品質管理で特に効果的な手法として注目されているのが「源流管理」です。源流管理とは、ある工程で不具合が発生した場合、不具合の現象だけでなく、上流(源流)工程にさかのぼって原因を突き止める管理手法のことです。
本記事では、源流管理がなぜ必要なのかやメリットと実践方法、具体的な事例を紹介します。さらに工程別の具体的な手法や源流管理を効率化するツールについても詳しく解説します。
「源流管理についてあまり知らない…」という方も「源流管理を取り入れている!」という方も参考にできることが多い記事ですので、ぜひご覧ください。
源流管理と同じく、品質管理を行う上で抑えておきたい考え方として、生産現場で起こり得る突発的な変化を予防する「変化点管理」があります。変化点管理の具体的な手法やトヨタグループにおける品質の作り込みについて解説した動画もご用意しておりますので、併せてご覧ください。
目次
源流管理とは?
源流管理とは、製品の設計~製造の過程でより上流の工程で品質を作り込みつつ、不具合発生時には源流(上流)にさかのぼり原因追及と改善に取り組む管理手法のことです。
源流管理は、単なる対症療法的な品質改善のみならず、根本的な原因を突き止め再発を防ぐことを目的としています。
他の呼び方として「川上管理」や「フロントローディング」とも呼ばれることがあります。ここでは源流管理について、以下の2点を解説します。
- 上流工程から品質を作りこもうとする考え方
- 源流管理の具体的な例
上流工程から品質を作りこもうとする考え方
源流管理の考え方として重要なのが、上流工程における品質の作りこみです。
下流(後工程)にあたる出荷前検査で不具合を発見した場合、上流(前工程)にあたる製造工程に原因がないか追及します。製造工程における不具合の原因が、「複雑な組み立て手順で作業ミスを誘発しやすい」という内容であれば、より上流にあたる開発段階で設計を見直すといったアプローチになるでしょう。
このように、源流管理は上流にさかのぼって不具合発生を未然防止しつつ、後工程で不具合を発生させないという考え方をします。
ここでは具体的な考え方として、以下の2点を解説します。
- 品質問題の特定と再発防止
- 設計・製造段階における品質の作り込み
品質問題の特定と再発防止
源流管理は、上流側の工程にさかのぼって品質改善に取り組む考え方です。そのため、品質問題を後工程に流さないように事前に特定し、将来的な再発を防止するアプローチが必要です。
後工程で不具合を発生させないために、より上流工程側で品質チェックを行う体制を整え、問題発生を未然に防ぐことは非常に重要だといえます。問題を設計段階で解決することで、手戻りや製造コスト増大を防ぐのは勿論、市場に不良品が流出することによる大きな経営問題の発生予防につながります。
具体的な取り組み内容として、設計段階でのデザインレビューやFMEA(故障モード影響分析)を徹底し、潜在的な不具合を早期に発見して修正できます。結果として、後工程での問題発生を未然に防ぎ、製品の信頼性を高めることが可能です。また設計と製造の各工程での問題点を洗い出し、再発防止策を講じることで、品質の向上も図れます。
関連記事:FMEA(故障モード影響解析)とは?品質向上の取組みをわかりやすく解説【フォーマット例付き】
設計・製造段階における品質の作り込み
設計・製造段階での品質を作り込む段階でのミスや見落としは、後工程での大きな問題に発展する恐れがあります。
例として、エアバッグに設計上の欠陥がある場合を考えてみましょう。エアバッグが正常に作動しないことで、本来であれば防げたはずの事故を未然防止できなかったことに加え、大規模な修理や不良品回収など重大な損失を招くことは想像に難くないといえます。
このような事態を避けるためにも、源流管理による上流工程での徹底的な品質管理を行うことで、製品の品質を設計段階から確保し後工程での不具合を未然に防ぐことが求められます。また、源流管理の実施は後工程での手戻りやムダを削減し、効率的な製造プロセスを実現することにも役立ちます。
関連記事:品質を作りこむ方法とは?仕組化に欠かせない視点や成功事例を紹介
源流管理に基づいた取り組みを行う具体的な例
源流管理の考え方に基づいて、具体的な取り組みを行っている企業事例として、以下の2社を紹介します。
- 本田技研工業株式会社
- トヨタ自動車株式会社
本田技研工業株式会社
本田技研工業株式会社の市場品質監理課では、顧客の声を反映した源流管理の実施により不具合の早期解決と再発防止を実現しています。
具体的な進め方として、顧客が販売店に持ち込んだ車の不具合を修理し、交換した部品と不具合の詳細を記載したレポートをもとに調査解析を行います。解析が必要な場合は、専用部門に回して対応を進めて最終的にリコールを判断し、不良の再発防止に努めています。
また、テレマティクス技術(自動車に搭載した機器を通じたリアルタイムな情報サービスの提供)を活用してリアルタイムで不具合情報を収集・解析し、迅速な対応を実現しています。このように、本田技研工業株式会社は高品質な製品を提供しつづけるための源流管理を徹底しています。
参照元:お客様の満足度向上に向けて──不具合ゼロを目指し解析に取り組む挑戦の日々
トヨタ自動車株式会社
トヨタ自動車株式会社における源流管理の取り組みは「サイマルテニアス・エンジニアリング」という品質マネジメント体制にもとづいています。
サイマルテニアス・エンジニアリングの体制では、設計・開発から生産準備に至るまでの各ステージでの活動を一体化し、設計品質と製造品質を同時に確立することを目指しています。従来型のプロセス体系では設計と製造が明確に分かれていたため、設計段階での問題が製造段階に持ち越され、後工程での手戻りやコスト増大が避けられない問題がありました。
しかし、トヨタ自動車では、設計・開発部門と生産準備部門が協力し、設計段階から製造に関する視点を取り入れることで、問題を早期に発見し解決することが可能になりました。
たとえば、設計段階でのデザインレビューや故障モード影響分析(FMEA)を実施し、生産技術部門や製造部門がその結果をもとに製造のしやすさやコスト効率を考慮した改善提案を行います。例のように、トヨタ自動車株式会社では源流管理により設計段階での問題を未然に防ぎ、製造段階での品質向上とコスト削減を実現しています。
参照元:トヨタ式 最強のモノづくり「サイマルテニアス・エンジニアリング」
源流管理はなぜ必要?3つのメリット
源流管理を導入し、上流工程での問題を早期に発見して根本原因に対処することで、トラブルの再発を防ぐことができます。
ここでは、源流管理の具体的なメリットとして以下の3点を解説します。
- トラブルを発生させない環境や仕組みを整備できる
- ムダなコストやロスを削減できる
- 品質が改善され顧客満足度が向上する
トラブルを発生させない環境や仕組みを整備できる
源流管理を実施することで、トラブルや不具合を未然防止する体制を整備できます。
発生した不具合に対する対策のみでは根本的な原因を排除できず、同じ問題が再発する可能性が高いケースが多いといえます。
源流管理の考え方に基づいた品質管理を行うことで、トラブルの根本原因に対処して問題の再発を防ぐ環境や仕組みを整備できます。源流管理では上流工程における品質管理を徹底し、設計段階から潜在的な不具合を洗い出して対策を講じます。結果として、後工程での手戻りや不具合の発生を未然に防ぐことが可能です。
また、源流管理を行うためには、製造工程の状況が把握できるデータが必要です。
製造工程におけるデータとは、主に良品率や不良品率、稼働率といった定量的に可視化できるものを指します。
定量的に可視化を行うことで、異常値を計測できるといったように不具合発生を未然に防ぐことも副次的なメリットだといえるでしょう。
関連記事:【DX促進】製造業におけるデータ活用の進め方とは?メリットや成功事例について解説!
ムダなコストやロスを削減できる
品質不具合が再発し続けた場合、それまで投入したリソースやコストがムダになり、改修が大規模かつ時間がかかるものになるリスクがあります。
たとえば完成間近の製品で不具合が発生した場合、製造に投入された材料や部品、労働時間などが全てムダになってしまいます。結果として製品全体のコストが増加し、納期遅延のリスクも高まります。
源流管理のように、上流工程での問題発見と対策を徹底することで、ムダなコストやロスを大幅に削減可能です。例として、上流工程でのデザインレビューなどを通じて潜在的な問題を早期に発見するということが挙げられます。
製造工程に入る前に課題を解決することで後工程での手戻りや修正作業が減少し、全体の製造コストを削減できるでしょう。
品質が改善され顧客満足度が向上する
応急処置的な対応だけでは不具合の根本原因を解決できず、同じ問題が再発する可能性があります。結果として、顧客の期待する品質を満たせず信頼を損ね、ブランドイメージや競争力が低下するリスクがあるといえます。
しかし、源流管理による対策であれば上流工程から問題を徹底的に解決するため不良品が下流工程に流れることがなくなり、品質の底上げにつながります。設計段階から製造段階まで一貫した品質管理を行うことで製品の信頼性が向上し、顧客満足度の向上につながるでしょう。
【工程別に見る】源流管理を実践するための具体的な手法
源流管理を効果的に実践するには、各工程に適した具体的な手法を取り入れることが重要です。ここでは、以下の工程における有効な手法について詳しく説明します。
- 設計・開発
- 生産準備
- 生産の各段階
設計・開発
設計・開発段階では、製品の品質を初期から確保することが不可欠です。設計・開発段階で最も重要なのは、デザインレビューと設計FMEAです。
デザインレビュー
デザインレビューとは、製品の設計が仕様通りに行われているかを確認し、潜在的な問題を早期に発見する手法のことです。
デザインレビューを実施することで設計段階で発見された問題を後工程に進む前に解決できるため、全体の手戻りを防ぎ、品質を確保できます。そのため設計ミスや不具合の原因を発見でき、設計段階で問題を取り除くことが可能です。
デザインレビューでは、設計図面や仕様書のチェック、設計の妥当性評価、技術的な課題の洗い出しが行われます。
具体的な進め方としては、まず初期設計段階でのレビューを実施します。次に、基本設計が完了した時点で再度レビューを実施します。詳細設計が完了する前に最終レビューを行い、設計に問題がないことを確認します。結果、設計段階での品質保証が確保され、後工程での手戻りを大幅に削減することが可能です。
デザインレビューに開発チーム全員が参加し、多角的な視点から問題点を指摘し合うことで、設計の精度を高められます。またデザインレビューの結果を文書化することで、後続の開発ステージでの参考資料として活用することが期待できます。
設計FMEA
設計FMEA(Failure Mode and Effects Analysis)とは、設計段階で潜在的な故障モード(不具合の原因)を特定し、影響を評価する手法のことです。設計FMEAにより、設計上のリスクを事前に把握して適切な対策を講じることが可能です。
設計FMEAの実施手順としては、まず製品の各構成要素について「どのような故障モードが考えられるか」をリストアップします。次に、それぞれの故障モードが製品全体に与える影響を評価し、リスクの大きさを判定します。評価結果にもとづいて、リスクの高い箇所は設計の見直しや強化策を講じます。
たとえば、自動車部品の設計において、エンジンの冷却システムにおけるポンプの故障が考えられる場合はポンプの設計を見直して故障しにくい構造に改良します。また、故障が発生した際の影響を最小限に抑えるための冗長設計を導入することも有効です。
設計FMEAの結果は設計文書に反映され、開発での品質管理に役立てられます。
生産準備
生産準備段階では、実際の製造に向けた準備が行われます。ここでの主な手法として、工程FMEA、プリプロダクション、作業手順書の整備が挙げられます。
工程FMEA
工程FMEAとは、製造工程で発生しうる故障モード(不具合の原因)を分析してその影響を評価する手法のことです。工程FMEAにより製造段階でのリスクを事前に把握し、対策を講じることが可能です。
工程FMEAの実施手順としては、まず製造工程を詳細に分析してそれぞれで発生しうる故障モードをリストアップしたのち、製品に与える影響を評価してリスクの大きさを判定します。評価結果にもとづいて、リスクの高い工程は製造プロセスの見直しや改善策を講じます。
たとえば、電子機器の製造工程においてはんだ付け工程での不具合が考えられる場合は、はんだ付け温度の管理や作業手順の見直しを行います。また故障が発生した際の影響を最小限に抑えるための検査工程を追加することも有効です。
工程FMEAの結果は製造手順書に反映され、次の生産ステージでの品質管理に役立てられます。
プリプロダクション(量産試作検証)
プリプロダクションは、量産に向けた試作検証を行う段階です。プリプロダクションにより、実際の製造工程での問題を事前に発見し、対策を講じられます。
プリプロダクションの実施手順としては、まず試作品を製造し、品質と製造工程の検証を実施。試作品の品質が規定の基準を満たしているかを確認し、不具合が発生した場合は原因を特定して製造プロセスを見直します。また試作品を通じて製造工程のボトルネックや効率化の余地を見つけ出し、改善策を講じます。
たとえば自動車部品の量産試作を考えてみましょう。試作段階で製造工程の不具合を発見した場合、原因を特定して製造設備や作業手順を見直します。
試作品の検証結果は製造手順書に反映され、量産段階での品質保証に役立てられます。
作業手順書の整備
標準化された手順書を整備することで製造作業のばらつきを防いで安定した品質を確保できるため、作業手順書の整備は製造工程での一貫した品質管理を実現するために重要です。
作業手順書の整備手順としては、まず製造工程を詳細に記述し、必要な手順やポイントを明確にします。次に作業手順書を実際の製造現場で試行し、フィードバックを受けながら改善。最終的には全ての製造作業者に手順書を共有し、統一された作業手順の実行を徹底します。
たとえば、精密機器の製造において組み立て工程の作業手順書を整備する際は組み立て手順や注意点を詳細に記述して作業者全員に周知徹底します。また定期的に手順書の見直しを行い、製造工程の改善点を反映することで、常に最適な手順書を維持します。
作業手順書の作成は、先述した通りトラブルを防ぐうえで重要な要素だといえますが、一方で「作業手順書はあるのに業務品質が安定しない…」「効果のある作業手順書の作り方がわからない…」とお悩みではないでしょうか?
そこで、数多くの現場を支援してきた私たちならではのノウハウが詰まった資料を以下にご用意しております。是非ご覧ください。
生産
生産段階では、実際の製造工程での品質管理が重要です。ここでの主な手法としては、インライン検査、SPC(統計的工程管理)、作業者訓練が挙げられます。
インライン検査
インライン検査とは、生産ライン内で製品をリアルタイムに検査する手法のことです。インライン検査により、製品の品質を継続的に監視して不良品の発生を早期に検出できます。
インライン検査の具体的な手法としては、自動化された検査装置や目視検査を用いることで、製品の外観や寸法、性能をリアルタイムで評価することが挙げられます。作業者の手間を減らし、高速かつ高精度な検査が可能となります。たとえば、電子部品の製造ではインライン検査装置を使用して基板上の部品配置や、はんだ付けの状態を常に監視します。異常が発生した場合はただちに生産ラインを停止し、原因を特定して対策を講じます。
インライン検査のメリットとしては、不良品の流出を未然に防ぎ、製品の品質を高水準に維持できることが挙げられます。またリアルタイムのフィードバックにより製造工程全体の改善点を迅速に特定し、プロセスの最適化を図ることが可能です。
▼関連記事▼
・目視検査の課題はどう解決する?原因や4つの対策を紹介
・AI外観検査とは?メリットや導入の流れ、事例を解説!
SPC(統計的工程管理)
SPC(Statistical Process Control)とは、製造工程の品質を統計的に管理する手法のことです。SPCにより、製造プロセスの変動を監視し、異常を早期に発見することが可能です。
SPCの具体的な実施方法として、製造工程で収集されたデータを統計的に分析し、管理図を作成することが挙げられます。作成した管理図を用いて、製造プロセスの変動が規定の範囲内に収まっているかを監視します。例を挙げると、機械加工において寸法測定データを管理図にプロットし加工が安定しているかを確認。異常な変動が検出された場合は、即座に原因を調査して機械を修正します。
SPCの導入により、製造プロセスの安定性と品質の一貫性が向上します。結果として不良品の発生を減少させ、製品の信頼性を高めることが可能です。
作業者訓練
作業者訓練は、標準化された作業手順や作業手順書に沿った手順を正しく実践できるよう教育するための重要な工程です。
新しい技術や手法、製品仕様の変更があった際には、作業者に対して適切なトレーニングを行い、最新の知識を習得させます。たとえば、新しい機械設備を導入した場合、操作方法やメンテナンス方法について詳細な訓練を実施することなどが考えられます。
製造業における作業者訓練の手法として、OJTや座学研修といったものが一般的でしょう。しかし製造業で教えるノウハウは、ヒト/モノ/機械といった動きにまつわるものです。このような動きは、口頭ベースによる教育や文字や写真といった二次元的な情報で理解を深めるのには限界があります。
そこで、製造業の作業者訓練において「動画マニュアル」が活用されるケースが増えています。
動画マニュアルは視覚的にわかりやすく、手順を正確に伝えることが可能です。作業者は実際の作業を見ながら学習できるため、複雑な作業でも理解度が高まります。また繰り返し視聴することで、手順の確認や復習が容易になります。
動画マニュアルのメリットやおすすめの動画マニュアルについては、後述する「源流管理を効率化するツール」か、以下の資料をご覧ください。
源流管理で取り組むべきポイント
効果的な源流管理を実現するために、以下に紹介する2つのポイントをおさえることで、品質管理のレベルを向上させトラブルの発生を最小限に抑えられます。
- 部門間の連携を強化する
- 「自工程完結」を徹底する
部門間の連携を強化する
源流管理を効果的に実施するには、全ての部門が参加して取り組むことが不可欠です。
製造プロセスの各工程は密接に関連しているため、特定の部門だけで問題解決を図ることは難しく、全ての部門が協力し合い、全体最適の意識を持つことで、品質管理の抜け漏れを防ぐことが可能です。
部門間の連携を強化することで、より綿密な源流管理を行えるようになるでしょう。
例として、設計部門が新しい設計を導入する際には、製造部門や品質管理部門と連携し、設計が生産現場で実現可能かどうかを確認することが必要です。結果として、設計段階でのミスや後工程での手戻りを防げます。
部門間の連携を強化するには、組織全体で目標を共有し、全体の最適化を図る意識を持つことが重要です。
利害関係が生じる場合もありますが、それぞれの部門が自分たちの利益のみを追いかけるのではなく、組織全体の利益を考えることで効率的な問題解決が可能となります。さらに、管理コストを惜しまない姿勢も必要です。初期投資はかかりますが、長期的には品質の向上と信頼性の確保につながります。
部門間の連携を密にする過程では、作業者の意識改革も欠かせません。
源流管理の重要性やメリットを周知し、「やらされている感」をなくすことで、全員が積極的に取り組む体制を整えます。結果、全社的な品質管理のレベルが向上し、不具合の発生を未然に防ぐことが可能です。
「自工程完結」を徹底する
源流管理を効果的に行うには、「自工程完結」への意識が求められます。自工程完結とは、各工程で品質を確保して次の工程に不良品を流さないというトヨタ流の考え方です。
自工程完結を実現するには、各工程でのチェックポイントを明確にし、標準化された手順に従って作業を行うことが重要です。たとえば製造ラインでの各作業工程ごとに、品質チェックを実施し、不良品が次の工程に流れないようにする仕組みを構築します。また各工程の作業者には、品質管理の重要性を理解させ、自分たちの手で品質を確保する意識を持たせることが必要です。
さらに定期的なフィードバックを通じて、各工程の品質状況を監視し、改善点を見つけ出すことが重要です。たとえば月次の品質会議を開催し、各工程の品質データを共有し、問題点を洗い出して改善策を講じることで品質の向上を図ります。
自工程完結の詳しい説明やトヨタ社における品質経営への取り組みについて、自工程完結の発案者である佐々木 眞一氏の講演レポート記事もございますので、併せてご覧ください。
関連記事:自工程完結を発案したトヨタ元副社長が語る『品質経営の歴史と課題』
品質教育を実施する
源流管理を継続的かつ効果的に行うには、従業員に向けた品質教育の実施も欠かせません。
品質教育は、全ての従業員が品質管理の重要性を理解して適切な知識とスキルを持つことを目的としています。
源流管理を効果的に実施するには、基本的な品質管理の概念や手法といった根本的な内容を教え、教育を通して品質に対する意識を養うことが重要です。たとえばQCサークル活動を通じて、現場の作業者が自ら問題を発見し、解決策を考える機会を与えます。さらに定期的な研修や勉強会を開催し、最新の品質管理手法や技術を学ぶ機会を設けます。たとえばFMEA(Failure Mode and Effects Analysis)や統計的工程管理(SPC)などの専門的な手法を習得することで、製造現場での品質管理の精度を高められるでしょう。
品質教育については別記事「品質教育では何を教える?教育の進め方や成功事例も解説」で詳しく解説しています。また、QCサークル活動の具体的な進め方やその効果については、トヨタ自動車出身の講師による詳しい解説動画がございますので、どちらも是非ご覧ください。
【現場で実践できる】源流管理に必要な体制つくりとは?
源流管理を効果的に実践するには、現場での具体的な体制づくりが不可欠です。具体的な取り組みとして以下の2つが挙げられます。
- 作業手順を標準化し、業務品質のムラをなくす
- 不具合をリアルタイムで可視化できるようにする
作業手順を標準化し、業務品質のムラをなくす
各従業員が好き勝手な手順で業務を進めている状態では、個々の作業者によって手順や方法が異なることで製品の品質にばらつきが生じるため、業務品質は安定しません。
業務品質にムラがある状態では、いくら源流管理を行い上流工程でトラブルを減らすよう整備しても、下流工程におけるミスは減らないといえるでしょう。
このようなばらつきを防ぐには、作業手順を統一し、標準化することが重要です。標準化された手順に従うことで、誰が作業を行っても同じ品質の製品を作ることが可能になります。
作業手順を標準化するには、まず現在の作業プロセスを詳細に分析し、最適な手順を明確にしましょう。その後、標準化された手順書を作成し、全ての従業員に共有します。手順書には、具体的な手順だけでなく、注意すべきポイントや品質チェックの基準も含めると良いでしょう。
さらに、標準化された手順が現場で確実に守られるように定期的なトレーニングや教育を実施することも重要です。作業者が手順を理解し正確に実行できるようになることで、業務品質のムラをなくし、安定した品質の製品を生産できます。また作業手順の改善点を現場からフィードバックしてもらい、必要に応じて手順を見直すことも大切です。
標準化された作業手順を徹底することで、製品の品質が向上し不良品の発生を抑えられます。結果として、製造コストの削減や納期の短縮にもつながり、顧客満足度の向上が期待できます。
標準化の具体的な進め方や成功事例については、以下の記事内でも詳しく解説しております。是非ご覧ください。
関連記事:業務標準化を進める6つのステップとは?成功事例や役立つツールも紹介
不具合をリアルタイムで可視化できるようにする
不具合をリアルタイムで可視化することは、トラブルの早期発見と被害の最小限化につながります。
問題が発生した時点で迅速に対応できれば、取り返しのつかない問題に発展する前に解決できるためです。特に製造業では、不具合の発生から発見までに時間がかかると、その間に製造された製品全てに不良が含まれる可能性があり、結果として大きな損失を招きかねません。
また、トラブルの発生状況やトラブルの詳細をリアルタイムで把握することで原因を究明しやすくなるため、源流管理には現場の状況を即座に反映したデータが必要です。
リアルタイムで不具合を可視化するには、デジタルツールの活用が有効です。デジタルツールを使えば、過去のデータも蓄積され、トラブルのパターンや原因を分析することが可能です。
中でもおすすめなデジタルツールとして、デジタル帳票が挙げられます。
紙の帳票では、不具合をリアルタイムで把握することが難しいという問題があります。他にも紙ベースの記録は手間がかかり、情報の共有や分析に時間がかかるため、迅速な対応が難しくなります。デジタル化されたシステムならデータが自動的に記録されすぐにアクセスできるため、問題の早期発見と対策がスムーズに行えます。
源流管理を効率化するツール
源流管理を効率的に実践するには、適切なツールを活用することが重要です。
ここでは源流管理を効率化するツールとして動画マニュアルとデジタル帳票を、それぞれおすすめなツールについて「tebiki」と「tebiki現場分析」を紹介します。
動画マニュアル
動画マニュアルは、従来の紙のマニュアルに比べて、作業手順や業務の標準化に大きな利点があります。動画という視覚情報と音声情報を通じて具体的な作業手順を示すことで、内容が理解しやすく、記憶に残りやすいところがメリットといえるでしょう。紙のマニュアルは情報量が多くてわかりにくい場合がありますが、動画マニュアルなら実際の作業をリアルタイムで行うのと同様に示せるため、直感的に理解できます。
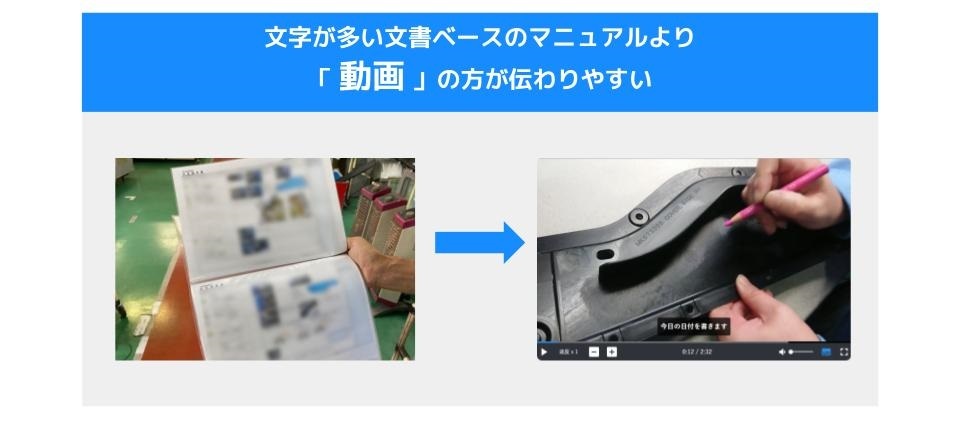
他にも、OJTや口頭による教育では教え方の差や内容の微妙な差異により、全員に均一な内容を教えることが難しいという課題がありましたが、動画マニュアルでは一度作った正しい「見本」を使って教えるため、大人数に同一の内容を効率的に伝達できるほか、スキマ時間で繰り返し視聴が可能なため先輩社員がいない場でも学習が可能です。
さらに動画マニュアルは、作業手順の変更や新しい手順の導入時にも有効です。紙のマニュアルでは、変更があるたびに再印刷が必要ですが、動画マニュアルなら簡単に更新できます。
動画マニュアルは、特に新人教育や新しい設備の導入時に効果を発揮します。新しい作業手順を習得する際、紙のマニュアルだけでは理解が難しい場合でも、動画であれば実際の動きを見ながら学べるため、早期に作業に慣れることが可能です。
製造業における動画マニュアルの活用事例や、動画マニュアルによるメリットを知りたい方に向け、詳細な資料をご用意しております。是非ご覧ください。
おすすめは「tebiki」
数ある動画マニュアルの中でも特におすすめしたいのが「tebiki」です。tebikiは、動画マニュアルを活用して作業手順を標準化し、業務品質を安定させるには非常に効果的なツールだといえます。
tebikiの主な機能として、動画の簡単作成と編集があります。現場の作業をスマートフォンで撮影するだけで簡単にマニュアルが作成できるほか、マルやバツ、矢印といった簡単な記号を画面に表示する編集も簡単に行えるため、専門的な知識や技術がなくても高いクオリティのマニュアルが完成します。
またtebikiでは、作業手順の動画をクラウド上で管理し、いつでもどこでもアクセスできるようにすることで、情報共有の効率が向上します。結果として、新人教育や技術伝承がスムーズに行われるようになります。さらに動画マニュアルは視覚的な学習をサポートし、従業員の理解度を高めるため、業務のミスを減少させる効果もあります。
実際にtebikiを活用している新日本工機株式会社の事例では、tebikiを導入することで、作業手順の標準化が進みました。
▼インタビュー動画:新日本工機株式会社▼
同社では、複雑な作業手順を動画マニュアルでわかりやすく説明し、新人教育の時間を大幅に短縮。結果として、作業品質が安定し、製品の品質向上につながりました。新日本工機株式会社のようにtebikiを活用することで、現場の生産性と品質を同時に向上させることが可能です。
新日本工機株式会社の詳しい事例については、以下のインタビュー記事をご覧ください。
インタビュー記事:人が育つ環境づくりとして動画マニュアルtebikiを活用。技術の蓄積と作業品質の安定を実現。
本記事でご紹介したtebikiの機能詳細や導入効果については、以下の資料でも詳しく解説しております。
業務標準化や品質向上に向けた具体的な手段をお探しの方は、是非ご参考ください。
デジタル帳票
デジタル帳票は紙の帳票と比べて、情報の入力・検索・分析が容易であり、迅速な対応が可能なことから源流管理に大きな強みを発揮します。紙の帳票では、記録の管理や情報の共有に手間がかかり、必要な情報をすぐに取り出すことが難しい場合がありますが、デジタル帳票を活用することで紙の帳票の課題を解決できます。
デジタル帳票は製造現場での記録を効率化し、リアルタイムでのデータ共有を可能にします。またデジタル帳票はデータの正確性を高める効果もあります。紙の帳票では、手書きによる記入ミスや情報の欠落が発生しやすいという課題がありますが、デジタル化することでフォーマットの統一や書き漏れへのアラートを行うことができ、ヒューマンエラーによるミスのリスクを軽減できます。
このように、デジタル帳票には数多くのメリットがありますが、「いきなり使い慣れた紙の帳票から移行するのは大変だし不安…。」という方も多いはず。
そこで、これからデジタル帳票の導入をお考えの方に向けた資料を以下にご用意いたしました。導入の流れや失敗パターンなど、事前に知っておきたい情報が記載されているため是非ご参考ください。
おすすめはtebiki現場分析
デジタル帳票を現場に導入する際に、是非おすすめしたいのが「tebiki現場分析」です。
tebiki現場分析は不具合をリアルタイムで把握し、迅速に対応するための機能を備えたツールであり、特に製造現場でのトラブル管理と品質向上に大きな効果を発揮します。
「tebiki現場分析」の主な機能として、リアルタイムでのデータ収集と分析があります。現場で発生する不具合や異常を即座に記録し、クラウド上でデータを共有することで問題の早期発見と対策が可能です。加えて正常値を登録することで異常値を検出し、異常発生時に即座にアラートメールを発信する機能も搭載されています。
リアルタイムでのデータ収集は、紙の帳票では実現が難しいでしょう。紙の帳票は手書きで記録されるため、記入ミスや情報の遅延が発生しやすく、情報の共有や検索も困難です。
しかし「tebiki現場分析」を利用すれば、データは自動的に収集されてクラウド上で一元管理されるため、必要な情報を迅速に検索できます。
他にも、tebiki現場分析の特徴として「データ分析機能」が挙げられます。デジタル帳票を通し蓄積されたデータを簡単にグラフ化できるこの機能により、分析用Excelへの転記や複雑な関数入力、資料作成といった手間を省き、必要な内容を即座に見える化することが可能です。
結果として、従業員は最新のデータに基づいて行動ができるため、不具合の発生に即座に対応することや、データを活かしたトラブルの未然防止が実現します。
本記事でご紹介したtebiki現場分析の機能詳細や導入サポート体制については、以下の資料でも詳しく解説しております。
データ活用やDXに向けた具体的な手段をお探しの方は、是非ご参考ください。
tebikiのツールを源流管理に役立てよう【まとめ】
源流管理とは、工程の上流から品質を作り込むことで、製品の不具合を未然に防ぐ管理手法です。
本田技研工業やトヨタ自動車の例からも分かるように、品質問題を特定し再発防止策を講じることが重要です。
具体的には、設計・製造段階でのデザインレビューやFMEA、工程準備でのプリプロダクション検証、作業手順書の整備が必要です。また部門間の連携や自工程完結、品質教育の徹底が求められます。
源流管理の取り組みを支えるツールとして、動画マニュアルやデジタル帳票、「tebiki」などが有効であり、現場の作業品質の向上とトラブルのリアルタイム把握を実現します。
この記事で紹介した動画マニュアルのtebikiとtebiki現場分析の資料は無料でダウンロード可能です。ぜひこの機会にtebikiの資料をダウンロードしてみませんか?