動画マニュアルツール『tebiki』が運営している現場産業向けメディア、現場改善ラボです。
食品工場で衛生管理を徹底するためには、ゾーニングの実施が欠かせません。しかし「ゾーニングを行う意味がよくわからない」「どのようにゾーニングを実施すればいいかわからない」と悩んでいる方も多いでしょう。
そこで、この記事では食品工場におけるゾーニングの目的や実施手順について解説します。仕切りに使えるものやゾーニングのポイントについても紹介するので、衛生管理を強化したい方はぜひ最後までご覧ください。
現場改善ラボでは、専門家による「HACCPに基づく衛生管理手法」の解説を動画でも無料公開しています。食品衛生管理における実践的なポイントを知りたい方は、以下からぜひご視聴ください。
目次
食品工場におけるゾーニングとは?目的は?
ゾーニングを検討している方は、まずその意味と目的をしっかり理解しておきましょう。
ゾーニングの本来の意味
ゾーニングとは、空間や地域を特定の目的に応じて区分けすることを指す言葉です。この言葉は、区域・範囲を意味する英語の「zone(ゾーン)」から派生しています。
zone(ゾーン)という名詞に「-ing」という接尾辞をつけることで動詞化し、ゾーン分けするという意味を持たせた「zoning(ゾーニング)」が生まれました。
もともと都市計画や建築分野で、土地や住宅地を用途ごとに分ける際に広く使用され、地域の特性に合わせた開発が行われていました。現在では、この概念が食品工場や医療機関をはじめとする多くの業界で採用されています。
食品工場での意味
食品工場における「ゾーニング」とは、工場内の各エリアを衛生レベルに応じて区分し、それぞれに適した作業や設備を配置することです。たとえば、原材料の受け入れエリア・保管エリア・加工エリアなど、作業内容に応じて明確に区分されます。
この区分けには、部屋を分けるだけでなく、パーテーションやカーテンなどでエリアを区切ることも含まれます。
食品工場におけるゾーニングの目的
ゾーニングは、食品の安全性を確保するための「HACCP」システムを効果的に導入する際に重要な役割を果たします。そのため、HACCPにもとづいた衛生管理を行う場合は、ゾーニングの目的を十分に理解する必要があります。
食品工場におけるゾーニングの目的は、以下の2つです。
- 衛生レベルの異なる作業を混在せずに隔離させるため
- 交差汚染が発生しやすい位置を把握し、重点的に対策するため
衛生レベルの異なる作業を混在せずに隔離させるため
ゾーニングを行うことで、異なる衛生レベルの作業を隔離し、異物混入や食中毒のリスクを大幅に低減できます。
たとえば、衛生管理が厳しく求められる最終製品の包装エリアと、原材料の処理や準備を行うエリアが同じ場所で行われた場合を考えてみましょう。
原材料のエリアでは、まだ洗浄されていない食材や外部から持ち込まれた包装材などによって、微生物や異物の汚染リスクが非常に高いです。このようなエリアと最終製品の包装エリアが同一の場所で混在していると、厳しい衛生基準が求められる最終製品に汚染物質が付着する可能性があります。
そのため、ゾーニングを活用して作業エリアを明確に分け、各エリアに求められる衛生基準を確実に維持することが必要なのです。
現場改善ラボでは、食品衛生のプロによる異物混入対策のアドバイスを動画でも無料公開しています。対策方法を従業員に徹底させる教育アプローチもご紹介していますので、以下をクリックしてぜひご覧ください。
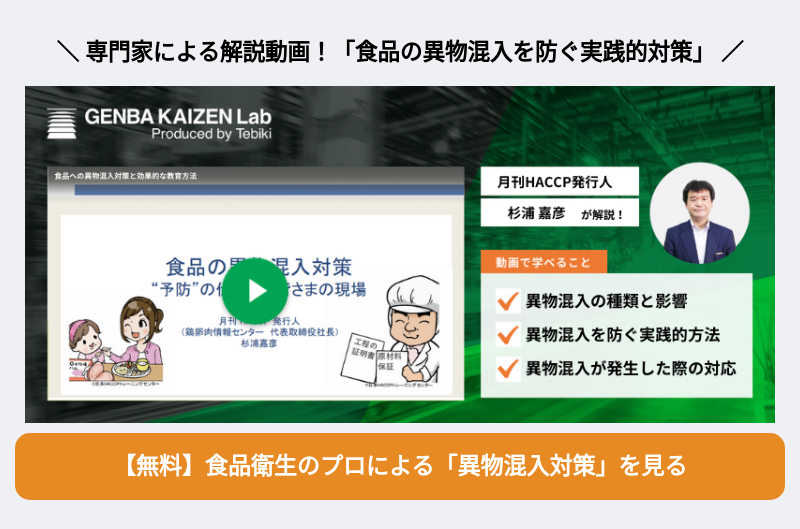
交差汚染が発生しやすい位置を把握し、重点的に対策するため
交差汚染とは、異なる物質やエリア間での不適切な接触や移動により、汚染物質や病原体が広がる現象です。ゾーニングにより、工場内の各エリアが衛生レベルにもとづいて区分けされることで「どのエリアからどのエリアに移動する際に交差汚染が発生しやすいか」を明確に把握できます。
たとえば、原材料を取り扱うエリアから加工エリア、または加工エリアから包装エリアに移動する際には、微生物や異物が持ち込まれるリスクがあります。ゾーニングを通じて、リスクの高いエリア間の移動ルートを事前に特定することで、交差汚染を防ぐための専用ルートの設定や消毒の徹底など、効果的な対策が取りやすくなります。
ただし、ゾーニングは工場内のエリアを区画割りして配置する手法に過ぎず、それだけでは交差汚染を完全に防ぐことはできません。そのため、ゾーニングを効果的に活用するには、エリア間のリスクを理解し、適切な対策を講じることが不可欠です。
ゾーニングにおける区域の種類
ゾーニングで設定される区域の種類は、以下の5つです。
汚染区域
汚染区域とは、工場内で最も汚染リスクが高いエリアを指します。具体的には、入荷室や出荷室が該当します。
入荷室では、外部から搬入された原材料や包装材が洗浄・消毒されていないため、微生物や異物が付着している可能性が高いです。一方、出荷室では清潔な状態の最終製品を扱うものの、外部との接触が再び発生するため、汚染のリスクがあります。
これらの汚染区域では、従業員が他のエリアに移動する際に適切な衛生管理を行わないと、汚染物質が他の区域に持ち込まれる危険があるため、移動時には特に注意が必要です。
準汚染区域
準汚染区域とは、汚染リスクが依然として高いものの、汚染区域ほど深刻ではないエリアのことです。具体的には、汚染区域から持ち込まれた物品が一時的に置かれるエリアが該当します。
このエリアでは、外部から搬入された段ボールや袋などの包装材が扱われるため、付着した汚染物質による汚染の可能性があります。
準清潔区域
準清潔区域とは、製造作業に適した一定の清潔環境が求められるエリアです。具体的には、原材料の洗浄・切断・調理といった初期段階の処理や加工を行う場所が該当します。
このエリアでは、清潔区域ほどの厳しい基準は求められないものの、最終製品に影響を与える可能性があるため、高いレベルの衛生管理が必要です。
清潔区域
清潔区域とは、製品の最終仕上げや包装が行われるエリアで、工場内で最も高い清潔度が求められる区域です。ここでの作業は、製品が消費者に届く直前の工程であるため、汚染リスクを最小限に抑えることが重要です。
清潔区域の高い清潔水準を維持するためには、アクセスを制限し、サニタリー区域を通過しなければ入室できない動線設計にする必要があります。
サニタリー区域
サニタリー区域は、清潔区域に入る前に必要な衛生準備を行うエリアであり、工場内での衛生管理の中枢となる場所です。この区域には、以下のような設備や機能を設置する必要があります。
▼サニタリー区域で必要な設備の例▼
エアシャワー | 高速の気流で作業服や持ち物についた微粒子を吹き飛ばす設備 |
手洗い設備 | 作業前に手指の汚染物質を除去するための設備 |
衛生準備室 | 作業前に作業服や靴を着用するための部屋 |
この区域を適切に管理することで、清潔区域の衛生水準を維持し、最終製品の安全性を高めることが可能です。
ゾーニングを実施するための手順
ゾーニングを実施する際は、次の手順を参考にしてみてください。
- 全ての作業工程を洗い出し、順番を付ける
- 作業工程を衛生レベルによって色分けする
- 作業工程の順に沿うように区域を配置する
- 区画と区画を仕切る方法を考える
- 各区画内でのルール・区画をまたぐ際のルールを決める
STEP1.全ての作業工程を洗い出し、順番を付ける
まず、工場内で行われているすべての作業工程を洗い出し、それぞれの工程がどの順序で進むのかを明確にしましょう。これには、原材料の受け入れから最終製品の出荷までの全工程が含まれます。初めてゾーニングを行う場合は、すべての作業工程を一つひとつ丁寧に確認し、流れを正確に把握することが重要です。
すでに実施している場合は、現行の作業工程が適切にゾーニングされているかどうかを再評価しましょう。工程の流れが変わっていないか、新しい工程が追加されていないかなど、最新の状態に合わせて見直すことでゾーニングの最適化が図れます。
STEP2.作業工程を衛生レベルによって色分けする
作業工程を洗い出したら、衛生レベルに応じて色分けを行いましょう。これにより、工場内の各エリアのリスク度合いを視覚的に把握しやすくなり、ゾーニングが効果的に進められます。
色の分け方は、HACCPなどで公的に定められているわけではありませんが、一般的にリスクの度合いを示す以下の3色を使うのがおすすめです。
- 赤色:汚染リスクが最も高いエリア(例:汚染区域)
- 黄色:中程度のリスクを持つエリア(例:準汚染区域、準清潔区域)
- 緑色:汚染リスクが低いエリア(例:清潔区域、サニタリー区域)
STEP3.作業工程の順に沿うように区域を配置する
色分けが終わったら、洗い出した作業工程が効率よく進行できるよう、それぞれの衛生レベルに応じた区域を工場内に適切に配置しましょう。作業工程の順番に沿って区域を配置することで、作業員が無駄な移動をせずに、効率的に作業を進められます。
さらに、作業員同士や物品の移動を最小限に抑える配置によって、交差汚染のリスクを低減することが可能です。初めてゾーニングを行う場合は、工場全体のフロアレイアウトを確認し、作業工程の順番を反映した配置を計画しましょう。
すでにゾーニングを実施している場合は、現在のレイアウトが作業工程の順番に沿っているか再確認します。工程が逆戻りするような動線や無駄な移動が発生している場合には、区域の配置を見直す必要があります。
STEP4.区画と区画を仕切る方法を考える
配置を検討した後は、区画と区画を適切に仕切る方法を考えましょう。各区画をしっかりと仕切ることで、交差汚染を防ぎ、各エリアの衛生レベルを維持できます。
区画を仕切る方法はいくつかあるため、工場の作業内容や予算に応じて選ぶ必要があります。具体的な仕切り方法については、後述の「ゾーニングの仕切りに使えるもの」で詳しく解説します。
STEP5.各区画内でのルール・区画をまたぐ際のルールを決める
最後に、異なる衛生レベルの区域間での作業や移動が適切に行われるように、各区画内でのルールや区画をまたぐ際のルールを明確に定めましょう。
▼ルールの例▼
各区画内でのルール | ・衛生管理のルール ・使用する器具や設備の規定 ・清掃や消毒の手順 ・廃棄物の処理方法 ・温度および湿度の管理基準 |
区画をまたぐ際のルール | ・作業員の動線管理ルール ・物品の取り扱い方法 ・入退室管理の方法 |
初めてゾーニングを行う場合は、実際の作業を想定し、そのルールが現実的に実行可能か確認することが大切です。すでにゾーニングを実施している場合は、現在のルールが適切に機能しているかを評価し、改善点を見つけましょう。
ルールを明確に設定することで、ゾーニングの目的である工場全体の衛生管理が強化され、安全で高品質な製品の製造が可能になります。
ゾーニングの仕切りに使えるもの
ゾーニングの仕切りには、次のようなアイテムが利用できます。
ライン
ラインとは、床や壁にテープ・塗料で印をつけてエリアを区分けする方法です。ラインを使った仕切りは、テープや塗料を使用するだけで済むため、他の仕切り方法に比べてコストを抑えられます。
また、設置が簡単で短時間で実施できるため、工場の稼働を止めずにゾーニングを進めたい場合にも有効です。さらに、位置調整や撤去も容易なため、工場内のレイアウト変更やゾーニングの見直しが頻繁に行われる場合にも柔軟に対応できます。
ただし、ラインは視覚的にエリアを区分けするだけで、空気の流れや汚染物質の移動を物理的に遮断することはできません。そのため、厳密な交差汚染防止が必要な場所ではなく、ローラー掛けや靴の履き替えを促す際に使用するのがおすすめです。
パーテーション
パーテーションとは、エリアを区分けするための仕切り板や壁のことで、可動式と固定式のものがあります。パーテーションは、他の物理的な仕切り方法に比べて低コストで設置できるため、予算を抑えつつゾーニングを強化したい場合に適しています。
しかし、パーテーションは視覚的な区分けや基本的な物理的な仕切りには効果的ですが、異物や空気中の微生物などの侵入を完全に防げません。そのため、空気の流れによる汚染が懸念される場合には、他の対策と組み合わせて使用する必要があります。
ビニールカーテン
柔軟で透明なポリ塩化ビニール製のカーテン「ビニールカーテン」を使って、エリアを仕切ることも可能です。ビニールカーテンは安価で購入でき、設置やメンテナンスも容易なので、予算が限られている場合にも活用できます。
透明度が高いものを使用すれば、作業員が向こう側のエリアを確認しやすくなり、コミュニケーションや作業の安全性が向上します。ただし、空気の流れや微細な汚染物質を完全に遮断するのは難しいため、清潔区域やサニタリー区域では他の対策が必要です。
また、ビニールカーテンは長期間の使用や頻繁な開閉により劣化しやすいため、使用頻度や設置場所によっては、こまめな交換やメンテナンスが必要になることがあります。
ドア・隔壁
ドアや隔壁を使用することで、異なる衛生レベルのエリアを物理的に完全に分離できます。これによって、交差汚染のリスクを大幅に減らし、厳密な衛生管理を行うことが可能です。また、気密性の高い設計のドアや隔壁を使用することで、さらに効果を高められます。
しかし、ドアや隔壁を設置する場合、他の仕切り方法に比べて費用が高額になることが多いです。さらに、一度設置するとレイアウトの変更が難しくなるため、工場のレイアウトを頻繁に変更する予定がある場合には適していません。
ゾーニングを実施する際のポイント
ゾーニングを実施する際には、次のポイントを押さえておきましょう。
サニタリー区域での衛生管理を徹底する
サニタリー区域の衛生管理は、工場全体の衛生レベルを左右する重要な要素です。この区域では、清潔区域や製品の最終工程に入る前の衛生準備が行われるため、徹底した衛生管理が不可欠です。
たとえば、手洗い設備を充実させ、適切な洗浄剤や消毒液を使用することで、手指の汚染を効果的に除去できます。また、サニタリー区域にエアシャワーを設置することで、作業員が持ち込む可能性のある微細な汚染物質を取り除くことが可能です。
導線が最短距離になる配置を考える
作業員や物品の導線が最短距離になるように区域を配置することは、工場の効率向上と交差汚染リスクの低減の両方において重要です。導線を最短距離にすることで、作業員は無駄な移動をせずに作業を進められ、生産効率が向上します。これにより、他の業務に時間を割けるようになり、長時間労働や忙しさによるミスを低減できるでしょう。
交差汚染のリスクが減少すれば、HACCPの遵守が容易になり、汚染による廃棄やロスの削減も期待できます。その結果、トラブル対応や廃棄物処理が減り、コスト削減や生産ラインの効率向上が図れます。さらに、重大な事故やリコールのリスクが軽減され、製品回収や賠償にかかる費用を抑えることも可能です。
交差汚染に気を付ける
ゾーニングの目的は、工場内のエリアを明確に分けることで衛生管理を徹底し、交差汚染のリスクを最小限に抑えることです。しかし、区域を分けるだけでは不十分であり、区域間を移動する際に交差汚染が発生する可能性があることに注意が必要です。
また、作業員や物品の移動だけでなく、設備や機器の共有も交差汚染の原因となることを認識しておく必要があります。たとえば、加工機械や計量器などを共有する場合、適切な洗浄や消毒が行われていないと、汚染が広がるリスクがあります。
そのため、区域ごとに専用の設備・機器を準備して共有を避けるか、清掃や消毒を徹底することが重要です。
空気の流れも意識する
清潔度が低い区域の空気が清潔度の高い区域に流れ込むと、清潔区域内の衛生環境が汚染される可能性があります。たとえば、原材料を扱う汚染区域の空気が、加工や包装が行われる清潔区域に流れ込むと、製品に微生物や異物が混入するリスクが高まります。
この問題を防ぐためには、空気の流れが清潔度の高い区域から低い区域へ向かうように設計することが重要です。具体的には、工場の設計段階で空気の流れを考慮した配置を行うことや、空気の流れを制御するシステムを導入することが有効です。
区域内の空気圧を周囲より高く保って外部からの空気流入を防ぐ「ポジティブプレッシャーシステム」や、空気の流れを物理的に制御する「エアバリア(風のカーテン)」を活用することで、工場の配置を変更せずに交差汚染を抑えられます。
ゾーニングだけでは不十分、衛生管理を高めるために重要なこと
ゾーニングはあくまで設備やエリアを整備する工程です。従業員が適切に衛生管理を行わない限り、その効果は発揮されません。そのため、次の3点を押さえて衛生管理を徹底することが重要です。
- 衛生教育を徹底して行う
- 衛生管理マニュアルを作成する
- 記録を取る
衛生教育を徹底して行う
ゾーニングを通じて衛生管理を強化するには、従業員が高い衛生意識を持ち、正しい手順で作業を行うことが不可欠です。特にサニタリー区域は清潔区域への入り口となるため、この区域で手洗いや消毒が徹底されていないと、清潔区域の衛生管理が無意味になります。
そのため、衛生教育を徹底し、各区域ごとの注意点や交差汚染のリスクを従業員に理解させることが重要です。具体的な施策としては、手洗い手順を示したポスターの掲示や衛生管理研修の実施などが有効です。
衛生管理マニュアルを作成する
衛生管理を徹底するには、すべての従業員が正しい手順で作業を行えるよう、衛生管理マニュアルを作成することが有効です。ゾーニングの目的や各区域ごとの衛生基準、異常発生時の対応方法などを記載することで、衛生管理のばらつきを防げます。
また、衛生管理マニュアルがあれば、新人も基本的な衛生管理の手順を短時間で学び、すぐに実行できるようになります。これから衛生管理マニュアルを整備する方は、更新や共有が簡単に行える動画マニュアルで作成するのがおすすめです。
記録を取る
ゾーニングや衛生管理を適切に実施したことを証明するためには、記録をしっかり取ることが大切です。特に、HACCPではリスクの分析と管理が徹底されていることを証明する必要があるため、日々の記録が重要な記録となります。これらの記録が適切に保管されていれば、監査や顧客からの問い合わせにも自信を持って対応できます。
一方、衛生管理の記録を怠ると、トラブル発生時に原因を特定するのが難しくなります。たとえば、製品に異物が混入した場合、その日の作業内容や従業員の衛生管理状況が記録されていないと原因の追求が困難になり、対策が後手に回る可能性があります。
最悪の場合、取引先の信頼を失って取引停止になるリスクもあるため、日々適切に記録を残せる環境を整えておきましょう。
衛生管理の「教育」と「記録」はtebikiで効率化!
衛生管理を高めるためには、衛生教育を徹底したり記録を取ったりすることが大切ですが、やはり「工数がかかる…」ということで中途半端になってしまっている事業者も少なくありません。
ここでは、それらの課題解決となるツール『tebiki』を2種類ご紹介します。
tebiki現場教育:動画マニュアル作成ツール
『tebiki現場教育』は、動画マニュアルを作成できるツールです。
▼動画マニュアル作成ツール「tebiki」紹介動画▼
非常にシンプルなデザインで、直感的な操作で動画編集や字幕の追加ができるため、パソコン操作やITスキルに自信がない方でも簡単に使いこなせます。
tebiki現場分析:帳票デジタル化ツール
『tebiki現場分析』は、帳票を電子化・ペーパーレス化できるツールです。現場で使われる帳票の作成はもちろん、記録や承認、分析などを簡単に行えます。また、画像の記録やリアルタイムでの情報確認も実現できます。
tebikiの動画マニュアルを「教育」に活用するメリット
では、なぜ『tebiki』が教育や記録を効率化できるのでしょうか?
ここではまず、『tebiki現場教育』のメリット、つまり動画マニュアルを教育に活用するメリットについて見ていきます。以下4つがメリットです。
- マニュアルの作成スピードが早くなる
- 教育内容が標準化される
- OJTにかかる工数が削減される
- 多言語に対応した教育が可能になる
マニュアルの作成スピードが早くなる
従来の動画編集ソフトでは複雑な操作が要求されるので、動画編集には膨大な時間がかかります。しかし、tebikiではスマートフォンでOJTの様子を撮影するだけで、音声認識システムが自動で字幕を生成するため、誰でも短時間で動画マニュアルを作成することが可能です。
また、正しい作業方法にはマル、不適切な作業方法にはバツなど、動画内に図形を挿入する機能が搭載されています。そのため、動画編集経験がない方やパソコン操作に不慣れな方でも、すぐに使いこなせます。
教育内容が標準化される
従来のOJTや紙マニュアルでは、教える人によって内容や質にばらつきが生じることがあります。しかし、動画マニュアルを活用することで、同じ内容を正確に伝えることが可能です。また、tebikiで作成したデータはクラウド上に保存されるため、常に最新の情報が反映され、教育の一貫性を維持できます。
OJTにかかる工数が削減される
新人教育において現場での指導は重要ですが、動画マニュアルを用いることで、事前に基礎知識や基本的な手順を学習させることが可能です。たとえば、工場での新入社員の教育では、現場に入る前に動画で基本的な作業手順や注意事項を学ばせることで、OJTの時間を短縮できます。
また、OJTにかける時間を減らすことで、現場の担当者が他の業務に専念できる時間が増え、生産性の向上が期待できます。
多言語に対応した教育が可能になる
tebikiは動画の字幕やタイトル、文書マニュアルを100ヶ国語以上に自動翻訳する機能を搭載しているため、外国籍の従業員にも正確に業務内容を伝えることが可能です。また、英語や中国語などの計15言語で字幕を読み上げられるため、母国語で説明を聞きながら正確に業務を遂行できるようになります。
食品製造業における動画マニュアルの活用事例をまとめた資料を無料でご用意しています。実際どのくらい効果があるのか、なぜ効果があるのかを実例に基づいて説明しています。ぜひ以下の画像からチェックしてみてください。
tebikiのデジタル現場帳票を「記録」に活用するメリット
続いて、『tebiki現場分析』が記録を効率化できる理由について見ていきます。
『tebiki現場分析』を活用するメリットは、以下の4つです。
- 記録を取るのが速くなり、ミスも減る
- 記録した数値をもとに分析できる
- 異常値に気づきやすくなる
- 必要なデータをすぐに見つけられる
記録を取るのが速くなり、ミスも減る
紙の帳票では、誤字脱字や読みにくい文字による記録ミスが起こりがちです。紙の帳票をExcelに転記する際には、打ち間違いや読み違いで誤った内容を記録してしまう可能性があります。
しかし、tebiki現場分析で帳票をデジタル化することで、直接データを入力できるようになり、記録ミスを減らすことが可能です。
記録した数値をもとに分析できる
紙で記録を行うと、分析用のExcelファイルへの転記や集計作業の手間が大きくなります。しかし、tebiki現場分析を使うと、データ分析の専門知識がなくても直感的な操作でデータの可視化や分析が行えます。
これにより、データをもとに製造プロセスの改善や設備の異常予防を実施し、不良品を削減することが可能です。
異常値に気づきやすくなる
紙の帳票では、異常を記録しても管理者がリアルタイムで把握するのが難しく、対応が遅れることも少なくありません。しかし、デジタル帳票では記録したデータが即座にクラウド上に反映されるため、管理者はいつでもどこでもリアルタイムで状況を確認できます。
さらに、正常値から外れたデータは自動的に異常値として検出され、承認者へアラートメールが送信されるため、異常値を見逃さずに迅速に対応することが可能です。
必要なデータをすぐに見つけられる
紙の帳票を使用すると、過去の記録を探すのに膨大な時間と労力がかかりますが、デジタル帳票では必要なデータを瞬時に検索できます。また、tebiki現場分析では記録内容をCSVファイル形式でダウンロードできるため、データの集計や分析も効率よく進められます。これにより、過去のデータをもとに衛生管理の施策を検討することが可能です。
tebiki現場分析の詳細は以下の画像からご覧いただけます。現場帳票のデジタル化に少しでも興味がある方は、ぜひクリックしてみてください。
tebikiを使って衛生教育を効率化した事例
tebikiが衛生教育を効率化した事例を3つ紹介します。
より多くの事例については、以下の資料に掲載しております。ぜひダウンロードして、tebikiの具体的な活用イメージをご覧ください。
株式会社大商金山牧場
食肉の生産から加工・販売までを行っている株式会社大商金山牧場では、FSSC22000取得拠点とそれ以外の拠点で衛生管理教育に大きなバラツキがあるという問題を抱えていました。そこで、全拠点で衛生管理教育の内容を統一するためにtebikiを導入し、品質保証室が食品安全マネジメントシステムの教育内容をもとに新人教育マニュアルを作成することに。
その結果、新人教育の質が向上し、会社全体の衛生教育レベルの底上げにつながりました。また、付きっきりで説明することがなくなり、OJTの教育工数を5割程度削減することに成功しました。
株式会社大商金山牧場の導入事例をより詳細に知りたい方は、こちらの記事をご覧ください。
インタビュー記事:衛生管理教育を徹底し、食肉の安全性を確実なものとするために動画マニュアルを活用!
ロイヤル株式会社
▼動画マニュアルtebiki活用事例動画:ロイヤル株式会社▼
ロイヤルグループ向けの袋入りレストラン用商品や機内食を製造しているロイヤル株式会社では、繁忙期に1日50名以上の新人受け入れ教育を行う必要があり、その負担が大きいという問題を抱えていました。そこで、新人受け入れ教育を効率化するためにtebikiを導入し、動画マニュアルを作成することに。
その結果、新人に同じ内容を繰り返し教える必要がなくなり、教育者の負担を大幅に軽減することに成功しました。また、動画を活用することで業務の属人化を解消し、教育担当者の突発的な休みにも対応できるようになりました。
ロイヤル株式会社の導入事例をより詳細に知りたい方は、こちらの記事をご覧ください。
インタビュー記事:1日最大50名勤務する短期バイトの方々への入場教育を動画マニュアルに置き換え、教育工数をほぼ0に削減!
イセ食品株式会社
鶏卵の製造を行っているイセ食品株式会社では、外国籍の従業員が多く、大事なことがうまく伝わらないという問題を抱えていました。そこで、従業員の理解度を向上させるためにtebikiを導入し、自動翻訳機能を活用しながら3ヶ月で現場作業の動画を200本以上作成することに。
その結果、外国籍の従業員がスムーズに業務内容を理解できるようになり、短期間で現場に入れるようになりました。また、動画を使うことで教育の効率が大幅に向上し、座学の時間を3日から2日に短縮することに成功しました。
イセ食品株式会社の導入事例をより詳細に知りたい方は、こちらの記事をご覧ください。
インタビュー記事:導入3ヶ月で動画200本作成。製造現場の作業標準化と多能工化を推進しています。
まとめ
この記事では、食品工場におけるゾーニングの目的や実施手順について解説しました。適切なゾーニングを実施することで、工場内の衛生レベルを維持し、交差汚染を防ぐことが可能です。
また、区域を明確に分けることで、作業効率の向上も期待できます。そのため、衛生管理や生産性を改善したい方は、この記事で紹介した手順を参考にしてゾーニングを導入してみてください。
効率よく衛生管理を改善したい方は、2種類のtebikiを活用するのがおすすめです。『tebiki現場教育』を活用して動画マニュアルを作成することで、衛生管理のルールや正しい作業手順を効果的に伝えられます。
さらに『tebiki現場分析』を用いて現場の帳票を電子化することで、短時間で記録を取れるようになり、記録を分析して衛生管理を改善しやすくなります。『tebiki』の資料は、以下から無料でダウンロード可能ですので、ぜひ詳細をチェックしてみてください。
・今すぐ無料で『tebiki動画教育』の資料をダウンロードする
・今すぐ無料で『tebiki現場分析』の資料をダウンロードする