かんたんデジタル現場帳票「tebiki現場分析」を展開する、現場改善ラボ編集部です。
タクトタイム・サイクルタイム・リードタイムという文字列を見ると『それぞれ何が違う?』という疑問をお持ちになる方もいるのではないでしょうか。本記事では、それぞれの意味や関係性、トヨタ生産方式との繋がりについて詳しく解説します。
また、タクトタイム・サイクルタイム・リードタイムそれぞれの計算式、最適な状態に改善する方法も詳しくご紹介していますので、ぜひ最後までご覧ください。
目次
製造業におけるリードタイムとは?意味や計算式
リードタイムとは、ビジネスにおける特定の業務開始から完了までの時間を指します。製造業では、製品の開発から顧客に納品するまでの期間を表す時間指標として用いられます。
製造業では製品の開発から調達、生産、そして納品までの全工程を効率的に管理することが重要です。すべての工程をひとくくりにした指標としてリードタイムを利用することが基本です。リードタイムは生産プロセス全体の生産性を可視化する指標として使用します。
製造業におけるリードタイムは、主に以下の4種類に分類分けすることができます。すべてを合算したものを「トータルリードタイム」と呼ぶケースもあります。
- 開発リードタイム:製品の企画や生産方法を確立するまでの期間
- 調達リードタイム:生産に必要な部品や材料の発注から入荷までの期間
- 生産(製造)リードタイム:製品の組み立てから完成までの期間
- 納品リードタイム:製品が製造工場から顧客まで運ばれる期間
リードタイムを算出する場合、4種類の時間を合算(開発リードタイム+調達リードタイム+生産リードタイム+納品リードタイム)して計算します。4種類それぞれのリードタイムを算出する計算式は、以下の画像の通りです。
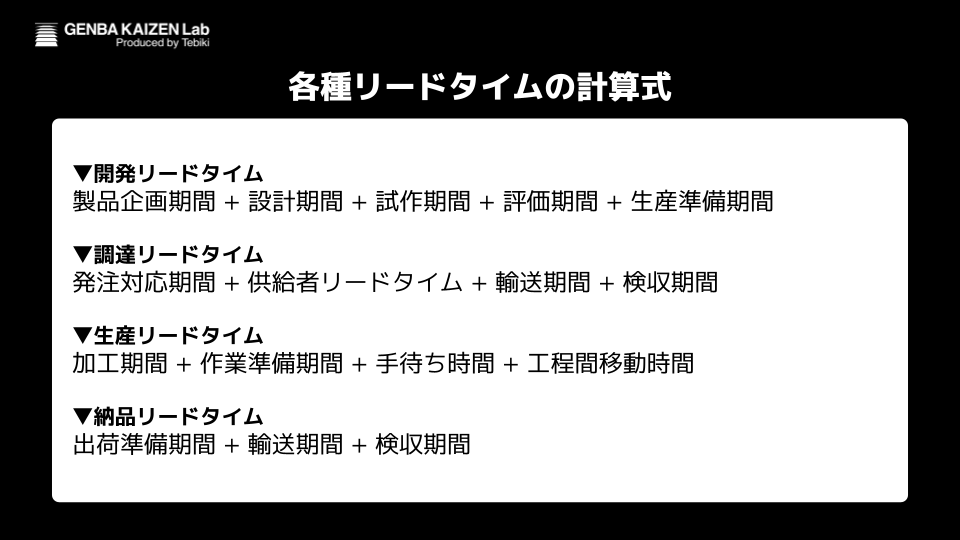
上記の計算式はあくまでも一例です。皆さんの現場で存在する工程が他にある場合は、それらの時間も合算して計算するようにしましょう。
リードタイムの計算式としては「フォワード法」と「バックフォワード法」の2種類あります。両者には、製造開始日から計算する/納期から逆算して計算するという違いがあります。
- フォワード法:製造の開始日から順に各工程を進めていく計算法
- バックフォワード法:納期から逆算して製造開始日を決定する計算法
生産プロセスが複雑ではなく「予測可能な製品」の場合にはフォワード法、顧客に対する「納期遵守」を重視したい場合はバックフォワード法といったように使い分けるとよいでしょう。
各工程の時間を効率的に集計する手段には、製造日報などの現場帳票をデジタル化する方法があります。
参考情報:現場帳票のデジタル化によって、日報の集計作業が1日1分まで短縮した事例
サイクルタイムとは?意味や計算式
サイクルタイムとは、原材料から製品を1つ生産するのに必要な時間を指します。
サイクルタイムが短いほど、同じ時間内に多くの製品を効率的に生産できているということになります。製造現場における生産性を計る重要な指標といえるでしょう。
サイクルタイムの計算式は「稼働時間 ÷ 生産した製品の総数」で算出します。
例えば、8時間のシフトで400個の部品を製造したとしましょう。サイクルタイムは8時間(480分/28,800秒)を400で割った1.2分(72秒)になります。つまり、1つの部品を製造するのに平均で1.2分(72秒)かかったということを意味します。
tebiki現場分析を活用すると、現場帳票の記録データに基づいて、各従業員のサイクルタイムが即時に計算されます。
▼tebiki現場分析でサイクルタイムを自動計算している例▼
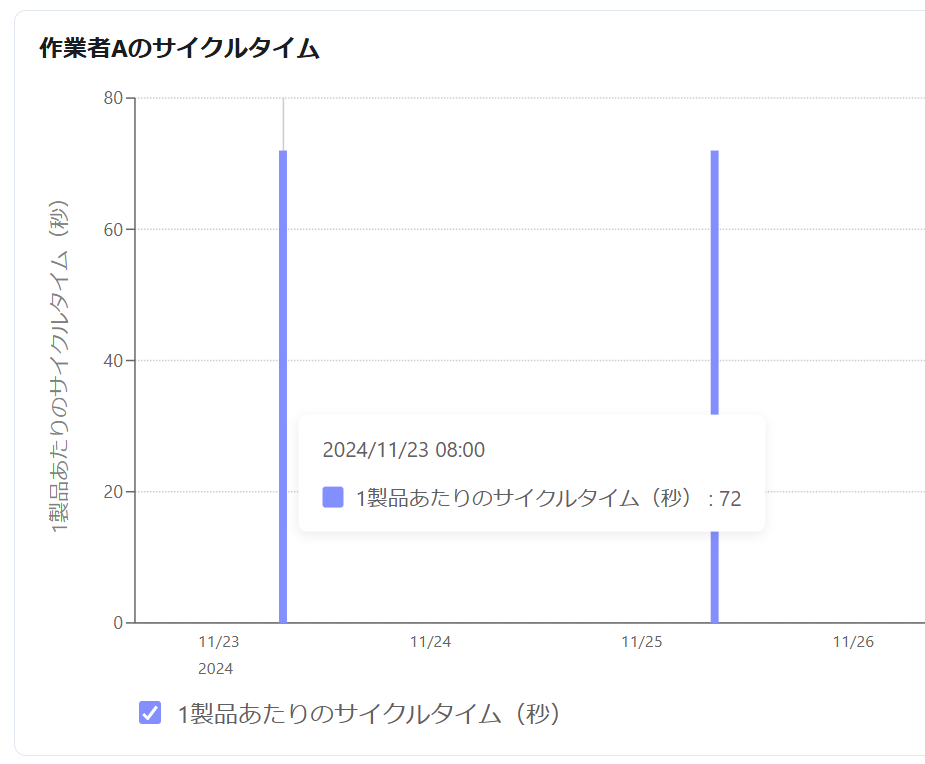
サイクルタイムにおけるボトルネックを可視化するときには、「マシンサイクルタイム」と「スループット」にも注目するとよいでしょう。
マシンサイクルタイムとは?
マシンサイクルタイムとは、ある特定の機械が1つの部品を製造するために要する時間のことです。具体的には、部品を取り付けてから取り外すまでの時間、すなわち機械が1つの作業サイクルを完了するまでの時間を意味します。
例えば、CNCフライス盤が金属ブロックを加工して部品を作る場合を考えてみましょう。フライス盤が金属ブロックを受け取ってから加工を終え、完成した部品を排出するまでの時間がマシンサイクルタイムとなります。
マシンサイクルタイムは、製造現場において機械のパフォーマンスを評価し、必要な改善を特定する上で重要なツールです。短いマシンサイクルタイムは高い生産効率を意味しますが、他の機械のサイクルタイムや、部品の取扱時間、機械のメンテナンス時間なども全体の生産時間に影響を及ぼすため、全体の生産ラインの効率が高くなるとは限りません。
スループットとは?
スループットとは、単位時間当たりにあるプロセスが処理できる作業量のことです。製造現場における生産能力を評価する主要な指標であり、高いスループットは高い生産性と関連しています。
例えば、自動車組み立てラインで1時間に20台の車を組み立てる能力がある場合、そのスループットは「1時間に20台」となります。スループットは資源(人手、機械、時間)の使用効率を示し、製造業者が生産能力を最大化するためにはどの部分を改善するべきかを示すことから、製造業における生産能力と効率性の把握が可能になります。
タクトタイムとは?意味や計算式
タクトタイムとは、顧客からの需要に対応するために、製品1つを製造する基準時間のことです。別名「ピッチタイム」「基準サイクルタイム」「標準サイクルタイム」とも呼ばれます。タクトタイムは次の式で計算されます。
タクトタイム = 稼働時間 ÷ 必要生産数
タクトタイムを順守することで、ムダな生産を防ぎ、製品の在庫過剰や供給不足を回避できるため、製造ラインのスピードを管理するための基準となります。例えば、顧客からの注文が1日に100個で、製造時間が8時間(480分)の場合、タクトタイムは480分÷100個=4.8分となります。
つまり、顧客の注文に納期遵守するために、1つの製品を作り終えるのに4.8分が基準になる、という意味です。一方で、すべての稼働時間が生産活動になるわけではありません。チョコ停の発生や段取り作業など、生産活動以外の要素も発生しています。
このような要素を考慮する場合、定時外の稼働も考慮した「実行タクトタイム」を設定します。
実行タクトタイムとは?
製造業では理想的な状況が常に続くわけではなく、定時以外の時間でタクトタイムを設定する必要が生じることもあります。実行タクトタイムとは、生産活動の中で適応を必要とする状況における、実際のタクトタイムのことです。
実行タクトタイムの計算式は「(定時の稼働時間+定時外の稼働時間)÷必要生産数」で表します。
例えば、機器の故障や原材料の遅延など、予期せぬ事態が発生した場合、生産ラインの動作時間が計画通りにはいかないかもしれません。計画通りではない状況では、顧客の需要に基づく理論的なタクトタイムだけではなく、現実的な制約を考慮した実行タクトタイムが必要となります。
サイクルタイム・タクトタイム・リードタイムの違い
ここまで、サイクルタイム・タクトタイム・リードタイムの概要をご紹介しました。この3つの違いを整理すると以下の内容になります。
- サイクルタイム:製品1個を生産するのに要する実際の平均時間
- タクトタイム:顧客需要に対応するため、製品1個を生産すべき基準時間
- リードタイム:原材料から最終的な製品が顧客に届くまでの全工程の総時間
特に混同しやすいものは、どちらも「製品1個」を指標としているサイクルタイムとタクトタイムの違いです。この違いは英語表記から読み解くと分かりやすくなります。
サイクルタイムの「Cycle」は、英語で繰り返しの動作やプロセスを表す単語です。つまり、サイクルタイム(Cycle time)は「一連のプロセスで生じた時間」と解釈することができます。
一方で、タクトタイムの「Takt」はドイツ語でリズムやテンポを表す単語です。つまり、タクトタイムは(Takt time)は「一定のリズムで刻む時間」と解釈することができます。
このように、タクトタイムは理想的な時間であることに対して、サイクルタイムは実際の現実的な時間という違いがあります。次章からは、この両者の関係性を深堀し、どのような状態が理想的な製造現場かを整理しましょう。
タクトタイムとサイクルタイムの関係性は?理想的な状態
前述したように、タクトタイムは「理想の生産性」でサイクルタイムは「現実の生産性」を表します。つまり、タクトタイムとサイクルタイムの両者が等しいか、あるいは非常に近い数値であることが理想的な状態といえるでしょう。
なぜなら、生産プロセスが効率的であり、顧客の要求(QCD)に適切に対応できていることを意味するからです。一方で、タクトタイム≒サイクルタイムではない場合、製造工程に何らかのボトルネックを抱えている可能性があります。
ここでは、次の2パターンについて、どのようなことが製造現場で起きているのかご紹介します。サイクルタイム/タクトタイムを最適な状態に改善する方法は後述しているので、こちらをクリックしてご覧ください。
- サイクルタイム>タクトタイムの時
- サイクルタイム<タクトタイムの時
サイクルタイム>タクトタイムの時
サイクルタイムがタクトタイムよりも長い場合、製品の製造に必要な時間が、顧客の要求を満たすために許容できる時間よりも長いため、製造プロセスが目標に追いついていないということを示します。
例えば、1時間に100個の製品を生産する必要があるのに対して、実際には1時間に80個しか生産できない場合、製造プロセスが目標に追いついていないため、問題になるでしょう。
この場合、作業者もしくは設備の原因で1個あたりの生産時間が悪化している恐れがあるため、製造日報や点検表などの現場帳票から実態を把握することが必要です。また、タクトタイム自体にムリが生じていないか確認することが必要です。
関連記事:【製造業】帳票の種類は?管理の手間を省くペーパーレス化や電子化を実現するツールを紹介
サイクルタイム<タクトタイムの時
サイクルタイムがタクトタイムよりも短い場合、製造は目標以上に効率的に行われています。一見、『生産性が高い良い状態では?』と感じるかもしれませんが、必要以上に生産性が高い状態は健全とはいえません。
顧客の要求以上に生産を行ってしまうと、超過分は過剰在庫となってしまいます。このような在庫は、物理的な保管スペースを必要とすることは勿論、実際に販売できるか不透明という在庫リスクを抱えています。販売できなかった場合、これらを処分する追加コストや生産時に生じた作業コストがムダとして発生します。
結果的にさまざまなムダを生み出すため、一概に生産性が良いとはいえないことはご理解いただけるのではないでしょうか。製造現場におけるムダ取りの考え方は、別記事「【トヨタ式】7つのムダとは?具体例を交えてムダを解説」をご覧ください。
では、タクトタイムとサイクルタイム、そしてリードタイムを最適な状態に改善するために必要なことはなんでしょうか?次章からは、製造現場のタクトタイム・サイクルタイム・リードタイム改善に必要な仕組みについて、私たちの考えをご紹介します。
製造現場のタクトタイム・サイクルタイム・リードタイム改善に必要な仕組み
製造現場のタクトタイム・サイクルタイム・リードタイムを、最適な状態に改善するためには「生産活動の状況をリアルタイムに可視化できる仕組み」が必要だと私たちは考えます。
特に、自社で管理を行いやすい生産工程におけるサイクルタイムの可視化ができると望ましいでしょう。
短期的なリードタイム改善を考える場合、サプライヤーなど第三者が介在しない工程を優先的に改善することで、改善のPDCAサイクルをスピード感を持って進行でき、早期に効果を出すことができます。
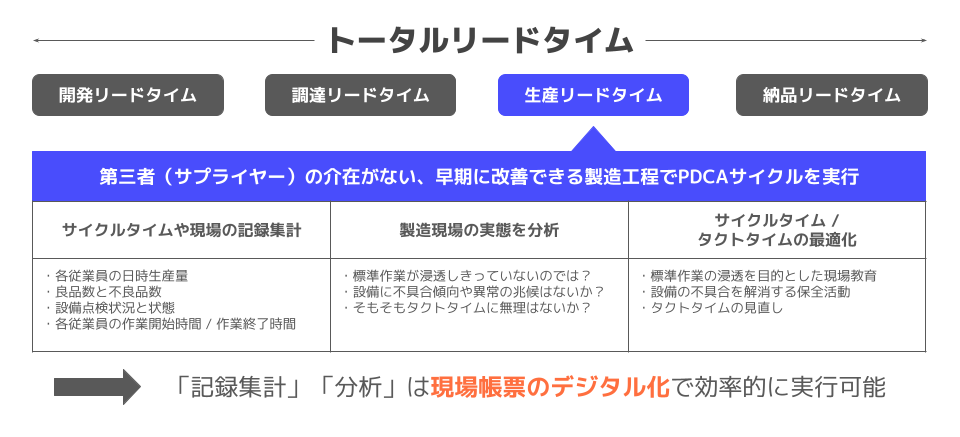
製造日報や点検表のような現場帳票で、サイクルタイムに直結する要素や良品数など、付随する現場データを集計しつつ、分析を通じてボトルネックを特定したうえでサイクルタイムの最適化を図るPDCAサイクルが理想的な状態だと、私たちは考えています。
タクトタイム・サイクルタイム・リードタイムを最適化させる改善アプローチとしては、以下の3つが基本的なものになります。
- ボトルネック工程を早期に特定する
- 設備のダウンタイムを防ぐ予知保全
- 標準作業を浸透させる現場教育の実行
この改善アプローチを手助けするツールとして、次章では「現場帳票デジタル化ツール」と「動画マニュアルによる教育改善ツール」の2つをご紹介します。
製造業のタクトタイム・サイクルタイム・リードタイム短縮を助ける2つのツール
現場帳票デジタル化による現場の可視化:tebiki現場分析
tebiki現場分析は、製造日報や点検表のような現場帳票をデジタル化し、記録/集計/分析の効率化によって、ボトルネックの早期改善を実現できるツールです。
紙やExcelで運用されているケースが多い現場帳票には、以下のような課題が生じています。現場帳票をデジタル化することで、これらの課題を解決することができます。
- 記入ミスにより正しい記録が蓄積されない
- 現場の管理者による再確認の手間が発生
- 承認待ちの現場帳票が膨大に存在し、素早く確認/承認することができない
- 分析のためにExcelへ転記する工数が追加で発生する
現場帳票デジタル化ツールであるtebiki現場分析の特徴として、改善策検討に直結する「分析」も効率的に実行することができます。帳票に異常値が記録された場合、即座に管理者へ通知が届くため、リアルタイムの異常検知を可能としています。
また、ダッシュボードには「記録データの自動グラフ化機能」を搭載しています。複雑な関数やマクロを組まなくても、管理図のようなQC分析を自動で行うことが可能です。
▼手間なくかんたんに製造現場の可視化を実行している事例▼
tebiki現場分析の詳細な機能やプランについては、別紙の概要資料からご確認いただけます。以下のリンクをクリックして、資料をご覧ください。
>>「かんたんデジタル現場帳票:tebiki現場分析」の機能概要を見てみる
動画マニュアルによる標準作業の徹底:tebiki現場教育
tebiki現場教育は、標準作業のような「動作」を動画マニュアルで視覚的に分かりやすく伝えられる、現場教育の改善を支援するツールです。
映像編集未経験者でも、かんたんに動画マニュアルを作成できるシンプルな編集機能に加え、マニュアルの活用状況を可視化できるレポート機能、マニュアルの理解度を確認するテスト機能、計画的な教育訓練を実行するスキルマップ機能など、教育推進を支援する周辺機能も備わっています。
▼動画マニュアルで作業不遵守を改善した事例▼
【tebiki現場教育導入事例:児玉化学工業株式会社より抜粋】
tebiki現場教育の詳細な機能やプランについては、別紙の概要資料からご確認いただけます。以下のリンクをクリックして、資料をご覧ください。
>>「かんたん動画マニュアル:tebiki現場教育」の機能概要を見てみる
【補足】タクトタイム・サイクルタイム・リードタイムとトヨタ生産方式の関係
タクトタイム・サイクルタイム・リードタイムは、それぞれトヨタ生産方式と密接に関係しています。トヨタ生産方式の2本柱として、「ジャストインタイム」「自働化」があります。両者のうち、ジャストインタイムなものづくりを実現するために、この3つのタイムのことを考慮する必要があります。
そもそもジャストインタイムとは、必要な製品を・必要な時に・必要なだけ作り・供給する、ムリムダムラが取り除かれたものづくりの進め方です。つまり、リードタイムの最適化がジャストインタイムの本質に直結するといえます。
そしてジャストインタイムを支える要素の1つとして「標準作業」があります。標準作業とは、ムリムダムラのない生産性が高い基準となる作業動作を指します。必要な製品を必要なだけ作り、滞りなく顧客へ供給するためには、工程内の滞留時間が少ない、最適な作業手順を踏む必要があります。
つまり、滞りなく必要な分を供給するためにタクトタイムが存在し、タクトタイムに沿ったものづくりを実行するために最適化されているものが標準作業といえます。
設定されたタクトタイムに対し、実態であるサイクルタイムと誤差が生じている場合、製造現場で何らかのボトルネックが存在していることになります。このボトルネックを特定し、対策を講じる一連の動きこそ、トヨタ生産方式における「カイゼン」の出発点ということです。
このように、タクトタイム・サイクルタイム・リードタイムとトヨタ生産方式は、密接に関係していることがお分かりいただけたかと思います。現場改善ラボでは、トヨタの製造現場を熟知する専門家による「トヨタ生産方式」の解説動画を無料で公開中です。
以下の画像をクリックするとご覧いただけますので、ぜひ本記事と併せてご活用ください。
「タクトタイム」「サイクルタイム」「リードタイム」を改善して生産性向上を実現【まとめ】
この記事では、製造業における生産効率の鍵となる「サイクルタイム」「タクトタイム」「リードタイム」について解説しました。それぞれの定義から計算方法、それぞれの関係性やトヨタ生産方式との繋がりまでを詳しく整理しました。
サイクルタイム・タクトタイム・リードタイムを最適な状態に改善するためには、「製造現場の可視化」が重要な要素だと私たちは考えています。リードタイムの中でも、第三者が介在しない生産リードタイムのサイクルタイムは、PDCAサイクルを素早く行うことができ、短期的な改善が期待できます。
サイクルタイムや良品数など現場の記録や、記録データの分析は「現場帳票のデジタル化」で効率的に実行することが可能です。分析で特定したボトルネックに対策を講じるためには、標準作業の確立が必要です。標準作業を正しく現場に浸透させるためには「動画マニュアルによる現場教育」が有効です。
現場帳票のデジタル化をかんたんに実現する手段にはtebiki現場分析、動画マニュアルによる現場教育を効率的に行う手段にはtebiki現場教育を展開しています。両ツールの機能概要を1冊にまとめた資料もご用意していますので、ぜひ以下の画像をクリックして資料をご覧ください。
▼クリックしてサービス資料を見てみる▼