かんたん動画マニュアル作成ツール「tebiki現場教育」を展開する、現場改善ラボ編集部です。
少子高齢化・労働力不足などの様々な社会問題を抱えている現代において、作業効率向上や人手不足解消への取り組みが求められています。このような課題に取り組む際に重要な考えは「省人化」です。この記事では、省人化の概念とその背景、省力化や少人化との違い、それぞれのメリットとデメリットについて分かりやすく解説します。
なお、現場改善ラボでは省力化・省人化・小人化の進め方やコツを通し、多能工化を推進するための仕組みやポイントについて、専門家による無料のセミナー動画を配信しています。気になる方はぜひご視聴ください。
目次
省人化とは
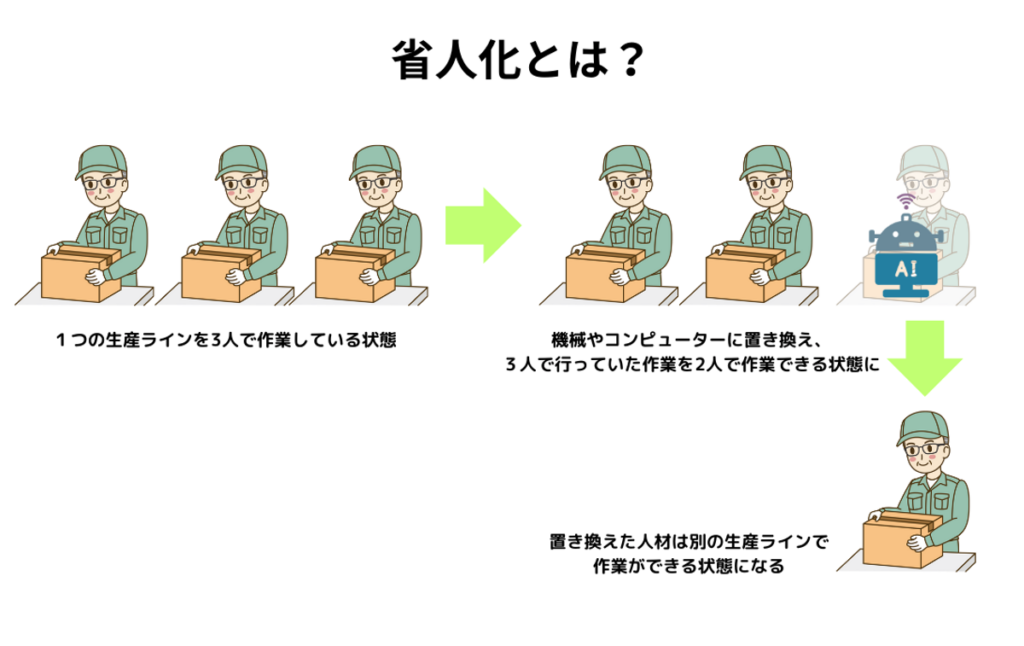
省人化とは読み方は「ショウジンカ」で、人間が行っていた作業を機械やコンピューターに置き換えて、人間が行う必要のない作業を減らすことで、労働力をより効率的に活用すること」を指します。
省人化の目的は、単純に人件費を削減するだけではなく、単純作業や繰り返しの作業を機械化したことで手があく作業者を、人手不足の他の工程や、高度な作業、人の思考を使う創造的活動に活かすことです。
製造業では、人が行っていた作業を産業ロボットに代替させることがひとつの具体的な省人化の方法となります。省人化の方法についてより具体的に理解したい方は専門家によるセミナー「省力化・省人化・小人化への具体的な対応策」(視聴無料)もご覧ください。
省人化はトヨタ生産方式から始まった
省人化は、徹底的な無駄排除を目指すための「トヨタ生産方式(TPS)」由来の言葉です。
TPSは、無駄を排除し、効率的な生産を追求するための手法であり、TPSの一環として省人化が採用された経緯があります。TPSの詳細は「トヨタ生産方式と現場改善~産業の垣根を超えた改善の着眼点~」(視聴無料)をご視聴ください。
製造業における省人化の取り組み状況
経済産業省が2017年12月に実施した「2018年版ものづくり白書 第2節」の調査では、人材の確保が「大きな課題となっており、ビジネスにも影響がでている」との回答が前年調査の22.8%とから32.1%に増加し、深刻な問題として顕在化しています。
このような人手不足の課題を解決すべく、企業では新卒採用の強化に重点が置かれている傾向がある一方、「自動機やロボット導入による自動化・省人化」、「IT・IoT・ビッグデータ・AI などによる生産工程の合理化」も大幅に増えている傾向です。
なお、自動機やロボット、データ活用などは、繰り返し行う単純作業や重労働、危険な場所での作業などに積極的な利活用が期待されています。また、単なる省人化だけではなく、業務全体の在り方を見直すなどの相乗効果が図れるなどの業務全体最適化を図る点でも有効な手段とされています。
省人化と少人化の違い
省人化と少人化は、両方とも人間の働き手の数を減らす傾向を表す言葉ですが、その背後にある理由や状況が異なります。少人化とは、後工程の需要の変化に応じて、最も少ない人数で業務に対応することが目的です。
つまり、省人化はあくまでも人員を減らすことを目的としていますが、少人化は人員を減らすことで、効率的に業務を遂行することを目的としています。
具体的な例を挙げると、省人化では、自動化設備を導入したり、業務の分担を見直したりすることで、人員を削減することができます。一方、少人化では、需要の変化に応じて、人員を増減させながら、効率的に業務を遂行することができます。
省人化・省力化を実現した企業事例
「製造業における省人化の取り組み状況」では、一例として製造業の省人化の状況を紹介しましたが、製造業に関わらず他の業界・業種でも同じような課題感を抱えている場合もあるかと思います。
ここでは、3つの業界で省人化・省力化を実現している企業の事例を紹介していきます。
大同工業株式会社
1933年に自転車チェーンの製造会社として創業し、オートバイ、自動車、産業機械、福祉機器などの幅広い製品のものづくりに携わる大同工業株式会社。同社では、新人教育の研修を非効率な体制で行っており、トレーナーごとの教え方にバラつきがあるなどの課題を抱えていました。
その課題を解決すべく、動画マニュアル作成ツールを導入し、新たな教育体制を構築しました。導入によって、2時間以上かかっていた文書マニュアルの作成や改訂が1時間以下まで削減することに成功しています。また、利用する中で各従業員から意見が活性化し、さらなる業務の効率化・最適化にもつながっています。
同社の具体的な取り組み内容は、以下のインタビュー記事をクリックしてご覧ください。
インタビュー記事:製造業の技術部門の業務を動画で標準化。教育工数を8割削減し、業務の効率化・最適化も実現。
株式会社安藤ハザマ
株式会社安藤ハザマは、高速道路や各種トンネルなどの土木事業や駅ビルや大型施設などの建築事業の2つを主軸に事業を展開している総合建設業です。
同社では、協力会社を含めた関係者が必要な情報を共有する「現場サポートシステム」を開発して展開していたところ、システム操作に関連する問い合わせが殺到してしまい、担当者の業務が圧迫される課題を抱えていました。
そこで、現場サポートシステムの操作方法を動画マニュアルにまとめて展開することにより、システムへの問い合わせが以前と比べて約7割削減し、省力化を実現しています。
同社の具体的な取り組み内容は、以下のインタビュー記事をクリックしてご覧ください。
インタビュー記事:建設現場で使用するシステムの「利用者からの問合せ」や「新システムの普及展開」に関わる工数を8割削減!
東急リゾーツ&ステイ株式会社
ホテル、ゴルフ場、スキー場、別荘地など全国100を超える施設運営を手掛ける総合運営会社の東急リゾーツ&ステイ株式会社。同社では、従業員ごとのサービスレベルにバラつきがあり、多能工化が進まない課題を抱えていました。
業務のバラつきを均質化するべく動画マニュアルを導入。施設ごとに異なっていたマニュアルを統一して管理することによって、当初の課題であった業務負担軽減を実現し、削減した労働時間を新たなサービスへの取り組み時間に転化することに成功しています。
同社の具体的な取り組み内容は、以下のインタビュー記事をクリックしてご覧ください。
インタビュー記事:従業員数2,500人超・全国100を超える施設で業務の平準化と多能工化を推進。
省人化・省力化のメリット
省人化・省力化のメリットは以下の4つです。
生産性の向上が見込める
省人化と省力化により、作業の自動化や効率化が進み、同じ時間でより多くの製品を生産することが可能になるため、生産性の向上が見込まれる点が大きなメリットです。
非効率な作業に人的なリソースを注ぐリスクがなくなるため、リソースの最適化が実現して、より生産性の高い環境を実現できるでしょう。
業務品質の向上につながる
人間の作業にはミスが生じる可能性がありますが、ロボットやAIによる自動化により、そのリスクを大幅に減らせるため、省人化・省力化には業務品質の向上の向上につながるメリットもあります。
例えば、精密な組み立て作業をロボットに任せることで、人間の作業によるミスを防ぎ、製品の品質を一定に保つことが可能になります。
なお、業務品質について詳しく知りたい方は、「業務品質の向上に必要な視点」「具体的な方法」を紹介しているこちらの記事もご覧ください。
人手不足解消や人材配置の最適化につながる
省人化・省力化に取り組むことによって、人が介入する作業の削減や機械への移行が実現します。そのため、リソースを最適化することができて、人手不足の解消につながります。
また、削減した分の人的リソースは、コア業務や新たな価値を作り出す作業に注ぐこともでき、人材配置・リソース配分の再低下にもつながるでしょう。
効率的な技術継承が行える
長期に渡って安定的な生産体制を構築するうえでは、技術・技能を適切に継承するのが重要です。しかし、ベテラン従業員ならではのカンコツ作業や暗黙知を要する作業を適切に、次世代に後継するのは非常に難しい取り組みと言えます。
省人化の過程で、標準化やロボットの活用が進んでいくことによって、技術伝承も効率的に進みます。
なお、以下の資料では、技術伝承の必要性や具体的な進め方、成功事例などを詳細にわかりやすくまとめています。技術伝承に課題感を抱えている方はぜひご覧ください。
省人化・省力化のデメリット
様々なメリットのある省人化・省力化ですが、デメリットの側面があるのも理解しておきましょう。デメリットは以下の4つです。
機械や設備を導入・維持のコストがかかる
省人化・省力化の取り組みは、製造業における生産性向上や品質向上に一役買いますが、一方で機械やロボットの導入には初期費用や維持コストが必要となるため、導入コストがかかるというデメリットがあります。
例えば、自動化ラインの設置やAIシステムの導入は、高額な投資が必要となります。また、導入に多くの時間や費用をかけたにも関わらず、自動化できた業務が投資コストに見合わなかったというリスクも存在します。
そのため、どれぐらいの業務が自動化でき、自動化によって生まれた時間をどの業務に割り当て、またどれぐらいの利益を生み出すのかなど、全体の流れをよく確認した上で導入を検討することが重要です。
専門人材の確保・育成が必要
省人化・省力化を推進するうえでは、機械やツールなどの導入や運用するための専門的な知識やスキルを持っているデジタル人材の確保や育成が欠かせません。
しかし、デジタルツールを使いこなせるデジタル人材は、業界を問わずに市場価値が高く確保するのも困難です。また、自社内にデジタル人材を育成するノウハウがないことも。経済産業省の「2018年版ものづくり白書」の結果では、デジタル人材の充足状況について、「質・量ともに充足できていない」と回答した人は77.4%にものぼっています。
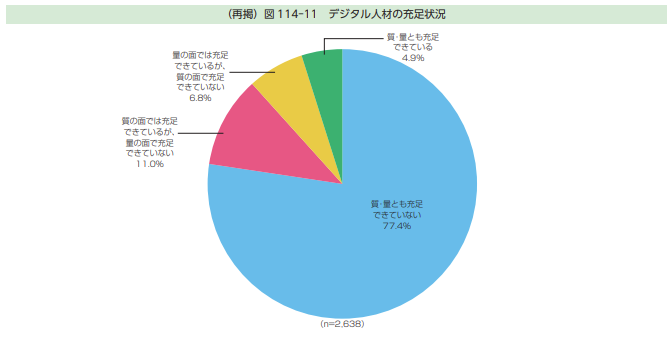
デジタル人材の確保・育成に向けた取り組みの課題や障害としては、「社内外の研修を受講する余裕がない」「社内に指導できる知見を持った人材がいない」などが挙げられています。また、高額な採用コストが発生するなどの要因もあり、デジタル人材の確保・育成は困難な傾向があるのです。
作業手順が変わるため従業員の理解を得る必要がある
省人化や省人化によって、従来の作業にロボットやツールが導入されるとこれまでのやり方から手順が変更されます。
従来から大きく変化することもあるので、実際に作業を行う従業員に対して事前に理解を得る必要があるでしょう。理解を得ていない状態で推進すると、手順の理解不足によって逆に作業効率が悪くなってしまう可能性も考えられます。
なお、製造業の一例として、Man(人)Machine(機械)Material(材料)Method(方法)のいずれかに意図的な変更を加える「4M変更」があります。4M変更や別に変更が発生した際に、変化を見過ごしたり、共有をしていなかったりすると品質面や安全面でのトラブルの元になる場合もあります。
そのため、省人化・省力化に取り組む理由や背景を明確に説明し、手順の変更があった際の共有や管理方法を従業員に納得してもらった上で進めるようにしましょう。
不具合やトラブルに対する対応が必要
省人化を進める上で機械を取り入れる場合、突発的に不具合が発生したり、予期せぬトラブルが発生したりすることも考えられます。このような不具合やトラブルに適切に対応をする必要があることを理解しておきましょう。
適切な対応方法を整理し、担当者を決めておかないと迅速に対応することができず、作業全体が停滞するリスクも考えられます。なお、不具合やトラブルへの対応などの作業は専門的なため、業務が属人化しやすい傾向があります。
このような属人化しやすい作業手順は、OJTや業務マニュアルによる共有ではなく、視覚的に動作を伝えられる「動画マニュアル」を活用するのが効果的な手段の1つです。
以下の資料では、動画マニュアルの有効性について、業務の属人化が起きやすい製造業を例に、活用事例をご紹介しています。省人化・省力化の壁となる、属人的な業務の解消を実現するヒントとしてご活用ください。
>>省人化・省力化の壁となる課題を解消できる「動画マニュアルの有効性」を事例で学ぶ
省人化・省力化を実現する具体的な方法
ここでは省人化・省力化に取り組む上での具体的な方法について紹介していきます。
既存の業務プロセスの見直し・改善
既存の業務プロセスを見直し、ムダな作業やプロセスがないかを見直して改善するだけでも効果を得られます。
人が行っている作業のどの部分を省人化・省力化できるのか、一つ一つの業務を分解して評価しましょう。見直し・評価を進める中で、これまでに表面化していなかった不要な業務が見えてくるはずです。
AI・Iot・ロボットによる自動化
AI・Iot・ロボットなどの技術を取り入れることで、人の手が必要な作業が削減されるため、作業の効率化や自動化が実現します。ルーティンワークなどの簡易的な作業だけではなく、様々な作業を自動化する革新的なツールやロボットが提供されています。
これらの技術を駆使することによって、省人化・省力化が見込めるでしょう。なお、技術は取り入れることが目的になることは少なくないので、導入によってどのような効果が得られるのか、どの程度の費用がかかるのかなど、様々な要素を加味した上で検討するのが重要です。
業務の標準化を進める
業務の効率化を進めるうえでは、作業の標準化は欠かせない要素の1つです。標準化されていない場合、業務の属人化や品質のバラつきなどが発生してしまい、品質不良や生産性の低下につながります。
一気に標準化を進めるのは難易度が高いため、作業ごとに細かく分割して、どの業務を標準化するべきかを検討しましょう。なお、業務を標準化するうえでは、マニュアルの動画化が有効です。マニュアルを動画化することで省人化・省力化につながる理由について、おすすめのツールと併せて紹介していきます。
省人化・省力化に向けた動画マニュアルの作成は「tebiki現場教育」
省人化・省力化を進めるうえでは、マニュアルを動画で作成できるツールの活用がおすすめです。作業風景を録画し、編集することで従業員の理解度を一定の水準まで引き上げることができ、作業の標準化がすすみます。なお、「tebiki現場教育」は、カンタンな操作性で動画マニュアルを作成できます。
専門性が高い作業を「動き」で学べる
「tebiki現場教育」は、文章では伝わりにくい専門性の高い操作や動きを視覚的に学ぶことができます。動画内に、正しい作業を◯、NGな作業に×を挿入でき、OK例とNG例を視覚的に表現することが可能です。
省人化を進めるうえでは、人の作業を見直して効率化することが重要なので、動画マニュアルを通じて全ての従業員が正しく作業内容を理解できれば、作業の効率化にも繋がります。
多能工化の推進で省人化・省力化が進む
紙のマニュアルとは違い、動画マニュアルは視聴する側に負担がかからず、デバイスがあれば作業の合間や就業後の空き時間に気軽に視聴できます。
自主的に学習する教育体制を構築できるため、学びが促進されて全ての従業員の習熟度を一定のレベルまで引き上げ、多能工化にもつながるでしょう。多能工化によって一人一人の作業効率が上がることにより、省人化にもつながるはずです。
「tebiki現場教育」の詳細を知りたい方は、特徴や機能を詳しく解説している「3分で分かる『tebikiサービス資料』」をご覧ください。
省人化・省力化を理解して業務改善にいかそう!【まとめ】
省人化・省力化は少子高齢化・労働力不足などの様々な社会問題を抱えている現代において、欠かせない取り組みの1つです。業務効率化や生産性の向上にもつながるため、積極的に推進する必要があるでしょう。
なお、様々なメリットがある一方で、コストがかかる・従業員からの理解を得る必要があるなどの注意点があるのも事実です。幅広い視野を持った上で、省人化・省力化に取り組む必要があると言えます。
省力化・省人化を進めるコツや現場への負担をかけずに推進する方法を知りたいなどの疑問を抱えている方に向けて、専門家による解説動画を用意しています。無料で視聴できるので、以下の画像をクリックして、動画を視聴してください。