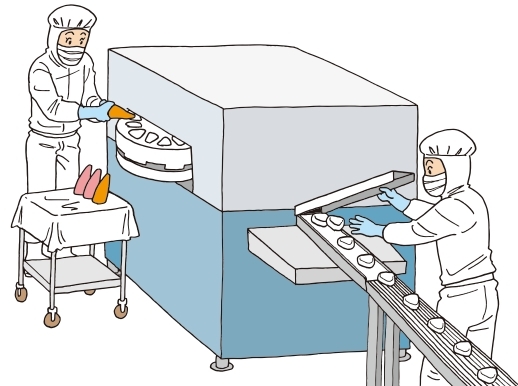
引用元:厚生労働省「食品加工作業におけるリスクアセスメント」
この場合のリスクアセスメントは、以下の通りです。
- 危険性・有害性の特定
作業者が安全カバーを外し、機械の中に誤って指を入れ、切断する
- リスクの見積もり
頻度 | 可能性 | 重篤度 | リスク(合計点数) |
---|---|---|---|
1 | 2 | 10 | Ⅳ(13) |
- リスク低減措置の検討及び実施
機械が止まらないと安全カバーが外れない構造にする
- 実施状況の記録と見直し
頻度 | 可能性 | 重篤度 | リスク(合計点数) |
---|---|---|---|
1 | 1 | 1 | Ⅰ(3) |
環境へのリスクアセスメントの事例
次にご紹介するのは、食品製造工場での事例です。作業者は荷物を両手で抱えて運んでいます。
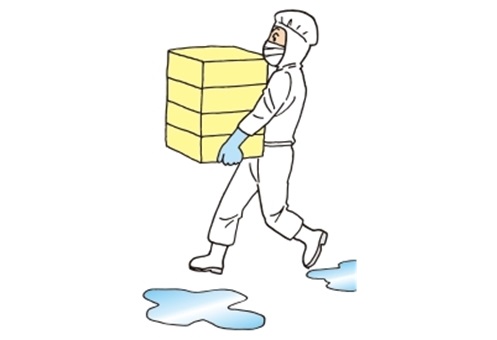
引用元:厚生労働省「食品加工作業におけるリスクアセスメント」
この場合のリスクアセスメントは、以下の通りです。
- 危険性・有害性の特定
荷物で足元が見えず、濡れている床を踏んでしまい転倒・打撲する
- リスクの見積もり
頻度 | 可能性 | 重篤度 | リスク(合計点数) |
---|---|---|---|
4 | 4 | 10 | Ⅳ(18) |
- リスク低減措置の検討及び実施
一定の量以上の荷物は台車に乗せて運ぶ
- 実施状況の記録と見直し
頻度 | 可能性 | 重篤度 | リスク(合計点数) |
---|---|---|---|
1 | 1 | 3 | Ⅰ(5) |
設備へのリスクアセスメントの事例
最後にご紹介するのは、回転体の周りに柵が設置された工場の事例です。対策前は、画像のように簡単に腕が入ってしまう状態でした。
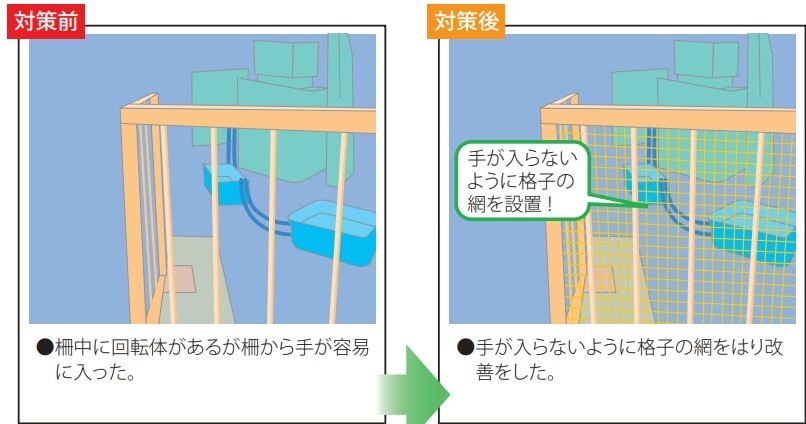
この場合のリスクアセスメントは、以下の通りです。
- 危険性・有害性の特定
作業者の手が柵の隙間に入ってしまい、機械に触れて打撲する
- リスクの見積もり
頻度 | 可能性 | 重篤度 | リスク(合計点数) |
---|---|---|---|
4 | 5 | 3 | Ⅳ(12) |
- リスク低減措置の検討及び実施
機械が止まらないと安全カバーが外れない構造にする
- 実施状況の記録と見直し
頻度 | 可能性 | 重篤度 | リスク(合計点数) |
---|---|---|---|
1 | 1 | 3 | Ⅰ(5) |
まとめ
本記事では、食品工場でのリスクアセスメントの基礎から導入方法、実際の導入事例まで解説しました。
簡単に言えば、リスクアセスメントとは工場内に潜むライオンを探し出して、その大きさや凶暴度を順位付けし、上位から出会わないような対策や出会ってしまった場合の対応を考えることです。
リスクアセスメントを通じて、職場に潜むリスクが明確になり、的確な安全対策を実施できます。また、衛生管理の徹底やルールの運用がスムーズになるなど、多方面のメリットが得られます。
リスクアセスメントについて専門的な内容をより詳しく知りたい方は、無料セミナーをご覧ください。専門家の視点から見た「危険を見極めるポイント」についてご紹介しています。