かんたん動画マニュアル「tebiki現場教育」を展開する、現場改善ラボ編集部です。
工場内の安全を確保するには、発生したヒヤリハットを認識し、適切な対策を講じることが大切です。しかし「ヒヤリハットが多発しているが、具体的な対策がわからない」「ヒヤリハットを未然に防ぐための教育方法に悩んでいる」という方も多いのではないでしょうか。
そこで、本記事では工場で発生しやすいヒヤリハット事例とその原因や対策について解説します。安全意識が高い現場による実際の対策事例や安全教育に有効なツールも紹介するので、安全管理に携わる方は最後までご覧ください。
目次
【8つのシーン別】工場で発生しやすいヒヤリハット事例
厚生労働省による「職場のあんぜんサイト」を参考に、発生した種類ごとのヒヤリハット事例を8つのシーン別に21件ご紹介します。
- はさまれ・巻き込まれ
- 転倒
- 動作の反動・無理な動作
- 墜落・転落
- 切れ・こすれ
- 激突
- 感電・火災
- 有害物との接触
工場内で発生しやすいケースも多いため、従業員の安全教育や安全対策にお役立てください。なお、下記のようなイラストつきでわかりやすいヒヤリハット事例集もご用意しておりますので、是非お役立てください。
>>現場の213名に聞いた!実際のヒヤリハット事例や対策集をみてみる(無料)
はさまれ・巻き込まれ
挟まれ・巻き込まれに関するヒヤリハットとして、以下の事例が報告されています。
作業の種類 | ヒヤリハットの状況 | 発生した理由 | 対策 |
---|---|---|---|
金属製品の切削加工作業(製造業) | フライス盤での作業中に切粉を払ったところ、軍手がドリルに巻き込まれそうになった。 | ・清掃中にフライス盤を停止させなかった。 ・切粉を除去する際に軍手を着用していた。 | ・清掃の際はフライス盤を停止させる。 ・ドリルに巻き込まれる恐れがある作業時は、軍手を外す。 |
プレス機械を用いた圧着成形作業(製造業) | 圧着後の金型を取り出す際、プレス機械に手を入れてしまい、挟まれそうになった。 | ・下降中にプレスの下に手を入れた。 ・設備の安全対策が不十分であった。 | ・工具を使用し、手を入れる必要がない作業内容に変更する。 ・身体の一部が危険領域に入った際に、機械が自動停止するようインターロックを取り付ける。 |
関連記事:【製造業】「挟まれ・巻き込まれ災害」を防ぐ6つの方法!事例も解説
転倒
転倒に関するヒヤリハットとして、以下の事例が報告されています。
作業の種類 | ヒヤリハットの状況 | 発生した理由 | 対策 |
---|---|---|---|
ダンボールの運搬作業(食品製造業) | トマトが入ったダンボール4箱を重ねて運ぶ際、斜路で滑りそうになった。 | ・作業靴の底がすり減っていたことに気付かなかった。 ・運搬通路の斜路が急かつ湿っていたため滑りやすくなっていた。 | ・作業靴を定期的に点検し、靴底がすり減っている場合は交換する。 ・斜路はゴムマットなどを用いて、滑り止め加工を行う。 |
アーク溶接作業(製造業) | 作業場を移動する際、床に散乱したアーク溶接機のコードに足を引っ掛けて転倒しそうになった。 | ・使用したホースや工具をそのまま放置していた。 ・工具などの置き場や管理方法、管理担当者が決められていなかった。 | ・コードやホースは床に放置せず、一定の場所に巻いて保管し、必要に応じて使用するようルール化する。 ・工具などの管理担当者を決めておく。 |
クリーンルーム内での洗浄作業(製造業) | クリーンルームでの洗浄作業後、マットに足を取られて転倒しそうになった。 | ・足元に注意を向けていなかった。 ・クリーンルームを使用する際の注意点を理解していなかった。 | ・粘着マットへの注意喚起ポスターをクリーンルーム内に掲示する。 ・クリーンルーム内の歩行方法や使用人数、注意点について教育する。 |
関連記事:【事例も紹介】転倒災害が発生しやすい環境とは?現場で実践できる改善策も
動作の反動・無理な動作
動作の反動・無理な動作に関するヒヤリハットとして、以下の事例が報告されています。
作業の種類 | ヒヤリハットの状況 | 発生した理由 | 対策 |
---|---|---|---|
点検作業 (製造業) | 大型ローラーコンベアの上を急いで歩いていた作業員が、ローラーに足を取られて転倒し、膝を打った。 | ローラーコンベア上を歩くことは禁止されていたが、守られていなかった。 | ・ローラーコンベア上での歩行禁止を徹底する明確なルールを作成し、作業員全員に周知する。 ・定期的に監視を行い、違反行為があれば厳格に対応する。 |
清掃作業 (製造業) | 天井近くの機器を清掃時に、ダクトの上でつま先立ちになり、滑り落ちそうになった。 | ・適切な足場や安全器具を使用せず、不安定な場所で作業を行っていた。 ・高所作業に対するリスク意識が不足していた。 | ・ローラーコンベア上での歩行禁止を徹底する明確なルールを作成し、作業員全員に周知する。 ・定期的に監視を行い、違反行為があれば厳格に対応する。 |
フォークリフトでの運搬作業(物流業) | フロント窓枠から身を乗り出したときに膝でレバーを引き、窓枠とマストの間で首が挟まりそうになった。 | 確認作業中に体を無理に乗り出したため、危険な姿勢になっていた。 | ・フォークリフトの操作手順を見直し、確認作業時に無理な姿勢を取らないよう指導を徹底する。 ・レバーの誤操作を防ぐためのガードやカバーを設置する。 |
関連記事:フォークリフトのヒヤリハット事例集と対策まとめ!危険予知の事例もあわせて解説
墜落・転落
墜落・転落に関するヒヤリハットとして、以下の事例が報告されています。
作業の種類 | ヒヤリハットの状況 | 発生した理由 | 対策 |
---|---|---|---|
フォークリフトによる資材荷上げ作業(野菜研究施設) | 中2階で荷物を受け取る際に、フォークリフトのパレットに足をかけてふらつき、落ちそうになった。 | ・フォークリフトのパレットに誤って足をかけた。 ・フォークリフトのフォークを中2階に差し込まなかった。 | ・荷物の積み込みや積み卸しを行う際には、フォークを作業床にしっかり差し込む。 ・必要に応じて安全帯を使用する。 |
トラックからの荷降ろし準備(運送業) | 荷台に載せた鋼材の上で作業した際、雨で濡れた鋼材で足が滑り、荷台から転落しそうになった。 | 足元への注意が不足していた。 | 荷台から落下しないように安全帯を着用する。 |
鋼板加工作業(製造業) | 台車上から作業用椅子を使って降りようとした際、ぐらついて転落しかけた。 | 作業用椅子を踏み台として使用した。 | 作業用椅子を踏み台の代用としないよう、ルールを整備し周知する。 |
切れ・こすれ
切れ・こすれに関するヒヤリハット事例は、以下の通りです。
作業の種類 | ヒヤリハットの状況 | 発生した理由 | 対策 |
---|---|---|---|
切断作業(製材業) | バンドソーを動かしたまま盤上のゴミを取り除こうとし、回転している刃に手が当たりそうになった。 | バンドソーを停止せずに清掃しようとした。 | 電源スイッチを切り、停止させた状態で清掃する。 |
食肉の加工作業(食料品小売業) | 豚肉の塊を切断する際、右手中指が安全カバーのないスライサーの回転刃に触れそうになった。 | ・スライサーの回転刃に安全カバーが設置されていなかった。 ・食材を支える際に専用の道具を使用せず、手で直接持って作業を行っていた。 | ・回転刃の使用しない部分にカバーをつける。 ・スライスする食材を支える時は専用の道具を使う。 |
激突
激突に関するヒヤリハットには、次のようなものがあります。
作業の種類 | ヒヤリハットの状況 | 発生した理由 | 対策 |
---|---|---|---|
製造設備機械の積卸し作業(製造業) | 機械をクレーンで吊ってトラックから下ろす際、荷が不安定だったため急に回転し、作業員に激突しそうになった。 | 荷が不安定な状態であったが、玉掛けを修正せずに吊り上げ作業を続行した。 | 荷物の積み下ろし作業時には、荷の形状や重心をよく確認し、最も安全な方法で玉掛けを行う。 |
市場内荷卸し作業(食品製造業) | 方向転換のためにフォークリフトをバックさせた際、近くにいた作業者と激突しそうになった。 | ・作業者がフォークリフトの作業場を自由に行き来できる状態だった。 ・フォークリフトの誘導員が配置されておらず、作業計画も十分に定められていなかった。 | ・フォークリフトの作業場に作業者が立ち入らないよう、ルールを整備する。 ・フォークリフトの作業計画を定めた上で周知徹底し、運行時には誘導員を配置する。 |
運搬作業(食品製造業) | 小走りで台車を運搬していた際、柱の角から急に出てきた作業員と衝突し、滑って転倒した。 | 通路床面が気化したバターや食用油で滑りやすくなっており、台車のブレーキが効きにくい状態であった。 | ・定期的に床面を清掃し、滑りやすい状況を防ぐ。 ・通路での歩行や運搬時の安全ルールを再確認し、小走りを禁止するように指導する。 |
感電・火災
感電・火災に関するヒヤリハットとしては、以下の事例が報告されています。
作業の種類 | ヒヤリハットの状況 | 発生した理由 | 対策 |
---|---|---|---|
製鋼作業(鉄鋼業) | 電気炉に近づいた際、酸素ガスの流量が異常に多いことに気づき、酸素バルブを閉止した。 密閉された空間であれば、高酸素濃度により燃え出す可能性があった。 | ・電源系のコードに異常があって停電したため、機械が停止した。 ・機械が停止しても、酸素の供給が止まらなかった。 | ・機械が停止した場合には、関連機器も自動的に停止するよう設定する。 ・流量や圧力などが規定範囲内を超えた際には、自動停止や警報装置を作動させる。 |
その他(喫煙スペースの管理) | 吸い殻をスチール缶に集めて通路に置いていたところ、自然発火した。 | ・吸い殻が完全に消火されず、スチール缶内で発火した。 ・通路に可燃物を置くリスクが認識されていなかった。 | ・吸い殻を捨てる前に完全に消火するよう徹底する。 ・専用の消火設備が整った耐火性の容器を使用し、吸い殻を置かないようにする。 |
溶接作業(建設業) | 水管の溶接作業中、アーク溶接の火花が作業員の作業服に引火し、慌てて消火した。 | ・作業員が適切な防火対策を講じていなかった。 ・作業服が耐火性ではなく、火花が引火しやすい材質であった。 | ・耐火性の作業服や防火エプロンの着用を義務付ける。 ・溶接作業エリアに消火設備を設置し、防火教育を徹底する。 |
有害物との接触
有害物と接触するヒヤリハット事例は、以下の通りです。
作業の種類 | ヒヤリハットの状況 | 発生した理由 | 対策 |
---|---|---|---|
洗浄作業(製造業) | エタノールを用いたブラシ洗浄作業中に、液体が飛散して目に入りそうになった。 | 作業中に適切な保護具(ゴーグル)が着用されていなかった。 | エタノールなどの化学薬品を扱う際は、必ずゴーグルやフェイスシールドなどの適切な保護具を着用することを義務付ける。 |
排出弁の閉塞物の除去作業(医薬品製造業) | フィルター装置底部にある排出弁を手作業で開けようとしたところ、突然排出弁から70〜80℃の3%濃度のNaOH水溶液が流出し、右足を火傷しそうになった。 | 閉塞物を棒で突いて取り除く作業の危険性を認知していなかった。 | ・安全教育で棒で突いて除去する危険性を周知し、適切な方法で除去できるようにする。 ・やむを得ず突く場合は、内圧がないことを確認したのち、保護衣・保護メガネ・手袋等を着用して慎重に行う。 |
ここまで、シーン別に工場で発生しやすいヒヤリハットの事例をご紹介してきました。ヒヤリハットが発生した理由は事故によって異なるものの、その状況に陥る不安全行動や判断などをしてしまう原因は別にあるでしょう。
次章では、ヒヤリハットにつながる行動や判断をしてしまう原因について整理します。
ヒヤリハットが発生する主な原因
ヒヤリハットにつながる不安全行動や判断をしてしまう背景には、下記のような原因が潜んでいる可能性があります。
- 作業手順の不徹底
- 教育・訓練の不足
- 作業環境の問題
- 作業者の疲労やストレス
- コミュニケーションの不足
ヒヤリハットに潜む原因や背景については、労働コンサルタントによる解説動画でも詳しくご紹介しています。以下のリンクをクリックして、参考情報としてご覧ください。
>>ヒヤリハットはなぜ起こる?減少に向けたヒントを専門家の解説動画から学ぶ(視聴無料)
作業手順の不徹底
作業手順の不徹底は、急速に人員が増加している職場やマニュアル/作業手順書の整備が不十分な職場で起こりやすいヒヤリハットです。作業手順が明確に設定や周知がされていない場合、作業者が自己判断で作業を進めることになり、事故やミスのリスクが高まります。
また、作業手順の重要性を認識していないと作業者が正しい手順を守らず、結果として事故を引き起こす可能性があります。たとえば、工作機械の整備前に電源を切る手順が定められていても、その手順が必要な理由が周知されていなければ、作業者が手順を守らずに機械を動かしたまま清掃を行う可能性が高いです。
このような状況では、工作機械に指を挟みそうになるヒヤリハットが発生しかねません。では、作業手順はどのようにして守らせるべきでしょうか?「手順が守られる」作業手順書を整備するポイントについて知りたい方は、以下のハンドブックをご覧ください。
>>“手順書通りにできない”から卒業!わかりにくい手順書を改善するコツをみる
教育・訓練の不足
教育・訓練の不足は、短期労働者や外国人労働者が多い職場で起こりがちなヒヤリハットです。教育や訓練が不十分だと、作業者が必要な知識やスキルを十分に習得できず、作業中にミスや誤解が生じやすくなります。
特に、新入社員や経験の浅い作業者が適切な教育や訓練を受けていない場合、作業手順や安全対策を正しく理解できず、予期せぬトラブルが発生しやすくなります。例として、化学薬品を扱う作業者が薬品の取り扱いや安全対策について十分に教育されていない場合、誤った操作で薬品が混合され、危険な化学反応が起こる恐れがあります。
このような状況では、火傷や健康被害を引き起こすヒヤリハットが発生しやすいです。
関連記事:製造業の現場教育が進まない原因と改善事例!新人教育手法も解説
作業環境の問題
作業環境の問題は、整理・整頓(2S)が行き届いていない職場や、照明や換気が不十分な職場で特に発生しやすいヒヤリハットです。実際に、現場改善ラボ会員231名を対象に行ったアンケート結果でも、作業環境や設備の問題を課題視する声が最も多い結果となりました。
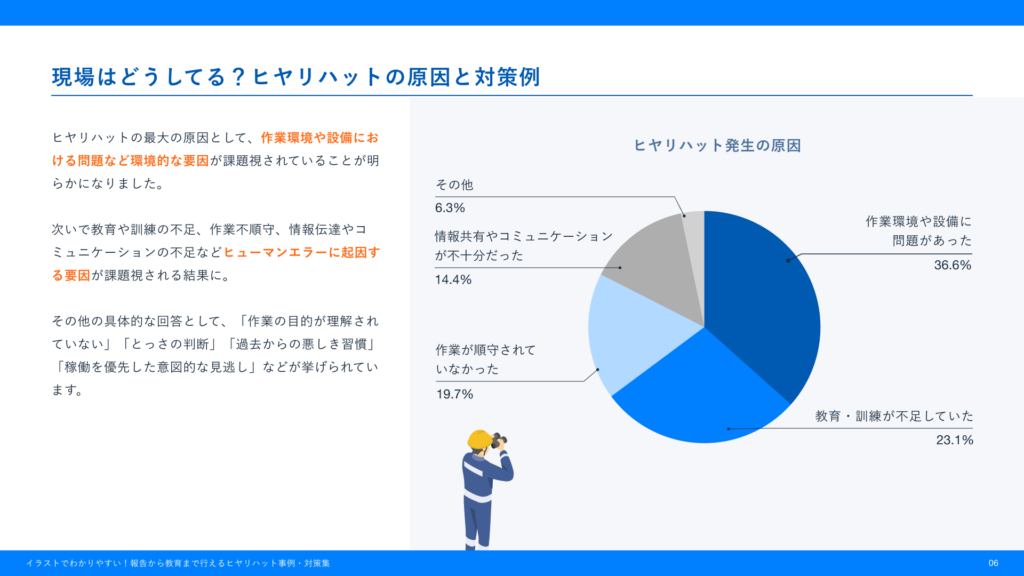
PDF資料「イラストでわかりやすい!報告から教育まで行えるヒヤリハット事例・対策集」より引用
作業環境が適切ではない場合、作業者は安全かつ効率的に作業を行うことが難しくなり、ヒヤリハットや事故のリスクが高まります。
たとえば、通路が狭く資材や道具が散乱している環境では、作業者がそれらにつまずいて転倒する可能性が高いです。さらに、照明が不十分で作業エリアが暗いと、道具で手を挟んだり、機械や壁にぶつかるヒヤリハットが起こりやすくなります。
作業者の疲労やストレス
長時間労働が常態化している職場や、精神的なプレッシャーが強い職場では、作業者が疲労やストレスによってヒヤリハットを引き起こしやすくなります。作業者が疲労やストレスを抱えると、集中力や判断力が低下し、作業ミスや事故のリスクが高まります。
たとえば、疲労により集中力が低下した作業者がフォークリフトを運転した場合、周囲の確認を怠り、近くにいる作業者に衝突しそうになるヒヤリハットが発生しやすくなるでしょう。
コミュニケーションの不足
シフト制や交代勤務の職場、外国人労働者が多い職場では、コミュニケーション不足によるヒヤリハットが起こりやすいです。コミュニケーションが不足すると、業務に関する重要な情報が正しく伝わらず、従業員が誤った作業を行うリスクが高まります。
例として、原材料や機器の置き場が変更された際、日勤のチームにはその変更が伝わっていても、夜勤のチームには正確に伝わらないことがあります。このような状況では、夜勤の作業者が過去の手順で作業を続けることにより、原材料や機器につまずいて転倒するヒヤリハットが起こる可能性が高いです。
ヒヤリハットの背景には、上記で挙げたようなヒューマンエラーによる課題のほか、機械や材料などモノに由来する課題も存在しています。
このような課題を含めた現場に潜むリスクを洗い出すには「リスクアセスメント」の実施が効果的です。リスクアセスメントの詳細や具体的な進め方について元労働基準監督署署長の解説による以下の解説動画も是非ご覧ください。
>>現場に潜むリスクはどう洗い出す?事故を発生させない「本質安全化」の実践方法(視聴無料)
ヒヤリハットを活用し、再発を防止する4つの対策
現場でのヒヤリハットは、労働災害に繋がりかねない要注意事項です。しかし、これらの小さな兆候こそが、将来発生しかねない重大事故を未然に防ぐための重要なヒントであるといえるでしょう。
ここでは、ヒヤリハットを活用して事故を未然防止できるような4つの対策についてご紹介します。
- ヒヤリハット報告の推奨
- 5S活動の徹底
- KYT(危険予知訓練)の実施
- マニュアル/作業手順書の整備
「似たような対策はすでにしているけど、なかなか再発防止に至っていない…」とお悩みの現場には、ある共通点があります。繰り返すトラブルの再発防止に向けたポイントについて、以下の無料動画内でも解説しているため併せてご覧ください。
>>ミスやトラブルの再発防止を組織で達成するには?効果のある再発防止策と現場で活かせる具体例
ヒヤリハット報告書の作成
ヒヤリハットを事故防止に活用するには、ヒヤリハットとの距離が最も近い現場の従業員からの報告が欠かせません。一方で、ヒヤリハット報告を行っていると回答した現場が約85%と高い一方で、「報告書を作成するのが面倒」「報告する意味を感じられない」「叱責されると思った」という理由から報告を避けてしまうケースがあることも判明しています。
そのため、作業者がヒヤリハットを即座に報告できる環境を整え、報告をもとに迅速に改善策を検討・実施する体制が求められます。例えば、簡単にヒヤリハットを報告できるフォーマットの整備や、報告した作業者を評価する制度を設けることで、作業者からの報告がより積極的になるでしょう。
▼ヒヤリハット報告書の例▼
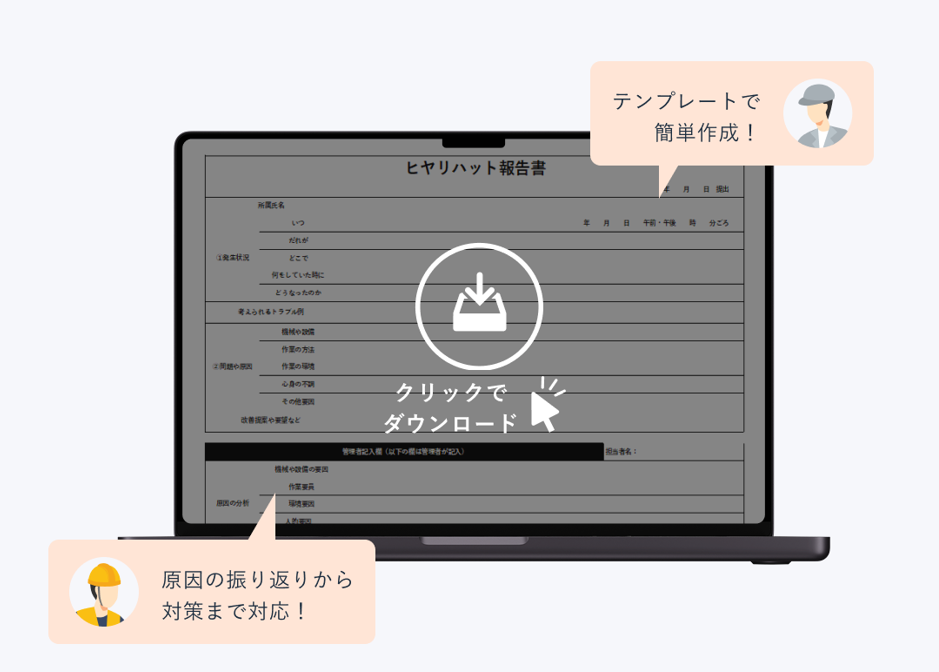
こちらのヒヤリハット報告書(Excel形式)については、以下のリンクから無料でダウンロードできる資料内に格納されているため、是非ご活用ください。
報告の「ネタ切れ」を防ぐには?
ヒヤリハット報告が継続的に行われるには、まずその目的を現場に浸透させることが重要です。ヒヤリハットが重大事故を防止するための有効な気づきであると認識してもらうことで、報告のモチベーションを維持しやすくなります。
また「誰のための取り組みか」を意識させることも効果的です。ヒヤリハットの報告が同僚や後輩、そして将来の作業者の安全を守る行為であると知ってもらうことで、その意義がより明確になり、ネタ切れを防ぐための取り組みにつながります。
さらに、ヒヤリハットの報告者を積極的に褒めることも重要です。「ヒヤリハットを報告すると責められる」と誤解し、非難を恐れてヒヤリハットを発見しても報告しない傾向があるかもしれません。そのため、ヒヤリハットの報告があった際は、「よく報告してくれた。事故を防ぐヒントをありがとう」という声掛けをすることで、積極的な報告が促進される可能性が高まります。
ヒヤリハットのネタ例や報告書の例文について知りたい方は、以下の記事もご覧ください。
関連記事:ヒヤリハットのネタ切れ対策方法とは?具体的な事例やネタを紹介
5S活動の徹底
5S活動(整理・整頓・清掃・清潔・しつけ)を徹底することで、作業環境を整備し、ヒヤリハットにつながる潜在的なリスクを取り除くことが可能です。具体的には、定期的な整理整頓活動や清掃当番の導入などが有効です。
まず、整理整頓を徹底することで、作業者の動線が確保され、つまずきや転倒のリスクを減らせます。また、清掃を徹底することで不要なものを排除し、火災や機械の故障による事故を防ぐことができます。
さらに、しつけを徹底して清潔な状態を維持することで、作業者全員が安全意識を持って行動するようになります。これにより、作業環境の整備と安全意識の向上が相まって、ヒヤリハットの発生を効果的に防ぐことができます。
5S活動の各要素や具体的な進め方について知りたい方は、数々の企業で5S改革を行った経歴を持つ講師による以下の解説動画をご覧ください。
>>単なる環境美化で終わらせない!効果的な5S活動の実践方法を学ぶ(視聴無料)
KYT(危険予知訓練)の実施
ヒヤリハットを活用した対策案を考えるには、KYT(危険予知訓練)の実施も効果的です。KYTは作業中に潜在する危険を事前に察知し、事故を未然に防ぐ実践的な安全教育の一種です。KYTを実施することで、作業者は現場でのリスクを把握し、適切な対策を講じる能力を高めることができます。
※危険予知訓練(KYT)の詳細や効果的な実践方法は、以下の記事で解説しています。
関連記事:危険予知訓練(KYT)の動画や4ラウンド法を用いた進め方!例題と解答つき
具体的には、月ごとのヒヤリハット事例をもとに、製造現場の危険箇所やその回避方法を全員で検討することが有効です。作業者全員でディスカッションを行い、KYTの成果を工場内の掲示板にまとめることで、日常業務の中で自然とリスク意識が高まります。これにより、安全な作業習慣を身につけることが可能です。
一方で、KYTが不十分であったり実施されていない場合、作業者は現場のリスクを十分に認識できず、ヒヤリハットに気づかずが重大な事故に発展するリスクが高まります。KYT(危険予知訓練)の進め方や例題を知りたい方は、安全衛生コンサルタントによる以下の解説動画もクリックしてご覧ください。
>>あなたのKYT、マンネリ化していませんか?改善に向けたヒントはこちら(視聴無料)
マニュアル/作業手順書の整備
現場で発生したヒヤリハット報告を収集し、その内容をもとにマニュアルや作業手順書を作成・見直すことで、重大な事故を防止できる可能性が高まります。
たとえば、作業者が機械の操作ミスによるヒヤリハットを報告した場合、その報告内容をもとに機械操作の手順書の注意点やチェックリストを改訂します。その後、改訂された手順書を作業者全員に共有し、内容が確実に伝わるようにすることで、操作ミスによる事故を防止できます。
一方で、ヒヤリハット報告をもとに作業手順が整備されていない場合、作業者は不完全な手順に従うことになり、怪我や事故につながるリスクが高まるため十分な注意が必要です。
効果的なマニュアルや作業手順書の整備に関しては、後述する『「tebiki」による教育で社内ノウハウを可視化し、事故を未然防止!』や、以下のガイドブックでも詳しくご紹介しています。是非ご覧ください。
安全意識を高める手段に「動画マニュアル」が注目されている
ヒヤリハットは、上手く共有・活用することで事故の未然防止につなげられる出来事です。そのためには、組織全体で高い安全意識を持ち、ヒヤリハットを安全文化の一部として根付かせることが重要です。
さまざまな現場の安全対策を支援してきた私たちTebikiは、安全意識を高めて安全文化が根付いている組織には、以下の特徴があると考えています。
危険感受性が高い | 職場における潜在的な危険要因を早期に察知し、事故や災害につながるような不安全行動や判断を回避できる |
現場の危険が可視化/記録されている | 現場における危険な作業やエリアなどが可視化されていたり、過去に起きた安全トラブルの記録が閲覧できる |
では、このような安全意識や安全文化を根付かせるには、どうすればいいのでしょうか?ここで、注目されているのが「動画マニュアル」の活用です。
「動画マニュアル」で危険を可視化し感受性を高める
従業員の危険感受性を高め、現場の危険を可視化するには、動画マニュアルを活用した教育がおすすめです。
動画マニュアルによる教育とは、作業手順や安全対策、製品の取り扱い方法などを動画形式でまとめ、社員教育に活用する方法です。従来の紙ベースのマニュアルとは異なり、視覚と音声を通じて具体的な手順や注意点を伝えられるため、社内に潜む危険やリスクを可視化しやすいというメリットがあります。
例として、以下の動画マニュアルサンプルをご紹介します。
▼ロール台車の扱い方(株式会社イセ食品様提供)▼
ロール台車の扱い方について動画で解説することで操作方法が視覚的に理解できるほか、事故のリスクが視覚的に伝わることでヒヤリハットをイメージできるようになり、危険感受性が向上することがうかがえます。
また、動画はいつでも繰り返し視聴できるため、社員は自分のペースで学習や復習ができ、現場でのスキルを効率的に習得できます。
さらに、動画マニュアルはヒヤリハット事例を用いた教育にも有効です。例として、発生したヒヤリハットを動画で再現し、マニュアルに落とし込むことで誤った作業方法と正しい手順を解説することや、ヒヤリハットの内容や原因、対策を1つの動画マニュアルに盛り込み、全部署に展開することが考えられます。
このように動画マニュアルを活用することで、ヒヤリハットを紙ベースの報告書よりもわかりやすく、かつ簡単に全従業員に伝えることができ、従業員の危険感受性を高め、現場の危険を可視化することが実現します。
実際に現場で活用されている動画マニュアルのサンプルや対策例についてより詳しく知りたい方は、以下のリンクからハンドブックを入手してご覧ください。次章では、多くの製造現場で活用されている動画マニュアルのツールについてご紹介します。
>>安全意識が高い現場はもう活用している!実際の動画マニュアルサンプルを見る
「tebiki現場教育」ならかんたんに作成、教育改善も!
動画マニュアルのメリットはわかっても、「編集スキルがないから、動画マニュアルの導入に踏み切れない」とお思いの方もいらっしゃるでしょう。
しかし、tebikiという動画マニュアル作成ツールを使用すれば、誰もが簡単に動画マニュアルの作成から教育管理が可能になります。実際に、紙の標準書だと作成に0.5~1ヶ月程度要していたところ、tebikiではわずか1日~2日程度で作成できたという例もあるほどです。
▼動画マニュアル作成ツール「tebiki」紹介動画▼
tebikiは、スマートフォンで撮影した動画に字幕やナレーションを簡単に追加できるため、スマートフォンで撮影するだけで現場の担当者が特別な機材や編集スキルなしにそのまま教育用マニュアルを作成でき、ヒヤリハット対策に活用できます。
例えば、「直近で発生したヒヤリハット事例とその原因」や「考えられる対策」などを動画にして共有すれば、作業者全員が視覚的に学ぶことができます。加えて、外国語への自動翻訳やマニュアルの読み上げにも対応しているため、外国人労働者がいるチームでも導入しやすいのが特徴です。
さらに、効率的な教育を実現するため、以下の機能も搭載されています。
- 動画の字幕などの自動翻訳
- オフライン再生
- 文書作成機能
- 動画の音声を認識して字幕の自動生成
- 自主学習を促すタスク機能
- レポート機能
- テスト機能
- スキルマップ機能
tebikiにはヒヤリハット教育や重大な事故の防止に役立つ機能がまだまだ搭載されています。詳しくは以下のサービスご紹介資料を是非ご覧ください。
tebiki現場教育をヒヤリハット対策に活用している事例
動画マニュアルtebikiを導入し、従業員教育やヒヤリハット対策に成功した事例を3つご紹介します。実際にどのような効果を得ているのか見ていきましょう。より多くの企業事例と効果を知りたい方は、以下の導入事例集もご覧ください。
>>動画マニュアルを活用した安全教育・ヒヤリハット対策事例をもっとみる
株式会社メトロール
工作機械や産業用ロボット向けのセンサを製造販売している株式会社メトロールは、未経験で入社する方が多く、文書や口頭で教育をしても具体的なイメージが伝わらない/トレーナーにより教育内容がバラついているといった教育課題を抱えていました。
そこで、作業動作などを伝えるうえで動画が有効だと考えtebikiを導入し、「アルコールが誤って目に入るヒヤリハットを防ぐために、正しく蓋を閉めましょう」といった新人向けの安全衛生に関するマニュアルを優先的に作成することに。新人向けの操作マニュアルなども作成した結果、教育時間を半分以下にまで抑えながらわかりやすい教育の実現に成功したそうです。
株式会社メトロールの導入経緯や効果をもっと詳しく読みたい方は、以下のインタビュー記事をご覧ください
インタビュー記事:世界で200社以上の装置メーカーに採用されているセンサの製造工程でtebikiを活用し、新人教育と多能工化を推進
御幸毛織株式会社
御幸毛織株式会社は、1921年設立の繊維メーカーです。長年にわたる経験と技術の蓄積を基に、高級スーツ生地を中心とした製品を提供しており、業界内での信頼と評判を確立しています。
同社では、製造工程における専門的な知識や技能の継承が難しく、新入社員や若手社員が熟練の技術を効率的に習得することが困難という課題を抱えていました。また従業員教育を一部の社員に依存しており、教育の質がばらつくことで、作業ミスや漏れなどのヒヤリハットが発生することも課題視していました。
そこで御幸毛織株式会社は、課題解決のために動画マニュアル「tebiki」を導入しました。
tebikiを活用することで、ベテラン社員の熟練した技術や知識を動画で記録し、新入社員や若手社員に効果的に伝えることが可能に。
特に、現場の事故によるトラブルや被害を視覚的に理解できる、“べからず動画”を作成し、潜在的に潜む危険性を動画で再現し訴えることでヒヤリハットの削減や現場の安全教育を促進されています。
結果として、属人的な教育方法から脱却し、標準化された教育内容を全従業員に提供できるようになりました。
御幸毛織株式会社の導入事例をより詳細に知りたい方は、こちらの記事をご覧ください。
インタビュー記事:明治時代創業の繊維会社が挑む技術伝承!ITテクノロジーを駆使して伝統芸を若手へ伝達
大同工業株式会社
大同工業株式会社は、オートバイや自動車、産業機械、福祉機器など幅広い事業を展開するグローバル企業です。
現場では新人教育をOJTで行っていたものの、技術や手順が我流化していました。結果として、教え方のバラつきによるヒヤリハットが発生しており、早急な対策が求められる状況でした。特に、試験手順の小さな違いが原因で、ヒヤリハットや評価結果のエラーが発生する問題を課題視していたとのこと。
そこで、動画マニュアルtebikiを導入し、部署内全員で試験手順を再標準化することで、ヒヤリハットや評価エラーの削減を実現しました。tebikiは視覚的に手順を確認できるため、言葉だけでは伝わりにくい「コツ」や「ポイント」も効果的に伝えることが可能です。
結果として、業務の標準化が進み、教育工数も大幅に削減されました。
大同工業株式会社の安田氏は、tebikiの導入によって、部署内での試験中のヒヤリハットや評価エラーが削減できたと実感しているとのことです。また、tebikiの動画マニュアルは、海外の拠点での現地スタッフの教育にも活用することが考えられ、グローバルな展開にも対応できると紹介されています。
大同工業株式会社の導入事例をより詳細に知りたい方は、こちらの記事をご覧ください。
インタビュー記事:製造業の技術部門の業務を動画で標準化。教育工数を8割削減し、業務の効率化・最適化も実現。
【おまけ】ヒヤリハットに関する基礎知識
ヒヤリハットに関する基礎知識を再確認し、事故の未然防止に活用したい方に向け、以下のお役立ち情報をまとめました。
- そもそもヒヤリハットとは
- ヒヤリハット対策の重要性
- ヒヤリハットとハインリッヒの法則の関係
上記の内容は下記の関連記事内でも詳しく解説しているため、本記事と併せてご覧ください。
▼関連記事▼
・ヒヤリハットとは?報告書の例文や業界別の事例、対処法について紹介
・ヒヤリハットのネタ切れ対策方法とは?具体的な事例やネタを紹介
そもそもヒヤリハットとは
ヒヤリハットとは、日常業務の中で発生する「事故には至らなかったが、事故が起きそうになった」事象のことを指します。これらの事象は、事故や大きなトラブルにつながる可能性があるため、重要な危険信号と捉えられています。
ヒヤリハット対策の重要性
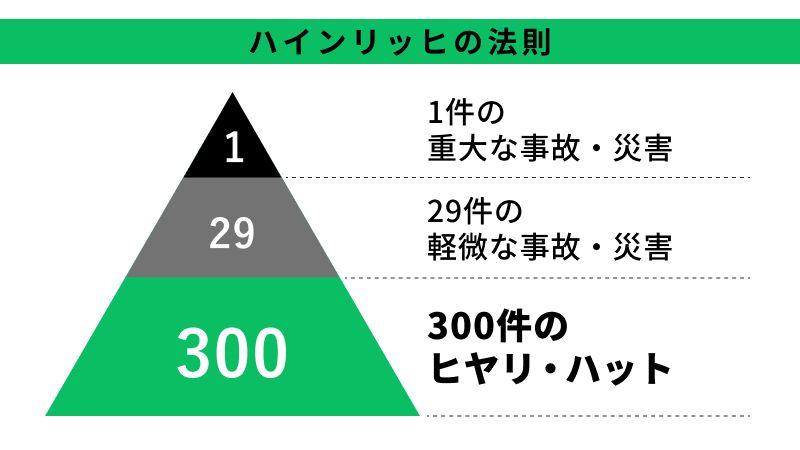
ヒヤリハットは、表面的には小さな出来事に見えるかもしれませんが、その背景には従業員の不注意や作業手順の不備など、根本的な問題が潜んでいることが多いです。
そのため、これらの問題を早期に発見し適切な対策を講じることで、将来的な重大事故の発生を未然に防クことが可能です。
ヒヤリハットとハインリッヒの法則の関係
ハインリッヒの法則は、労働災害や事故発生のメカニズムに関する考え方です。この法則によると「1つの重大事故の背後には29の軽微な事故があり、さらにその背後には300のヒヤリハットが存在する」とされています。
これは、ヒヤリハットを軽視せず、早期対応が重大な事故の発生を防ぐために大切であることを示しています。ヒヤリハットは、日常で起こっているこの300件の事故寸前の気付きを共有・対策することで、事故が起きることを未然防止できます。
そのため、ヒヤリハットの原因深堀や対策は、現場の全従業員を安全に守るために必要不可欠な取り組みです。
関連記事:ハインリッヒの法則とは?事故予防の取り組み例をかんたんに解説!
まとめ
この記事では、工場で発生しやすいヒヤリハットの事例や具体的な対策について解説しました。工場では転倒・転落・激突など、さまざまなヒヤリハットが発生しています。
また、ヒヤリハットの原因も作業手順の不徹底や教育不足など、多岐にわたります。そのため、この記事を参考にしながら自社のヒヤリハットを分析し、どのような事故防止対策を実施すべきかを検討してみましょう。
効果的な事故防止対策を行いたい方は、動画マニュアル「tebiki」を活用するのがおすすめです。作業手順や注意点を視覚的に示すことで、文章や口頭での説明よりも理解が深まり、ミスによる事故を効果的に防止できます。
さらに、作業の流れやタイミングを正確に伝えられるため、誤操作や不注意によるヒヤリハットを低減することが可能です。動画マニュアル「tebiki」の資料は、以下の画像から無料でダウンロード可能ですので、ぜひ詳細をチェックしてみてください。