かんたん動画マニュアル作成ツール「tebiki」、かんたんデジタル現場帳票「tebiki現場分析」を展開する現場改善ラボ編集部です。
不良品検知は品質管理の基本かつ重要な業務です。不良品を早期に発見し、製品の品質と信頼性を維持することは企業の競争力に直結する重大な課題だといえます。本記事では、不良品検知の種類や導入時の課題、解決方法までわかりやすく解説します。
もし、「品質不良を未然に防ぐための現代的な品質検査の手法」についていち早く知りたい方は、「製造業の品質不良を未然防止する次世代の品質検査(pdf)」をダウンロードしてご覧ください。不良品検知を改善するための重要なエッセンスのみを抽出し、まとめています。
不良品検知とは?不良の例も解説
不良品検知とは、製造プロセスで発生する傷・欠け・寸法不良などの欠陥を見つけ出し、不良品の流出を防ぐプロセスです。高品質な製品を生み出すためには、常に精度の高い不良品検知が重要です。
不良品検知のための技術は日々進歩し、市場としても成長を続けています。日本の試験・検査・認証市場は、2023年の約1兆8160億円(120億5,096万米ドル)から、2032年には2兆7630億円(183億1,391万米ドル)と、今後も堅調に成長すると予測されています。(株式会社レポートオーシャン調べ)
製造業で考えられる不良の種類
製造業における不良品は、主に外観不良(製品の外見における不良)と寸法不良(製品の大きさにおける不良)の2つに大別されます。金属、樹脂、食品など、各分野によって不良品の特徴は異なります。
各分野における代表的な不良の例を以下の表にまとめました。
分野 | 不良品の分類 | 不良品具体例 |
---|---|---|
金属 | 外観不良 | 変色、異物混入、気泡の混入 |
寸法不良 | 変形、寸法誤差、ゆがみ | |
樹脂 | 外観不良 | 成形不良、色ムラ、異物混入、印字ミス |
寸法不良 | 変形、寸法誤差 | |
食品 | 外観不良 | 変色、異物混入、印字ミス |
寸法不良 | サイズの不揃い、内容量不足 |
不良品を検知する3つの方法と課題
不良品検知には、主に以下3つの方法があります。それぞれの方法におけるメリット・デメリットについて解説します。
- 目視検査
- ルールベース検査
- AIを活用した検査
目視検査による不良品検知
目視検査は、熟練した検査員が製品を直接目で確認する検査方法です。柔軟な判断ができ、細かいニュアンスも見極められることや、機械や装置の購入といった大幅な初期投資が必要ないというメリットがあります。
しかし、検査員の疲労や個人の経験値といった差によって検査の質にばらつきが生じやすいのがデメリットです。また長時間の単調な作業は検査員の注意力を低下させ、見逃しや誤判定のリスクが高まります。他にも、ベテランの検査員になるには教育訓練に時間がかかる場合があることもデメリットとして挙げられます。
関連記事:目視検査の課題はどう解決する?原因や4つの対策を紹介
ルールベース検査機による不良品検知
ルールベース検査機は、画像認識や定められた閾値に基づいて不良品を検出する検査システムです。
あらかじめ設定された明確な基準に従って検査を行うため、非常に正確で大量の製品を高速に検査できるメリットがあります。具体的には、寸法、色、形状、表面の傷などを数値化された基準と照合し、不良品を判定します。
デメリットは、検査機が高額であることや、細かな設定の調整が必要で運用コストがかかることです。また、予期しない不良品や複雑な異常への対応が難しく、目視検査だとすぐにわかる明らかな不良でも、想定外に発生した場合は大量に見逃しが起こるリスクもあります。このため、完全な自動化は困難と言えるでしょう。
ルールベースの異常検知について詳しく知りたい人は、以下の記事もご参照ください。
関連記事:異常検知とは?機械学習不要で実施できるツールも紹介!
AIによる不良品検知
AIを活用した不良品検知は、大量の良品・不良品データを機械学習し、人間の目視では判別が難しい微細な異常を高精度で検出する最新技術を活用した検査です。複雑な欠陥パターンも認識可能となり、検査の高速化と精度向上が実現できるため、導入事例も増加傾向にあります。
一方で、初期導入コストが高く、継続的なデータ学習と定期的なシステムチューニングが必要です。また、誤検知を完全になくすことは困難で、人間による最終確認が依然として重要となっています。
このように、不良品の検知を検査機やAIに全て任せるのは非常に困難であり、未だ課題があるといえるでしょう。次の章で詳しく解説します。
不良品検知は完全にデジタル化できる?導入の課題6選
検査機器の技術は急速に進歩していますが、完全なデジタル化は現時点では難しいといえます。先述したAIやルールベース検査機は一次スクリーニングに有効ですが、最終的な判断には人間の経験と柔軟な判断力が必要不可欠です。
ここでは、不良品検知の導入にありがちな以下6つの課題について解説します。
- 初期費用が高額になりがち
- 費用対効果が見合わない可能性がある
- プログラミングなどの高度な専門知識を求められる場合がある
- 検査結果を紙の帳票に記載している場合はリアルタイム監視が難しい
- 従業員の教育不足により適切に運用できない
- AI導入には良品/不良品の写真が大量に必要
初期費用が高額になりがち
ルールベース検査機やAIシステムの導入には、高額な初期投資が必要です。ルールベース検査機の場合、業種によって数百万円から数千万円以上のコストがかかることがあります。とくにミクロン単位の精密な検査を要する業種では、さらに高額になる傾向があります。
AI検査システムの場合も、高性能カメラ、専用PC、適切な撮影環境の整備、学習モデル構築のためのプログラミングなど、多岐にわたる費用が発生します。これらの高額な初期投資は、とくに中小企業にとって大きな導入障壁となっています。
費用対効果が見合わない可能性がある
不良品検知システムの導入において、費用対効果は重要な検討事項です。
AIや検査機を用いた不良品検知では、AIや検査機で一次スクリーニングを行い良品はそのまま出荷、検出された不良品を人の目で最終判断するのが一般的です。しかし一次スクリーニングでの不良品検出率が高い場合、結果的に人間の行う検査工数が多いままになるリスクがあります。つまり、高額な投資に見合うだけの生産性向上ができない可能性があります。
効果的な不良品検知システムの導入には、自社の生産プロセス、不良品の特性、検査要件を綿密に分析し、適切なシステムを選択することが求められます。単純な装置導入ではなく、総合的な生産性向上の視点が重要です。
プログラミングなどの高度な専門知識を求められる場合がある
ルールベース検査機やAIシステムの導入には、高度な専門知識が必要です。検査機の複雑な設定や、AIの学習モデル構築には、専門的なプログラミングスキルが求められます。
また導入時だけでなく、システムの継続的なメンテナンスや調整においても、技術的な理解が不可欠です。専門知識を持つ人材が不足している場合、誤った設定や運用により、システムの効果が大幅に低下するリスクがあります。とくに中小企業では、このような専門的な人材の確保が深刻な課題となっています。
検査結果を紙の帳票に記載している場合はリアルタイム監視が難しい
検査を自動化しても、生産記録と検査結果の帳票が別々のシステムで管理されていると、効率的な品質管理が困難です。リアルタイムで検査結果を確認できないため、不良品の傾向を迅速に把握し、対策を講じることが難しいケースがあります。また、手作業による記録には転記ミスや記入漏れのリスクがあり、データの正確性が損なわれる可能性もあります。
逆に、検査結果と生産記録を一元管理してリアルタイム監視が可能になれば、品質改善や生産性の向上に大変役立ちます。
従業員の教育不足により適切に運用できない
高度な不良品検知システムを導入しても、従業員の教育が不十分であれば、その効果を十分に発揮できません。たとえば、不良品の判断基準を現場の従業員が正確に理解していないと、誤判定への対応が遅れ不良品の流出や過剰選別のリスクが高まります。
また、AI検査機の設定や調整方法を知らないと、判定基準の厳格化に対応できず、システムの精度が低下したまま運用される可能性があります。従業員のAIへの過度の依存は、異常の見逃しや機械任せの判断を招き、品質管理の精度を低下させる恐れもあるでしょう。
このように検査機やAIを導入した後でも、従業員の教育は非常に重要です。
AI導入には良品/不良品の写真が大量に必要
AIによる不良品検知システムを効果的に構築するには、大量の学習用画像データが必要です。最低でも、良品は250枚以上、不良品は不良の種類ごとに100枚の写真が必要と言われています。
これらの画像は、様々な角度、照明条件、製造環境で撮影される必要があり、データ収集と整理には膨大な時間と労力が求められます。中小企業や少量生産の現場では、このような大量の画像データを準備することが大きな課題となり、AI導入の障壁となっていると言えるでしょう。
不良品検知に組み込んで活用できるおすすめツール2選
このように検査機の技術は日々進歩していますが、導入やメンテナンス、最終的な判断には人の手が必要で、完全なデジタル化は難しいのが実状です。人間とデジタル、双方の能力を最大限発揮するためには、2つをサポートするツールの活用や教育が非常に重要になります。
記録のデジタル化で不良の発生状況を可視化
不良品検知はただ検知して流出を防ぐだけではなく、不良品が発生した原因を突き止め対策を打っていくことが必要です。
不良品を効果的に削減するためには、検査結果を分析し、不良品の発生源を特定し、継続的な改善を行いましょう。生産記録や検査結果をデジタルで一元管理することで、不良品の傾向、発生頻度、原因などを可視化し、より効果的な品質改善策を立案できます。またデジタル化されたデータは、新たな検査機の導入など、長期的な品質管理戦略の立案にも大きく貢献します。
tebiki現場分析なら異常検知もリアルタイムで行える
生産記録や検査結果をデジタルで一元管理するツールとして、「tebiki現場分析」がおすすめです。検査結果などを簡単な操作でグラフ化し、迅速な分析を可能にします。
▼tebiki現場分析によるデータのグラフ化イメージ▼
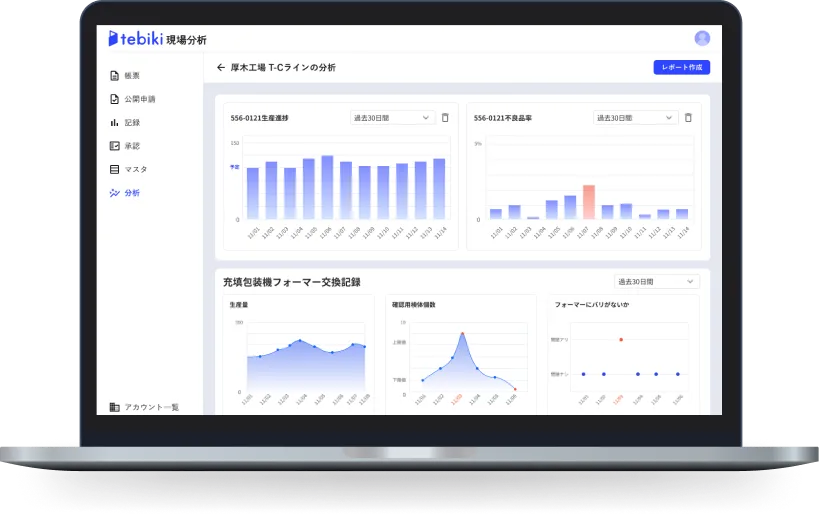
実際に、株式会社日本電気化学工業所では、データの蓄積と分析が容易になり、長期的な品質改善計画の立案が可能となりました。リアルタイムでデータを可視化することで、異常値を素早く検知し、即座に対応できるため、不良品発生のリスクを大幅に低減できます。
インタビュー記事:品質不良の未然防止をリアルタイムデータで実現。 異常値検知を迅速にできた理由。
tebiki現場分析の詳細な資料を詳しく知りたい方は、以下のリンクをクリックしダウンロードしてください。
動画マニュアルによる教育で不良を削減
「導入の課題6選」の章でも述べた通り、高精度な検査機やAIであっても最終的な判断は人間が行うため従業員のスキルは依然として重要です。効果的な現場教育を通じて、AIと人間の協力体制を構築することが、品質管理の鍵となります。
従来のOJT(On-the-Job Training)では限界がある教育プログラムを、動画マニュアルなどのデジタルツールの活用で、標準化された検査手順を効率的に伝えることが可能です。文字や図だけのマニュアルと比較して、動画は作業のコツや細かな動作が直感的に理解できるため、教育効果が高まります。
「tebiki現場教育」ならかんたんにマニュアルが作成できる
検査機やAIの導入により、不良品検出の精度が上がり大幅な効率化を期待できます。一方、検査機やAIのメンテナンスや運用管理、検査設定を決めるための検査基準の明確化など、従業員には新たなスキルが求められます。また、不良品の削減には製造工程での標準作業教育も欠かせません。
このように検査機やAIの導入で、従業員には新たなスキルや標準作業が重要になりますが、教育マニュアルの作成が従業員の負担になっているケースが散見されます。
「tebiki現場教育」は、撮影した動画で簡単にマニュアルが作成・共有でき、現場で実際に行う作業手順を分かりやすく伝えることが可能です。また、スマートフォンやタブレットで手軽に閲覧できるため、従業員が自分のペースで復習でき、スキル向上を促進します。
従業員の高いスキルとテクノロジーとの相乗効果が、さらなる品質向上につながります。
実際に「tebiki現場教育」で動画マニュアルを導入したクマガイ特殊鋼株式会社では、新人教育期間が5日から3日に短縮され、受講者の理解度が大幅に向上しました。視覚的で分かりやすい動画コンテンツにより、複雑な検査手順や注意点を効果的に伝えることができ、人材育成の効率化に大きく貢献しています。
インタビュー記事:人材危機に立ち向かう創業100年以上の中小企業。tebikiの活用で教育体制の改革と多能工化を推進!
tebiki現場教育の詳細な資料を知りたい方は、以下のリンクをクリックしダウンロードしてください。
まとめ
不良品検知技術は日々進化し続けていますが、人間による判断と検査の重要性は変わりません。AI、ルールベース検査機、目視検査など、それぞれの方法にはメリット・デメリットがあり、最適な品質管理には、これらを適切に組み合わせることが求められます。テクノロジーと人間の知識を融合させることが、製造業の品質向上につながります。
本記事でご紹介した「tebiki現場分析」「tebiki現場教育」を活用することで、現場での不良品検知精度をさらに向上させることができます。詳細な資料をご覧になりたい方は、以下の画像から是非ダウンロードしてください。