かんたん動画マニュアル作成ツール「tebiki」と、かんたんデジタル帳票「tebiki現場分析」が運営するWEBメディア・現場改善ラボです。
TPM(Total Productive Maintenance)とは、製造工場や設備のロスをゼロに近づけ、企業の利益を生み出す管理システムです。
生産システムを支えるそれぞれの要素の効率を最大化し、コストの削減や品質の向上を通じて、生産性や企業の競争力を強化することを目的としています。
本記事では、TPMの基礎から具体的な活動内容である「8本の柱」、削減すべき「16大ロス」について解説します。TPMの実際の活動例や効果的な活動のコツ、役立つツールも解説しますので是非最後までご覧ください。
目次
TPMとは?
TPM(Total Productive Maintenance)は、1971年に社団法人日本プラントメンテナンス協会(JIPM)によって提唱され、特に製造現場における「全員参加の生産保全」として広く知られている管理手法です。主に「総合的生産保全」と訳されます。
日本プラントメンテナンス協会では、以下のように定義されています。
製造工場および設備におけるロスをゼロにすることを目的として、主に自動化ラインを中心とした製造業やプラント産業における設備管理と生産性維持のためのマネジメントシステム。
ここでは、TPMの基礎知識として以下の3点を解説します。
- TPMの基本理念
- TPMの目的
- TPMとTQMの違い
TPMの基本理念
TPM(Total Productive Maintenance)は、企業全体の体質を強化し、持続的な成長を目指すための以下5つの柱で構成されています。
▼TPMを構成する基本理念(5つの柱)▼
儲ける企業体質づくり | ロスを極限まで削減し、生産システムを効率化する |
予防哲学(未然防止) | ロスやムダを未然防止することで、利益を生み出す |
全員参加(参画経営・人間尊重) | 全従業員が主体的に改善活動に取り組む |
現場現物主義 | 実際の現場で事実に基づく議論を重視する |
常識の新陳代謝 | 既成概念を打破し、新しい考え方も積極的に取り入れる |
TPMでは上記5つの柱のうち、「儲ける企業体質づくり」と「予防哲学」が特に重要視されています。「儲ける企業体質づくり」と「予防哲学」の効果をより発揮できるよう、他3本の柱が推奨されています。
TPMの目的
TPMの目的は、設備の維持や改善により生産活動のあらゆる「ロス」を未然に防ぎ、生産システム全体の稼働率を高め、企業を「設ける企業体質」に変えていくことです。特に、設備の故障や生産性の低下、製品不良の発生を防ぐことで、安定した生産ラインの維持を目指します。
TPMは、生産システムを支える「設備」が最大限に効率的に稼働することを通じて、コストの削減や品質の向上を実現し、企業の競争力を強化します。予防保全や改善活動を通じて、企業が持続的に利益を生み出す仕組みの構築が期待できます。
TPMとTQMの違い
TQM(Total Quality Management)とは、製品・サービスの提供までのプロセスやシステムの維持向上、改善・革新を行うことで、「総合的品質管理」と訳されます。
TPMとTQMを比較すると、TPMは「設備」、TQMは「品質」に注目している点が大きな違いです。
TPMは主に「設備の稼働率最大化」に重点を置き、設備管理を中心に全員参加で改善活動を行います。設備の故障や不良品発生の予防に特化しており、製造ラインの安定を図ることが主な目的です。
一方、TQMは「品質管理」にフォーカスし、製品の品質を全社的に向上させることを目的としています。TQMでは、品質の向上を通じて顧客満足を達成し、組織全体の成長を目指します。
TQMについて詳しく知りたい方は、以下の別記事もご覧ください。
関連記事:TQM(総合的品質管理)の目的は?進め方やトヨタ式などの事例を解説!
TPMを構成する「8本の柱」とは?
TPM(Total Productive Maintenance)は、製造現場でのロスを削減し、生産性を最大限に引き出す「8本の柱」と呼ばれる活動で構成されます。
ここでは、それぞれの内容について具体的に解説します。
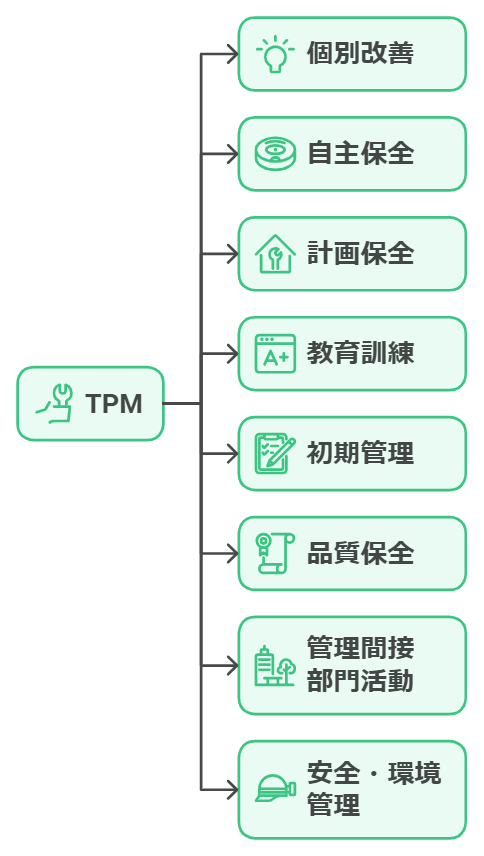
個別改善
個別改善は、設備や生産プロセスの中で発生するロスを発見し、解決にむけて改善する活動です。例として、レス機で頻発するチョコ停(短時間停止)について原因分析を行い、センサーの取り付け位置を変更して誤作動を防止するといったことが考えられます。
『TPMの「16大ロス」』でも後述するように、小さなロスでも積み重なることで大幅なコスト増加や生産遅延につながります。ロスを見過ごすと、無駄なコストや設備の停止時間などが発生し、結果として利益が減少します。
そのため、発見したロスについて個別に改善することで重大なトラブルに発展することを予防し、全体的な生産性を向上させることが求められます。個別改善は、短期的には細かい対応に見えるかもしれませんが、積み重ねることで設備の稼働率を飛躍的に向上させ、生産性を最大化する大きな力となります。
自主保全
自主保全とは、現場のオペレーターが設備の点検やメンテナンスを自主的に行う活動です。例として、プレス機の金型交換後に金型の取り付け部分や周辺の清掃を行い、金属片や油汚れが残らないようにすることで、次回の生産トラブルを防ぐ活動などが挙げられます。
日常業務を通し、最も設備に接する機会が多いといえるオペレーターが保全活動を日常的に行うことで、設備の状態を常に把握し、大きな故障を未然に防げます。自主保全により、設備の停止時間を最小限に抑えることが可能です。
オペレーターが設備の異常に気づかないままだと、故障が重大化し、生産ライン全体が停止するリスクが高まります。オペレーターが毎日、機械の作動音や振動、部品の摩耗をチェックすることで、故障の予兆を見逃さずに対処できます。
自主保全の7ステップ
自主保全は、TPM活動の中でも重要な位置を占める活動です。現場のオペレーターは日常的に設備と向き合っているため、異常や問題にいち早く気付ける立場にあります。
そのため、オペレーター自身が保全活動に積極的に取り組むことが設備の寿命を延ばし、生産効率の向上につながります。
自主保全は、主に以下の手順に沿った活動で進められます。
ステップ | 内容 |
---|---|
1. 初期清掃 | 設備を清掃し、初期の異常や故障を確認する。 |
2. 発生源対策 | 異常発生の原因や対応の優先順位を特定し、作業効率を向上させる。 |
3. 基準の作成 | 点検基準を作成し、設備の最適状態を維持する。 |
4. 総点検 | 設備全体を徹底的に点検し、不具合を洗い出す。 |
5. 自主点検 | オペレーターが自主的に設備の点検を行い、改善点を発見する。 |
6. 標準化 | 点検作業を標準化し、全員が同じ基準で保全を行えるように整備する。 |
7. 自主管理 | 保全活動を継続し、設備の安定稼働を維持する。 |
計画保全
計画保全は、設備の故障や劣化を予測し、定期的なメンテナンスを計画的に行う活動です。
例として、コンプレッサーのフィルターを半年ごとに交換することで、圧縮効率を維持しながらトラブルを未然に防ぐといった活動が考えられます。
近年ではAI技術などを活用して、設備の状態をリアルタイムで監視する予知保全も行われています。
設備の突発的な故障は全体の生産効率に大きな影響を及ぼしますが、定期的な保全活動を計画的に行うことで、安定した稼働が維持され生産性が向上します。
教育訓練
教育訓練は、従業員が設備の保全や改善に必要な知識とスキルを身につけるための活動です。特にオペレーターや保全担当者をはじめとする現場の従業員が、自主保全や計画保全に取り組むための技術を習得することが重要です。
例として、オペレーターに対して設備の基本的な構造や動作原理を学ぶ機会を設けることで、異常の早期発見能力を高めることができます。また、保全担当者には部品交換や調整作業の効率的な手順や、トラブルシューティングの技術を習得させることで、設備の稼働率向上に貢献できるようになります。
教育訓練を効果的に進めるには、単なる座学だけでなく、実際の設備を使った実地訓練が欠かせません。
たとえば、設備が停止している時間を活用して清掃や点検の実演を行うことで、理論と実践を結びつけた学習が可能になります。また、トラブル発生時のシミュレーションを実施することで、迅速な対応力を養うことも効果的です。
適切な教育訓練がなければ、スキルや技術が身につかないことに加え、問題が発生しても適切な対処ができず、結果として設備の故障や生産性の低下につながることがあります。教育訓練は、全従業員がTPMを行える土台作りであり、生産効率の向上に直結する重要な要素です。
初期管理
初期管理は、新しい設備や製品を開発・導入する際に、設計段階からロスの発生を防ぐ活動です。生産プロセスが開始される前にどのようなロスが起こりうるかを予測し、対策を講じることで稼働後のトラブルを防ぎます。
ロスを予測せずに導入すると、稼働後に頻繁なトラブルが発生し、生産効率が大幅に低下します。
例として、新しい設備を導入する際に設備の設置場所や動線を事前に検討し、主要な操作パネルや材料供給箇所を作業エリアの近くに配置するなど、作業者のムダな動きというロスを発生させないレイアウトを計画することが挙げられます。
初期管理のもう1つの重要な取り組みとして、設備の操作手順や保全計画の標準化があります。新しい設備が現場に導入される際、操作手順や保全方法が明確でないと、稼働中にオペレーターのミスや保全の遅れが発生する可能性があります。
そのため、分かりやすい手順書やマニュアルを作成することで、スムーズな立ち上げを実現できます。
複雑な内容でもわかりやすく伝えられ、標準化が進むマニュアルについては、後述する『「教育による標準化」と「現場記録の可視化」はtebikiで解決!』で詳しくご紹介します。
品質保全
品質保全は、製造工程における品質問題を未然に防ぎ、安定した製品品質を維持するための活動を指します。これは、設備やプロセスに起因する不良品の発生を防ぐことを目的とし、設備と品質管理を一体化させた保全活動です。
不良品が発生すると、修正や廃棄によるコストが増加し、納期遅延や顧客満足度の低下につながります。品質保全は、このようなリスクを防ぐための活動です。
品質保全の活動では、不良品が発生する原因を設備の状態や作業手順の視点から徹底的に分析し、根本的な対策を講じることが求められます。品質検査を行い、不良品を流通させないという取り組みももちろん重要ですが、品質不良の原因を根本から断ち切ることが重要です。
例えば、設備の劣化や部品の摩耗が品質に影響を及ぼす場合、日常的な点検や予防保全を通じて早期に問題を発見し、対処することが重要です。また、作業手順や設備の条件を標準化することで、操作ミスや条件のばらつきによる不良品発生を防ぐことも行うと良いでしょう。
管理間接部門活動
管理・間接部門活動は工場の運営をサポートし、業務全体の効率を改善するための活動です。
製造現場を直接支援する間接部門(例:生産管理部門、工場総務部門など)が対象となることが多く、これらの部門は製造ラインそのものを直接操作するわけではありませんが、その運営やサポートを最適化することで、全体的な生産効率の向上に貢献します。
主な活動例として、生産現場の5S(整理・整頓・清掃・清潔・躾)活動の推進や、在庫管理の最適化、物流の効率化などが含まれます。
5S活動は単なる「片付け」ではなく、作業が効率的に行われ、ムダな動きや時間が排除されている状態を目標とした活動です。
5S活動の具体的な実践方法や、生産性向上につなげるコツを知りたい方は、以下の画像をクリックし専門家による講演動画をご覧ください。
安全・環境管理
安全・環境管理は製造現場での労働災害や環境負荷を最小限に抑えるための活動です。安全教育や定期的な設備点検を行い、作業者の安全を守るとともに、環境への配慮を行います。
労働災害が発生すると、従業員の健康や命に影響がおよび、企業の信頼にも悪影響を与えます。また、環境への配慮は持続可能な経営のために欠かせません。
そのため、安全・環境管理では、リスクアセスメントの実施による労働災害や環境破壊リスクの低減、定期的な安全教育の実施などを行うとよいでしょう。
安全教育は企業が行うべき義務でもあり、労働災害を防ぐ重要な要素です。一方で、「安全教育を行っているにもかかわらず、ヒヤリハットや労働災害が減らない…」とお悩みの方も多いのではないでしょうか。
効果のある安全教育には、従業員の安全意識が継続することが欠かせません。
現場改善ラボでは、労働安全コンサルタントによる「従業員の安全意識が継続する効果的な安全教育の取組み」を解説した動画をご用意しております。本記事と併せ、是非ご覧ください。
TPMの「16大ロス」
TPM(Total Productive Maintenance)では、生産現場で発生するロスを16のカテゴリに分類しています。具体的な分類は以下の通りです。
設備効率化に関する8大ロス
設備効率化に関する8大ロスは、設備の故障や不具合、稼働効率の低下によって発生します。
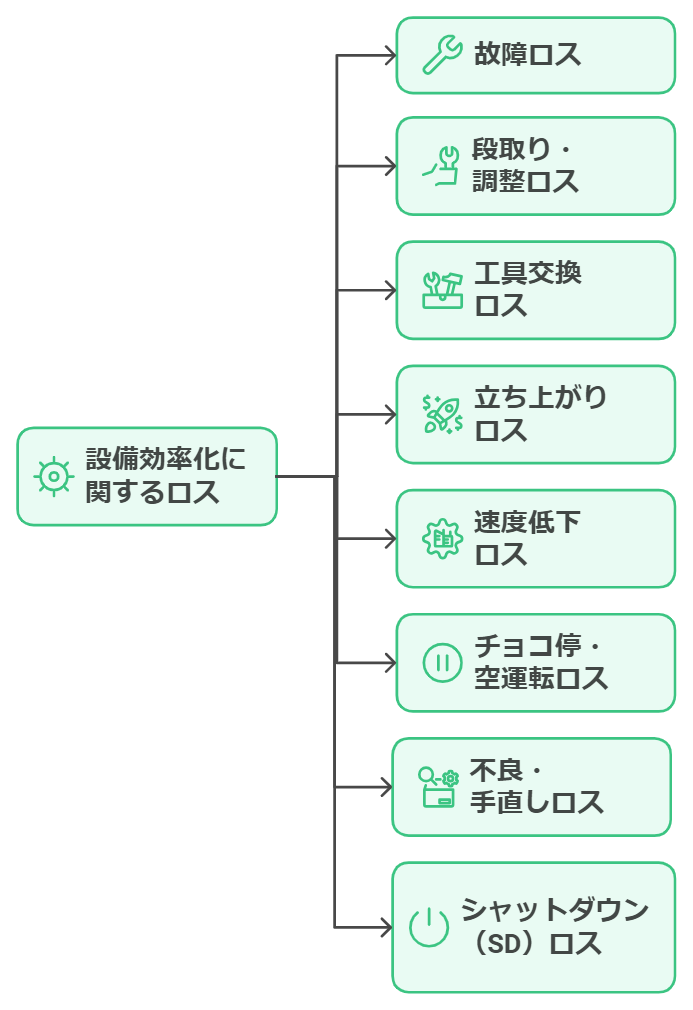
ロスの内容や影響、例について以下の表にまとめました。
ロスの名称 | ロスの内容・影響 | ロスの例 |
---|---|---|
故障ロス | 設備が突然停止することで生産が中断し、復旧や作業の遅れ、不良品増加といったロスが発生 | 主要な生産設備の故障修理に3時間かかり、予定よりも製品の仕上がりが遅延した |
段取り・調整ロス | 製品の切り替えや調整作業に時間がかかり、生産の立ち上げが遅れることで発生するロス | 新製品ラインの立ち上げに2時間を要し、その間に不良品が発生し続けた |
刃具交換ロス | 生産過程で使用される工具や刃具の交換に伴い、作業が一時的に止まることで発生するロス | 刃具を交換するために生産ラインが1時間停止し、その前後に不良品も多数発生した |
立上がりロス | 設備を起動してから、安定して良品を作るまでにかかる時間。特に初期段階ではトラブルが発生しやすい | 設備を再起動した後、30分以上品質が安定せず、不良品が続出した |
チョコ停・空転ロス | 短時間の機械停止によって発生するロス | コンベアでの製品詰まりによりラインが数分間止まり、生産が遅れた |
速度低下ロス | 設計時の生産速度と実際の稼働速度が異なることで発生するロス | 設備能力として本来1時間に100個生産できるはずだったが、速度低下により80個の製造に留まった |
手直し・不良ロス | 不良品が発生した際の修正作業に伴う時間的ロスや、廃棄することで生じる物量的なロス | 不良品の発生により手直しに1時間を要し、その間に他の作業が進まなかった |
シャットダウン(SD)ロス | 設備の定期メンテナンスや調整時に生じるロス。特にメンテナンス後の再調整時にもロスが発生することが多い | 定期点検のために1日稼働を止めた後、再稼働時にトラブルが発生し、さらに2時間の停止を要した |
人の効率化に関する5大ロス
人の効率化に関する5大ロスは、作業者の動作や作業の順序、管理体制に起因します。具体的には以下の5つです。
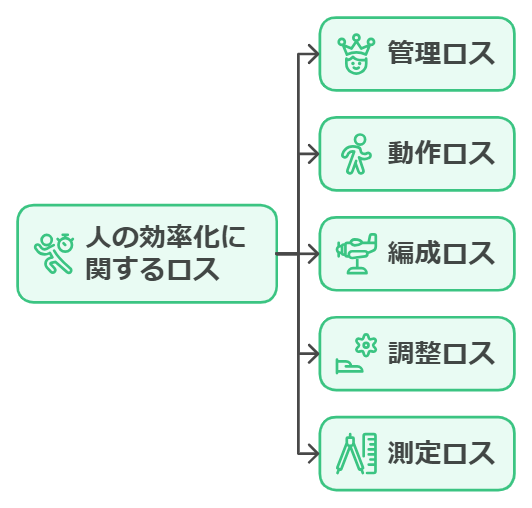
ロスの内容や影響、例は以下の通りです。
ロスの名称 | ロスの内容・影響 | ロスの例 |
---|---|---|
管理ロス | 材料の準備待ちや指示の遅れ、設備の修復を待つ時間など、管理上の要因で発生するロス | 材料が届かず、作業員が2時間以上待機した |
動作ロス | 作業者のムダな動作や、作業手順の非効率によって発生するロス | 道具を取りに行くために何度も行き来することが多く、1日の作業効率が10%程度低下した |
編成ロス | ラインのバランスが取れておらず、一部の作業者が手待ち状態になることから発生するロス | 作業ラインで一部の作業員が余る一方で、他の作業員は忙しすぎて、全体の効率が悪くなっていた |
自動化置き換えロス | 自動化すれば省力化できる作業を手作業で行っているために発生するロス | 自動化すれば50%の時間削減が見込まれる製品検査について、すべて手作業のまま行っている |
調整測定ロス | 品質管理のために頻繁に測定や調整を行うことで、設備の稼働が一時的に止まることによるロス | 1時間ごとに製品の品質測定が必要で、そのたびに設備が一時停止し、生産効率が下がる |
原単位の効率化に関する3大ロス
原単位とは、製品を生産するために必要な原材料、エネルギー、時間を意味します。原単位の効率化に関する3大ロスは以下の通りです。
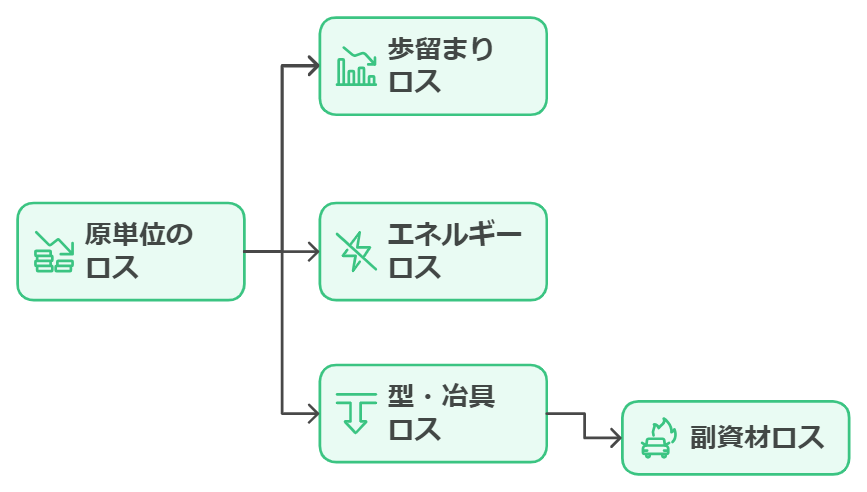
ロスの内容や影響、例は以下の通りです。
ロスの名称 | ロスの内容・影響 | ロスの例 |
---|---|---|
歩留まりロス | 原材料のムダや加工効率の低さにより発生するロス | 100kgの原材料を投入しても、製品として有効なものは80kgで、20%が廃棄される |
エネルギーロス | 生産活動に必要なエネルギー(電気、水、燃料など)のムダ使いによって発生するロス | 設備が不要に長時間稼働し続けているため、電力消費が無駄に増加した |
型・治工具ロス | 生産に必要な型や治工具のメンテナンスや交換に時間がかかることで発生するロス ※冷却材や潤滑油など、副資材(部品や材料以外)のロスも含まれる | ・生産用の型が頻繁に故障し、修理や交換に時間がかかるため、作業の遅れが常態化している ・加工機の交換のたびに、潤滑油の交換作業が必要 |
TPM活動の事例
TPM活動の事例として、以下の4社を紹介します。
- 旭化成ケミカルズ株式会社
- 小川工業株式会社
- サカタインクス株式会社
- オリエンタルモーター株式会社
旭化成ケミカルズ株式会社
旭化成ケミカルズ株式会社は、合成樹脂や化学製品を製造・販売する化学メーカーです。同社千葉工場は、設備の経年劣化や技術伝承の課題を抱えていました。また中国やアジア地域の競争力向上も大きな脅威でした。
このような問題を解決し、国際競争力を強化するため、2004年にTPM(Total Productive Maintenance)活動を導入しました。
具体的には、オペレーターによる自主保全や個別改善、定期的な計画保全を実施し、環境安全部会によるパトロールとリスクアセスメントを強化しました。また、従業員のスキル向上を図る教育訓練も充実させました。
結果として、無災害30年を達成し、生産性向上やコスト削減、品質維持に成功しています。
小川工業株式会社
小川工業株式会社は、主に金属加工や機械部品の製造を行う製造業の企業です。同社は、教育訓練が属人的で継続性がなく、人材育成に課題を感じていました。そこで、教育の一環としてTPM活動を導入。
TPM導入後は、ISO品質環境マネジメントシステムに基づいた全社的な教育訓練を計画的に実施し、OJTやOff-JTを通じてスキルの向上に取り組んでいます。
具体的には、技能検定やQC検定の資格取得を支援し、報奨金制度を導入したことで、従業員のモチベーションも向上しました。
結果として、機械保全技能士72名が育成され、設備故障は18年前の10分の1以下に減少し、生産性も向上しました。売上は約2倍に増加し、従業員数も1.3倍となる成果を上げています。
参考元:厚生労働省「人材育成事例045」
サカタインクス株式会社
サカタインクス株式会社は、印刷インキや関連製品を製造・販売する化学メーカーです。
同社は、競争の激しい事業環境に対応できるような企業体質の強化が課題でした。そこで1998年にTPM(全員参加の生産保全)活動を導入し、生産システム全体におけるロスをゼロにする取り組みを開始しました。
活動内容は「個別改善」「自主保全」「計画保全」「品質保全」など幅広く展開され、また同社が理想とする生産方式である「サカタインクス・ダイレクト・プロダクション・システム(SDPS)」の確立も目指しました。
TPM活動の効果として、労働生産性の向上や設備故障の減少、品質クレームの低減が達成され、さらにCO2排出量削減や廃棄物リサイクル率の向上など、環境面でも大きな成果を上げています。
参考元:サカタインクス株式会社「TPM」
オリエンタルモーター株式会社
オリエンタルモーター株式会社は、グローバル競争が激化する中で、設備の老朽化や生産効率の向上が課題でした。これに対応するため、2000年代初頭にTPM(Total Productive Maintenance)活動を導入し、生産ラインの安定稼働と効率化を目指しました。
活動内容としては、「自主保全」「計画保全」「品質改善」「個別改善」に重点を置き、全従業員が参加する形で展開。TPM活動の効果としては、設備故障件数の大幅な削減や、作業効率の向上が実現されました。また、不良品の減少や品質の安定化が達成され、結果として生産コストの削減と納期の短縮にも成功しています。
効果のあるTPM活動には「教育による標準化」と「現場記録の可視化」がマスト
TPM活動の成功には、全員が自主的に参加し、業務の標準化と現場でのデータを可視化することが重要です。具体的な方法として「重複小集団活動」がありますが、以下2つのポイントに絞って解説します。
- TPMを全員で自主的に取り組むには「重複小集団活動」を
- 重複小集団活動には「教育による標準化」と「現場記録の可視化」が欠かせない
TPMを全員で自主的に取り組むには「重複小集団活動」を
TPM活動は、全員が参加し、自主的に取り組むことで最大の効果を発揮します。各従業員が「自分の設備を自分で守る」という意識を持ち、改善を積極的に行うことが求められます。ここで有効となるのが「重複小集団活動」です。
「重複小集団活動」は、組織内のさまざまなレベルのメンバーが横断的にチームを組み、互いに協力しながら課題に取り組む仕組みです。重複小集団活動では、現場の意見やアイデアが経営トップに届きやすく、全員が自主的に参加できる環境が整います。
また複数の小集団で活動を行うため、現場で発生した問題や改善点を即座に反映できるのも特徴です。結果的に、現場の知識とスキルを向上させ、TPM活動の持続的な成功を支えられます。
TPMには「教育による標準化」と「現場記録の可視化」が欠かせない
重複小集団活動によるTPM活動には、正確な記録データと教育による改善策の標準化が不可欠です。ここでは以下の2点について解説します。
- 分析に使える正しい記録データ
- 教育による改善策の標準化
分析に使える正しい記録データ
TPM活動でロスを削減するには、十分な量を満たした定量的なデータと分析が必要です。たとえば、設備停止時間や故障頻度を正確に記録し、これを集計・分析することで、どの設備が最もロスを引き起こしているのかを特定することができます。
このように、計測したデータにもとづいた分析なくては、改善のための正確な対策は導けません。特に、重複小集団活動のように様々なデータを数多くの人が活用するような場面では、共通のデータをすぐに共有できることが求められるでしょう。
正確なデータを確保するには、計測器やデジタル記録ツールを用いたリアルタイムでのデータ収集のほか、製造日報や点検表など、日々のデータを記録した「現場帳票」を活用することが理想です。現場帳票には、作業状況や機械の稼働状況、作業者の動きなどの情報が含まれており、これらを定期的に見直すことで、過去の傾向や問題点を把握することができます。
たとえば、製造日報を通じて特定の工程での作業遅延や設備の不具合が頻発していることが分かれば、その原因を探るための追加分析が可能になります。
製造現場の「カイゼン」につなげる、正しいデータ活用の進め方やデータ収集の具体的な手順については、以下の専門家による動画でも詳しく解説しています。本記事と併せ、是非ご覧ください。
教育による改善策の標準化
分析し状況を把握したとしても、それはゴールではなく、あくまで「前段階」です。分析を通じて課題を洗い出し、対策を考え改善までつなげることが目標です。さらに、対策が実際の作業手順や工程として定着し、改善が持続的に行われることが成果につながります。
そのため、分析と対策の検討を行った後は、現場に落とし込んで「標準化」することが重要です。たとえば、新しい作業手順を導入した後、手順をすべての作業員が一貫して実行できるように標準作業書を作成し、現場での教育訓練を行う必要があります。
TPMを行う際は、分析部分にだけ注力するのではなく、その後の実行と定着までを見据えた全体的なプロセス=標準化を考慮することが求められます。
標準化はTPMのほか、作業効率や品質の向上にも欠かせない要素です。一方で、作業手順書やマニュアルを整備しても、なかなか改善が見られないというお悩みもよく耳にします。
現場改善ラボでは、効果的な標準化の進め方について専門家が解説した動画もご用意しております。本記事と併せ、是非ご覧ください。
次章からは、現場記録の可視化と教育による標準化を後押しする、便利で効果的なツールについてご紹介します。
「教育による標準化」と「現場記録の可視化」はtebikiで解決!
TPMを活用した現場改善を助けるツールとして、動画マニュアルとデジタル帳票が有効です。
ここではおすすめのツールとして、動画マニュアル「tebiki」と、デジタル帳票ツール「tebiki現場分析」を紹介します。
教育には「動画マニュアルtebiki」
標準化はTPMに必要な要素のみならず、製造業における重要な課題です。しかし、現場での教え方や内容のムラ、ベテラン作業員のノウハウの伝達不足が原因で、標準化が進まないことがあります。
この課題を解決し、標準化をサポートするツールとして、「動画マニュアル」が挙げられます。動画による視覚的な情報伝達は効率的な学習を促進し、現場での負担を軽減することが可能です。
ここでは動画マニュアルについて、以下の2点を解説します。
- 標準化に動画マニュアルが有効な理由
- tebikiなら簡単に動画マニュアルを作成!
標準化に動画マニュアルが有効な理由
動画マニュアルの最大の利点は、教育のばらつきをなくせることです。動画という同じ教材を使うことで、誰でも同じ情報を学ぶことが可能なため、「AさんとBさんで教え方や教える内容に差が生じてしまう」といった状況を回避できます。
また、動画であれば3次元的な動きを含むため言語化が難しい複雑な作業や、ベテランならではのカンコツ=暗黙知も、見たそのままの動きを視覚的に学べます。
紙のマニュアルでは伝えきれない細かいニュアンスや、実際の動きを伝えることが可能になり、作業や業務のムラを解消することが期待できます。
さらに、動画であれば場所や時間を問わず繰り返し視聴できるため、OJTやマンツーマンの教育に頼らず、効率的に標準化を進められます。たとえば、新入社員が何度も同じ動画を見て学ぶことで、現場での教える手間が省け、作業の標準化が進みます。結果として、現場に負担をかけず、効率的に標準化を実現できます。
動画マニュアルによる教育効果や、標準化に役立つメリットについては、以下のハンドブックでも詳しくご紹介しています。本記事と併せ、是非ご覧ください。
tebikiなら簡単に動画マニュアルを作成!
動画マニュアルの中では、現場に嬉しい機能が多数搭載された「tebiki」がおすすめです。
▼動画マニュアル作成ツール「tebiki」紹介動画▼
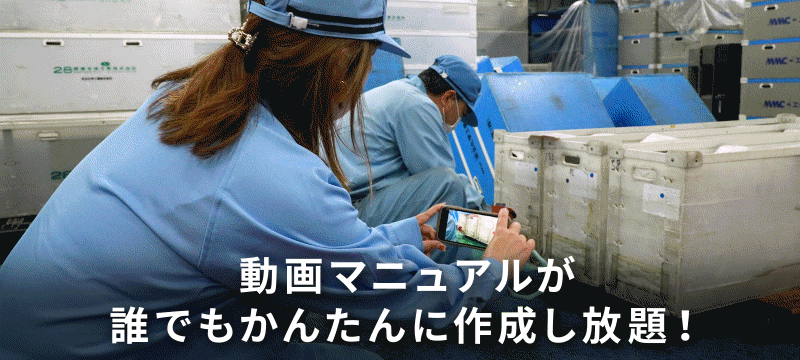
tebikiの1番の特長は、誰でも簡単に動画マニュアルを作れる点です。シンプルな操作画面だからこそ、動画編集経験がない方でも直感的に操作することができます。
編集に時間がかかる字幕生成を自動で行う機能も搭載されているため、1つの動画をサッと15分程度で作成している企業の方も多いです。tebikiを使えば、以下の画像のようにたった3STEPで動画マニュアルを作成できます。
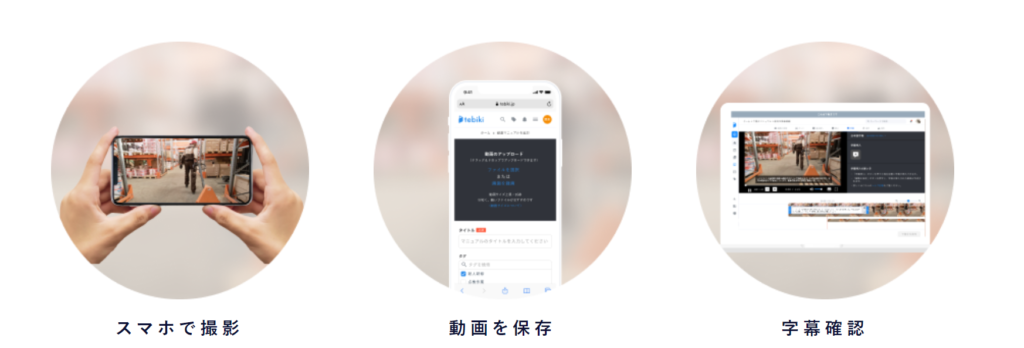
またtebikiには、マニュアルの視聴状況がわかる組織レポート機能や、マニュアルの内容をテストとして出題できる「テスト機能」が備わっています。
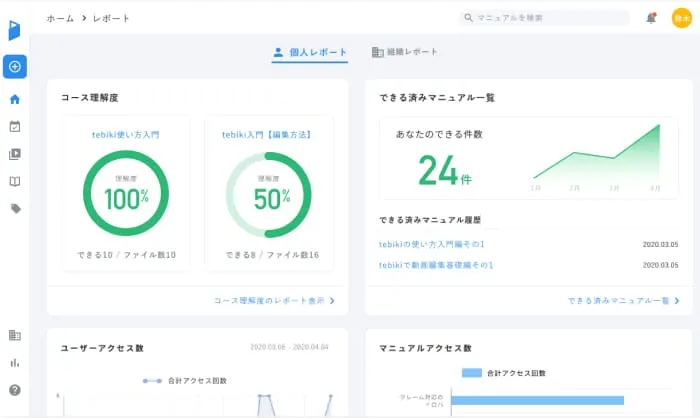
ユーザーごとのマニュアル視聴状況が可視化されるため、標準化の習熟度や浸透具合を把握しやすくなります。たとえば、作業員がどの程度マニュアルを視聴し理解しているかを確認することで教育の効果を定量的に評価し、必要に応じて追加の指導を行うことが可能です。
実際に、複雑な作業工程もこのツールを使うことで効果的に標準化し、現場の効率を向上させた事例があります。
tebikiの機能詳細や導入の費用対効果、実際の導入事例については、以下のハンドブックでも詳しく解説しています。標準化や現場教育を効果的に改善したい方は、是非ご覧ください。
現場記録には「tebiki現場分析」
現場改善につながるIEには、正確なデータの記録とその迅速な分析が不可欠です。しかし、手書きやExcelを使用した帳票管理には多くの課題があり、現場での記録が負担となることが多いでしょう。
そこで、デジタル帳票を導入することで記録作業を簡素化し、データの正確性を向上させることがおすすめです。
ここではデジタル帳票について、以下の2点を解説します。
- デジタル帳票が現場記録の可視化に役立つ理由
- tebiki現場分析ならリアルタイムで正しいデータを集めて分析できる!
デジタル帳票が現場記録の可視化に役立つ理由
手書きやExcelでの記録では時間がかかり、記録漏れや誤記入が発生しやすいという課題があります。また手書きの場合は字が汚くて読めない、書き方や書く量に差があるといった問題もあり、データの統一性を欠くことが多い傾向があります。
一方、デジタル帳票を使用すると、タブレット上で簡単にデータを入力できるため記録作業が迅速かつ正確に行えます。デジタル帳票により、手書きの際にかかる時間や誤記入のリスクを減らし、一定水準のデータを集めることが可能です。またデジタル帳票には入力必須項目を設定できる機能があるため、記録漏れを防ぐ仕組みが構築できます。
現場改善ラボでは、これからデジタル帳票の導入を検討される方に向け、デジタル帳票の主な機能やデジタル化の進め方など、帳票のデジタル化に役立つ情報をまとめたハンドブックを以下にご用意いたしました。本記事と併せ、是非ご覧ください。
tebiki現場分析ならリアルタイムで正しいデータを集めて分析できる!
帳票のデジタル化には、「tebiki現場分析」がおすすめです。
tebiki現場分析とは、現場帳票の作成・記録・承認・分析が簡単に行えるシステムです。本サービスを活用することで、IEに必要な現場データを効率的に収集・分析することができます。
tebiki現場分析はスマートフォンやタブレットでの入力に特化したわかりやすい操作画面を採用しており、難解な研修を受けずとも誰でも簡単に帳票を記入し、編集できます。また紙では難しかった画像記録もデジタルで簡単に行えるため、現場の状況を視覚的に把握することが可能です。
他にも、「帳票のピンどめ」により使用頻度が高い帳票を優先して表示させる機能や、毎回の記録で共通する内容の入力を省略できる「定時記録」の機能を使うことで、日常的に発生する進捗管理業務をよりスムーズに記録することも可能です。これにより、現場の状況をリアルタイムでデジタルデータとして記録し、分析に役立てることが可能です。
実際に、1日あたり2時間を要していた集計作業が1分に短縮され、記録データをもとに設備トラブルの予防措置が実行できるようになった事例もあります。
さらにtebiki現場分析には収集したデータを簡単にグラフ化する機能を備えており、視覚的に進捗状況を分析できます。分析機能をTPMと併用して活用することで、現場に潜むボトルネックや異常、ムダを定量的なデータをもとに簡単に特定し、改善につなげることが期待できるでしょう。
tebiki現場分析の機能詳細や導入サポート体制については、以下のハンドブックでも詳しくご紹介しています。デジタル帳票で現場データを可視化し、分析や改善につなげたい方は是非ご覧ください。
TPMを理解して効果的な現場改善に活用しよう【まとめ】
TPM(Total Productive Maintenance)は、製造現場のロスをゼロにし、生産効率を最大化するための全員参加型の活動です。基本理念は「災害ゼロ」「不良ゼロ」「故障ゼロ」を目指し、企業全体の体質を強化することにあります。
活動の柱は「個別改善」「自主保全」「計画保全」など8つに分かれており、特に自主保全はオペレーターが自ら設備を守ることで、故障を未然に防ぎます。さらに、TPMでは「16大ロス」を削減し、生産性向上を実現することを目標としています。
効果のあるTPMには、全員が参加し、自主的に取り組む「重複小集団活動」が有効ですが、これには「教育による標準化」と「現場記録の可視化」が欠かせません。
「教育による標準化」と「現場記録の可視化」には、本記事でご紹介した動画マニュアル「tebiki」と、デジタル現場帳票「tebiki現場分析」が有効です。
詳しい情報については、以下の画像をクリックして詳細な資料を是非ダウンロードしてください。