かんたんデジタル現場帳票「tebiki現場分析」を展開する、現場改善ラボ編集部です。
傾向管理とは、工程から生じるデータを収集・分析し、その推移から異常の兆候を早期発見、将来的な問題を予測し対策を講じる管理手法のことです。
本記事では、品質管理担当者、製造現場リーダーなど品質向上に関心のある方々へ、傾向管理の基本、管理図の活用法だけでなく、傾向管理に失敗する要因と対策についても言及します。
本記事でお伝えする情報は、製造業の生産性を向上させるための重要な情報と言えます。より生産的な業務を目指して、傾向管理について学んでいきましょう。
目次
傾向管理とは?
製造業における傾向管理とは、データ分析を通じた問題の早期発見と未然防止を図る継続的な「品質改善活動」です。単なるデータ収集を指すのではなく、データ分析の結果に基づいた具体的な改善策の実行や効果検証といった一連の工程を指します。
すなわち傾向管理は不良率の低減、3M(ムリ・ムダ・ムラ)の排除、稼働率の向上に繋がり、企業の収益性向上を実現します。
補足ですが、傾向管理の似た言葉として「傾向異常」や「傾向監視」も使われることがあります。これらとの違いもご紹介します。
傾向異常との違い
「傾向異常」は、収集・分析されたデータにおいて、正常な範囲から逸脱したパターンや、通常とは異なる傾向が見られる状態を指します。つまり、問題が発生している、あるいは発生する可能性が高いことを示す警告信号が傾向異常です。
したがって両者の違いは、「傾向管理」が活動であり、「傾向異常」は状態であると言えます。傾向管理が健康診断であり、健康診断で見つかった異常が傾向異常である、と理解するとイメージしやすいかもしれません。
製造業における例で言うと、「製品寸法の測定データに傾向異常が確認されたため、直ちに製造ラインを停止し原因を調査した」というような文脈で使用されます。
傾向監視との違い
「傾向監視」は、特定のデータや工程を継続的に観察し、その推移や変動パターンを把握することを指します。つまり、より具体的な問題の早期発見に繋がる継続的なモニタリング活動です。
傾向管理が健康診断であれば、傾向監視は「毎日血圧を測定し、グラフにつけて推移を観察する」ようなイメージです。
製造業における例で言うと、「設備の稼働状況を傾向監視することで、故障の予兆を早期に捉え、計画的なメンテナンスを実施している」というように使われます。傾向監視は、問題が発生する前に予防的な対策を講じることを可能にし、安定した品質の維持を実現できます。
管理図を用いた傾向管理の実践手法
管理図はQC7つ道具の1つで、収集したデータを時系列に沿ってプロットし、工程の安定性や異常の有無を視覚的に判断するためのツールです。
適切に活用することで、品質の維持・向上、不良品の削減、改善などに活用可能です。
関連記事:【改善事例あり】製造業における品質不良の原因と8つの対策
管理図を構成する主要な要素
管理図の作成やチェックの際に見るべき基準として、主に「中心線(CL)」「上限管理限界線(UCL)」「下限管理限界線(LCL)」の3つが挙げられます。
中心線(CL)
中心線(CL:Central Line)とは、管理対象となっている特性値(例えば、製品の寸法、不良率など)の平均的な値を示します。工程が安定状態にあるときの、データの中心的な位置を表す指標であると言えるでしょう。
上限管理限界線(UCL)
上限管理限界線(UCL:Upper Control Limit)とは、管理対象となっている特性値が、統計的に見て、これ以上は外れることがほとんどないと考えられる上限値を示します。
したがって、点がこの線を上回る場合は、通常とは異なる原因で品質が悪化している可能性があります。
下限管理限界線(LCL)
下限管理限界線(LCL)とは、工程が安定していると期待される下限を示す値です。工程に異常が発生したことを検知するための上限側の基準となります。
つまり、データがこの線を超えた場合、偶然の変動ではなく、何か特別な原因(異常原因)によって変動が生じた可能性が高いと判断します。
管理図の種類
計量値管理図(Xbar-R管理図、Xbar-s管理図、X-Rs管理図など)
計量値の管理図は、寸法、重量、温度など、連続的に測定されるデータ(計量値)の管理に用いられます。
代表的なものに、Xbar-R管理図とXbar-s管理図があります。Xbar-R管理図は、平均値(Xbar)と範囲(R)を、Xbar-s管理図は平均値(Xbar)と標準偏差(s)をプロットします。Rは計算が簡単で現場でも理解しやすく、sはデータのばらつきをより正確に表します。また、X-Rs管理図は、個別の測定値(X)と移動範囲(Rs)をプロットします。
これらの管理図を用いることで、データの平均値の変動だけでなく、ばらつきの大きさの変化も捉え、工程の異常を早期に発見することが可能です。
計数値管理図(p管理図、np管理図など)
計数値の管理図は、合格/不合格、良品/不良品、欠点の有無など、数えられるデータ(計数値)の管理に用いられます。代表的なものに、p管理図、np管理図、c管理図、u管理図があります。
p管理図は不良率、np管理図は不良数、c管理図は欠点数、u管理図は単位あたりの欠点数を管理します。サンプルサイズが変動する場合は、p管理図またはu管理図を使います。これらの管理図を用いることで、不良や欠点の発生傾向を把握し、工程改善の優先順位を決めるのに役立つでしょう。
計量値管理図の作り方や実践方法
ここでは、代表的なXbar-R管理図について解説します。傾向管理において、最もよく使われるのがXbar-R管理図です。製品の寸法や重量などの品質特性値は、必ずばらつきを伴います。Xbar-R管理図は、このばらつきが正常範囲内にあるか、異常な傾向がないかを判断するための強力なツールです。
データの収集
X-R管理図を作成するには、まず、一定期間ごとに一定個数のサンプルを採取します。サンプルサイズ(群の大きさ)とサンプル数は、工程の特性や管理目的に応じて決定します。サンプルは、同じ条件で製造された製品からランダムに抽出することが重要です。例えば、1時間ごとに5個の製品の長さを測定するといった具合です。
データの計算
次に、各サンプル(群)について、平均値(X̄)と範囲(R:最大値 – 最小値)を計算しましょう。
Xbar = (X1 + X2 + … + Xn) / n R = 最大値 – 最小値 |
そして、すべての群の平均値(X)と、すべての群のRの平均値(R)を計算します。
Xbar – bar = (Xbar1 + Xbar2 + … + Xbark) / k (kはサンプル群の数) Rbar = (R1 + R2 + … + Rk) / k |
管理限界線の計算
続いて、X管理図とR管理図のそれぞれについて、中心線(CL)、上方管理限界線(UCL)、下方管理限界線(LCL)を計算します。X管理図とR管理図の計算式は以下の通りです。
▼X管理図の計算式 CLx = Xbar UCLx = Xbar + A2 × Rbar LCLx = Xbar – A2 × Rbar ▼R管理図の計算式 CLr = Rbar UCLr = D4 × Rbar LCLr = D3 × Rbar |
D3と𝐷4はサンプルサイズ (n) に応じた定数で、決まった値を以下の統計表から得られます。
サンプルサイズ (n) | A2 | D3 | D4 |
---|---|---|---|
2 | 1.88 | 0 | 3.267 |
3 | 1.023 | 0 | 2.575 |
4 | 0.729 | 0 | 2.282 |
5 | 0.577 | 0 | 2.114 |
6 | 0.483 | 0 | 2.004 |
7 | 0.419 | 0.076 | 1.924 |
8 | 0.373 | 0.136 | 1.864 |
9 | 0.337 | 0.184 | 1.816 |
10 | 0.308 | 0.223 | 1.777 |
サンプル数n=5の場合、上記の表からA2 = 0.577、D3 = 0.000、D4 = 2.114となります。
そこで計算式に当てはめると、以下のような計算式になります。
UCLx = Xbar + 0.577 × Rbar LCLx = Xbar – 0.577 × Rbar UCLr = 2.114 × Rbar LCLr = 0.000 × Rbar |
最後に、横軸に群番号、縦軸にXまたはRの値をとるグラフ用紙を用意し、中心線(CL)、上方管理限界線(UCL)、下方管理限界線(LCL)を引きます(CLは実線、UCLとLCLは破線または一点鎖線)。各群のXとRの値をプロットし、点を線で結びます。
プロットされた点が管理限界線の内側にあり、ランダムに分布していれば、工程は安定状態にあると判断可能です。管理限界線を超える点や連続する点が特定のパターンを示す場合(連、傾向変動など)は、工程に異常がある可能性を示唆するため、原因を調査し、対策を講じます。管理図は定期的に見直し、必要に応じて管理限界線を再計算します。
計数値管理図の作り方や実践方法
一般的な管理図の作り方について解説します。p管理図は、不良率(不適合率)を管理するための管理図です。
p管理図を作成するには、まず一定期間ごとに、一定数のサンプルを採取し、各サンプル中の不良品の数を記録します。サンプルサイズは一定である必要はありません。サンプルサイズが変動する場合は、各サンプルの不良率を計算し、それを用いて管理限界線を計算します。
次に、各サンプルの不良率(p)を計算します。pの計算式は、不良品数=d、サンプルサイズ = nで「p = d / n」となります。そして、すべての群のpの平均値を計算します。
dの合計値 = (d1 + d2 + … + dk) (kはサンプル群の数) nの合計値 = (n1 + n2 + … + nk) そして計算式に当てはめれば、pの平均値は「pbar = dの合計値 / nの合計値」となります。 |
続いて、中心線(CL)、上方管理限界線(UCL)、下方管理限界線(LCL)を計算します。i個のサンプルがある場合は以下のような式です。
CL = pbar UCL = pbar + 3 * √( (pbar * (1 – pbar)) / ni ) LCL = pbar – 3 * √( (pbar * (1 – pbar)) / ni) |
最後に、横軸に群番号、縦軸にpの値をとるグラフ用紙を用意し、中心線(CL)、上方管理限界線(UCL)、下方管理限界線(LCL)を引きます。各群のpの値をプロットし、点を線で結びます。
X-R管理図と同様に、点が管理限界線の内側にあり、ランダムに分布していれば、工程は安定状態にあると判断可能です。管理限界線を超える点や特定のパターンを示す場合は、工程に異常がある可能性を示唆するため、原因を調査し、対策を講じます。
補足:【テンプレあり】エクセル(Excel)による管理図の作成や活用
管理図はQC7つ道具の中でも、比較的容易に導入できるツールであり、Microsoft Excelでも十分に作成・活用可能です。テンプレートを利用すれば、データ入力だけで自動的に管理図が更新されるように設定することも可能です。
そこでここでは、無料ですぐ使える!QC7つ道具/新QC7つ道具のExcelテンプレートをご紹介します。以下のリンク先でダウンロードが可能なので、まずはExcelでの活用を考えている方はご活用ください。
Excelテンプレート:無料ですぐ使える!QC7つ道具/新QC7つ道具のExcelテンプレート
傾向管理が機能しない製造現場の共通点
傾向管理や管理図を導入しても、運用が続かず、機能していない製造現場は少なくありません。高度な技術や専門性が求められる傾向管理の特性上、現場でいくつかの課題が生じてしまうことが主な原因です。ここではさらに踏み込んで、傾向管理が機能しない製造現場の共通点として以下の3点を解説します。
- 傾向管理の業務が属人化している
- リアルタイムで異常を発見できない
- 継続的な改善活動が行われていない
傾向管理の業務が属人化している
傾向管理に用いるツールが複雑である場合、特定の技術者に負担が集中しがち、つまり属人化になりがちです。例えば、複雑なマクロを組んだExcelで管理図を運用している場合、マクロの作成・修正ができる担当者が不在になると、途端に運用が滞ってしまいます。
リアルタイムで異常を発見できない
データの集計に時間がかかり、異常値の発見が遅れる、あるいは異常値に気付けないという問題も、製造現場ではよく挙がっています。これは、データの源泉となる現場帳票が紙やExcelで運用されていることが主な要因です。
例えば以下の図のような紙帳票の管理は、記録者や承認者にとっても大きな負担になっているだけでなく、必要なデータを参照したいときにすぐに参照できない、という問題も抱えています。
集計作業に時間を費やすあまり、本来注力すべき異常値の分析や対策の検討が疎かになり、工場全体の生産性低下につながります。結果として、傾向管理が機能していないと判断され、運用自体が形骸化することもあるでしょう。
傾向管理がうまくいっている現場では、現場帳票をデジタル化し、現場に設置されたディスプレイを通じて常にダッシュボードを確認できるような体制が整備されています。
例えば以下の画像は、製造業の「株式会社日本電気化学工業所」で実際に運用されているダッシュボードです。
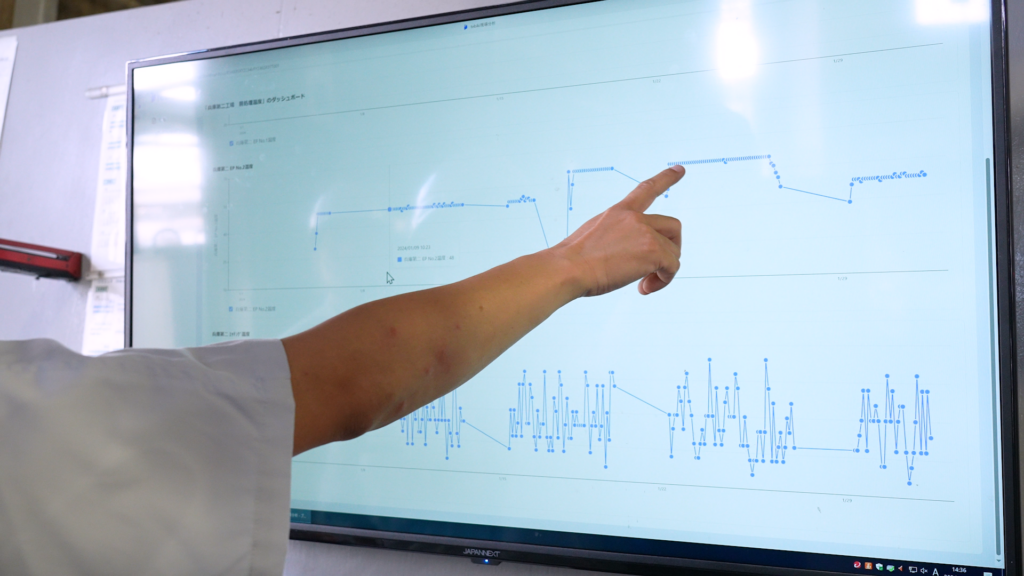
現場帳票をデジタル化している同社では、設備の温度データをリアルタイムで検知しています。通常の温度パターンとは異なるデータに気づき、設備の配管に穴が開いていたというアクシデントを迅速に発見できたという事例もありました。
同社の詳細な取り組み事例は、「インタビュー記事:品質不良の未然防止をリアルタイムデータで実現。異常値検知を迅速にできた理由。」をクリックしてご覧ください。
このように、現場帳票のデジタル化は、データ分析体制を整備するうえで非常に重要です。デジタル現場帳票の導入や推進方法については、以下のPDF資料に簡単にまとめられていますので、あわせてご覧ください。
継続的な改善活動が行われていない
傾向管理は、データを収集・分析し、そこから得られた知見をもとに改善活動を行い、その効果を検証するというPDCAサイクルを回すことで、はじめて真価を発揮します。しかし、データの蓄積と集計がままならない状況では、PDCAサイクルを回すためのスタートラインにも立てません。
場当たり的な対策に終始し、継続的な改善活動が行われず、品質の安定・向上が実現できないまま、傾向管理の取り組み自体が頓挫してしまいます。
失敗しない傾向管理に必要な手段:現場帳票のデジタル化
これまでの解説通り、傾向管理が成功するには、データ集計の源泉となる「現場帳票」が「デジタル化されること」が重要だと言えます。データが自動集計され、必要なデータにいつでもアクセスでき、常に最新のデータが反映されている環境整備が必要だからです。
より具体的に解説すると、現場帳票のデジタル化がもたらす効果は以下の3点に集約されます。
- グラフ作成や異常判定が自動化されるから
- リアルタイムで異常を発見できるから
- データ集計の負担が大幅に軽減されるから
では、現場帳票をデジタル化する方法は何が適切なのでしょうか?
そのひとつの答えとして、デジタル現場帳票サービスの代表例である「tebiki現場分析」が挙げられます。tebiki現場分析は帳票のペーパーレス化だけでなく、リアルタイムデータ集計によるグラフ作成の自動化や、パソコン上での帳票の一括承認、異常値が集計された際の自動通知機能など、製造現場を様々な角度から支援する機能が備わっています。
tebiki現場分析の詳しい機能や活用事例は、以下の画像をクリックしてご覧ください。デジタル現場帳票によって製造現場がどのようにDX化されるのか、具体的にイメージできるようになります。
グラフ作成や異常判定が自動化されるから
デジタル現場帳票を導入するメリットの1つは、データの可視化が容易になることです。多くのデジタル現場帳票ツールでは、入力されたデータをもとに、管理図などのグラフが自動的に作成されます。
例えば以下のような紙の帳票があるとします。
この紙の帳票をデジタル化すると、ツールによっては、以下のようなグラフが自動で作成されます。
また、データを蓄積していくなかで、異常値が検出された場合にアラートを発する機能も備わっているツールもあります。例えば、デジタル現場帳票の「tebiki現場分析」にはグラフ作成と異常判定の自動機能があります。デジタル現場帳票により、担当者はデータ分析に時間を割けるようになり、より迅速な問題解決が可能になります。
リアルタイムで異常を発見できるから
現場帳票をデジタル化するとデータをリアルタイムで計測できるので、異常値が検出された際はその場ですぐに気付けます。例えば「tebiki現場分析」は、記録項目ごとに正常値を設定できます。そして、正常値の範囲外のデータが記録された瞬間に、関係者全員に以下の図のような「異常アラート」の通知が送信されます。
「異常アラート」により、異常発生の見逃しを防ぎ、迅速な状況確認、業務指示、対策の実施を可能にします。問題の早期発見と対応は、不良品の発生を抑制し、生産ラインの停止時間を最小限に抑える上で必要です。
データ集計の負担が大幅に軽減されるから
紙の帳票やExcelでのデータ管理では、データの転記や集計作業に多大な時間と労力がかかります。一方、デジタル現場帳票では、データ入力と同時に自動的に集計が行われます。自動集計により、担当者は煩雑な集計作業から解放され、より付加価値の高い業務に集中できるでしょう。また、人的ミスのリスクも低減され、データの信頼性も向上します。
デジタル現場帳票で傾向管理の運用に成功している企業事例
株式会社日本電気化学工業所は、1935年創業のアルミニウム表面処理を専門とする企業です。アルマイト加工を中心に、建材、自動車、航空機、電子機器など幅広い業界に表面処理の業務を行っています。
同社では以前は、紙ベースの帳票管理が中心で、データの活用が進まず、異常検知の遅れ、承認作業の非効率性、過去データ参照の困難さといった課題がありました。記録が目的化し、データは品質改善に活かされず、異常値の発見も遅れがちに。管理者は現場を巡回して帳票を確認・押印し、過去データを探すのも一苦労という状況でした。
こうした課題を解決するため「tebiki現場分析」を導入し、現場帳票のデジタル化を推進しました。
▼現場帳票のデジタル化事例 インタビュー動画▼
「tebiki現場分析」導入により、製造工程の重要パラメータ(温度など)はリアルタイムで監視可能に。温度データのわずかな変化から配管の穴を発見し、大規模故障やライン停止を未然に防いだ事例は、デジタル化によるデータ収集、そしてリアルタイム分析が即座の異常発見、対応につながった典型例です。異常値判定メール機能も、迅速な対応をサポートしています。
データの蓄積・分析が容易になり、長期的な品質改善計画も立案可能に。さらに、デジタル化によって現場従業員の意識改革も進み、記録の正確性に対する意識が向上しました。
「tebiki現場分析」の詳細な機能や他の活用事例についても知りたい方は、以下のPDF資料もあわせてご覧ください。
>>>かんたんデジタル現場帳票「tebiki現場分析サービス資料」を見てみる
まとめ:傾向管理の第一歩は「現場帳票のデジタル化」
本記事では、品質管理における重要な手法である「傾向管理」について、その基本概念から実践方法、課題、そして解決策までを解説しました。
傾向管理は、データを収集・分析し、その傾向から工程の異常を早期に発見、未然防止するための活動です。管理図(QC7つ道具の一つ)を用いることで、計量値・計数値データの変動を視覚的に把握し、異常原因の特定と対策を迅速に行えます。
しかし、傾向管理が機能しない現場では、業務の属人化、リアルタイムな異常検知の困難さ、継続的な改善活動の不足といった共通の課題が見られます。これらの課題を克服し、傾向管理を成功させるための鍵となるのが「現場帳票のデジタル化」です。
デジタル化により、グラフ作成や異常判定の自動化、データへの即時アクセス、データ集計の負担軽減が実現します。特に、「tebiki現場分析」のようなデジタル現場帳票ツールは、傾向管理をサポートし、工場全体の異常発見と未然防止を可能にします。
この記事で紹介した「tebiki現場分析」は以下のリンクからダウンロード可能です。データにもとづいた客観的な判断と迅速な対応で、品質向上と生産性向上を実現しましょう。