明治時代創業の繊維会社が挑む技術伝承!
ITテクノロジーを駆使して伝統芸を若手へ伝達
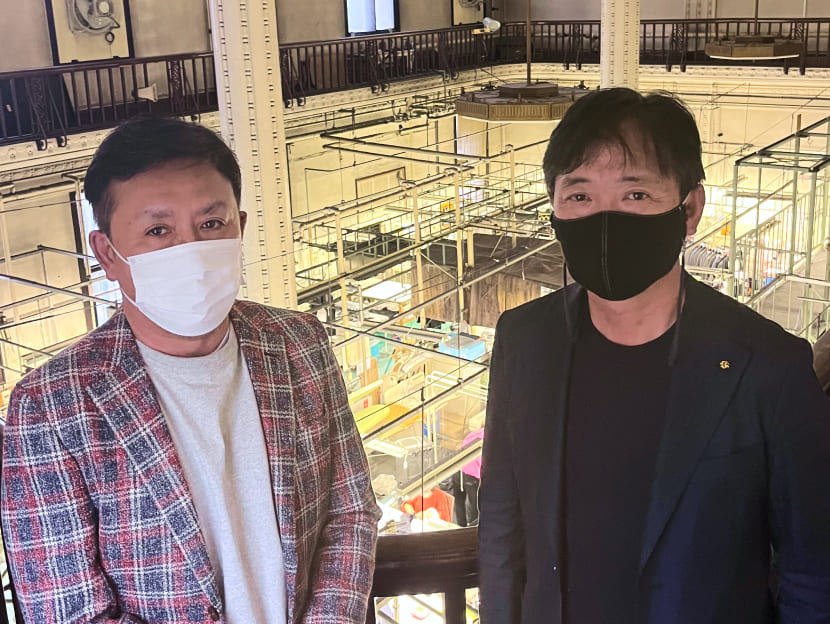
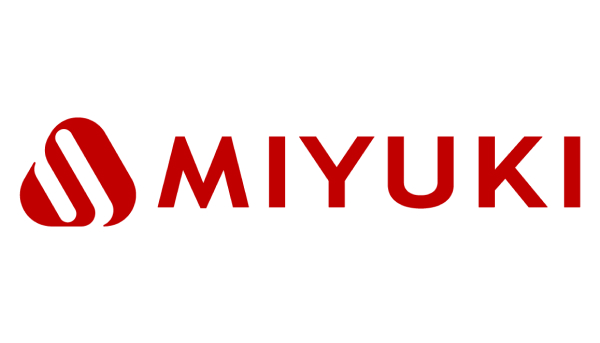
御幸毛織株式会社
- 業種 :製造
- 従業員数 :101~500名
お話を伺った方:生産統括部 小幡 晃義様
-
課題
- 若年層への技術伝承
- 職人技術の属人化
- 業務/作業のニュアンスが紙では伝わりにくい
- 紙マニュアルは作って終わりで使われない
-
効果
- 技術伝承が進むようになった
- 属人的な業務が減っていっている
- 動画で細かい作業や微妙なニュアンスが伝わりやすくなった
- 動画を見たか、業務ができるようになったか教育管理ができるようになった
研修の効率化、業務標準化、技術伝承など幅広い業務において全国規模でtebikiを活用中
貴社の事業内容と、tebikiの対象業務を教えてください。
小幡さん: 弊社は1905年に創業し、テキスタイル事業、オーダースーツ事業、ユニフォーム事業などを、紡績から縫製、販売まで一貫して服飾に携わっています。また、紡績工場や加工工場、縫製工場、販売店など全国に拠点を持っています。tebikiは、小樽の縫製工場では現場のカン・コツなどの業務ノウハウの可視化や業務標準化、長崎工場では研修者の工程実習の動画化による職人技術の共有、四日市工場では、新人教育のSOP用動画として活用されています。
もう少し具体的にお話すると、例えば四日市工場で行っているトップ染という工程では、機械操作と熟練の技の連携が必要となります。その熟練の技を持つベテラン社員が行う業務の動きを動画に納めて、ノウハウを凝縮させた動画を作成し、若手へいつでもtebikiの動画で技術を学べるようにしました。次の整理工程では、頻度が低く作業手順を忘れがちな大型機械の定期点検や整備業務などのメンテナンス業務を動画化し、作業ミスや漏れなどのヒヤリハット案件の削減を目的に、業務の辞書的な役割をtebikiが担っています。また、整理工程でも熟練の技が求められる100%手作業の生地補修の作業においてもノウハウの可視化と共有をtebikiで行っています。そして、100%外注している製織工程でも、外注工場に長期研修に行った技術者が持つ業務ノウハウを可視化して製織技術を社内に展開して、継承できる仕組み作りにも着手しています。
こういった取り組みはtebikiを活用しながら、ノウハウの可視化と共有は若手社員中心で進められ、ベテラン社員のフォローで成り立っています。 一見バラバラの工程から進めているように思うかもしれませんが、“やってみなはれ”の精神で、できるところから着手して、自分達で課題を見つけて、業務ノウハウを会社全体に展開して共有しています。
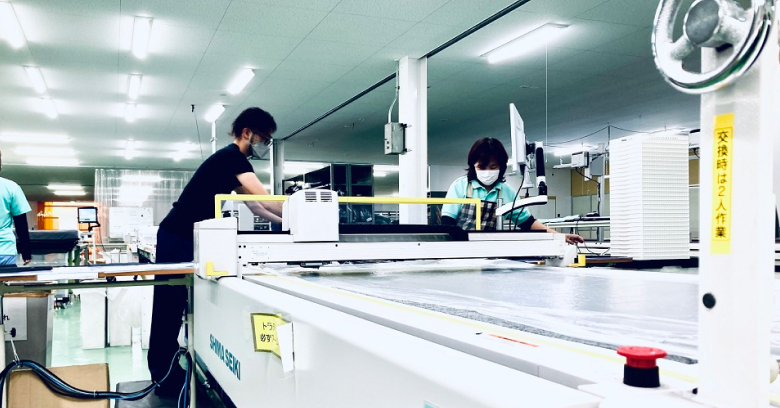
90年代の厳しい外部環境で新卒採用がストップしていたため、若手への技術伝承が喫緊の課題に
どのような課題があったのでしょうか?
小幡さん: 少し繊維産業の歴史の話となりますが、戦後、繊維産業は国を興す産業として一世を風靡しましたが、しかし、90年代以降衣料品の低価格化が進み、中国を中心とした海外生産に国内市場を席巻されました。ただ、一方で品質にこだわり、高付加価値を持つオーダースーツなどの衣料品に関してはその影響が限定的で、弊社は国内生産でも生き残ることができました。しかしながら、その生き残りの中で、2005年から2014年まで新卒などの採用をストップさせていた時期があり、社員の年齢分布は40代から50代に偏っています。
弊社は品質のこだわりから、機械に頼った製造工程だけではその高い品質を担保することはできず、職人の微妙なコントロールによって成せる品質であることから、40代と50代のベテラン社員の技をいかに若手へ継承するか、それが喫緊の課題でした。弊社の繊維事業は糸をつくる紡績工程から染色工程、製織工程、整理工程、そして洋服を縫う縫製工程まで、服の完成まで一貫した生産体制であることから、1つ1つの工程で職人の技が駆使されており、いずれかの工程で低い品質で作業が行われると全体工程に影響が及んでしまい、全ての工程で高い品質を担保する職人の技の技術伝承が経営課題でした。
モノづくり現場における技術ノウハウの継承とDXの融合を目指して
tebikiの導入方法と、その効果を教えてください。
小幡さん:Tebiki導入前は紙ベースでの教育だったため、なるべく分かりやすく、相手に伝わるようになんて書こうかと苦心しながら、紙マニュアルに文字を起こして、マニュアルを作り、OJTを交えながら実務作業を教えていました。
紙ベースのマニュアルだと、苦心して作成した文章でも手の細かな動きや微妙なニュアンスを相手に伝えにくく、せっかく作成したマニュアルもあまり使われていませんでした。 動画SOPの案は、元々小樽の工場長からのアイディアでした。紙マニュアルでは伝えきれない自社独自の縫製技術を残したいという希望が昔からあり、動画で残していきたいという強い想いがありました。しかしながら、動画ソフトは一定のITスキルが必要で、動画マニュアルにしてしまうと、作成担当者が一部に限定されてしまう。そうなってしまうと、特定の担当者に業務が集中してしまい、マニュアルの更新も途絶えてしまうだろうと思い、決断できずにいました。
そんな時、Facebookでtebikiの広告を見て、これなら直感的に操作でき、簡単に動画マニュアルが作れると思い、すぐにTebikiさんにコンタクトをとりました。思っていたとおり、操作は簡単で誰でも作成でき、紙マニュアルを作成する時のように文章を考える必要もなくなり、作成工数は3割~4割削減できて、紙では重要な手順のみしか伝えられなかったが、動画なら、伝わりにくい細かいニュアンスも伝わりやすくなりました。
そして、動画マニュアルによる現場教育が始まると、効果は多岐に渡るものでした。まず、作業手順が伝わりやすくなったことでミスやトラブルが少なくなり、こうしたら危ないというのが文字ではなく、視覚的にも伝わることで、安全教育などにも効果が出ていると感じます。
各工場に関して申し上げると、まず、裁断センターがある四日市工場では、メンテナンス作業の教育がtebikiに置き換えたことで、ベテラン社員など一部の従業員しか行えなかったが、誰でも動画を見ながらメンテンナンス作業できるようになり、業務の属人化が減りました。その他、補修作業といった細かい作業についても、外部で研修した成果、スキルを動画マニュアルで社内に共有することができ、技術伝承が進みやすくなりました。このように業務ノウハウを社内で簡単に共有/伝達できる手段が作れたことで、全員が外部で研修する必要がなくなり、コストの削減も年間百万円という規模感で進みそうです。
次に、長崎工場については、高付加価値の服飾工程があり、この工場だけの技術だったものが、他の工場にも伝承されつつあります。服飾の個性を出す高付加価値の作業はベテラン社員のみが持つもので、往来、直接工場に往訪する必要があったが、今は動画マニュアルで技術伝承が行えています。ベテラン社員の移動は簡単ではないし、動画に置き換わって、業務効率化の面でも効果を感じます。
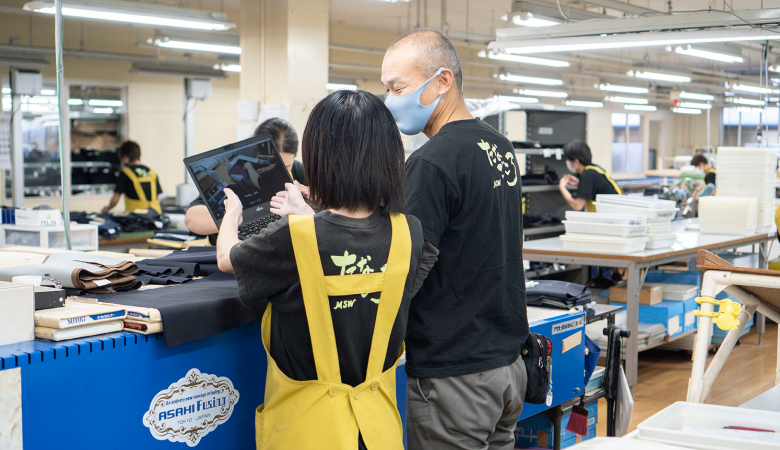
若手とベテラン社員の一体チームで、技術伝承という経営課題を乗り越える!
動画マニュアルを社内に浸透させるコツを教えてください。
小幡さん: 動画マニュアルのプロジェクトは、若手社員が中心となり、推進役として普段の業務やOJTをどんどん動画に収めていきました。ベテラン社員の業務を後ろからスマートフォンなどで撮影する感じです。もちろん撮影するだけでは、良い動画マニュアルは作成できませんので、撮影後に業務のポイントや話した内容以外にどんな字幕や説明文を付けるかなど、若手からベテラン社員に聞きに行き、定期的にミーティングやも開催してベテラン社員の業務ノウハウが詰まった質の良い動画マニュアルを作り上げていきました。
若手は技術を早く身につけたいというモチベーションが強く、動画などITリテラシーが高い。一方で、ベテランは業務で忙しく、教えたいが、OJTにはなかなか業務リソースを割くことができない。こういった状況を見ながら、プロジェクトチームを発足させました。
このチームが見事にハマり、職人気質なベテラン社員も若手社員からのコミュニケーションに気持ちよく対応してもらえて、動画マニュアルの作成が進み、スムーズに社内に浸透していきました。
暗黙知は動画に置き換えられないとよく言われたりしますが、私個人としては、動画で暗黙知の業務やノウハウも動画で伝達できると考えています。技術伝承は教える側と教わる側の2つの側面があります。
カギとなるのは、教わる側だと思います。動画に業務ノウハウを詰めた後、教わる側がその業務ノウハウを習得する努力が不足してしまうことがあると思います。暗黙知のような職人技は見るだけでは習得できません。何度も繰り返しその業務を行うことでだんだんと動画にあるような動きができるようになるのです。暗黙知、その他形式知的な業務やノウハウを動画として蓄積し、共有できる体制までは確実に作れると思います。つまり、技術伝承は、教える側の指導方法だけでなく、受け手側の努力も同時に必要になるということです。これが暗黙知の伝承においてカギとなっているのだと思います。
動画マニュアルtebikiは単なる動画マニュアル作成ツールではない
最後に、tebikiのオススメポイントを教えてください!
小幡さん: まず、直感的に動画マニュアルの作成が可能であることです。動画マニュアルを自社で作成しようとするとかなりの業務負荷となりますが、tebikiなら、動画マニュアルの作成も共有も負荷少なく簡単に開始できます。また、特にスマートフォンなど多様なデバイスから視聴できて、社員が動画を見たか、業務ができるようになったかが一目瞭然で、さらに理解度テストでしっかりと教育の進捗が確認できる機能まで備えており、tebikiは単なる動画マニュアルの作成ツールではありません。
加えて、TebikiのCS担当者が手厚くサポートしてくれます。例えば、他社で効果があった事例や動画作成のコツ、どの業務から動画マニュアルを作成していくかなど全体的な進め方など、定例会で教えてくれるし、気になったところもすぐに聞くことができます。
SOPの水平展開、ヒヤリハット案件のさらなる削減、テスト機能を活用した徹底した習熟度管理による業務標準化
今後のtebikiの活用の展望をお聞かせください。
小幡さん: 今後の展開は、3つ考えています。まず1つ目は、現場へタブレットを配布して動画マニュアルを現場により近づけて、動画SOPを完成させて、あらゆる部門・現場でSOPをtebikiの動画に置き換えて業務効率化を進めながら、属人化したOJTを減らして、OJTの効率化を図る。
2つ目は、普段は潜在的に潜む危険性を動画が再現し訴えることができる動画のメリットを活用し、現場の事故によるトラブルや被害を視覚的に理解し、“べからず動画”の作成して、ヒヤリハットの削減や現場の安全教育を進める。
3つ目は、テスト機能を活用して作業者の習熟度を可視化してマイスター制度をつくり、技術習得の促進を進める。tebikiは動画マニュアルの作成だけにとどまらず、業務ノウハウを可視化して、貯蓄し、共有できる社員の教育プロセスを抜本的に変革できるツールです。使い方によっては圧倒的に業務を効率化したり、伝承しにくい暗黙知、習熟度や業務品質のバラツキ、技術伝承など長年抱えてきた現場の課題を解決できると考えています。
また、動画マニュアルtebikiの直接的なお話ではありませんが、人事制度の改定を行い、技術や資格を評価する制度を設けて、技術や資格と給与を連動させるようにしました。タレントマネジメントシステムを導入する予定で、tebikiのテスト機能とタレントマネジメントシステムと連動させることで、公平な人事評価を行う社内評価システムを構築する予定です。遠い将来ですが、全社員に多能工を推進し、スキルや資格、評価の可視化ができるようにしていきたいと考えています。
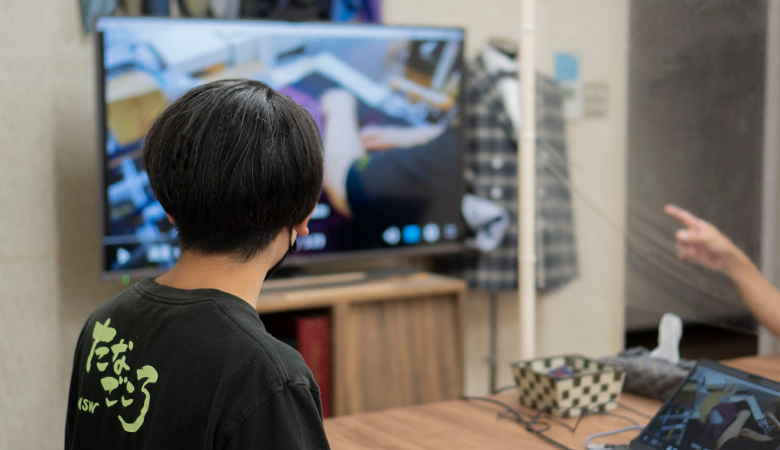