かんたん動画マニュアル作成「tebiki現場教育」を展開する現場改善ラボ編集部です。
属人化とは「特定の従業員に業務知識やスキルが集中し、その従業員がいなければ業務が滞ってしまう状態」を指しますが、特に製造業では属人化が急速に進んでいる状況です。喫緊の課題ではあるものの「具体的な打ち手が分からず放置してしまっている製造現場」が数多く存在しています。
そこで本記事では、製造業に潜む「属人化を生む根本的要因」を分析するとともに、属人化を解消するための改善策を解説します。要因と対策をセットで理解することで、属人化を解消するための具体的な推進方法が分かるはずです。
ちなみに製造業における属人化は、新人教育の体制整備ができているかどうかに大きく依存します。属人化を発生させない教育体制の整備方法について先に知りたい方は、PDF資料「新人教育に失敗する製造現場に潜む3つの構造的要因と新しい教育アプローチ」をご覧ください。
目次
製造業の属人化が急速に進む背景
製造業における属人化は、業務効率の低下、品質のばらつき、人材育成の遅延など、企業にとって深刻なリスクをもたらします。近年、この属人化が製造業で急速に進んでいる背景には、以下3つの構造的要因が複雑に絡み合っているためです。
人材不足と高齢化
製造業においては、就業者数は直近では横ばいで推移しているものの、人材の高齢化と構造的な人手不足が長年にわたって課題となっています。厚生労働省の調査資料である「2024年版ものづくり白書」(下図,図2)によると、製造業における従業員数過不足DIは、2014年頃から一貫してマイナスの値を示しており、コロナ禍の一時期を除けば「継続的に人手不足感が強い状態が続いている」ことが分かります。
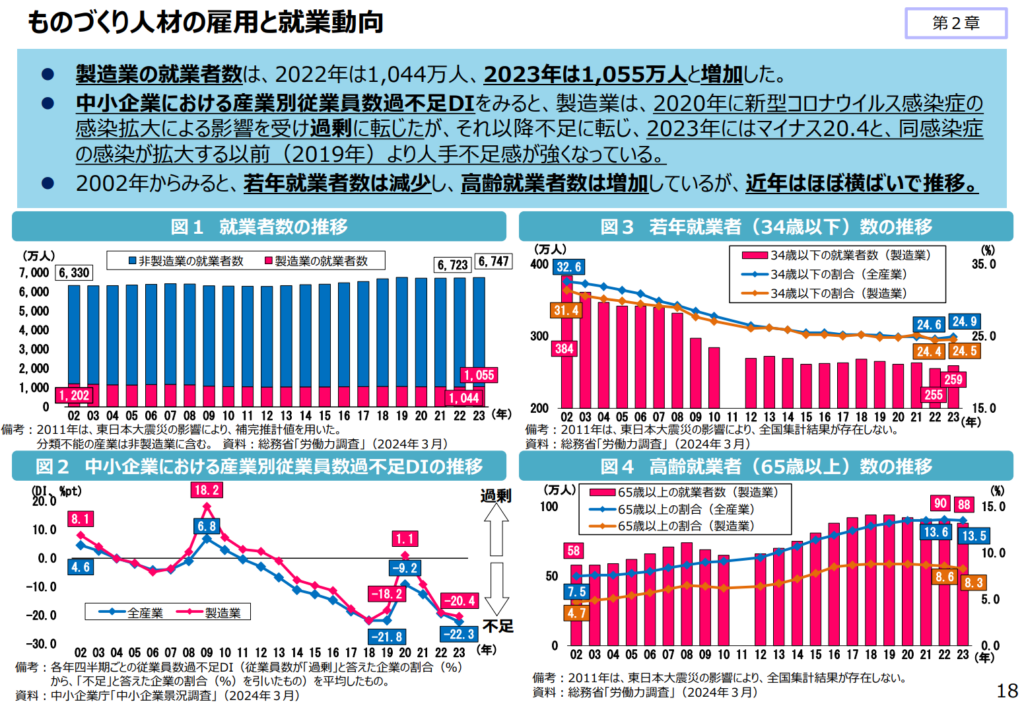
【「2024年版 ものづくり白書(P18) – 厚生労働省」より抜粋】
特に、2020年のコロナ禍による一時的な人材過剰感を経て、不足感が再び強まっており、コロナ禍以前の水準近くまで戻っていると言えます。
さらに、同白書(図3)によると、製造業における若年就業者(34歳以下)の割合は長期的に低下傾向にあります。つまり人材の高齢化が進んでいることが分かります。
このような長年にわたる人手不足と人材の高齢化が重なる状況は、特定の従業員に業務が集中する属人化を助長する大きな要因になっていると言えるでしょう。
進まない技術継承
前述した人材不足や人材の高齢化によってもたらされる課題が「技術継承」です。
製造業の現場では、長年の経験によって培われた高度な技術やノウハウを持つベテラン従業員が多く活躍しています。しかし高齢化が進む中で、これらの貴重な技術を次世代にスムーズに伝承することが難しくなっています。
技術継承が進まないことで、製造業特有の「複雑なプロセスが伴う業務」を遂行できる従業員が限られる場面、つまり属人化が進むことになります。
製造業における技術伝承をうまく推進するには、ベテラン社員が持つカンコツや暗黙知の可視化が鍵を握ります。そのためのポイントをまとめたPDF資料「技術伝承を成功させるポイント」を以下のリンクに掲載しているので、あわせてご覧ください。
DX化による業務スキルの高度化
現場DXが徐々に推進され始めている昨今は、これまで活用していた設備や機械がデジタル化により刷新される「転換期」でもあると言えます。すなわち、従来とは異なるやり方で業務を推進する場面も増え、求められる業務スキルがより高度化していると解釈できます。
例えば、これまで活用していた古い異常検知の機械が他製品にリプレイスされたことで、操作方法や求められる技術も変わり従業員のスキルがなかなか追いつかない、というようなケースです。
そのためこれからの製造現場では、現場の作業粒度に即した、従業員全体のスキルの可視化と一元管理が求められます。言い換えれば「従業員のスキル習得状況が適切に把握できるスキルマップを整備し、人員配置や生産計画を立てる」ことがより重要です。それを実現する例として、製造現場に特化したクラウド型スキルマップ「tebiki現場教育」では、下図のように「従業員ごとのスキル習得状況」を可視化します。
【「動画マニュアルが紐づくクラウド型スキルマップ – tebiki現場教育」より抜粋】
【事例あり】製造業の属人化が改善されない3つの要因
ここまでは「製造業が属人化しやすい理由」を産業構造の視点から解説しました。ではここからは、「なぜ製造業は属人化が進む構造になっているのか」を解説します。
結論から言うと、製造現場に潜む以下3つの要因が根強く残っていることが要因です。これらがなかなか改善されない限り、属人化解消のきっかけは掴めないと言えるでしょう。
- 形骸化したマニュアルや作業手順書
- OJT教育指導者の「教育品質のばらつき」
- 部署間や工場間の連携の取りにくさ
以下、それぞれの詳細を解説します。
形骸化したマニュアルや作業手順書
製造業が属人化しやすい要因のひとつに「マニュアルの形骸化」が挙げられます。製造現場では、マニュアルや作業手順書が形骸化している場合が珍しくありません。例えば以下のようなケースです。
- マニュアルはあるが読まれていない
- 作業手順書はあるが最新の内容に更新されていない
- 更新や翻訳が手間で運用がストップしている
こうした側面から、一部の従業員のみが必要な技術や知識を把握している状態が生まれ、全社共有されず、結果的に属人化を助長します。
例えば、工作機械や産業機械の製造販売を担う「新日本工機株式会社」は、「紙マニュアルの内容が正確に理解されにくい」「人によって内容の解釈が異なる」等から、紙マニュアル活用の限界を感じていました。結果的に同社は、動画マニュアル作成ツール「tebiki」を導入し、紙マニュアルからの脱却に成功しました。
紙マニュアルから動画マニュアルに乗り換える製造現場は徐々に増えてきており、動画は現場教育の有力な手法になりつつあります。製造業における動画マニュアルの活用事例をもっと読みたい方は、以下のPDF資料もあわせてご覧ください。
>>>PDF資料「製造業における動画マニュアル活用事例集」を見てみる
OJT教育指導者の「教育品質のばらつき」
前述したように、製造現場ではマニュアルの整備が難しいため、OJT(On-the-Job Training)による教育手法が採用されることが多いです。製造業における業務は複雑な作業手順や危険の伴う作業が多いので、むしろOJTによる教育は重要であり、ベテラン社員が直々に指導することで従業員の命や安全が守られていると言えます。
そんなOJT教育はメリットがある一方で、「教育担当者によって指導方法・指導内容が異なる」点が大きな課題となっています。指導者側のスキルや経験に依存した教育手法になるため、OJT教育の質はばらつきが生じやすいと言えます。
例えば、アサヒグループに所属する飲料の製造販売会社「アサヒ飲料株式会社」では、OJTによる課題の改善案を模索していました。
人材育成は基本的にOJTで行っていましたが、習熟者の力量が安定しないという課題がありました。その一つの原因として、教育担当者の教え方にバラツキがあるのではないかと考えています。また、頻度が多い業務の中には、OJTで直接教えてそのまま実践するので、手順書がないものもありました。手順書がないのは、作成するのに多大な労力がかかるので後回しになっていたからです。
同社は最終的に、教育品質のバラツキを解消する手段として「動画」による教育を導入。結果、手順書作成工数の大幅な削減や教育品質の均一化を実現しました。製造業における動画マニュアルの活用事例をもっと読みたい方は、以下のPDF資料もあわせてご覧ください。
>>>PDF資料「製造業における動画マニュアル活用事例集」を見てみる
業務の複雑性(標準化の難しさ)
製造業の現場では、製品の種類や製造工程が多岐にわたり、それぞれの業務に必要な知識やスキルが異なるため、業務が複雑化し、属人化が進みやすい状況にあります。特に以下のような側面が、製造業特有の業務の難しさを助長していると言えます。
- 高度な専門知識や特殊技能の必要性
- 業務の細分化と全体像の不明瞭化
- 業務の標準化や可視化の困難性
誰もが業務内容を理解し、遂行できるような環境整備が重要ですが、それを実行するのは決して容易ではありません。業務標準化は、あらゆる製造現場で課題のひとつとして認識はされているものの、改善まで一筋縄ではいかないのが実情です。
例えば、化学製品の製造・販売を手掛ける総合化学企業「堺化学工業株式会社」では、作業ノウハウの属人化を防ぐために「標準化」を課題として掲げていました。同社は「動画で作業の全貌を理解してもらいながら、実際に作業してもらえば改善につながる」と判断し、動画による教育フローを導入しました。
作業者は動画を見ながら1人でも作業ができるようになる。教育をする側も、受ける側も、負担が減ると思いますし、属人化を防げます。まさに標準化ですね。
なかでも製造現場に特化した動画マニュアル作成ツール「tebiki」は、クラウド上で動画を一元管理できるため、従業員がどこにいてもデバイスですぐマニュアルを確認できるのが強みであり、標準化につながった一因だと言えるでしょう。
tebikiの動画マニュアルで製造現場の標準化や教育が改善された事例や、tebikiの詳細機能についてまとめたPDF資料は、以下の画像をクリックしてご覧いただけます。あわせて参考にしてみてください。
製造業の属人化を放置するリスク
ここまで「属人化が進む製造業の産業構造」および「製造現場に潜む根本的要因」について解説しました。
それでは次に、属人化を放置し続けるとどのようなリスクが生じるのかについて、解説を進めます。以下5つが、属人化によって引き起こされる問題と言えます。
逆に言えば、属人化を解消するメリットはこの5つが解消されることでもあると言えます。
品質のばらつきと不良品の増加
属人化が進むと、作業品質が担当者に大きく依存するようになります。標準化された手順やマニュアルが整備されていないと、担当者ごとの経験や解釈に基づいて作業が行われるため「品質のばらつき」が生じやすくなるのです。
その結果、不良品の発生率が高まり、顧客からの信頼を失うだけでなく、損失の増大にもつながります。
例えば、あるベテラン作業員は長年の経験から独自のコツを持って作業を行い、高い品質を維持できていたとしても、その方法が共有されていなければ、他の作業員が同じ品質を再現することは困難です。このような状況では、不良率が高まったり、品質の安定性が損なわれたりするリスクがあります。
技術・技能のブラックボックス化による人員計画/生産計画の阻害
特定従業員のみが業務を把握する状態は、技術やスキルのブラックボックス化を招くため「効果的な人員配置や生産計画の策定」が著しく困難になります。従業員の能力が不明瞭なため、適材適所の人材配置が実現できず、結果として生産効率の低下や品質のばらつきが生じるのです。
さらに、属人化はISO9001(品質)やISO45001(労働安全衛生)の認証取得・維持の障害にもなります。これらの規格が要求する「組織の知識」の明確化・管理、従業員の「力量」確保、プロセスの標準化が、属人化によって困難になるためです。重要な業務知識は個人に偏在し、スキル把握も不十分で、業務は標準化されず、品質や安全性のリスクが高まります。
つまり、属人化は業務効率化の阻害だけでなく、企業の品質保証、労働安全衛生、信頼性や競争力にまで悪影響を及ぼす重大な問題です。ゆえに、スキルや業務知識を「見える化」し、組織全体で共有・活用できる体制構築が急務です。
スキルや業務知識を見える化するには、スキルマップの整備が必須です。例えば、製造業に特化したクラウド型スキルマップ作成ツール「tebiki現場教育」であれば、従業員ひとりひとりのスキル習得状況を一覧で可視化し、適材適所の人員配置を手助けします。tebikiの詳細機能や活用事例について簡単にまとまったPDF資料は、以下の画像をクリックするとご覧いただけます。あわせてご覧ください。
生産性の低下と納期遅延
属人化は業務の効率性を著しく低下させる要因となります。特定の担当者しか業務を遂行できない場合、その担当者が不在になった際に業務が滞ってしまいます。例えば、ある機械の操作やメンテナンスが特定の担当者しか行えない場合、その担当者が休暇や病気で不在になると、機械の稼働が停止し、生産ライン全体に影響が及ぶ可能性があります。
また、担当者の業務負荷が大きすぎる場合、納期遅延が発生するリスクも高まります。納期遅延は、顧客との信頼関係を損ねるだけでなく、契約解除や損害賠償請求につながる可能性もあります。
担当者の負担増と離職
属人化は、特定の担当者に過度な負担を強いることになります。業務が集中することで、担当者は常に時間に追われ、精神的にも肉体的にも疲弊してしまいます。
このような状況が続くと、担当者のモチベーションは低下し、最終的には離職につながる可能性が高まります。「離職」は、単に人員が減るだけでなく、企業にとって貴重なノウハウや経験の喪失を意味します。特に、熟練した技術を持つ人材の離職は、企業にとって大きな痛手となります。
新人教育や多能工化の停滞
属人化によって、特定の担当者しか業務を遂行できない状態が常態化すると、組織全体としての人材育成が進まなくなります。熟練者の技術やノウハウが若手人材に伝わらず、技術の継承が途絶えてしまうだけでなく、他の従業員が複数の業務をこなせる多能工化も進みません。
新人教育と多能工化は生産性向上に欠かせない要素ですが、属人化が進む製造現場ではいずれも停滞しがちであり、生産性を低下させます。
したがって新人教育の体制整備がなかなか進まない製造現場では、あらゆる対策が講じられている状況ですが、そのなかでも有効な教育アプローチ方法は限られています。製造業における新人教育のポイントや実践策について知りたい方は、以下のPDF資料もあわせてご覧ください。
>>>「新人教育に失敗する製造現場に潜む3つの構造的要因と新しい教育アプローチ」を見てみる
製造業における属人化の解消に必須な指針3つと具体策
属人化は、放置すれば企業にとって大きなリスクとなりますが、適切な対策を講じることで解消することが可能です。属人化を解消するためには、場当たり的な対応ではなく、組織全体で取り組むべき明確な指針を持つことが重要です。
以下、属人化解消に必須となる3つの指針を掲げます。
これら3つの指針を満たす打ち手が、属人化を改善するための最善策であり、その打ち手もあわせて解説していきます。
技術・ノウハウの継承を促進する仕組みづくり
属人化の大きな要因の一つは、熟練者の持つ暗黙知が形式知化されず、組織内に共有されないことです。そのため、個人の持つ技術やノウハウを組織全体で共有し、後進に確実に継承していくための仕組みづくりが不可欠です。
単なる技術だけでなく、長年の経験から得られる勘やコツといったノウハウも継承の対象とすることで、より効果的な技術伝承が可能になります。考えられる主な取り組みとしては、以下のようなものが挙げられます。
- ベテラン社員の技術が可視化されたマニュアルの整備
- 研修制度の充実
- ナレッジ共有ツールの導入
これらの仕組みを整備することで、属人化を防ぎ、組織全体の技術力向上に繋げることができます。一番推奨される取り組みは「マニュアルの整備」です。しかし紙マニュアルではベテラン社員のカンコツや暗黙知といった「文字では伝わらない技術」を可視化できません。
そこで、技術継承の手段として採用されている現代の教育方法が「動画マニュアルによる教育」です。
例えば、自動車部品や住宅設備等のプラスチック成形品を手掛ける製造企業である「児玉化学工業株式会社」では、現場従業員が以下の動画マニュアル「ヤスリでバリを取る業務プロセスの解説」を作成し、技術をスムーズに共有しています。
▼動画マニュアルによる技術継承の例(音量にご注意ください)▼
※現場従業員が「tebiki」で作成
一目で「何をどうすればいいか」が把握でき、文字では伝えにくい動きもすべて理解できるようになっています。
業務の「標準化」と「可視化」を推進する環境整備
業務プロセスが標準化・可視化されていない場合、担当者によって作業手順や品質にばらつきが生じ、属人化が進みやすくなります。そのため、業務プロセスを標準化し、誰でも同じ品質で業務を遂行できるようにすることが重要です。また、業務を可視化することで、業務のボトルネックや改善点を発見しやすくなり、効率的な業務運営が可能になります。
誰もが同じ品質で業務を遂行できるようになるには、「作業手順書の整備」が重要です。多くの製造現場では、作業手順書が整備されていない、または「手順書はあるが更新されていない」状態が目立ちます。
また、整備されていても「読み手によって解釈が異なる」「複雑な動きが明文化されていない」という実態もあり、作業手順書が形骸化していることが多いです。
したがって、「誰もが簡単に作成・更新できるマニュアル」かつ「一目で見て業務内容が把握できるマニュアル」の整備が最善です。それを実現する有力な手段として「動画マニュアル」が挙げられます。
例えば以下の動画は、工作機械や遠心力鋳造管・産業機械の製造/販売を手掛ける「新日本工機株式会社」の現場従業員が作成した動画マニュアルです。スマートフォンで撮影しています。
▼動画マニュアルによる標準化の例(音量にご注意ください)▼
※現場従業員が「tebiki」で作成
このように、現場従業員でもスマホで手軽に撮影・編集ができる動画マニュアル作成ツールであれば、業務プロセスの標準化や可視化が可能になります。
教育担当者が不在でも新入社員が学習できる教育基盤の構築
従来のOJTに偏った教育方法では、教育の質が教える担当者に依存し、属人化を助長する可能性があります。また、OJT担当者の稼働時間を圧迫し、生産性の低下にもつながります。
したがって、「教育担当者がいなくとも新入社員が学習できる教育体制」が必須です。その手段のひとつとして「動画」による教材が挙げられます。
例えば以下の動画は、食肉販売専門店である「株式会社ジャンプ」で実際に使われている動画マニュアルです。
▼教育担当者不在でも学習できる動画マニュアルの例(音量にご注意ください)▼
※現場従業員が「tebiki」で作成
教育担当者がいなくとも、教育担当者の動きを目で理解することが可能です。また、「誰が教えても同じ教育内容」になるのも、教育品質のばらつきを解消できる動画のメリットとなります。
ここまで紹介した動画マニュアルはすべて、製造現場に特化した動画マニュアル作成ツール「tebiki」によって作成されています。tebikiの詳細機能や活用事例についてもっと知りたい方は、以下のPDF資料もあわせてご覧ください。
動画マニュアルtebiki導入で属人化を解消させた事例
動画マニュアルtebiki導入で属人化を解消させた事例として、以下の2社を紹介します。
- 新日本工機株式会社
- トーヨーケム株式会社
新日本工機株式会社
新日本工機株式会社は、若山鐵工所という名称で創業し、1949年に現在の新日本工機(SNK)というブランドで設立した企業です。事業としては工作機械や遠心力鋳造管、産業機械の製造販売があり、工作機械の売上が全体の9割程度を占めています。
新日本工機株式会社は、特定の作業者が独自のノウハウを持ってはいるものの、他のスタッフには伝わっていない状態で属人化が発生していました。従来のマニュアルは文字情報のみで、具体的な作業の様子やコツが伝わりにくかったことが原因です。
そこで、新日本工機株式会社はtebikiを導入し、作業手順やノウハウを動画で記録し始めました。結果として新日本工機株式会社はtebikiを活用することで、新しいスタッフも短期間で作業を覚えられるようになり、属人化の問題が大幅に解消されました。
参考元:人が育つ環境づくりとして動画マニュアルtebikiを活用。技術の蓄積と作業品質の安定を実現。
トーヨーケム株式会社
トーヨーケム株式会社は、東洋インキグループでポリマーや塗加工関連の事業を中心に展開している企業です。
トーヨーケム株式会社は、特定の技術者や担当者にしか知られていない技術やノウハウが存在することが課題でした。技術者が不在の際や退職した場合、ノウハウが失われるリスクを抱えていました。また、新人教育や技術の継承に時間がかかり、OJTのムラや非効率性が生じるといった課題を抱えていました。
トーヨーケム株式会社は、属人化を解消するために動画マニュアルtebikiを導入。tebikiを活用することで、技術やノウハウを動画で可視化し、社員間で共有することが可能となりました。具体的には、新人からベテランまでの社員教育、安全教育、さらには社員紹介など、幅広い用途での活用が実現しています。
動画マニュアルは文字や静止画よりも分かりやすく、実際の作業の流れをリアルに伝えられるため、技術伝承や多能工化の教育がスムーズに進むようになりました。さらに、マニュアルの作成工数が半分に短縮され、OJTの時間も大幅に削減されました。
参考元:新人からベテランまで700名を超える組織教育のグローバルスタンダードを目指す
まとめ:製造業の属人化を解消する鍵を握るのは「現場教育」の整備
製造業の属人化は、産業構造の観点からみると必然的に起こり得る事象です。しかし、放置し続ければ以下のような大きなリスクを招きます。
- 品質のばらつきと不良品の増加
- 生産性の低下と納期遅延
- 担当者の負担増と離職
- 新人教育や人材育成の停滞
だからこそ適切な対策を講じる必要があり、その指針として以下3つの視点が必須であることを解説しました。
- 技術・ノウハウの継承を促進する仕組みづくり
- 業務の「標準化」と「可視化」を推進する環境整備
- 担当者に偏らない多角的な育成システムの構築
これらを実現する手段のひとつに「動画マニュアル」が挙げられます。ベテラン社員の技術を可視化し、教育担当者がいなくともベテラン社員の動きがその場で見てわかるようになるからです。多くの製造現場で動画マニュアルは導入され始めています。
なかでも、製造現場に特化した動画マニュアル作成ツール「tebiki現場教育」は、現場担当者でもスマホひとつで手軽に動画を撮影・編集できます。
マニュアルや作業手順書は「暗黙知を理解している現場担当者が作成することに価値がある」ので、tebikiで属人化を解消し、現場教育の体制整備を検討してみてください。