かんたん動画マニュアル作成ツール「tebiki」、かんたんデジタル現場帳票「tebiki現場分析」を展開する、現場改善ラボ編集部です。
予防保全とは、定期的に保全業務を行い、機械や設備の安定稼働を目指す活動のことです。一方、予知保全は機械や設備の故障や不具合の予兆を検知し、検知したタイミングでの保全業務を指します。
本記事では、予防保全が失敗しがちな原因やその解決策、保全業務の効果を最大化するツールについて解説します。
製造現場の生産性を脅かす設備トラブル。その原因を特定し効果的に解決するためには、従来の予防保全や予知保全だけでは不十分であり、現場のDXが求められる場合があります。「設備保全のトラブルを解消するDX」については以下の資料でも解説しておりますので、本記事と併せてご覧ください。
目次
予防保全とは
予防保全とは、事故や故障などのトラブルを予防することを目的に行われる設備保全のことです。PM(Preventive Maintenance)と呼ばれることもあります。
計画的な点検やメンテナンスを行うことで、設備が故障する前に問題の兆候を発見し、安定した稼働の維持を目指します。この手法は突発的なトラブルによる生産ラインの停止や修理費用の増大を防ぐだけでなく、設備の寿命を延ばし、総合的なコスト削減にも寄与します。
予防保全の種類や例
予防保全には、大まかに分けて以下の4種類があります。
時間基準保全(TBM)
時間基準保全(TBM)は英語でTime-Based Maintenanceと呼ばれ、設定された期間ごとに行う保全活動のことです。この手法は、特に設備の劣化が使用時間や経年によって予測可能な場合に有効です。
実施のタイミング | 設備や機械が使用される時間や経過年数に基づいて計画的に実施 |
目的 | 故障の発生リスクを最小限に抑え、設備のパフォーマンスを一定に保つ |
例 | ・1年に1回の定期点検 ・5年に1回のオーバーホール |
利用基準保全(UBM)
利用基準保全(UBM)は英語でUsage-based Maintenanceと呼ばれ、設備の利用回数や利用量を基準に行う保全活動を指します。使用頻度や負荷のかかり方が一定でない設備に適しており、過剰な保全や保全不足を防ぎたい場合に有効です。
実施のタイミング | 稼働時間や生産回数などの使用状況に基づいて実施 |
目的 | 設備の稼働量や負荷に応じた適切なタイミングで保全を実施することで、過不足なくメンテナンスを行う |
例 | ・800ショットごとの穿孔機メンテナンス ・走行距離10,000kmごとにエンジンオイルを交換 |
状態基準保全(CBM)
状態基準保全とは (CBM)は英語でCondition-based Maintenanceと呼ばれ、定期的に設備の稼働状態を測定し、状態が悪化した設備に対して行う保全活動です。
実施のタイミング | センサーや点検で設備の状態を監視し、異常兆候があれば実施 |
目的 | 状態監視を通じて異常を予測することで、突発的な故障による生産停止やコストの増加を最小限に抑える |
例 | ・振動や温度センサーによる軸受の異常検知 ・油圧機器の異常圧力検出 |
故障発見保全(FFM)
故障発見保全(FFM)は英語でFailure Finding Maintenanceと表記し、設備の故障を早期に発見して大規模なダウンタイムを防止する保全活動を指します。故障発見保全(FFM)は隠れた故障を検出することを目的としており、特に安全性や信頼性が重要視される場面で有効です。
実施のタイミング | 法規制や社内基準に基づいた定期点検時や、設備の運転停止時や特定のイベント前など |
目的 | 故障した設備を修理・交換し、正常稼働に戻す |
例 | ・常用発電機の定期的な起動試験 ・安全装置の動作確認 |
予知保全とは
予知保全(PdM:Predictive Maintenance)とは、近年注目されている設備保全の方法で、設備の状態をリアルタイムで監視し、異常や劣化の兆候をデータに基づいて予測することで、適切なタイミングでメンテナンスを実施する手法です。
従来の定期的な保全活動や、設備が故障してから修理を行う事後保全とは異なり、故障の兆候を検知して適切なタイミングで対処することを目的としています。そのため、設備の稼働効率を最大化しながら、不要な点検や部品交換を減らすことが可能です。
予知保全は、IoT(モノのインターネット化)に代表される技術の発展が大きく影響しています。設備のデータをリアルタイムで監視・分析し、それをもとにAIが異常兆候を検出することで、劣化が進んでいる箇所や潜在的な故障の可能性を早期に特定することが実現できるようになりました。
▼予知保全の種類や例▼
設備 | 仕組み | 効果 | 例 |
---|---|---|---|
IoTセンサー | 温度、振動、圧力などを監視し、閾値を超えたデータを検出 | ・異常の早期発見 ・故障の未然防止によるダウンタイムの最小化 | 温度センサーが過熱状態を検知し、システムの停止や修理を実施する |
加速度センサー | 設備の振動を検知し、異常振動を検出した際に警告を発する | ・設備の摩耗や損傷の進行を未然に防止 ・計画的な部品交換の実現 | モーターの異常振動を検知し、運転を停止して修理を行う |
AEセンサー | 設備から発生する超音波を検知し,分析して異常を特定 | ・微細な損傷や劣化の兆候を早期に把握 ・主要部品の完全な故障を防ぎ、保全コストを削減 | ベアリングの異常音を検知し、劣化が進む前に交換する |
電流センサー | 設備の消費電流を監視し、通常の動作範囲を超える電流値を検出し警告 | ・電子部品の過熱や劣化を未然防止 ・設備寿命を延ばしエネルギー効率を向上 | 過大な電流を検知し、回路の保護装置が作動。問題箇所を修理する |
事後保全とは
事後保全とは、設備や機器が故障やトラブルを起こした後に対処する保全のアプローチです。機械や設備などの故障や障害が既に発生した後に被害を最小限に抑え、できる限り早く機械を復旧させるための活動を指します。
事後保全は故障やトラブル発生後に対処する保全方法で、「修理保全」とも呼ばれます。
初期費用が抑えられる一方、突発的な停止や修理費用の増加といったリスクがあります。特に、稼働頻度が低い設備や修理が容易な場合には有効ですが、長期的には効率低下やコスト増を招く可能性もあります。現在では、予防保全や状態監視保全と併用し、リスク軽減を図るケースが増えています。
事後保全の種類や例
事後保全には、主に以下2つの種類があります。
- 緊急保全(EBM)
- 計画事後保全(BM)
緊急保全(EBM)
緊急保全(EBM)は英語でEmergency Breakdown Maintenanceと呼ばれ、設備が突発的な故障や異常で停止した際に迅速な対応を行う保全活動です。例として、生産ラインで使用している機械が突然停止した場合や、重要なコンプレッサーが異常音を出し動作を停止した場合などが挙げられます。
緊急保全のメリットは、迅速な対応により生産のダウンタイムを最小限に抑えられる点です。一方でデメリットとして、突発的な対応に伴うコスト増加や根本的な原因追求に十分な時間を割けないことが挙げられます。緊急保全は生産ラインの稼働を優先する場合に適した方法のため、予防保全と併用することでより安定した生産環境を構築できるでしょう。
計画事後保全(BM)
計画事後保全(BM)は英語でBreakdown Maintenanceと呼ばれ、設備が故障した際の対処をあらかじめ計画し、予備機や部品を準備しておくことで、迅速な修理や切り替えを実現する保全方式です。生産ラインで使用されるコンベアベルトが故障した場合、事前に予備のベルトを準備することで即座に交換作業を行い、ダウンタイムを最小限に抑えるといった例が挙げられます。
計画事後保全は突発的な故障が発生した際の対応を迅速に行うことが目的であるため、設備の予測不能な故障に対して即座に反応できる準備が求められます。そのため、予備の部品や必要なツール、作業手順書の整備といった事前準備が重要です。
一方で計画事後保全は予防保全に比べて依存度が高く、長期的にはコストがかさむ可能性があるため、予防保全とのバランスを取りながら運用することが重要です。
予防保全・予知保全・事後保全の違い
予防保全と予知保全、事後保全の違いをまとめると、以下の通りです。
保全方法 | 予防保全 | 予知保全 | 事後保全 |
---|---|---|---|
保全のタイミング | 定期的または計画的に実施 | 設備の状態に基づいて実施 | 故障発生後に実施 |
保全のきっかけ | 設定された期間、利用回数、または状態 | センサーやデータ解析による異常兆候の検出 | 設備の故障やトラブルの発生 |
メリット | ・設備の寿命延長 ・予期しない故障の防止 ・コスト削減 | ・効率的なメンテナンス ・ダウンタイムの最小化 ・ムダな保守の削減 | ・初期投資が少ない ・即時対応可能 |
デメリット | ・過剰なメンテナンスによる非効率的な保全の発生 | ・高度な技術が必要 ・初期投資が必要 ・データ収集と分析が求められる | ・設備のダウンタイム発生 ・修理費用がかさみやすい ・事後の対応が遅れる |
予防保全はなぜ重要?メリット・デメリット
予防保全のメリット
予防保全のメリットとして、主に以下の4点が挙げられます。
品質の維持
設備が不調な状態では製品の品質に不具合が生じる可能性があるため、予防保全は品質維持に不可欠です。予防保全は定期的なメンテナンスを行い、計画的に設備を整えることで品質の安定を図ります。
例えば、機械部品が摩耗していると製品の精度に悪影響を及ぼす恐れがありますが、事後保全では故障後の対応となり、製品品質に影響を及ぼすリスクが高まります。
予防保全は、故障が発生する前にこれらの問題を特定し早期に対策を講じることができるため、品質を維持するために有効です。
生産性の向上
予防保全が生産性の向上に寄与する理由は、設備の稼働時間を最大化し、突発的な故障や不具合を事前に防ぐことで安定した生産環境を確保できるからです。計画的なメンテナンスを通じて設備の故障を予測し、問題が大きくなる前に対処することが可能になります。これにより、設備の稼働率が高まり、効率的な生産が実現します。
一方、事後保全は設備が故障した後に対応するため、予期しないダウンタイムや修理作業が発生し、その間は生産が停止します。このダウンタイムは、製品の生産計画や納期に影響を及ぼす可能性があり、結果として生産性が低下します。
設備の延命化
予防保全による定期的なメンテナンスは、故障を未然に防ぐことで設備全体の寿命を延ばす効果があります。例えば、特定の摩耗部品を早期に交換することで他の部品や設備全体への負荷を軽減し、長期間の使用が可能となります。
一方、事後保全では故障が発生した後に修理を行うため、設備が故障するまでその状態を見守ることになります。この場合、予期しないダウンタイムや部品交換が発生し、設備の状態が劣化する可能性があります。設備の故障やトラブルが大きくなる前に対処できないため寿命が短くなり、全体的な設備投資の効率も低下するリスクがあります。
保全計画が立てやすい
予防保全は定期的に行われるため、保全作業のスケジュールを事前に計画することが可能です。予防保全では、設備の使用状況や過去の故障履歴に基づいて、あらかじめメンテナンスのスケジュールや対象となる作業を設定することができます。このため、必要な点検や部品交換を事前に見積もり、定期的に実施するためのリソース(人員、予算、時間)を効率的に割り当てることが可能になります。
事後保全では設備が故障した後に修理計画を立てるため、いつ何を修理するかが予測できず、突発的なダウンタイムや設備の空き時間に対応するための計画が立てにくいといえます。予知保全の場合、リアルタイムで異常を検出して即時対応するためあらかじめ保全計画を立てることが難しく、柔軟性はあるものの計画性は弱くなります。
予防保全のデメリット
予防保全のデメリットとして、以下の3点が挙げられます。
上記のようなデメリットは現場の効率や生産性に強く影響します。こうした課題を避ける方法については、「生産性低下を解消する設備保全のDX」というPDF資料で詳しくご紹介しています。以下のリンクよりご覧ください。
>>>予防保全 / 予知保全の効果を得にくい現場に必要な対策について学ぶ(無料)
コストがかさみやすい
予防保全では設備が正常に稼働している場合でもメンテナンスを実施するため、部品交換費や作業コストが増える可能性があります。例えば、使用可能な部品を早めに交換する場合、その分のコストが余計にかかることがあります。また、定期的な点検やメンテナンスが必要なため、作業員や専門技術者の時間も確保しなければなりません。
その一方で、予防保全は長期的な視点で見ると突発的な故障による大規模な修理や交換を未然に防ぐ効果があるため、結果的に大きなコスト削減につながる場合があります。また、予防保全によって設備の稼働率や生産性が安定し、突発的な生産停止が減少することで、長期的には安定した収益を確保することが可能になります。
突発的なトラブルへの対応が難しい
予防保全は定期点検を中心に計画されているため、突発的な故障や異常の発生には対応が難しい場合があります。対して、予知保全はセンサーやデータ分析を活用し、リアルタイムで異常を検知するため、突発的なトラブルの対応力で優位性があります。
保全工数が負担になりやすい
定期的なメンテナンス実施のため、点検や保守作業にかかる工数が増加するケースが考えられます。特に、紙の点検表を使った保全活動は記録の作成や整理に時間がかかるだけでなく、手書きによる記入ミスや抜け漏れが発生することで修正や確認の手間が増え、点検作業そのものが非効率になりがちです。
さらに、点検結果を関係者と共有する際は紙の帳票を回覧したり、データ入力を行ったりする必要があり、情報伝達の遅れにつながることもあります。
その結果、迅速な対応が求められる故障予兆の見逃しや、適切なメンテナンス時期の判断が遅れるリスクが高まります。また、過去の点検履歴を参照する際にも、膨大な紙のファイルから必要な情報を探す手間が発生し、分析や改善活動に割ける時間が減少してしまいます。
こうした作業負担の蓄積により、現場の保全担当者の負担が増大し、本来の設備維持や改善業務に十分なリソースを割くことが難しくなる可能性があります。
こうした課題を解決する手段として、「帳票のデジタル化」が注目されています。『デジタル帳票』の概要やメリットは後述しますので、是非ご覧ください。
予防保全の効果的な進め方や方法
予防保全の具体的な進め方について、以下の4ステップにそって解説します。
保全の優先順位を設定する
まず、すべての設備について点検結果などをもとに重要度や故障リスクを分析し、優先順位をつけることが重要です。文部科学省によると、「リスク=異常事象の発生確率×異常事象が引き起こす被害」と定義されています。
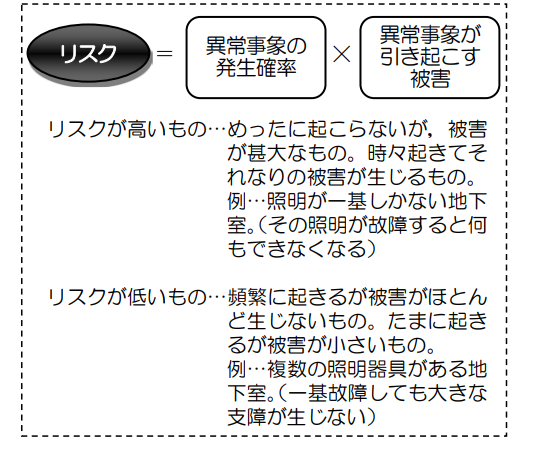
引用元:文部科学省「学校施設の長寿命化改修の手引」
リスクを基準に優先順位を明確化することで限られたリソースを効率的に配分でき、重要設備への集中投資が可能になります。設備の重要性や稼働状況に応じて、
重点的に保全を行うべき設備を特定する方法には、以下の2つが考えられます。
- FMEA(故障モード影響解析): 各設備がどのような故障を起こし、その影響がどれくらい重大であるかを評価し、リスクの高い部分を特定します。
- 設備重要度分析: 生産における影響度が大きい設備に優先的にリソースを割り当てます。例として、以下のような表を作るとわかりやすいです。
▼設備重要度分析の例▼
区分 | 定義 |
---|---|
Ⅰ:健全 | 機能に支障が生じておらず、生産性に影響を与えていない状態 |
Ⅱ:予防保全段階 | 機能に支障が生じていないが、予防保全の観点から措置を講ずることが望ましい状態 |
Ⅲ:早期措置段階 | 機能に支障が生じる可能性があり、早期に措置を講ずべき状態 |
Ⅳ:緊急措置段階 | 能に支障が生じている、又は生じる可能性が著しく高く、緊急に措置を講ずべき状態 |
ここまでリスクについて解説してきましたが、リスクに潜む危険性を調査して低減/除去するまでの一連の手法を「リスクアセスメント」と呼びます。具体的な進め方は以下の動画で解説しておりますので、是非ご覧ください。
>>>トラブルを発生させないリスクアセスメントの進め方は?(視聴無料)
保全計画を策定する
次に、設備の状態や使用条件に基づいて、定期的な点検や保守作業のスケジュールを立てます。保全計画は、以下のような観点を考慮して作成します。
- メーカー推奨のメンテナンス周期: 設備のマニュアルに基づいて、適切なタイミングでメンテナンスを実施します。
- 使用頻度や稼働時間に応じた点検: 設備の運転時間や稼働状況に合わせて、メンテナンススケジュールを調整します。例えば、長時間稼働している設備には頻繁に点検を行います。
点検項目と作業手順を明確にする
予防保全を実施する前段階として、定期的な点検項目や作業手順を標準化し、作業員に明確に伝えることが必要です。これには、以下の要素を含めることが重要です。
- 点検項目のリスト: 設備ごとに点検するべき部分(部品の摩耗、オイルレベル、温度管理など)を明確にします。
- 作業手順書の作成: 点検作業や交換作業の手順書を作成し、スタッフが適切に作業を進められるようにします。
このとき、「誰がどの設備保全を行えるのか」という点も明らかにすることで、より抜け漏れのない保全活動が期待できます。そのためには、スキルマップを作成し従業員のスキルを可視化すると良いでしょう。
設備保全のスキルマップを作成する方法やすぐに使えるテンプレートについては、以下の記事で詳しくご紹介しています。
関連記事:【無料DL可能】設備保全スキルマップの作り方や活用方法は?
効果の評価と改善を行う
予防保全を実際に行った後は、予防保全がどれだけ効果を上げているかを評価し、改善点を洗い出すことが大切です。効果的な予防保全が行われていれば、設備の稼働率や生産効率が向上し、ダウンタイムの削減が実現します。定期的に保全活動を振り返り、必要に応じて改善策を講じることが求められます。
ここまで、予防保全の具体的な進め方について解説しました。一方で、「予防保全は一応進めたが、中々効果が出ない…」とお悩みの方も多いのではないでしょうか?
次章では、予防保全の成功を妨げる要因や課題について記載します。
意味がない?予防保全の失敗要因や課題
予防保全は効果的に機能することで設備の安定稼働を支える重要な活動ですが、適切に運用されなければその効果を発揮できず、無駄なコストや時間が発生することもあります。その失敗要因や課題として以下が挙げられます。
属人化により対応メンバーが限られている
予防保全の活動が特定の作業員や技術者の経験や知識に依存している場合、属人化が進み、対応できるメンバーが限られることがあります。この結果、設備トラブル時の対応が遅れるだけでなく、保全の質にばらつきが生じるリスクも高まります。
属人化が進む理由として、技術やノウハウの共有不足、保全業務の記録や手順書の未整備が挙げられます。対応メンバーが限られると突発的なトラブルや多発する問題に迅速に対応できず、ダウンタイムが長期化するリスクが高まります。
現場改善ラボでは、「自社の設備保全も属人化しているのでは…?」とお悩みの方に向け、設備保全コンサルタントによる「属人化を解消する3つの秘訣」という講演動画をご用意しております。
属人化のチェックシートや作業分析・改善のポイントについてわかりやすくまとめましたので、是非ご参加ください。
保全の方法やコツがマニュアル化されていない
保全業務がマニュアル化されていない場合、作業手順が統一されず対応のばらつきや作業ミスが発生する可能性があります。例えば、経験豊富な技術者が保全業務のノウハウを口頭で共有しているだけでは、他の作業員が同じ品質の対応をすることは難しいでしょう。
その結果、重要な点検項目が見落とされたり、作業ミスが発生するリスクが増加します。これを防ぐには、保全の具体的な手順や作業標準を明文化し、全員が理解できる形でマニュアル化することが重要です。
特に、マニュアルは動画化がおすすめです。文章や図だけでは伝わりにくい細かい作業のコツや注意点も、映像であれば一目で理解できるため、習熟度に差がある作業者でも統一した手順で作業を進められます。高品質な動画マニュアルが簡単に作成できるツールについては、後述する『教育には「tebiki現場教育」』にて詳しくご紹介します。
保全の記録を活用できていない
保全業務の記録を適切に活用していない場合、同じ問題が繰り返される可能性があります。例えば、過去に特定設備で頻発していた故障の原因やその対策が記録されていない場合、新たなトラブルの際にゼロから原因を特定する必要が生じます。
保全記録には設備の劣化傾向や問題の発生頻度など、多くの貴重なデータが含まれています。このデータを蓄積し分析することで、将来的なトラブルの予測や保全計画を最適化することが可能です。
一方で、紙帳票による記録では情報の検索や共有が難しく、蓄積したデータを活用しきれないケースがあります。
紙の記録は保管スペースを必要とし、過去の記録を振り返る際にも多くの時間を要するため、迅速な意思決定や対応が妨げられることがあります。さらに、記録の記入漏れや内容の不明瞭さによって、データとしての信頼性が損なわれるリスクもあります。
こうした課題を解決するには、帳票をデジタル化し、記録を一元管理する仕組みを導入することが有効です。デジタル帳票を導入する流れや費用対効果について知りたい方は、以下のPDF資料をご参照ください。
>>>「はじめての現場帳票デジタル化ガイド」でデジタル帳票について学ぶ(無料)
予防保全の効果を最大化する2つのツール
先述した課題の解決には、「保全業務の標準化」と「記録/帳票のデジタル化」が必要です。この2つを叶えるツールとして、以下の2つをご紹介します。
- 動画マニュアル
- デジタル帳票
動画マニュアル
予防保全の効果を最大化するには、作業手順を統一し、誰が作業を行っても同じ結果が得られるようにする=保全業務の標準化を進める必要があります。この点で、動画マニュアルは非常に効果的なツールです。
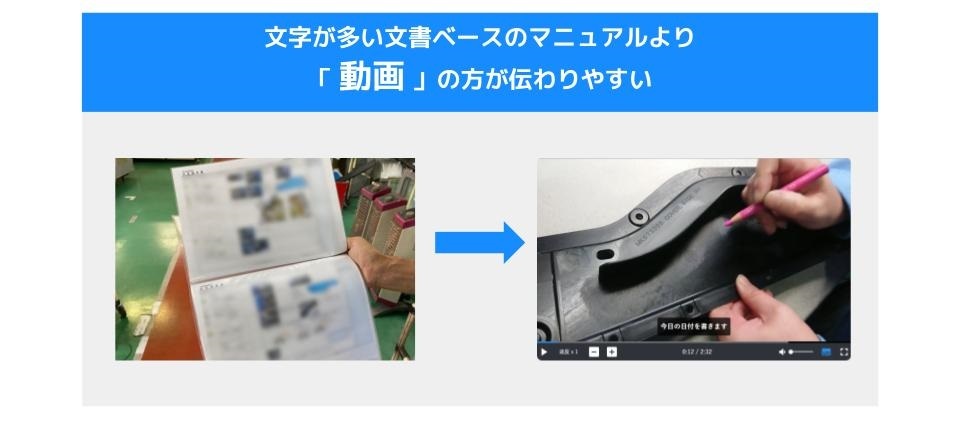
動画による説明は視覚的に情報を伝えるため、文字だけの手順書に比べて理解しやすく、記憶に残りやすい特徴があります。また、動画という同一の教材を使って教育することで、指導者ごとの教育のばらつきが生じず、OJTなどで教える負担がないことも大きなメリットです。
例えば、特定の設備の分解手順を動画化しておけば、初めてその作業を行うスタッフでも正確かつ効率的に作業を進めることが可能です。同様に、緊急対応時に動画を参照すれば必要な手順を素早く確認でき、作業ミスの防止や対応時間の短縮が期待できます。
これにより、保全業務の属人化を防ぎ、現場全体の保全スキルを底上げする効果が期待できます。マニュアルの動画化は、保全業務の属人化を防ぎ、作業の効率と品質を同時に向上させるための有力な手段といえるでしょう。
動画マニュアルの教育効果や現場で活用している事例については、以下のPDF資料で詳細に解説しています。
>>>製造業で動画マニュアルを活用するメリットや事例について知る(無料)
デジタル帳票
予防保全では設備や部品の点検結果、トラブルや作業の履歴といったデータを正確に記録し、それを活用することが重要です。デジタル帳票は、これらの情報をリアルタイムで記録・管理できるツールとして非常に有用です。
従来の紙帳票では情報が分散し、記録や検索に手間がかかるため、必要なデータを迅速に活用することが難しいという課題がありました。対して、帳票をデジタル化することで情報を一元管理し、保全記録やトラブル履歴を簡単に検索できる環境を構築できます。
例えば、保全記録をデジタル帳票で管理すれば、現場で過去のデータをすぐに確認でき、設備の状態をリアルタイムで把握することが可能になります。結果として、リスクの高い設備や劣化が進んでいる部品の特定が容易になり、適切なタイミングでのメンテナンスが実現します。
さらに、帳票のデジタル化は現場作業者の負担軽減も実現します。手書きでは避けられない記録ミスや入力漏れを削減できるだけでなく、スマートフォンなどを活用した入力の自動化も可能です。
デジタル帳票を導入する流れや費用対効果について知りたい方は、以下のPDF資料をご参照ください。
>>>「はじめての現場帳票デジタル化ガイド」でデジタル帳票について学ぶ(無料)
次章からは、特におすすめな動画マニュアル・デジタル帳票についてご紹介します。
2つの「tebiki」で効果のある予防保全を!
予防保全の効果を最大化させるのに役立つ2つの「tebiki」というツールをご紹介します。「tebiki」は、現場改善をサポートし、設備のトラブルを未然に防ぐ体制を整備するための強力な手段となります。
それでは、システムの機能内容を詳しく見ていきましょう。
教育には「tebiki現場教育」
tebiki現場教育は、動画編集未経験者でもかんたんに動画マニュアルが作成できるツールです。スキルマップなどを用いた、従業員の教育管理も行えます。
▼tebiki現場教育 紹介動画▼
「現場の動き」を視覚的に分かりやすく伝え、製造現場の業務標準化が可能です。tebiki現場教育には、主に「動画を簡単に作成できる機能」と「教育管理ができる機能」があります。
- 音声認識による自動字幕生成
- 100カ国語以上への自動翻訳
- 字幕の読み上げ(多言語にも対応)
- アクセス履歴等がわかるレポート機能
- オリジナルのテストを作成できるテスト機能
- 従業員のスキルを評価・可視化できる機能 など
実際に導入いただいている企業からは、「tebikiは単なる動画作成ソフトではなく“社員教育ツール”」という声もいただくほど現場教育に特化したツールです。そのため、保全作業を標準化させる教育体制の整備が可能になるでしょう。
tebiki現場教育には、まだまだ現場教育に便利な機能が搭載されています。より詳細な情報や料金プランについては、以下のサービス紹介資料からぜひご確認ください。
記録には「tebiki現場分析」
tebiki現場分析は、紙やExcelで運用されている製造日報などの現場帳票をデジタル化し、内容の記録/承認/集計/分析を効率的に行えるツールです。
帳票の雛形作成が簡単で、現場の作業者はストレスなく記録できます。さらに日々の記録をデジタル化することで異常を即座に検知し、管理者は素早い対策指示が可能になります。tebiki現場分析でできる主なことは、以下の通りです。
- クラウド上に誰でも簡単に帳票を作成・管理できる
- 正常値を設定することで、異常値アラートを出せる
- 記録した数値を自動でグラフ化できる
- 画像をアップロードして、そのまま記録できる など
実際に導入いただいている企業では、温度データをリアルタイムで確認できたことでわずかな温度低下を発見し、現場で詳細な点検を行ったところ、配管の小さな穴を発見しています。
この早期発見により、大規模な故障や生産ラインの停止といった深刻な事態を未然に防ぐことができました。「もし従来の紙ベースの記録管理だったら、このような微細な変化を見逃してしまい、問題が大きくなってから気づいたかもしれません。」と、tebiki現場分析導入の効果を実感されています。
今回ご紹介していない具体的な機能のご紹介、プランなどの情報は以下の画像をクリックして概要資料をご確認ください。
tebikiで未然防止につながる予防保全を行おう
本記事では、予防保全の重要性とその具体的な取り組みについて解説しました。予防保全は、機械や設備の故障を未然に防ぎ、生産性向上やコスト削減に寄与する重要な手法です。
その中で、作業手順の標準化や効率的な保全計画の実施がポイントとなります。さらに、デジタルツールの活用が、情報の可視化や従業員のスキル向上を助け、予防保全をより効果的にすることが説明されています。
本記事でご紹介した2つのツール「tebiki現場教育」と「tebiki現場分析」を活用することで、作業手順の標準化と効率的な保全計画を実現するための大きな一歩を踏み出すことができます。これらのツールを組み合わせることで、予防保全の実施はさらに効果を発揮し、従業員の作業効率や安全性が向上します。
tebiki現場教育とtebiki現場分析の詳細や導入事例、導入のメリットについては以下のリンクから詳しい資料を入手してご覧ください。
>>>予防保全の効果を最大化させる「tebiki」のツールの詳細を見てみる
【おまけ】その他の保全
最後に、その他の保全として以下の4つを解説します。
- 保全予防
- 定期保全
- 計画保全
- 予兆保全
保全予防
保全予防とは、設備や機械の故障やトラブルを発生させないための活動です。保全性の高い設備になるよう設計段階から作りこむことや、使用条件や運転環境をあらかじめ最適化することで「保全を発生させない」取り組みが該当します。
そのため、「決められた時期に決められた内容の保全活動を行う」予防保全とは、実施するタイミングが異なります。
機械や設備の故障は生産ラインの停止を引き起こし、製造業にとっては大きな損失となりますが、保全予防により故障しにくい機械の設置を行えば、故障自体を少なくすることも可能です。
例えば、コンベヤーベルトの軸受けなどの動作部位には潤滑油が必要となりますが、自動給油装置を付けることで設備保全を必要としない設備としたり、部品の取り替えが簡単な設備を導入するといった対策が挙げられます。
定期保全
定期保全とは、機械や設備の故障を防ぐために、定められた期間や運転時間ごとに行われる保全活動のことです。時間基準保全(TBM)とほぼ同意義と捉えても良いでしょう。
例えば、自動車のエンジンオイル交換は定期保全の一例だといえます。オイルが劣化するとエンジンの潤滑が悪くなり故障につながる可能性があるため、一定の走行距離ごとに交換する必要があります。
計画保全
計画保全とは、設備の故障を未然に防ぐため、計画的に保全体制を整備する保全活動のことです。
計画保全の目的は、故障をなくす体制づくりにあります。具体的には、設備の利用可能性を高めるために平均故障間隔の延長と平均修復時間の短縮を行います。結果として、生産性の向上が期待できます。
予兆保全
予兆保全は、予知保全と同じ意味と考えてよい言葉です。予兆保全は、機械や設備のモニタリングや分析を行い故障を予防するための手法で、設備が故障する前に異常を検知・予測し、適切なメンテナンスを行うことを目指します。
そのため、予兆保全(予知保全)の導入で機械の故障を未然に防ぎ、生産効率を向上させることが可能となります。