製造業では日々、品質をよくするための改善活動が活発に行われています。この改善活動こそが、品質を安定させている要因だと言っても過言ではありません。
しかし、改善活動を成功させるためには再現性ある手法を取らなければいけません。やみくもに活動を行うだけでは、原因の把握や今後の対策なども客観的に示すことができないからです。
そこで問題解決に役立つものとして「QCストーリー」があります。本記事ではQCストーリーの具体的な進め方や成功事例について詳しく解説します。
現場改善ラボでは、トヨタの現場でQC活動を行われてきた古里 和敬氏による『トヨタ式QCストーリーの進め方』を解説した動画を無料で視聴できます。ぜひ以下よりご覧ください。
目次
QCストーリーとは?わかりやすく解説
QCストーリーという言葉を一度は耳にした人も多いかもしれません。製造業における品質改善には欠かせない考え方のため、ここではQCストーリーの概要について紹介します。
そもそもQCとは
QCとは「品質管理」のことを指します。
品質管理は、製造する製品の品質にバラつきが出ないようにするための取り組みです。製造業にとって品質管理は顧客の要求を満たすために大変重要な活動となっています。
品質管理を適切に行うためには、製造現場にまつわるデータを分析し、品質に影響を与えている真の要因を洗い出したうえで、適切な対策を実行する必要があります。このような分析を行うツールとしてQC7つ道具や新QC7つ道具、QCストーリーといったQC手法があります。
QCストーリーをはじめとするQC手法を活用することで、適切な品質管理のもと効果的に品質改善を行うことができます。品質管理の目的や手法など、基礎的な情報は以下の記事でより詳しく解説しています。
関連記事:品質管理の基本を解説!目的や品質保証との違い、主な手法は?
QCストーリーの概要とQCサークルとの関係
QCストーリーとは、品質に関わる問題を解決するための手順や道筋を示したものです。
問題を把握してから解決にいたるまでのプロセスを、QCストーリーに沿った手順で進めることにより品質改善を達成できます。
QCストーリーにおける問題解決までのステップは主に以下の8つです。各ステップの具体的な取り組み内容やポイントは、後ほど【問題解決につなげるQCストーリーの8ステップ】で詳しくご紹介します。
- 職場の問題からテーマを選定する
- 現状把握のための調査/情報収集
- 問題解決につながる目標を設定する
- 活動スケジュールを計画する
- 問題の原因を把握する
- 対策案を検討、実行する
- 対策の効果をチェックする
- 効果が出たものを標準化(歯止め)する
QCストーリーでは「問題」と「課題」の定義を明確に分けているのがポイントです。
問題とは、あるべき姿と現実との差のことを言います。すでに設定している目標と現実との差のことです。一方の課題とは、将来ありたい姿と現実との差のことを言います。将来的に設定しようとしている目標と現実との差のことです。
品質不良のように現段階で起きている問題を取り上げるのか、不良率を〇%減らして品質向上を狙うにあたる課題を取り上げるのか、品質管理で取り組みたいことによって使用すべきQCストーリーの型が変わってきます。まず両者を区別することが大切です。
QCストーリーの型とそれぞれの使い分けは、後ほど【QCストーリーにおける3つの型と使い方】でご紹介します。
また、QCストーリーと似た言葉にQCサークルがあります。
QCサークルとは、数名の小集団で取り組む品質改善活動のことです。QCサークルはQCストーリーの流れをベースに、品質改善の取り組みを進めていくため、QCストーリーとQCサークルは品質改善において切り離せない重要な取り組みだといえます。
QCサークルの基礎知識や進め方は、トヨタ出身の専門家による「形骸化させないトヨタ式QCサークル活動の進め方」の解説動画をこちらからご覧ください。(視聴無料)
QCストーリーのメリットやデメリット
QCストーリーのメリットとして、活動の効率化/メンバー内での情報共有が挙げられます。
QCストーリーは問題解決におけるテーマ選定から標準化までの手順が示されており、やるべきことが明確になっているため、現場の改善活動を効率化させることができます。
また、QCサークルのような複数人で行う活動においても、QCストーリーのように解決までのステップが可視化されていることで、メンバー間での進捗状況の共有が容易になり、現場状況を的確に把握することができます。
一方で、デメリットとしてQCストーリーが形骸化する恐れがある点が挙げられます。QCサークルのような活動の場合に「QCストーリーに沿ってやればいい」と形だけになることもあります。
このデメリットを解消するためには、QCサークルの活性化がカギを握る要素となります。活性化させる進め方については、別記事内「【トヨタ式メソッドも】QCサークル活動を活性化させる進め方とポイント」で解説しています。
QCストーリーにおける3つの型と使い方
QCストーリーには「問題解決型」「施策実行型」「課題達成型」といった3つの型があります。
それぞれの型によって品質改善のアプローチが変わるため、自社の課題はどの型に当てはまっているのかを確認して実行に移しましょう。
現場改善ラボでは、元トヨタの専門家が解説する「QCストーリー3つの型の進め方やポイント」を動画を無料でご覧いただけます。ぜひこの機会にご活用ください。
問題解決型
問題解決型は現在起きている問題を解決して、あるべき姿になることを目的としています。
例えば、商品Aの品質不良が多発しているとすれば、品質不良の元となっている原因を特定して、不良品が出ないような対策を実行していくという流れになっています。
問題解決型の具体的な手順は以下の8ステップになります。
- ステップ1:テーマ選定
- ステップ2:現状把握
- ステップ3:目標の設定
- ステップ4:スケジュール計画
- ステップ5:原因追求
- ステップ6:対策実行
- ステップ7:効果の確認
- ステップ8:標準化
問題解決型でのポイントは、問題を正確に把握した後の原因追求に重きを置いているところです。たとえば「異物混入のクレームを年5件までに抑える」という目標を設定したなら、異物混入の原因を追求することに力を入れます。
施策実行型
施策実行型は、問題解決型のQCストーリーで施策を実行して、再び発生した問題に対して課題を設定して解決していくことを目的としています。したがって、対策を優先することが重視するポイントとなります。施策実行型では3〜5年後の課題に対して考えるものとなっています。
先述の「異物混入のクレームを年5件までに抑える」という例で、「髪の毛の混入が一番多い」という原因が分かっていたとします。対策として「入退室時のローラーがけを重点的に行う」ことが決まっているなら、それを徹底させることをスピーディに行うのです。
課題達成型
課題達成型のQCストーリーでは、今後会社がぶつかりそうな課題に対して対策していくものを担っています。具体的には5年より先の長期的な視野から問題を取り扱います。
課題達成型の具体的な進め方は以下の8ステップになります。
- ステップ1:テーマ選定
- ステップ2:攻めどころの設定
- ステップ3:目標の設定
- ステップ4:スケジュール計画
- ステップ5:方策の立案
- ステップ6:成功シナリオの追及と実施
- ステップ7:効果の確認
- ステップ8:標準化
問題解決型と違う点は、課題達成型では攻めどころを設定した後の方策の立案や成功シナリオに重点を置いていることです。一般的には、まだ実現したことのない高い目標などに関して使用します。たとえば「不良率を〇%にしたい」「生産性を〇%向上させたい」などの課題を設定するのが望ましいです。
トヨタの元エンジニアとして品質管理に従事してきた古里 和敬氏によるQCストーリーの講演によると、トヨタでも「このまま自動車を作り続けていいのだろうか?」という考えから、自動車製造以外にも視野を広げて「人」「モノ」「情報」の移動を可能にするモビリティカンパニーを目指し、その実験として富士山の麓でスマートシティの建設に取り組んでいるとのことです。
問題解決につなげるQCストーリーの8ステップ
では、QCストーリーの具体的な進め方について見ていきましょう。ここでは問題解決型を例にとって、概要や意識すべきポイントについて紹介します。
- 職場の問題からテーマを選定する
- 現状把握のための調査/情報収集
- 問題解決につながる目標を設定する
- 活動スケジュールを計画する
- 問題の原因を把握する
- 対策案を検討、実行する
- 対策の効果をチェックする
- 効果が出たものを標準化(歯止め)する
職場の問題からテーマを選定する
QC活動においてテーマ選択は非常に重要です。なぜなら、製造現場では様々な問題が潜んでおり、適切なテーマを選べるかどうかでその後の成果が大きく変わってしまうからです。
数多くの問題の中から適切なテーマ選定するにはマトリックス図を活用するのが効果的です。マトリックス図では、複数の問題を行に配置し、その問題の重要性や解決した時の効果などの評価項目を列に配置します。縦軸/横軸の交点で最も評価が高い部分が解決すべきテーマとなります。
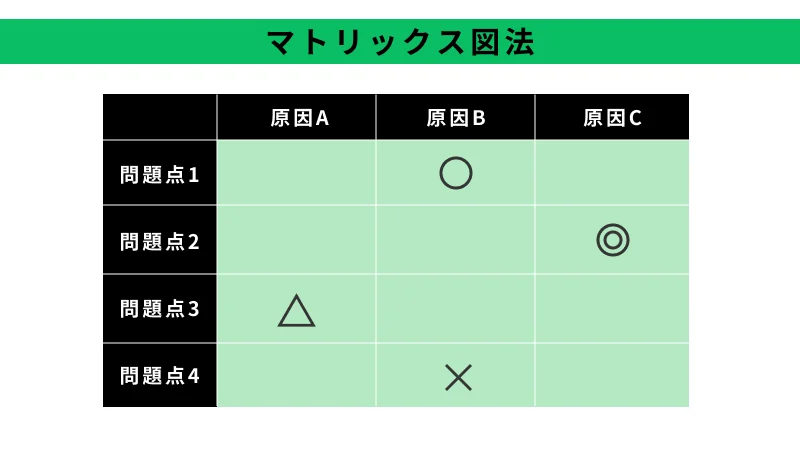
また、良いテーマ選びを行うためには日頃から現場のデータを収集することが大切です。
不良品が発生することによるロス金額や、生産ラインごとの不良率などの数値データはより重要な問題を導き出してくれるものです。金額や不良率の多い項目をテーマとして選定すると効果があります。
品質改善のために『どのようなデータを集めればよいのか?』『収集したデータをどのように分析して改善するのか?』と思われた方は、専門家による「生産品質向上のためのデータ分析と改善活動」の解説動画を以下よりご覧ください。
もし問題をいまひとつ認識できない場合には「7つのムダ」の視点から考えてみるのもよいでしょう。
7つのムダとは、職場に潜在している問題を以下7つの視点から捉えたもので、トヨタ生産方式を実現させるための手法の1つです。現場のあらゆるムダ排除を目的としており、最終的には業務効率化の効果を期待できます。
- 加工のムダ
- 在庫のムダ
- 不良や手直しのムダ
- 手持ちのムダ
- 作りすぎのムダ
- 動作のムダ
- 運搬のムダ
それぞれのムダがどのようなものか?排除方法については、下記の記事で詳しく解説しています。
関連記事:【トヨタ式】7つのムダとは?具体例を交えてムダを解説
現状把握のための調査/情報収集
テーマを選定したら、続いて問題の現状把握です。現状を正しく把握するためには、現場に直接足を運んで、現地・現物・現認という三現主義の観点から物事を見るようにしましょう。
関連記事:三現主義とは?トヨタやホンダの事例と5ゲン主義の意味
このステップにおいてもデータの収集が大事となります。
問題となっている現象がどの程度悪いのかを数値で把握することで、その後の目標を設定しやすくなります。例えば、包装工程における不良率を削減したいのであれば製品/製造日程/機械ごとの不良率を収集することで、現状を正確に把握することができます。
稼働状況や不良率といった数値を把握するためには、製造現場で使用されている帳票を確認することが手段の1つです。
後のステップで原因の追及が出てくるため、この段階では原因を考えることまではせずに、あくまでも問題の程度を把握するまでにとどめておきます。
関連記事:【製造業】帳票の種類は?管理の手間を省くペーパーレス化や電子化を実現するツールを紹介
問題解決につながる目標を設定する
目標は「いつまでに」「どれくらい」といった観点で設定しましょう。具体的な目標を設定することで、活動スケジュールを計画しやすくなります。
例えば「12月までに不良率を101%まで下げる」「7月の異物混入のクレーム件数を月5件にする」などの具体的な数値にまで落としましょう。
目標はギリギリで達成できそうな値に設定しましょう。低い目標だと解決しても効果を得られなくなり、現場の改善に繋がりません。また、現実的に不可能な高すぎる目標では、メンバーの意欲低下に関わります。
したがって、問題解決につながり、なおかつ解決した時に効果を感じられる目標を設定しましょう。
活動スケジュールを計画する
目標設定のステップで定めた期日までに問題解決できるように、このステップでは活動のスケジュールを計画します。
具体的には、QCストーリーの各ステップを誰が/何を/いつまでに/作成するのかを決定します。一般的にはガントチャートを用いて、縦軸に1〜8までの各ステップを置き、横軸を時間軸として担当者の予定を記入します。各ステップの担当者を一元で管理しておくことで、QCストーリーが滞りなく進みます。

問題の原因を把握する
QCストーリーの中で重要なステップが「問題の原因を把握する」ことです。
問題には、それを引き起こす原因が潜んでいます。原因をすぐに見つけることは難しいですが、基本的には以下の2つの手段で問題の原因/真因を明らかにしていきます。
- 4Mの視点で発生している問題を洗い出す
- なぜなぜ分析で原因/真因を把握する
4Mの視点で発生している問題を洗い出す
4Mとは「Man(人間)・Method(手順)・Machine(機械)・Material(材料)」の頭文字で、製造現場を構成する大きな4要素です。
それぞれで意図的に変更したもの、意図せず変化があったものが品質に影響を与える主要因となっており、4Mの観点から考えることで問題の原因を発見しやすくなります。
例えば、生産ラインで不良が発生するなら、その原因は「作業者のミスによるものか」「作業手順がそもそも悪いのか」「機械に不具合があるのか」「材料が良くないのか」と追及していきます。以下の記事では4Mの概要や詳しい進め方について詳細に解説しています。
関連記事:4Mとは?分析方法や変更管理の目的とポイントを解説
なぜなぜ分析で原因/真因を把握する
なぜなぜ分析は、問題が発生した理由を「なぜ?」と繰り返していくことで真の原因を発見する方法です。4Mの視点から問題が発生した原因について「なぜ?」「なぜ?」と問いかけることによって問題の原因を特定することができます。
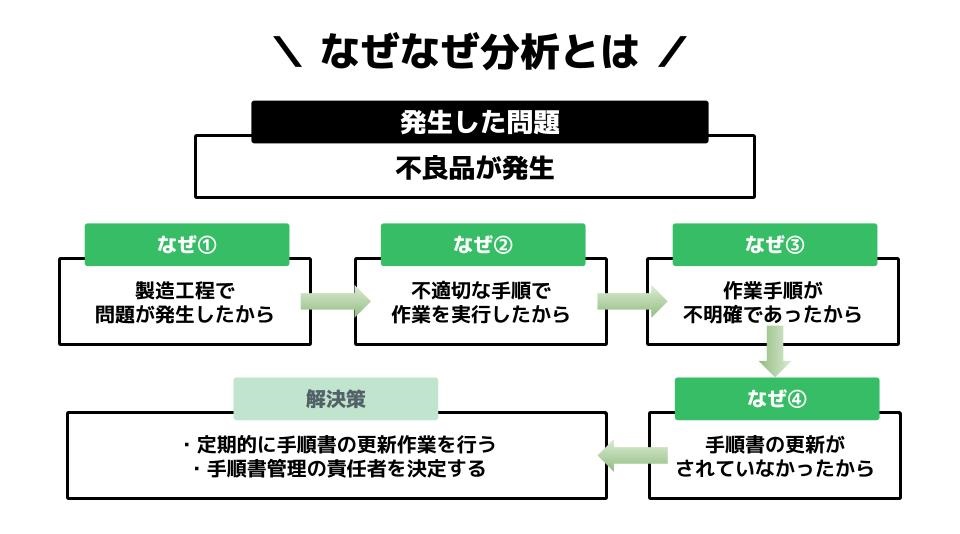
しかしなぜなぜ分析を進めると、結果的に人に対する追及になってしまうという声を聞くケースが度々あります。その場合、深掘りが足りないことが想定され、適切な対策を講じることができず問題が再発する恐れがあります。
したがって、なぜなぜ分析で深掘りをする際には人を追及するのではなく、作業手順や工程といった仕組みに不備がなかったか?という視点で取り組むことがポイントです。
とはいえ『なぜなぜ分析は難しい…』と感じる方も多いでしょう。
現場改善ラボではなぜなぜ分析に関する解説記事だけでなく、トヨタの訓練指導者としてなぜなぜ分析を教えていた専門家による「トヨタ式なぜなぜ分析」に関する講演を無料でご覧いただけます。ぜひこの機会に、正しいなぜなぜ分析の手法を以下よりご覧ください。
対策案を検討、実行する
原因を見出したら、次にやるべきことは対策案を検討し、実行に移すことです。対策案を考える時に注意することは、現場や作業者の負担が増えない対策にすることです。
例えば、製品の検査をする際にチェック漏れによって不良品が発生したとします。この時に、真っ先に考えられる対策案は、ダブルチェックを導入することです。
しかし、ダブルチェックなどは追加型の改善とも言われるように、作業を止めてチェックしなければならないため現場の負担を増やしかねません。
そこで、現場の負担を増やさない対策案として以下の「ECRSの4原則」を元に考えることが効果的です。
- 排除(Eliminate):作業や手順をやめる
- 結合(Combine):作業と確認を同時にするなど業務をまとめる
- 交換(Rearrange):工程や手順を入れ替えて効率化する
- 簡素化(Simplify):作業を単純化・簡素化させる
検査工程でチェック漏れが発生したという問題であれば、製造と同時に確認する作業を組み込むことで、現場の負担をかけることなくチェック漏れの発生を減らすことができます。
ECRSの4原則に関する具体的な活用方法や成功事例については、下記の記事で詳細に解説しています。
関連記事:ECRSの4原則とは?製造業での具体的な改善方法やメリット
対策の効果をチェックする
対策の効果を確認するステップでは、対策前と同じ条件でデータを取りましょう。例えば、1週間のデータであれば効果の確認も同じ期間にすることで、正しく効果を測定できます。
効果を測定する際は、不良品率〇〇%削減といった定量的な数値で表した方が、達成度合いが客観的に分かります。結果が可視化されることで、品質改善における従業員のモチベーションアップにも繋がるため、定量的な視点から考えることは大切です。
また、期待した効果が得られない場合は、PDCAサイクルを回すように再び計画を立てて原因を取り除くための対策を立てていきます。対策は大掛かりなものよりも、小さくてもよいのでスピーディに実行するようにしましょう。
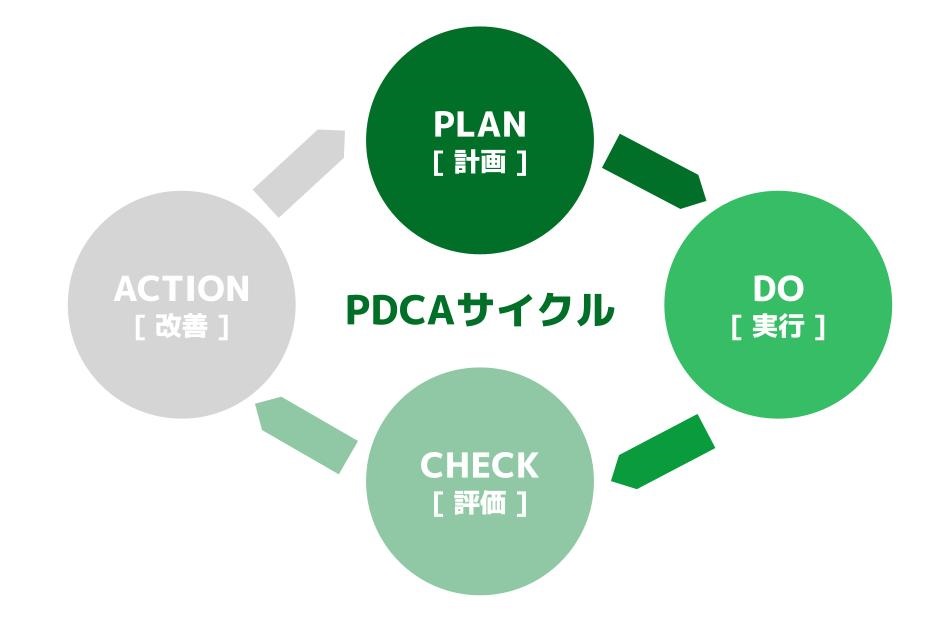
効果が出たものを標準化する
効果が出たものは、職場に定着させるために標準化を図ります。一度改善できたものでも継続的に維持できなければ、本当の改善とはなりません。
そのため「誰がやっても」「いつまで経っても」という視点から改善策を標準化させることが重要となります。改善策を標準化させるには、QC工程表やSOPなどの作業手順書を整備して作業者に徹底させることが必要不可欠です。
トヨタの現場で品質保証/品質管理に従事していた古里 和敬氏によるQCストーリーの講演では、従業員に伝わりやすい作業手順書を作成する際のコツとして「やってはいけない作業は理由もいれて記載する」「手元の写真を入れてイメージを持たせやすくする」ことが重要であると紹介していました。
誰にでも伝わりやすい作業手順書を作成することで、運用が形骸化せず現場で使用され、標準が定着しやすくなることが期待できます。作業のカンコツを分かりやすく伝える作業手順書はどのように作成すればよいか?そのポイントについては、以下の参考資料で図解も交えて詳しくご紹介しています。
QCストーリーの成功には標準化がカギ
「効果が出たものを標準化する」で紹介したように、QCストーリーに沿って品質改善を実現するためには標準化がカギを握っています。一方で『製造現場で従来の手法だと標準化が進みにくい…』とお悩みを抱える方もいらっしゃるのではないでしょうか?
一般的にマニュアルや作業手順書の整備、OJTや座学による教育で標準化を進めるケースが多いですが、従業員に対して正しく理解されず問題が起きてしまうという現場を、私たちは数多く見てきました。
ここからは、製造現場で標準化が進みにくい理由と、標準化に関するお悩みを解決する手段について事例を交えながらご紹介します。
標準化が進みにくい理由
製造現場での標準化が進みにくい理由としては、主に以下の3つが挙げられます。
- 人によって教え方が異なり、教育する内容がバラバラになっている
- 標準化したい業務ノウハウを言語化できなくて伝えられない
- 画像や文字ベースの手順書で伝えているが動作が分かりにくい
製造現場ではOJTや紙の手順書で標準化を伝えることが多いと思います。しかし、OJTのような口頭による教育では、人によって教え方や内容が異なりやすく、結果的に正しく標準が伝わらないことで作業不遵守のようなヒューマンエラーによって品質不良が発生してしまいます。
また、人によって教え方が異なれば、技能やノウハウは必然的に「個々の従業員の経験則として蓄積」されていきます。つまり「暗黙知の蓄積」と「ベテラン社員への依存」という2つの問題が深刻化=属人化するのです。
このように、現場教育がうまくいかない製造業にはいくつかの要因が存在しますが、その要因をすべてまとめたPDF資料「新人教育に失敗する製造現場に潜む3つの構造的要因と新しい教育アプローチ」もあわせてご覧いただくと、より理解が深まると思います。
また画像や文字ベースの手順書では、現場での細かい動作や作業のタイミングなど三次元的な動きが伝わりづらく、誤った理解からヒューマンエラーに繋がってしまいます。
そのため、標準化を進めるには作業手順の可視化と、それを十分に伝えるための仕組みが重要です。そこで製造現場で標準を伝えるための手段として、業界内で注目を集めているのが「動画マニュアル」です。
なぜ標準化に動画マニュアルが効果的なのか?次章では実際の事例も交えて詳しくご紹介します。
標準化を実現する効果的な手段は「動画マニュアル」
現場の標準化を実現するには動画マニュアルの活用が効果的です。
動画マニュアルは現場での標準作業を撮影して、マニュアルに落とし込むことで、現場での複雑な動きを可視化して伝えることができるため、正しい作業手順を理解しやすいです。また、1つの動画を共通の正しい教材として教育に使用できます。
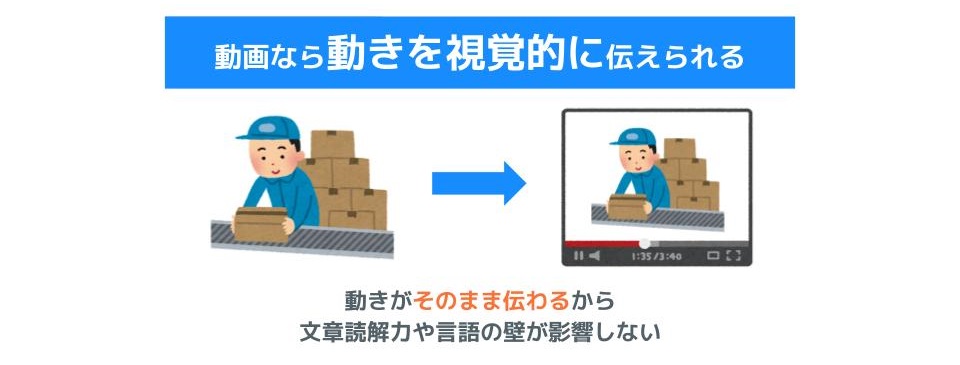
OJTのような、教育者によるバラつきがなくなることで、教育内容の統一化や、繰り返し見返すことで理解度の向上も期待できます。
動画マニュアルの作成はYouTubeなどの内製化や有料ツールを活用した作成など様々な方法がありますが、特にオススメな動画マニュアルサービスとしてtebikiをご紹介します。
現場教育システムtebikiは、製造業を中心とした現場産業で多く活用されている動画を軸とした教育システムです。
tebikiには以下のような特徴があり、製造現場の標準化を助ける機能も多数用意しています。
- 動画の撮影/編集はスマートフォン/タブレットでできる
- 撮影した動画の音声は自動で文字起こしされて字幕に
- シンプルな編集画面で作業を熟知する作業者自身でマニュアル作成が可能
- 字幕は100を超える言語に自動翻訳が可能で外国人教育にも活用できる
- 一部言語の字幕読み上げに対応し母国語で学べる環境構築が可能
- 閲覧状況/テスト機能を活用し従業員の理解度を可視化
- スキルマップ機能で従業員のスキル取得状況を可視化
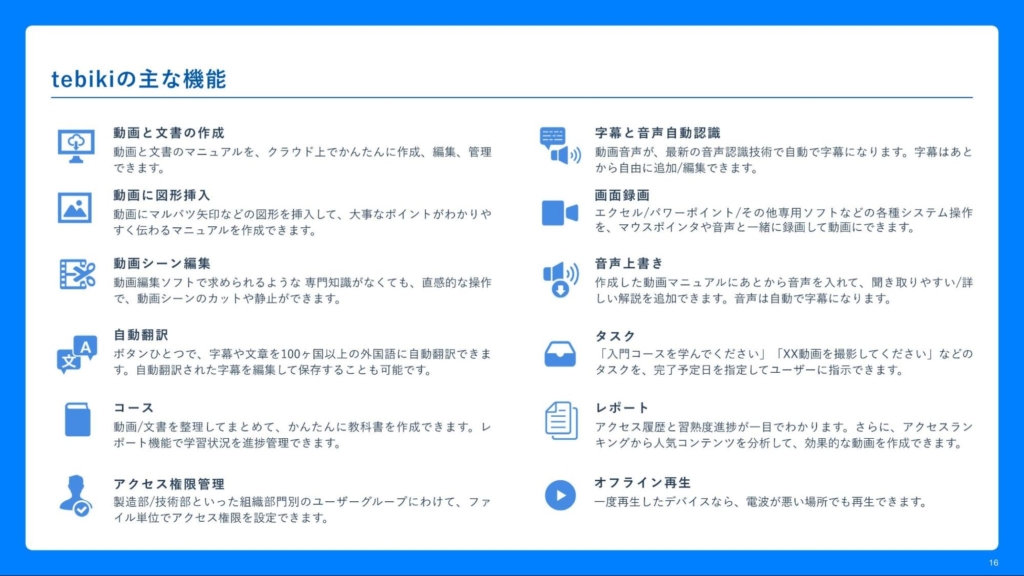
『より具体的に機能を知りたい』という方は、tebikiに関するサービス資料をご用意しています。以下のバナーよりダウンロードしてご覧ください。
動画マニュアルによる標準化の成功事例
動画マニュアルtebikiを活用して現場教育の標準化を推進した事例として、今回は工作機械、遠心力鋳造管、産業機械の製造を行っている新日本工機株式会社の事例をご紹介します。
▼インタビュー動画:新日本工機株式会社▼
新日本工機は売上全体の9割を工作機械が占めており、重工業・一般機械業界、航空機業界、自動車業界の3つの業界においてお客様のニーズに応えた機械を提供しています。新日本工機では現場で『標準化プロジェクト』を立ち上げ、作業手順書の整備など様々な取り組みを行っていましたが、紙の作業手順書に限界を感じていました。
新日本工機はtebikiを導入し、作業標準化や作業品質の安定化を実現させました。また、ベテラン頼りであった作業も動画マニュアルで可視化することで、技術伝承にも成功しています。
tebiki導入前に抱えていた課題 | tebiki導入後の効果 |
作業手順が標準化されておらず、作業者や管理者によって認識が異なっていた 作業要領書を整備しても、文字ベースの情報で内容が正確に理解されず認識がバラついていた 分かりにくい要領書が読まれず作業品質のバラつきが生じ、作業の後戻りが発生していた 海外工場向けのマニュアル翻訳に膨大な時間がかかっていた | 要素作業の解説と注意点の解説を動画化することで、動きが伴う内容が視覚的に伝えられるようになった ベテランに依存していた作業も、動画によってノウハウを可視化でき技術伝承も進むようになった 紙マニュアルでは伝わらなかった標準化された作業を正確かつ簡単に伝わるようになり、業務効率化を実現 マニュアル翻訳がボタン一つでできるため、海外工場向けの手順書作成工数が0になった |
新日本工機株式会社ではtebikiを活用し、作業標準書の整備だけではなく、安全作業や保守/点検作業など多岐に渡る作業をマニュアル化しており、効果的かつ効率的なマニュアル整備を実現しています。
また、紙マニュアルでは伝わりづらかった細かい動きも動画に置き換えたことで標準化された作業を正確かつ簡単に伝えることができるようになり、作業品質の安定化にも繋がっています。
新日本工機株式会社のより詳細な動画マニュアル活用事例は、以下のインタビュー記事も併せてご覧ください。
インタビュー記事:人が育つ環境づくりとして動画マニュアルtebikiを活用。技術の蓄積と作業品質の安定を実現。
こちらの事例のように、動画マニュアルは製造現場での活用が拡がりつつある教育手法の1つです。他の事例や効果など詳しく知りたいという方は、以下の動画マニュアル活用事例集もご覧ください。
QCストーリーを進めるうえで役立つQC手法
ここまでQCストーリーの3つの型や進め方、効果的に標準化を進める手段まで網羅的に解説してきました。最後にQCストーリーを進めるうえで役立つQC手法について以下の2つをご紹介します。
- QC7つ道具
- 新QC7つ道具
QC7つ道具
「問題解決につなげるQCストーリーの8ステップ」で解説した通り、QCストーリーを進める上では問題の原因を把握することが重要であり、その際に役立つのがQC7つ道具です。
QC7つ道具とは製造現場で集められるデータを以下7つの道具を使い分けながら分析することで、問題を見える化する手法です。
- パレート図
- 特性要因図
- グラフ
- ヒストグラム
- 散布図
- 管理図
- チェックシート
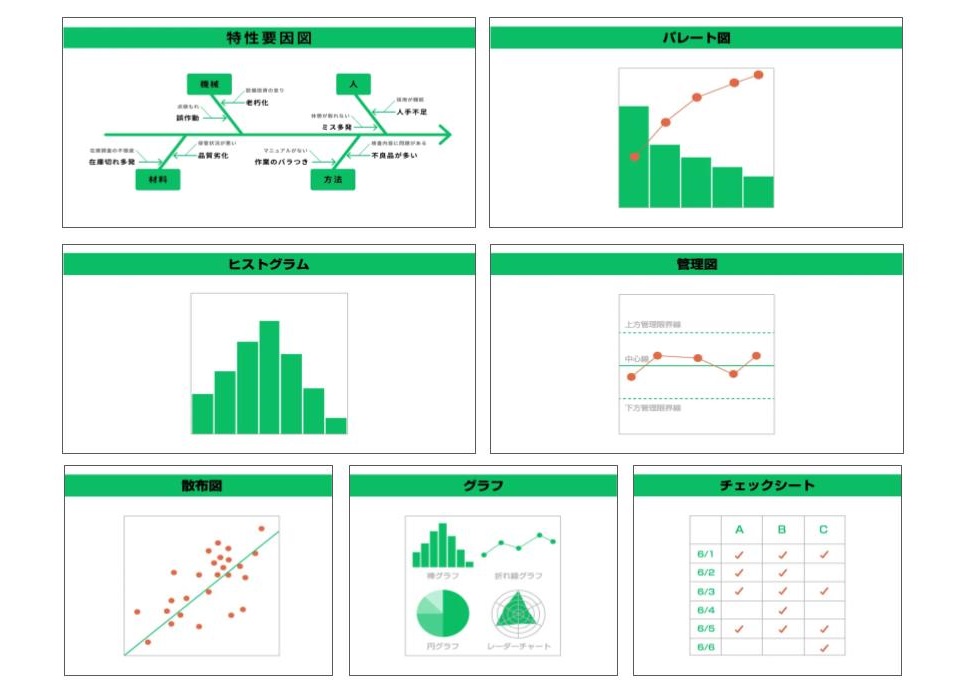
QC7つ道具それぞれの解説や使用例については、こちらの解説記事か専門家による『品質問題の原因を見つける正しいQC7つ道具の使い方』に関する無料の解説動画を以下よりご覧ください。
新QC7つ道具
新QC7つ道具も製造現場における問題の原因を把握することを目的としていますが、「異物が混入した」「バリが発生した」などの数値では表せないデータから分析するという点にQC7つ道具との違いがあります。
また、それぞれの使い分け方として、QC7つ道具は実際に問題を解決していく際に活用しますが、新QC7つ道具は現場の状況を整理するために用いられます。下記は新QC7つ道具の手法です。
- 親和図法
- 連関図法
- 系統図法
- アローダイアグラム
- マトリックス図法
- マトリックスデータ解析法
- PDPC法
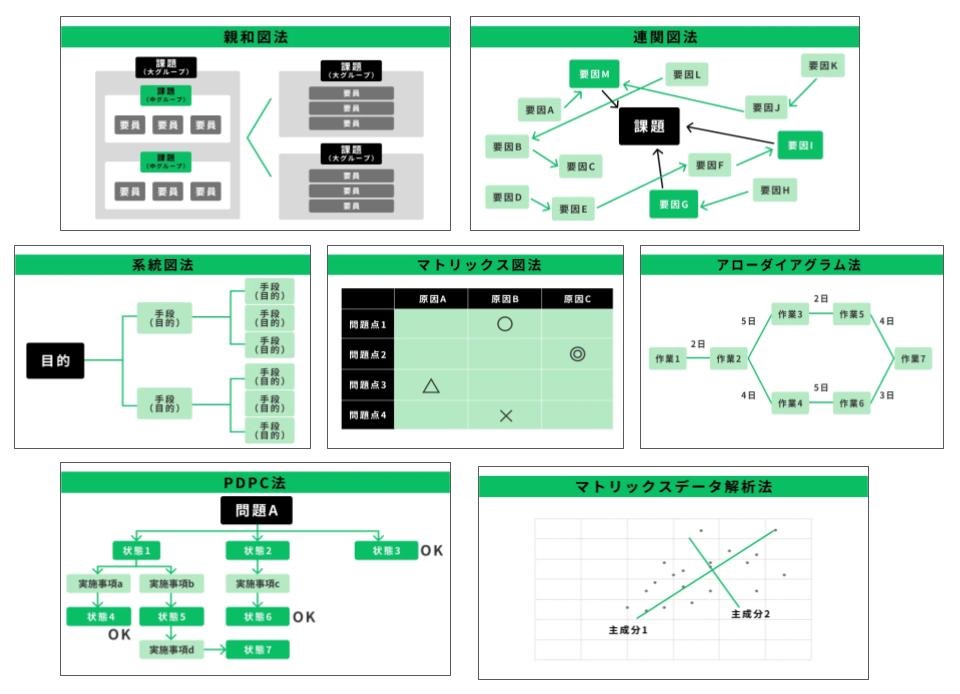
新QC7つ道具の各手法に関する解説や使い方については、以下の記事で図解を用いながら分かりやすく解説しています。
関連記事:【図解あり】新QC七つ道具とは?QC七つ道具との違い、各手法をわかりやすく解説!
まとめ
品質管理で欠かせないQCストーリーの各ステップについて解説してきました。
QCストーリーとは、品質に関わる問題を解決するための手順や道筋を示したものであり、QCストーリーに沿った手順で進めることによって品質改善を達成できます。
また、QCストーリーには「問題解決型」「施策実行型」「課題達成型」の3つの型があり、よく用いられる問題解決型の具体的な手順は以下の通りだと紹介しました。
ステップ1:テーマ選定
ステップ2:現状把握
ステップ3:目標の設定
ステップ4:スケジュール計画
ステップ5:原因追求
ステップ6:対策実行
ステップ7:効果の確認
ステップ8:標準化
特にQCストーリーの成功にはステップ8の標準化が重要であり、標準化には作業手順書を整備して作業者に徹底させることが必要不可欠です。
QCストーリーに沿って改善を実施することで、行き当たりばったりの改善活動をするよりも改善の成功確率を上げることができます。各ステップでの注意点を念頭に置いて、QC7つ道具などを駆使して現場を改善に導きましょう。
現場改善ラボでは、トヨタの現場で品質管理に従事してきた古里和敬氏による、トヨタ式なぜなぜ分析から紐解く正しいQCストーリーの進め方に関する解説動画を無料で視聴できます。ぜひ併せてご覧ください。