動画マニュアルtebiki、デジタル帳票「tebiki現場分析」が運営するWEBメディア・現場改善ラボです。
IE(インダストリアル・エンジニアリング)とは、生産工程を分析し、製造やサービスのプロセスを効率化するための手法です。工場の生産性向上や業務改善を目指す企業にとって、IEの導入は欠かせないステップの1つだといえます。
本記事では、IEの定義や目的、具体的な事例、活用のメリットについてご紹介します。分析手法、効果的なIEのために必要な要素、そして現場改善を助けるツールも詳しく解説します。IEについて網羅した内容となっていますので、是非ご参考ください。
目次
【基礎知識】IEとは?目的や資格、事例も紹介
最初にIE(インダストリアル・エンジニアリング)の基礎知識として以下の3つを解説します。
IEとは「生産工程を分析・改善して生産性を高める技術と手法」
IE(インダストリアル・エンジニアリング)とは、生産工程を分析し改善することで、生産性を向上させる技術と手法のことです。
日本IE協会によると、IEは「価値とムダを顕在化させ、資源を最小化することでその価値を最大限に引き出そうとする見方・考え方であり、それを実現する技術」と定義されています。
IEは20世紀初頭にアメリカのフレデリック・テイラーによって提唱され、現在では製造業だけでなく、サービス業や農業、公共団体、家庭生活にも広く活用されています。
IEは何に活用できる?
IEは、あらゆる作業や工程におけるムリ・ムダ・ムラを明確にして改善することで、生産性を向上させる考え方です。そのため、製造業だけでなく、サービス業や物流業界など、あらゆる業界で幅広く活用できます。
具体的には、作業の効率化や設備の最適配置、作業員の動線改善、標準作業の策定などを通じて、現場の生産性を飛躍的に高めることが可能です。たとえば、製造業では作業の動作分析や時間研究を行い、最適な作業方法を導き出すことでムダな動きを排除し、効率的な生産が実現されます。
またサービス業では、IEを用いてサービス提供の流れを分析し、ムダな手順を削減することで、顧客満足度の向上とコスト削減を同時に達成することが可能です。たとえば、飲食業におけるオーダーから提供までの流れを見直すことで無駄な動きを削減し、回転率と顧客満足度を向上させることができます。
さらに農業における具体例として、収穫作業を天候や作物の成長段階に応じて調整し、収穫のタイミングや方法を最適化することで作業のムラを減らしながら収穫効率を高めることが可能です。
公共団体でも、申請手続きの流れを整理し、書類の確認プロセスを最適化することで、窓口対応の時間短縮と職員の負担軽減などが期待できます。
例で示したように、IEは多くの業界で効果的な生産性向上に貢献する重要な手法だといえます。
IEに役立つ資格
IEに役立つ資格として、有名なものでは「IE士資格認定制度」があります。IE士資格認定制度は、日本能率協会(JMA)が提供する「生産革新プロフェッショナルコース(IE士養成コース)」で取得可能です。
生産革新プロフェッショナルコース(IE士養成コース)は、生産・製造部門のマネージャーやリーダーなどを対象にしており、IEの基本的な理論や実践的な改善手法を学べる内容となっています。具体的には、IEの基礎テクニックや分析手法、さらには社内でIEを指導・育成するための教育内容が該当します。
IEの目的
IEの目的は、生産管理の最適化にあります。具体的には、以下の2点が挙げられます。
- 現場の3M(ムリ・ムダ・ムラ)の排除
- 生産管理のスキルを備えた人材の育成
生産工程に潜む3M(ムリ・ムダ・ムラ)の排除
IEの目的の1つは、生産工程に潜む3M(ムリ・ムダ・ムラ)を排除することといえます。現場に3Mが存在すると、生産性が低下してコストが増加します。
「ムリ」とは作業者や設備に過剰な負担をかけることを指し、ムリが続くと故障や事故の原因となります。「ムダ」とは付加価値を生まない活動のことで、ムダな動作や待ち時間、過剰な在庫などのこと。「ムラ」とは作業のばらつきや不均一性を指し、生産の効率を低下させる要因を指しています。
IEの手法を用いることで、3Mを見える化して定量的に分析することが可能です。例として、作業測定によって標準時間を設定することで、標準時間に収まらない作業を特定し、業務品質や効率のばらつきを減少させられます。
一方で、「作業現場のどこに3Mが潜んでいるのかよくわからない・把握できていない」という方も多いのではないでしょうか。
そこで、作業現場の3Mを見つけ出す視点や具体的な改善のコツについて学べる解説動画をご用意いたしました。本記事と併せ、是非ご覧ください。
>>「ムリ・ムダ・ムラ」を見つける視点と改善について無料で学ぶ
生産管理のスキルを備えた人材の育成
IEには、生産管理のスキルを持つ人材を育成するという目的も存在しています。IEの基本的な考えや分析手法を学ぶことで、作業者や管理者は生産工程を分析し、ムダを排除して生産性を高めるスキルを身につけられます。IEの手法を学ぶことで、作業者や管理者は生産工程の問題を体系的に捉え、改善策を提案・実行する能力を養えるでしょう。
また、IEを通じてデータの収集・分析を基にした改善活動が継続的に実施されることで、現場は市場や技術の変化に柔軟に対応できるようになります。最終的に、IEを通じて育成された人材は、工場全体の生産管理能力を底上げし、持続的な成長に寄与する存在となることが期待できます。
生産管理や生産品質の工場には、まずIE等を用いて現場のデータを「見える化」し、データを分析して改善点を見つけ出すことが必要不可欠です。
とはいえ、「データ分析ができる人材が限られている」「そもそもどのようなデータから集めればよいか不安」という方も多いのではないでしょうか。
そこで、指標とすべきデータの種類や収集方法、実際にデータ分析を行う実践的な方法を事例を踏まえながらわかりやすく解説した動画をご用意いたしました。本記事と併せ、是非お役立てください。
>>「製造現場で生産品質を向上させるデータ分析の進め方」を動画で学ぶ
具体的なIEの事例
具体的なIEの事例として、以下2つの業界例について解説します。
- 製造業
- サービス業
製造業
歯車の加工工程において、IEを活用した事例を紹介します。
事例の企業では、歯車(ワーク)の脱着作業に時間がかかり、生産効率の低下が問題となっていました。そこで、IEの基本的な分析手法を適用し、現状分析を実施。
まず時間研究を実施し、要素作業ごとの作業時間を測定しました。測定した結果、作業者ごとで作業時間に大きなばらつきがあり、特定の作業が時間を要していることが判明しました。
そこで、各作業者の脱着作業を動画化して見直し、作業の早い作業者に近づけるための意見交換を全員で行ったところ、意見交換前は脱着作業に88~112秒かかっていたのに対し、意見交換後は作業時間が75秒まで短縮され、最速の作業者の数値である70秒にまで近づけたという効果がありました。
また、動作研究を行い、作業者間の動作の違いを分析したところ、特に加工完了ワークの寸法検査やピックテストの際に時間がかかっていることが明らかになりました。
分析結果にもとづき、加工完了ワークの検査を脱着作業後に行うように順序を変更。工作機械の停止時間を短縮し、稼働率を向上させました。
またピックテストの時間短縮のため、レーザー距離計などの非接触測定具を導入し、マグネットスタンドの設置とピックテストの先端位置調整の時間を大幅に削減しました。
参照元:IE手法を用いた工作機械におけるワーク脱着作業の分析と改善提案
サービス業
ペットサロンのトリミング工程において、IEを活用した事例を紹介します。
事例の企業では、トリミング作業の効率化が課題でした。カット対象の犬が動いたり暴れることで作業工数がかかることに加え、作業時間のわりに報酬が低く生産性が低いことを課題視していました。
そこで、IE手法の一つであるECRS (Eliminate, Combine, Rearrange, Simplify) を導入しました。具体的には、各トリミング工程の作業区分を実施し、稼働分析を行いました。
結果、トリミング業務において「ヘアカット時間が長い」「トリミングの仕上がりにつながる付加価値作業時間が長い」「犬種により作業時間のムラがある」といった課題が洗い出されました。
この課題の解決に向け、トリマーの作業時間、仕上がり写真や作業履歴といった標準を定めて作業の標準化を図ったほか、さらに従業員の作業フローを分析し、効率的な配置と役割分担を再設計するといった目標が新たに定められ、改善に向けた活動が実現しています。
IEを活用する5つのメリット
IEには数多くのメリットがありますが、ここでは以下の5点に絞って解説します。
生産プロセスの最適化
IEを活用し作業の流れや動作を詳細に分析することで、ムダな動きが排除され、最も効率的な作業手順が実現します。たとえば、工程分析では工程ごとの動作や作業フローを観察し、改善することでムダな移動や待ち時間が削減できます。
結果、作業フローがスムーズになることで生産プロセス全体の作業効率が高まり、短時間で多くの製品を生産できるようになります。
生産効率の向上
生産プロセスの最適化に伴い、ムダな作業や遅延が削減されることで生産効率が向上します。例として、機械の稼働時間が不均一であったり、作業者が待機する時間が多い場合、IEを活用して稼働スケジュールや作業分担を調整します。その結果、設備の稼働率が向上し、従業員一人あたりの生産量も増加します。
さらに、動作分析によって作業者の動きを最適化し、必要な労力を軽減することが可能となるため、作業の疲労が減り、安定したパフォーマンスを維持できるようになります。
コスト削減
IE活用により材料や動作のロス・ムダが削減され、リソースの最適配分が実現することでコストの削減が期待できます。例として、稼働分析が挙げられます。稼働分析を通して作業者のムダな動きや機械の待機時間、材料や部品の消費状況を可視化できるため、コスト削減に向けた具体的な改善策の立案に繋がるでしょう。
また、ムダな作業時間や非効率な作業フローが排除されることで、労働力を有効に活用でき、必要以上の人員配置を回避することができます。
結果として、全体の製造コストが低減され、企業の収益性向上が期待できます。
品質改善
IEは、品質改善にも大きな効果を発揮します。IEによる分析や改善を通じて作業の標準化と最適化が実現することで製品の品質が安定し、不良品の発生を大幅に減少させることが期待できるでしょう。
標準化された作業手順は作業者間のばらつきを減らし、同じ品質の製品を一貫して生産するための基盤となります。
例として、動作分析で作業者が行う一連の動作を細かく分解し、最も効率的で正確な動作を標準化します。これにより、作業のばらつきを減らし、生産性向上と品質の安定化を同時に達成することができます。
また、データに基づく品質管理の導入により、リアルタイムでの品質チェックやフィードバックが可能となり、問題を早期に発見し、迅速に対応することができます。
これにより製品の信頼性が向上し、顧客満足度の向上にも繋がるといえるでしょう。
組織全体のチームワーク向上
IEの活用で部門間の連携強化と共通目標への協力が実現するので、組織全体のチームワークが向上します。たとえば、IEプロジェクトを通じて生産部門と品質管理部門が密に連携する場合が挙げられます。協力体制が組織全体に波及し、他のプロジェクトでも部門間の協力が促進され、組織全体のパフォーマンスが向上します。
また、IEは作業プロセスの可視化や標準化を通じて、各メンバーの役割や責任を明確にします。結果、全員が何をすべきかを具体的に理解でき、誤解や不必要な重複作業を減らすことができます。
例えば、工程分析や動作分析を用いることでチーム内での作業の流れが一貫して管理され、メンバー間の調整がスムーズになります。これにより、コミュニケーションが円滑になり、チーム全体で効率的に目標を達成する体制が整うでしょう。
IEの分析手法
IEの分析手法を大まかに分類すると、以下の3つが有名なものとして挙げられます。それぞれ深掘りしていくので、是非ご覧ください。
IEのような分析やデータ活用を行うことで、生産性向上や品質トラブルの未然防止といったカイゼンが期待できます。
一方で、「有効なデータが集まらない」「分析結果を活用するイメージがわかない」といった課題も多いのではないでしょうか?
現場改善ラボでは、製造現場で効果的なデータ活用の進め方を整理し、具体的な改善につなげるためのアプローチを動画で詳しく解説しています。本記事と併せ、是非ご覧ください。
方法研究
方法研究とは、作業の方法に着目し、最も効率が良い作業を見つけ出すことで最適化を追求する手法です。日本産業規格では、「作業又は製造方法を分析して、標準、総合化によって作業方法又は製造工程を設計・改善するための手法体系」と定義されています。
方法研究には、主に以下のような分析方法があります。
- 工程分析
- 動作研究(作業分析)
- 運搬分析(マテハン分析)
工程分析
工程分析とは、製造工程や各作業など、生産プロセス全体の過程を分析する手法です。工程分析では、工程の流れや動作、停滞時間などを工程図を用いて可視化し、問題点を特定して改善策を実施する点が特徴です。
工程分析には、主に製品化の流れに着目した「製品工程分析」と作業活動の流れに着目した「作業者工程分析」があります。
例として、部品の組み立て工程で材料の供給タイミングが遅れ、全体の生産フローに停滞が発生している場合、製品工程分析を行い材料の供給プロセスを見直し、タイミングを調整することでスムーズな流れを確保します。
動作研究(作業分析)
動作研究は作業分析とも呼ばれ、作業者の「動き」に着目し、最も効率的でムダのない動作を設計する手法です。作業者の動作を観察してムダな手の動きを排除することで、作業時間を短縮します。
例として、頻繁につかんで離す動作が多すぎる場合、その回数を減らすための改善策を導入し、作業のスムーズさを向上させることが可能です。
動作研究の具体的な手法としては、作業者の右手と左手の動作を工程図に落とし込んで可視化する「両手動作分析」や、つかむ・手を離すといった基本的な18パターンの動作を記号化して記録する「サーブリッグ分析」などが挙げられます。
運搬分析(マテハン分析)
運搬分析とは、製品や材料・部品といった「モノ」の流れに着目し、移動の過程に含まれるムダやロスを分析して可視化することを指します。「マテリアル・ハンドリング分析」を略した「マテハン分析」とも呼ばれます。
モノの運搬はそれ自体が直接的な付加価値を生むわけではない「付随作業」ですが、価値を生み出す作業には欠かせない要素です。そのため、運搬に潜むムダやロスを排除することが、結果として生産効率の向上やコスト削減につながります。
運搬分析の具体的な手法として、運搬の一連の流れと状態を記号で表して分析する「運搬工程分析」や、モノの移動の難易度(活性)を数値化して分析する「運搬活性分析」などが挙げられます。
作業測定
作業測定とは、主に作業にかかる時間に着目し、模範的な作業時間である「標準時間」を設定することでムダを排除して効率を向上させる手法です。具体的には以下の2つの分析方法があります。
- 時間研究
- 稼働分析
時間研究
時間研究(タイムスタディ)とは、作業にかかる時間を正確に計測し、作業の効率化を図るための手法を指します。
具体的な分析手法として、ストップウォッチを用いて実際の作業時間を直接測定する「ストップウォッチ法」や、動作ごとにあらかじめ決められた時間値をもとに作業時間を割り出す「PTS法」などが挙げられます。
時間研究を通し標準時間を設定することで作業者ごとのばらつきを減らし、効率的で安定した作業パフォーマンスを維持することが期待できます。
稼働分析
稼働分析とは、作業者や設備の稼働率や稼働時間などの状況に着目した分析手法です。
稼働分析で作業者や設備の実際の稼働状況を詳細に把握することで、作業効率や設備の利用率を向上させるための改善点を特定します。これにより、作業のムダやボトルネックが明らかになり、生産性向上に繋がる具体的な対策を講じることが可能です。
稼働分析の具体的な手法として、作業状況を観察や動画で撮影することで連続的に分析する「連続観測法」や、稼働状況をあらかじめ定められた時点で観測し、統計的に分析する「瞬間観測法」などが挙げられます。
組み合わせ手法
組み合わせ手法は方法研究と作業測定を統合し、全体的な生産効率を最大化する手法です。具体的な手法として、以下の3点が挙げられます。
- ラインバランス分析
- 連合作業分析
- プラントレイアウト
ラインバランス分析
ラインバランス分析とは、生産ライン上のムラを解消し、各作業工程における作業負荷を均等にするための分析手法です。
ラインバランス分析では工程分析と時間研究を組み合わせた分析が行われます。例として、時間研究を通じて各作業の標準時間を割り出し、工程分析でその作業の順序や流れを見直すことで、負荷が集中している工程や余裕のある工程を可視化します。
この情報をもとに作業を分割したり、設備や人員を再配置することで、各工程の処理時間をバランス良く整え、生産全体のスムーズな流れを実現します。
連合作業分析
連合作業分析とは、作業者や機械の組み合わせ(連合)を対象とした分析手法です。人対人の「組作業分析」や、人対機械の「人・機械分析」などが行われます。
連合作業分析では、複数の作業者や機械がどのように連携して作業を進めているかを詳細に観察し、作業の効率を最大化するための改善点を特定します。
例として、人対人の組作業分析では、各作業者がどのタイミングでどの作業を行っているかを分析し、無駄な待ち時間や重複作業がないかを確認します。これにより、作業の割り当てやタイミングを最適化し、チーム全体のパフォーマンス向上を図ることが可能です。
プラントレイアウト
プラントレイアウトとは、ムダのない生産や作業を実現するために必要なレイアウト(配置)を計画する分析手法です。ここでの配置は、機械や設備だけに留まらず、作業者も含みます。
例として、マテハン分析を通じて明らかになった「理想的な運搬の流れ」を反映したプラントレイアウトを設計することで、運搬距離や時間のムダを削減することができます。マテハン分析で最適な物の流れを把握し、それに基づいて機械や作業ステーションを配置することで、作業者の移動時間や運搬コストを大幅に減らせます。
また、作業者が効率よく動ける動線を考慮し、安全性も向上させることが可能です。
ここまで、IEの具体的な分析手法について解説しました。一方で、現場に即した分析を行い、改善点を見つけるには「ある2つのこと」が欠かせません。
次章では、効果的なIEを実現するために必要な要素について解説します。
効果的なIEのために必要な2つの要素
IEを効果的に活用するには、正確な記録データと改善策の標準化が不可欠です。ここでは以下の2点について解説します。
- 分析に使える正しい記録データ
- IEによる改善策の標準化
分析に使える正しい記録データ
分析は主観的な内容ではなく、製造現場にまつわる定量的なデータをもとに行います。そのため、IEの分析には、十分な量を満たした定量的なデータが必須です。たとえば、製造ラインでの作業時間の短縮を目指す際は、各作業工程の時間を正確に計測し、計測したデータにもとづいた分析なくては、改善のための正確な対策は導けません。
正確なデータを確保するには、計測器やデジタル記録ツールを用いたリアルタイムでのデータ収集のほか、製造日報や点検表など、日々のデータを記録した「現場帳票」を活用することが理想です。現場帳票には、作業状況や機械の稼働状況、作業者の動きなどの情報が含まれており、これらを定期的に見直すことで、過去の傾向や問題点を把握することができます。
たとえば、製造日報を通じて特定の工程での作業遅延や設備の不具合が頻発していることが分かれば、その原因を探るための追加分析が可能になります。
製造現場の「カイゼン」につなげる正しいデータ活用の進め方やデータ収集の具体的な手順については、以下の専門家による動画でも詳しく解説しています。本記事と併せ、是非ご覧ください。
IEによる改善策の標準化
IEは、ただ分析し状況を把握することがゴールではありません。分析を通じて課題を洗い出し、対策を考え改善までつなげることが目標です。さらに、対策が実際の作業手順や工程として定着し、改善が持続的に行われることが成果につながります。
そのため、IEによる分析と対策の検討は、現場に落とし込んで「標準化」することが重要です。たとえば、新しい作業手順を導入した後、手順をすべての作業員が一貫して実行できるように標準作業書を作成し、現場での教育訓練を行う必要があります。
IEを行う際は、分析部分にだけ注力するのではなく、その後の実行と定着までを見据えた全体的なプロセス=標準化を考慮することが求められます。
標準化はIEのほか、作業効率や品質の向上にも欠かせない要素です。一方で、作業手順書やマニュアルを整備しても、なかなか改善が見られないというお悩みもよく耳にします。
現場改善ラボでは、効果的な標準化の進め方について専門家が解説した動画もご用意しております。本記事と併せ、是非ご覧ください。
IEによる現場改善を助ける2つのツール
IEによる現場改善を助けるツールとして、動画マニュアルとデジタル帳票が有効です。ここではおすすめのツールとして動画マニュアル「tebiki」と、デジタル帳票ツール「tebiki現場分析」を紹介します。
『標準化が進まない…』ケースは動画マニュアル
標準化はIEに必要な要素のみならず、製造業における重要な課題です。しかし、現場での教え方や内容のムラ、ベテラン作業員のノウハウの伝達不足が原因で、標準化が進まないことがあります。
この課題を解決し、標準化をサポートするツールとして、「動画マニュアル」が挙げられます。動画による視覚的な情報伝達は効率的な学習を促進し、現場での負担を軽減することが可能です。
ここでは動画マニュアルについて以下の2点を解説します。
- 業務標準化に動画マニュアルが有効な理由
- tebikiなら簡単に動画マニュアルを作成!
業務標準化に動画マニュアルが有効な理由
動画マニュアルの最大の利点は、教育のばらつきをなくせることです。動画という同じ教材を使うことで、誰でも同じ情報を学ぶことが可能なため、「AさんとBさんで教え方や教える内容に差が生じてしまう」といった状況を回避できます。
また、動画であれば3次元的な動きを含むため言語化が難しい複雑な作業や、ベテランならではのカンコツ=暗黙知も、見たそのままの動きを視覚的に学べます。紙のマニュアルでは伝えきれない細かいニュアンスや、実際の動きを伝えることが可能になり、作業や業務のムラを解消することが期待できます。
さらに、動画であれば場所や時間を問わず繰り返し視聴できるため、OJTやマンツーマンの教育に頼らず、効率的に標準化を進められます。たとえば、新入社員が何度も同じ動画を見て学ぶことで、現場での教える手間が省け、作業の標準化が進みます。結果として、現場に負担をかけず、効率的に標準化を実現できます。
動画マニュアルによる教育効果や、標準化に役立つメリットについては、以下のハンドブックでも詳しくご紹介しています。本記事と併せ、是非ご覧ください。
tebikiなら簡単に動画マニュアルを作成!
動画マニュアルの中では、現場に嬉しい機能が多数搭載された「tebiki」がおすすめです。
▼動画マニュアル作成ツール「tebiki」紹介動画▼
tebikiの1番の特長は、誰でも簡単に動画マニュアルを作れる点です。シンプルな操作画面だからこそ、動画編集経験がない方でも直感的に操作することができます。
編集に時間がかかる字幕生成を自動で行う機能も搭載されているため、1つの動画をサッと15分程度で作成している企業の方も多いです。tebikiを使えば、以下の画像のようにたった3STEPで動画マニュアルを作成できます。
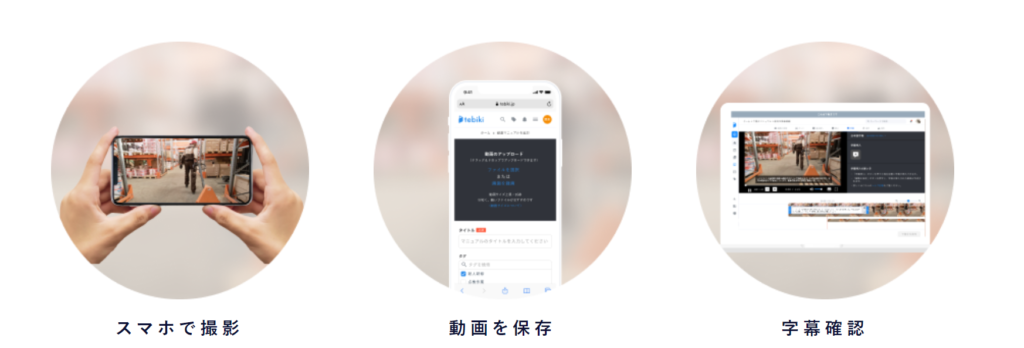
またtebikiには、マニュアルの視聴状況がわかる組織レポート機能や、マニュアルの内容をテストとして出題できる「テスト機能」が備わっています。
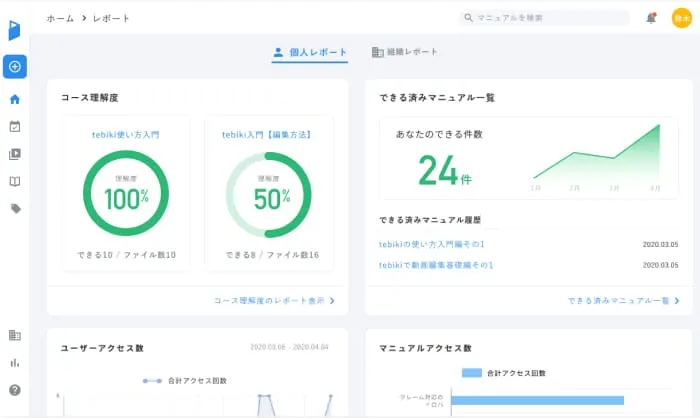
ユーザーごとのマニュアル視聴状況が可視化されるため、標準化の習熟度や浸透具合を把握しやすくなります。たとえば、作業員がどの程度マニュアルを視聴し理解しているかを確認することで教育の効果を定量的に評価し、必要に応じて追加の指導を行うことが可能です。
実際に、複雑な作業工程もこのツールを使うことで効果的に標準化し、現場の効率を向上させた事例があります。
tebikiの機能詳細や導入の費用対効果、実際の導入事例については、以下のハンドブックでも詳しく解説しています。標準化や現場教育を効果的に改善したい方は、是非ご覧ください。
『記録に負担がかかる…』ケースはデジタル帳票
現場改善につながるIEには、正確なデータの記録とその迅速な分析が不可欠です。しかし、手書きやExcelを使用した帳票管理には多くの課題があり、現場での記録が負担となることが多いでしょう。
そこで、デジタル帳票を導入することで記録作業を簡素化し、データの正確性を向上させることがおすすめです。
紙やExcelの帳票では正しいデータを集めにくい
手書きやExcelでの記録では時間がかかり、記録漏れや誤記入が発生しやすいでしょう。また手書きの場合は字が汚くて読めない、書き方や書く量に差があるといった問題もあり、データの統一性を欠くことが多い傾向があります。
デジタル帳票を使用すると、タブレット上で簡単にデータを入力できるため記録作業が迅速かつ正確に行えます。デジタル帳票により、手書きの際にかかる時間や誤記入のリスクを減らし、一定水準のデータを集めることが可能です。またデジタル帳票には入力必須項目を設定できる機能があるため、記録漏れを防ぐ仕組みが構築できます。
現場改善ラボでは、これからデジタル帳票の導入を検討される方に向け、デジタル帳票の主な機能やデジタル化の進め方など、帳票のデジタル化に役立つ情報をまとめたハンドブックを以下にご用意いたしました。本記事と併せ、是非ご覧ください。
tebiki現場分析ならリアルタイムで正しいデータを集めて分析できる!
帳票のデジタル化には、「tebiki現場分析」がおすすめです。
tebiki現場分析とは、現場帳票の作成・記録・承認・分析が簡単に行えるシステムです。本サービスを活用することで、IEに必要な現場データを効率的に収集・分析することができます。
tebiki現場分析はスマートフォンやタブレットでの入力に特化したわかりやすい操作画面を採用しており、難解な研修を受けずとも誰でも簡単に帳票を記入し、編集できます。また紙では難しかった画像記録もデジタルで簡単に行えるため、現場の状況を視覚的に把握することが可能です。
他にも、「帳票のピンどめ」により使用頻度が高い帳票を優先して表示させる機能や、毎回の記録で共通する内容の入力を省略できる「定時記録」の機能を使うことで、日常的に発生する進捗管理業務をよりスムーズに記録することも可能です。これにより、現場の状況をリアルタイムでデジタルデータとして記録し、分析に役立てることが可能です。
実際に、1日あたり2時間を要していた集計作業が1分に短縮され、記録データをもとに設備トラブルの予防措置が実行できるようになった事例もあります。
さらにtebiki現場分析には収集したデータを簡単にグラフ化する機能を備えており、視覚的に進捗状況を分析できます。分析機能をIEと併用して活用することで、現場に潜むボトルネックや異常、ムダを定量的なデータをもとに簡単に特定し、改善につなげることが期待できるでしょう。
tebiki現場分析の機能詳細や導入サポート体制については、以下のハンドブックでも詳しくご紹介しています。デジタル帳票で現場データを可視化し、分析や改善につなげたい方は是非ご覧ください。
tebikiを利用してIEを推進しよう【まとめ】
インダストリアル・エンジニアリング(IE)は、生産工程を分析・改善し、3M(ムリ・ムダ・ムラ)を排除することで生産性を高める技術と手法です。IEの活用により、生産プロセスの最適化、生産効率の向上、コスト削減、品質改善、チームワーク向上といった多くのメリットが得られます。
効果的なIEを実現するには、分析に使える正しい記録データが必要であり、結果から対策を検討することが重要です。分析に使える正しい記録データを得るには、従来の手書きやExcelから、デジタル帳票への乗り換えが有効です。
特に「tebiki現場分析」は、リアルタイムでの状況把握や簡単な記入・承認が可能で、製造業の現場改善に最適なツールです。
また、IEによる改善策を現場に落とし込み、作業手順や工程として標準化させることで、改善の成果を確実にする必要があります。
標準化が進まない場合には、動画マニュアルの活用が有効です。特に「tebiki」を使えば、スマホで簡単に動画マニュアルを作成し、テスト機能や視聴状況を管理できるため、標準化の習熟度を把握しやすくなります。
「tebiki現場分析」「tebiki」の機能詳細や導入効果、事例などをまとめた資料は以下の画像から無料でダウンロードが可能ですので、効果のあるIEや現場改善にご興味のある方は是非ご覧ください。