かんたん動画マニュアル作成ツール「tebiki現場教育」を展開する、現場改善ラボ編集部です。
放電加工(EDM)とは、電気エネルギーを利用して金属を精密に加工する技術のことで、超硬合金やチタンなどの難削材でも高精度な加工が可能です。
この記事では、放電加工とは何か?原理や種類と違い、メリット・デメリットなど基礎知識を詳しく解説します。また、放電加工の作業時によくあるトラブルと対策例など実践的な内容も解説していますので、参考情報としてご活用ください。
目次
放電加工(EDM)とは?原理や電極をわかりやすく解説
放電加工はどんな加工方法?最適な素材は?
放電加工とは、電極と工作物の間に高電圧を印加し、絶縁破壊によって発生する放電の熱エネルギーを利用して金属を溶かしながら削る加工技術です。
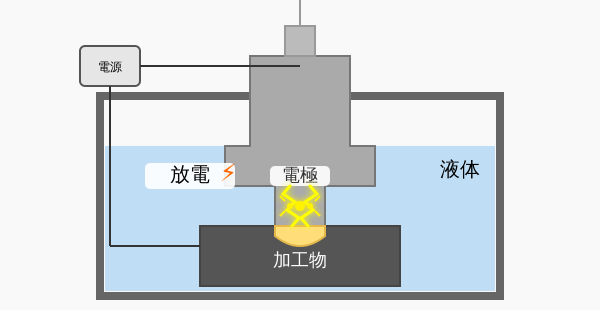
英語では「Electrical Discharge Machining」と表現し、省略してEDMと表記されます。一般的な切削加工とは異なり、工具と工作物が接触しないため、物理的な負荷をかけることなく複雑な形状や微細な加工を実現できます。
超硬合金やチタンなどの難削材でも高精度に加工できるため、金型や精密部品の加工に利用されている技術になります。
放電加工の原理
放電加工の原理について分かりやすく理解するため、ここからは以下の4つの観点から解説しましょう。
- 放電加工は「雷」と同じ原理で金属を削る
- 放電の繰り返しによる精密加工
- 放電の繰り返しによる精密加工
- 放電加工ならではの特徴
放電加工は「雷」と同じ原理で金属を削る
放電加工は、雷や静電気と同じ「放電現象」を利用して金属を削る加工方法です。
自然界の雷は空気中に発生しますが、放電加工では工作物を絶縁性の高い「加工液」に沈めた状態で行われます。加工液が重要な役割を果たし、放電を制御するとともに、冷却や金属粉の洗浄を担っています。
加工の流れ
最初は電極と加工対象物の間に高電圧を印加します。そのとき、電極と加工対象の距離が0.01~1mm程度まで近づくと、絶縁性のある加工液が「絶縁破壊」を起こし、瞬間的に電流が流れます。
電流によって「放電」となり、局所的に6000℃以上の高温を発生させます。高温によって金属が溶解し、さらに蒸発することで、少しずつ金属が除去されていきます。
放電の繰り返しによる精密加工
放電は1回だけではなく、非常に短い時間(マイクロ秒単位)で発生・消失を繰り返します。1秒間に数千回~数十万回繰り返すことで、微細な部分を精密に削ることが可能になります。
また、加工液が繰り返しの過程で金属粉を洗い流し、短絡(ショート)を防ぎながら加工を続けます。
放電加工ならではの特徴
放電加工は、従来の切削加工とは異なり、工具が工作物に直接接触しません。そのため、物理的な負荷が発生せず、硬度の高い素材や複雑な形状の加工にも適しています。
また、加工中に発生する熱は加工液によって瞬時に冷却されるため、工作物が熱で変形するリスクも低くなります。
放電加工で用いる電極
銅電極
銅は放電加工で最も使われる電極材料です。熱伝導性と電気伝導性が高いため、加工時に発生する熱を素早く放散し、効率的に加工を行えます。
また、比較的柔らかいため、加工形状に合わせて自由に加工できる点もメリットです。しかし、柔らかさゆえに摩耗が早く、高硬度の素材を加工する場合には消耗が激しくなることが欠点となります。
グラファイト電極
グラファイト(黒鉛)は、耐熱性と耐摩耗性に優れた電極材料です。加工時に変形しにくく、放電による摩耗が少ないため、高精度な加工が求められる場面で多く使用されます。
また、自己潤滑性を持ち、放電時の熱による影響を受けにくい点も特長です。ただし、加工時に粉塵が発生しやすく、導入コストが高い点がデメリットです。
銅タングステン電極
銅タングステンは、銅の柔軟性とタングステンの硬度を兼ね備えた材料です。特に、高硬度の超硬合金などの加工に適しており、放電による電極の摩耗を抑えられます。
ただし、銅やグラファイトに比べると加工が難しく、コストも高くなるため、用途を選ぶ材料と言えます。
銀タングステン電極
銀タングステンは、非常に高い電気伝導性と熱伝導性を持つため、放電のエネルギーを効率的に伝えることが可能です。そのため、加工速度が速く、精密な仕上げが可能です。
特に航空宇宙産業や医療機器の精密加工に使用されることが多いですが、高価であるためコスト面での課題があります。
放電加工(EDM)のメリットとデメリット
放電加工の最大の強みは、硬度の高い金属でも精密に加工できる点です。例えば、金型製造に使われる超硬合金やチタン、モリブデン、ステンレス鋼など、従来の切削加工では加工が難しい素材でも対応可能です。
ただし、放電加工は電気を通す素材にしか適用できません。樹脂やセラミックのような非導電性の材料は加工ができないため、素材選定時には注意が必要です。
このように放電加工は長所と短所がはっきり分かれます。本章では、放電加工の主なメリットとデメリットを詳しく解説します。
主なメリット
高精度な加工が可能
放電加工は1μm(ミクロン)単位の精密加工が可能です。切削加工では工具の摩耗によって精度が変動しますが、放電加工では非接触のため、極めて安定した寸法精度を維持できます。
一方で、電極の摩耗や消耗が進むと加工精度に影響を与え、品質不良につながることがあります。対策として、作業者ごとに認識がバラつかないように、電極の消耗具合の基準を動画マニュアルで共有知化し、適切な交換タイミングを管理するといった取り組みも手段の1つです。
>>製造業における「動画マニュアルの活用シーンや改善事例」を見てみる
硬い材料でも加工できる
放電加工の強みとして、超硬合金やチタン、インコネル、モリブデンなどの高硬度な金属も加工できることが挙げられます。
切削加工のように物理的な力を加えず、電気エネルギーによって金属を少しずつ溶解・蒸発させるため、航空宇宙部品、医療機器、金型製造など、高強度の部品が求められる業界では欠かせない技術となっています。
自動化・無人運転が可能
放電加工は数値制御(NC)による自動加工が可能であり、長時間の無人運転にも対応しています。自動化・無人運転により、製造現場の生産性向上や人手不足対策としても有効です。
特に、夜間や休日に加工を進めることで、生産コストを抑えられます。
物理的負荷がかからず、複雑な形状を実現
放電加工は非接触加工のため、薄肉構造やシャープな角、深い溝などの複雑な形状も加工可能です。特に、従来の切削加工では工具が入り込めないような部分でも、電極の形状を工夫することで加工が可能になります。
一方で、複雑な形状の加工では、加工中に電極が摩耗して形状精度が落ちることがあります。電極の作り直しや補正方法といった作業を動画マニュアル化することで、作業者による業務品質のバラつきを抑え、加工の再現性を高めることが可能です。
>>製造業における「動画マニュアルの活用シーンや改善事例」を見てみる
主なデメリット
加工速度が遅い
放電加工の最大のデメリットは加工速度が遅いことです。金属を1μm単位で少しずつ削るため、大量生産には不向きです。例えば、同じ形状を切削加工と放電加工で比較した場合、放電加工の方が数倍以上の時間を要することがあります。
加工スピードの遅さは、複数の放電加工機を並行稼働させることや加工条件を最適化することで改善可能です。
加工コストが高い
放電加工では、電極が消耗品であり、消耗が激しいため、加工コストが高くなりがちです。特に、ワイヤー放電加工では大量のワイヤー電極を消費するため、材料コストが高くなる傾向があります。
電極の消耗が激しい場合は、最適な電極材料を選定することでコストを削減できます。また、電極の寿命管理や交換手順を動画マニュアルで統一することで、ムダな消耗を減らし、コスト削減につなげることが可能です。
製造現場では、動画マニュアルで標準作業を視覚的に伝え、業務上のムリムダムラを解消している事例が増えています。このような動画を活用した改善事例は、別紙の事例集で詳しくご紹介していますので、以下のリンクをクリックしてご覧ください。
>>動画マニュアルで現場改善を実現している製造業の事例を見てみる
電気を通さない素材は加工不可
放電加工は、電気を通す金属材料しか加工できないという制約があります。例えば、樹脂やセラミックなどの絶縁体は放電を起こせないため、加工ができません。
加工後の表面処理が必要な場合がある
放電加工では、加工面に熱影響層(白層)が発生し、仕上げ処理が必要になることがあります。また、加工後の表面が梨地状(ザラザラした状態)になるため、用途によっては追加の研磨や仕上げ加工が求められます。
仕上げ加工には手作業が必要な場面が多く、熟練者が持つカンコツのようなスキルが要求されるケースがあります。表面処理のような、属人化しやすいカンコツ作業の標準化にも取り組むことで、品質のばらつきを抑えられます。
カンコツ作業を標準化する方法は、別紙のガイドブックで図解も交えて詳しく解説しています。以下のリンクをクリックして、本記事と併せてご活用ください。
>>「“伝わらない”“属人化している”カンコツ作業を標準化する最適解」を見てみる
加工環境の管理が重要
放電加工では、加工液の汚れや微細な金属粉の堆積が加工精度に影響を与えるため、適切な管理が必要です。ろ過装置の性能が低いと、加工中の放電が不安定になり、仕上がりの精度が低下するリスクもあります。
加工環境の維持には、定期的なろ過装置の点検やメンテナンスなど設備保全が必要です。設備トラブルの発生は、生産ラインの停止など生産性に影響を及ぼす問題のきっかけになります。
保全業務の標準化や異常を予知する傾向管理など、デジタル技術による設備保全の改善方法は、以下の画像をクリックしてガイドブックをご覧ください。
放電加工(EDM)の主な種類と違い
放電加工(EDM)は、加工対象や求められる精度によって主に3種類に分けられます。それぞれの違いを簡単に説明すると以下の通りです。
- ワイヤー放電加工:ワイヤー電極を連続的に送りながら放電し、材料を切り離す加工方法
- 形彫放電加工:型(電極)の形状通りに放電を行い、材料に同じ形状を彫り込む加工方法
- 細穴放電加工:細いパイプ電極で放電を行い、微細な穴や深穴を高速で加工する方法
本章では、3種類の加工方法の概要と違いを詳しく解説します。
ワイヤー放電加工
ワイヤー放電加工(ワイヤーカット放電加工)は、細いワイヤー電極を使用し、糸ノコギリのように金属を切断する加工方法です。直径0.02mm~0.3mmほどの極細ワイヤーを使用し、数値制御(NC制御)により電極を動かしながら放電を発生させ、加工対象物を溶かしながらカットします。
通常、ステンレス鋼や超硬合金、チタン合金などの高硬度材料にも適用され、切削加工では不可能な微細加工や精密な金型製作に多く利用されます。
ワイヤー電極は消耗品であり、加工中に常に新しいワイヤーが供給される仕組みになっています。そのため、摩耗による精度低下を抑え、安定した加工の実現が可能です。
しかし、消耗するワイヤー電極のコストがかかるため、経済性の考慮が必要です。また、ワイヤーは工作物を完全に貫通する必要があるため、底付きの加工ができないという制約があります。
ワイヤー放電加工は、特に金型製造・精密部品の製作・電子機器部品の加工において、高精度で複雑な形状の加工を求められる場面で活用されます。高精度なカットが可能な一方で、加工速度は比較的遅いため、大量生産には向いていません。
形彫放電加工
形彫放電加工は、あらかじめ加工形状に成形した電極を用いて、工作物を彫り込むように加工する方法です。ワイヤー放電加工が「糸ノコギリで切断するイメージ」に近いのに対し、形彫放電加工は「型で工作物を彫る」イメージに近いといえます。
金型製作や複雑な凹凸形状の部品加工に適しており、特に射出成形用の金型や航空宇宙分野の精密部品などで活用されています。
形彫放電加工の最大のメリットは、底付きの加工が可能な点です。ワイヤー放電加工では、必ず貫通した形状にしか加工できませんが、形彫放電加工では、深い溝や立体的な凹み、複雑なアンダーカット形状の加工が可能です。また、電極の形状を工夫することで、さまざまなパターンの加工ができます。
一方で、電極を個別に作る必要があるため、加工コストが高く、作業工程が増えるというデメリットがあります。また、電極の摩耗によって加工精度に影響が出るため、電極の管理が重要です。そのため、高精度の形状を維持するためには、電極の消耗を考慮した加工条件の最適化が求められます。
形彫放電加工は、試作品の製作や精密加工が求められる部品製造に適しており、小ロット生産に向いているため、コストと加工精度のバランスを考慮しながら導入することが重要です。
細穴放電加工
細穴放電加工は、細い電極を用いて金属に極小径の穴を開ける加工方法です。通常、直径0.1mm~3mm程度の穴を加工するのに適しており、切削加工では難しい超硬合金やチタンなどの難削材にも対応可能です。特に、航空機や自動車部品、電子部品、医療機器の分野で活用されており、冷却用の微細穴や精密な流体制御部品の加工に欠かせない技術となっています。
細穴放電加工の特徴は、ドリル加工では難しい極細穴や深穴加工が可能である点です。例えば、ジェットエンジンの冷却孔や放熱性を向上させるための微細な通気孔の加工など、通常の機械加工では実現が難しい領域で活用されています。また、放電による非接触加工であるため、切削時のドリルの摩耗や折損のリスクを回避しながら加工を行うことが可能です。
しかし、加工速度が遅いため、大量生産には向かないことがデメリットとして挙げられます。また、加工精度を維持するためには電極の摩耗や消耗を適切に管理する必要があり、加工条件の調整が求められる点も注意が必要です。さらに、加工液の管理が不十分だと、穴内部の放電が不安定になり、加工不良の原因となるため、適切なメンテナンスが不可欠です。
放電加工(EDM)でよくあるトラブルと対策例
放電加工(EDM)は、精密な加工が可能な一方で、作業中に品質や安全に関するトラブルが発生しやすい加工方法でもあります。
ここからは、放電加工における代表的なトラブルとその対策を具体的に解説します。
「メンテナンス業務や段取り作業」による品質トラブルと対策例
放電加工の品質を左右する要因のひとつが、メンテナンス業務や電極交換など段取り作業です。
電極の消耗や加工素材の変更に伴う調整作業が適切に行われないと、寸法精度の低下や品質不良の発生につながります。ここでは品質トラブルと対策について以下の順に解説します。
- 加工素材変更に伴う電極選定ミス
- 電極の消耗による品質低下
加工素材変更に伴う電極選定ミス
加工素材が変更された際に、適切な電極を選定しないと、放電が不安定になり、加工不良の原因となります。例えば、超硬合金を加工する際に銅電極を使用すると、摩耗が激しくなり、寸法精度の確保が難しくなるといったトラブルが発生します。
対策として電極選定の標準化と事前テストが挙げられます。加工する素材ごとに推奨される電極の種類を事前にリスト化し、作業者が迷わず適切な電極を選べるようにするのが効果的です。また新しい素材や形状の加工を行う場合は、試験加工を実施し、適した電極を決定しましょう。
電極交換の流れや電極の選定基準を動画マニュアルとして整備し、標準作業を統一することも効果があります。標準作業のような「現場のルール」を守らせる方法は、以下のガイドブックでも解説していますので、クリックしてご活用ください。
>>「“手順書通りにできない”から卒業!作業ルールを守らせる効果的な方法」を見てみる
電極の消耗による品質低下
放電加工では、電極が放電によって徐々に摩耗するため、適切なタイミングで交換しなければ、加工形状の乱れや寸法精度のばらつきが発生することがあります。摩耗した電極を使い続けることで、加工表面の粗さが増し、仕上げ加工の工数が増加する恐れがあります。
対策として、標準作業に電極の消耗測定を組み込むことが挙げられます。電極摩耗の進行を定期的に測定し、交換基準を明確にすることで、加工品質を一定に保てます。また、測定結果を記録し、作業者全員で情報を共有することで、誰が作業しても安定した加工品質を維持できる体制を構築することが可能です。
「標準作業の共有」は前述のように動画マニュアルが効果的です。「測定結果の記録・共有」の手段としては、デジタル現場帳票の活用が効果的です。測定結果をデジタル上で共有することで、異常値などがあった場合に管理者へ通知を出すなど、リアルタイムで異常検知して不良品発生を未然防止することもできます。
デジタル現場帳票を活用し、現場の異常を早期に検知して品質不良を未然防止した事例として、株式会社日本電気化学工業所の事例をご紹介します。
▼インタビュー動画:株式会社日本電気化学工業所▼
同社の改善事例は、以下のインタビュー記事でも詳しく解説していますので、リンクをクリックしてご覧ください。
>>「品質不良の未然防止をリアルタイムデータで実現。異常値検知を迅速にできた理由。」を見てみる
「手順不遵守や不安全行動」による安全トラブルと対策例
放電加工は高電圧を扱うため、感電や火災といった重大な安全トラブルが発生しやすい作業環境です。特に、安全手順を守らないことが原因で発生する事故が多く、作業者の意識と適切な教育が不可欠となります。
ここでは、実際に起こりやすいトラブルとその防止策について以下の順に解説します。
- 感電事故のリスクと対策
- 火災発生の危険性と防止策
- 保護具未着用など作業服着用の誤りによる事故の危険性
感電事故のリスクと対策
放電加工機は高電圧を利用して金属を加工するため、適切な絶縁処理や安全確認が不十分な場合、作業者が感電する危険性があります。特に、機械のメンテナンス時に通電したまま作業を行うと、思わぬ事故につながります。誤って加工液に手を入れたり、電極や工作物に触れてしまうことで、高電圧に触れ感電するケースもあります。
感電事故のリスクを防ぐためには、作業前に必ず電源をOFFにし、ロックアウト(機械の電源を完全に遮断する仕組み)を実施することが重要です。また、絶縁手袋や適切な作業着を着用することで、万が一の事故を防げます。
安全手順が適切に守られないと、作業者の命に関わる重大事故につながる可能性があります。そのため、製造現場の安全教育はもちろん、工場の安全対策を徹底することが欠かせません。製造業における安全対策の取り組み例は、以下の記事で詳しく解説しているので、併せてご覧ください。
関連記事:工場の安全対策10選と好事例を解説!製造業の安全宣言例も紹介
火災発生の危険性と防止策
放電加工では、加工中に高温の放電が発生するため、加工液の管理が不十分だと火災の原因になります。
特に、加工液が汚れていると放電が不安定になり、異常発熱が起こることがあります。引火点が低い加工液を使用していた場合、より火災のリスクが高くなります。
また、作業場に可燃性の物質が近くにあると、飛び散った火花が引火し、大きな事故を引き起こす危険性もあります。
火災を防ぐためには、まず加工液の交換基準を明確にし、定期的にろ過や交換を行う必要があります。加工液が劣化すると、放電時の熱が適切に分散されず、異常発熱のリスクが高まります。また、作業場では防火対策として消火器や防炎シートを設置し、万が一の火災発生時にも迅速に対応できる環境を整えることが重要です。
作業者全員が消火設備の使い方を把握しているかどうか、定期的なKYT(危険予知訓練)やKY活動を行うことも効果的でしょう。現場改善ラボでは、それぞれの取り組みについて、専門家が実践的な内容を解説する動画を無料で公開しています。
以下のリンクをクリックするとご覧いただけますので、ぜひこの機会にご活用ください。
▼専門家による解説動画を見てみる
・効果のあるKYTとは?KYTの実情、3つの課題とその解決策
・元労基署長が解説!事故を未然防止するKY活動と4ラウンド法の在り方とは?
保護具未着用など作業服着用の誤りによる事故の危険性
放電加工では、加工中に微細な金属粒子が発生するため、適切な保護具を着用しないと、作業者の目や皮膚に悪影響を及ぼす可能性があります。
特に、保護メガネを着用していない場合、飛散した金属粉が目に入ることで視力に影響を与えることもあります。また、加工時に発生する放電の熱によって火傷を負うリスクもあるため、耐熱性の作業服や手袋を適切に使用することが求められます。
しかし、作業服の着用は「不慣れな新人の着用ミス」「ベテランの慣れによる軽視」が起こりやすい部分です。作業前点検を標準化し、作業者自身が保護具を適切に装着しているかチェックする仕組みが大切です。
安全教育や安全対策の側面で動画マニュアルを整備し、正しい着用手順を視覚的に見せたり、保護具を着用しなかったことで発生した事故例を動画で共有することで、安全意識を高める効果が期待できます。
▼「正しい作業服の着用方法」を動画マニュアルで見せる例▼
今回ご紹介したように、安全トラブルを防ぐ手段として動画マニュアルを活用する製造現場も多いです。安全教育や安全対策の一環で、動画マニュアルを活用している製造業の事例集を公開しているので、以下のリンクをクリックしてご覧ください。
>>「安全意識が高い製造現場はやっている! 動画マニュアルを活用した安全教育・対策事例」を見てみる
放電加工(EDM)のトラブルは「動画マニュアル」で対策
放電加工(EDM)は、精密加工が可能な一方で、品質トラブルや安全トラブルが発生しやすい加工方法です。
そのため、作業の標準化や安全管理が不可欠ですが、紙や文字の作業手順書だけでは伝わりづらい場面も少なくありません。そこで、多くの製造現場で活用され始めているのが「動画マニュアル」です。
ここからは放電加工のトラブルに対する動画マニュアルの有効性、多くの製造現場で導入されているツールをご紹介します。
放電加工特有の課題に対する「動画マニュアル」の有効性
放電加工の現場では、メンテナンス業務や段取り作業の正確性が、加工品質や機械の安定稼働に大きく影響します。しかし、こうした作業は手順が多く、新人や経験の浅い作業者、外国人従業員が正確に覚えるのが難しいという課題があります。
そこで、動画マニュアルを活用することで、作業の手順を「動作」として視覚的に伝え、誰でも理解しやすい環境を整えられます。
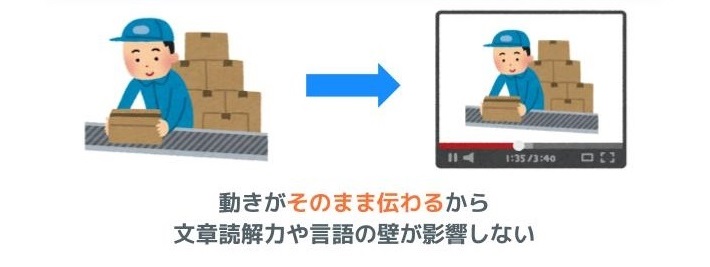
例えば、電極の交換作業や加工液の管理方法など、実際の手順を映像で示すことで、言葉だけでは伝わりづらい細かいポイントを分かりやすく解説できます。また、加工前の段取り作業においても、動画を見ながら確認することで、ミスを防ぎ、加工精度を安定させる効果が期待できます。
動画があれば、経験の浅い作業者でも「どのように動作すればよいか」を見て学べるため、作業の標準化が進み、品質トラブルや安全トラブルを抑止することが可能です。
このような製造現場における動画マニュアルの活用事例は、以下のリンクをクリックするとより詳しくご覧いただけますので、併せてご覧ください。
多くの製造現場で活用されている動画マニュアルツール
品質トラブルや安全トラブルといった現場課題の改善を目的に、多くの製造現場で活用されているのが、かんたん動画マニュアル作成ツール「tebiki現場教育」です。
動きが伴う作業手順やポイントを視覚的に分かりやすく伝え、品質改善や安全対策だけに限らず、業務標準化や新人教育の効率化、技術伝承、外国人従業員の教育など、現場の教育課題を解決する手段として活用されています。
このような製造現場の課題を解決するため、動画マニュアルの編集以外にも以下のような機能を搭載しています。
- 100カ国語以上への自動翻訳
- 字幕の読み上げ(多言語にも対応)
- アクセス履歴等がわかるレポート機能
- オリジナルのテストを作成できるテスト機能
- 従業員の力量管理やスキルマップ、教育計画作成などの人材スキル機能 など
実際に、製造現場の品質・安全トラブルの対策として、動画マニュアル「tebiki現場教育」を活用している事例として、児玉化学工業株式会社をご紹介します。
同社はtebiki現場教育を活用したことで、手順不遵守を9割削減して品質向上や従業員の不安全行動解消といった改善を実現しています。
▼インタビュー動画:児玉化学工業株式会社▼
児玉化学工業株式会社の取り組み内容をより詳しく知りたい方は、こちらをクリックしてインタビュー記事をご覧ください。tebiki現場教育の機能概要やプラン、その他の改善事例などを詳しく知りたい方は、以下のリンクをクリックしてサービス概要資料をご覧ください。
>>加工工程の品質トラブル・安全トラブルを改善できる「tebiki現場教育」の詳細を見てみる
放電加工のトラブルも動画マニュアルで解決しよう【まとめ】
放電加工(EDM)は、高精度な加工が可能である一方、品質トラブルや安全トラブルが発生しやすい加工方法です。
電極の摩耗や加工液の管理不足による寸法精度の低下、不適切な段取り作業が原因で発生する加工不良など、作業者の理解不足がトラブルの要因となることが少なくありません。また、高電圧を扱うため、感電や火災などの安全リスクも伴い、作業の正確性と安全対策が求められます。
こうした課題を解決するためには、動画マニュアルの活用が有効です。作業の流れや適切な動作を視覚的に伝えることで、新人でも正しい手順を理解しやすくなり、品質トラブルを抑止できます。また、不安全行動による事故のリスクを映像で伝えることで、作業者の安全意識を向上させ、トラブルを未然に防ぐことが可能になります。
放電加工の安定した品質管理と安全な作業環境の確立には、標準作業の確立とその徹底が不可欠です。紙のマニュアルでは伝わりにくい細かな動作や注意点も、動画マニュアルを活用することで、誰もが理解しやすくなります。放電加工におけるトラブルを最小限に抑え、生産性向上と安全管理を実現するためにも、動画マニュアルを活用し、現場の作業品質を底上げしていきましょう。
かんたん動画マニュアル作成ツール「tebiki現場教育」の資料は、以下のフォームを入力してチェックしてみてください。