製造業において、品質管理は顧客の信頼性を維持するために大変重要です。製造現場での品質管理の手法としてQCサークルがあり、QCサークル活動を上手く活用することで製造現場における品質維持・品質向上に繋がります。
この記事では、QCサークル活動とはどのようなものでどう進めるのか、テーマの選び方やポイントについて解説します。また最後には職場で実際に活動し、目標達成した成功事例や目標を達成できなかった失敗事例も併せて紹介しますので、現場でのQCサークル活動にお役立てください。
現場改善ラボでは元トヨタのエンジニアが「形骸化させないQCサークル活動の進め方」を解説した動画を無料で視聴できます。ぜひこの機会に以下よりご視聴くださいませ。
目次
QCサークル活動(小集団改善活動)とは?
QCサークル活動(小集団改善活動)とは、現場業務に携わる従業員を小集団に分け、品質管理・品質改善する小グループ活動です。
この小グループは、自主的に運営し、QC(Quality Control)手法を最大限に活用しながら、職場の仲間とともに職場の問題や課題を解決する目的で、意見を交わしやすい5人から10人程度の規模で活動します。
活動のゴールは問題解決や課題解決ですが、活動を通じて、サークル員の能力向上や活力のある職場づくり、お客さま満足度向上を目指す活動でもあるのです。
QCサークル活動の基本理念は?
QCサークルの歴史は1950年代にまで遡ります。
当時、アメリカの統計学者であるW・エドワーズ・デミング氏が日本の経営者に対して「PDCAサイクル」による品質管理の手法を提唱しました。このデミングの考えをトヨタ自動車を中心とした日本企業が独自に改良して生まれたのがQCサークルです。
QCサークル活動を全国に広めてきた日本科学技術連盟によると、QCサークル活動の基本理念は以下の3つだとされています。
- 従業員の能力を最大限に発揮して、無限の可能性を引き出す
- 従業員の人間性を大切にし、生きがいを感じられる明るい職場環境を整える
- 企業の体質を改善し、その成長と発展に貢献する
QCサークル活動は従業員の自主性と能力を高めながら、品質の向上による企業成長に貢献することができるため、非常に重要な活動だといえます。
QCサークル活動のメリットやデメリット
製造業におけるQCサークル活動は、品質改善・品質向上以外にも数多くのメリットがある一方でデメリットも存在します。ここでは、QCサークル活動のメリットとデメリットについて紹介します。
メリットとしては、製造現場での日々の改善活動を繰り返すことで、品質管理や改善のための手法が身につき、問題解決や課題解決能力が向上したり、業務効率化によるコスト削減などがメリットとして挙げられます。
また、デメリットとしてQCサークル活動がQC発表会のための活動に陥りやすく意義ある議論ができない可能性があります。活動することが目的となっている現場では、結果が見えているテーマを短時間で解決し、資料作成、発表という流れになり、本来の意義ある活動になりにくくなっています。
このようなデメリットに陥ってしまうと、活動メンバーの『時代遅れでは?』という意識が生じてしまう恐れがあります。
次章で紹介するようなQCサークル活動の目的をメンバー間で認識を共有しておくことで、活動の停滞を予防し活性化させることが期待できます。
時代遅れ?QCサークル活動の目的
QCサークル活動は品質向上において重要な取り組みです。従業員が現場の問題点を共有し、改善策を話し合うことで品質維持・品質向上に繋がります。
一方で『QCサークル活動は時代遅れでは?』と感じている方もいらっしゃるかもしれません。そのように感じてしまう背景には、現場のQCサークル活動が形骸化してしまっている実態があるかもしれません。
- 「ずっとやってきた決まりだから」と慣習として残り続けている
- 現場改善が目的ではなく、従業員による改善提案/発表の場と化している
- QCサークル活動による改善効果を生み出せていない
品質改善につながる価値あるテーマを選定できておらず、決まりだからと形骸化してしまっているQCサークルの活動は活性化せず、結果的に効果も出ないことで『時代遅れだ』と感じてしまうのではないでしょうか。
QCサークルでは現場で抱えている具体的な課題をテーマに選定することで、管理者や経営層が現場の問題を正確に把握することにつながります。
潜在的な問題が放置されてしまうと、リコールや商品回収が伴うような大きな経営問題に発展するリスクが高まります。現場の課題を早期に発見し、現場/管理者/経営層が効果的な対策を講じるという目的のためにもQCサークルは活発に行われる必要があります。
トヨタの現場で品質保証や品質管理を担当されていた古里 和敬氏の講演では、QCサークル活動の考え方として「自分たちの作業は自分たちで、自分たちのために改善する」という意識がトヨタで浸透しているというお話もありました。自分たちがより良く業務を進めやすくするという目的で取り組む形もよいのではないでしょうか。
次章からはQCサークルの形骸化をストップし、活動を活性化させる進め方について、専門家による解説動画も交えながらご紹介します。
【トヨタ式メソッドも】QCサークル活動を活性化させる進め方とポイント
QCサークルは目的を正しく認識して取り組まないと、改善効果を生み出す活動にならず形骸化してしまいます。ここではQCサークル活動を活性化させる進め方について以下のステップに沿って解説します。
- サークルメンバーの決定
- 取り組むテーマの決定
- 現状把握
- 要因分析
- 目標設定
- 改善案の検討/実行
- 効果確認
- 標準化
各ステップで、トヨタの現場で品質保証/品質管理/組立などに従事されていた経験がある、古里 和敬氏による解説動画からポイントも一部抜粋しながらご紹介します。
トヨタ式のQCサークル活動の進め方を全編を通じて見たい方は、以下より無料でご覧いただけますので併せてご活用ください。
1.サークルメンバーの決定
QCサークル活動のメンバーは5人〜7人程度が適任です。
なぜなら、メンバーが5人未満だと1人にかかる負担が大きくなるからです。メンバーが多すぎると、リーダーポジションのメンバーが全員を取りまとめる負担が大きくなります。加えて、積極的に活動に参加しない人が出てきてしまい、QCサークル活動の停滞感や形骸化を引き起こす恐れがあるため、リーダーが対応できる人数として5~7人程度がよいでしょう。
メンバーを選定する基準としては、議論が活発になるように以下のような軸から選び、役割を明確にするとよいでしょう。
- 共通の業務に取り組んでいる
- 現場で類似する課題を抱えている
同時に、QCサークルのメンバーを支える環境も併せて整えましょう。
メンバーになった従業員にとって、QCサークル活動は現場課題の原因を正確に捉え、改善策を立案するという練習の機会になります。
古里 和敬氏の解説動画『トヨタ式QCサークル活動の進め方』によると、トヨタにおけるQCサークル活動ではQC手法に知見のあるアドバイザーや、サークルリードに対するリーダー教育を行う指導員など、知識を持つ従業員がサークルメンバーをフォローする体制を整えているとのことです。
フォロー体制も整備することで、サークルメンバーのスキル向上や次世代リーダーの育成といった人材開発の場にもなるでしょう。
2.取り組むテーマの決定
QCサークル活動を活性化させるには、活動の方向性を決めるテーマ選定が最も重要です。改善したいことを明確に決めることで問題の洗い出しや対策の立案がスムーズに進みます。
テーマを選定する際にはメンバーが自由に選ぶのではなく、品質/安全/生産性といった最も会社の成果に貢献できる課題について取り組みましょう。
QCサークル活動は業務時間内に行うものであるため、会社や部署の改善に貢献できるようなテーマを選ぶべきです。そのようなテーマで改善が成功した場合、結果的に会社に貢献ができたという成功体験からメンバーのモチベーション向上も期待できます。
テーマ選定は自由/メンバー自身の悩み/目的のない改善アイデア出しといったテーマでは大きな成果は生まれず、モチベーションの低下や『やっても意味ない』という停滞感につながってしまいます。
QCサークル活動を活性化させるためには、会社/部署に貢献できるような現場課題をテーマに選定しましょう。
3.現状把握
テーマ選定をしたら現状把握を行い、どこに課題があるのか特定しましょう。
現状把握する際には、QC7つ道具といったQC分析手法を用いて定量的に可視化することが有効的です。可視化することで、どの作業工程にボトルネックがあるのか?解決すべき課題を特定することができます。
QC7つ道具は以下のような使い方をするとよいでしょう。
- パレート図:どの製品で品質不良が多く発生しているのか整理
- 円グラフ:該当製品で発生している品質不良の分類分けを行い、不良の要因を特定する
一方で『QC7つ道具を使いこなすのが難しい…』『メンバーに上手く教えられるか不安…』とお悩みの方もいらっしゃるでしょう。そのような方はこちらの解説記事か、専門家がQC7つ道具の使い方を解説する無料動画を以下よりご覧ください。
4.要因分析
解決すべき対象を特定したら、なぜ問題が発生しているのか要因を分析します。
要因分析をする際には「いつ」「どこで」「誰が」「何が」「なぜ」「どのように」といった5W1Hの考えの元、QC7つ道具である特性要因図や散布図を使いながら整理していきましょう。
顕在化している問題がなぜ起きているのか?「なぜ」を深堀することで問題の真因を突き詰めることができます。真因を特定するためにはなぜなぜ分析を活用し、サークルメンバー内で『なぜ?』『なぜ?』とさまざまな視点から考えてみましょう。
なぜなぜ分析の進め方は別記事の解説をご覧いただくか、トヨタ社内でなぜなぜ分析の研修を担当していた専門家による以下の解説動画をご覧ください。
5.目標設定
QCサークル活動における目標設定は具体的な数値を設定することが重要です。
要因分析で見つけた改善部分を可能な限り数値化し、その現状値に対する目標値も具体的に数値化しましょう。それにより効果を実感しやすくなり、改善に対するメンバーの意欲やコミュニケーションが高まります。
ここでは、どれくらいの目標設定にするかサークル内でしっかりと議論することが大切です。
高すぎる目標はサークル員のモチベーション低下につながり、低すぎる目標はテーマ完了時の達成感が得られにくいです。目標は具体的に数値化し、高すぎず、低すぎず、バランスが保てる設定にすることでQCサークル活動が活発化します。
6.改善案の検討/実行
解決すべき問題の真因を追求したら、具体的な改善案を決めて実行に移しましょう。
対策案を出す際には従業員同士で複数の意見を出し合って1つの対策案に絞り込むことが大切です。対策案を選択する際には、以下の選択基準を参考に総合的に考えましょう。
- すぐできる
- お金がかからない
- 効果が高い
- 副作用がない
- 自部署で出来る
それぞれの選択肢を5段階で定量的に評価することによって、最適な改善案を選択することができます。
トヨタ自動車にて人材育成を行われていた石井 住枝氏は、改善とは『知恵を使って、現状の仕事をさらに良くするために継続的に続けるカイゼン』であるとお話しています。ぜひ改善案の検討~実行を進める際には一度、石井 住枝氏によるカイゼンをテーマにした記事をご覧ください。
関連記事:カイゼン思考の土台づくり『カイゼンってなぜ必要?』
7.効果確認
改善策を実施したら、期待していた効果と実際の効果を比較してその差異を詳細に分析します。
効果を確認する際には「誰がやっても」「いつまで経っても」を基準に考えることが重要です。例えばAさんができたことを他の従業員はできなかった場合や、Aさんも1ヶ月後には元通りに戻ってしまったといった場合には効果が出たとはいえません。
会社や部署の現場課題をテーマに選定し「誰がやっても」「いつまで経っても」効果が出る改善案を出せれば、事業成長に貢献できている活発なQCサークル活動であると評価されるでしょう。
もしも期待した効果が得られなかった場合、ステップ3の現状把握に戻り、要因を分析してPDCAサイクルをまわす要領でQCサークル活動を継続しましょう。
8.標準化
実際に効果が出た改善策は、現場の基準として標準化させましょう。
改善策を標準化させることはQCサークル活動において最も重要です。標準化とは作業手順における基準を整えて、二度と失敗しないような再発防止策を立てることです。
特定の部門で「誰がやっても」「いつまで経っても」効果が出る再現性が確認できれば、他部署や他拠点に横展開しても改善効果を上げることが期待できます。
具体的には、全従業員が基準となる正しい作業手順について理解し、作業手順に沿って作業することができる体制を整えるということです。標準化された改善策を実行していくことで永続的に現場を進化させることができます。
標準化を進めるための主な手法として、作業手順書やマニュアルの整備/OJTによる教育が一般的です。一方で文字や口頭で標準手順のような動きを伝えることには限界があり、手順不遵守が止まらないというケースも少なくありません。
そのような現場の方にオススメしたい標準化手法の1つに「動画マニュアル」があります。なぜ標準化に動画マニュアルが効果的か?次章では実際の事例も交えて詳しくご紹介します。
改善策を現場で標準化するには「動画マニュアル」を活用
ここまで、QCサークル活動を形骸化させないために特に重要な「標準化」を進めるためには、動画マニュアルの活用をオススメするというお話をしてきました。
ここからはなぜ標準化に動画マニュアルが効果的か?実際の事例も交えながらご紹介します。
特に製造業の現場では、動画マニュアルを活用するシーンが拡大しています。詳しく活用事例を知りたいという方は、以下の参考資料も併せてご活用ください。
標準化の手段として動画マニュアルが有効な理由
製造現場では標準化を進めるにあたり、紙の作業手順書や文字ベースのマニュアルを展開したり、OJTで直接教えることが多いでしょう。
しかし、文字や口頭で動きを伝えることは難しく作業者ごとに理解度がバラつき、結果的にヒューマンエラーを起こす引き金になります。
こうした課題を解決するための手段として動画マニュアルは非常に有効的です。動画マニュアルは標準作業の動きを撮影してマニュアル化することで、紙や写真では伝わりづらい細かい動きや作業のタイミングをわかりやすく伝えることができます。
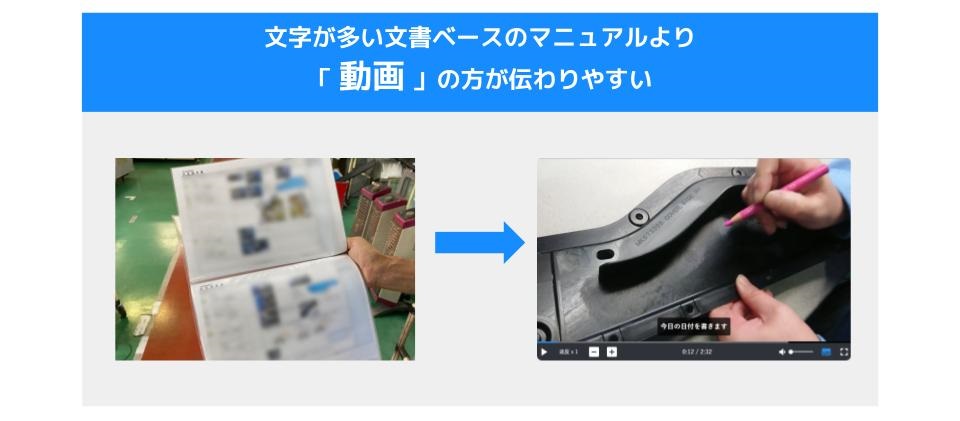
しかし、一般的な動画編集ソフトを使用して動画マニュアルを整備しようとすると、以下のような課題に直面して上手くいかないケースがあります。
- ソフトを使える従業員が限られ、マニュアル作成が属人化/負担が集中する
- 機能が豊富すぎるがゆえに動画マニュアルの作り方を統一化できず、見やすさがバラついてしまう
- 動画本数が増えるにつれて管理工数が増加
- 従業員の閲覧状況が追えず習熟度合いが分からない
- 手順変更に伴う動画マニュアルの改訂工数が増加
このような課題を未然に防ぐためには「誰でもかんたんに動画作成ができ、管理/習熟度チェックまで行えるツール」が必要です。
現場教育システムtebikiを活用することで、このような動画マニュアル活用環境の整備を実現することができます。
動画マニュアル活用には「tebiki」がオススメ
現場教育システムtebikiは、製造業を中心とした現場産業で多く活用されている動画を軸とした教育システムです。
以下のような特徴があり、製造現場の標準化を助ける機能も多数用意しています。
- 動画の撮影はスマートフォン/タブレットでできる
- 撮影した動画の音声は自動で文字起こしされて字幕に
- シンプルな編集画面で作業を熟知する作業者自身でマニュアル作成が可能
- 字幕は100を超える言語に自動翻訳が可能で外国人教育にも活用できる
- 一部言語の字幕読み上げに対応し母国語で学べる環境構築が可能
- 閲覧状況/テスト機能を活用し従業員の理解度を可視化
- スキルマップ機能で従業員のスキル取得状況を可視化
『より具体的に機能を知りたい』という方は、tebikiに関するサービス資料をご用意しています。以下のバナーよりダウンロードしてご覧ください。
動画マニュアルを活用した業務標準化事例
動画マニュアルtebikiを活用して作業手順の標準化を推進した事例として、今回は食品製造会社のタマムラデリカ株式会社の事例をご紹介します。
タマムラデリカは大手コンビニエンスストアの専用工場として、そば/うどん/中華麺や軽食惣菜などの開発製造を手掛けている食品メーカーです。安全な製品をお客様に提供するため製品品質を重要視する一方、従業員の作業を高い水準に標準化させるためにさまざまな現場課題を抱えていました。
現場課題を解決する手段として「動画マニュアルの内製化」に取り組むものの、作成者の属人化に直面し、内製化の課題も解決するためにtebikiを導入したことで、業務標準化を推進することができました。
tebiki導入前に抱えていた課題 | tebiki導入後の効果 |
紙のマニュアルでは細かいニュアンスが伝わらず、マニュアルが活用されなかった。 従業員間や工場間での指導内容に差が生じ、標準化を推進することができていなかった。 外国籍従業員向けに多言語マニュアルが必要だったが、作成に手間がかかっていた。 動画マニュアルを作れる人員が限られており、マニュアル化が追いついていなかった。 | マニュアル作成にかかる時間が1時間から15分まで大幅に削減された。 操作が簡単なため動画マニュアルが作成できるメンバーが3名から20名に大幅に増えた。 翻訳機能の活用で多言語化の手間が解消され、マニュアルの内容も正しく理解されるようになった。 新入社員が動画マニュアルを一通り見るだけで、基本的な作業を行えるようになった。 |
tebikiを活用し、細かい動きやニュアンス/カンコツが伝わるようになったことや、新人社員が動画を見返して復習できるようになり、自学自習が進んだことにより、作業品質が安定し業務標準化が進みました。
タマムラデリカ株式会社のより詳細な動画マニュアル活用事例は、以下のインタビュー記事も併せてご覧ください。
インタビュー記事:動画マニュアル作成時間が75%削減!教育体制を強化し、お客様に喜ばれる商品を提供したい
成功例や失敗例は?QCサークル活動の事例
ここまでQCサークル活動を活性化させる進め方やポイント、標準化を進めるオススメの手法など網羅的にご紹介してきました。
最後に、実際にQCサークル活動が成功した事例/失敗した事例をご紹介します。皆さんがQCサークル活動を進める際の参考情報としてご覧ください。
成功事例
QCサークル活動でコスト削減に取り組むに当たり、改善を達成した成功事例を1つ紹介します。法や条例、協定の排水水質基準を満たしつつ、健全な装置の運転を維持しながら、使用する薬品量を低減させた事例です。
▼選定テーマ
排水処理装置用薬品使用量の低減
▼目標
薬品コストの削減
▼活動内容と結果
プラントから排出された水の内、再使用できない水は、排水処理装置を通じて浄化し、排水水質基準値を満足させて排出しています。
排水は、汚れ度合が高い場合を考慮した薬品注入濃度で処理していましたが、過去の経験と実績、ジャーテストによる適正な薬品注入濃度を確認した上で、最終的には薬品使用量が低減し、コスト削減となりました。副次的な効果として、薬品溶解作業が減り、業務効率化も図れました。
▼活動の評価
従来の運用に満足することなく、適正な濃度を都度テストしながら対策したことで、若年層のレベルアップと中堅層の改善意識が向上しました。
失敗事例
QCサークル活動では、自分のサークル内では解決できないテーマもあります。
特に設備の管理箇所が異なるテーマを選定すれば、他課との調整に時間を費やし、スケジュールが大幅に遅れ、結果的に長期的な取り組みになる可能性があるのです。その失敗した事例をご紹介します。
▼選定テーマ
純水装置採水量増加による再生薬品量低減と運用の改善
▼目標
薬品コストの削減と業務効率化
▼活動内容と結果
大規模プラントを持つ事業所では、配管などの腐食を防止する目的で、純水装置を設置しています。純水装置とは、事業所で使用する工業用水の不純物を取り除き、純粋な水に仕上げる設備です。
純水装置内のイオン交換樹脂は、腐食の要因となるイオンを水素イオンと水酸化イオンに交換する働きがありますが、交換能力にも限界があり、ある一定の通水量になれば停止します。停止した後、工業用薬品でイオン交換樹脂を再生し、健全な状態に戻してから、また採水を開始するというサイクルを繰り返しています。
装置の設計基準は過去の工業用水の水質により採水量を決定していたため、イオン交換能力には余裕がありました。そこで、純水装置の出口水質の悪化を抑えながら、採水量を徐々に上げるテストを実施しましたが、工業用水の水質や再生温度など複雑な条件がからみあい、目標を達成できませんでした。
そのため、他課の協力を得て再度テストを開始しましたが、設備的な不具合とテストのための手動操作が増えたことにより、当初のスケジュールが大幅に伸び、再生薬品量も大幅な削減につながらず、運用の改善にも至りませんでした。
▼活動の評価
机上では、設備の運用や再生手順などを理解したうえで活動しましたが、実装置では、思いもかけないトラブルが発生し、自サークルでは解決できないという判断までに時間がかかり、スケジュールが大幅に変更を要しました。
また。また他課に協力を仰ぐ際には、さまざまな手続きや不具合の改善、調整などに手間がかかったため、コスト削減や業務効率化を目指した目標未達となりました。
テーマに取り組む前の事前確認不足が大きな要因となった目標未達成です。
まとめ
QCサークル活動は、日常業務の問題や課題に対し、小集団グループで継続的に改善を行う活動です。QCサークル活動を通じて、お互いにコミュニケーションを取り合うことで品質改善だけでなく、従業員の能力向上にもつながります。
QCサークル活動は課題解決能力が向上したり、業務効率化によるコスト削減などがメリットとして挙げられる一方で、QC発表会のための活動に陥りやすく形骸化しやすいというデメリットもあります。そのため、QCサークル活動を活発化させるには以下のステップに沿って進めることが重要であるとご紹介しました。
- サークルメンバーの選定
- テーマ選定
- 現状把握
- 原因追及
- 対策の立案/実行
- 効果確認
- トヨタ式メソッドを取り入れた標準化
また、QCサークル活動を進める上で改善策の標準化は品質向上において最も重要であり、標準化には動画マニュアルの活用が効果的です。特にご紹介した動画マニュアルtebikiは誰でも簡単に動画マニュアルが作成することができるため、効果的に標準化を進めることができます。
tebikiのサービス資料は下記のバナーからダウンロードできます。tebikiを活用したQCサークル活動を進めて製造現場の品質向上を進めてみませんか。