品質保証部門と製造部門がONEチームで取り組んだ業務標準化と技術伝承
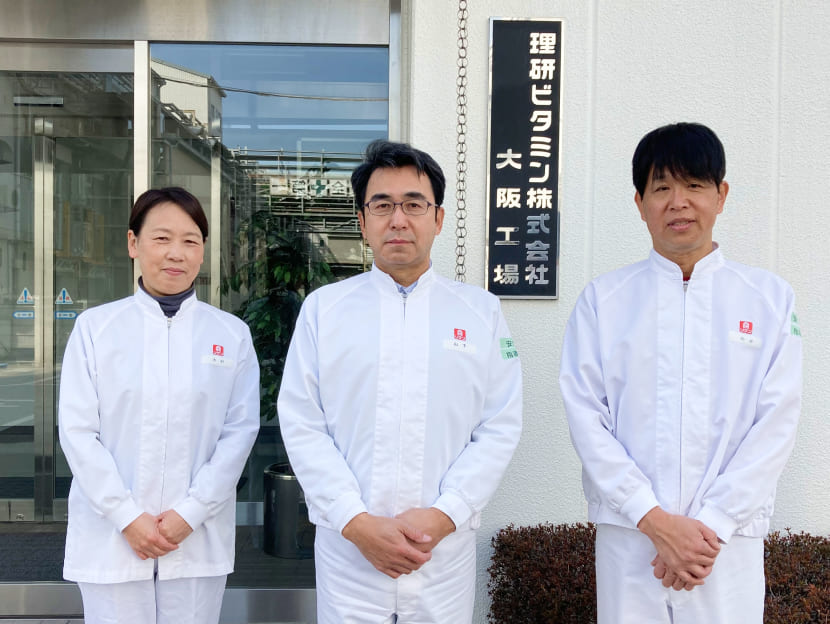
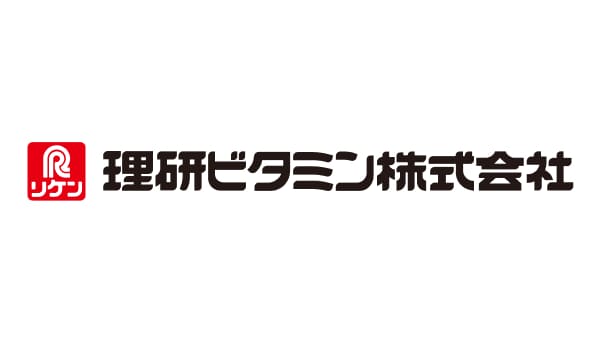
理研ビタミン株式会社
- 業種 :製造
- 従業員数 :501-1,000名
お話を伺った方:大阪工場 工場長/山下 俊幸様、品質保証本部品質保証部 大阪工場担当品質保証課 品質保証係 係長/岡田 真也様
-
課題
- 紙マニュアルでは伝えきれない
- 教育内容や教育の質にムラがある
- 全員に教育の機会を設けるのが難しい
- 紙マニュアルの文字情報だけでは技術伝承が進まない
-
効果
- 細かい作業や微妙なニュアンスが伝わりやすくなった
- 業務が伝わりやすくなったので教育のムラがなくなった
- 全員に教育の機会を設けられるようになった
- 業務の動きや音など文字以外の情報も伝えられるので、技術伝承が進むようになった
大阪工場の現場業務だけでなく品質管理や生産技術などの製造現場の周辺業務でも動画による教育が行われ始めています。
貴社の事業内容と、tebikiの対象業務を教えてください。
山下さん:弊社は理化学研究所からビタミンA部門を引き継ぐ形で、1949年8月に設立した会社です。スーパーマーケットなどで見かけたことがある方がいらっしゃるかと思いますが、「ふえるわかめちゃん®」や「リケンのノンオイル 青じそ」、「わかめスープ」、粉末、顆粒だしなどの調味料、加工食品などに含まれる乳化剤などを製造しています。
生産拠点は日本国内の5工場とグループ会社のほか、アメリカ、中国、マレーシアでも製造しており、それぞれの工場ごとに製造品目が違う多様な生産体制を敷いています。
岡田さん: 動画マニュアルtebikiは、主に乳化剤を製造している大阪工場において、業務に動きが伴う製造部門を中心とし、品質管理や生産技術などの現場業務の周辺領域、さらには安全教育、FSSC22000などの全体的な研修、点検業務やメンテナンス業務など幅広い業務における人材教育で活用されています。
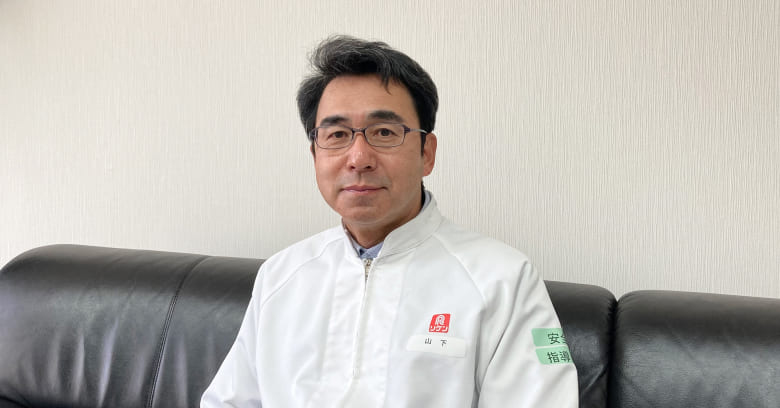
現場の課題は人材教育絡みが多く、業務品質を上げていくには人材への投資が不可欠
どのような課題があったのでしょうか?
岡田さん:大阪工場では、3つの課題がありました。1つ目は、紙マニュアルでは伝えきれない内容がある。2つ目は、教育内容や教育の質にムラがある。3つ目は社員全員に十分な教育の機会を設けるのが難しい、というものでした。
まず前提として、製造部門では生産性向上・業務効率化のための機械化が進んでいます。しかし、その機械の点検業務、メンテナンス業務など人のオペレーションも多数あり、機械と人の混合オペレーションとなっています。品質保証部門でも、分析はHPLCやGCなど機器分析による機械化が進んでいますが、全ての分析業務が機械化されているわけではなく、また文書作成業務など人のオペレーションが主となる業務が存在します。
この状況は理研ビタミンだけでなく、製造業においてはどの会社も同じだと思いますし、今後も人のオペレーションが完全にゼロになることはないと思います。また機械化されたのは比較的単純な作業であり、複雑な業務はどうしても人によるオペレーションに集中します。したがって、生産性向上において、機械化といったハード面だけでなく、人材教育によるソフト面への投資も重要だと考えています。
1つ目の「紙マニュアルでは伝えきれない内容がある」についてですが、紙マニュアルによる業務手順の伝達だと、どうしても伝わりにくく、業務のバラツキが生まれてしまうことがあります。例えば、品質保証部門での分析手順書に「フラスコに試薬Aと試薬Bを入れて、よく振り混ぜる」というのがあります。この「よく振り混ぜる」という文字の情報だと、人によっては一方向だけに振る、縦方向に振る、小刻みに振る、といったバラツキが生まれてしまいます。
この情報を文字ではなく動画で説明すると、実際に「振る」様子を確認することができ、バラツキが生まれることはありません。つまり、動きが伴う業務を文字で説明することには限界があり、紙マニュアルでは文字量を増やすという手段や画像を用いるなど情報の追加が必要になってしまう為、マニュアルの作成工数が一気に上がってしまいます。
次に「教育のムラ」の問題ですが、大阪工場は24時間稼働しており、部門によっては日勤と夜勤の交代勤務や、フレックス勤務、時短勤務、在宅勤務など多様な働き方を推進しています。この多様な働き方の中では、安全教育や法改正、ISO規格のバージョンアップなど全従業員を対象とした研修の実施が困難になってきます。勉強会に参加する人、資料のみで勉強する人などそれぞれに合った研修を用意しても、教育内容に濃淡が出てきてしまい、理解度の差が出て誤った認識のまま業務を遂行してしまう可能性があります。
3つ目の「全従業員に教育の機会を設けるのが難しい」課題については、教育のムラをなくすために勉強会を複数回行うなどの対策が考えられます。しかし、多様な働き方をしている環境下で全従業員に複数回の研修会や講習会を設けるのは現実的ではありません。できたとしてもかなりの労力をかけなくてはいけません。
山下さん: また、先述した顕在的な課題の他にも「技術伝承」という潜在的かつ経営的な課題もありました。技術伝承をスムーズに行うには、人の動きや作業の音、現場の情報を少しでも多く伝えることが大切だと思っていますが、紙マニュアルという文字情報だけでは業務ノウハウを伝えきれず、技術伝承が進みません。
これらの諸課題を解決する方法として、2021年9月に動画マニュアルtebikiの導入を決めました。
品質保証部門から工場全体に始まった業務標準化と属人化解消の動き
tebikiの導入方法や導入当時のエピソードを教えてください。
岡田さん:
当社では現場の課題やお客様からの要望の声をいただいた時など、品質保証部門と現場の製造部門が連携して一緒になって解決していく、という文化があります。動画マニュアルによる人材教育には私も元々興味があり、過去には一部の部門で動画マニュアルによる教育を内製で進めたこともありました。
しかし動画編集は簡単ではなく特定の担当者しか編集できないことや、作成した動画マニュアルをどうやって工場全体に共有していくかなど作成面と運用面で課題が多く、うまく軌道に乗りませんでした。
製造業においては、現場の生産性向上や多様な働き方に対する柔軟なワークシフトへの対応、そして技術伝承といった現場の課題に対応していかなければなりません。諦めずに色々と調べていたら、動画マニュアルtebikiの存在を見つけました。
資料請求をしたらすぐに連絡をいただいて、動画マニュアルの操作性や機能などの説明をしていただけるというので、製造部門に声をかけて一緒に製品の説明を受けました。マニュアルを作成、更新していくのは担当者です。
担当者がこのtebikiというサービスを理解し、実際に操作ができそうか、運用に乗りそうかイメージがつくようにしてもらわないといけません。製造部門である現場の巻き込みは必須だと考え、積極的に声をかけました。日ごろから製造部門と連携していたこともあり、今回も共に協力して進められたと思います。
OJT時間の削減など定量的な効果だけでなく、業務手順が伝わりやすくなったことや多能工など定性的な効果も
tebikiの導入効果を教えてください。
岡田さん:
動画による研修の垣根が下がったなと感じます。動画ならではの伝わりやすさが業務手順の改善につながるだろうと期待していましたが、例えば品質保証部門では新規配属者のOJT教育に使っていた紙マニュアルの4割を動画マニュアルに置き換えることができ、OJT教育の時間を2割削減することができました。
現在当工場で公開済みの動画マニュアルの本数は538本で、想定していた以上に作成することができています。
山下さん: QC活動においても、業務手順や紙マニュアルではわかりにくい部分はtebikiを活用した動画に置き換えることで対策した、という定性的な効果も社内から届いています。これ以外にも、多能工教育への効果も少し感じ始めています。大阪工場では多能工教育に5年や10年かかったりしますが、動画によって業務が伝わりやすく覚えやすくなり、少しずつ時間短縮に繋がるのではないかと期待しています。
今でこそ、定量的にも定性的にも導入した効果を実感していますが、どこまで社内に動画マニュアルが浸透するか、定着するか少し不安でした。というのは、動画マニュアルの内製化を進めたことが過去にあり、その時はビデオで撮影して、PCのローカルに落として、動画編集されていないものを自部門だけで活用していました。なかなか動画の活用が浸透せず、簡単に動画編集ができるものを探していましたが、tebikiの導入に興味を持った社員の熱意に応え、社員を信じて任せることにしました。
また、導入に当たっては他社の製品も検討しましたが、tebikiは初期費用が少なく、利用料についてもリーズナブルでシステムの買い切りのような大きな投資額は不要だったので、ある程度安心して導入に踏み切ることができました。
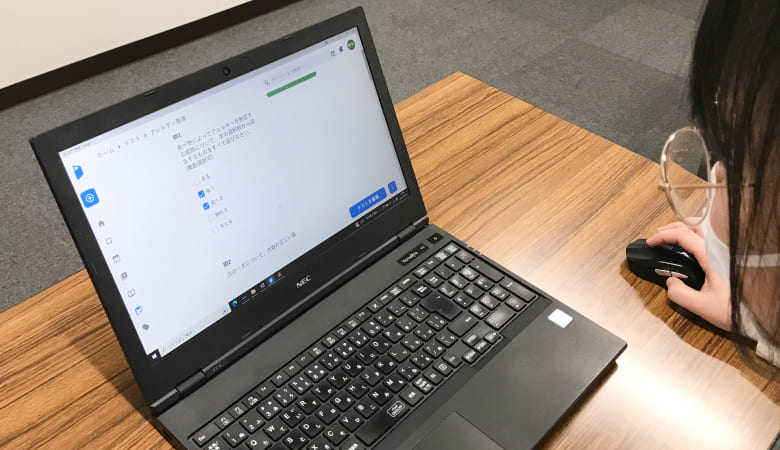
部門横断イベントを活用して工場全体へtebikiを浸透させた
動画マニュアルを社内に浸透させるコツを教えてください。
岡田さん:製造部門や品質証部門の一部に限定した活用ではもったいないので、どうやって大阪工場全体に広げていくかを考え、2つのステップに分けて取り組んでいくことにしました。
ステップ1は、"tebikiを知ってもらう、触ってもらう"。ステップ2は、"tebikiが役に立つ、使えると認知してもらう"。それぞれのステップを達成するためのアクションとしてどんなものがあるのか、洗い出し、効率的にtebikiの浸透を進めました。
ステップ1のアクションとして最終的に選んだのは、「社内コンテストでのtebikiの活用推進」でした。当然ながら、導入当初はtebikiの導入に関わった関係者のみが知っているだけだったため、関係部門以外の部門にもtebikiの存在を知ってもらう必要があります。
さらに、ただ存在を知ってもらうだけでなく、少しでもいいから実際に使ってもらい、簡単に動画マニュアルが作成できると知ってもらわないといけません。その機会を作れると考えたのが社内コンテストでした。大阪工場では毎年、品質管理大会というQC活動の内容を発表するイベントがあり、そのイベントと同時にコンテストを開催しました。
tebikiを使って各職場で職場の紹介動画を作っていただき、どの動画が良かったかを投票してもらい、良い職場動画を作成された方にtebikiTシャツを着てもらい、トロフィーを贈呈するなど少しでも認知されるように細かい部分まで事前に設計、実施しました。
ステップ2は「部門横断の座学講習会でtebikiを活用する」というアクションをとりました。
FSSC22000の概要や食物アレルギー教育など、全従業員が理解しなければならないテーマの講習会が実施される際、講習会当日の内容を録画して後日tebikiで視聴できるようにしておき、加えて理解度テストも設けてtebikiの機能を活用した充実の講習会を用意しました。
ステップ1の社内コンテストの対象者はコンテストの参加者に限られていましたが、講習会は全社員が対象なので、多くの社員の方にtebikiを知ってもらう良い機会となりました。
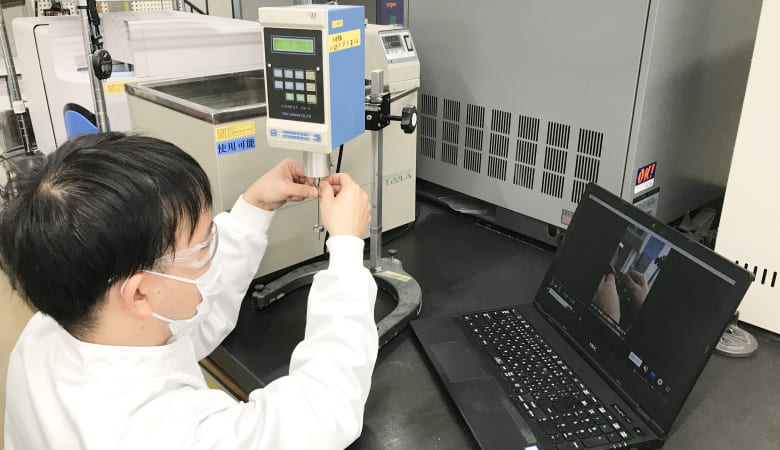
半年後にはOJTの時間を半分にしたい。さらに、属人化解消や多能工など活用の幅を広げていきたい。
今後のtebikiの活用の展望をお聞かせください。
岡田さん: これまでは「動画マニュアルの作成」と「社内におけるtebikiの知名度向上&活用の浸透」に重きを置いてきました。その結果、tebikiの利用は11部門にまで広がり、動画マニュアルの作成本数は500本以上となり、総視聴時間も150時間を超えるまで浸透させることができました。
今後は、1日1本以上ペースを維持しながら、視聴時間を伸ばすことにフォーカスしていきたいと思います。また、新人社員のOJT時間を2023年9月頃には導入前の半分にしたいと考えています。現在取り組みが顕著に進んでいるのは一部の部門に限られているので、他部門においても新人教育を動画に置き換える動きを促進していきたいと思っています。
山下さん: さらに「属人化」も解消していきたいと思っています。特に設備メンテナンスは属人化が顕著だと感じています。生産設備がトラブルや故障で止まってしまうと、生産全体が停止してしまうので設備メンテナンスは重要な業務である一方で、作業実施の頻度が低いため特定の従業員の経験に頼らなくてはいけません。
また、設備のトラブルや故障は常に潜在的なリスクであり、どうしても属人化の解消は後回しにされがちです。設備メンテナンスは動きが伴うため、紙マニュアルでは表現できない部分が多いので、活用頻度だけでなくリスクという観点からも動画化する対象業務を選定していってもらいたいと思っています。
あとは「脱属人化」と大阪工場方針の1つに挙げている人材育成の中で「多能工」という人材教育のキーワードにも大阪工場全体で挑戦しています。大阪工場は部署異動が少なかったことから他部署の業務理解度が上がらず、人のローテーションによる「多能工」を考えていましたが、動画によって教育工数を減らし、熟練工の作業動画教育である程度の水準まで理解できるような体制を整備できるのではないかと思っています。
また、動画はクラウドに保存されており、自主的または自律的にいつでも学習ができるので、tebikiの動画で「多能工」の教育体制の整備にも貢献できると思っています。
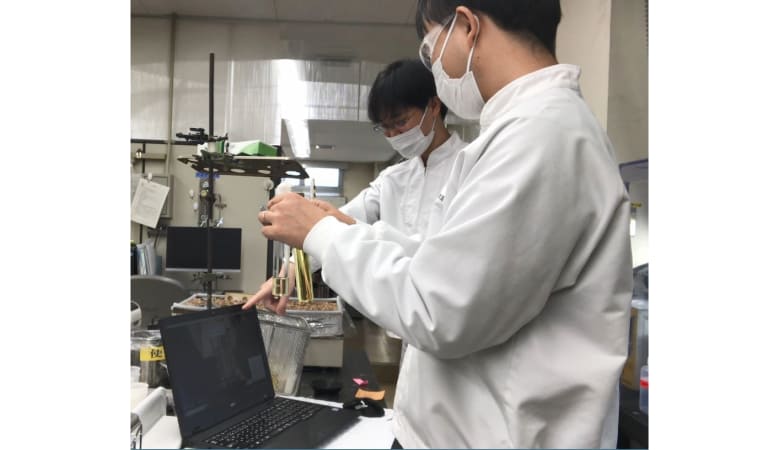
現場教育のブレイクスルーになって欲しい!
最後に、tebikiのオススメポイントを教えてください!
山下さん:tebikiは目指しているレベルが高いと思います。「現場の人が使いやすい」そういう声が出るようにもっと開発を進めてください!教育のやり方のブレイクスルーになる気がしています。どんどんtebikiの開発を進めて欲しいです!
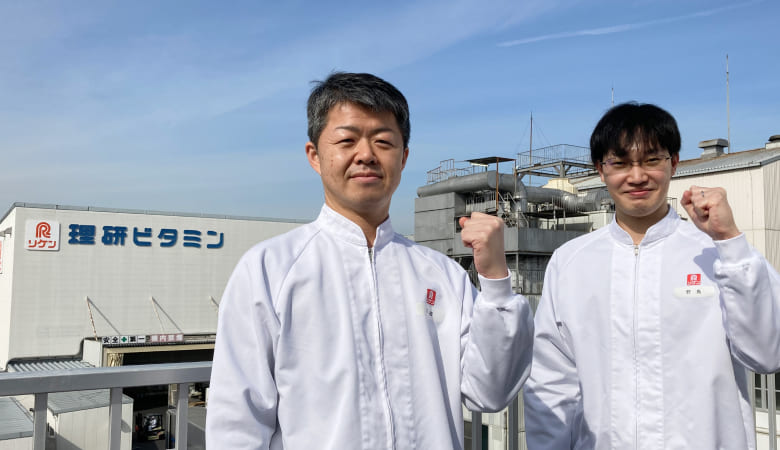