かんたん動画マニュアル作成ツール「tebiki」を展開する現場改善ラボ編集部です。
ジャストインタイム(JIT)は、ムダを徹底的に排除して在庫の最適化や生産リードタイムの短縮を実現するトヨタ生産方式の柱の1つです。この記事では、ジャストインタイムの意味や取り入れる具体的なメリット・デメリット、3つの原則などについて分かりやすく解説していきます。
なお、現場改善ラボではトヨタ自動車出身の小森 治氏による「トヨタ生産方式と現場改善」に関するセミナー」(視聴無料)をご用意しております。トヨタ生産方式やジャストインタイムの概念を学びたい方は以下の画像をクリックしてご覧ください。
目次
ジャストインタイム(Just In Time)の意味とは?トヨタ生産方式との関係
ジャストインタイムとは、トヨタが取り入れている独自開発の生産方式であり、「必要なものを、必要なときに、必要なぶんだけつくる」ことが目的です。ジャストインタイムの実践によって、生産におけるあらゆるムダを削減でき、生産リードタイムの短縮につながります。余剰在庫を抱えることなく、使った分だけをタイムリーに生産することによって、生産の効率化・コストの削減を目指すことができるのです。
ジャストインタイムは「生産工程の同期化」をコンセプトにしたトヨタ生産方式の2本柱の1つであり、もう一つの柱は後述する「ニンベンのついた自動化」です。
トヨタにおけるジャストインタイムは以下3つの原則で実践されています。
- お客様が必要なものを必要な時に必要なだけ
- 物や情報を途中で停滞させずに
- 売れたペースでつくる
トヨタ生産方式は自動車業界を中心とした製造業では欠かせない改善の哲学です。以下では、トヨタ自動車出身の講師によるトヨタ生産方式に基づいた改善の着眼点について解説している動画を無料でご視聴いただけます。以下の画像をクリックしてご覧ください。
ジャストインタイムの歴史
製造業において、ジャストインタイムが広く知られる前は、「大量生産方式(フォード方式)」といって、ひとつの製品を大量に生産することで低価格の製品を市場に供給する方式が主流でした。
大量生産方式が完成したのは1913年頃のアメリカ、フォード社であるといわれています。大量生産方式は、コストが抑えられる上に、製品の種類が少ないことから品質にバラツキが生じにくいというメリットもあり、アメリカから世界に広がりました。
当時のアメリカは、クルマが当たり前のように日常生活に根付いており、その実情を見たトヨタ自動車の創設者である豊田喜一郎氏は日本でも国産乗用車の製造を決意しました。しかし、当時の日本では資金・資材が現代のように豊富ではなかったこともあり、貧しい日本国内の環境でムダな在庫を抱えずに製品を作る「ジャストインタイム」を提唱したのです。
トヨタによるジャストインタイム方式の生産や経営の効率化が明らかになると、多くの製造業がジャストインタイムの考え方に基づく生産方式を取り入れました。今では、製造業をはじめ小売や物流などの他業種にも、ジャストインタイムの考え方が広がっています。
2本柱のもう一つは「ニンベンのついた自動化」
トヨタ生産方式においての「自動化」とは、自動化に人間の知恵をつけた「ニンベンのついた自動化」を指します。人間の知恵とは、品質異常や機械・設備異常などが発生した際、設備自体が異常を検知して自動で停止したり、作業者が停止スイッチを押して生産ラインを止められるようにしたりすることです。
単なる自動化だけでなく人間の知恵をつけることによって、不良品の流出を防止でき、品質を工程で作り込むことに繋がります。また、異常を検知して自動停止することで機械/設備を見張る必要がなくなり、省人化も可能になるのです。
ジャストインタイムを実現する「かんばん方式」
かんばん方式とは、ジャストインタイムを実現するための仕組みであり、かんばんとは、発注情報が書かれた発注書の役割を果たす書類のことです。ジャストインタイムでは、後工程が前工程に必要な部品を発注し、前工程が後工程に完成した部品や製品を渡すときに納品書のかわりとしてかんばんも送ります。
かんばんが存在することで、各工程の作りすぎによる過剰在庫を防止できます。かんばん方式については「【図解あり】かんばん方式をわかりやすく解説!メリットとデメリットは?」の記事で図解を使用して詳しく解説していますので併せてご覧ください。
ジャストインタイムの前提:平準化生産ができる
平準化とは物事を均一化して偏りを無くすことであり、製造業においては、「リードタイムやコストを揃えること」「商品や部品の種類を平均化すること」を指し、生産量や製品科目をいつでも一定に生産できる状態のことです。
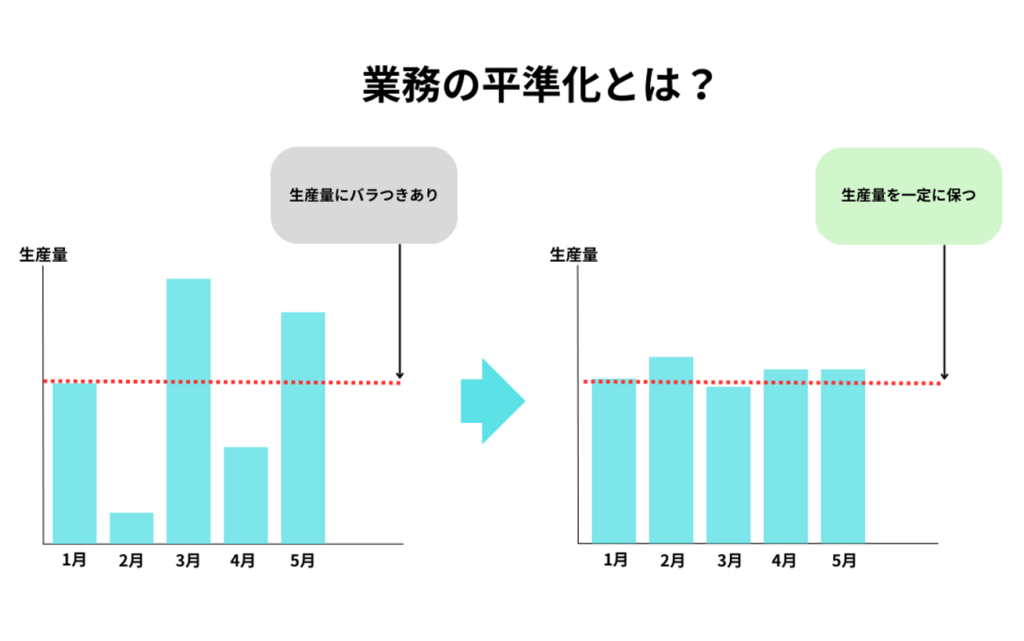
時間や工程によって、生産数量のバラツキが出てしまうと、「暇な工程」と「忙しい工程」が生まれてしまい、人件費がムダになってしまいます。また工程によって在庫量に差がでてしまうことにもなりかねません。
そのため、ジャストインタイムをするうえでは、この平準化生産ができる状態であることが大前提としてあります。業務平準化が求められる理由や実現する方法などを詳しく知りたい方は、以下の記事もチェックしてみてください。
関連記事:業務平準化とは?業務標準化との違いや実現させる方法を紹介!メリットデメリットや成功事例も合わせて解説
ジャストインタイムの3原則
ジャストインタイムの3原則は以下の3つです。
- 後工程の引き取り
- 生産現場の流れをつくる
- 必要性でピッチタイムを決める
後工程の引き取り
後工程の引き取りとは、後の工程が前の工程に対して必要な製品を発注し、前工程は受注分だけ生産することをいいます。そして、前工程は後工程が引き取っていったものと同数の製品を生産します。後工程の引き取りのポイントは、前工程が後工程が引き取っていた製品と同数を生産することです。
完全な受注生産にしてしまうと、生産完了までのリードタイムが長くなってしまいますが、この方法であれば最低限の在庫を持つことになりますので、リードタイムを短縮できます。
製造業におけるリードタイムの詳しい意味や計算式などを詳しく知りたい方は「タクトタイム・サイクルタイム・リードタイムの計算と改善方法【意味や違いも解説!】」の記事もチェックしてみてください。
生産現場の流れをつくる
「生産現場の流れをつくる」とは、部品が前工程から後工程に送られていく流れが逆流、停滞したりしないようにすることです。ジャストインタイムの3原則である生産現場の流れは「細く速い流れ」と表現されます。
生産現場の流れは「一個流し」で作ります。一個流しとは製品や部品を1工程で1つずつ生産をして次の工程に流していく生産方法です。一個流しを徹底すれば、原材料や仕掛品や完成品の在庫を最小限に抑えることができます。
必要性でピッチタイムを決める
ピッチタイムは、稼働時間と顧客の要求量から計算されるものです。ピッチタイムは以下の計算式で求めます。
ピッチタイム(タクトタイム)=生産可能な時間÷生産要求量
たとえば稼働時間が8時間で、必要な生産量が160個だった場合の製品1個当たりのピッチタイムは3分です。ピッチタイムを計算したらサイクルタイムを計算します。サイクルタイムとは実際に製品を作るためにかかってある時間のことです。サイクルタイムは以下の計算式で求めます。
サイクルタイム=稼働時間÷実際の生産数
稼働時間が8時間で実際の生産数が80だった場合、ピッチタイムは6分となります。ピッチタイムよりもサイクルタイムが大きい場合には、必要な量に生産が追いついていないということです。逆にピッチタイムがサイクルタイムよりも短ければ、顧客の必要量を満たしており、その工程で最大量を生産すれば過剰在庫が生まれてしまうということです。
こうしてピッチタイムとサイクルタイムを比較して、ピッチタイムを調整することでムダな人件費や在庫管理費を削減できます。
ジャストインタイム(Just In Time)のメリット
「必要なものを、必要なときに、必要なぶんだけつくる」ジャストインタイムは様々な製造現場で用いられていることからも、数多くのメリットがあることがわかります。ここでは、具体的なメリットについて紹介していきます。
余剰在庫を防止でき、在庫の最適化が実現する
ジャストインタイムは、ムダな在庫を抱えずに必要なものを必要なときに必要なぶんだけつくる考えであるため、余剰在庫を防止できるのが大きなメリットです。
製品や部品の在庫を多く抱えてしまうことによって、「在庫維持費用の増加」「劣化や陳腐化による商品価値の低下」「キャッシュフローの減少」など、大小限らず様々な悪影響があります。ジャストインタイムによって、これらのリスクを防止でき、在庫の最適化が実現します。
リードタイム短縮による機会損失を防げる
ジャストインタイムの前提である平準化生産により、1つの製品が前工程から後工程へ停滞・後戻りなくスムーズに流れる「工程の流れ化」が推進されます。工程の流れ化ができない場合でも、1つのロットを小さくして製品の切り替え頻度を向上させ、ロット生産工程と1個流し工程との間の在庫量を減らす「小ロット生産化」で流れ化をはかることができます。
これによって、生産リードタイムの短縮につながり、注文に対して迅速に対応できるようになるのです。結果として、販売の遅延や機会損失のリスクの軽減が実現できるでしょう。
健全なキャッシュフローを保てる
製造業において余分な在庫を常に抱える状態は、保管するためのコストが増加してしまい、必要以上のコストがかかってしまいます。
一方で、余計な在庫を抱えずに必要な分だけ生産するジャストインタイム方式を採用することで、不必要なコストがかからずに健全なキャッシュフローを保つことができるのです。
現場にある7つのムダを可視化できる
トヨタ生産方式では、ムダを「付加価値を高めない現象や結果」としており、具体的には以下を「7つのムダ」と定義しています。
- つくりすぎのムダ
- 手待ちのムダ
- 運搬のムダ
- 加工のムダ
- 在庫のムダ
- 動作のムダ
- 不良・手直しのムダ
必要なものを必要なときに必要な分だけ生産するジャストインタイムを取り入れることによって、これらのムダを可視化し排除できます。7つのムダについては、別記事「7つのムダ、一番悪いのは〇〇!改善方法も解説」でそれぞれのムダを具体的に解説しているので併せてご覧ください。
また、トヨタ生産方式の「3M(ムリ・ムダ・ムラ)」も製造業の根幹となる考え方の1つです。3Mについてより詳しく理解したい方は、製造業の経営コンサルティング企業「株式会社GEMBAコンサルティング」代表の大原 健佑氏による解説動画も併せてご視聴ください。
不良品を作り続けるリスクを低減できる
ジャストインタイムは、大量生産をするわけではなく、必要なものを必要なときに生産する方式です。大量生産と比べて、1つの部品や製品にかける時間的なコストに余裕があり、製品のチェック体制を整えられるため、不良品を作り続けるリスクを低減できます。
製造の管理体制の強化や作業環境の整備などに時間を割けるのは、ジャストインタイムのメリットと言えるでしょう。
関連記事:【改善事例あり】製造業における品質不良の原因と8つの対策
ジャストインタイム(Just In Time)のデメリットや問題点
様々なメリットのあるジャストインタイムですが、一方で注意しておくべきデメリットがあるのも事実です。ここでは、ジャストインタイムのデメリット・問題点について紹介していきます。
- サプライヤーの価格変動の影響を受けやすい
- 消費者の需要に対応しきれない可能性がある
- 原材料不足によって在庫を補填できない可能性がある
- 流通過程の自然災害・事故によって影響が生じる
- サプライヤーへ負担が増加してしまう
サプライヤーの価格変動の影響を受けやすい
消費者需要にあわせて製品を製造するジャストインタイムでは、製造に必要な部品や材料を必要になった分だけサプライヤーに納品してもらう形になります。
この場合には、価格変動の影響を受けてしまう点に注意しておく必要があります。様々な価格が高騰している昨今では、サプライヤーから提供される部品の価格も変動するため、場合によっては通常よりも高価格になる可能性があるのです。
また、サプライヤーで抱えている在庫には劣化や陳腐化を防ぐための維持管理コストも発生しているため、人件費も考慮された上で価格も変動する場合もあるでしょう。
消費者の需要に対応しきれない可能性がある
ジャストインタイムは消費者のニーズに沿って必要な分だけ、部品を調達して製品の製造を進めます。余分な在庫を持たないという考えであるため、消費者の需要が高まってしまうと在庫が不足してしまい対応しきれない状況も考えられるので注意が必要です。
移り変わりが激しく消費者のニーズが目まぐるしく変化する昨今では、どのタイミングで需要が変動するのかを予測するのは困難といえます。需要に対応できない場合には、満足度の低下や消費者離れなどのリスクも考えられるでしょう。
原材料不足によって在庫を補填できない可能性がある
在庫となる部品を生産するための原材料は常に世の中にあるわけではありません。日経XTECKの調査結果によるとおよそ9割のメーカーで部材不足によって生産計画に影響が発生していると回答しています。
予定している材料の入手ができないために製品が作れず、納期が遅れてしまうという悪循環に陥っている企業が多いのです。ジャストインタイムでは、部品を納品するサプライヤーが機能しなければ生産が停止してしまうリスクを常にはらんでいます。生産停止や消費者への納品が遅延してしまうと、企業にとって莫大な損失をもたらす可能性があるでしょう。
流通過程の自然災害・事故によって影響が生じる
サプライヤーが部品や製品を納品する過程で台風や豪雪、地震をはじめとした自然災害や不慮の事故など、流通の場面で発生する事象によって大きな影響が生じる可能性があります。
自然災害や事故については、いくら予防をしたとしても外部的な要因が大きいためにゼロにするのは困難です。
サプライヤーへ負担が増加してしまう
ジャストインタイムの導入によって、サプライヤーへの負担が増加してしまう点にも注意が必要です。サプライヤーにとって、頻繁な納品や小ロット生産は負荷が大きく、労力やコストの増加につながる可能性があり、生産性が低下してしまうリスクがあるのです。
また、在庫をサプライヤー側で抱えなければならない場合、納品するためのドライバー雇用や継続して納入するための見込み生産予測などあらゆるコストと負担がかかってしまいます。サプライヤーにしわ寄せがいってしまう構図になりかねないので、注意が必要です。
ジャストインタイム(Just In Time)の実践には「作業者の生産性」が大切
ジャストインタイムを実践するうえでは、あらゆるムダの排除が欠かせません。デジタル技術の活用や機械設備の自動化などによって製造現場の生産性自体は向上できるものの、最終的に生産性に関わるのは人です。人の生産性を維持し向上させるためには、標準作業の確立が必須と言えるでしょう。
標準作業を確立するためには、作業手順書が必要になりますが、作成方法は様々です。次の見出しでは、標準作業の確立に動画の活用をおすすめする理由について紹介していきます。
作業手順書の作成には紙ではなく”動画”の活用が最適
作業手順書は、作業方法の基準を定めたものを指し、作業に対してどのやり方を基準とするのか、標準を定めることによって、作業の所要時間や必要な工数などが明らかになります。一般的に、作成されていますが、わかりやすい作業手順書を作成するためには「動画」の活用がおすすめです。
作業手順書の作成に動画を活用することで以下のようなメリットがあります。
- 複雑な作業を動画わかりやすく伝えることができる
- OK例/NG例を比較して学べる
- 視聴端末があればいつでも反復して学習できる
- 紙と比べて作成工数を圧倒的に短縮できる
- 教育内容を画一化できる
複雑な作業をテキストや画像のみで表現するよりも、動画で伝えた方がカンコツを要する細かい作業の動きが明確に伝わり、従業員ごとのバラつきや作業への認識を標準化できます。
なお、「動画編集の経験がない…」「どのように導入を進めればよいのかわからない」という方に向けて、動画マニュアルの導入を5STEPでまとめたはじめての動画マニュアル作成ガイドを用意しました。興味のある方は以下より資料をご覧ください。
動画マニュアルの活用で生産性向上を実現した事例
実際に動画マニュアルの活用で生産性を向上した好事例として、株式会社アルバックを紹介します。
世界最高水準の真空技術を活かし、真空装置、コンポーネントなど多様な真空技術を幅広い業界に提供する株式会社アルバック。同社では、2拠点で生産活動を展開していたものの、両拠点の生産性に大きな差があることが課題でした。1枚の同じ製品を作成するのに両拠点で74分もの差があったのです。
そこで両拠点のノウハウ共有を促進して全体的な生産効率の向上を目的に動画マニュアル作成ツール「tebiki現場教育」を導入。半年間の集中的な取り組みの結果、作業進捗が悪い工場の制作時間を78分短縮し、生産性を167%改善することに成功しています。
同社の詳しいインタビューは、以下よりご覧ください。
>>人員・労働時間を変更せずに、ボンディング工程の生産性を167%に改善
なお、動画マニュアルの「tebiki現場教育」は、数多くの製造現場で導入されている実績があります。大同工業株式会社以外の事例も知りたい方は、「製造業における動画マニュアル活用事例集」をご覧ください。
次に大同工業株式会社で導入されている「tebiki現場教育」の特徴や機能などについて紹介致します。
動画マニュアルをカンタンに作れる「tebiki現場教育」
「tebiki現場教育」は、動画編集の経験がない方でもかんたんに動画のマニュアルを作成できるツールです。
▼動画マニュアル作成ツール「tebiki」紹介動画▼
紙の標準書では表現することが難しい、動きが伴う作業のカンコツやポイントを視覚的に分かりやすく伝えることができ、標準作業を確立できます。標準作業で活用する場合に有効なtebiki現場教育の機能は以下の通りです。
- 音声を認識して自動での字幕作成
- 大事なポイントを強調する図形挿入
- ワンクリックで100ヶ国以上の言語に自動翻訳
また、標準作業の確立だけではなく、技術伝承や新人作業の効率化などのあらゆる現場課題を解決するための手段として、多くの製造現場で活用が進んでいます。以下で「tebiki現場教育」を3分でわかるサービス資料をご用意しております。詳しく知りたい方はぜひ、ダウンロードしてご覧ください。
【補足】ジャストインタイム(Just In Time)が適している企業の特徴
ジャストインタイムは全ての製造現場で向いている手法ではありません。ここでは、ジャストインタイムが適している企業の特徴について紹介していきます。
サプライチェーンが安定している
ジャストインタイムでは在庫を持たないのが前提にあるため、部品を供給できるサプライチェーンが安定していれば導入を検討しても良いでしょう。仮に、サプライチェーンが安定していない状態で導入してしまうと、生産が止まってしまうなどで在庫切れになる可能性があります。
また、自然災害などの外的な要因によって生産が中断されてしまうリスクが無いかという点も重要です。これらの条件に当てはまっている場合には、供給量の予測がしやすいため、ジャストインタイムの導入で効率的な生産計画を立てて実行できるでしょう。
安定した需要がある
需要が安定していることによって、必要な部品や材料の供給を明確に調整することができます。また、急激な需要の増減がないことにより、生産・供給のバランスが保てるため、需要が安定している企業ではジャストインタイムの導入を検討しても良いでしょう。
逆に製品の生産個数が急激に変動してしまう場合、サプライヤーへの負担がかかってしまうなどのリスクもあります。サプライヤーを含めて双方のメリットになるのがジャストインタイムのあるべき姿なので、いずれかの負担に繋がる場合には導入すべきではありません。
【補足】ジャストインタイム物流とは?
ジャストインタイムは製造業向けに考案された方式ですが、物流業界でも転用されており、これを「ジャストインタイム物流」と呼びます。
ジャストインタイム物流では、「必要なものを、必要なときに、必要な量だけ配送する」物流方式であり、多頻度小口配送や提示配送などを実施して、小売店の欠品を無くすことを目的に幅広く導入されています。
慢性的な人手不足を抱えている物流業界では、労働力不足が著しく低下している傾向です。この現状を改善するために、限られた労働力で、物流を最適化・効率化しなければなりません。
そのため、在庫量の最適化や作業効率の向上、コスト削減などの物流業界における様々な課題を解決につながるジャストインタイム物流に注目が集まっているのです。
まとめ
トヨタ生産方式の柱の1つであるジャストインタイムは、実践することによって、生産におけるあらゆるムダを削減でき、生産リードタイムの短縮が実現します。
余剰在庫の防止や健全なキャッシュフローの実現、リードタイム短縮による機会損出の防止など様々なメリットがある一方で、サプライヤーへの負担や在庫調整が困難などのデメリットもあります。それぞれを理解した上で、本当にジャストインタイム方式を実践すべきか、判断することが重要です。
ジャストインタイムを含めてトヨタ生産方式についてより詳しく学びたい方は、トヨタ自動車出身の講師によるセミナー動画をご覧ください。以下の画像をクリック頂くと無料で視聴できます。