かんたん動画マニュアル作成ツール「tebiki」を展開する、現場改善ラボ編集部です。
標準作業とは、特定の業務や作業を効率的かつ安定的に行うために定められた、一連の手順や方法のことを指します。本記事では、標準作業を構成する3要素や、製造現場で活用する「標準3票」など、概要を詳しく解説します。
また、よくある『標準作業が守られない…』という課題に対し、標準作業の徹底に上手くいっている好事例や方法などもご紹介します。
目次
標準作業とは?目的や作業標準との違い
標準作業とは、安全かつ効率的に品質が担保された製品を生産できる作業手順のことです。標準作業を明確にすることで、作業者の安全性確保や作業のムダを省き、製品の品質や現場の生産性向上が期待できます。
標準作業で得られる効果は?明確にする目的やメリット
標準作業を明確する目的として、以下のようなメリットを効果として得られる背景があります。
従業員の不安全行動を防ぎ、労働災害を未然防止する
標準作業とは、作業者の安全性が担保されている作業手順です。安全第一である製造現場において、標準作業を明確にして作業者が守ることは、ミスによる労働災害を予防することにもつながります。
標準作業が明確ではない場合、作業者自身が慣れによる手順の省略などを行い、不安全行動を意図せず行うリスクが生じます。このような不安全行動をさせない目的で、標準作業を明確にする必要があるといえるでしょう。
関連記事:工場の安全対策10選と好事例を解説!製造業の安全宣言例も紹介
ヒューマンエラーによる品質不良を削減する
製造業において品質不良が発生する原因の1つとして、生産活動におけるヒューマンエラーが挙げられます。
標準作業が明確になっていない場合、製造ラインの組立工程で部品を組み付ける順序の誤りや、使用する治具の誤りといった理由で、製品不良を引き起こすリスクがあります。
標準作業を明確にすることで、作業者の違いによる業務品質のバラつきを抑え、ヒューマンエラーによる不良発生を未然に防ぐ効果が期待できます。また、標準作業を明確にすることで改善点が見つけやすくなり、現場の改善活動にも役立てることが可能です。
関連記事:【改善事例あり】製造業における品質不良の原因と8つの対策
作業上のムリ/ムダ/ムラを排除して生産性を高める
「ムリ/ムダ/ムラ」とは、業務や作業プロセスにおける非効率的な要素を指す言葉で、3Mとも呼ばれています。
- ムリ:体力的または精神的に過度な負担がかかる状況
- ムダ:必要のない作業や資源の浪費
- ムラ:作業のばらつきや不均一性
標準作業は、このような3Mが排除されている状態で、一定の生産性が担保されているという前提があります。つまり、標準作業を明確にすることで、作業者による業務品質や業務量が平準化され、製造現場の生産性が向上する効果が期待できます。
関連記事:製造現場の生産性が67%向上した事例や改善方法【指標や計算式も解説】
標準作業と作業標準の違い
標準作業と似ている言葉で作業標準というものがあります。この2つの違いを端的に表すと、以下の違いがあります。
- 標準作業 ⇒ 特定の作業を行う際の一連の手順や方法
- 作業標準 ⇒ 標準作業の実行に必要なルールや管理条件
標準作業は「作業をいかに効率的かつ同じ品質で行うか」を定めているのに対し、作業標準は「一定の品質や安全をいかに確保するか」という点に焦点を当てています。
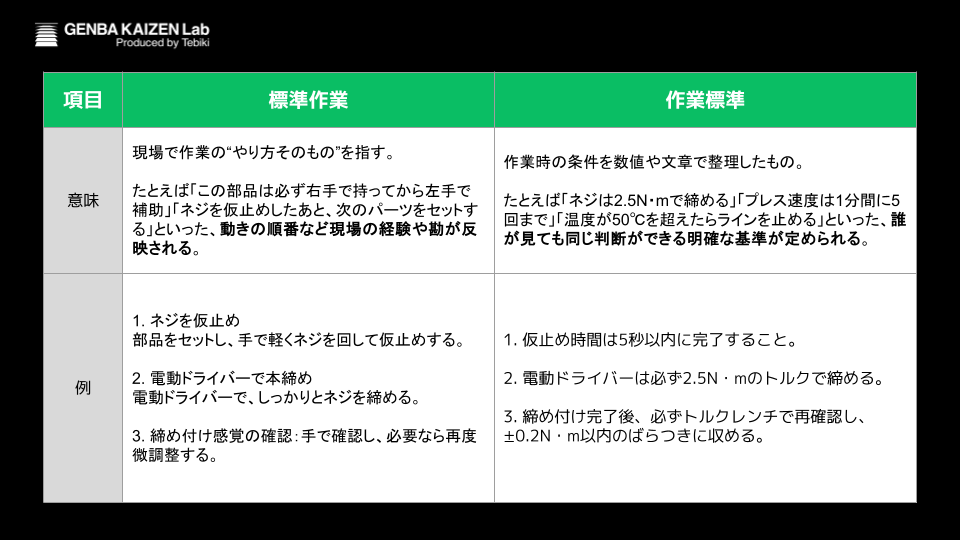
標準作業や作業標準の内容は、作業手順書や標準作業書、製造指図書といった文書で製造現場に展開するケースが多いです。一方で、手順書などの内容が『現場で守られない…』といった現場も少なくなく、手順書整備に工夫が必要です。
>>「“手順書通りにできない”から卒業!作業ルールを守らせる効果的な方法」をPDF資料で見てみる
標準作業を構成する3要素
標準作業は効率的で一貫性のある作業を実現するために、次の3つの要素で構成されています。
これらの要素が明確に定まっていない場合、作業効率・安全性・品質管理が損なわれ、結果として生産性が低下します。したがって、これらの3要素を満たしていない作業は標準作業とは見なされません。
タクトタイム
タクトタイムとは、必要な数の製品を生産・提供するためにかかる時間の目安を指します。タクトタイムは「定時稼働時間÷必要生産数」で求めることができます。
<1時間に10個の製品を生産する必要がある場合> 60分 ÷ 10個 = 6分/個 つまり、必要な数の製品を生産するには、タクトタイムは「1製品につき6分」となる。 |
タクトタイムを明確に設定することで、作業者はどの程度のスピードで作業を進めるべきかを把握できるため、標準作業の要素として大切です。
関連記事:タクトタイム・サイクルタイム・リードタイムの計算と改善方法【意味や違いも解説!】
作業順序
作業順序は、最も効率的に作業を行う際の具体的な手順や順番のことです。正確な作業順序を定めることで、作業者全員が同じ手順で効率よく作業を進められます。
たとえば、食品工場で包装材を容器にセットし、その後に製品を充填するという順序が最も効率よく製品を作れる場合、これが作業順序になります。作業順序が設定されていないと、各作業者が異なる手順で作業を行うリスクがあり、結果として品質のばらつきや効率低下、安全トラブルの発生を招く可能性があります。
作業順序を明確にすることで、このようなトラブル発生を未然防止できるため、標準作業に必要な要素となります。
標準手持ち
標準手持ちとは、作業順序を守りつつタクトタイムを守るために、繰り返し同じ作業を遂するために必要な最低限の仕掛品のことです。仕掛品とは「製造工程の途中にある、未完成の製品」を指します。
標準手持ちの数が多すぎず少なすぎない、最適な数量を設定することで、作りすぎや手待ちといったムダ、工程間での作業の滞りやロスがなくなり、効率的な生産が実現できます。
したがって、標準手持ちを超えて生産しないというルールを徹底するためにも、標準作業として設定する必要があるといえるでしょう。
これら3要素を製造現場で確立するため、「標準3票」という現場帳票を現場で活用していきます。次章からは、この3票の概要について詳しく解説します。
標準作業の確立に必要な現場帳票「標準3票」とは?
標準3票とは、以下3つの現場帳票を総称したもので、標準作業を確立するために作業手順を正確に把握・管理するためのツールです。標準3票はトヨタ生産方式において、標準作業を確立するツールとしても活用されています。
それぞれの帳票類に関する概要やポイントは、トヨタの製造現場を熟知する専門家による無料の解説動画でも詳しく解説していますので、以下のリンクをクリックしてご覧ください。
>>トヨタの現場を熟知する専門家が教える「トヨタ式標準化の進め方」を見てみる(視聴無料)
工程別能力表
工程別能力表とは、各工程ごとの作業能力や達成可能な生産量を示す帳票です。活用することで各工程の処理能力や負荷状況を把握し、改善すべき工程の優先順位を明確にできます。
たとえば、冷凍食品の製造ラインでは、各工程の冷蔵時間と包装速度を工程別能力表に記録します。これにより、どの工程が生産の遅延を引き起こしているかを特定し、冷却時間の短縮や包装設備の交換などの改善策を講じることが可能です。
工程別能力表の活用は、連続的な生産が求められるラインや、多数の工程が関わる製造プロセスに適しています。飲料の製造ラインを例に挙げると、充填工程やラベル貼り工程の生産能力を工程別能力表で分析し、特定の工程におけるボトル詰め速度が全体の生産性に与える影響を評価することができます。
工程別能力表の作り方
工程別能力表を作成する際は、以下の手順をもとに進めると良いでしょう。
- 工程のリストアップ
- 各工程の生産能力の測定・記入
- 生産ライン全体のボトルネック特定
- ボトルネックを解消するための改善計画を立案・実行
例として、自動車部品の製造ラインの場合は材料切断や部品成形などの工程を書き出し、各工程での生産能力を測定します。材料切断の生産能力を「100個/時」のように記入し、最も生産能力が低い工程を特定します。
その後、ボトルネックを改善するために最新機器の導入や作業手順の見直しを行い、改善が完了したら工程別能力表を更新しましょう。このように工程別能力表を作成することで、効率的な生産と安定した品質が達成でき、標準作業を効果的に運用できます。
標準作業組合せ票
標準作業組合せ票とは、作業者の作業をどのように組み合わせ、時間をどう割り振るかを示す帳票です。この帳票を活用し、作業のタイミング・順序・それぞれの作業にかかる時間を視覚的に把握することで、生産ラインの効率化を実現できます。
たとえば、エアコンの組み立てラインでは、標準作業組合せ票を用いて部品取り付け時間や機械の稼働時間、作業者の移動時間を記録します。もし、特定の工程で作業者の移動に膨大な時間がかかっている場合、工程の配置を再設計して効率化を図ることで、全体の生産性を向上させることが可能です。
標準作業組合せ票は、タクトタイムが明確に設定される工程や、人と機械の動きを効率的に組み合わせる必要がある工程に適しています。例として、化粧品の製造ラインでは、標準作業組合せ票を使用して各工程の充填時間や容器の搬送時間を分析し、効率的な作業順序を決定します。
これにより、容器の搬送時間を最小限に抑え、充填工程と次工程の間の待機時間を削減することで、全体の生産効率を向上させることが可能です。
標準作業組合せ票の作り方
標準作業組合せ票を作成する際は、以下の手順を参考にしてみてください。
- 作業の洗い出し
- 作業時間の測定
- 作業順序と組合せの決定
- タイムラインの作成
- 製造ライン全体のバランスの確認・調整
例として、電子部品の組立作業の場合は部品の取り付けやハンダ付けなどの作業を洗い出し、各作業にかかる時間を測定します。その後、作業の順序と組合せを決定し、各作業の開始時間と終了時間を明記したタイムラインを作成します。
最後に、作業の流れがスムーズかを確認し、問題がないかを確認しましょう。このように標準作業組合せ票を作成し、作業の流れを最適化することで、標準作業を運用しやすくなります。
標準作業票
標準作業票は、標準作業の内容を1枚のシートにまとめた帳票です。作業手順や使用する工具、注意すべきポイントを一目で理解できるようにすることで、標準作業を実行しやすくなります。
例として、組立ラインでは標準作業票を活用して各工程の作業内容を記録し、作業者がどの順序で部品を取り付けるべきかを明確に示します。
これにより、組立作業における品質のばらつきを減らし、品質の安定化と生産効率の向上を実現することが可能です。標準作業票は複数の作業者が関わる工程で、作業の流れを統一して効率化を図る場合に有効です。
たとえば、金属部品の加工ラインでは標準作業票を用いて作業者の動きと機械の配置を示し、加工工程全体の効率化を図ります。その結果、作業者が各工程でスムーズに機械を操作できるようになり、作業のムダや停滞を最小限に抑え、全体の生産効率を向上させられます。
このようにして作成された標準作業票を参照することで、作業者は各工程を正確に実行し、高い品質を維持することが可能です。
標準作業票の作り方
標準作業票を作成する際は、以下の手順を参考にしてみましょう。
- 作業内容のリストアップ
- 作業手順の整理
- 作業時間と標準時間の設定
- 使用する工具や材料の記載
- 注意事項の記載
- レイアウトとデザインの調整
例として、鉄鋼工場の検査作業では寸法検査や強度試験などの作業内容をリストアップし、作業の流れがスムーズになるように整理します。各作業にかかる時間を設定し、マイクロメーターや圧縮試験機などの必要な工具・機器をリスト化します。
その後、検査時に注意すべきポイントや安全に関する注意事項を記載し、すべての情報を見やすいレイアウトで1枚のシートにまとめましょう。
このように、標準3票を活用することで標準作業の確立と浸透を進めることができる一方、作業を100%遵守されるということは難しく『標準作業がなかなか守られない…』と、悩むケースも少なくありません。
次章以降では、標準作業が守られない原因や、標準作業の徹底に成功している企業事例を詳しくご紹介します。ここまでご紹介した内容は、専門家による解説動画「トヨタ式標準化の進め方」でも詳しく解説していますので、以下の画像をクリックして本記事と併せてご活用ください。
『標準作業が守られない…』製造現場で不遵守が起きる原因
標準作業の存在や内容が認知されていない
標準作業が現場で認知されていない場合、従業員は正確な作業手順を理解・実行できず、結果として生産性や品質が低下するリスクがあります。
認知されていない主な原因は、適切な情報伝達と教育が不足している点にあります。新しい作業手順の導入は4M変更に該当し、作業ミスが起こりやすい3H(初めて・変更・久しぶり)作業でもあるため、適切な作業手順の共有は必要です。
標準作業の確立が目的による手順変更にも関わらず、情報共有や現場教育が手薄だった場合、手順不遵守による安全/品質トラブルが起こりかねません。標準作業を明確にすることがゴールではないので、どのように浸透させるか?という視点もとても大切です。
製造業の場合、標準作業には「動き」が伴うため、動作を視覚的に分かりやすく伝える手段として、動画マニュアルを活用することも手段の1つです。製造現場で動画マニュアルを活用する有効性は、以下の事例集で詳しくご紹介しているので、クリックしてご覧ください。
>>品質/安全/生産性…製造現場で動画を活用する有効性は?「動画マニュアル活用事例集」を見てみる
目的が理解されていない
標準作業は品質維持や生産性向上、安全性の担保を目的として策定されますが、その意図が現場の従業員に伝わっていない場合、「慣れている手順から変えざるを得ない」と必要性が軽視されがちです。
新入社員や経験の浅い従業員の場合、標準作業は「ただの作業ルール」として認識されがちで、実際の作業にどのように役立つのか?守らないことで起こりうるトラブルを十分に理解していないケースが考えられます。
また、ベテランな従業員でも「慣れている手順から変える煩わしさ」から、意図的に標準作業に沿わないという場合もあります。標準作業がどのような理由で策定され、どのような効果をもたらすのか?具体的に伝えることが大切です。
現場の実情に即していない
標準作業は、現場の安全性や生産性を考慮して明確にしますが、実際の作業者視点から見たときに実情に合っていないという場合は不遵守が起きやすいです。
タクトタイムなど、定量データによって望ましい生産目標を設定する一方で、人員の配置や設備の稼働状況などによって、そもそも達成が難しい恐れがないか考慮する必要があります。この基準で現場と認識に相違があった場合、標準作業を提示されたとしても『現実的ではない』と受け取られ、手順に従う意識が薄れる恐れがあります。
標準作業の内容が現場の現状と乖離していないか?実際の作業ルールや制約と矛盾していないか?など、標準作業を実行する従業員の意見も聞きながら、標準3票の作りこみなどを進めていきましょう。
次章からは、このような手順が守られない課題を乗り越え、標準作業の徹底に成功している企業事例と取り組み内容を詳しくご紹介します。
標準作業の徹底に成功している好事例と方法
標準作業の浸透に成功している企業事例
標準作業の浸透に上手くいっている好事例として、住宅設備・自動車向け合成樹脂加工や産業機器の製造などを行っている児玉化学工業株式会社の事例をご紹介します。
▼インタビュー動画:児玉化学工業株式会社▼
多品種少量生産の現場で製品数が多く、作業手順書の作成や更新が追い付かず、業務内容を正しく現場へ展開する難しさを抱えていました。また、多国籍の外国人従業員を受け入れていることで、OJTなど直接教える難易度からも、標準作業の徹底が進みにくい状況にありました。
そこで同社は、作業手順書の作成/改訂の効率化や外国人従業員の業務理解度向上を目的に、作業手順を視覚的に理解できる動画マニュアルを活用しています。
結果的に、手順書作成工数が紙の1/3に削減されたほか、「動作」をわかりやすく理解できるようになったことで、手順不遵守が9割減り、作業ミスによる品質不良が大幅に改善されています。まさに標準作業の徹底を行った結果、現場改善につながっている好事例の1つといえるでしょう。
同社の取り組み内容は、インタビュー記事でもより詳しくご紹介をしているので、以下のリンクをクリックしてご覧ください。
インタビュー記事:手順書作成の工数は紙の1/3になったと思います。動画で作るのはかんたんだし、学ぶ側にもわかりやすいですよね。
標準作業の徹底で活用されている方法
児玉化学工業株式会社の改善事例でご紹介したように、標準作業を製造現場で浸透/徹底させる方法として「動画マニュアル」が活用されるケースが増えています。
標準作業の浸透に動画マニュアルを活用することで、主に以下のようなメリットがあります。
- 新人や外国人でも手順を「視覚的」に学ぶことができる
- OJTなどトレーナーによる指導内容のバラつきが起きない
- 4M変更時の手順書改訂と共有が効率的にできる
一方で、動画と聞くと『編集が難しいのでは…?』と感じるかもしれませんが、映像編集未経験者でもかんたんに使用でき、導入半年で400動画を作成した事例もあるツールが「tebiki現場教育」です。
標準作業の徹底を実現する手段として、動画マニュアルの作成だけでなく現場教育の実行を手助けする機能が取り揃えられています。
- 字幕は100カ国超の言語に瞬時に自働翻訳:作業者が母国語で学べる
- レポート機能で閲覧状況を可視化:未閲覧者へのフォローが可能
- 教育計画や教育予定の策定:標準作業の教育を計画的に実行
- 教育記録やスキルマップの整備:標準作業に関するスキル習得状況を可視化
上記の機能はあくまでも一例ですが、標準作業の浸透に必要な教育訓練の計画から、標準作業に関係する従業員のスキル習得状況の可視化など、標準作業の浸透を計画的に行うことができる機能が揃っています。
tebiki現場教育の具体的な機能やプラン、活用事例などを知りたい方は、以下のリンクをクリックしてサービス概要資料をご覧ください。
>>かんたん動画マニュアル「tebiki現場教育」の概要を詳しく見てみる
【補足】標準作業の徹底に向けた改善の進め方
標準作業を徹底する場合、基本的には以下のような進め方でPDCAを繰り返していくことが定石です。
従業員教育を実施する
従業員に対して標準作業の内容や目的をしっかりと教育することで、従業員がその重要性を理解し、適切な方法で作業を行うようになります。
そのため、新人が入社した際には標準作業の目的や重要性を説明する研修を行い、標準作業の手順を基礎から確認するOJTを実施しましょう。定期的な教育を通して、従業員が手順を正確に把握することで、作業効率や品質の向上を実現できます。
また、教育を実施する際はただ標準作業を教えるだけでなく、なぜその作業手順を守ることが重要なのか、具体的な例を挙げて説明することが大切です。例として、過去に作業手順を守らなかった場合に発生したトラブルやミス、または手順通りに作業を行ったことで得られた成果を挙げると、従業員はその重要性をより深く理解できるでしょう。
標準作業が守られているかチェックする
標準作業の遵守状況を定期的にチェックする体制を整えることで、誤った手順での作業による品質不良や事故を防止できます。具体的には、管理者や監督者が現場を巡回し、作業者が標準作業に従っているかを確認することが有効です。
問題を発見した場合、手順に誤りがあることや、その場で適切な手順に戻すよう指導することで、作業のばらつきを抑えられます。また、作業者が自分の作業を自己確認できるように、チェックリストを提供することも効果的です。
チェック体制を整えることで、従業員は標準作業が常に監視されていることを意識し、手順を遵守する意識が高まります。ただし、厳しいチェック環境では過度なプレッシャーがかかる恐れがあるため、作業者がリラックスして作業できるよう、監視方法や指導の仕方に注意する必要があります。
標準作業の定期的な見直しと更新を行う
作業者のフィードバックをもとに、現場での作業手順と標準作業を比較し、不適切な点や改善の余地があれば標準作業を更新します。また、標準作業が古くなったり、現場の状況が変わったりした場合は、新しい技術や手法を取り入れてアップデートします。
このように定期的に見直しと更新を行うことで、現場にもっとも即した標準作業を浸透させることが可能です。たとえば、製造現場で新しい機械が導入された場合は、従来の標準作業がその機械に適しているかや、従業員がこれまでと同様に操作できるかを確認します。
標準作業の改訂が必要な場合は、新しい機械に適応した内容に修正することで、機械導入後もスムーズに標準作業を徹底できます。さらに、現場の作業者と協力して更新を行うことで、現場の意見を反映した標準作業が完成し、従業員のモチベーション向上にもつながります。
標準作業を見直す際には、更新後の標準作業を速やかに全従業員に周知し、新しい手順が確実に定着するようにサポート体制を整えることを心がけましょう。
標準作業を可視化する
標準作業を視覚的に表示し、現場で常に確認できる環境を整えることも大切です。たとえば、作業エリアに標準作業のフローチャートや手順書を掲示し、誰でもすぐに参照できるようにします。
また、作業台や機械の近くに作業手順のポスターやマニュアルを配置し、作業中に簡単に確認できるようにします。このような取り組みを行うことで、作業者は常に手順を確認しながら作業を進められ、標準作業の遵守率を向上させることが可能です。
可視化する際には、作業エリアに合わせたサイズ・配置・色を選定し、作業者が自然に目に入るように工夫しましょう。
マニュアル/標準作業手順書を整備する
作業手順・使用する工具・材料・注意事項など、作業内容を詳しく記載したマニュアルや標準作業手順書を整備すると、作業者の業務品質を一定にして作業を進めることが可能です。医薬品の製造ラインの場合、使用する器具や化学薬品、品質管理のチェック項目などを記載します。
このようなマニュアルや標準作業手順書を作成すると、作業のばらつきが抑えられ、製品の品質が向上します。作成する際は、現場の実態をよく理解し、作業者が実際に使用する場面を想定して作成することが重要です。
特に、複雑な手順の作業やリスクの高い作業については、詳細な説明や安全対策を盛り込むことが求められます。
注意点として、作業手順書は「作って終わり」ではなく、従業員に内容が正しく伝わり、遵守されることがゴールです。にもかかわらず、手順書はあるものの読まれずに形骸化しているというケースもよく耳にします。
そのような事態を避けるべく、現場改善ラボでは「現場で使われる作業手順書のポイント」を詳しくまとめたハンドブックをご用意いたしました。以下の画像をクリックし、是非ご覧ください。
【補足】標準作業における3つのタイプと違い
標準作業は業務の特性に応じて、次の3つのタイプに分類されます。
タイプ1
タイプ1は、先述した「3要素」に沿って毎日繰り返し行うことができる作業を指します。タイプ1の作業はタクトタイムという目標があり、かつ標準化された手順に沿って進めることを目的としているため作業効率を高めやすく、業務品質が安定しやすいことが特徴です。
例として、電子部品製造工場におけるプリント基板への部品実装作業などが考えられます。この作業は、作業者が特定の配置順序に従い正確に部品を取り付ける必要があるため、タイプ1に分類されます。タイプ1では手順を厳守することが求められるため、後述する「標準3票」と呼ばれる帳票が活用されます。
これにより、作業者は正しい手順に沿いながら、効率的かつ正確に作業を進めることが可能です。
タイプ2
タイプ2は、繰り返し行うものの、状況や条件によってサイクルタイムが変わる作業を指します。
タイプ2の作業は、多品種生産や組み合わせの種類が多いケースによくみられます。そのため、作業者ごとに作業量が異なる場合や、標準作業が定めにくい場合があります。そのため、タイプ2の作業においては、タクトタイムとサイクルタイムが一致するような生産体制を目指すとよいでしょう。
例として、顧客からのカスタムオーダーに基づいた家具の製造などが考えられます。顧客からの要望に応じてさまざまなデザインや仕様の家具を臨機応変に製造するため作業内容が一定なことが少なく、サイクルタイムや手順が一律に設定できない場合が多いといえるでしょう。
タイプ3
タイプ3は、繰り返しの作業を行わない工程でよくみられます。例として、緊急点検やクレーム・トラブル対応などイレギュラーな業務や作業が該当します。
そのため、タイプ3の作業では、作業にかかる全体の負荷量(作業量)が、計画通りの時間内に収まることが望ましいでしょう。
まとめ
この記事では標準作業の概要や重要性、現場に定着させるためのポイントについて解説しました。標準作業を徹底することで、現場のばらつきを解消し、トラブルの発生を防ぐことが可能です。
また、標準作業が適切に守られていると、品質や生産性が向上し、コスト削減にもつながります。そのため、現場のトラブルが多いと感じている方は、この記事を参考にしながら教育方法や帳票を改善してみてください。
効率よく標準作業を整備・定着させるためには、動画マニュアル「tebiki」の活用がおすすめです。作業内容を動画で見せることで、直感的にやるべきことや業務の流れが理解できるため、正しい手順で作業できるようになります。
さらに、tebikiには従業員のアクセス状況や人気コンテンツを見える化する「レポート機能」や、習熟度を管理する「テスト機能」が搭載されており、効果的に標準作業を現場に定着させられます。動画マニュアル「tebiki」の資料は、以下の画像から無料でダウンロード可能ですので、ぜひ詳細をチェックしてみてください。