かんたんデジタル現場帳票「tebiki現場分析」およびかんたん動画マニュアル作成ツール「tebiki現場教育」を展開する、現場改善ラボ編集部です。
製造現場における生産性向上の鍵は、「ボトルネック工程」の特定と改善にあります。他の工程がどれだけ生産効率が高くとも、生産性が著しく低い工程が存在するだけで、工場全体の生産効率は大きく低下します。
そこでこの記事では、ボトルネック工程の見つけ方を解説しつつ、改善の方法や事例もあわせてご紹介します。
目次
ボトルネック工程とは?生産性向上の鍵
ボトルネック工程とは、生産全体の効率を決定づける「制約」の箇所です。そこを見極め改善することが、生産性向上と経営改善の鍵となります。
ここでは具体的にボトルネックについて以下の3点を解説します。
- ボトルネック工程の定義
- なぜ改善が重要なのか?
- 製造業におけるボトルネックの具体例
ボトルネック工程の定義
ボトルネック工程とは、生産プロセス全体の中で最も生産能力が低く、全体の出力を制限してしまう「制約」となる工程のことです。
以下の図のように、他の工程がどれだけ高い生産パフォーマンスを持っているとしても、1つのボトルネック工程が存在するだけで、一気に生産効率は落ちることになります。
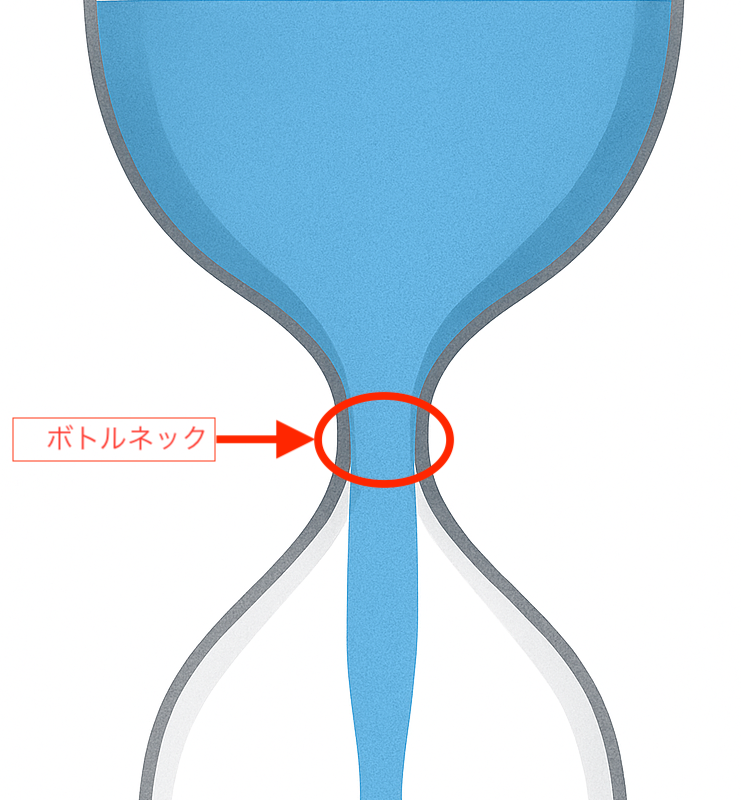
例えば、一連の組立工程で1つの機械の処理能力が極端に低ければ、そこがネックとなって全体の流れが滞ります。こうした制約は放置すれば、生産の遅れやコスト増を招くため、工程全体の中でどこが最も弱い部分なのかを明確にし、図解やフローで視覚的に把握しながら、早期に改善に取り組むことが重要です。
なぜ改善が重要なのか?
ボトルネック工程を放置するとリードタイムの長期化、仕掛品の増加、納期遅延、機会損失、そして不要な人員配置や設備投資によるコスト増大など、企業にとって重大なリスクを引き起こします。こうした状況が続けば、顧客満足度や収益性にも悪影響を及ぼしかねません。
一方で、ボトルネックを改善することで、生産性の向上、リードタイムの短縮、キャッシュフローの健全化、さらには現場スタッフの負担軽減にもつながります。
単なる効率化にとどまらず、企業経営全体の改善になるため、ボトルネック解消の意義は極めて大きいと言えるでしょう。
関連記事:製造現場の生産性が67%向上した事例や改善方法【指標や計算式も解説】
製造業におけるボトルネックの具体例
製造業の現場では、ボトルネックは主に「設備」「人」「検査」に集中します。
例えば、旧式の機械が生産スピードに追いつかず、段取り替えにも時間がかかる場合、それが設備的なボトルネックです。
また、作業内容が熟練者に依存し、標準化が進んでいない場合、人的なボトルネックとなり、生産が属人化してしまいます。
さらに、検査工程においてチェック項目が多すぎる、精度が求められるなどの理由で処理に時間がかかると、検査自体がボトルネックになります。
こうした工程を見極め、優先順位をつけて改善を進めることで、生産ライン全体のスループットが大幅に向上します。
ボトルネック工程の見つけ方
ボトルネック工程を正確に見つけるには、工程の「見える化」とデータ分析、現場観察による検証、関係者との合意形成という5つのステップが不可欠です。
- ステップ1:現状の工程を「見える化」する
- ステップ2:各工程のデータを収集・分析する
- ステップ3:生産能力を比較し、最も低い工程を特定する
- ステップ4:現場観察でデータとの乖離を確認する
- ステップ5:特定したボトルネック工程を関係者と合意形成する
ステップ1:現状の工程を「見える化」する
ボトルネックの特定には、全体の作業工程の「見える化」を行いましょう。客観的な事実に基づいて議論を進めるための共通の土台を築きます。
工程の見える化には、主に「プロセスマップ」と「QC工程表」という2つのツールが有効です。
プロセスマップで全体像を把握する
まず、製品が原材料の投入から完成に至るまでの一連の工程を、大きな流れで捉える「プロセスマップ」を作成します。フローチャートなどを用いて、各工程の順序、役割、担当部署などを書き出し、プロセス全体の骨格を可視化します。
これにより、どこで何が行われているのか、関係者全員が共通の認識を持つことができます。
QC工程表で詳細を定義する
次に、プロセスマップで描いた各工程をさらに掘り下げ、ボトルネック分析に不可欠な詳細情報を落とし込んだものが「QC工程表」です。
QC工程表は、単なる作業手順書ではありません。各工程における管理項目(機械の稼働条件、作業者のスキルなど)や品質特性(寸法、重量、外観など)、そしてその管理方法までを明確に定義した、いわば「モノづくりの設計図」です。
後続のステップ2で行うデータ収集・分析では、このQC工程表に定められた管理項目や品質特性が、「何を・どのように測定すべきか」の具体的な指標となります。もし、現場に既にQC工程表が存在する場合は、まずその内容が現状の作業実態と一致しているかを確認することから始めましょう。形骸化しているケースも少なくないため、実態との乖離があれば見直しが必要です。
QC工程表がない、または古い場合は、これを機に作成・更新することをお勧めします。
QC工程表の具体的な作成方法については、以下の記事で詳しく解説しています。ボトルネック工程の解消に寄与するため、あわせて参考にしてみてください。
関連記事:【サンプル有】QC工程表の作り方と2つの落とし穴~項目例も解説~
ステップ2:各工程のデータを収集・分析する
工程を可視化したら次は数値での裏付けが必要です。収集すべきデータは、サイクルタイム・段取り替え時間・設備稼働率・停止時間・仕掛品の数・不良品率などが挙げられます。
これらの数値を把握することで、ボトルネック工程発見のヒントが見えてくるでしょう。逆に言えば、ボトルネック工程を見つけるには、現場全体のパフォーマンスが常に数値化されている状態が作られていなければなりません。
数値把握を妨げるよくある要因が「手書き(紙)の帳票」です。例えば以下のような帳票が該当します。
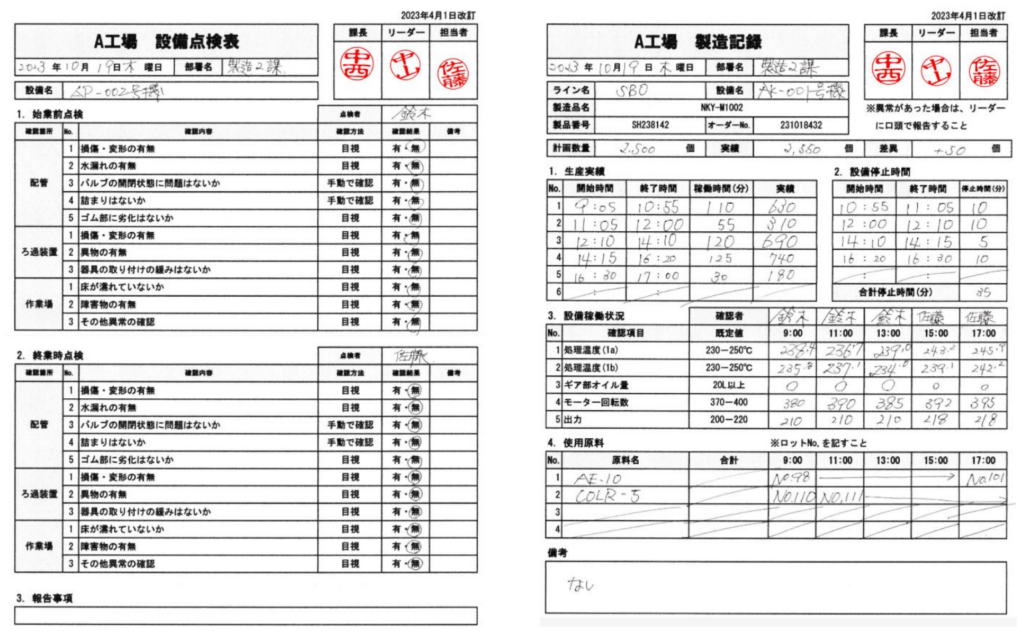
必要な数値を見つけるまでに時間がかかったり、記入されている数値に誤りがあったり、数値が記入されたタイミングが現状と乖離があったり等、リアルタイムなデータ分析が難しいのが紙の現場帳票です。
したがって、もし現場全体の数値を正確かつ迅速に分析し、改善の一手を速やかに打ちたい場合は、現場帳票のデジタル化が1つの有効手段になります。電子端末上の帳票に数値を入力するだけで、ツールによっては、例えば以下のようなグラフが端末上で自動で表示されるようになります。
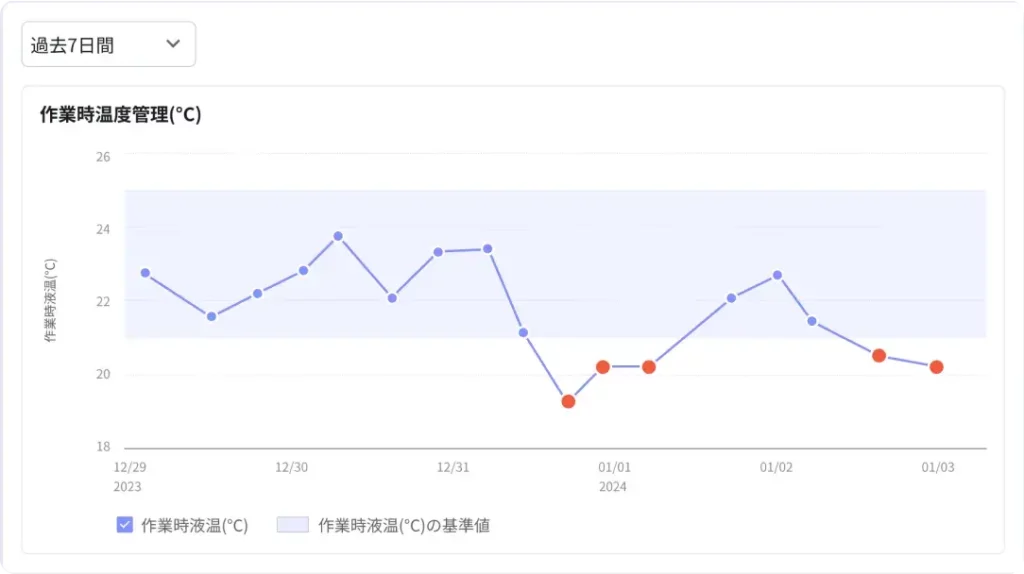
※デジタル現場帳票「tebiki現場分析」のサンプル画面を引用
データ活用の現場構築を実現する第一歩を検討している場合は、デジタル現場帳票の詳細なメリットや導入事例についてまとめられた資料(下のリンクをクリック)もあわせてご覧ください。
>>>「はじめての現場帳票デジタル化ガイド(pdf)」を見てみる
ステップ3:生産能力を比較し、最も低い工程を特定する
収集したデータをもとに各工程の単位時間あたりの処理能力を算出します。そして、最も能力が低い工程をボトルネック候補と仮定します。仕掛品が滞留している工程やその直前で手待ちが発生している工程も注目しましょう。
こうした現象は、工程間のバランスが崩れていることを示し、処理能力の差異がボトルネックを生んでいる可能性があります。仮説ベースで特定することで、改善の優先順位が明確になります。
現場の実態を知るためには、生産能力を示す数値指標も多数把握しておかなければなりません。例えば稼働率、不良率、歩留まり率、直行率等。こうした数値指標に関する解説は、以下の記事群で詳しくまとめられているので、あわせて参考にしてみてください。
▼関連記事▼
・稼働率とは?低下する工場が陥りがちな3つの損失と改善事例
・製造業の歩留まり改善「6つの秘訣」と直行率や良品率も向上するムダの排除法とは?
・不良率とは?計算法やPPMの目安・原因分析と改善事例
ステップ4:現場観察でデータとの乖離を確認する
数字だけでは見えない現場の「リアル」を知るためには現地・現物・現認が欠かせません。特定したボトルネック工程に実際に足を運び、作業者の動きや設備の使い方、モノの流れを観察しましょう。
例えば、「作業手順書通りに行われているか?」「ムリ・ムダ・ムラ(3M)が潜んでいないか?」といった視点が重要です。データでは優秀に見える工程でも、実際には非効率な動きや不安定な作業が隠れているケースも多くあります。
特に作業手順のバラつきによる品質不良や生産ラインの停滞は、多くの現場で重要視されている課題です。しかし、作業標準は重要だと認識しながらも、改善になかなか動けない現場は少なくありません。
そこで、作業標準が浸透するポイントについてまとめられたのが、下の資料「トヨタ流に学ぶ 作業標準の見直しで実現する製造現場の生産性向上」です。トヨタで実践されている標準の見直しと改善方法を知りたい方はあわせてご覧ください(下の画像をクリック)。
ステップ5:特定したボトルネック工程を関係者と合意形成する
ボトルネックの特定後は必ず現場の関係者と情報を共有し、合意形成を図ることが必要です。改善は1人で完結するものではありません。なぜその工程がボトルネックなのか、データと現場観察の両面から根拠を示し、納得感を得ることで、現場からの協力が得られます。
特に管理者や作業者、品質・生産・工程設計など他部門の理解が必要です。合意形成ができてはじめて、改善施策の実行と定着が進み、継続的な改善が可能になります。
【原因別】ボトルネック工程の改善アプローチ
ボトルネックを改善するには、まず基本となる考え方を理解し、その上で現場の状況に応じた具体的な原因別の対策を講じることが重要です。
ここでは、改善の基本思想である「TOC(制約理論)」と代表的な3つの原因(人的・設備的・プロセス的)に対応する解決策を紹介します。
- 【基本思想】TOC(制約理論)で全体の生産性を最大化する
- 【解決策①】作業の標準化と教育体制の整備で「人的要因」を解消する
- 【解決策②】設備改善・保全で「設備的要因」を解消する
- 【解決策③】帳票のデジタル化で「プロセス・管理的要因」を解消する
【基本思想】TOC(制約理論)で全体の生産性を最大化する
ボトルネック工程を改善するうえで重要なのが「全体最適」の視点を持つことです。その基本となる考え方がTOC(Theory of Constraints:制約理論)です。
TOCは工場の生産性は、最も能力の低い工程に制約されるという前提のもとで、全体の流れを改善していく管理手法です。
従来の生産改善では、各工程を個別に最適化しようとしがちですが、TOCでは全体のスループット(処理能力)を最大化することを目的とします。そのためには、まずボトルネックを正確に特定し、その工程を「止めない」「詰まらせない」ための工夫を優先的に実施します。
TOCには、改善のための5つのステップが用意されています。
- 制約条件を見つける
- 制約条件を最大限に活用する(止めない工夫)
- 他工程を制約に従属させる(ペース調整)
- 制約の能力を向上させる(改善・投資)
- 惰性に注意し、再び①に戻る(継続的改善)
1つ目は、制約条件(ボトルネック)を見つけることです。制約条件は工程の見える化とデータ分析、現場観察によって特定します。
2つ目は、制約条件を最大限に活用することです。例えば、作業の段取りを簡略化する、材料供給を優先するなど、ボトルネックを止めない工夫が求められます。
3つ目は、制約以外の工程を制約に従属させることで、非ボトルネック工程を無駄に作り過ぎて在庫を増やすのを防げます。
4つ目は、制約の能力を引き上げることです。これは、設備投資や要員増強、工程の見直しによって可能です。
最後は、改善の効果に満足せず、再び制約を探すことです。ボトルネックを解消すれば、次に制約となる工程が必ず現れます。そのたびに1へ戻り、改善サイクルを継続するのがTOCの特徴です。
【解決策①】作業の標準化と教育体制の整備で「人的要因」を解消する
現場で発生するボトルネックの多くは、人に起因する「属人化」によるものです。特定の作業を一部の熟練者しかこなせない状態や作業者によってスピード・品質にばらつきがある状態では、生産性が安定せず、ボトルネックとなって全体の流れを滞らせてしまいます。
このような人的要因のボトルネックを解消するうえで重要なのが、作業手順の標準化とそれを全員に浸透させるための教育体制の整備です。特におすすめなのが動画マニュアルの活用です。
動画マニュアルは、熟練者の動作や作業のコツをそのまま記録・可視化できるため、紙のマニュアルよりも圧倒的にわかりやすく、教育スピードも飛躍的に向上します。言葉だけでは伝えにくいポイントや、作業環境ごとの注意点も映像で直感的に把握できるため、新人や外国人スタッフでも理解しやすく、早期戦力化につながります。
例えば、自動車部品や住宅設備等のプラスチック成形品を手掛ける製造企業である「児玉化学工業株式会社」では、現場従業員が以下の動画マニュアル「ヤスリでバリを取る業務プロセスの解説」を作成し、技術をスムーズに共有しています。
▼動画マニュアルによる技術継承の例(音量にご注意ください)▼
※現場従業員が「tebiki」で作成
一目で「何をどうすればいいか」が把握でき、文字では伝えにくい動きもすべて理解できるようになっています。
製造業における動画マニュアルの活用事例をもっと知りたい方は、下のリンクから資料をご覧ください。どういった作業が動画で教育が可能になるのか、よりイメージがつきやすくなると思います。
>>>「製造業における動画マニュアル活用事例集(pdf)」を見てみる
【解決策②】設備改善・保全で「設備的要因」を解消する
ボトルネックの原因として次に多いのが、設備に起因する制約です。例えば、処理能力が低い旧式の機械、頻繁なチョコ停(小停止)、段取り替えの長さ、突発的な故障やメンテナンス遅れなどが挙げられます。
こうした設備的ボトルネックの改善には予防保全(定期点検・清掃・潤滑など)の徹底を行いましょう。日々の点検項目を決め、ルールに基づいた記録と報告を習慣化することで、早期に異常を発見でき、突発停止(いわゆる「ドカ停」)のリスクを大幅に下げることが可能になります。
さらに、データの蓄積と分析により、予知保全にもつなげることが可能です。振動・温度・運転時間などのデータをIoTやセンサーで取得すれば、「そろそろ異常が出る」という兆候をつかみ、事前に対処できます。
属人化しがちな保全業務も、デジタル化によってノウハウを形式知化すれば、誰でも一定品質で対応可能になります。
設備の突発的な停止(ドカ停)を防ぎ、保全業務の属人化を解消したい方には「設備保全のDX化」が1つの有効手段です。保全業務のノウハウを形式知化し、安定生産を実現する方法がまとめられた資料もあわせて参考にしてみてください(下の画像をクリック)。
【解決策③】帳票のデジタル化で「プロセス・管理的要因」を解消する
製造現場では工程自体は問題ないのに、情報の遅れや管理の非効率さが原因でボトルネックが生まれることも少なくありません。例えば、前工程の部品供給が遅れる、承認や検印が滞る、計画の精度が低く現場に混乱を与えるなどが挙げられます。
こうしたプロセス・管理的なボトルネックには、帳票のデジタル化が有効です。紙の帳票やExcel管理では、情報が分断され、入力・転記・報告に時間がかかります。一方で、現場帳票をクラウド上で運用できるツールを導入すれば、データはリアルタイムで集計・可視化され、関係者間で即時共有が可能になります。
例えば株式会社日本電気化学工業所は、現場帳票をデジタル化したことで、設備の温度異常をリアルタイムで検出できたことで品質不良を未然防止することに成功しています(下のリンクから事例の詳細が読めます)。
インタビュー記事:品質不良の未然防止をリアルタイムデータで実現。異常値検知を迅速にできた理由。
デジタル現場帳票の導入を検討している方は、詳細なメリットや導入効果についてまとめられた資料もあわせてご覧ください(下の画像をクリック)。
ボトルネック工程を改善した製造業の3つの事例
ここからは、ボトルネック工程を改善した製造業の事例を3つご紹介します。
株式会社日本電気化学工業所:リアルタイムのデータ活用で品質不良を未然に防ぎ、検査工程のボトルネックを解消
株式会社日本電気化学工業所は、アルミニウムの表面処理を専門とし、建材・自動車・航空機など幅広い業界に製品を販売しています。同社は、品質管理の徹底と環境配慮を両立させた生産体制を築いてきましたが、紙の帳票による運用にはいくつかの課題を抱えていました。
特に、異常値の発見に時間がかかり対応が遅れることで品質リスクが高まること、記録が目的化して改善活動に活かされていなかったこと、承認作業に現場巡回を要することなど、管理工数が大きい点が問題となっていました。
こうした課題に対して、同社はデジタル現場帳票(tebiki現場分析)を導入。帳票のデジタル化により、温度などの製造パラメーターをリアルタイムで監視できるようになり、微細な変化にも即座に対応できる体制を構築しました。さらに、異常値の自動通知機能や承認作業のオンライン化により、現場の業務負担を軽減し、品質管理の効率と精度を大きく向上させています。
株式会社日本電気化学工業所の詳細な事例は、以下のインタビュー記事からご覧いただけます。
インタビュー記事:品質不良の未然防止をリアルタイムデータで実現。異常値検知を迅速にできた理由。
株式会社アルバック:拠点間の作業分析で生産性167%向上。作業のバラつきというボトルネックを克服
株式会社アルバックは、真空技術を基盤に半導体・FPD・電子機器など幅広い産業に装置や材料を提供する製造企業です。同社は同じ製品の製作において最大74分の作業時間差があるなど、生産性の地域差が深刻な課題となっていました。
特に、ボンディング工程の効率に大きなギャップがあり、1日の生産量に明確な差が出ていました。
同社は、生産量の差分が発生する要因の1つに「作業手順のバラつき」が存在することを特定し、「動画マニュアルによる現場教育体制(tebiki現場教育)」を整備しました。作業の映像化により、属人的なノウハウを可視化・言語化し、全社的な標準化と技術伝承を加速させたのです。
結果的に、東北工場の作業時間は78分短縮され、1日あたりの生産可能枚数は167%に向上し、67%の生産性向上を達成する成果につながりました。
さらに、定点カメラで撮影した動画を活用し、九州・東北両工場の合同上映会を実施。作業の比較と意見交換により、暗黙知を共有しながら最適な作業標準を再構築しました。
株式会社アルバックの詳細な事例は以下のインタビュー記事からご覧いただけます。
インタビュー記事:人員・労働時間を変更せずに、ボンディング工程の生産性を167%に改善
御幸毛織株式会社:動画による技術伝承で「ベテラン依存」のボトルネックから脱却
御幸毛織株式会社は、1905年創業の老舗繊維メーカーで、紡績から縫製・販売まで一貫体制で高品質なオーダースーツやユニフォームを提供しています。
同社はかつての採用停止により社員の年齢が40~50代に偏り、職人技術の若手への伝承が経営課題となっていました。特に繊維業では、細かな手作業や熟練者の微調整が製品品質に直結するため、暗黙知の継承が急務でした。従来は紙マニュアルによるOJTが中心でしたが、細かな動きやニュアンスが伝わらず、活用も進みませんでした。
そこで同社は動画マニュアル(tebiki現場教育)による技術伝承を推進。現場でスマートフォンを使い、若手がベテランの作業を撮影し、字幕や解説を加えて技術を可視化・蓄積しました。
導入後は作業の属人化が解消され、補修・整備・縫製といった工程の技術が効率よく共有されるようになりました。また、事故リスクの高い作業を「べからず動画」で再現するなど、安全教育にも活用。技術伝承とDXの融合による生産性と品質の両立を実現しました。
御幸毛織株式会社の詳細な事例は以下のインタビュー記事からご覧いただけます。
インタビュー記事:明治時代創業の繊維会社が挑む技術伝承!ITテクノロジーを駆使して伝統芸を若手へ伝達
まとめ:ボトルネック工程は「人(作業)」「設備」「データ管理」から発見する
生産性向上の鍵となるボトルネック工程は、生産プロセス全体の能力を抑制する最大の制約点です。これを的確に特定し改善することが、生産性向上に不可欠です。
ボトルネックは主に、熟練度に依存する「人(作業)」、旧式化や故障が多い「設備」、そして情報共有の遅れや非効率な「データ管理」に潜んでいます。これらを発見するには、まず工程の「見える化」を行い、収集したデータ分析と現場観察を通じて候補を特定し、関係者と合意形成することが重要です。
しかし、データ分析は容易ではありません。データ集計するだけでも一苦労な現場もあれば、データ分析の基盤がそもそも構築されていない現場もあるでしょう。
常にリアルタイムでデータ集計・分析がなされる仕組みを作って初めて、ボトルネック解消の一手を担うことができます。その1つの手段として「デジタル現場帳票」を本記事では何度か推奨しました。自社の状況に合わせて、導入を検討してみてください(下の画像をクリック)。