かんたん動画マニュアル作成ツール「tebiki」と、かんたんデジタル現場帳票「tebiki現場分析」を展開する現場改善ラボ編集部です。
本記事ではフェイルセーフの概念やフールプルーフとの違いを紹介するだけでなく、業界別フェイルセーフの設計事例やフェイルセーフを根付かせるための実践的な方法2つについても解説します。
フェイルセーフを浸透させたい製造業の現場責任者には特に重要な情報をまとめているので、現場改善のヒントにお役立てください。
目次
フェイルセーフとは?フールプルーフとの違いについても解説
フェイルセーフとは?
フェイルセーフとは、機器やシステムに異常が発生した際、被害を最小限に抑え、安全を確保するために作動する仕組みのことです。製造業の現場では、機械の故障や人的ミスは、重大な事故や生産ラインの停止・労働災害に直結します。フェイルセーフはそのようなリスクを軽減し、安全な作業環境を実現するための「最後の砦」と言えるでしょう。
例を挙げると、フェイルセーフは以下のような動作を行うことで安全を確保しています。
■異常を検知し、システムを安全な状態に移行させる
例えば、機械の異常な振動を検知したら、自動的に運転を停止させる。
■異常が発生した部分を切り離し、影響範囲を限定する
例えば、電気系統のショートを検知したら、該当回路のみを遮断し、他のシステムへの影響を防ぐ。
■代替手段に切り替えて、機能を維持する
例えば、メインの制御システムがダウンしたら、バックアップシステムに自動的に切り替える。
これらは、現場でよく目にする「非常停止ボタン」や「安全装置」といった身近な例にも表れています。作業者が危険を察知した際に即座に機械を停止させたり、危険な状態を未然に防いだりする、フェイルセーフの典型的な例です。
製造業の現場におけるフェイルセーフの考え方は、単なる「安全装置」の設置にとどまりません。 機器の設計段階から、異常発生時の挙動を想定し、被害を最小限に抑えるための対策を組み込むことが重要です。これは「本質安全」という考え方にもつながります。
つまり、故障や誤操作が起こりにくい設計、そして万が一発生しても、それが重大な事故につながらないような設計を心がけることがフェイルセーフであり、製造現場における安全対策の基本なのです。
補足ですが、製造現場の安全対策には「動画マニュアルによる教育」 が非常に有効です。複雑な作業も、動画なら一目で理解でき、ヒューマンエラーを抑制できます。また、教育内容を標準化できるため、指導者による教育品質のばらつきも解消されます。
安全意識が高い製造現場では、すでに動画マニュアルが活用されています。 導入事例や効果については、以下のPDF資料「安全意識が高い製造現場はやっている! 動画マニュアルを活用した安全教育・対策事例」をご覧ください。
フールプルーフとの違い
「フェイルセーフ」とよく混同される概念に「フールプルーフ」があります。どちらも安全性を高めるための仕組みですが、その目的とアプローチは異なります。ここでは、製造業の現場における具体例を交えながら、両者の違いを明確に解説します。
フールプルーフとは、人間の誤操作や誤使用を防止する設計や仕組みのことです。 例えば以下のような例が挙げられます。
- 機械の危険な部分に手が入らないように、安全カバーを設置する。
- 操作手順を間違えないように、手順書を分かりやすく図解する。
- 電気プラグの形状を工夫して、誤ったコンセントに差し込めないようにする。
これらは「そもそもミスが起こらないようにする」ための対策です。言わば、「予防安全」の考え方に基づいています。
一方、フェイルセーフは、異常が発生した際に、被害を最小限に抑えるための仕組みです。 つまり「ミスや故障が起こることを前提として、その影響を最小限に抑える」という考え方です。
▼フェイルセーフとフールプルーフとの違い▼
フェイルセーフ | フールプルーフ | |
---|---|---|
目的 | 異常発生時の被害最小化 | 誤操作・誤使用の防止 |
アプローチ | ミスや故障が起こることを前提に対策する | そもそもミスが起こらないようにする |
具体例 | 非常停止ボタン、自動ブレーキシステム、冗長化システム | 安全カバー、手順書の図解、プラグ形状の工夫 |
製造現場での例 | 異常温度検知時の自動シャットダウン、バックアップ電源の確保 | 作業エリアへの立ち入り制限、インターロック機構 |
製造業の現場では、フールプルーフとフェイルセーフを組み合わせて、多層的な安全対策を講じることが重要です。 フールプルーフで人的ミスを減らし、フェイルセーフで機械的な故障や予期せぬ事態に備える。この両輪によって、より安全な作業環境を実現できるのです。
フェイルセーフの重要性
フェイルセーフは、単なる安全対策の一つではなく、現代の製造業において不可欠な要素となっています。その重要性は、社会的背景、技術的要因、そしてマーケティング戦略という3つの側面から説明できます。
社会的背景
フェイルセーフが重要とされる1つとして「社会的背景」が挙げられます。社会的背景を掘り下げると、以下3つが挙げられます。
- 安全性への意識の高まり
- リスクアセスメントの法制化
- 企業の社会的責任(CSR)
安全性への意識の高まり
近年、製品の安全性に対する消費者の意識は著しく高まっています。製品の欠陥による事故や健康被害は、企業の信頼を大きく損なうだけでなく、訴訟や損害賠償請求といった深刻な問題に発展する可能性があります。また、労働者の安全に対する意識も向上しており、企業は従業員に対して安全な労働環境を提供する責任があります。労働災害は、生産性の低下や人材の損失を招くだけでなく、企業の社会的評価にも悪影響を及ぼします。
さらに、製造現場における事故の多くは「ヒューマンエラー」に起因していることが指摘されています。どんなに優れた設備や安全装置を導入しても、それらを扱う人間の不注意や誤操作があれば、事故を防ぐことはできません。そのため、従業員一人ひとりの安全意識を高め、ヒューマンエラーを減らすための教育・訓練が非常に重要になっています。
ヒューマンエラーの具体的な対策方法は、以下のリンクからPDF資料をダウンロードしてご覧ください。
>>>PDF資料「製造業におけるヒューマンエラーの未然防止と具体的な対策方法」を見てみる
また、安全意識が高い現場では紙の作業手順書から脱却し、動画マニュアルを活用した教育を積極的に導入しています。 動画マニュアルは、実際の作業手順を視覚的に示すことができるため、理解度や記憶の定着率が高く、ヒューマンエラーの防止に効果的です。また、外国人労働者など、日本語の理解が難しい従業員に対しても、動画であれば直感的に理解しやすく、教育の質を均一化できるというメリットもあります。
動画マニュアルによる安全性向上を実現している製造業事例について理解を深めたい方は、以下の画像をクリックしてPDF資料「安全意識が高い製造現場はやっている! 動画マニュアルを活用した安全教育・対策事例」もあわせてご覧ください。
リスクアセスメントの法制化
多くの国や地域で、リスクアセスメントの実施が法的に義務付けられるようになってきました。リスクアセスメントとは、作業に伴う危険要因を特定し、そのリスクの大きさを見積もり、対策を講じる一連の手法です。
製造業においては、機械設備の設計・運用、作業手順の策定など、あらゆる場面でリスクアセスメントが求められます。フェイルセーフは、リスクアセスメントで特定されたリスクを低減するための有効な手段として、その重要性が増しています。
企業の社会的責任(CSR)
企業の社会的責任(CSR)が重視される現代において、安全配慮義務は企業が果たすべき重要な責任の一つとされています。
企業は、自社の事業活動が、従業員、顧客、地域社会などに危害を及ぼさないよう、最大限の努力を払う必要があります。フェイルセーフの導入は、この安全配慮義務を具体的に実践する上で、欠かせない取り組みと言えるでしょう。
技術的要因
フェイルセーフが重要とされる要素には「技術的要因」も挙げられます。具体的には以下のような要因です。
- 制御システムの複雑化
- 技術の進展に伴う安全課題
制御システムの複雑化
近年の製造業では、生産効率の向上や多品種少量生産への対応などを目的として、システムの自動化・複雑化が進んでいます。しかしその一方で、制御システムが高度化するほど、潜在的なリスクも増大します。高度化した制御システムに対し、安全対策もそれ相応の技術が求められるようになるからです。
つまりシステムの複雑化は、製造現場における新たな安全課題を生み出していると言えます。
技術の進展に伴う安全課題
技術の進展も、フェイルセーフを後押しする要素になっています。例えば、製造業における大きな潮流として、自動化やIoT化の進展が挙げられます。これらの技術は工場全体の生産性に寄与する一方で、新たな安全課題が生まれる要因にもなるのです。
例えば、人と同じ空間で作業を行う「ロボット」は、人間の作業効率を改善しつつも、「接触事故」のリスクも潜んでいます。それだけでなく、デバイスに記録されたデータに欠損や誤りがあった場合、予期せぬ誤作動を起こしかねず、何かしらの労働災害につながる危険性もあります。
労働災害による死傷者数は製造業が特に多く、安全性には十分に配慮しなければなりません。補足として、製造業における労働災害の発生件数が多い事例を以下の記事にまとめました。あわせてご覧ください。
関連記事:【労働災害ランキング】製造業の安全対策や死亡事故事例も
マーケティング戦略
マーケティング戦略も、フェイルセーフの必要性を高める要因です。以下のような要因が挙げられます。
- 安全・安心ブランドの確立
- 安全認証の取得と顧客への信頼醸成
安全・安心ブランドの確立
製造業において、「安全性」は製品の重要な付加価値となります。フェイルセーフ機能を備えた製品は付加価値に応えるものであり、「安全・安心」というブランドイメージを確立する上で強力な武器になると言えるでしょう。
例えば、この「安全性」を前面に押し出し、安心・安全ブランドを訴求するためのプロモーションはマーケティング戦略のひとつです。「安全」をテーマにした特設ウェブサイトを開設し、自社の安全技術や取り組みを詳しく紹介することで、顧客からの信頼を獲得する、というようなブランディングも例として挙げられるでしょう。
このように、フェイルセーフをはじめとする安全技術は、単なる機能の1つではなく、製品の差別化を図り、市場競争を勝ち抜くための重要な要素となっているのです。
安全認証の取得と顧客への信頼醸成
製品の安全性を客観的に証明する手段として、安全認証の取得も有効です。例えば、国際的な安全規格であるISOやIEC規格、各国の法規制に基づく認証など、様々な安全認証が存在します。これらの認証を取得することで、製品の安全性が一定の基準を満たしていることを示すことができ、顧客の信頼獲得につながります。
さらに企業によっては、製品の安全性だけでなく、労働者の安全と健康を確保するための「安全衛生マネジメントシステム(OSHMS)」を構築・運用している場合があります。代表的な規格としてはISO 45001などがあります。このシステムは、組織が労働安全衛生リスクを管理し、安全な労働環境を構築するための枠組みを提供します。安全衛生マネジメントシステムの導入は、製品の安全性向上に間接的に寄与するだけでなく、企業の社会的責任(CSR)を果たす上でも重要な取り組みとなります。
フェイルセーフ設計に用いられる手法
フェイルセーフ設計を実現するためには、製品やシステムの潜在的なリスクを洗い出し、適切な対策を講じる必要があります。そのための代表的な手法として、以下の2つがあげられます。
- FMEA(故障モード影響解析)
- FTA(故障の木解析)
FMEA(故障モード影響解析)
FMEA (Failure Mode and Effects Analysis) は、製品やシステムを構成する部品やプロセスに、どのような失敗モード(故障や不具合の形態)が起こりうるかを分析し、その影響の大きさを評価する手法です。製造業では、製品の設計段階や製造プロセスの検討段階で広く用いられています。
ここで言う「失敗モード」とは、単なる機械的な「故障」だけでなく、設計ミス、製造ミス、人的エラーなど、様々な要因によって引き起こされる「意図しない状態」や「期待される機能を果たさない状態」を広く含みます。 これは、フェイルセーフが「故障」だけでなく、より広い範囲の「失敗」に対して安全を確保する考え方に基づいているためです。
FMEAは、一般的に以下の手順で実施されます。
手順 | 概要 | 詳細 |
---|---|---|
1 | 対象の明確化 | 分析の対象となる製品やプロセス、範囲を明確にします。 |
2 | チーム編成 | 設計、製造、品質保証など、関連する部門からメンバーを集め、チームを編成します。 |
3 | 失敗モードの洗い出し | 対象となる部品やプロセスについて、想定される失敗モードをすべて洗い出します。 |
4 | 影響(リスク)の評価 | 各失敗モードが製品やシステムにどのような影響を与えるかを評価します。影響の大きさはS・O・D=「厳しさ(Severity)」、「発生頻度(Occurrence)」、「検出度(Detection)」などの指標で評価されます。 |
5 | リスク優先度(RPN)の算出 | 手順4で評価した影響(S・O・D)の指標を掛け合わせ、リスク優先度(RPN:Risk Priority Number)を算出します。RPNは、各失敗モードのリスクの大きさを相対的に表す数値です。 |
6 | 対策の検討 | RPNが高い失敗モードから優先的に、対策を検討します。対策としては、設計変更、製造プロセスの改善、検査の強化などが挙げられます。 |
7 | 対策の実施と有効性の確認 | 検討した対策を実施し、その効果を確認します。 |
製造現場におけるFMEAの活用例としては、自動車のブレーキシステムの設計が挙げられます。 ブレーキパッドの摩耗、ブレーキフルードの漏れ、ブレーキキャリパーの固着、さらにはブレーキペダルの踏み間違いなどの人的エラーまで、様々な失敗モードを想定し、それぞれが車両の安全性にどのような影響を与えるかを評価します。
そして、RPNが高い失敗モードに対しては、より耐久性の高い部品を採用する、冗長設計を導入する、定期的な点検項目に追加する、警告システムを導入するなどの対策を講じます。これらの対策が、フェイルセーフ設計の考え方に基づき、ブレーキシステムの安全性を高めています。
このように、FMEAは、製品やプロセスの設計段階で潜在的なリスクを特定し、対策を講じることで、フェイルセーフ設計を実現するための有効なツールとして活用されています。
関連記事:FMEA(故障モード影響解析)とは?品質向上の取組みをわかりやすく解説【フォーマット例付き】
FTA(故障の木解析)
FTA (Fault Tree Analysis) は、システムに発生する可能性のある重大な事故や故障をトップダウンで分析し、その原因となる事象の組み合わせを特定する手法です。分かりやすく解説すると、「最悪の事態」を最初に想定し、その原因を段階的に掘り下げていくようなイメージです。
- 飛行機が墜落する
- 自動車が意図せず急加速する
- 化学プラントで爆発が起こる
最悪の事態とは上記のような例が挙げられます。これらがトップ事象となり、トップ事象に起因する事象を下図のフォルトルリー(故障の木)のように段階的に洗い出していきます。
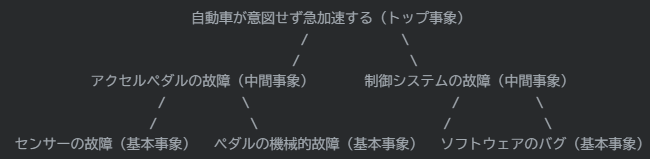
FTAは、一般的に以下の手順で実施されます。
手順 | 概要 | 詳細 |
---|---|---|
1 | トップ事象の定義 | 分析の対象となる重大な事故や故障(例:航空機の墜落、原子炉のメルトダウン)を定義します。 |
2 | 故障の木の作成 | トップ事象を頂点とし、その原因となる事象を階層的に展開して、故障の木(フォルトツリー)を作成します。事象間の関係は、論理記号(ANDゲート、ORゲートなど)で表されます。 |
3 | 基本事象の特定 | 故障の木の最下層に、それ以上展開できない基本的な事象(例:部品の故障、人的ミス)を特定します。 |
4 | 発生確率の評価 | 各基本事象の発生確率を評価します。 |
5 | 解析 | 故障の木を解析し、トップ事象の発生確率を算出したり、トップ事象の発生に最も影響を与える基本事象(クリティカルパス)を特定したりします。 |
6 | 対策の検討 | 解析結果に基づき、トップ事象の発生確率を下げるための対策を検討します。対策としては、信頼性の高い部品の採用、冗長設計の導入、フェイルセーフ機能の追加などが挙げられます。 |
FMEAとFTAは、どちらもリスクを分析し、対策を検討するための有効な手法ですが、FMEAはボトムアップ的なアプローチに対し、FTAはトップダウン的なアプローチという違いがあります。製造業では、製品やシステムの特性、分析の目的に応じて、これらの手法を使い分けたり、組み合わせたりして活用されています。
【業界別】フェイルセーフの設計事例
この章では、様々な業界におけるフェイルセーフの具体的な設計事例を紹介します。各業界の事例を通して、フェイルセーフがどのように適用され、安全性の確保に貢献しているのかを解説します。
製造業:化学プラントの緊急遮断システム
化学プラントでは、化学反応の異常などにより、爆発や有害物質の漏洩などの重大事故が発生する危険性があります。これらの事故を未然に防ぐため、緊急遮断システム(ESD)が導入されています。
ESDは、プラント内の温度、圧力、流量などのプロセス値を常に監視し、異常を検知すると、直ちにバルブを閉止するなどして、プラントを安全な状態に停止させます。こうしたフェイルセーフの設計により、現場従業員の命を守っています。
自動車:ブレーキシステム
自動車業界では、人命に直結するブレーキシステムに、古くからフェイルセーフの考え方が導入されています。
油圧式ブレーキでは、ペダルに加えられた力を油圧で各車輪のブレーキ装置に伝えますが、配管の破損などで油圧が失われると、制動力が著しく低下します。このリスクを回避するため、油圧系統を前輪と後輪、あるいは対角輪で2系統に独立させ、冗長化を図っています。これにより、一方の系統が故障しても、もう一方の系統で制動力を確保できます。
自動車のブレーキシステムは、フェイルセーフ設計の重要性を示す代表的な事例と言えるでしょう。
航空機:飛行制御システム
航空機では、飛行制御システムに多重化や系統独立などのフェイルセーフ設計が施されています。
例えば、操縦翼面を動かす油圧系統は、複数の独立した系統で構成されています。1つの系統が故障しても、残りの系統で操縦を維持することが可能です。また、飛行制御コンピュータも複数搭載され、互いに監視しあうことで、1つに異常が発生しても、即座に正常な系統へ切り替わり、安全な飛行を維持します。
鉄道:自動列車停止装置(ATS)
鉄道の安全運行に欠かせない自動列車停止装置(ATS)は、フェイルセーフの好例です。ATSは、運転士が信号を見落としたり、適切なブレーキ操作を行わなかったりした場合に、自動的に列車を停止させるシステムです。
例えば、停止信号を冒進した場合、ATSが作動し、非常ブレーキをかけることで、衝突事故を未然に防ぎます。近年では、曲線や分岐器などでの速度超過を検知し、自動的に減速させる機能を持つATSも普及しています。
このように、ATSは、人間のミスを機械が補完することで、鉄道の安全性を高めているのです。
医療:緊急時の電源供給
医療現場では、停電は人命に関わる深刻な問題です。特に、人工呼吸器や輸液ポンプなどの生命維持装置は、継続的な電力供給が不可欠です。そのため、多くの医療機関では、非常用電源装置(UPS:無停電電源装置)や自家発電設備を設置し、停電に備えています。
これらの設備は、商用電源が途絶えた際に、自動的にバックアップ電源に切り替わることで、医療機器の継続的な動作を保証します。このように医療現場では、多重の電源供給システムによって、停電という緊急事態においても、患者の安全を守るフェイルセーフ設計が施されています。
フェイルセーフ運用の落とし穴
フェイルセーフは、機器やシステムの安全性を高める上で非常に有効な手段です。しかし、設計や導入だけで満足してしまい、運用面がおろそかになると、その効果は十分に発揮されません。
そこでここでは、フェイルセーフ運用における落とし穴と、形骸化を防ぎ、実効性を高めるためのポイントについて解説します。
ルールだけでは現場は変わらない
フェイルセーフは、あくまでも機器やシステムの異常に対処するための仕組みであり、人間のミスを完全に防ぐことはできません。 どんなに優れたフェイルセーフ機構を設計・導入したとしても、それを使用する人間がルールを守らなければ、事故のリスクを減らすことはできません。
例えば、製造現場で非常停止ボタンが設置されていても、作業員が「面倒くさい」「これくらい大丈夫だろう」といった理由で、安全手順を省略したり、非常停止ボタンの使用をためらったりすれば、事故が発生する可能性は高まります。
つまり、フェイルセーフを形骸化させないためには、ルールを遵守する現場の意識が重要なのです。
とはいえ、高度な専門性かつ複雑な作業プロセスが求められる製造現場の作業ルールを、新入社員含め従業員全体で遵守してもらうことは非常に難易度が高いです。そこで、ルールを守ってもらうためのポイントをまとめたPDF資料「“手順書通りにできない”から卒業!作業ルールを守らせる効果的な方法」を参考にすると、作業遵守を浸透させるためのヒントが得られるはずです。
下の画像をクリックして、「手順が守られる」仕組み作りの参考にPDF資料をダウンロードしてみてください。
安全教育や訓練の限界
ルールを徹底させるためには、安全教育が欠かせません。しかし、多くの企業で実施されている安全教育は、あまり機能していないケースが少なくありません。例えば、専門用語が多く読んでも理解が難しい分厚い紙の作業手順書は、特に新入社員の教育に機能せず、結局「OJT」や「口頭指導」で補われることが多いです。
OJTや口頭指導は、指導担当者によって教え方がバラつくので、新人スタッフのスキルにもバラつきが生じ、結果的に適切な安全教育につながりません。その結果、現場ではルールが形骸化し、フェイルセーフが有効に機能しなくなる可能性があります。
フェイルセーフ+安全教育による事故の未然防止
フェイルセーフを有効に機能させるためには、ハード面の対策(フェイルセーフ設計)だけでなく、ソフト面の対策(安全教育)を組み合わせることが重要です。
例えば塗加工関連事業を担う「トーヨーケム株式会社」では、安全教育の体制を徹底的に整備するために、「動画マニュアル(tebiki現場教育)」による教育を導入しました。同社は、作業中に想定される事故を動画上におさめ、現場従業員全員で動画を確認し、安全意識を高める動きを仕組化しています。
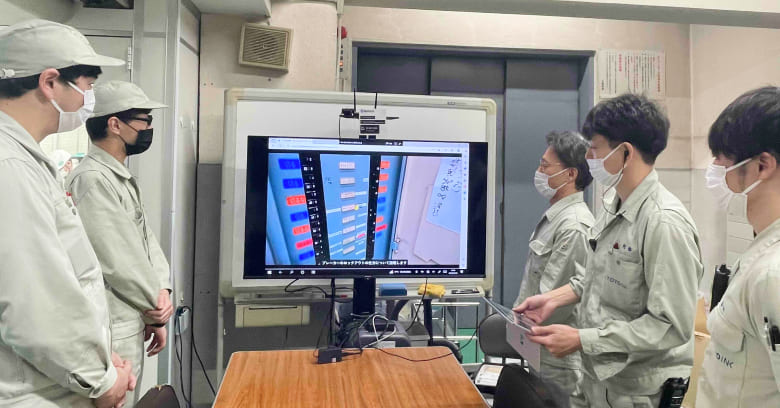
「インタビュー記事:トーヨーケム株式会社の安全教育事例」より抜粋
安全教育にとどまらず、技術やノウハウを動画で可視化し、社員間で共有することが可能となりました。動画マニュアルは文字や静止画よりも分かりやすく、実際の作業の流れをリアルに伝えられるため、技術伝承や多能工化の教育がスムーズに進むようになったのです。さらに、マニュアルの作成工数が半分に短縮され、OJTの時間も大幅に削減されました。
製造業で安全教育のために動画マニュアルを活用するケースは増え続けています。他にも製造業の動画マニュアル活用事例が知りたい方は、以下のPDF資料「製造業における動画マニュアル活用事例集」もあわせてご覧ください。
>>>PDF資料「製造業における動画マニュアル活用事例集」を見てみる
補足ですが、トーヨーケム株式会社が安全教育の整備を実現した動画マニュアル作成ツールは「tebiki現場教育」です。製造業に特化した動画マニュアル作成ツールなので、現場従業員が自ら撮影・編集できるのが強みであり、新入社員への技術継承や多能工化にも寄与する現場DXツールとなっています。
製造業に特化した動画マニュアル作成ツール「tebiki現場教育」の詳細機能や活用事例については、以下の画像をクリックしてPDF資料「3分でわかるtebikiサービス資料」もあわせてご覧ください。
フェイルセーフ実現には「設備保全」が不可欠
フェイルセーフは、機器やシステムの故障・異常時に、安全を確保するための仕組みです。しかし、その仕組みを支える設備そのものが故障してしまっては、元も子もありません。 そこで、この章では、フェイルセーフを実現する上で欠かせない「設備保全」の重要性について解説します。
特に予防保全や予知保全の徹底に課題を感じている現場担当者や、保全業務の形式知化を実現したい製造業の方には参考になるかと思います。本記事には書き切れていない、設備保全の実践的なポイントをいち早く知りたい方は、以下の画像をクリックしてPDF資料「製造業の設備トラブルによる生産性低下を解消する設備保全のDX」を先にご覧いただくことを推奨します。
フェイルセーフを担う機械の保全業務も重要
フェイルセーフは、あくまでも「故障や異常が発生した際の安全確保」を目的としたものです。そのため、故障や異常そのものを予防・抑制する「設備保全」とは、本来的に一体となって運用されなければなりません。
例えば、製造ラインに設置された非常停止ボタンは、フェイルセーフの代表例です。しかし、ボタン自体が故障して押せなくなっていたり、電気系統の不具合で信号が伝わらなかったりすれば、いざという時に機能しません。
つまり、フェイルセーフ機構を確実に作動させるためには、それを構成する設備が常に正常な状態に保たれている必要があるのです。 日常的な点検、定期的なメンテナンス、計画的な更新といった、適切な保全業務は、フェイルセーフの実効性を担保する上で、必要不可欠な要素なのです。
設備保全に欠かせない「データ収集」
効果的な設備保全を実施するためには、「データ収集」 が鍵となります。設備の点検、修理、部品交換などの履歴を正確に記録・蓄積し、分析することで、故障の予兆を察知したり、最適なメンテナンス時期を予測したりすることが可能になります。
例えば、ある部品の交換頻度が高いことがデータから分かれば、その部品の選定や取り付け方法に問題がある可能性を疑うことができます。また、設備の稼働時間と故障発生の関係を分析すれば、予防保全や予知保全に役立てることができます。
このように、データに基づいた設備保全は、故障や異常の発生を未然に防ぎ、フェイルセーフ機構への依存度を下げ、システムの安全性をより高めることにつながります。
設備保全の要は「現場帳票のデジタル化」
データに基づいた設備保全を実現するためには、「現場帳票のデジタル化」 が非常に有効です。従来、紙ベースで行われてきた点検記録や作業報告書などをデジタル化することで、データの蓄積・共有・分析が容易になります。
例えば、タブレット端末を使って点検結果を入力すれば、そのデータは即座にデータベースに反映され、関係者間でリアルタイムに共有されます。これにより、迅速な状況把握や、データに基づいた意思決定が可能になります。
また、デジタル化は、トレーサビリティの確保にも役立ちます。過去の点検記録や修理履歴を容易に追跡できるため、問題発生時の原因究明や再発防止に効果を発揮します。
一方、紙ベースの記録では、情報の検索や追跡に手間がかかり、データの活用が限定的です。つまり、現場帳票のデジタル化は、設備保全の効率化と高度化を実現し、フェイルセーフが有効に機能する環境を支える、重要な基盤となるのです。
現場帳票デジタル化を推進する方法やポイントについて詳しく知りたい方は、以下の画像をクリックしてPDF資料「はじめての現場帳票デジタル化ガイド」をダウンロードし、帳票デジタル化のポイントを押さえてみてください。
まとめ:フェイルセーフ実現の鍵は「現場教育の体制整備」と「現場帳票のデジタル化」
フェイルセーフは、単に機器やシステムに安全装置を付加するだけの話ではありません。設計、運用、保守といった、製品やシステムのライフサイクル全体を通じて、安全性を確保するための包括的な取り組みです。
その中でも、フェイルセーフを真に有効なものとするためには、「現場教育の体制整備」と「現場帳票のデジタル化」が、特に重要な役割を果たします。
「現場教育の体制整備」 は、フェイルセーフ運用の落とし穴である「ルールだけでは現場は変わらない」、「安全教育・訓練の限界」で述べた課題を克服するために不可欠です。現場作業者一人ひとりが、フェイルセーフの重要性を理解し、ルールを遵守し、安全意識を高く持つことが、事故の未然防止につながります。そのためには、現場の実態に即した実践的な教育、双方向のコミュニケーション、継続的な訓練、KYTやヒヤリハット事例の共有などを通じて、現場の安全文化を醸成していくことが重要です。
一方、「現場帳票のデジタル化」 は、設備保全の効率化と高度化を実現し、フェイルセーフを支える機器やシステムの信頼性を維持・向上させるために不可欠です。点検や修理の記録をデジタル化し、データとして蓄積・分析することで、予防保全や予知保全が可能となり、故障や異常の発生を未然に防ぐことができます。 また、リアルタイムな情報共有やトレーサビリティの確保は、迅速な状況把握と的確な意思決定を支援し、事故発生時の被害を最小限に抑えることにもつながります。
このように、「現場教育の体制整備」と「現場帳票のデジタル化」は、フェイルセーフ実現の両輪と言えるのです。製造現場をはじめ、あらゆる産業において、この2つを徹底することが、安全で安心な社会の構築に貢献すると考えます。それら2つを支援する「tebiki」は、製造現場における安全性を底上げします。現場改善を検討されている方は、動画マニュアル作成ツール「tebiki現場教育」と、現場帳票デジタル化「tebiki現場分析」のサービス資料を、以下の画像からぜひご覧ください。