かんたんデジタル現場帳票「tebiki現場分析」を展開する、現場改善ラボ編集部です。
設備総合効率(OEE)は設備の使用効率を示す数値で、時間稼働率、性能稼働率、良品率の三要素から構成されます。
本記事では、設備総合効率とは何か?計算方法や設備総合効率を低下させる「7大ロス」の原因について解説します。また、7大ロスに対抗して設備総合効率を上げるカギもご紹介するので、ぜひご活用ください。
目次
設備総合効率(OEE)とは?重要性やTEEPとの違い
設備総合効率(OEE)とは、設備の使用効率を評価する指標のことです。英語では「Overall Equipment Effectiveness」と表記し、OEEという略称でも呼ばれています。
設備総合効率に着目することで生産ラインの問題点が明確になり、改善策を講じることが可能です。まずは、設備総合効率に注目する重要性やTEEPとの違いなど、基礎知識を解説します。
設備総合効率は「設備の使用効率」を示す数値
日本産業規格によると、設備総合効率(OEE)は「設備の使用効率の度合いを表す指標」と定義されています。
また、OEEは製造業の生産効率とパフォーマンス評価を標準化する国際規格「ISO22400」の指標の1つとして用いられ、設備の稼働時間に対する付加価値の度合いを表します。
OEEは時間稼働率、性能稼働率、良品率で構成され、設備の運転時間中の生産性と品質の両面を考慮し、「どれだけ効率的に設備が利用されているかを示す数値」です。
関連記事:稼働率とは?低下する工場が陥りがちな3つの損失と改善事例
OEEの各要素を分析することで、どの部分に改善の余地があるかを具体的に把握可能です。
たとえば自動車部品の製造ラインにおけるOEEを考えた場合、時間稼働率は設備が計画通りに稼働しているかを表しており、性能稼働率は実際の生産速度が理想の速度に対して「どれだけ達成されているか」を表します。同様に、良品率は生産された製品が「どれだけ規格を満たしているか」を示します。
データをもとに、ダウンタイムの削減や速度の最適化、不良品の減少など具体的な改善策を導き出すことが可能です。このように、製造業の生産性に直結する指標になることから、製造現場のKPI指標として使用されることも少なくありません。
設備総合効率の基礎知識は、専門家による解説動画でもより詳しくご紹介しています。無料でご覧いただけますので、以下の画像をクリックしてご覧ください。
設備総合効率(OEE)を活用する3つの重要性
設備総合効率(OEE)を活用することで設備の稼働状態や生産プロセスの効率を評価し、改善点を明確にすることが可能です。OEEの活用には以下3つのメリットがあります。
- コスト削減
- 生産効率の向上
- 品質の向上
コスト削減
OEEを活用することで、設備の稼働効率を向上させると同時にコスト削減が期待できます。具体的には「保全コスト」「製造コスト」の削減が可能です。
OEEに着目することで設備の故障予測や適切なメンテナンス時期の把握が可能になり、保全コストが削減できます。
たとえば、時間稼働率の変動に着目することで計画外のダウンタイムを発見できます。また、性能稼働率や良品率の低下変化から、特定の調整不良や部品の摩耗異常をを検知し、早期に対処することができます。結果として突発的な故障を防ぎ、計画的な設備保全を実施することで保全コストを削減できます。計画外のダウンタイムが減少し、長期的な運用コストを抑えられるためです。
他にもOEEを向上させることで、製造コストの削減も期待できます。
たとえば、良品率が向上することで品質の高い製品を手戻りなく生産できるようになり、無駄なリソースの浪費を防げます。結果的に、不良品や再作業による材料費や労務費が削減できます。
さらに、OEEデータを活用してボトルネックや非効率な工程を特定し、生産速度を上げることで生産ライン全体の効率を向上させ、単位あたりの生産コストを削減できるでしょう。品質の高い製品を一度で生産でき、無駄なリソースの浪費防止や製造原価の削減といった効果が期待できます。
▼関連記事
・設備保全の目的とは?課題やあるべき姿、IoT化について解説
・製造原価とは?計算方法、削減方法について解説!
生産効率の向上
OEEは時間稼働率、性能稼働率、良品率の3つの要素により、設備の稼働効率や生産速度、製品の品質を評価して最適な改善策を導き出します。OEEを活用することで、設備のポテンシャルを最大限に引き出し、効率的な生産が実現します。
たとえば、時間稼働率が低い場合、計画外のダウンタイムが原因であることが多い傾向もあるでしょう。対処するためには、予防保全の強化が有効です。
また、性能稼働率が低い場合、生産速度の低下や小さな停止が影響している可能性があります。設備のメンテナンスやオペレーターのトレーニングが必要ということが明らかになるでしょう。さらに良品率が低い場合、品質管理の改善が必要です。
関連記事:製造業の生産性を向上させる4ステップとは?生産性の指標や計算式の求め方も紹介!
品質の向上
OEEの良品率が高まることで、不良品が少なくなり、安定した品質の製品を生産できるようになります。
具体的にはOEEを活用して生産プロセスを最適化し、標準化することで一貫した高品質の製品を提供することが期待できます。
たとえば、良品率に着目し生産ラインのどの工程で不良品が発生しているかを把握すれば、その部分のプロセスを見直せます。そこで品質の問題を早期に発見し、迅速に対処することが可能です。
またOEEを用いて製造工程全体を監視することで、品質管理の強化を図ることが可能になります。結果として製品の信頼性が向上し、顧客満足度の向上にもつながります。
関連記事:製造業における品質改善/向上8つの手法は?品質バラつき防止の取組事例を解説
設備機器総合有効生産力(TEEP)との違い
設備総合効率(OEE)と似ている言葉に、設備機器総合有効生産力(TEEP)があります。
設備機器総合有効生産力(TEEP)とは、設備の24時間365日の総合的な使用効率を示す指標です。英語では「Total Effective Equipment Performance」と表記し、TEEPとも呼ばれています。OEEが実際の稼働予定時間中の効率を評価するのに対し、TEEPは1年間を基準にして効率を評価する違いがあります。
TEEPの評価は24時間体制での生産を目指す場合に重要です。
たとえば自動車部品メーカーがTEEPを活用することで、稼働シフトを最適化し、生産ラインの全体的な効率を向上させることが可能です。夜間や週末の稼働時間も含めて評価することで、さらに生産性を向上させるための具体的な施策を講じられます。
設備総合効率(OEE)の構成要素と計算式
設備総合効率は、時間稼働率/性能稼働率/良品率の3要素から構成されている指標です。それぞれの計算式をまとめると、以下の画像の通りです。
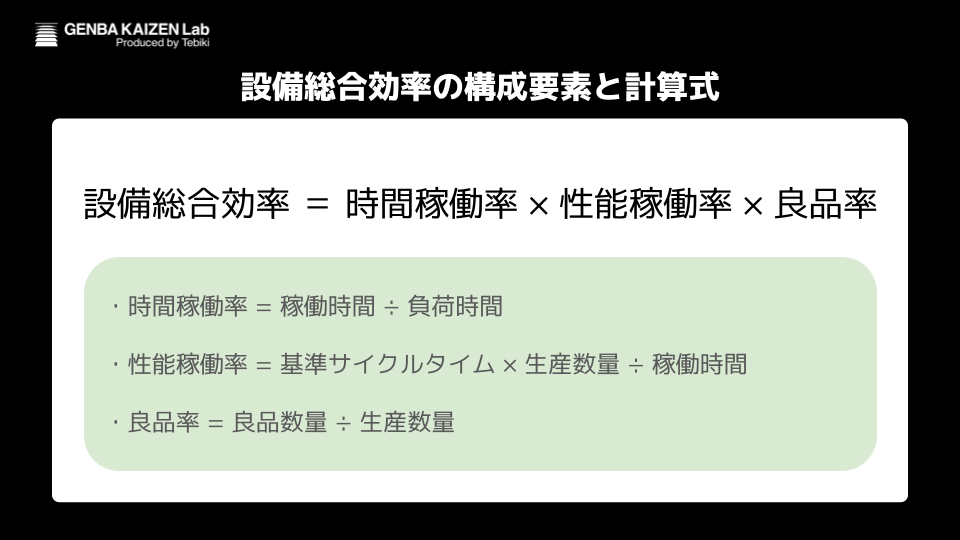
ここからは、それぞれの計算例も交えて詳しく解説していきます。
設備総合効率の計算式と目安
設備総合効率(OEE)は、時間稼働率×性能稼働率×良品率で算出できます。
たとえば時間稼働率が80%、性能稼働率が90%、良品率が95%の場合、OEEは80%×90%×95%=68.4%となります。OEEの目安として、数値が低い場合には問題がありますが、「高い数値だから良い状態だ」と一概には言えない場合があります。
例として、過剰生産により性能稼働率が高まり、OEEは見かけ上高い数値となっていても、実際はムダな在庫が管理コストを圧迫しているといった場合や、高いOEEを維持するために過度な人力やリソースを投入している場合、コスト効率が悪化し悪影響となっている場合が考えられます。
そのため、OEEの数値のみを判断基準とせず、OEEの数値を実際の現場の状況と照らし合わせながら良し悪しを判断することが重要です。『OEEが悪い…』というときには、7大ロスに着目して改善を行いましょう。
7大ロスに関する解説は、後述の「設備総合効率を低下させる「7大ロス」の原因と対策」をご覧ください。
時間稼働率の計算式
時間稼働率とは、設備が稼働できる時間の中で実際に稼働していた時間の割合を示す指標のことです。
時間稼働率は、設備が計画通りに稼働しているかを評価するために用いられます。計算式は「時間稼働率 = 稼働時間 ÷ 負荷時間」で表すことができます。
負荷時間は設備が稼働できる時間の和を指し、稼働時間は負荷時間のうち実際に稼働していた時間を指します。たとえば1日の負荷時間が8時間(480分)で稼働時間が6時間(360分)だった場合、式は以下の通りです。
時間稼働率 = 360分 ÷ 480分 = 75% |
時間稼働率が低い場合は計画外のダウンタイムやメンテナンス時間が長いことが原因と考えられ、改善には予防保全や迅速なトラブルシューティングが有効です。
性能稼働率の計算式
性能稼働率とは、設備が稼働している間にどれだけの生産量を達成したかを示す指標のことです。計算式は「性能稼働率 = 基準サイクルタイム × 生産数量 ÷ 稼働時間」で表すことが可能です。
基準サイクルタイムとは、1つの製品を生産するのに理想的にかかる時間を指します。たとえば基準サイクルタイムが1分で、生産数量が300個、稼働時間が360分だった場合、式は以下の通りです。
性能稼働率 = 1分 × 300個 ÷ 360分 = 83.3% |
性能稼働率が低い場合、機械の速度低下や微細な停止などが原因で生産速度が遅れていることが考えられます。改善策としては、設備のメンテナンスやオペレーターのスキル向上が挙げられます。
良品率の計算式
良品率とは、全生産数量に対して規格を満たした良品の割合を示す指標のことです。計算式は「良品率 = 良品数 量 ÷ 生産数量」で表すことが可能です。たとえば生産数量が1,000個でそのうち良品が950個だった場合、式は以下の通りです。
良品率 = 950個 ÷ 1,000個 = 95% |
良品率が低い場合、設備の不具合や摩耗、操作ミスやヒューマンエラーが原因で不良品が増えていることが考えられます。対策として、適切な設備保全や作業マニュアルの見直しなどが挙げられます。
【補足】 設備機器総合有効生産力(TEEP)の計算式
補足情報として、前章でご紹介した「設備機器総合有効生産力(TEEP)」の計算式もご紹介します。
TEEPは、設備総合効率にローディング(稼働時間/総時間)を掛け合わせた数値で表現されます。計算式は「TEEP = ローディング × OEE」で表すことができます。
ローディングとは、設備が実際に稼働している時間を総時間で割った値です。たとえば週に5日、1日8時間稼働する設備の場合、負荷時間は=5日×8時間=40時間となり、総時間は=7日×24時間=168時間となります。ローディングは40時間÷168時間=約23.8%(40時間/168時間)です。
さらにTEEPを計算しましょう。OEEが61.9%の場合、TEEPは次のように計算できます。
TEEP = 23.8% × 61.9% = 14.7% |
計算結果からわかるように、OEEだけでは見えなかった潜在的な効率の向上余地が明確になります。
ここまで、設備総合効率を中心に関連指標の計算方法と例をご紹介しました。設備総合効率の目安は現場によって適切な値が異なるものの、生産性を測る指標として注目すべきです。
もしも『自社の設備総合効率が低い』と感じる場合は、その原因となりうる7大ロスに着目して原因と対策を検討しましょう。次章からは、7大ロスについて詳しく解説していきます。
設備総合効率(OEE)を低下させる「7大ロス」の原因と対策
設備総合効率を計算してみることで、『自社のOEEが低いかも?』というボトルネックが可視化できるようになります。OEEが低い場合、その原因として以下の7大ロスが考えられます。
7大ロスに適切に対処し、設備総合効率を上げていきたい方は、後述の【7大ロスに対抗し、設備総合効率を上げるには「製造現場の可視化」】をクリックしてご覧ください。
故障
故障は、設備の機械的なトラブルや部品の破損によって発生するロスです。
故障が発生する主な原因は、定期的なメンテナンス不足や老朽化した設備の使用です。たとえば、製造ラインで重要な機械が故障すると、ライン全体が停止して生産が中断されます。
結果として、計画外のダウンタイムが発生し生産スケジュールに遅れが生じるだけでなく、納期遅延による顧客満足度の低下や緊急修理のためのコスト増加が発生します。
故障を防ぐには、予防保全の強化や設備の定期的な更新が必要です。
関連記事:設備保全の目的とは?課題やあるべき姿、IoT化について解説
段取り・調整
段取り・調整は、新しい製品や異なる製品ラインへの切り替え時に発生するロスです。
段取り・調整には、機械の設定変更や試運転が含まれます。たとえば、成形工場では製品の形状やサイズが変わるたびに金型の交換や調整が必要です。
段取り・調整が頻繁に発生すると都度生産が中断され、性能稼働率や生産性が低下するでしょう。
工具交換
工具交換は、製品の製造過程で使用する工具が摩耗、破損した際に必要となる交換作業を指します。
工具交換が発生する原因は、工具の寿命や製品の加工条件に影響されます。たとえば、金属加工工場では切削工具を頻繁に交換しなければならない状況である場合、そのたびに生産が一時停止します。
結果、生産スケジュールに遅れが生じ、 性能稼働率が低下するでしょう。
工具交換のロスを減らすためには、高品質な工具の使用や工具寿命を延ばすための加工条件の改善、定期的な工具のメンテナンスが重要です。
立ち上がり
立ち上がりロスは、設備を始動してから安定稼働に至るまでの間に発生するロスです。
立ち上がりロスは、設備の初期設定や試運転、不良品の発生が主な原因です。たとえば、工場では設備を立ち上げた直後に製品の品質が安定しないことがあります。
立ち上がりの期間に発生する不良品は再加工が必要となり、時間稼働率が低下します。
速度低下
速度低下は、設備が設計された速度よりも遅く稼働することで発生するロスです。
速度低下の原因には、機械の老朽化や不適切なメンテナンスがあります。たとえば、工場では設備の速度が低下すると生産量が減少し、納期遅延のリスクが増加します。
速度低下のロスを防ぐためには、定期的なメンテナンスや設備の更新が必要です。
チョコ停・空運転
チョコ停は、短時間の頻繁な停止を指し、空運転は設備が稼働しているが生産していない状態を指します。
チョコ停・空運転が発生すると、そのたびに生産が中断され、時間稼働率や性能稼働率が低下します。チョコ停・空運転を減少させるためには、操作手順の見直しや自動化の導入、従業員への再教育が有効です。
関連記事:チョコ停が減らない原因と改善策【定義や計算式、ドカ停との違い】
不良・手直し
不良・手直しは、製品が品質基準を満たさないために再加工や修理が必要となるロスです。
不良・手直しの原因には、製造工程の管理不足や設備の不調があります。たとえば部品の製造において不良品が発生すると、再加工のための時間とコストがかかり、生産効率が低下します。
不良・手直しを防ぐためには、工程の管理強化や設備の定期点検、業務標準化が必要です。
関連記事:【改善事例あり】製造業における品質不良の原因と8つの対策
このように、設備総合効率に影響を及ぼす7大ロスはその原因が多岐に渡ります。そのため、悪いと気づいたときにボトルネックを見つけようとすると、分析に工数を要し対策実行までに時間のロスが発生する可能性があるでしょう。
設備総合効率を上げていくためには、ボトルネックを即座に特定し対策を素早く行える状態が望ましいです。この状態を実現するためには「製造現場の可視化」が必要です。
次章からは、かんたんに製造現場の可視化が実行できる具体的な手段をご紹介します。
7大ロスに対抗し、設備総合効率を上げるには「製造現場の可視化」を
7大ロスには稼働ロスや速度ロス、不良ロスなど、設備や作業プロセスに起因する問題が含まれます。これらのロスを解消して、設備総合効率を上げるためには「製造現場の可視化」がカギを握っています。
製造現場では、課題が複雑に絡み合っており、単一の要因ではなく複数の要因が設備の非効率を生んでいます。これらを把握し、優先順位をつけて改善を行うには、以下のような可視化が必要でしょう。
- 稼働状況のリアルタイム監視
- 作業工程のデータ分析
- 不良品の発生要因の追跡
設備の稼働状況を明確にすることで、稼働率の低下要因を把握できます。また、作業速度やミスの発生頻度など、作業工程における生産性を可視化することで、作業効率の状況を把握できます。また、不良品がどの工程で発生したのかをデータとして記録することで、製品品質の向上に役立ちます。
このような記録/データをかんたんに可視化するには、製造日報や点検表のような現場帳票のデジタル化が有効です。現場帳票をデジタル化する手段には、分析機能も備わっている「かんたんデジタル現場帳票:tebiki現場分析」が適切です。
最後に、tebiki現場分析の機能概要と実際の活用事例と効果をご紹介します。
製造現場の可視化ができる「tebiki現場分析」とは?
かんたんデジタル現場帳票「tebiki現場分析」は、現場帳票をクラウド上でかんたんに作成・記録・承認・管理ができるだけでなく、ダッシュボード機能によって現場のボトルネックや異常をリアルタイムで可視化できるツールです。
シンプルな操作画面で、直感的に現場帳票のひな形を作成することができるほか、入力時の正常値設定やExcelのような表形式による記録も行えます。記録データは自動グラフ作成機能によって、複雑な関数やマクロを組まなくても、かんたんに現場の可視化/データ分析が行えます。
tebiki現場分析を活用している株式会社日本電気化学工業所では、現場帳票のデジタル化とダッシュボード機能によって、設備の不具合傾向を早期に捉えて設備停止やチョコ停、不良発生などのロスの未然防止を実現しています。
▼株式会社日本電気化学工業所:インタビュー動画▼
tebiki現場分析を用いた製造現場の可視化によって、7大ロスの未然防止を通じた設備総合効率の向上につなげることができます。具体的な機能やプランは、以下のリンクをクリックしてサービス概要資料をご覧ください。
>>かんたんデジタル現場帳票「tebiki現場分析サービス資料」を見てみる
tebiki現場分析を利用して設備総合効率の向上を実現しよう【まとめ】
設備総合効率(OEE)とは、製造業における設備の使用効率を示す重要な指標です。
OEEは時間稼働率、性能稼働率、良品率の3つの要素から構成されます。
さらにOEEと関連する指標として設備機器総合有効生産力(TEEP)があります。TEEPは、OEEをもとに全時間に対する設備の使用効率を示すものです。
OEEの向上は、コスト削減、生産効率の向上、品質の向上という3つのメリットをもたらします。OEEの向上には7大ロスを早期に捉えて対策を講じることが有効で、「製造現場の可視化」がカギを握ります。可視化をかんたんに実現する方法としては、製造日報のような現場帳票のデジタル化が効果的です。
現場帳票のデジタル化を実現できるtebiki現場分析の導入により、現場データのデジタル化と効率的な管理が実現し、異常値アラートや簡単な分析機能を通じて設備総合効率の向上が期待できます。
本記事でご紹介したtebiki現場分析の機能詳細や導入効果、導入までの流れについては以下の資料からご確認ください。