かんたん動画マニュアル作成ツール「tebiki現場教育」を展開する、現場改善ラボ編集部です。
曲げ加工は金属板を所定の角度に曲げて立体的な形状を作り出す成形技術であり、自動車や電子機器、精密部品など多岐にわたる製品づくりにおいて活用されています。しかし、曲げ加工は見た目以上に繊細な作業を伴い、適切な条件設定や技能を欠くと不良が発生してしまいます。
そこでこの記事では、曲げ加工の基本から、不良が発生する原因と対策、さらには現場での実例をもとにした改善ツールの活用法まで、品質改善に役立つ実践的な情報を詳しく解説します。
目次
曲げ加工とはどんな加工方法?概要とよくある課題
曲げ加工の概要
曲げ加工とは、金属板に外部から圧力を加え、特定の角度に曲げて目的の形状を作り出す加工方法のことです。せん断や絞りと並ぶプレス加工の基本的な手法であり、特に車体部品や電子機器用の精密パーツなど、広範な分野で活用されています。
加圧にはダイやパンチと呼ばれる金型が使われ、「ボトミング」や「コイニング」などの手法によって、曲げの精度や仕上がりが変化します。
しかし、材料には常に内部応力が存在するため、「スプリングバック(反発による角度ズレ)」が起きやすく、加えて、曲げ部分に「割れ」や「曲げコブ」などの不良が発生することもあります。
そのため、設計から加工条件の設定、作業工程に至るまで、精度と品質を維持するための高い技術力と管理力が求められるのが曲げ加工の特徴です。
曲げ加工を行う現場が抱える課題
曲げ加工の現場では、「カンコツ」がものを言う作業が多くを占め、熟練者の技術力に依存しがちです。
特に材料の突き当て位置や曲げ角度の微調整などは、経験に基づく感覚と判断が求められ、作業の成否を大きく左右します。そのため、新人や経験の浅い作業者では同じ品質を保つことが難しく、作業の属人化が発生します。属人化が進むと、作業品質にばらつきが生じやすくなり、品質不良も発生しやすくなります。
このようなカンコツ作業の属人化を解消する目的で、技術伝承に取り組むことが増えていますが、OJT(現場教育)の難しさや作業手順書の整備工数など、さまざまな現場課題によって曲げ加工で要求されるカンコツ作業の教育を難しくしています。
加えて、製造現場で増加傾向にある外国人作業者への教育も、言語や文化の違いによって、重要な作業手順が十分に伝わらないケースも少なくありません。現場の人材構成や教育体制が不十分なままでは、曲げ加工における品質の安定化は困難を極め、製品不良のリスクが常に付きまといます。
現場改善ラボでは、このようなカンコツ作業の属人化を解消する最適解について、図解も交えて解説するガイドブックを無料で公開中です。以下のリンクをクリックして、資料も併せてご覧ください。
>>「“伝わらない”“属人化している”カンコツ作業を標準化する最適解」を見てみる
曲げ加工によって生じる不良の例と原因
曲げ加工では主に以下の4つの現場を悩ませる不良が発生します。それぞれの原因を知ることで、適切な対策が可能になります。
- 割れ(クラック)
- 曲げコブ
- スプリングバック
- 寸法不良
曲げ加工を含む、プレス加工全般の不良例を知りたい方は、以下の記事をご覧ください。
関連記事:プレス加工の不良原因と対策!品質向上を難しくする壁は?
割れ(クラック)
「割れ(クラック)」は曲げ加工で最も致命的な不良の1つです。特に材料の圧延方向と曲げ線が平行になる場合、板材の繊維構造に沿って割れが発生しやすくなります。
割れは通常、材料の端部から発生し、板厚や表面の粗さ、さらには曲げ半径の小ささが影響します。例えば、曲げ半径が板厚の5倍以下になると、応力が集中し割れやすくなります。
また、バリ面を外側にして曲げると表面が粗くなり、割れを誘発します。熟練者であれば、材料の圧延方向を考慮し、せん断面側を外側にして曲げるなど、割れを防ぐ工夫を行います。割れを防止するには、設計段階での圧延方向の考慮や、バリ面の取り扱い、適正な曲げ半径の設定が重要です。
とくに厚板の場合は、切り欠きを入れるなどの処置で割れ防止効果を高められます。
曲げコブ
曲げ加工により、板の端面が盛り上がる「曲げコブ」は、次工程での干渉や不良の原因になります。特にボトミング加工やコイニング加工で顕著に発生しやすく、板厚に応じてコブの大きさが変化します。目安としてはボトミング加工の場合は板厚×0.15、コイニング加工の場合は板厚×0.12です。
曲げコブを放置すると、箱曲げ時に隙間が生じたり、精密部品の穴に干渉したりと、通り精度や組み付けに支障をきたします。
コブの対策として、板厚以上の径の穴を設けたり、展開時に逃げを設計したりといった工夫が求められます。量産現場でコブ除去の作業工数が増えると、生産性や納期にも悪影響を与えるため、試作段階からの予防策が不可欠です。
スプリングバック
「スプリングバック」は、曲げた後の材料が元に戻ろうとする現象で、曲げ角度が意図よりも開いてしまう不良です。スプリングバックは、曲げ加工中に材料内部に残留する圧縮応力と引張応力のバランスにより生じます。
とくに高張力鋼板など、剛性が高い材料ではスプリングバックの影響が顕著になります。対策としては、目的の角度よりも深く曲げる「オーバーベント」や、金型に「ストライキング(突起)」を設けて反発を抑制する方法が取られます。
さらに、加工前にノッチを入れることで、反発の影響を局所的に抑える方法も有効です。設計段階からスプリングバックを考慮した形状や材料選定を行うことで、再調整や不良品発生のリスクを低減できます。
寸法不良
寸法不良は、曲げ角度や加工条件のズレによって発生し、組み付け不良や機能不良の原因となります。材料のバラつきや金型の摩耗、プレス機のストローク設定ミスなど、原因は多岐にわたります。
とくに「カス上がり」による打痕や傷が、微細ながらも寸法誤差を引き起こし、精密部品では大きな問題になります。また、スプリングバックや曲げコブも、結果として寸法不良に直結するケースが多いです。
対策としては、加工条件の最適化とともに、金型やプレス機の定期的なメンテナンス、スクラップ除去の工夫、例えばキックピンやエアブローの活用などが有効です。
ここまで曲げ加工で生じやすい不良の例と原因について、概要をご紹介しました。次章からはこのような不良を低減するために、どのような対策を講じればよいか?例を解説します。
曲げ加工の不良を低減する対策例
曲げ加工の不良は「材料」「設計」「加工条件」「作業手順」それぞれの精度と管理が重要です。具体的には以下の5つの対策が重要です。根本原因に合わせた対策で、不良を抑え、品質と歩留まりを改善しましょう。
- 材料表面の傷や異物を除去する
- 板厚や材質など原材料のバラつきを抑える
- 圧延方向などを考慮した製品設計にする
- 曲げ角度やストローク料などの加工条件の最適化
- 標準作業・作業標準の整備と手順遵守の仕組み作り
材料表面の傷や異物を除去する
材料表面の微細な傷や異物は、曲げ加工時に「割れ」や「打痕」といった不良の原因となります。特に端面の粗さが割れ発生に直結するため、材料の表裏やバリ面の確認、前処理の徹底が欠かせません。
バリ面が曲げの外側にあると、粗い面が応力を集中させ、割れを誘発するため、せん断面側を外にして曲げる工夫が有効です。また、カス上がりによって付着したスクラップが表面に傷をつけることもあるため、キックピンの活用やパンチへのエアブロー装置導入で異物の付着を防ぐとよいでしょう。
製品の特性・特徴によっては、工程内検査の1つとして目視検査を実施する手段もあります。曲げ加工の場合、材料表面だけでなく、曲げ試験や引っ張り試験など目視で判断する場面があるため、検査項目として目視を取り入れることも効果的です。
関連記事:目視検査の課題はどう解決する?原因や4つの対策を紹介
板厚や材質など原材料のバラつきを抑える
板厚や材質のばらつきは、曲げ角度や寸法精度に大きな影響を与え、不良品の原因となります。
とくに厚板では「曲げコブ」や「スプリングバック」のリスクが高まるため、安定した原材料供給が重要です。材料ロットによる硬度の違いや板厚偏差がスプリングバック量に影響し、加工後の角度ずれや通り精度の乱れを引き起こします。
対策としては、信頼性の高い仕入れ先の選定や受入時検査での板厚・材質のチェックを徹底することが基本です。また、ばらつきを見越した「マージン設計」や、ロットごとの加工条件の微調整による対応も現場では有効です。
圧延方向などを考慮した製品設計にする
材料の圧延方向は、曲げ部の強度や割れの発生に関わります。
圧延方向と曲げ線が平行だと、繊維構造に沿って割れが起きやすくなるため、設計段階で曲げ線が圧延方向と直角になるよう配置するのが基本です。また、異形状や複雑形状の製品では、突き当てや段取りに時間がかかり、位置ズレや突き当てミスによる不良リスクが増加します。
こうした形状には、治具の工夫や逃げ部の設計が効果的です。さらに、曲げコブによる干渉を防ぐため、穴開けや切り欠き処理などを盛り込むことで、後工程でのトラブルも防げます。
曲げ角度やストローク料などの加工条件の最適化
適切な加工条件の設定は、不良の発生率を大きく左右します。
例えば、曲げ半径が板厚の5倍以下だと割れが発生しやすくなり、スプリングバックの影響も大きくなります。また、ストローク量が過大または不足すると、曲げコブの膨らみが増加し、寸法不良の原因になります。こうした問題を防ぐには、金型の刃先Rを大きくする、ストロークの再設定を行うなどの調整が有効です。
また、ボトミングやコイニングなど加工方式ごとのコブの膨らみ量、目安としてはボトミング加工の場合は板厚×0.15、コイニング加工の場合は板厚×0.12をもとに、事前に膨らみを見越した設計や工程設計を行うことで、後工程での干渉を防止できます。
標準作業・作業標準の整備と手順遵守の仕組み作り
属人化を防ぎ、安定した加工品質を実現するには、標準作業の徹底が不可欠です。
とくに曲げ加工では、突き当て位置や材料の表裏の判断など、ミスが品質に直結するため、作業者による判断のばらつきを抑える仕組みづくりが重要です。現場では「勘と経験」に依存しがちですが、これを視覚化・言語化し、誰でも同じ品質を再現できる作業手順書や標準書の整備が必須です。
一方で、以下のような課題から手順書や標準書の整備が進まず、手順遵守が徹底できないケースをお話としてよく伺います。
- カンコツの言語化が難しく、文章として落とし込めない
- 製品数が多く、手順書/標準書の作成や更新が追い付かずOJTに依存
- 熟練者にOJT負担が集中、指導者によって教育内容がバラつく
次章以降では、このような曲げ加工の不良低減を難しくしている理由を整理し、品質向上策の手法として有効な取り組み内容を解説します。標準作業のような作業ルールを守らせる、効果的な方法は別紙のガイドブックで詳しく解説しているので、以下の画像をクリックして参考資料をご覧ください。
曲げ加工の不良削減が難しい3つの理由
曲げ加工の不良は技術・人材・コミュニケーションの壁が原因で削減が難しくなります。ここでは以下の3つの理由を解説し、現場で起きている根本課題を明らかにして、曲げ加工の不良の削減に向けた対策の糸口を探ります。
- 金型やプレス機のメンテナンスなど、作業者にカンコツが要求される
- 個人作業が中心で属人化しやすく、OJTを難しくしている
- 外国人籍の従業員へ、うまく作業内容を伝えられない
金型やプレス機のメンテナンスなど、作業者にカンコツが要求される
曲げ加工の品質維持には、金型やプレス機の状態管理が欠かせません。
しかし「日々のメンテナンス」こそが、熟練者の勘と経験に頼りがちな属人的作業です。例えば、金型の摩耗やプレス機のストロークずれなど、細かな異常を早期に察知し、トラブル対応するには高度な技能が求められます。
技術・技能伝承が進まない現場では、こうした判断が後手に回り、不良品の発生を招く原因となります。また、定期的なメンテナンスが不足すると、突き当て精度のズレや加工条件のばらつきが起きやすくなり「割れ」や「寸法不良」など多様な不良を引き起こします。
つまり、不良削減を進めるには、設備保守の知識・技術を継承できる仕組みと予防保全を徹底する現場文化の構築が不可欠と言えるでしょう。現場改善ラボでは、技術・技能伝承の推進による品質向上策について、元トヨタのトップ技能者が解説する動画を無料で公開中です。
以下のリンクをクリックして解説動画をご活用ください。
>>「元トヨタのトップ技能者に聞く 品質不良を改善するトヨタ式技能伝承」を見てみる
個人作業が中心で属人化しやすく、OJTを難しくしている
曲げ加工では、加工品目や材料が変わるたびに「段取り替え」や「金型交換」が発生し、そのたびに作業手順も変わります。膨大な業務パターンに対して、手順書の作成や改訂が後回しにされがちで、現場ではOJT(実務を通じた教育)が中心となり、指導者の負担が増加します。
その結果、作業内容の伝達にバラつきが生じ、思わぬ手順ミスが品質不良を生みます。属人化した作業が常態化すると、「誰がやるか」で品質が左右され、歩留まりの安定化が難しくなります。人材の流動が激しい現場では、手順やノウハウを「見える化」し、教育工数が負担にならないように考慮することが必要です。
このような製造現場特有の教育課題と具体的な解決策は、別紙のガイドブックで詳しく解説をしています。以下の画像をクリックして、参考資料としてご覧ください。
外国人籍の従業員へ、うまく作業内容を伝えられない
プレス加工を行う業種、例えば金属製品や自動車部品の製造や電子機器製造では、多くの現場で外国人労働者が働いています。しかし、曲げ加工のように工程が多く、作業ごとに注意点が異なる現場では、言葉の壁が大きな障壁になります。
例えば「突き当ての位置」や「材料の表裏の確認」といった基本的な作業手順でさえ、誤解や認識のズレが生じることで不良が発生します。特に、手順遵守が徹底されていない現場では、外国人従業員のミスが品質不良に直結するケースが後を絶ちません。
このような作業ミスを防ぐ、外国人従業員への教育方法やポイントを解説する記事を公開しているので、併せてご覧ください。次章では、ここまでご紹介した曲げ加工の品質改善を難しくする背景に基づいて、生産活動で品質向上に取り組んでいる製造業の事例をご紹介します。
生産活動の品質向上に取り組む製造業の事例と活用ツール
曲げ加工では、突き当て作業や金型交換、材料のセット方法など、動作と判断が密接に関わる工程が多く、紙の手順書では「伝わらない」ことが多々あります。
例えば、金型の微調整や曲げコブの除去手順などは、実際の手の動きや姿勢を見ないと理解しづらく、経験の浅い作業者や外国人従業員にとっては、理解度の差がそのまま不良や安全トラブルにつながってしまいます。
動画マニュアルを活用することで、実際の動作やコツをそのまま「見せる」ことで伝えられるため、教育効果が飛躍的に向上します。たとえば、突き当てミスを防ぐポイントや、スプリングバック対策の設定方法なども、動画なら誰でも直感的に理解できます。
本章では、実際に動画マニュアルを活用して作業ミスによる品質不良を削減している企業事例をご紹介します。
手順不遵守を9割削減し、品質改善を実現した事例
住宅設備や自動車向けの合成樹脂加工、産業機器の製造などを手掛ける児玉化学工業株式会社では、「外国人従業員の教育」と「紙の手順書の形骸化」、そして 「不明確な社内ルール(暗黙の了解)」 による作業のバラつきによる、作業ルールが守られないといった課題を抱えていました。
▼インタビュー動画:児玉化学工業株式会社▼
500種類にも及ぶ膨大な製品品番に対し、日本語がわからない従業員も多く、紙の手順書だけでは「伝わらない」問題が顕在化。実際に、手順が正しく伝わらず不良品が発生し、作業者によって作業方法が異なるなど、品質に直接影響が出ていました。
そこで作業手順を視覚的に分かりやすく共有する目的で「動画マニュアル」を活用し、結果的に手順不遵守による作業ミスを9割削減し、製品品質の向上を実現しています。
動画による手順共有により、外国人・日本人問わずルールが視覚的に伝わるようになっただけでなく、手順書作成の工数を紙の1/3に削減することにも成功しています。また、同社が活用した、かんたん動画マニュアル「tebiki現場教育」には、字幕や自動音声の翻訳機能を搭載しているため、外国人従業員が母国語で学べる体制も構築できました。
児玉化学工業株式会社の具体的な取り組み内容は、以下のインタビュー記事をクリックしてご覧ください。
インタビュー記事:手順書作成の工数は紙の1/3になったと思います。動画で作るのはかんたんだし、学ぶ側にもわかりやすいですよね。
多くの製造現場で活用されている教育改善を目的としたツール
ここまで曲げ加工について述べてきた通り、プレス機などの自動化が進んでも、製造現場における人手は完全にはゼロにはなりません。むしろ、メンテナンスや段取り作業など、作業者に求められるスキルや判断力は高度化しています。
製品の品質向上を実現するには 「教育の質と伝達手段の改善」 が不可欠であり、その有効な手段として動画マニュアルを活用する製造現場が増えています。動画マニュアルを活用する製造現場で、導入実績があるツールが「かんたん動画マニュアルtebiki現場教育」です。
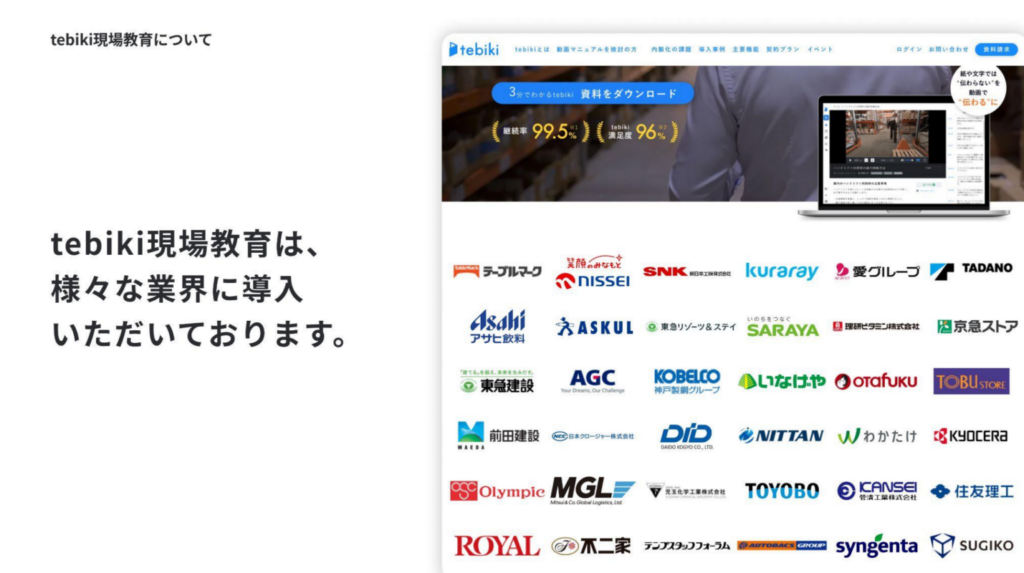
スマホで簡単に撮影・編集ができ、100カ国語以上に対応した自動翻訳、テスト機能やスキルマップ、教育履歴の可視化なども搭載。教育の効率化と質の向上を両立でき、多くの製造現場で導入が進んでいます。
実際に先述の児玉化学工業株式会社では、tebikiを活用し、手順不遵守による不良を9割削減する成果を実現しています。「tebiki現場教育」の具体的な機能やプラン、活用事例は以下のリンクをクリックして概要資料をご覧ください。
>>かんたん動画マニュアル「tebiki現場教育」の概要やプランを詳しく見てみる
曲げ加工の不良の対策もtebikiがおすすめ【まとめ】
曲げ加工の現場では、品質不良の原因が多岐にわたり、熟練者に依存した属人化や教育の難しさが課題です。
自動化が進む中でも、メンテナンスや段取りなど人の力が必要な作業は多く、教育の質が品質を左右します。
そこで効果を発揮するのが「動画マニュアル」です。視覚的にわかりやすく、誰でも正しい作業手順を理解・実践でき、不良削減や作業の標準化につながります。
この記事で紹介したおすすめの動画マニュアルのtebiki現場教育の資料は、こちらのリンクをクリックしてこの機会にチェックしてみてください。