かんたん動画マニュアル作成ツール「tebiki」を展開する現場改善ラボ編集部です。
製造現場では、生産性向上やコスト削減を実現するために「段取り改善」が欠かせません。しかし、「段取りが大切なのはわかっているけど、具体的にどう改善すればいいかわからない」「今の取り組み方で本当に効率化できているのか不安」という悩みを抱える方も多いのではないでしょうか。
本記事では、段取りとは何かを改めて整理し、段取り改善によって得られる効果や、製造現場で段取りがうまく進まない理由をわかりやすく解説します。段取り改善によって現場全体のパフォーマンスを底上げしたい方は、ぜひご覧ください。
目次
段取りとは?
製造現場における「段取り」とは、作業を行うための順序や手順を決め、必要な設備・材料・道具を事前に整えることです。たとえば、製品を組み立てる前に部品を揃え、工具を配置し、機械の設定を済ませる一連の準備が「段取り」にあたります。
段取りが不十分だと、「作業開始後に部品が見つからない」「工具が使えない」などのトラブルが発生し、作業が中断してしまいます。全体の生産効率低下にもつながる可能性があるため、単なる準備作業にとどまらず、生産性を左右する大切な工程です。
この重要性を端的に表した言葉に、「段取り八分、仕事二分」があります。これは「作業の成否は、段取りの段階で8割方決まっている」という意味です。つまり、段取りをしっかり行えば、実際の作業はスムーズに進み、生産効率も格段に向上するのです。
製造現場での成果を高めるためには、まず段取りの重要性を再認識し、確実な準備を徹底することから始めましょう。
段取り改善が製造現場にもたらす効果
段取りを改善することで、製造現場にはさまざまなポジティブな効果がもたらされます。ここでは代表的な4つの効果を紹介します。
作業のムダ削減による生産効率の向上
段取りを最適化すると、作業のムダが減り、生産ラインの稼働率が向上します。たとえば、必要な部品や工具がすぐに取り出せるように整理されていれば、作業の手戻りや待ち時間が減少し、スムーズな流れを実現可能です。
逆に、段取りが不十分な場合は、生産の途中で中断ややり直しが発生し、結果的に稼働率が低下してしまいます。段取り改善は、生産全体のスピードアップに直結する重要な施策です。
製造コスト削減への貢献
製造コストを下げるためには、材料費やエネルギーコストの見直しだけでなく、作業工程そのものの効率化も欠かせません。段取り改善によって作業時間が短縮されれば、稼働時間に伴う人件費を削減でき、コスト全体の引き下げにつながるからです。
段取りがスムーズになることでミスややり直しが減少し、不良品によるロスコストも低減できます。
品質の安定と不良率の低減
安定した段取りを確立すれば、作業の流れに無理やムダがなくなり、製品の品質も安定します。段取りがしっかりしていれば、生産中に中断するリスクが少なくなり、ミスや不具合の発生率も抑えられるためです。
結果として、全体の不良率の低下、歩留まりの改善などが見込まれるでしょう。
従業員のタイムマネジメント向上
段取り改善は、現場作業者一人ひとりのタイムマネジメント能力向上にも寄与します。計画的に準備ができるようになれば、作業の見通しが立てやすくなり、業務の進行管理がしやすくなるからです。
その結果、ムダな残業を減らし、定時内で作業を完了できるようになり、従業員の労働環境改善にもつながります。
製造現場で段取りの改善が進まない3つの要因
段取り改善が重要だとわかっていても、実際にはなかなか改善が進まない現場も多いのが実情です。ここでは、製造現場で段取り改善が進まない主な3つの要因について詳しく解説します。
現場の整理整頓が行われていない
段取りのスムーズさは、現場の整理整頓状況に大きく左右されます。工具や部品が定位置に置かれていなかったり、作業スペースが乱雑だったりすると、必要なものを探すために余計な時間がかかり、段取りに遅れが生じます。
整理整頓ができていない現場では、段取りにおいて「探す」「移動する」といったムダな動作が増えてしまうため、結果的に改善が進みにくくなります。これらを改善するためにも、5S活動(整理・整頓・清掃・清潔・しつけ)を徹底することが、段取り改善の第一歩となるでしょう。
5S活動は世界中で使われている改善活動であり、多くの企業で取り組まれているものの、思うように浸透しないなど失敗する企業も多く、中にはどのように取り組むべきかわからないケースも多いです。そんな方に向けて、数々の企業で5S改革に取り組んできた専門家による解説動画を用意しています。具体的なアクションや戦略の設計などを解説していますので、下の画像をクリックして動画をご覧ください。
属人化によって作業にバラつきが発生している
段取り作業が特定のベテラン社員に依存して属人化している場合も、改善が進まない大きな要因です。
たとえば、新入社員への教育が十分でない現場では、段取り作業を一部の熟練者だけが担当することになり、誰でもできる状態になっていません。そのため、担当者が不在だったり、急な休暇に入ったりすると、段取り作業が滞り、生産ラインがストップしてしまうリスクも高まります。
属人化を放置すると、作業のバラつきが生まれ、標準化が進まないだけでなく、改善活動そのものも個人に依存してしまいます。段取り作業は誰でも再現できるように標準化し、教育体制を整えることが重要です。
属人化は段取り改善の改善を阻むだけではなく、生産性や作業品質の低下につながるため、早急な改善が必要です。以下の動画では、属人化する原因や解消するための具体的な方法を専門家の視点でわかりやすく解説していますので、下のリンクからご視聴ください。
>>「品質と生産性の向上を実現する属人化からの脱却戦略(資料無料)」を見てみる
段取りの時間が十分に確保されていない
製造現場では、機械を動かしている生産工程が最優先されるため、段取りに十分な時間が確保できないケースがみられます。
そもそも段取り時間とは、「ある製品の加工が終わってから、次の製品加工に切り替え、スムーズに生産できる状態にするまでにかかる時間」のことです。この時間を確保せずに急いで生産を続けてしまうと、必要な設備や材料の準備不足が発生し、結果として生産中断などにつながってしまいます。
本来、段取りの時間は「利益を生み出す準備」として積極的に確保すべき工程です。しかし、生産を優先するあまり、段取り工程が軽視されてしまうことで、かえってトータルの生産性が落ちるリスクが高まってしまいます。
【5ステップで解説】製造現場の段取りを改善する方法
段取り改善を効果的に進めるには、やみくもに取り組むのではなく、正しいステップに沿って進めることが重要です。ここでは、製造現場における段取り改善の具体的な進め方を5つのステップで解説します。
Step1.現状の段取り作業を把握する
まず最初に行うべきは、現状の段取り作業を正確に把握することです。
段取りの手順がどのように行われているかを観察し、手順書どおりに進められているかをチェックします。作業の中にムダな動きや手戻りがないか、改善の余地がないかを確認し、気づいた問題点はすべて書き出しておきましょう。
現状を「見える化」することで、どこに改善の余地があるのか明確になります。現状把握は、すべての改善活動の土台となる非常に重要なプロセスです。
Step2.内段取りと外段取りに分類する
次に、現行の段取り作業を「内段取り」と「外段取り」に分類します。
- 内段取り:機械や作業を停止して行う段取り作業
- 外段取り:機械や設備を稼働させたまま実施できる段取り作業
たとえば、部品の準備や工具の確認などは、本来機械を止めなくてもできる外段取りに該当します。この分類によって、どの作業が生産停止の要因になっているかを明確にできるため、次の改善施策へとつなげやすくなります。
Step3.外段取り化で準備作業を短縮する
外段取り化とは、本来内段取りだった作業を、外段取りに移行する取り組みです。
たとえば、段取り替え前に必要な部品や治具をあらかじめ準備しておく、必要なセッティングを事前に整えておくといった取り組みがあげられます。
外段取りを増やすことで、機械の停止時間を大幅に削減でき、生産性を落とさずに段取り作業を進められるようになります。生産ラインの稼働率を上げたいなら、外段取り化は避けて通れない重要なステップです。
Step4.改善項目を洗い出し優先順位をつける
現状把握と分類ができたら、改善できるポイントを洗い出し、それぞれに優先順位をつけます。改善項目の具体例は、以下のとおりです。
- 属人化している作業の手順を標準化する
- 複数名で協力して行える作業に切り替える
- 作業内容そのものを簡易化・省力化する
一度にすべてを改善しようとするのではなく、影響が大きいものから優先的に取り組むことで、確実な効果を得やすくなります。
Step5.ムダを徹底的に排除する
最後に取り組むべきは、段取り作業に潜んでいる「ムダ」の徹底排除です。
ここで意識したいのが、「3M(ムリ・ムダ・ムラ)」の考え方です。
- ムリ(作業員に無理な負荷をかけている)
- ムダ(必要のない動きや作業が発生している)
- ムラ(作業のバラつきが大きい)
これらの要素は、作業効率や品質を大きく低下させる原因になります。作業場の動線を見直したり、設備の配置を最適化したりすることで、ムダな動きや時間を徹底的に削減していきましょう。
日常的に取り入れられる段取り改善のポイント
段取り改善は一度だけの取り組みで終わるものではありません。現場に根付かせ、継続的に改善を進めていくためには、日常的な工夫と習慣化が欠かせません。ここでは、段取り改善を定着させるための3つのポイントを紹介します。
継続的な教育と定着化を図る
段取り作業を属人化させないためには、まず標準的なマニュアルを作成することが基本です。しかし、単にマニュアルを作っただけでは、知識が現場に定着するわけではありません。
マニュアルの内容を確実に現場に浸透させるには、継続的な従業員教育が必要です。たとえば、定期的な段取り作業の振り返り研修や、改善事例の共有会を開催することで、従業員一人ひとりが段取りの重要性を再認識し、正しい手順を習慣化できます。段取りを効率的に行えるスキルを「現場全体の当たり前」にすることが、長期的な改善効果につながります。
一方で、段取り作業を手順書にまとめて教育を実施しても、定着するまでに時間がかかり、中々手順書通りにできない場合もあるはずです。以下の資料では、作業者視点でなぜ手順を守れない理由、わかりにくい手順書の共通点を踏まえ、整備するうえでのポイントをまとめています。下のリンクをクリックして資料をご覧ください。
>>「“手順書通りにできない”から卒業!作業ルールを守らせる効果的な方法」を見てみる
現場の声を拾い、改善につなげる
段取り改善を進めるうえで見落としてはならないのが、現場で実際に作業をしている人たちの声です。管理者がトップダウンで進めるだけでは、実際の課題や細かな不便を拾いきれず、形だけの改善に終わってしまうリスクがあります。
たとえば、「この道具は取り出しにくい」「この作業工程はムダが多い」といった現場からのリアルな意見を収集し、それをもとに段取りを見直していくことが重要です。現場の体験に基づくフィードバックを反映することで、より実践的で使いやすい段取り改善が実現できます。
必要な段取り作業を可視化する
段取りをスムーズに進めるためには、必要な作業を「見える化」することも大切です。
たとえば、作業手順を掲示板や表示シートにまとめて明示したり、工具置き場にラベルを貼って定位置を明確にしたりする方法があります。
誰が見ても一目で作業の流れがわかる状態を作ることで、迷いなく段取り作業が進められるようになり、作業ミスや時間ロスの防止にもつながります。また、新人や経験の浅い作業者でもすぐに対応できるようになるため、段取り作業の標準化にも効果的です。
段取り作業の改善を実現した企業事例
ここでは、動画マニュアルの導入によって、段取り作業を含む作業の標準化を成功させた新日本工機株式会社の取り組みを紹介します。
同社では、作業の多くがベテラン技術者の経験に依存し、技術伝承ができなかったり、指導者による技量や教え方にバラツキがあり、後戻り作業(リワーク)が頻繁に発生したりなどの課題を抱えていました
こうした課題に対して取り組んだのが、動画マニュアル「tebiki現場教育」を活用した技術伝承の可視化です。具体的には、作業手順を動画で記録し、ベテラン技術者のノウハウを「誰でも見て学べる」形に落とし込み、以下の効果が現れています。
- 経験に依存していた作業が標準化され、作業品質が安定
- 後戻り作業の大幅な削減
- 技術の伝承がスムーズに進み、新人教育の効率が向上
同社の詳しい事例は、こちらのインタビュー記事をご覧ください。
段取り作業の標準化には動画マニュアルが有効
段取り改善を推進するうえで、もう一つ重要な視点となるのが「標準化」です。誰でも同じ品質で段取り作業ができるようにするためには、マニュアル整備が欠かせません。
その中でも『段取り作業の改善を実現した企業事例』で紹介した事例のように、「動画マニュアル」の活用が有効です。ここでは、動画マニュアルが持つ2つの大きなメリットについて紹介します。
視覚的に理解を促進し、習得スピードを向上させる
紙の手順書やテキストベースのマニュアルの場合、段取り作業の細かな動きやニュアンスなどが十分に伝わらないこともあり、理解するまでに時間がかかるケースがあります。また、受け手によって解釈が異なる場合もあるので、誤った認識で作業が行われてしまうリスクもあるでしょう。
一方、動画マニュアルを活用すれば、作業をしている風景を収めた動画を通じて具体的な動きを見て理解できるため、紙と比べて段取り作業をはじめ様々な業務の習得スピードの向上が見込めます。
実際に動画マニュアルを活用している株式会社アルバックでは、「作業のスピード感や手の動き、工具の使い方など、細かな技術的ポイントが明確になり、技能向上にも大きく貢献している」と効果を実感しています。
理解度のバラツキを減らし、標準化を実現する
紙マニュアルだけでは、読む人の理解度に差が出やすく、「わかる人」と「わからない人」が発生してしまうことがあります。結果、作業のバラツキやミスが起こり、段取り改善が思うように進まない原因にもなりかねません。
動画マニュアルを導入すれば、誰が見ても同じ作業イメージを持てるため、理解度の差を大幅に縮められます。
かんたんに動画マニュアルを作成できる「tebiki現場教育」
新日本工機株式会社や、株式会社アルバックの事例のように、現場において動画マニュアルが活用されるケースは増加しています。
「動画編集の経験がないと難しいのでは…?」と感じる方も多いかもしれませんが、編集経験がない方でも簡単に使用でき、導入からわずか半年で400本以上のマニュアルの作成実績があるツールがかんたん動画マニュアル「tebiki現場教育」です。
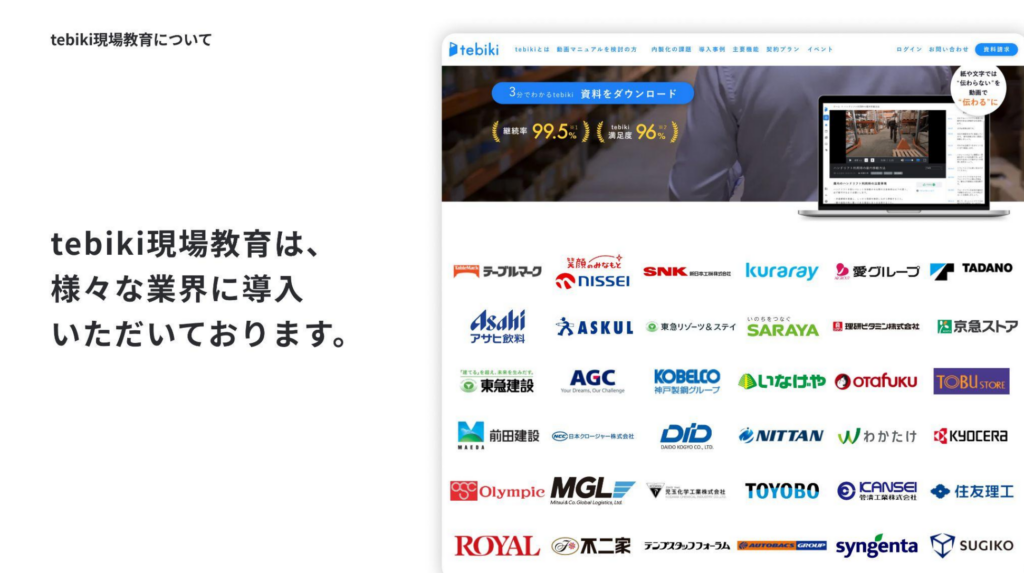
作業手順やルールなどのポイントを誰でもかんたんに視覚的に伝えられる動画マニュアルを作成することができます。tebiki現場教育に関するより詳しい機能概要やプラン、その他の改善事例などを詳しく知りたい方は、以下のリンクをクリックしてサービス概要資料をご覧ください。
>>「3分でわかるtebiki現場教育のサービス資料」を読んでみる
段取り改善を加速させるフレームワーク活用法
段取り改善を効果的に進めるためには、個別の工夫だけでなく、体系的なフレームワークを取り入れることが重要です。ここでは、特に有効な「5S活動」と「QCD」について解説します。
5S活動
段取り作業をスムーズに行うためには、作業環境そのものを整備する必要があります。そこで役立つのが「5S活動」です。
5Sとは、以下の5つの頭文字をとった改善活動です。
- 整理(Seiri)
- 整頓(Seiton)
- 清掃(Seiso)
- 清潔(Seiketsu)
- しつけ(Shitsuke)
製造現場において5Sを徹底すると、必要なものがすぐに取り出せる環境が整い、段取り作業におけるムダな探し物や移動が減少します。また、清掃や清潔を保つことで作業ミスや機器トラブルの防止にもつながり、結果的に段取り効率が大きく向上します。5S活動への理解を深めたい方は、こちらの記事か、専門家の視点で具体的な実践方法や成功させるポイントを解説した以下の動画をご覧ください。
>>【専門家が解説】生産性を高める5S活動の具体的な実践方法を見てみる(視聴無料)
QCD
段取り改善を考える際には、「QCD」の視点も欠かせません。QCDとは、以下の3つのバランスを最適化する考え方です。
- 品質(Quality)
- コスト(Cost)
- 納期(Delivery)
段取り作業においても、ただスピードを追求するだけでなく、品質を落とさずに、コストと納期も管理する必要があります。たとえば、段取り時間の短縮ばかりに目を向けると、結果的に作業品質が低下して不良品が増えるリスクがあるからです。
QCDのバランスを意識しながら段取り改善に取り組むことで、製造現場全体の最適化が図れ、持続的な生産性向上につながります。
まとめ:段取り改善で製造現場の生産性と品質を同時に高めよう
段取り改善は、製造現場における生産性向上と品質安定を同時に実現するために欠かせない取り組みです。生産効率を高めるだけでなく、製造コスト削減や不良率低減、従業員のタイムマネジメント力向上にも直結します。
段取り改善するためには、現状の段取り作業を正確に把握し、内段取りと外段取りを整理したうえで、ムダを洗い出して排除する体系的なアプローチが必要です。加えて、属人化を防ぐためにマニュアル化や動画活用による標準化も重要です。
さらに、5S活動による作業環境の整備や、QCD(品質・コスト・納期)バランスの最適化といったフレームワークを取り入れることで、段取り改善を着実に加速させられます。
製造現場の未来を支えるのは、日々の小さな「段取りの質」の積み重ねです。標準化と継続的な改善を意識しながら、誰もが実践できる段取り改善に取り組みましょう。
本記事で紹介した動画マニュアル「tebiki現場教育」のより詳細な機能説明や活用例については、以下の資料で詳しく紹介しています、下の画像をクリックして資料をご覧ください。