製造現場において、労働者が安全に働く環境を整えることは事業者の責務だといえます。現場の労働災害を防ぐ手法として、「リスクアセスメント」の実施が効果的であり、企業の努力義務としても定められています。製造業では取り扱う製品によって発生しうる労働災害も異なるため、現場独自でリスクを発見し除去/低減する活動が重要です。
本記事ではリスクアセスメントの意味や必要性、進め方や役立つツールについて解説します。
また本記事ではリスクアセスメントの具体的な手法やコツとして、元労働基準監督署署長が解説するセミナー動画「現場のキケンを見極めるリスクアセスメント術」の内容も抜粋してご紹介します。セミナー動画については以下の画像から無料でご視聴いただけますので、是非ご覧ください。
目次
リスクアセスメントとは?意味を簡単に紹介
リスクアセスメントとは、現場に潜む危険性や有害性を調査し、低減/除去するまでの一連の手法のことです。
たとえ重大な事故や労働災害が発生していなくとも、常日頃からさまざまな場所にリスクやヒヤリハットは必ず潜んでいます。それらのリスクをあらかじめ低減/除去することで、現場で働く作業員の安全を守ることにつながります。
リスクアセスメントの目的とは?
リスクアセスメントの目的
リスクアセスメントの目的は、事業所の全員が職場に潜むリスクやその対策に関する実情を把握し、災害に至るリスクを事前に取り除くことで労働災害が発生しないような職場にすることです。
リスクアセスメントに取り組むことによって、以下のような効果が期待できます。
- 職場に潜むリスクが明確になる
- 潜むリスクを事業者/労働者全員で共有できる
- 必要な安全対策について合理的に優先順位を決められる
- 残留リスクに対して「遵守事項」の理由が明確になる
- 職場全員の参加によって「危険」に対する感受性が高まる
リスクアセスメントを効果的に行うポイントは、事業者だけでなく労働者も含めた職場全員で取り組むことです。事業者や上層部のみならず全員がリスクアセスメントに参加することで、職場全体の危険に対する意識向上につながります。
また、これまでの労働災害防止策は、災害発生後に原因を調査し再発を防止することを重視していたため、新たに発生する恐れのある潜在的なリスクは放置される傾向にありました。
しかし、技術の発展によって機械や化学物質の導入など取り扱うものが増えているため、事業場に潜むリスクはますます多様化してきています。そこで、法律の有無に関わらず潜在的なリスクを見つけ、対策を講じるリスクアセスメントが求められているといえます。
法令におけるリスクアセスメントの位置づけ
リスクアセスメントは法律により、企業が取り組むべき問題だとされています。実際に、労働安全衛生法の第28条の2項によって、各事業所にリスクアセスメントの実施が努力義務として求められています。
具体的には「建設物や設備、原材料、ガス、蒸気、粉じん、または作業行動その他業務に起因する危険性又は有害性等労働者の就業に係る全てのもの」が対象です。
また、同条項内では「化学物質等による危険性又は有害性等の調査等に関する指針」(平成18年危険性又は有害性等の調査に関する指針公示第2号)や「機械の包括的な安全基準に関する指針」についても言及されています。
【参照元:危険性又は有害性等の調査等に関する指針】
労働災害の統計
令和4年度(2022年)の業種別労働災害発生件数は、製造業が26,694件と前年比で約+1.0%増えています。労働災害を発生させないためにも、リスクアセスメントは非常に重要な作業だといえます。
▼ 令和4年 業種別労働災害発生状況 ▼
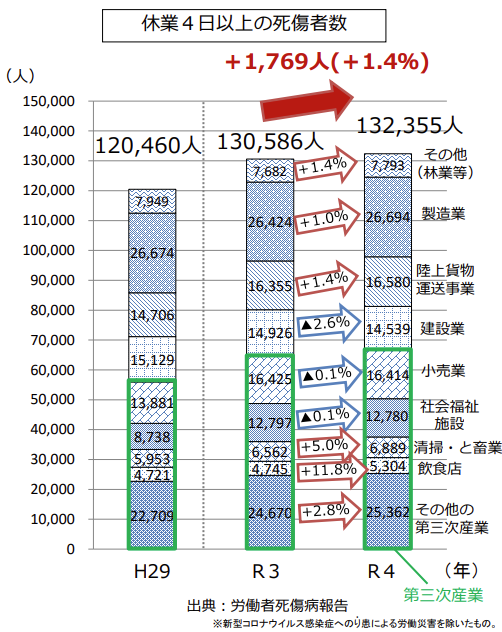
【厚生労働省『令和4年 労働災害発生状況』より引用】
リスクアセスメントがもたらす4つの効果
リスクアセスメントがもたらす効果として、以下の4つが期待できます。
- 事故が発生するリスクを減らし、労働災害を防ぐ
- 職場に潜んでいるリスクを共有し対策できる
- 防災に対する取り組みの方針を明確にできる
- 現場の安全意識が向上する
事故が発生するリスクを減らし、労働災害を防ぐ
リスクアセスメントを行うことで事故の発生確率を低減でき、従業員の安全を確保できます。
例えば、粉塵作業のリスクとして大量の粉塵を吸ってしまうと、じん肺を発症する恐れがあります。ここで、リスクアセスメントとして局所排気装置の設置や防塵マスクを着用することで、じん肺が発症するリスクを低減でき、健康被害を抑えることが期待できます。
職場に潜んでいるリスクを共有し対策できる
リスクアセスメントを行うことで、他の作業者にも作業リスクを可視化して共有し、対策に活かすことが可能です。
作業リスクを抽出し対策を決定した後は、関係部署に承認をもらうために共有シートなどを作成し共有するとよいでしょう。これにより、どの作業にどんなリスクが潜んでいるのかを異なる部署間でも把握し、具体的な対策につなげることができます。
防災に対する取り組みの方針を明確にできる
リスクアセスメントを行うことで、リスク対応策の優先順位がつけられます。全てのリスクに対応することは、時間・コスト・労力が必要であり現実的ではありません。
そのため、まずは現場と従業員の安全を確保するために危険なリスクを洗い出したうえで最優先に取り組みましょう。
現場の安全意識が向上する
リスクアセスメントに参加させることで、従業員の安全意識を高めることが期待できます。従業員に対し、作業に潜んでいるリスクはあるか、対応策をどうするのか、それぞれ役割を与えて取り組みをさせることで主体的に危険箇所を無くすようになり、安全意識の高い職場になるでしょう。
労働災害を減らすには、従業員が安全意識を持って業務を遂行することが重要です。一方で、適切な安全教育が不足することで安全意識は形骸化し、事故やトラブルのリスクが高まります。
現場改善ラボでは労働安全コンサルタントによる「安全意識を形骸化させない安全教育の進め方」について解説した動画を以下にご用意しておりますので、併せてご覧ください。
分析方法も紹介!リスクアセスメントの手法と進め方
まず、リスクアセスメントの進め方について解説します。現場に潜む危険性や有害性の特定から、対策の実施、効果の確認まで以下のような4つのステップで進めます。
- 労働災害につながる危険性/有害性を特定する
- 特定したリスクの重大性/発生頻度を分析して対応優先度を決める
- 優先度が高いリスクから対策を進める
- 対策した結果の記録/効果を確認する
より具体的で実践的なリスクアセスメントの方法を知りたい方は、元労基署署長が解説する以下の解説動画も併せてご活用ください。
労働災害につながる危険性/有害性を特定する
リスクアセスメントを進める際は、まず労働災害につながる危険性/有害性を特定します。
労働災害につながる危険性/有害性を特定するには、現場内に潜むリスクを見落とさずに列挙することが大切です。そのため、リスクを洗い出す際は現場の熟練者をチームに加えて話し合いを行うなど、実際に現場でリスクに触れる可能性がある人も交えて活動しましょう。
また、現場に潜む危険性/有害性を特定するには、「災害までのプロセス」を予測します。災害までのプロセスを予測する際は、「〜するとき/〜したので」+「〜になる」または「〜なので」+「〜する」という形で書き出しましょう。
そして、現場に潜むリスクを特定するには、職場の環境や業務の流れなどを把握する必要があります。リスクアセスメントに取り組む際は、以下のような情報を集めておくとよいでしょう。
- 作業標準書などのマニュアル
- 機械設備のレイアウト
- ヒヤリハットや過去の労働災害記録
- 安全施工サイクル
- 前年度の労働災害発生状況
特に、重大な事故の前兆であるヒヤリハットには労働災害が発生する原因や対策のヒントが詰まっています。そのため、日頃からヒヤリハット報告書の書き方や内容の粒度については、現場で標準化しておくことが大切です。
ヒヤリハット報告書の項目例や書き方のポイントは、以下の記事で詳しく解説しているので併せてご覧ください。
関連記事:ヒヤリハットとは?報告書の例文や業界別の事例、対処法について紹介
特定したリスクの重大性/発生頻度を分析する
次に特定したリスクの重大性/発生頻度を分析します。機械設備や作業内容などによって、発生しうる災害の重大性や発生頻度はさまざまです。
そのため、挙がった事例を手当たり次第に対策するのではなく、重大性や発生頻度の高いものから対策する必要があります。特定したリスクは、以下のように「重大性」「発生頻度」のそれぞれに点数をつける形で分析しましょう。
【重大性】
- 3:極めて重大(死亡/永久的損傷/休業災害 1ヶ月以上/腕や足の切断/重症中毒)
- 2:重大(休業災害 1ヶ月未満)
- 1:軽微(不休災害やかすり傷)
【発生頻度】
- 3:発生が確実/可能性が極めて高い
- 2:発生する可能性がある
- 1:発生する可能性はほとんどない
上記のように、「重大性」「発生頻度」をそれぞれ評価する際は、できるだけ複数人で実施するとよいでしょう。多様な観点がある方が、1人で行う場合よりも適切に分析ができるからです。
また、分析内容にばらつきが生じた場合でも無理やり「こうであるべき」と決めつけてはいけません。平均値や多数決で決めずに、メンバー全員が合意した分析結果を出しましょう。
リスクの見積もり方法は下記2点の方法で行うことが一般的です。
- マトリックス式
- 加算式
マトリックス式
マトリックス式は、「重篤度」と「発生の可能性」の組み合わせからリスクを見積もる手法です。3段階による評価の場合、以下のような図で算出することができます。
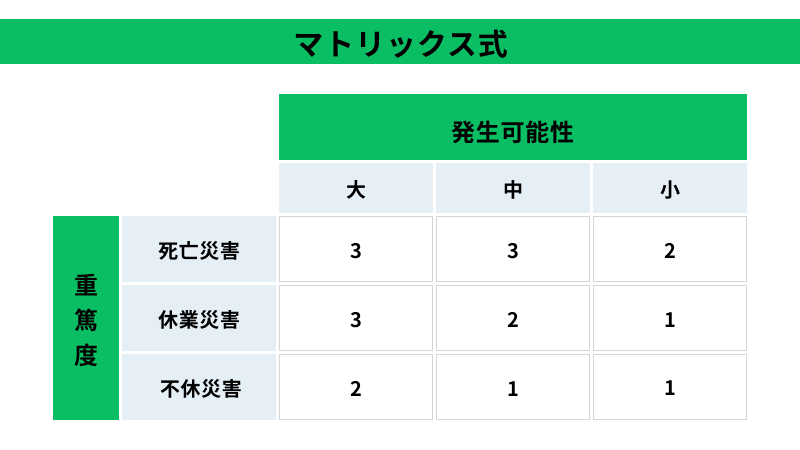
リスクについてより細分化する場合は、自社独自の基準を作成することもおすすめです。
加算式
加算式は「重篤度」、「発生の可能性」、「危険性又は有害性に近づく頻度」を算出し、加算した合計点数で対策の必要性を判断する方法です。
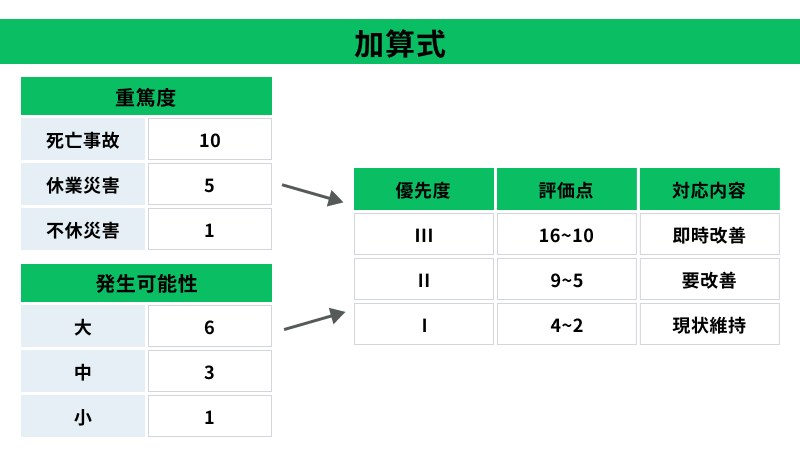
加算式に置けるリスクの見積もり例としては、以下のような分類が考えられます。
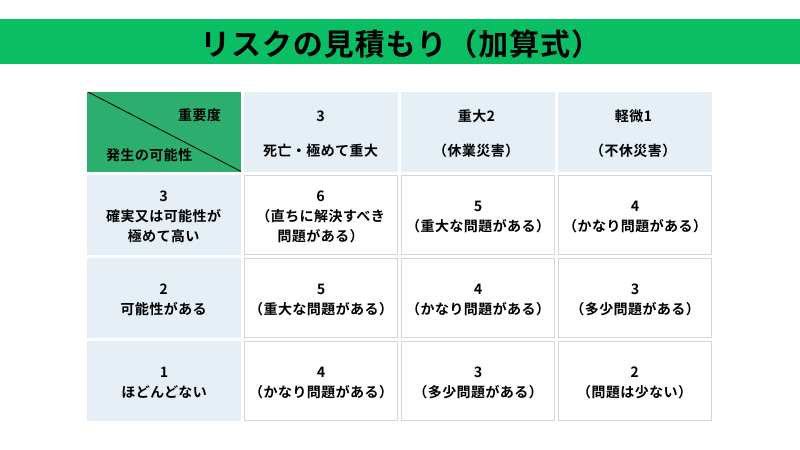
マトリックス式と同様に、自社のルール基準を更に細分化して作成してみることもリスク洗い出しの精度を高めることに役立つでしょう。
分析した内容からリスクの対応優先度を決定し対策を進める
特定したリスクの重大性/発生頻度を分析したのちに、その内容からリスクの対応優先度を決めます。上記で分析した「重大性」と「発生頻度」の点数を加算した数字がその事象のリスクレベルです。
例として、加算した数字を以下に当てはめた時に点数が高いほど対応優先度が高いリスクとして認定されます。
【対応優先度(=重要度+発生頻度)】
- 6:直ちに解決すべき問題である
- 5:重大な問題である
- 4:非常に問題である
- 3:多少問題である
- 2:問題は少ない
それぞれの事象のリスクレベルを明らかにしたのちに、優先順位の高い事象からリスクの低減/除去に進みましょう。
リスク低減措置の種類と優先順位は下図の通りです。
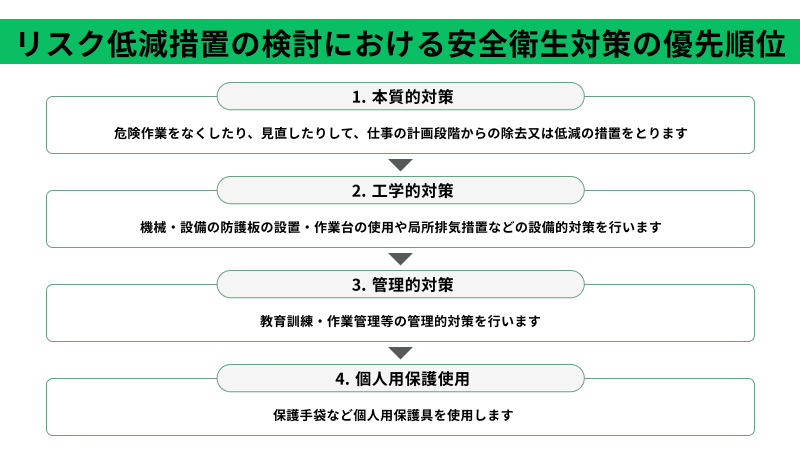
本質的対策
第一に、危険な作業そのものの見直しや撤廃といった本質的対策を行いましょう。
例えばフォークリフトで荷物を降ろす作業がある場合、リスクとしてフォークリフトの作業中に周囲の人に衝突をして怪我をさせてしまうかもしれません。本質的対策としては、衝突をしないようフォークリフト走行エリアと歩行エリアを分離することが挙げられます。
工学的対策
第二に、設備や機械による工学的対策を行いましょう。
例えば、安全柵の中でプレス機が作業しているとします。安全柵にインターロックが設置されていなければ、プレス機が運転中に作業現場に入ることになり、はさまれ・巻き込まれる危険性があります。
安全柵にインターロックを設置していれば、中に入るとプレス機が停止し事故を起こす危険性はなくなります。
労働災害の中には、工程を止めたくない理由でインターロックを一時的に停止して作業エリアに入ったところプレス機に挟まれ死亡した事例もあります。安全を最優先に作業できる環境を整えましょう。
管理的対策
第三に、教育や仕組化による管理的対策を行いましょう。
例えば、侵入禁止エリアに日本語で立入禁止の掲示しかされていないことが原因で、外国人労働者が製造現場の侵入禁止エリアに入ったとします。この場合、外国人労働者の母国語による立入禁止の文言もを記載すれば、言語の壁による事故を防ぐことができるでしょう。
管理的対策を行う際のコツとして、製造現場における掲示のほか、マニュアルや作業手順書にも考えられるリスクやその原因、対処法について記載し、教育の段階でリスクを避けられるような土壌が整備されるようにしましょう。
マニュアルは「作って終わり」や「書いて終わり」ではなく、記載した内容が現場に正しく伝わり、活用されることが目標です。
現場で正しく効率的に伝わるマニュアルを作る手法や、マニュアル整備の効果的なプロセスについて解説した動画を無料でご覧いただけますので、是非ご参考ください。
保護具の使用
第四に保護具の使用など、個人単位で行える対策について実施しましょう。
本質的対策、工学的対策、管理的対策でリスクを除去できなかった場合の手段として、保護具の使用など各従業員の間で行えるリスク対策を検討することも一つの手段です。
優先度が高いリスクから対策を進める
上記のようにリスクの対応優先度を決めたのちは優先度が高いリスクから対策を進めます。対策を講じる際は、まず「そのリスクが除去できるかどうか」を判断することが重要です。
リスクを除去することは、リスクを低減するよりもトラブルの抑止に効果があります。リスクを除去できるのであれば除去を、除去が難しい場合は低減策を検討し、実施しましょう。対策を講じた後は、作業者への周知も忘れずに行ってください。
一方で、すぐに対策を実行できないものもあるでしょう。そのような場合には、すぐに対策を実施できない事象を「残留リスク」と位置づけ、現場の作業者に対して周知する必要があります。
残留しているリスクの内容や労働災害を招かないためのルール、その理由などを周知し暫定措置を実施することが重要です。保護具の着用やマニュアル遵守の徹底など、リスク対策がまだできていない場合もルールを定着させ、安全に仕事ができる環境づくりに努めましょう。
対策した結果の記録/効果を確認する
リスクへの対策を講じた後は、対策した結果の記録や効果を確認します。対策した結果を記録することで、次回のリスクアセスメントを進める際の参考資料になります。
また、対策したものをそのままにせず、行った対策が適切だったかも評価しましょう。
現場改善ラボが過去に開催したセミナー「元労基署長が解説!事故の現場から見た安全管理のこれから」で元労基署署長の村木 宏吉氏は、講じた対策が思っていた結果と異なる場合や、誤った対策を講じた際は新たなリスクが発生すると論じています。
そのため、効果検証のためにも定期的に観測し、正しい効果が確認されない場合は再度リスクアセスメントを実施しましょう。
他にも現場改善ラボでは、村木氏の解説による安全管理をテーマにした講演も無料で公開しています。実際の労働災害事例をもとにした具体的な防災対策や、現場での安全管理を徹底する方法について解説していますので、こちらも併せてご覧ください。
【イラストつき】業界別にみるリスクアセスメントの事例
業界別のリスクアセスメント事例を下記2点紹介します。
- 道路貨物運送業
- 金属製品製造業
道路貨物運送業の事例
作業者がダンプの上で積み込み作業をするリスクアセスメントを見てみましょう。
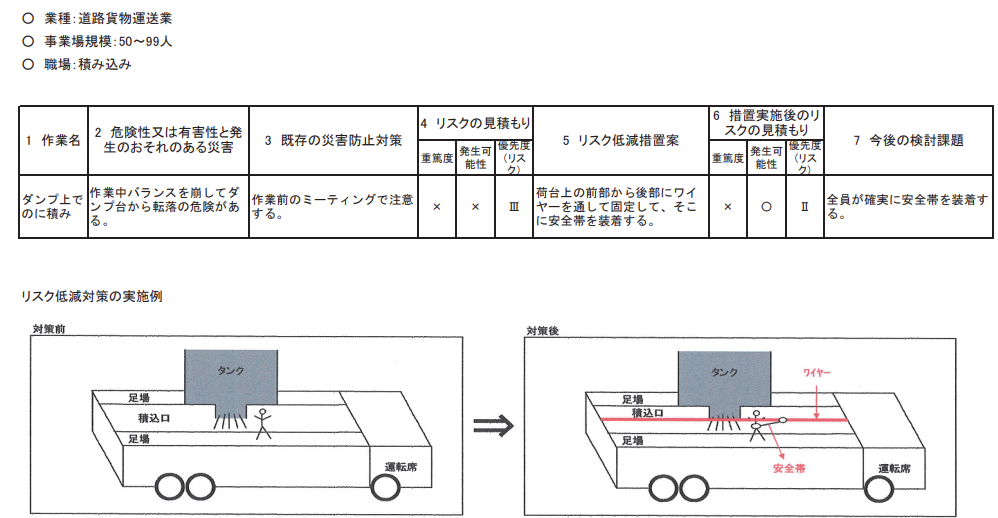
危険性または有害性と発生のおそれのある災害として、ダンプの上で作業中にバランスを崩し、転落する危険があります。
そこで、リスクアセスメントとして現場に潜むリスクを洗い出したところ、既存の災害防止対策として、作業前のミーティングにおける注意するだけにとどまり転落しない仕組みは講じられていない状態が判明しました。これでは、作業者がいくら注意をしていても事故発生のリスクについて対策できていないといえるでしょう。
その後、基準からリスク見積もりを行い、本質的対策や工学的対策に即したリスク低減措置案が考案されました。本事例では荷台上のにワイヤーを通し固定したうえで安全帯を装着することが提言され、転落や怪我のリスクに直接アプローチすることが期待できます。
金属製品製造業の事例
製品の移動作業におけるリスクアセスメントを見てみましょう。
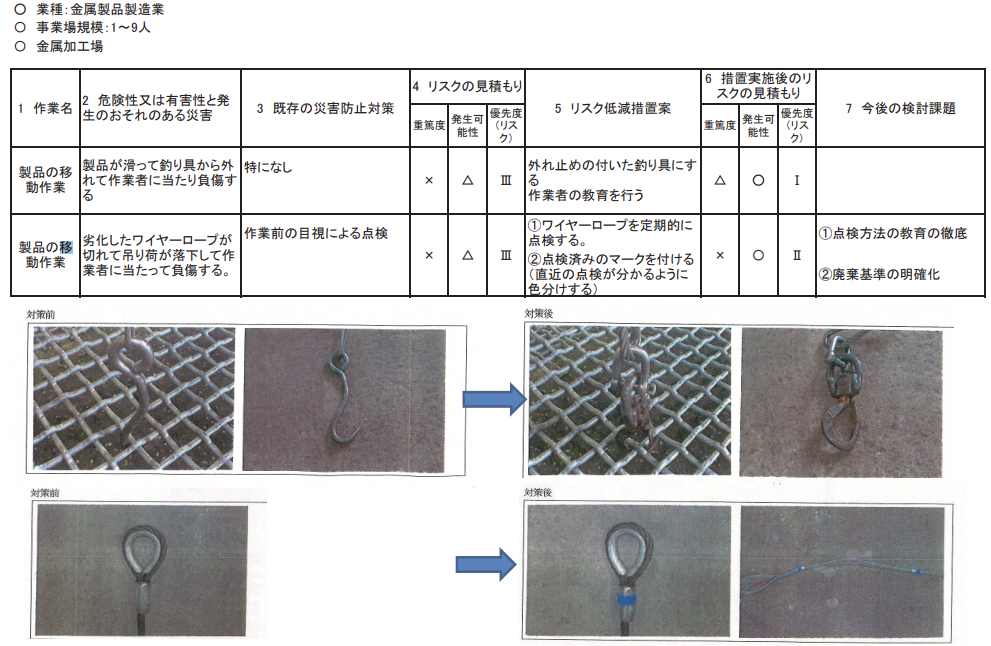
危険性または有害性と発生のおそれのある災害として、製品を持ち上げる釣り具が外れ、周囲の作業者に当たり負傷させる恐れがあります。このような状況にも関わらず、既存の災害防止対策はありませんでした。
そのため、リスクアセスメントとして基準からリスク見積もりを行い外れ止めの付いた釣り具にすることで製品の落下を根本から防ぐ対策のほか、ワイヤーロープの定期的な点検を行うことが低減されました。
今後の検討課題としては、点検方法を現場に定着させるため作業者に向けて教育を実施することが計画されており、リスクに対して除去を行いつつ、リスクを発生させない体制づくりの良い例だといえるでしょう。
リスクアセスメントに取り組んでいる企業事例
リスクアセスメントについて効果的に取り組んでいる企業の事例について、経済産業省が公開している「リスクアセスメント良好事例集」から一部抜粋し紹介します。
良い企業事例を参考に、リスクアセスメントを実施しましょう。
- 大阪国際石油精製株式会社
- 東レ株式会社
- 中部電力株式会社
大阪国際石油精製株式会社
大阪国際石油精製株式会社では、リスクアセスメントとして他社での事故事例を定期的に収集/データベース化して活用しています。収集した他社での事故事例を自社におけるケースに落とし込み対策を検討することで、未然に自社での労働災害を防いでいます。
また、リスクアセスメント実施の際に外注先の社員や管理者層からの評価を取り入れていることもポイントです。社員や管理者層、そして社外の外注先にまで及ぶリスクアセスメントを実施することで、製品に関わる全ての現場での危険意識の向上につなげています。
東レ株式会社
東レ株式会社では、設備の新増設や改造の実施にあたって部署長や関連専門部署、工場長など上層部の承諾を得なければ実施できないという基本ルールを確立し、社内全体でリスクに対する対策が行われています。ほかにも、過去のヒヤリハット事例や他社での事故事例を積極的に活用した教育を推進していることもポイントです。
また、社内だけにとどまらず外注企業社員に対してもリスクアセスメントの教育体制を整えています。自社内だけでなく自社の製品に関わる全ての人に教育を実施することで、製品に関わる全ての現場におけるリスクアセスメントにつなげています。
中部電力株式会社
中部電力株式会社では本部と事業所を中間する組織によって、他社の事故事例や成功事例を分析したものを共有する体制がとられています。本部をはじめ各事業所にも展開されることで、結果として全社で安全への意識向上につなげていることがポイントです。
また、突発的な事故やトラブルにも対応できるよう、日頃からベテラン社員と若手社員を交えたトレーニングを行いながらリスクアセスメント教育を実施しています。毎年1回はローテーションに沿った法令内容やその年の関心事項を含めた勉強会が実施されるなど、社員に対する教育体制が重視されています。
リスクアセスメントを進める際の注意事項
元労働基準監督署署長の村木宏吉氏による講演「現場のキケンを見極める『リスクアセスメント術』」では、リスクアセスメントを行う際に以下のような注意事項があると述べられています。
- 被害は厳格に見積もる
- 遠慮や忖度のない意見を交わす
- 労働安全衛生法令を熟知したメンバーが参加する
被害は厳格に見積もる
被害を厳しく見積もることでより徹底的な対策が行えるようになりますが、会社の予算によっては限られた対策しか実施できないこともあります。
実現可能な対策について社内で話し合うことが必要です。
遠慮や忖度のない意見を交わす
リスクアセスメントはリスクを徹底的になくすための場であるにもかかわらず、メンバーが遠慮や忖度してしまうと話が停滞するほか、必要なアイデアが生まれずにリスクに対して対策できない恐れがあります。
そのため、日頃から意見交換が活発に行われる環境づくりを行うことや、場合によってはベテラン作業員が新人作業員の発言や主張を促すことがおすすめです。
労働安全衛生法令を熟知したメンバーが参加する
そもそものリスクが労働安全衛生法令に違反した環境に起因する場合も考えられます。労働安全衛生法令を無視した状態で労働災害が発生した場合、会社と責任者の双方に罰金が科されるほか、悪質なケースでは書類送検や裁判に発展する場合があります。
このようなことが起こらないように、リスクアセスメントを実施する際は労働安全衛生法令を熟知した方が参加するようにしましょう。
業種別に確認しておきたいリスクアセスメントのポイント
リスクアセスメントは業界に応じて意識すべきポイントがあります。ここでは下記3つの業界別に焦点を当てて紹介します。
- 製造業
- 建設業
- 福祉介護業
製造業
製造業では、機械操作や荷物の運搬など負荷のかかる作業が多く、労働災害が発生しやすい業界です。とくに、転倒や動作の反動・無理な動作による怪我のほか、死亡事故や重大な労働災害のリスクがある現場も多く、リスクアセスメントの重要性が顕著だといえます。
製造業におけるリスクアセスメントとして、まずは怪我や労働災害が発生するリスクへの対応が最優先であり、対策として危険な作業の除去が考えられます。除去が不可能であれば類似の業務を結合し、負担を軽減していきましょう。
建設業
建設業は製造業と類似する点も多い業界ですが、大きく異なる点もあります。製造業は業務の標準化や品質の維持といった観点から作業内容がルーティーン化することが多いのに対し、建設業はプロジェクトの内容により作業内容が変化することや、天候や地形といった環境要因の変化に合わせた柔軟な対応が求められることがあります。
そのため、意図しないリスクが発生する可能性が高い環境だといえます。
加えて、建設業の作業現場には複数の下請け業者が入っています。元請け業者が統括しているものの、個々の作業者まで把握することは難しく、作業場や作業内容が都度異なるということも考えられます。
そのため、建設業におけるリスクアセスメントにはケース別の対応や、異なる作業における定期的な実施が求められます。
「一度リスクアセスメントを実施したからよい」という考えは無くし、考えられるリスクをできるだけ減らせるような対策をするようにしましょう。
福祉介護業
福祉介護業における労働災害発生状況は年々増加しており、原因として移乗介助や入浴・食事介助時に負担がかかる動作をしていること、入浴介助中に浴室で足を滑らせて転倒するなど福祉介護業特有の業務が挙げられます。
他にも、利用者から暴力を受ける、利用者やその家族とコミュニケーション面でトラブルになるなど、精神的なリスクが多いことも特徴です。
福祉介護業では各作業に労働災害やトラブルの原因となるリスクが潜み、介助者だけでなく利用者も巻き込んだ事故に発展するおそれがあります。そのため、介助者の身体的/精神的な負担を軽減するリスクアセスメントを実施し、職員や利用者の安全を担保することが求められます。
リスクアセスメントにはマニュアルの活用や教育機会の整備も重要
リスクアセスメントを効果的に実施し、安全な職場環境を作るためにはマニュアルや教育機会の整備が不可欠です。
教育による現場の作業者ひとりひとりの安全に対する意識の向上が現場に潜むリスク回避にもつながり、労働災害のない安全な職場環境の実現に近づきます。「どんな作業に注意すべきなのか」「なぜ注意しなければいけないのか」を具体的に教育し、職場全体で潜むリスクを共有できれば、より効果的にリスクアセスメントを進められるでしょう。
しかし、マニュアルや教育機会を整備しても、なかなか活用しきれていない現場が多いです。正しい作業手順が伝わらずにいつの間にか独自のやり方が蔓延し、マニュアルが形骸化することや、教育者ごとの教え方や内容の差により教育方法がばらついている現場では、リスクアセスメントを実施しても正しくリスクを可視化できず、現場に潜むリスクが増大する恐れがあります。
そのため、リスクアセスメントを効果的に実践できる現場づくりのためにはまず動画マニュアルによる教育の標準化に取り組みましょう。
動画マニュアルで教育を標準化し、リスクに正しく対応できる現場作りを実現
教育内容や作業手順のムラがなく、リスクに正しく対応できる、かつリスクの少ない現場の実現には「動画マニュアルの活用」がおすすめです。
動画マニュアルは、作業手順などを文字や図面ではなく撮影した動画で示す形式のマニュアルです。従来の紙マニュアルでは伝えきれなかった複雑な動作や手順でも、動画や音声でわかりやすく教えられることから、効果のある教育を実践できるツールとして知られています。
他にも、安全に関する教育や作業手順書の作成を動画マニュアルで進めることには様々なメリットがあります。従来のOJTでは、教育係ごとに教える内容や教え方に微妙な差異があることで正しい内容を伝達できずに教育のムラが発生しやすい傾向がありましたが、動画マニュアルは「動画」という同じ教材を使って教えるため、教育内容が均一になります。
加えて動画は好きなタイミングで繰り返し視聴ができるため、教育やOJTの担当者がつきっきりで教える必要がなくなり負担を減らせる効果も期待できます。
また動画マニュアルは簡単に共有できるため、異なる部門間や全社規模で教育レベルを上げることにもつながります。
そのため、マニュアルや教育機会の整備には動画マニュアルの活用がおすすめです。
おすすめの動画マニュアルは「tebiki」
動画マニュアルでおすすめしたいのは「tebiki」のサービスです。
現場教育の課題として、人によって教育のばらつきがある、言語の壁があり外国人労働者に教育が実施できない、正しい作業手順が伝達できず属人化しているなど様々な課題があります。
tebikiの動画マニュアルはそれらの課題を解決し、業務効率化や標準化、ヒヤリハットや労働災害といったリスクの削減につなげられます。
動画マニュアルは編集が難しい、管理できないのでは?と思う方も多いかと思われます。
しかし、動画マニュアルtebikiは、動画マニュアルを誰でも簡単に作成・編集・管理できることを重要視したツールのため、専門知識や特別なツールを使わずに高品質なマニュアルを作成できます。
具体的には、実際の作業や教育を行っている様子をスマートフォン等で撮影し、ワンクリックで完了する簡単な編集を加えるだけで動画マニュアルを作成することができます。
さらにtebikiには吹き込まれた音声を自動で文字におこし字幕化する機能も搭載されており、映像のほか文字情報もマニュアルに落とし込むことができます。
他にも、tebikiには100カ国語以上に対応した自動翻訳機能により外国人労働者にも高度な教育を実施できるほか、組織レポート機能による習熟度管理の実現など、現場で働く様々な方に便利な機能が多数搭載されています。
tebikiの機能詳細や導入効果、導入までのサポートについては以下の画像から詳しい資料をダウンロード可能ですので、是非ご参考ください。
動画マニュアルtebikiで安全に関する教育を標準化した事例
動画マニュアルtebikiを安全教育の場で活用し教育を標準化したほか、様々な課題解決につなげている事例を2社ご紹介します。
- 児玉化学工業株式会社
- 株式会社ロジパルエクスプレス
他にもtebikiを導入し、現場の課題を解決した事例についてより知りたい方は、以下の画像からダウンロード可能な資料もご参考ください。
児玉化学工業株式会社:動画マニュアルの活用で作業不順守が9割減少
児玉化学工業は1946年に創業した化学メーカーであり、主に住宅設備・自動車向け合成樹脂加工や産業機器の製造を手掛けています。
同社では、不明確な社内ルールである「暗黙の了解」などの課題に直面していました。製造現場には部品を作るための要領書や作業標準書が膨大に存在し、作業手順やコツ、背景にある意味などが伝えきれないことで正しいルールがブラックボックス化していました。安全に関する教育や安全指導でも同様の事例が発生しており、製品不良の原因だけでなくヒヤリハットのリスクが高まっていました。
そこで課題解決のために動画マニュアルtebikiを導入したところ、従業員間の「暗黙の了解」や「慣例」に頼ることなく、明確なルールや手順を共有することが可能になりました。結果として製品の品質向上だけでなく、OJTの効率化や業務の標準化、作業不順守が9割減少したという結果が出ています。ほかにも、tebiki導入により手順書作成の工数が紙の1/3と大幅に短縮され、外国語への翻訳も容易になったという効果も生じています。
児玉化学工業社によるtebiki導入の様子や、導入による効果は以下のインタビュー記事で詳しく紹介しています。是非ご参考ください。
インタビュー記事:手順書作成の工数は紙の1/3になったと思います。動画で作るのはかんたんだし、学ぶ側にもわかりやすいですよね。
株式会社ロジパルエクスプレス
株式会社ロジパルエクスプレスは、倉庫や車両などの自社資産を活用した物流サービスを提供している物流企業です。
同社では紙のマニュアルでは正確な情報が伝わりにくく、正しいルールやマニュアルが形骸化していたことを課題視していました。実際に、「台車で運ぶ荷物の積み上げは胸の高さまで」という情報も人によって意識される胸の高さにばらつきがあることで正しい基準よりも高積みしてしまい、台車から荷物を落としてしまうといった事故も起きていました。
そこで課題解決のためにtebikiを導入し活用したところ、動画により業務上の危険や業務解像度が伝わりやすくなり、安全品質意識の向上に成功しています。同社では社内で定めた事故防止強化月間にあわせて、フォークリフトの危険予知トレーニングや商品の取り扱いルールを動画マニュアル化し、安全教育に活用しています。
ロジパルエクスプレス社による動画マニュアルを活用した仕組み作りや導入の効果については、以下のインタビュー記事で詳しく紹介しています。是非ご参考ください。
インタビュー記事:動画で全拠点の安全品質意識の向上と業務ノウハウの可視化を達成
リスクアセスメントに関するQ&A
リスクアセスメントは誰がやる?
リスクアセスメントは基本的に現場の作業員のほか、監督者や安全衛生に関わる従業員が行います。現場の危険箇所を最も理解している従業員がリスクアセスメントを行うことで、リスクの洗い出しや対策がスムーズに進むでしょう。
リスクアセスメントとヒヤリハットの違いは何ですか?
リスクアセスメントは現場に潜む危険性や有害性を調査し、低減/除去するまでの一連の手法のことです。
これに対しヒヤリハットは、仕事中や日常生活で危険だと感じた出来事そのものを指すという違いがあります。
リスクアセスメントは義務ですか?
リスクアセスメントの実施は事業者の努力義務とされていますが、一部では義務化が法律により定められています。平成18年(2006年)4月には労働安全衛生法により、リスクアセスメントの実施が努力義務とされていますが、平成28年(2016年)6月1日には労働安全衛生法が改正され、一定の危険有害性のある化学物質(640物質)について事業場におけるリスクアセスメントが義務づけられました。
▼引用元▼
リスクアセスメントの法的な位置づけ
労働安全衛生法が改正されました(平成28年6月1日施行)
まとめ
従業員の日々の安全を保障することは、事業者の責務であり、現場に潜む労働災害や事故のリスクに対処するにはリスクアセスメントの実施が求められます。またリスクアセスメントは事業者だけでなく、従業員も含めた事業場全員で活動することが望ましい活動であり、現場全員で情報を共有することで職場全体のリスク意識が向上しリスクを防ぐことにつながることが本記事で紹介したリスクアセスメントの企業事例からも表れています。
一方でリスクアセスメントを効果的に実施するには、マニュアルや教育に対する整備も必要です。マニュアルを活用しきれていなかったり、教育機会の整備が進まないことでリスクに対する認識に差が生じ、現場に潜むリスクに対応できずに重大な事故につながる可能性があります。マニュアルや教育機会の整備/充実には、動画マニュアルの導入がおすすめです。動画マニュアルの活用によって、コストの削減や教育水準の向上が期待できます。
とくに製造現場におけるマニュアル/教育体制の整備には本記事で紹介した「動画マニュアルtebiki」がおすすめです。tebikiの活用により複雑な作業手順も動画でわかりやすく伝えられ、教育を標準化することで現場に潜むリスクに正しく対応できる職場づくりが実現できるでしょう。
今回紹介した内容を参考に、是非リスクアセスメントの実施やリスクを発生させない仕組み作りを実現してください。本記事で紹介した動画マニュアルtebikiは無料でダウンロード可能ですので、ぜひ以下のリンクからダウンロードしてみてください。