かんたん動画マニュアル作成ツール「tebiki現場教育」を展開する、現場改善ラボ編集部です。
品質向上とは、業務プロセスや製品の品質を改善し、顧客に提供する「価値」を高める活動全般を指します。業務効率の向上やコスト削減にも繋がり、企業の競争力強化に不可欠です。
本記事では、製造業における品質改善/向上で有効な手段を解説します。取組事例についても解説しますので、品質安定を実現するヒントを得ていただけますと幸いです。
目次
製造業における品質向上とは?
製品の品質向上
製品の品質向上とは、最終的に顧客に届けられる製品そのものの質を高めることを指します。製品の種類や顧客のニーズによって大きく異なりますが、一般的には以下の要素が含まれます。
- 機能性
- 使いやすさ
- 安全性
- デザイン など
作業の品質向上
作業の品質向上とは、製品を作る・サービスを提供するといった「作業」そのものの質を高めることを指します。作業品質の向上は、製品品質向上に直接繋がる重要な要素です。作業の種類によって異なりますが、一般的には以下の要素が含まれます。
- 正確性
- 効率性
- 安全性
- 一貫性 など
現場改善ラボでは、品質問題の原因を洗い出す手法について解説したセミナーを無料配信中です。「はじめて分析をする」という方でもわかりやすく解説していますので、以下をクリックして動画をご視聴ください。
「品質向上」と「品質改善」の違い
品質改善と品質向上は、どちらも品質を良くする活動ですが、「現状」と「目標」が異なります。
品質改善は、修正して正しい状態にする活動です。現状が本来望んでいた姿や期待していた品質状況になっていないのを改め、「不良率の高い状態を改善する」「入力ミスの多い事務処理を改善する」などのように使います。
品質向上は、今よりも上の目標を設定して、特性/バラつき/サービスを改良する活動です。現時点では問題になるような状況ではないが、「作業時間を短縮して生産性を向上する」「帳票の電子化により事務処理を楽にして従業員満足度を向上する」などのように使います。
製造業の品質改善/品質向上を難しくしている原因
製造業で品質改善や品質向上を難しくしているのは、以下のような原因が考えられます。
- 手順書の不整備などによる手順のバラつき
- 教育リソースの不足による人的ミスの発生
- 熟練工による高度な技術の伝承が困難
- 紙帳票によるデータ管理の不十分さとリアルタイム性の欠如
- 従業員の安全性や品質意識の欠如
- 検査基準の曖昧性
- 潜在的不良の発見の困難さ
上記のような課題を放置していると“現場力”が弱まってしまい、品質管理や改善施策の対応力低下、異常の早期検知や予防の遅れが発生するなど様々なリスクに発展する可能性があります。
【組織で取り組む】製造現場の品質改善 / 品質向上の具体的な対策
製造現場の品質改善/向上に取り組むうえでは、対策を設定した上で、組織全体が一丸となり共通の意識を持って改善に取り組む必要があります。ここでは、組織で取り組む具体的な対策を紹介していきます。
作業標準が必然的に遵守される環境の整備
現場の作業品質を向上させるうえでは、従業員の作業標準が遵守されるような環境作りが重要です。
”一目で作業手順やルールを理解できる”手順書を作成 / 整備
製造現場で活用するマニュアルは、テキストメインで作成されていることも多く、記載されている内容を瞬時に判断できないことが多いです。読み手によって受け取り方が異なってしまうため、正しい作業手順が遵守されずに作業品質が低下するリスクがあります。
このようなリスクを防止するためにも、業務習熟度や経験年数に関わらず誰が見ても「一目で理解できる」マニュアルを作成しましょう。フローチャートや機械設備の操作方法のキャプチャなどを活用し、視覚的に理解しやすい要素を盛り込むのがポイントです。
なお、一目で理解できるマニュアルを作成する上で、マニュアルを「読み込む」のではなく「直感的にわかる」ようにするため、マニュアルの動画化が注目されています。以下の動画は実際の製造現場で活用されているマニュアルのサンプルです。
※「tebiki現場教育」で作成されています。
このように、手順書を動画に移行して整備している現場は徐々に増えてきています。製造現場でどのように動画マニュアルが活用されているのかについては、以下のPDF資料で詳しく解説しているので、下のリンクをクリックして資料をご覧ください。
>>「製造業における動画マニュアル活用事例集(PDF資料)」を見てみる
フールプルーフでミスの発生自体を無くす
機械設備の操作ミスや部品を間違えて取り付けるなど、ヒューマンエラー(人為的なミス)による作業ミスがそもそも発生しないようにする「フールプルーフ」への取り組みも重要です。
誤った操作をした際に次の操作ができないようにしたり、危険な状態になると警告音を発したりなどがフールプルーフであり、これによって不良品の発生や品質の低下を未然に防止できます。
些細なミスが重大な品質不良や事故に発展することも少なくない製造現場では、リスクを見越して一歩先を見据えた対策が欠かせません。ヒューマンエラーによる品質不良や事故を未然に防止するための実践的な方法を知りたい方は、以下のPDF資料をご覧ください。
>>「製造業におけるヒューマンエラーの未然防止と具体的な対策方法(PDF資料)」を見てみる
品質低下などの異常を検知する仕組みの構築
作業や製品の品質低下を人力で検知するのは非常に困難であり、知らず知らずのうちに不良率が向上したり、歩留まりが悪化することも少なくありません。
このようなリスクを防止するためにも、異常が発生した際に自動的に検知する仕組みの構築が重要です。
現場で作成する帳票を電子化して、異常を自動で検知する
製造現場では、紙やExcelで帳票が作成されるケースが一般的ですが、転記ミスや記録漏れなどが多く、データの集計や分析に手間と時間がかかっているケースも多いです。加えて、記録すること自体が目的になり、製造現場の改善に向けた活用が進まない問題も往々にしてあります。
このような課題の解決に向けた取り組みとして有効なのが、帳票の電子化(デジタル化)です。各種タブレットを活用し、現場で帳票を記録することで、リアルタイムでデータの取得ができ、以下のようなダッシュボードやグラフをPC / タブレットなどで可視化できます。
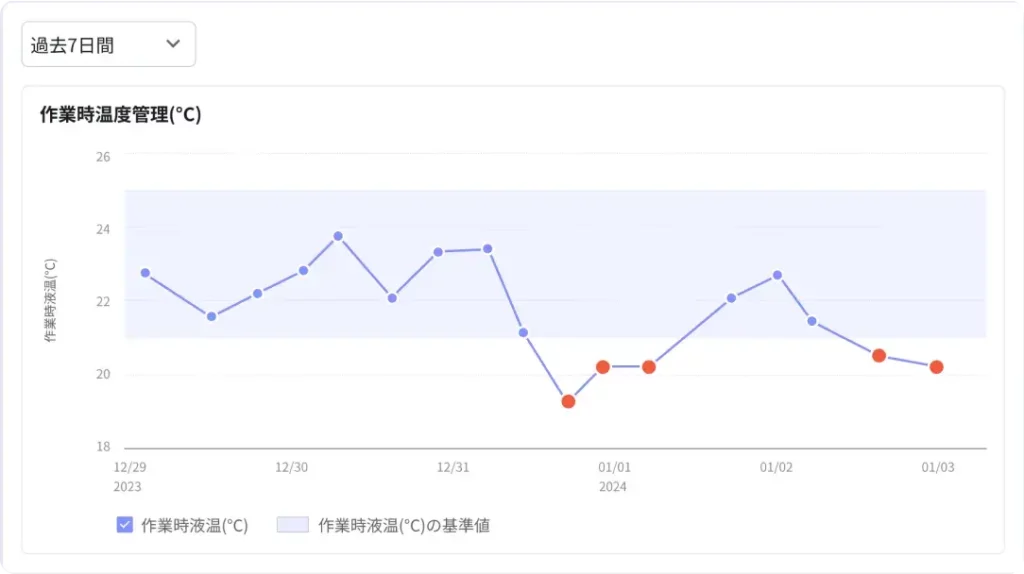
※デジタル現場帳票「tebiki現場分析」のサンプルグラフから引用
実際に「tebiki現場分析」を活用して、帳票を電子化している「株式会社日本電気化学工業所」では、ダッシュボードで温度データを確認していた際、普段とは少し異なる温度の推移に気づき、現場で詳細な点検を行ったところ、配管に小さな穴が開いていることが判明。早期に異常を検知できたことで、大規模な故障や生産ラインの停止といった深刻な事態を未然に防止しています。
同社の事例を詳しく読んでみたい方は、以下のインタビュー記事をご覧ください。
インタビュー記事:品質不良の未然防止をリアルタイムデータで実現。異常値検知を迅速にできた理由。
4M変更のタイミングを理解し、適切な対策を講じる
4M(Man、Machine、Material、Method)に変更があった際は、製品の品質不良が発生しやすくなります。
例えば、新たな従業員(Man)が配属される場合、スキルがないため作業ミスが発生したり、新たな機械(Machine)を導入する場合、初期の設定や操作などでミスが発生し、製品に不具合が生じたりなどが考えられるでしょう。
このように、4Mが変更された際の品質低下を防止するためにも、変更が行われるタイミングを理解し、作業手順の見直しや従業員への再教育などを徹底することが重要です。
なお、4M変更変更と類似した概念として、変化点管理があげられます。いずれも製造現場の変化が品質に与える影響を評価して、リスクを最小限に抑える手法です。変化点管理について理解を深めたい方は、専門家による以下の解説動画の視聴がおすすめです。以下の画像をクリックして動画を視聴してみてください。
品質低下につながっている課題を追求~改善する手段の実施
品質の低下につながっている課題を把握し、適切な手段を講じることによって改善が見込めます。ここでは、課題の追求し、改善するためのフレームワークや手段について紹介していきます。
「なぜなぜ分析」で課題を突き止める
品質低下の事象に対して、「なぜ?」を繰り返して表面的な原因だけではなく、根本の原因まで深堀りする「なぜなぜ分析」も有効な手段の1つです。
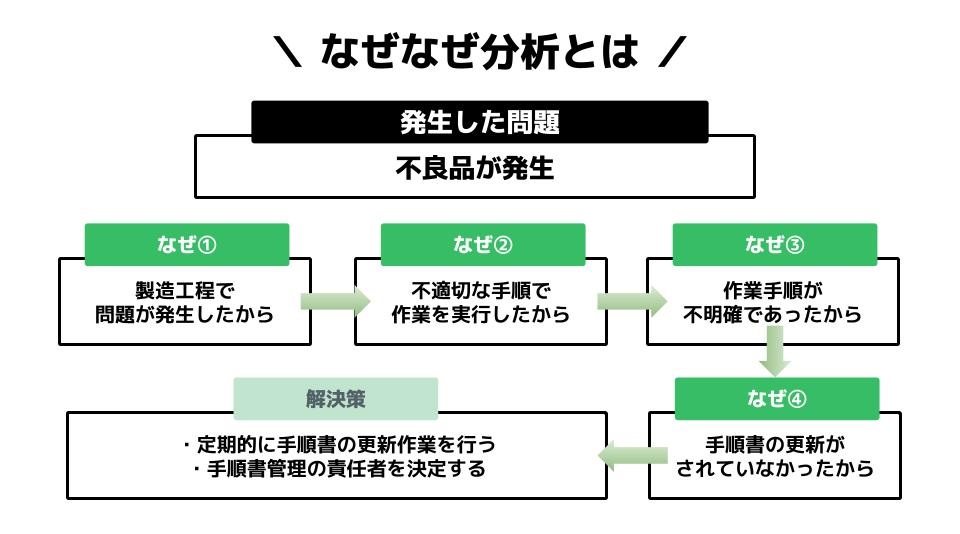
例えば、製造した製品にキズやへこみなどがついてしまう品質不良が多発している場合のよくある対策としては、作業上の注意を促す掲示物の提示や声掛け、ダブルチェックの導入などですが、これではその場しのぎの対策に過ぎません。
なぜなぜ分析に取り組むことで、想定していない機械設備の不具合が見つかったり、作業手順そのものが不適切であったりなどの課題を突き止めることも可能です。
なぜなぜ分析の具体的な実践方法や具体的な事例など、より実践的な理解を深めたい方は、トヨタ自動車の社内で「なぜなぜ分析の研修」の講師を担当していた講師の動画を視聴してみてください。以下のリンクをクリックすると動画をご覧頂けます。
>>【視聴無料】「トヨタで学んだ『なぜなぜ分析』ヒューマンエラーに対するトヨタの考え方は?」を見てみる
「QC7つ道具」「新QC7つ道具」で原因を分析する
品質問題を可視化する「QC7つ道具」、品質管理を行うための「新QC7つ道具」のそれぞれを活用し、定性的 / 定量的なデータを用いて、発生している品質課題を整理して分析するのも有効な手段の1つです。
それぞれの違いは、「QC7つ道具」は数値データを、「新QC7つ道具」は言語データを扱う点です。製造現場における品質のトラブルは不良率をはじめ定量的なデータで現れますが、不良が発生している原因を追求する過程で、定性的な言語で表現する必要があるため、両者は品質管理のために欠かせない分析手法と言えるでしょう。
現場における使用事例や両者を組み合わせた分析方法などについて、専門家による解説動画を用意しています。品質問題を整理する上でのヒントが得られるはずなので、ぜひ以下の画像をクリックして動画を視聴してみてください。
5S活動で作業を阻害するムダを排除する
整理・整頓・清掃・清潔・躾の5つで構成される取り組みである「5S活動」は、作業品質を向上させる上で基本となる取り組みの1つです。
作業スペースや作業エリアが整理・整頓されていることによって、作業に必要なもの / 不要なものがわかるので、作業に集中できて不要な判断や行動がなくなります。また、清掃を通じて設備の故障となる原因を除去することによって、設備の誤作動による品質低下の防止が期待できるでしょう。
5S活動の具体的な実践方法、現場に定着させる方法などを詳しく知りたい方は、数々の企業で5S改革を行ってきた専門家による動画の視聴がおすすめです。以下のリンクをクリックして動画を視聴してみてください。
スムーズなコミュニケーションが実現する職場環境の構築
職場環境のコミュニケーションが不足していることで、連携ミスや作業基準の不統一などが生まれ、結果的に品質に影響している場合も考えられます。これらの解消に向けて、円滑なコミュニケーションが実現する職場環境の構築する術について紹介していきます。
図や動画などの視覚的に情報を伝達できる手段の活用
現場の教育で活用されている手順書やマニュアルなどがテキストベースで一目で理解できない場合、適宜OJTを実施する必要があるため、作業が断続的になってしまいます。
そのため、情報を伝える際には一目で視覚的にわかるような工夫を講じるとよいでしょう。例えば、注意喚起をする掲示物はテキストを少なくしてイラストを活用したり、手順書やマニュアルは動画を活用したりなどです。
参考になる好事例として、冷凍食品の製造販売を行っているテーブルマーク株式会社では、機械に動画マニュアルが閲覧できるQRコードを貼り付けて、わからないときにiPadでQRコードを読んでマニュアルが見られるような体制を構築しています。
QRコードを読み込み、動画マニュアルを確認する様子-1024x576.png)
この取り組みによって、作業者自身が自発的に復習できるため、OJT担当者による繰り返し教育する手間の防止が実現しています。同社の取り組みの詳細を知りたい方は、以下のインタビュー記事をご覧ください。
インタビュー記事:属人化業務の指導工数を83%削減!標準化教育により安心安全な食品を提供
多言語に対応したツールの活用
外国人労働者を抱えている現場では、作業手順は理解してもらえても、その背景や目的などの詳細な部分までを伝えることができずに、結果として作業品質に影響してしまう場合も少なくありません。
国籍の異なる外国人従業員を抱えている場合、それぞれの母国語に合わせて業務の説明や手順書を用意する必要があり、円滑なコミュニケーションは非常に困難です。そこで、外国人労働者に合わせた多言語化が可能なツールの活用が有効な手段としてあげられます。
例えば、製造業の「タマムラデリカ株式会社」では、多数の外国籍従業員を抱えており、マニュアルの翻訳 / 多言語化に負担を抱えていましたが、自動翻訳機能を搭載した動画マニュアル作成ツール「tebiki現場教育」の活用し、言語の課題を解消しています。
同社のように、外国人労働者に対しての言語の壁を動画マニュアルによって解消している企業は増加しています。以下のPDF資料では、外国人労働者の教育課題を解消した事例をまとめていますので、合わせてご覧ください。
>>「外国人労働者に「伝わらない」を解決した動画マニュアル活用事例集(PDF資料)」を見てみる
【個人で取り組む】製造現場の品質改善 / 品質向上の具体的な対策
現場の品質向上を進めるうえでは、基本的に組織で一丸となって推進しますが、個人の作業に対しての意識や取り組み方を変えるだけでも品質向上に寄与する場合があります。
個人単位で取り組める製造現場の品質に向けた具体策は、以下のようなものがあげられます。
- 作業ごとにチェックリストを作成して見える化する
- 指差呼称で品質への意識を高める
- 常に余裕を持ったスケジュールで作業する
製造現場の品質改善/品質向上を実現した企業事例
ここでは、製造現場における品質改善/品質向上を実現した企業の好事例について紹介していきます。
新日本工機株式会社
工作機械、遠心力鋳造管、産業機械の製造販売を手掛けている新日本工機株式会社では、作業手順が標準化されておらず、作業者や管理者によって認識が異なっていたことで、各作業時のチェック内容の取り決めが不十分になる課題を抱えていました。
結果として、作業者によって品質のバラつきが生じて、結果的に作業の後戻りが発生していたそうです。誰もが標準手順通りに作業ができる体制の構築を模索する中で、注目したのは既存とは別角度からのアプローチである動画マニュアル「tebiki現場教育」の導入です。
作業要領書の内容だけでなく、安全作業や保守/点検作業など多岐に渡る作業のマニュアルを動画化することで、若手や中堅への技術伝承が進み、標準化された作業を正確に行えるようになったため品質のばらつき解消を実現しています。
同社の事例を詳しく知りたい方は、以下のインタビュー記事をご覧ください。
インタビュー記事:人が育つ環境づくりとして動画マニュアルtebikiを活用。技術の蓄積と作業品質の安定を実現。
株式会社Archem
「シートパッド事業」「産業用化成品事業」「事務機器用精密部品事業」の事業を展開している株式会社Archemでは、日本国内だけではなく、アジア・アメリカにも工場を構えて製品製造に取り組んでいます。
同社のアメリカ工場において、母国語が英語以外の一部のメンバーは、英語の作業指示書を読めずないため、OJTのみで教育を実施していましたが実際の作業工程に詳細に理解できずに作業品質にばらつきが生まれる課題を抱えていました。
そこで取り組んだのが、言語の壁を越えながら教育内容を標準化できる動画マニュアル「tebiki現場教育」を活用した教育の標準化です。工程ごとに設置しているモニターに動画マニュアルを繰り返し再生し、いつでも閲覧できる環境を整備したことで、作業のバラつきを解消できたことに加えて作業の習熟が早くなる効果も得られています。
同社の事例を詳しく知りたい方は、以下のインタビュー記事をご覧ください。
インタビュー記事:アメリカ3工場にて言語の壁を乗り越え、製品品質と生産性を向上
現場作業の標準化が実現する動画マニュアル作成ツール「tebiki現場教育」
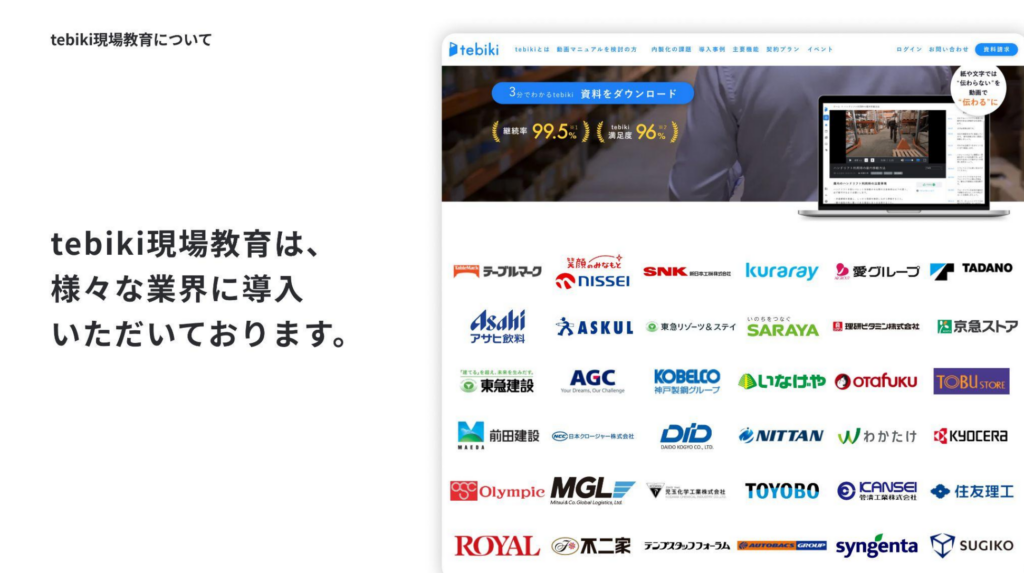
現場作業の標準化を進める上では、動画マニュアル作成ツール「tebiki現場教育」の活用です。
タブレットで作業風景を撮影してかんたんな編集作業のみで動画マニュアルを作成できるため、動画編集経験がない方でも安心して利用することができます。
また、従業員ごとのスキルを可視化して管理できるのも標準化が促進されるポイント。実態に即した教育を実施できるため、習熟度のばらつきを防止して標準作業が実現します。tebiki現場教育のサービス内容を詳しく知りたい方は、以下のリンクをクリックして資料をご覧ください。
>>>3分でわかるtebiki現場教育のサービス資料を読んでみる
株式会社日本電気化学工業所
アルマイト加工を中心に、建材や車両などの表面処理などを手掛けている株式会社日本電気化学工業所。同社では、異常値の発見に時間がかかる、収集したデータを改善活動に活用できない、などの非効率な業務フローにより、製品の品質が不安定になったことで不良率が向上してしまう課題を抱えていました。
そこで同社では、タブレット上で現場データをリアルタイムで監視・蓄積・分析できる体制を整備し、微細な異常の早期発見や迅速な対応ができる環境の構築を実現しています。
▼タブレットで記録・集計したデータを分析する様子▼
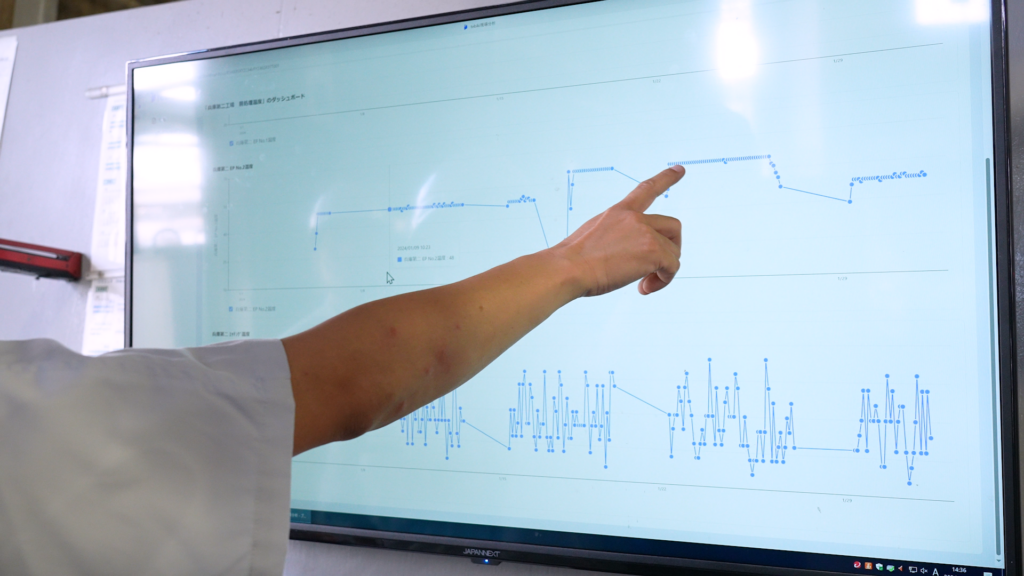
異常値の自動通知や全記録の一括承認機能により、管理者の業務負担も大幅に軽減され、品質の安定化と現場の意識改革を同時に実現しています。同社の事例を詳しく読んでみたい方は、以下のインタビュー記事をご覧ください。
インタビュー記事:品質不良の未然防止をリアルタイムデータで実現。異常値検知を迅速にできた理由。
帳票のデジタル化で品質の異常を検知できる「tebiki現場分析」
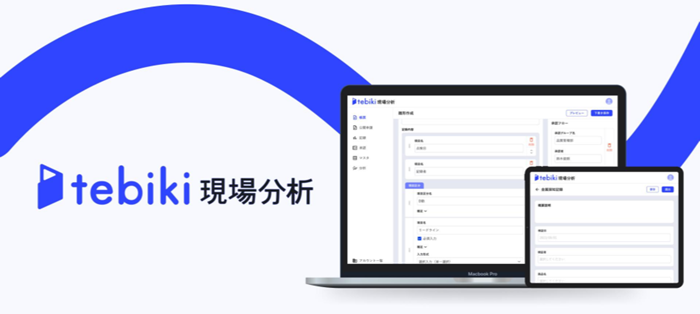
日々の記録をデジタル化することで異常を即座に検知し、管理者は素早い対策指示が可能になります。tebiki現場分析でできる主なことは、以下の通りです。
- クラウド上に誰でも簡単に帳票を作成・管理できる
- 正常値を設定することで、異常値アラートを出せる
- 記録した数値を自動でグラフ化できる
- 画像をアップロードして、そのまま記録できる など
今回ご紹介していない具体的な機能のご紹介、プランなどの情報は以下のリンクをクリックして資料をご確認ください。
まとめ
製造現場の品質向上 / 改善に向けては、「tebiki現場教育」を用いた動画マニュアルによる人材育成、異常検知の仕組みを実現する、「tebiki現場分析」を用いた現場帳票のデジタル化が有効な手段です。
本記事でご紹介した2つのシステムの機能概要やプラン、詳しい改善事例は以下の概要資料に掲載しています。ぜひ品質向上に向けた情報収集の一環で、フォームをご入力のうえ資料をご覧ください。