かんたんデジタル現場帳票「tebiki現場分析」を展開する、現場改善ラボ編集部です。
本記事では、QC7つ道具とは何か?基礎知識や覚え方、新QC7つ道具との違いを解説します。また、品質問題の「可視化」につなげるQC7つ道具の使い方を、専門家による解説動画も交えてわかりやすくご紹介します。
>>専門家による「品質問題を見逃さないQC7つ道具の使い方」を動画で見てみる
目次
QC7つ道具とは?覚え方は?
QC7つ道具とは、製造現場で発生している品質問題を改善するために、定量的なデータを用いて分析する7つの手法のことです。
- パレート図
- 特性要因図
- グラフ(層別)
- ヒストグラム
- 散布図
- 管理図
- チェックシート
上記のような図やグラフで定量的なデータを表現し、品質問題を客観的に捉えることで解決の優先順位付けや、改善効果の確認をします。
QC7つ道具は、「サンチェ監督引っ張れそう」という語呂合わせを用いると憶えやすいので、知っておくとよいでしょう。
- サン:散布図
- チェ:チェックシート
- 監 :管理図
- 督 :特性要因図
- 引っ:ヒストグラム
- 張れ:パレート図
- そう:グラフ(層別)
QC7つ道具と新QC7つ道具の違い
QC7つ道具は数値データを、新QC7つ道具は言語データを扱うという違いがあります。言語データとは、「食品に異物が混入してしまった」「バリが発生してしまう」などの数値では表せないデータのことです。
製造現場における品質問題は、数値として拾い上げる前に、課題を体系化する必要があります。複雑に絡み合った要素から問題点をつかむために、言語データを活用するために新QC7つ道具を、数値データを活用するためにQC7つ道具が利用されるのです。
関連記事:新QC7つ道具の使い方は?QC7つ道具との違いや併用方法、覚え方を解説!
【図解】QC7つ道具の手法一覧と使用事例
ここからはQC7つ道具の各手法について、使用事例も交えてわかりやすく解説します。それぞれのテンプレートもご用意していますので、ぜひご活用ください。
より実践的な各手法の使い方や品質改善の考え方を知りたい方は、以下のリンクをクリックして専門家による解説動画もご活用ください。
>>専門家による「品質問題を見逃さないQC7つ道具の使い方」を動画で見てみる
パレート図
パレート図は、問題点を数値化し、大きい順に並べることで優先的に対策すべき項目を可視化する手法です。
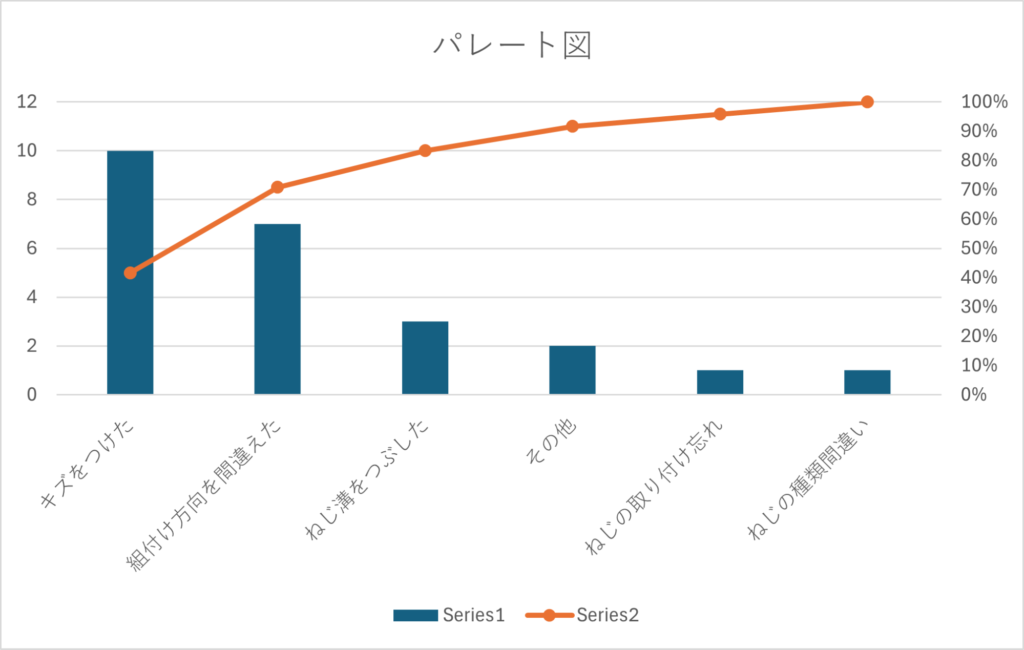
例えば組付け不良の原因を分析すると、全体の約70%が「キズをつけた」と「組付け方向を間違えた」に集中しています。しかし「キズ」の改善が難航する場合、次に多い「ネジ溝をつぶした」と「組付け方向間違い」(計10件)への対策を先行することで、約40%の不良削減が期待できます。
このようにパレート図は、発生件数の多寡だけでなく、改善の難易度やスケジュールを考慮した最適な取り組み順を検討する際にも有用です。
特性要因図
特性要因図は、不具合など望ましくない事象が起きた際、原因を体系的に洗い出すQC手法です。

魚の骨の形状を模した構成からフィッシュボーンチャートとも呼ばれ、4M(Method、Material、Machine、Man)という製造の基本要素を大骨子にして原因を分類します。
さらに「なぜなぜ分析」を組み合わせて原因を深掘りし、仮説を立てて再現実験で検証することで真の要因を特定します。例として金属部品の加工漏れでは、未加工の要因を4Mで列挙し、1つずつ検証する流れとなります。原因が特定できたら再発防止策を講じ、品質向上を図ります。
グラフ(層別)
グラフはパレート図と同様に、数値データを見える化して分かりやすく見るための手法です。
集めたデータを数字で見ていても、増えた、減ったなどの傾向を読み取ることが難しかったり、どれが多い、少ないを把握することは容易ではありません。棒グラフ、円グラフ、折れ線グラフなどを使い分けて、情報を容易に読み取りやすくします。主なグラフの種類として以下の4つが挙げられます。
- 棒グラフ
- 円グラフ
- 折れ線グラフ
- レーダーチャート
棒グラフ
棒グラフでデータを層別し、年度ごとの製品A、B、Cの売上を色分けして表示することで、項目別の売上規模やトレンドを比較しやすくなります。

具体的には、製品Bの売上が伸び、製品Cはほとんど変わらないなどの変化が一目瞭然です。また、棒の高さから全体売上が堅調に増加していることも把握できます。このように、各製品の売れ行きの違いや全体傾向を同時に確認できるため、分析や戦略立案に有効な手段といえます。
円グラフ
円グラフは各項目の比率を直感的に把握でき、時系列で並べると増減や変化も見やすくなります。
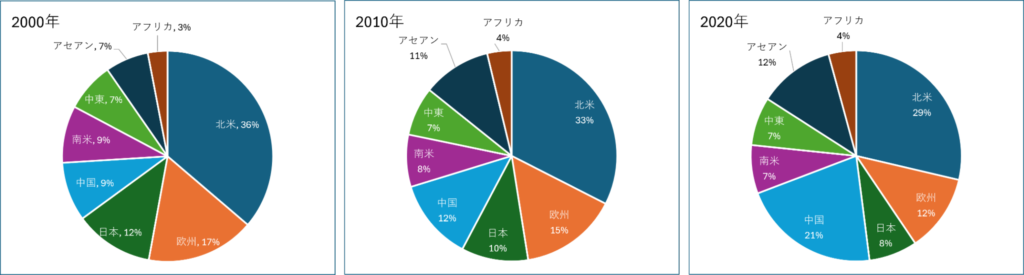
飲食チェーンの地域別売上の例では、中国の比率が大きく伸び、2020年には北米と合わせて全体の半分を占めるまでに拡大しました。こうした可視化により、今後どの地域に注力するか、あるいは縮小すべき地域はどこかといった経営判断につなげられます。
数字だけでは把握しづらい情報を円グラフで整理することで、戦略立案をより的確に進められるのです。
折れ線グラフ
折れ線グラフは、データを時系列で可視化し、増減や安定傾向を把握しやすい手法です。
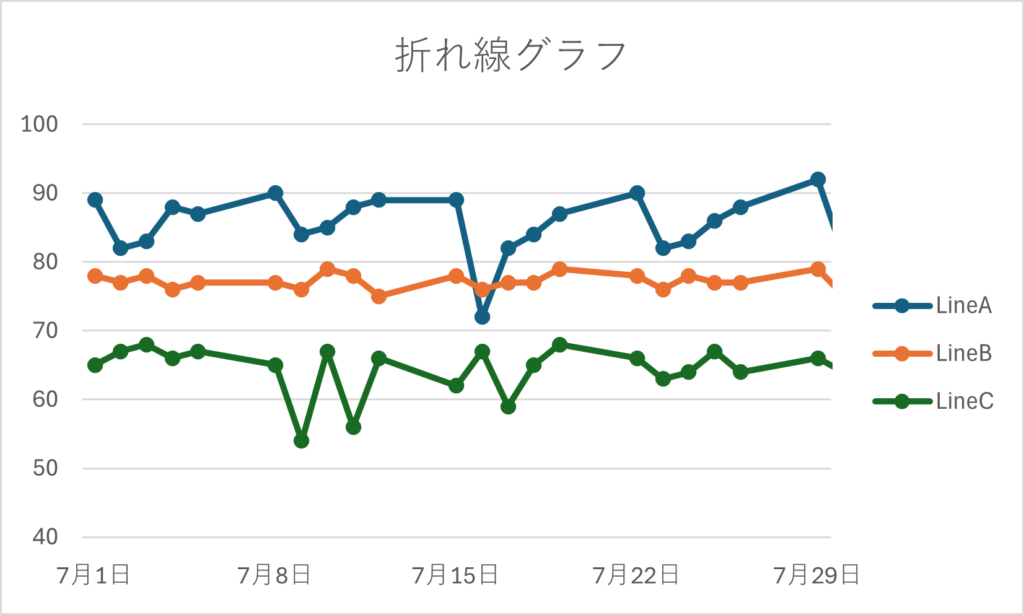
例えば、生産ラインごとに1ヵ月の生産数を追えば、Line Aは週中に落ち込む周期性、Bは安定、Cはランダムかつ低水準といった差異を比較できます。複数の折れ線を重ねることで特徴を見極め、対策立案にも繋げられます。
このように折れ線グラフは時系列変化を直感的に捉えるのに有効で、製造現場からビジネス分析まで幅広く活用されます。
>>専門家による「折れ線グラフの活用方法や事例」の解説も見る
レーダーチャート
レーダーチャートを使えば、複数の評価項目を点数化して強み・弱みを一目で可視化できます。
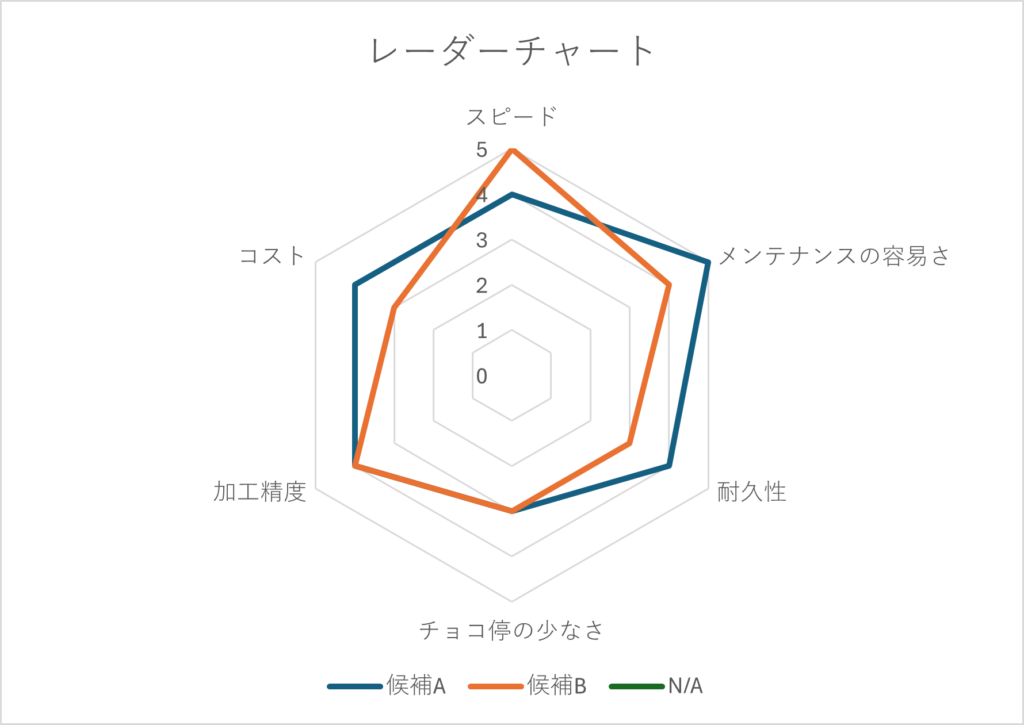
例えば設備比較では、Aはスピードが速い反面、メンテナンスや耐久性に難があることが分かります。一方で、Bは速度面ではAに及ばないものの、他の要素や投資経済性で優れており、総合的に有利な選択肢となる可能性が高いのです。
こうした可視化を通じて、効果的な課題発見や戦略立案につなげられます。その結果、必要に応じた最適な設備選定や改善策の立案をスムーズに行えるのです。
>>専門家による「レーダーチャートの活用方法や事例」の解説も見る
ヒストグラム
ヒストグラムは、集めたデータを区間に分け、その区間ごとの度数を棒グラフで可視化する手法です。
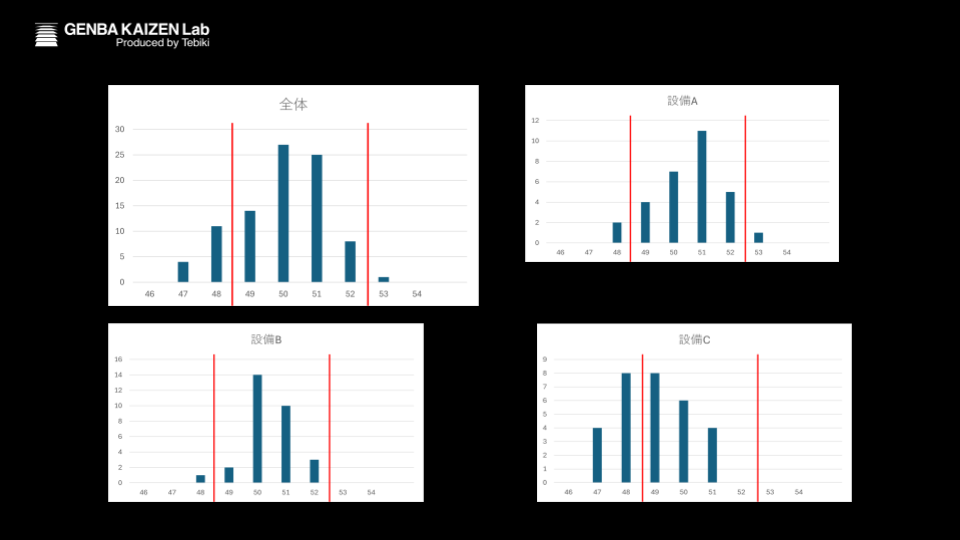
数値のばらつきや分布の中心を把握しやすいため、寸法管理や工程の安定度管理に活用されます。実際に金属部品の加工現場では、寸法検査データをヒストグラム化した結果、分布が規格の中心からずれて左右に偏りがあることが判明しました。
さらに層別して加工機ごとに比較すると、設備Cの加工品に原因が集中しているとわかりました。こうして工程上の問題点を明確にし、有効な対策を立案できるのがヒストグラムの強みです。品質管理の現場で可視化と原因追究を行う際に非常に有用な手法といえます。
>>専門家による「ヒストグラムの活用方法や事例」の解説も見る
散布図
散布図は、2つの事象(横軸と縦軸)の間に相関があるかを可視化するグラフです。
強い相関があればデータが線状に並び、右上がりなら正の相関、右下がりなら負の相関、ランダムに散らばれば無相関と判断できます。
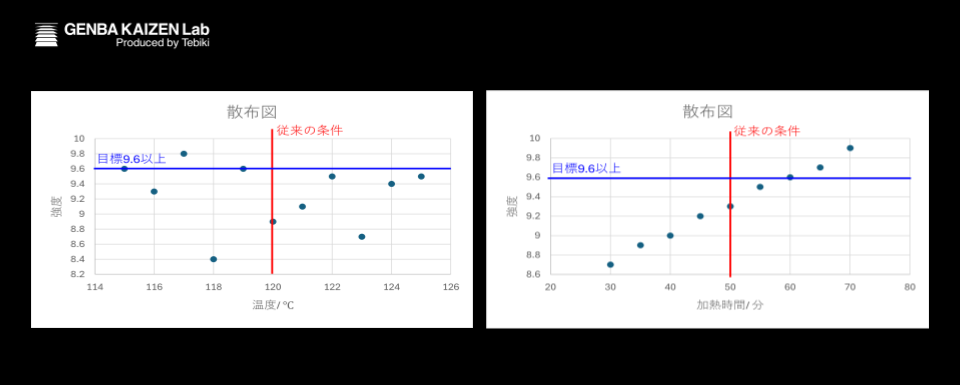
実際にプラスチック製品の強度を高めるため、加熱処理の温度と時間を散布図で調べたところ、温度と強度には関係がない一方で、加熱時間を長くすると強度が上がる正の相関が認められました。そこで従来と同じ温度を保ちつつ加熱時間を1.5倍にすることで、廃棄ロスの原因だったヒビを防ぎ、より強度の高い製品を作ることに成功しています。
このように散布図を用いれば、制御因子を変えることで目的特性がどう変動するかを把握でき、品質向上のための有効な対策を立てやすくなるのです。
管理図
管理図は、製造工程で得られる特性値を定期的に測定・プロットし、その変動が通常範囲内か異常範囲かを見極める品質管理手法です。もっとも広く用いられるXbar-R管理図では、取得したサンプルの平均値(Xbar)と範囲(R)をそれぞれプロットし、管理線(UCL/LCL)を超えると異常として警告を発します。

たとえばゴム製品の硬さを監視していた工場では、8番目のデータが上限管理線を超えたことから原因を究明し、期限切れ硬化剤の使用が発覚しました。翌日には正常に戻ったため、この特定ロットのみを回収し、不良品の出荷を防げたのです。
こうした定期的な計測と管理図による「工程の健康診断」によって、異常を早期に検知して原因を特定し、迅速な対策を講じることが可能になります。
チェックシート
チェックシートは、決められた項目について状態をOK/NGで確認したり、回数を記録するために使用されます。
一定期間情報を集めたら周期性がないかや、NGが頻発している箇所がないかを全体像から把握します。製造現場で使用されているチェックシートは、大きく「点検用チェックシート」と「記録用チェックシート」の2つに分類できます。
点検用チェックシートは、設備の状態を日々・定期的に確認するために使用され、油圧や動作音、揺れの有無などの重要点をもれなく点検できるよう項目が設定されます。過去の故障サイクルから点検頻度を決めるのが特徴です。
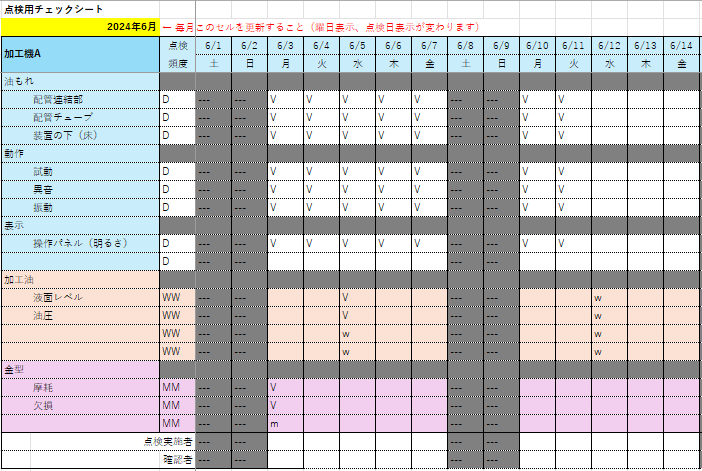
一方で、記録用チェックシートは工程内の不具合発生頻度を記録・集計し、パレート図で優先的に対策すべき問題点を特定する際に役立ちます。さらに安全衛生チェックシートでは、現場の安全確保を最優先とし、定期的に巡回しながらリスクを発見して改善活動につなげます。これらチェックシートの活用により、品質や安全に関する課題を可視化し、一層迅速な対応が可能となります。
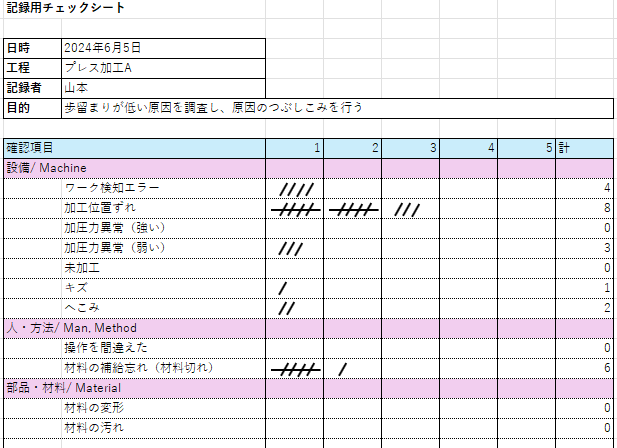
>>専門家による「チェックシートの活用方法や事例」の解説も見る
QC7つ道具はあくまでも手段。品質問題の解決には「現場データの収集」も大切
ここまで、QC7つ道具の各手法について使用事例を交えてご紹介しました。
製造現場の場合、品質トラブルが発生したときに現場にまつわる定量的なデータを集めて、QC7つ道具をはじめとするQC手法による分析を行う流れになります。
しかし、データの可視化や収集を行う段階で、以下のような課題に直面するケースが珍しくありません。
- 紙の記録ではデータが効率的に収集できず、Excelへの転記が負担
- 記入ミスなどにより正しいデータで分析ができない
- データの種類が多く統合(クレンジング)が困難
- Excelやマクロによる分析作業が属人化しやすい
上記の背景から、現場データを効率的に蓄積できず、集計作業に膨大な工数が前段階で発生してしまいます。
また、仮に集計を追えたとしても、誤りがあるデータでQC7つ道具のような分析を行ってしまい、品質問題の真因を明確にできず、QC7つ道具が『使えない』となってしまいます。
このような、現場データの記録や集計、分析にまつわる課題を解決できる手段として「現場帳票のデジタル化」が効果的です。現場改善ラボが製造業に従事する会員の方に行ったアンケート調査では、デジタル化によってデータ抽出や分析、記録が楽になったなど、多くの付帯業務で効果を実感されています。
【「製造現場の生産性を向上するペーパーレスの進め方」より抜粋】
実際、製造日報や点検表などの現場帳票をデジタル化した共栄工業株式会社では、紙やExcelによる運用で、記録や集計に1日2時間割いていた状況から1日1分まで短縮し、分析から改善立案までを早期に行えるような状態を実現しています。
また、かんたんデジタル現場帳票「tebiki現場分析」のような、記録の自動計算機能や自動グラフ化機能を持つツールを活用することで、属人的なQC手法による分析から脱却しつつ、リアルタイムで傾向管理を行うことが可能です。
▼自動グラフ化機能で、傾向管理をリアルタイムで行うイメージ▼
【「現場帳票デジタル化事例:株式会社 日本電気化学工業所」より抜粋】
現場帳票のデジタル化によって、製造現場にまつわるデータ収集を効率化し、管理図やパレート図など、QC7つ道具の分析を自動で行うことができます。
デジタル化する有効性について、より詳しく確認したいという方は、以下のリンクをクリックして参考資料をご覧ください。
【補足】無料ですぐ使える!QC7つ道具のExcelテンプレート
最後に、QC7つ道具のExcelテンプレートをご紹介します。それぞれ無料で、ダウンロード後にすぐ使えるフォーマットとなっています。ぜひこの機会にご活用くださいませ。
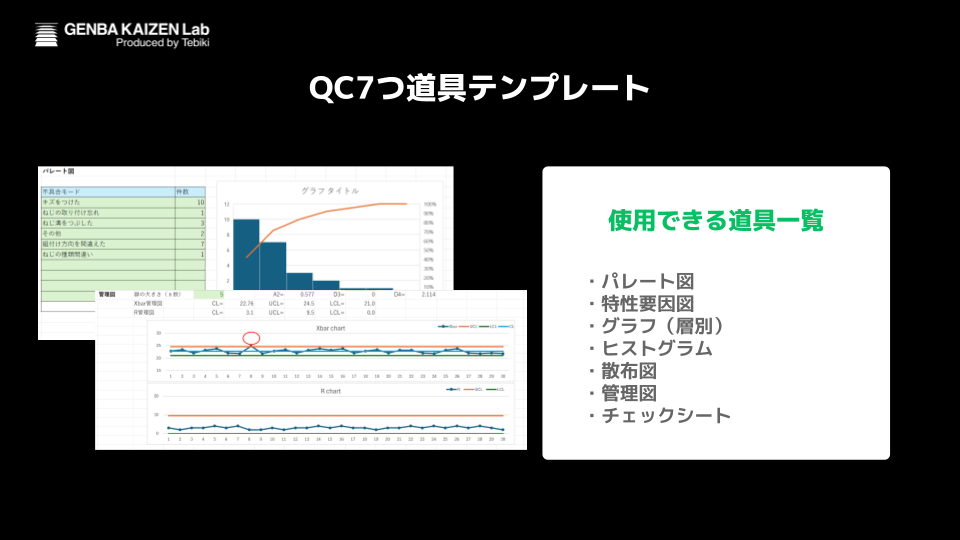
以下のフォームをご入力のうえ送信いただくと、QC7つ道具の各種テンプレートを入手いただけます。
まとめ
ここまで、品質問題を課題を解決に導く改善手法として、QC7つ道具を詳しく解説しました。
QC7つ道具は単体では「使えない」分析に陥るリスクがあり、分析を行うデータ整備も同様に大切です。しかし、現場にまつわるデータを集める現場帳票は紙やExcelで運用されることが多く、誤データの記録や集計工数の負担など、付帯業務が多く分析から改善活動につながりにくいのが現実です。
この課題を解決する手段として「現場帳票のデジタル化」が効果的で、tebiki現場分析であれば管理図やパレート図などのグラフも自動で分析される仕様になっています。
tebiki現場分析の具体的な機能や活用事例、プランなどの概要資料は以下のリンクをクリックしてご覧ください。