かんたん動画マニュアル作成ツール「tebiki現場教育」を展開する、現場改善ラボ編集部です。
ポカヨケ(Poka-Yoke)とは、製造現場の人による作業ミスを防止する仕組みや装置のことです。たとえば、裁断機の刃物部分に人の手が接触する危険がある場合、自動で機械が止まる仕組みがポカヨケです。
この記事ではポカヨケの意味や語源といった基礎知識から、製造現場で有効なポカヨケ対策例や実際の事例、私たちが考える最も重要な取り組みを詳しく解説します。
目次
ポカヨケとは?【意味・語源・英語表記】
ポカヨケとは、製造ラインで作業者のミス(ポカ)を避ける(ヨケる)仕組みを指す言葉です。英語では「Poka-Yoke」と表記され、語源は諸説ありますがフールプルーフ(fool proof)にあるとされています。
そのため、ポカヨケとフールプルーフの意味合いに違いはなく、同じと捉えて問題ありません。直訳するとフール(愚か者)プルーフ(耐えられる)で「どんなバカでも作業ミスをしない」というニュアンスから、当初はバカヨケと呼ばれていました。
しかし、ポカミスはどんな人であってもゼロにはできないので、人ではなくポカミスに目を向けたポカヨケという表現に改められたとされています。
次章以降ではポカミスをゼロにする難しさと、製造業がポカヨケに取り組む目的について解説していきます。
製造現場のポカミスはゼロにできる?
製造業では人が行う作業が多く、ポカミスようなヒューマンエラーが起きやすいです。そのため、品質不良の発生や従業員の労働災害といったリスクがつきまとうため、限りなくポカミスをゼロにすることが理想です。
しかし、どのようなポカヨケを講じてもヒューマンエラーのようなポカミスをゼロにすることは難しいでしょう。
その理由について、トヨタ自動車でトップ技能者と認定され、トヨタ社内研修の講師として実績がある伊藤 正光氏によるセミナー内容を一部ご紹介します。
トヨタ流のヒューマンエラーに対する考え方は以下の2つです。
- ヒューマンエラーをゼロにすることは困難。極力少なくするしかない。
- ヒューマンエラーを抑えるためには、標準作業を確立し、守る以外に道なし。
今の世の中では数多くの電車が動いていますが、ミスはほとんど出ていません。それは運転手の手順が標準として確立されひたすら遵守しているからです。
このように、製造現場のミスをあらゆる手段で排除しようとしているトヨタ自動車でも、ヒューマンエラーのようなポカミスをゼロにすることは難しいと考えています。ポカヨケ対策の方向性として、ヒューマンエラーを極力減らす対策や仕組みの例を解説した記事もヒントになるのでオススメです。
ポカヨケに関する具体的な内容を知りたい方は、後述の「製造現場で実践できるポカヨケ対策」か、専門家による解説動画を以下のリンクをクリックしてご覧ください。
>>専門家による「ヒューマンエラーの未然予防:ポカヨケ対策」の解説動画を見てみる(視聴無料)
製造業がポカヨケに取り組む目的やメリット
従業員の安全を担保するため
ポカヨケに取り組むことで、従業員の不安全行動による労働災害を回避できるメリットがあります。
例えば、プレス機械のような重機の操作ミスによる事故は、挟まれのような重大な事故をもたらす恐れがあります。しかし、ポカヨケが導入されていれば、操作ミスが起きたとしても設備の設計によって事故が回避され、安全に停止できる状態になるでしょう。
しかし、機械設備側にポカヨケのような安全対策を施したとしても完全に防げるわけではないので、従業員の安全教育にも取り組んで安全意識を高めることも大切です。製造業の場合、従業員の安全教育を行う手段の1つとして、動画マニュアルを活用する事例が増えています。
>>「 動画マニュアルを活用した製造業の安全教育・対策事例」を見てみる
品質不良の改善
ポカヨケは、ヒューマンエラーによるシステムの誤操や作業ミスを事前に避ける効果が期待できるため、品質不良の改善につながるメリットがあります。
私たち現場改善ラボが会員の方向けに実施したアンケート調査(回答数419件)では、製造現場で発生したヒューマンエラーの原因として多いものとして、手順不遵守(40.4%)や不注意(30.6%)が挙げられる結果でした。
【「手順不遵守に起因する品質不良対策の考え方と対策」より抜粋】
製造現場でポカヨケを講じることで、ヒューマンエラーによる品質トラブル発生を抑止することができるでしょう。安全面と同様に、機械設備への対策だけでなく、従業員の品質教育といった取り組みもセットで行うことが望ましいです。
>>「手順不遵守に起因する品質不良対策の考え方と対策」を見てみる
製造現場でポカヨケ対策を行うタイミング
製造現場のミスを防ぐため、ポカヨケ対策を講じるタイミングは「生産開始前」と「不具合/トラブル発生時」が適しています。その理由について、それぞれご紹介しましょう。
生産開始前
生産開始前にポカヨケを講じることで、量産開始後の製品設計や生産ラインの大幅な変更を避けてポカミスを抑制できます。
設計段階で部品やネジの形状を工夫したり、治具やインターロックを組み込むことで、作業者の取り付けミスや誤操作を防ぎます。生産開始前に、現場で起こりうるヒューマンエラーを洗い出して対策を講じておくことで、量産フェーズの品質安定や安全トラブルの予防に大きく寄与します。
不具合やトラブル発生時
生産中に不具合やトラブルが起きた場合、まずは異常発生に気づく仕組みが大切です。代表的な例としては、後述しているトヨタ自動車の「アンドン」が挙げられます。ポカミスに早期に気づくようにすることで、後工程への影響を最小限に留めることが可能です。
また、発生したトラブルがなぜ起きたのか、真因を明確にして再発防止策を講じることがポカヨケ対策として効果的です。
対策によっては作業手順の見直しが発生するため、ここでは従業員に対して内容を周知することが欠かせません。
このような作業ルールを周知・徹底するための手段として、作業手順書の作成や更新が行われることが一般的です。再発防止策が守られるようになる効果的な方法は、以下の画像をクリックして参考資料をご覧ください。
実際の企業で行われているポカヨケ実践事例
トヨタ自動車株式会社
トヨタ自動車では、トヨタ生産方式の柱の1つ「自働化」の一環でポカヨケに取り組んでいることを公式YouTubeで紹介しています。
トヨタ生産方式を実現するために、業務のあらゆるムダ(7つのムダ)を排除し標準を徹底しているトヨタ自動車において、ポカヨケを防ぐための教育体制が整備されているのは言うまでもありません。
本動画は、標準化を徹底する中でもゼロにしきれなかった、ネジの締め付け不良という異常をランプ(アンドン)によって知らせるエラープルーフ化の一例といえるでしょう。締め付け不良があればランプで従業員に知らせ、再度締め付け作業を行います。
仮にランプに気付かなくても、生産ラインが止まり不良品は後工程に流れないため、問題を最小限に留めるエラープルーフ化も併せて運用されているといえます。
児玉化学工業株式会社
住宅設備や自動車向けの樹脂製品を製造/販売する児玉化学工業株式会社では、動画マニュアルで手順不遵守が起こりやすい作業を視覚的に伝えることで、ポカミスのような作業ミスを9割減らし、人材育成という切り口でポカヨケ対策を行っています。
▼インタビュー動画:児玉化学工業株式会社▼
多国籍の従業員を抱え、紙の作業手順書/マニュアルでは作業の手順やコツを伝えきれずポカミスが発生していた中で、動画マニュアルを活用したことで動きを視覚的にわかりやすく伝えることができました。
従業員が理解しやすくなかったことで作業手順の標準化が進み、結果的に手順不遵守による品質不良を9割削減しています。児玉化学工業の動画マニュアルを活用した取り組みは、こちらのインタビュー記事で詳しくご覧いただけます。
同社のようにポカミスを防ぐため、業務標準化を推進する手段として動画マニュアルを活用する製造現場が増えています。「動画マニュアルを活用した製造現場の改善事例集」では、同社のような事例を多数ご紹介していますので、以下のリンクをクリックして資料をご覧ください。
>>「動画マニュアルを活用した製造現場の改善事例集」を見てみる
製造現場で実践できるポカヨケ対策【”標準作業の確立と遵守”が最も大切】
ここからは製造現場で実践できるポカヨケ対策の例を4つご紹介します。
この中でも、私たちは「標準作業の確立と遵守」が最も大切だと考えます。本章ではその理由についても詳しくご紹介します。他にもポカミスの例を知りたいという方は、以下の画像をクリックして専門家によるポカミス対策の解説動画をご覧ください。
FMEAやリスクアセスメントによるトラブルの予測
生産開始前にFMEAやリスクアセスメントを行うことで、ポカミスが起こりうるリスクを工程ごとに洗い出し、ポカヨケ対策を施すことができます。
FMEAとは、製品や生産ラインの設計段階で、起こりうるリスクと影響を定量評価する手法です。FMEAでは、故障モードや影響度を定量評価し、部品取り付けミスや工具選択間違いなど、モノに対して物理的に対策を組み込みます。
一方のリスクアセスメントとは、作業環境や人的要因を含めた包括的なリスク評価を行う手法です。労働環境や作業環境など、潜在的に潜むヒトにまつわるリスクを総合的に評価することで、労働災害など重大事故に至るリスクが高い工程にポカヨケ対策を施すことができます。
製品や生産ラインの設計初期段階で行うことで、ポカミスの未然防止に繋がり、安全かつ安定した生産を実現できます。
>>元労基署長による「現場のキケンを見極めるリスクアセスメント術」の解説動画も見てみる
フールプルーフ・フェイルセーフに基づいた工程設計を行う
フールプルーフとは、人が操作/手順ミスをしたとしても物理的・構造的にトラブルが起きない設計にする考え方です。たとえば、部品の形状を複雑にして特定方向以外からは差し込めなくする、操作手順を単純化して判断の余地を最小化するなど、そもそもヒューマンエラーが発生しないよう仕組みを組み込むのが特徴です。
一方のフェイルセーフは、万が一にエラーやミスが起きても被害を最小限に抑え、安全に設備が制御される設計思想です。具体例として、異常を検出したら設備が自動停止するインターロックや、電源断でも安全姿勢を保つアクチュエータなどが挙げられます。
この2つの設計思考を組み合わせることで、想定されるポカミスの発生自体を封じ込めつつ、仮に想定外のヒューマンエラーが起きたとしても、フェイルセーフの仕組みによって重大トラブルを防ぐポカヨケ対策となります。
デジタル技術やIoTを取り入れる
デジタル技術やIoTを活用するポカヨケ対策の例として、RFIDを用いた自動認識によって部品の取り違えをリアルタイムで検知し、作業を停止させるような仕組みが挙げられます。また、トルクや締付回数などの作業をセンサーで計測し、異常値が出た時にラインを一時停止するような制御と連動させる方法も効果的です。
このようなデジタル・IoTのアプローチを取り入れることで、ポカミスの発生を物理的に防ぐだけでなく、誤操作や不具合を即座に検知、対処できる体制を整備しやすいポカヨケ対策となります。
標準作業の確立と従業員が遵守する仕組み作り
前述の3つは物理的に講じる対策例ですが、大前提として「標準作業(作業ルール)を遵守する」ことが必要です。標準作業は、安全で一定の品質が担保された手順であるため、遵守することでポカミスを回避することができます。
一方で、ここまでご紹介してきたように、ポカミスのようなヒューマンエラーはゼロにすることが難しいため、万が一発生したときの対策として物理的な対策を施します。他にご紹介した物理的対策は万が一の備えであり、標準作業を従業員が遵守するための教育が前提として行うべきポカヨケ対策です。
製造業の場合、標準作業を伝える手段は作業手順書が一般的ですが、「動き」が伴う製造現場の業務内容は文字や写真では表現が難しく、従業員に標準作業が正しく伝わらないことでポカミスにつながるケースが少なくありません。
そこで次章で詳しくご紹介している「動画マニュアル」を活用する製造現場が増えつつあります。
ポカヨケにつながる「標準作業の確立と遵守」には動画マニュアルが有効
製造業のポカヨケに「動画マニュアル」が有効な理由
製造業におけるノウハウは「ヒト/モノ/機械の三次元的な動き」です。そのため、二次元的な情報である文字ベースのマニュアル/作業手順書では、動作の流れをつかみにくく理解を妨げる原因となります。そこで業務手順を撮影した動画マニュアルを活用することで、視覚的に業務手順を理解することが可能です。
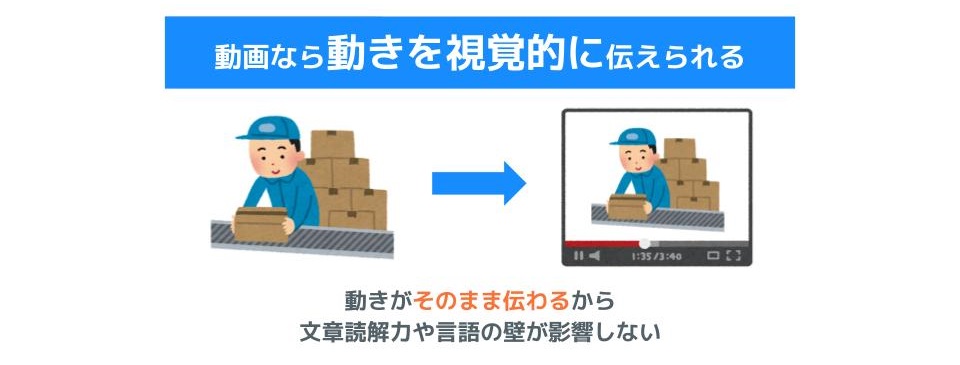
一度、現場の実態に則した正しい内容で動画マニュアルを作成することで、管理者や教育担当者が標準作業を伝えるための教育工数削減につながり、管理者の業務効率化も期待できます。
また撮影した動画を観察することで、手順書の文章/写真では発見できないミスが置きやすい作業の発見ができるため、動画マニュアル活用が潜在的なポカミス発見にもつながります。
このような製造現場における動画マニュアル活用例と有効性は、別紙のガイドブックで詳しく解説しています。以下のリンクをクリックして、参考資料も併せてご確認ください。
多くの製造業で活用されている動画マニュアルのツール
かんたん動画マニュアル作成ツール「tebiki現場教育」は、多くの製造現場で活用されている現場教育の課題を解決するクラウドサービスです。
スマートフォンやタブレットなどで撮影した動画を、映像編集未経験者でもかんたんに編集でき、現場教育の効率化や標準作業の浸透を目的に活用されています。標準作業の遵守を実現する機能として、主に以下の機能を搭載しています。
- 100カ国語以上への自動翻訳によって外国人も学習可能
- 従業員がアクセスしたマニュアルがわかるレポート機能
- 従業員の理解度をチェックできるテスト機能
- 部署や工程単位で設計できる教育訓練計画の整備
- 従業員のスキルを評価/可視化するスキルマップ機能 など
またtebiki現場教育は、全プランで動画マニュアルの保存本数が無制限で、ポカミスを予防するために必要な動画マニュアルを上限なく必要に応じて整備いただけます。
まず『tebiki現場教育を活用した、製造現場の改善事例を詳しく知りたい!』という方は、製造業における動画マニュアル活用事例集をクリックしてご覧ください。『tebiki現場教育の詳細な機能やプランなど、サービスの概要を詳しく知りたい!』という方は、以下のリンクをクリックして概要資料をご覧ください。
>>多くの製造現場で活用されている「tebiki現場教育」の詳細を見てみる
製造業のポカヨケ対策には「動画マニュアル」も効果的【まとめ】
製造業のポカヨケ対策には、標準作業の確立と従業員が遵守する仕組み作りが重要です。しかし、標準作業を伝える手段である作業手順書は、文字や写真による表現が中心で、現場の動きやコツを伝えきれず、結果として手順不遵守やポカミスが発生するケースが少なくありません。
そこで「動画マニュアル」を活用することで、動作や手順を視覚的にわかりやすく伝えられるため、作業者の理解度が向上し、ポカミスの予防に効果的です。また、動画なら現場の実態に即した内容で標準作業を共有でき、管理者や教育担当者の工数削減にもつながります。さらに、作業者自身が動画を見て手順を確認できるため、教育の均一化やミスの自己改善が期待できます。
動画マニュアルを活用することで、製造現場のポカミスを未然に防ぎ、品質と安全性を高めることが可能です。tebiki現場教育は多くの製造現場で活用されている動画マニュアルツールなので、まずはサービスの概要などをぜひご覧ください。