かんたんデジタル現場帳票「tebiki現場分析」を展開する現場改善ラボ編集部です。
製造業のDXを進めるうえで「デジタルスレッド」が注目されています。デジタルスレッドは、製品に関わるすべてのデータを一本の“スレッド(糸)”のようにつないだ状態のことで、品質向上やコスト削減が可能です。
本記事では、デジタルスレッドの概念から、混同されやすいデジタルツインとの違い、導入する際の課題や実例までをわかりやすく解説します。現場での活用を検討している方は、是非ご覧ください。
デジタルスレッドは製造業におけるDXのひとつですが、DXはあくまで手段。「製造現場をITツールやデータを用いて可視化し、改善する」という目的を達成する必要があります。
製造業でデータ分析を行う実践的な方法や、改善活動へどう落とし込むかを知りたい方は、以下の解説動画をご覧ください。
目次
デジタルスレッドとは?
製造業では、製品の開発から生産、運用、保守まで、多くの部門や工程が関わります。しかし、工程ごとにデータの管理方法が異なると情報が分断され、無駄やミスが発生しやすくなります。
デジタルスレッドは、こうした分断されたデータを一本の「糸(スレッド)」でつなぎ、製品情報をライフサイクル全体で一元管理するための考え方です。製造業DXの広がりとともに近年ますます注目されています。
たとえば、設計図面、材料情報、検査データ、修理履歴といった情報が連携されていれば、過去のトラブル事例をもとに改良したり、将来の不具合を予測したりすることが可能になります。
この仕組みによってミスを減らし、品質を向上させるとともに、製品開発のスピードと効率も高められます。
関連記事:【24選】製造業で実用的なDXツール一覧!活用事例やDX成功のポイントも解説
PLMとの違い
PLM(Product Lifecycle Management)は、製品の企画から設計、製造、販売・アフターサービス、廃棄までの製品のライフサイクル全体を通じてデータを管理するシステムです。ただしPLMは「製品データの保管・管理」にフォーカスしているのが特徴です。
一方で、デジタルスレッドはPLMだけでなく、他の業務システムも含めた“情報の流れ”そのものに着目した概念です。PLMがデジタルスレッドの一構成要素と言えるでしょう。
デジタルツインとの違い
デジタルツインは、物理的な製品や設備をデジタル上に再現する技術です。現実と仮想空間が同期しており、挙動のシミュレーションや遠隔監視に使われます。
一方で、デジタルスレッドはあくまでも「情報のつながり・流れを管理」する考え方です。
この2つは別物ですが、組み合わせることでシミュレーションの精度向上や不具合の早期検出など、開発・生産現場でのDXを強力に推進できます。
これらの違いや具体例について、以下の表にまとめました。
内容 | メリット | 活用例 | |
---|---|---|---|
デジタルスレッド | ばらばらだった製品・プロセス情報を一気通貫で管理できるようにする仕組み | ・業務効率の改善 ・製品、サービスの改善 ・顧客満足度の向上 | ・生産現場の遠隔監視 ・ARによるカスタマーサポート ・部門間のプロジェクト連携 |
PLM | ライフサイクル全体を管理するシステム(デジタルスレッドの一要素) | ・業務効率化 ・生産性の向上 ・品質の向上 ・コスト削減 | ・見積もりと製品仕様選定を自動化し最適な提案を実現 ・3Dモデルを自動生成し、設計工数を削減 ・3Dモデルから情報を抽出し、製造、調達と自動で連携 |
デジタルツイン | 物理的な製品やシステムをデジタル上で再現する技術 | ・品質の向上 ・売上増加 ・業務効率的化 ・アフターサービスの充実 ・資源の削減 | ・仮想空間上の3Dモデルで設計検討 ・蓄積された生産データを活用した予知保全 ・工場の遠隔監視 |
デジタルスレッド活用のメリット3選
デジタルスレッドの活用によるメリットは多くありますが、ここでは製造現場で期待できるメリットに絞って3つご紹介します。
データ活用による品質向上
部門ごとに保管されていたデータをデジタルスレッドで統合することで、「どこで、何が、なぜ起きたのか」がすぐに分かります。これにより、設計段階での不具合の早期発見や、生産中の異常の即時対応が可能です。
また、試作段階の評価データをリアルタイムで共有することで、製造での品質ばらつきを未然に防ぐことができます。結果として、品質クレームの削減につながります。
データ活用は生産性向上や品質トラブルの未然防止に役立つことが期待できる一方、適切なアプローチと具体的な方法論なくして実践的な分析は難しいでしょう。現場改善につなげるデータ活用の進め方について知りたい方は、以下の解説動画もご覧ください。
サプライチェーン管理の改善によるコスト削減
サプライチェーンとは、製品や商品が消費者に届くまでの生産・流通プロセスのことです。自社だけではなく原材料や部品の購入先も含み、材料の調達から自社での生産、物流、納品まで、複数の企業や部門が関わる複雑なプロセスです。
デジタルスレッドにより各工程の状況を“見える化”できれば、在庫過多や納期遅れといったリスクを事前に把握できます。需要変動に柔軟に対応できる体制が整い、無駄な在庫を持つ必要がなくなるため、全体のコスト削減にもつながります。
PLMとの統合による開発スピードの向上
設計データ、試作情報、製造条件などをデジタルスレッドでリアルタイム共有できる環境が整うことで、部門間の“やり直し”や“すれ違い”が減少します。
例として、PLMで管理されている設計情報をそのまま生産部門に連携できれば、設計変更の反映漏れや伝達ミスを防ぐことが可能です。結果として、開発期間の短縮と、生産のリードタイムの短縮を実現でき、企業の競争優位性の確立につながります。
デジタルスレッドの活用場面
出荷データから需要予測による生産計画や在庫の調整の精度が向上する
デジタルスレッドを活用により、出荷データをリアルタイムで分析し、需要予測の精度向上が可能です。その結果、生産計画や在庫調整が的確に行え、過剰在庫や欠品による機会損失を防ぎ、利益率の改善につながり、コスト削減と顧客満足度の向上が期待できます。
設計・生産データから傾向の管理を行い、予防保全・不具合予測が可能になる
設計段階での変更履歴や、生産現場での稼働データを蓄積・分析することで、機器の劣化傾向や潜在的な不具合を早期に検出できます。
たとえば、「高温多湿な時期に特定工程で故障率が上がる」といった傾向が見えれば、事前に予防保全を行うなどの対策を打つことが可能です。
このような予防保全の計画が立てやすくなり、突発的な故障を減少させ、設備の稼働率向上とメンテナンスコストの削減が実現します。
関連記事:予防保全・予知保全・事後保全は何が違う?メリットデメリット、事故を防ぐポイント
サプライヤーとの連携を強化し、サプライチェーンのパフォーマンスが改善する
デジタルスレッドの活用でサプライヤーとの情報共有がリアルタイムで行われ、調達から製造、納品までのプロセスがスムーズになります。
製品の仕様変更やサプライヤーの納期変更が生じた場合でも、リアルタイムで情報共有できれば、調達計画や製造スケジュールの修正も簡単に行うことが可能です。
サプライチェーンの可視性が向上すれば、部品不足による生産停止の防止、在庫の最適化によるコスト削減、納期遵守率の向上など、サプライチェーン全体のパフォーマンス改善が期待できます。
▼関連記事
・【専門家解説】サプライチェーンマネジメント(SCM)とは?基本概念と仕組みをわかりやすく解説
・【専門家解説】サプライチェーンマネジメント成功事例から分かる、SCM最適化に不可欠な要素とは?
デジタルスレッドの導入実例
建設機械・自動車業界
建設機械・自動車業界のような部品数の多い業界ではデジタルスレッドの導入が進んでいます。たとえばスウェーデンのVolvo Construction Equipment (CE) 社では、製品データの一元管理を実現しました。
デジタルスレッドの概念を取り入れたことで、設計・生産・サービスの各プロセスを連携させ、業務全体の最適化を行い、全社レベルの生産性向上を推進しています。
航空機業界
航空機業界では、複数企業が関与する共同開発において、異なる情報システムやデータ形式が障壁となり、企業間の連携が困難でした。
この課題を解決するため、JAXA(国立研究開発法人宇宙航空研究開発機構)は「SACRA(Standards-based Active Collaboration Realization for Aviation)」というデジタルDXプラットフォームを開発しています。SACRAは、設計、製造、認証の各プロセスをシームレスに繋ぎ、データアクセスを適切に管理しながら、OEMや機種ごとに異なる開発領域と共通利用する利活用領域から成る構成を持ちます。
これにより企業間のデータ連携が効率化され、開発プロセスの統合が可能となりました。将来的には分散アクセス制御技術の研究開発も進められており、航空機業界でもデジタルスレッドの活用が広がっています。
製造現場でデジタルスレッドを導入する際の課題
デジタルスレッドは製品ライフサイクル全体のデータを「つなぐ」ことで、製造業の品質や効率を大きく改善できる可能性があります。しかし、現場への導入にはいくつかの大きな課題があることも事実です。ここでは、実際の製造現場で想定される代表的な3つの課題を紹介します。
初期投資が膨大
デジタルスレッドの導入には、ITインフラの整備、ソフトウェアの導入、既存業務の見直しといった多くのステップが必要です。
さらに、導入にあたっては専門的な知識を持った人材が必要になるため、人材確保や教育にもコストと時間がかかります。これらの初期負担が重くのしかかるため、「導入したいけど、今は動けない」と判断せざるを得ない企業も多く存在します。
実際には、ROI(投資対効果)が数年単位でしか見込めない場合も多く、目の前の利益や工数削減に追われがちな現場では、長期的な視点での投資判断が難しいのが現状です。
データの移行が困難
製造現場では、部門ごとや工程ごとにばらばらの帳票フォーマットが使われているケースがあります。たとえば、品質管理部門はExcel、製造ラインは紙のチェックリスト、生産管理は独自のシステム、といった具合です。
このように形式が統一されていないデータを一元化するには、まず既存データの収集と変換という膨大な作業が発生します。しかし、製造業では「まだ紙で記録している」現場が今も少なくありません。こうした紙の帳票をデジタル化し、さらにデジタルスレッドに対応させるには、現場とのすり合わせや試行錯誤が必要になります。
また、現場の人が「どの項目をどう記録していたか」を理解しないと、正確にデータを再現できません。帳票の読み解きと再構築だけで相当な時間がかかることもあります。
文化的な変革が必要
デジタルスレッドの最大の価値は、製品に関わるあらゆるデータをリアルタイムに、関係者全員が使える状態にすることです。しかしその効果を最大限に発揮するには、単にツールを導入するだけでなく、「現場がデータを活用する文化」を根づかせる必要があります。
一方で、データ活用が新たな業務負担やストレスと受け取られることも少なくありません。たとえば、これまで現場の判断で進めていた作業に対し「なぜそう判断したのか?」をデータで説明するよう求めると、抵抗が生まれることもあります。
そのため、現場とのハレーションを避けながらデジタルスレッドを根づかせるには、単に仕組みを押しつけるのではなく、現場の声を聞きながら「なぜこのデータが必要か」「それによって何が改善されるのか」を丁寧に伝え、納得と理解を得るプロセスが欠かせません。
同時に、現場の作業員が迷わず使えるツール選定や段階的なトレーニング、社内教育や業務慣習の変革にも力を入れることも必要です。
デジタルスレッドの導入には「製造データの一元管理」から
製造現場でデジタルスレッドを導入し運用するには、先述したような課題の解決に加え、「製造データの一元管理」が求められます。。というのも、製品ライフサイクル全体の情報を“つなげる”ことが本質である以上、そもそもデータが部門・工程ごとに分断されていては、スムーズな導入や活用は困難です。
しかし、実際の製造現場では、工程ごとに異なるフォーマット(紙・Excel・独自システムなど)が使われており、データの収集や変換に非常に手間がかかるのが現状です。また、誰がどの項目をどう記録しているのかが属人化していることも多いため、形式をそろえるだけでなく、意味まで正確に読み解く必要があります。
だからこそ、デジタルスレッドを機能させるには、まずは帳票のデジタル化やデータ項目の標準化から着手し、全体のデータ構造を統一する必要があります。最初からすべてをつなげようとせず、特定工程や製品群に絞って小さく始め、段階的に統合を進めることが現実的かつ効果的なアプローチです。
「そもそも帳票のデジタル化とは?」「慣れ親しんだ紙帳票からいきなり切り替えるのは不安…」というお悩みをお持ちの方に向け、デジタル帳票の導入に役立つガイドブックをご用意いたしました。つまづきやすい失敗パターンや導入の費用対効果が算出できるシートも内包しているため、現場DXやデータ分析にご興味のある方は是非ご覧ください。
>>「はじめての現場帳票デジタル化ガイド」で導入の費用対効果を算出してみる
tebiki現場分析で製造データを管理して現場課題を解決!
まずは「製造データの一元管理」から始めるのが、デジタルスレッド導入の第一歩です。ここで役立つのがかんたんデジタル帳票「tebiki現場分析」です。tebiki現場分析を活用すれば、現場での帳票記録からリアルタイムなデータの可視化を実現できます。
tebiki現場分析とは?
かんたんデジタル現場帳票「tebiki現場分析」は、現場帳票をクラウド上でかんたんに作成・記録・承認・管理ができるだけでなく、ダッシュボード機能によって現場のボトルネックや異常をリアルタイムで可視化できるツールです。
製造現場で使用されているPCや外部モニターはもちろん、スマートフォンやタブレットのような縦型の端末でも記入や閲覧できる画面になっており、製造現場で使いやすい機能が複数搭載されています。
シンプルな操作画面で、直感的に現場帳票のひな形を作成することができるほか、入力時の正常値設定やExcelのような表形式による記録も行えます。記録データは自動グラフ作成機能によって、複雑な関数やマクロを組まなくても、かんたんに現場の可視化/データ分析が行えます。例えば、以下の画像は実際にtebiki現場分析で可視化された帳票データのダッシュボードです。

主な特徴は以下の通りです。
- 項目ごとに正常値設定が可能:正常値以外の記録は異常値として管理者にアラートが届く
- 使いやすいインターフェース:デジタル端末に不慣れでもかんたんに操作可能
- 正しい現場データを蓄積:マスタの登録、バーコード読取による情報入力、画像記録も可能
- データ分析の専門知識は不要:パレート図や管理図、テーブル形式の表示が自動で更新
帳票の検索機能やCSV出力など、管理面の機能も取り揃えています。tebiki現場分析のより詳細な情報は、以下のリンクをクリックして概要資料をご覧ください。
>>誰でも簡単にデジタル帳票が作成!分析・異常検知もできる「tebiki現場分析」の特徴をもっとみる
tebiki現場分析ならアフターフォローもバッチリ
tebiki現場分析は導入後もサポート体制も充実しており、現場のフィードバックをもとに継続的な機能改善が行われています。常に“現場に寄り添う”アップデートがされているため、使い続けることで現場力が高まります。
たとえば、金属加工を行っているNACL(株式会社日本電気化学工業所)では、tebiki現場分析の導入によりリアルタイムでデータを監視できるようになり、異常の早期発見と迅速な対応が可能になりました。またデータの蓄積と分析が容易になったため、長期的な品質改善計画の立案にも役立っています。
▼ダッシュボードで分析する様子▼
|ダッシュボードで分析する様子.png)
他にも、スチール製家具製造の共栄工業株式会社では、1日2時間かかっていた紙帳票からExcelに転記・集計する作業がわずか1分に短縮されました。リアルタイムに作業状況を把握できたことで、意思決定のスピードや作業効率が改善しています。
▼タブレットで記録・集計したデータを分析する様子▼
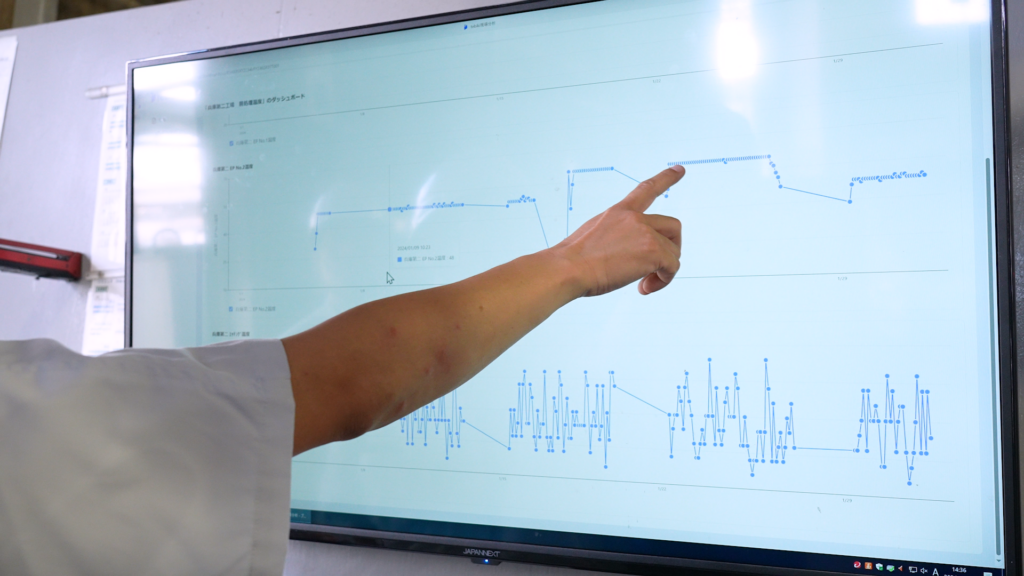
まとめ
デジタルスレッドは、製品ライフサイクル全体にわたるデータの「つながり」を可視化し、製造業を品質・コスト・納期の3つの側面から強化します。
ただし、導入には高いハードルがあり、現場目線での段階的な取り組みが成功のポイントです。まずはtebiki現場分析のような「現場で使えるデータ活用ツール」から始めて、着実にデジタルスレッドの構築へとつなげていきましょう。
本記事でご紹介したtebiki現場分析の資料は、以下の画像をクリックいただくと無料でダウンロード可能です。現場帳票の電子化や現場のペーパーレス化を検討されている方は、是非ご覧ください。