かんたん動画マニュアル作成「tebiki現場教育」や、かんたんデジタル現場帳票「tebiki現場分析」を展開する現場改善ラボ編集部です。
歩留まり(ぶどまり)とは、生産量に対する完成品の割合を示す言葉です。主に製造現場で、製造原価の抑制や生産性向上のために指標として用いられます。ビジネスシーンでは、採用活動における応募数に対する採用数/採用率、Webセミナーの申込数に対する参加数/参加率といった比率を確認する際に使用します。
製造現場の場合、歩留まりを計算することで原材料といった製造コストのムダを把握できます。その原因を洗い出し、改善策を講じることで効率的な生産が期待できます。
本記事では歩留まりの意味や歩留まり率の計算方法、製造業で歩留まりが悪化する要因や改善手法について解説します。
目次
歩留まり/歩留まり率とは?計算方法や重要性を解説
製造業における歩留まりとは、原材料や素材など原料の使用量に対する完成品の割合のことを指します。
歩留まり率とは、歩留まりを百分率で示した数値のことです。たとえば、100kgのステンレス板をプレス加工して80kgの製品が完成した場合の歩留まり率は80%となります。
歩留まり率は、製造業の製品開発や生産管理において重要な指標です。
製品価格の見積もり、材料の発注量の計算などに歩留まり率の把握が欠かせません。生産効率や粗利率の向上に取り組む際も、現状の歩留まり率について知っておく必要があります。
まずは歩留まりの計算方法や、歩留まり率に関係するその他の指標について説明します。
歩留まり/歩留まり率の計算方法
歩留まり率の計算方法は以下の通りです。
【歩留まり率の計算式】
完成品数÷原材料数×100=歩留まり率(%)
歩留まり率が高い場合、原材料のロスが少なく効率的に生産できている良い状態だといえます。基本的に、完成品は良品のことを指しますが、不良品を含む場合もあります。
ただし、業種によっては歩留まり率の分子を完成品数ではなく良品数としていることもあります。
『良品率や直行率と何が違う?』歩留まり率と似た言葉との違い
歩留まり率と混同される用語に「良品率」や「直行率」があります。それぞれ以下のような違いがあります。
- 歩留まり率:原料から完成品(良品)をどれほど製造しているかの割合
- 良品率:不良品を含むすべての完成品のうち、一定の品質基準を満たしている製品の割合
- 直行率:不良品を含むすべての完成品のうち、一度の工程で良品になった製品の割合
良品率の意味と計算式
完成品のうち、手直し済み良品(再格付品)と手直しをしていない良品を足したものの割合が「良品率」です。手直しをして、良品になった製品のことを再格付品、手直しをしても品質上の基準を満たさない製品を不良品と呼びます。
【良品率の計算式】
良品数÷完成品数×100=良品率(%)
80個の完成品のうち、良品が60個(うち再格付品は10個)だった場合の良品率は75%です。製造業の現場では「そのままでは不良品になるけれど、バリ取りをすれば良品になる」というように、手直しによって良品にカウントできるものもあります。
直行率の意味と計算式
完成品のうち、手直しを経ずに良品にカウントできる製品の割合を示すのが「直行率」です。
【直行率の計算式】
手直しせずに良品になる製品の数÷完成品×100=直行率(%)
80個の完成品のうち手直し不要な製品が78個だった場合の直行率は97.5%となります。直行率を向上させることは、歩留まり率の改善以外にも品質向上や生産性向上のために重要な施策だといえます。
歩留まりが重要な理由
製造業において歩留まりは重要な指標の1つです。
歩留まりは、原材料をどれほど効率的に利用できているかを定量的に表すため、歩留まり率の値が製造コストや製品の収益性といった要素に直接影響します。現状の歩留まり状況を踏まえて、原材料の発注量や生産計画の検討などを決める指標にもなります。
また歩留まり率が低い場合、現場の生産効率が悪い/品質トラブルが潜んでいるといった問題の可視化するきっかけにもなるでしょう。歩留まりの状況で生産工程の課題を見つけ、適切な改善策を講じることで歩留まり率や良品率、直行率の向上による生産効率の向上が期待できます。
このように製造業における歩留まりは、生産計画の検討から生産効率、製造コストや収益性に影響を与える点で重要な要素といえるでしょう。
適正な歩留まり率の平均値とは?
歩留まりについて調べている方の中には『歩留まり率の一般的な指標を知りたい』という方もいるでしょう。
しかし適正な歩留まり率は、一概に算出することはできません。なぜなら、歩留まり率は製品の形状や材料、加工方法によって異なるからです。
具体的な解説は後述しますが、自社における適切な歩留まり率は以下の視点から検討し、定期的に見直しを行う形がよいでしょう。
- 過去、最も生産効率がよかった時期の数値を目標に設定する
- 顧客の要求品質や納期が達成できる歩留まり率を求める
- 原材料やリードタイムなど製造コストに見合う歩留まり率を求める など
加工方法によって異なる歩留まり率
たとえば金属抜き型のプレス製品や切削品は、原材料を切ったり削ったりして製造しているため、歩留まり率は低い傾向にあります。
一方で、樹脂ペレットを射出成形機に投入して成型する樹脂製品や金属を折り曲げる板金加工の歩留まり率は高くなります。金属や樹脂を金型に流し込んで成型する鋳造品も歩留まり率は高い傾向です。
このように同じ姿の完成品であっても、製造方法によって歩留まり率は変わります。
たとえば「ネジ」を製造する場合、切削加工であれば、歩留まり率は45%から50%ですが、冷間鋳造であれば90%以上の歩留まり率も実現可能です。しかしながら、冷間鋳造には製品ごとに金型が必要となりますので、冷間鋳造を選択したからといってすぐさま製造原価が減少するわけではありません。
不良品が歩留まり率に与える影響
歩留まり率を「良品数÷原材料数」で算出する場合は、加工機への材料残りや切削によるロスの発生に加えて、不良品が歩留まり率を悪化させます。
たとえば樹脂成形品における「完成品数÷原材料数」で算出した歩留まり率が90%であった場合、原材料数が1000だった場合は完成品数は900となります。この製品の良品率が90%の場合の良品数は810です。したがって「良品数÷原材料数×100=歩留まり率(%)」の式に当てはめると、歩留まり率は「810÷1000×100=81%」となります。
製造過程で止む無く生じるロスの減少は容易ではありません。
しかし、不良品の発生は作業標準の策定や人材育成、スキルの向上といった施策によって抑制可能です。したがって、歩留まり率の適正化の第一歩は不良品の減少にあるといえます。
歩留まり悪化の2大要因は「不良品の発生」と「材料ロス」
歩留まり率を直接的に低下させる要因は、大きく以下の2つに分類できます。
1つは「不良品の発生」です。これは、投入した材料から製品を加工する過程で何らかの欠陥が生じ、最終的に良品としてカウントできない製品が増えてしまっているケースを指します。
もう1つは「材料ロス」です。これは、製品として完成する以前の段階で、材料そのものが無駄になってしまうケースを指します。
では、「不良品の発生」と「材料ロス」は具体的にどのような原因によって引き起こされているのでしょうか?
「不良品の発生」の原因:「5M+1E」で探る
不良品の発生原因を特定するには、製造プロセスを構成する各要素を網羅的に検証しましょう。その際に広く用いられるのが、「5M+1E」という品質管理のフレームワークです。
- Man(人)
- Machine(機械)
- Material(材料)
- Method(方法)
- Measurement(検査・測定)
- Environment(環境)
これらの頭文字を取ったものです。これらの観点から不良の根本原因を探ります。それぞれの分析観点をここから解説しますが、5Mについて別途理解を深めたい方は、以下の記事もあわせて参考にしてみてください。
関連記事:【分析例も紹介】「5M」とは?活用して製造現場を管理する方法
Man(人的要因):作業者
人的要因とは、作業者のスキル、行動、意識に関連する問題点を指します。主な要素は以下の通りです。
- スキル不足・習熟度のバラつき
- ヒューマンエラー(手順誤り、確認漏れ、誤判断、不注意など)
- 作業標準の不遵守・形骸化
- モチベーションの低下
特に、新人作業員や経験の浅い作業者による作業は、不良を発生させやすい代表的な要因の1つです。例えば、作業者の感覚や経験・カンコツに頼る部分が多い工程では、作業者間のスキル差がそのまま製品品質のバラつきに直結し、歩留まりに影響を与えます。
また、手順の誤りや確認漏れといったヒューマンエラー(人為的ミス)は、不良発生の直接的な原因となります。
ヒューマンエラーによる不良の発生は「仕方ない」と割り切られがちで、多くの製造現場が抱える根深い課題ですが、現場の仕組みづくり次第で未然防止が可能です。ヒューマンエラーがなぜ起こるのか、そのメカニズムと具体的な未然防止策について書かれた資料があるので、下の画像をクリックしてご覧ください。
Machine(設備要因):機械・設備
機械や設備に起因する問題も、不良発生の大きな原因となります。主な要素は以下の通りです。
- 設備の老朽化・精度劣化
- メンテナンス不足(予防保全・予知保全の不備)
- 治工具の摩耗・不備
長期間にわたる設備の使用は、部品の摩耗や劣化を引き起こし、設備の加工精度や動作安定性を低下させることがあります。これが、製品の寸法不良や外観不良などを生み出す原因となります。
それだけでなく、製品の品質を安定させるために使用する治具や工具が摩耗していたり、そもそも設計や選定が不適切であったりすると、加工精度の低下や作業ミスを誘発し、不良の原因となります。
設備の安定稼働は、高品質な製品を効率的に生産するための大前提です。設備トラブルによる生産性の低下を防ぎ、予防保全・予知保全を推進するための「設備保全のDX」について解説した資料も、現場の課題解決のヒントになるかもしれません。
下のリンクをクリックすると、資料のダウンロードが可能です。
>>>「製造業の設備トラブルによる生産性低下を解消する設備保全のDX」を見てみる
Material(材料要因):原材料・部品
使用する原材料や部品の品質も、歩留まりに影響を与えます。例えば以下のような要素です。
- 材料品質のバラつき
- 不適切な材料選定
仕入れ先から納入される材料の品質が、ロットごと、あるいは納入時期によって不安定である場合、後工程での加工条件の調整が難しくなり、不良発生のリスクが高まります。
また、製品に求められる要求品質や加工方法に対して、そもそも使用している材料の選定がミスマッチである場合も、品質不良の原因となり得ます。
そもそもの原材料や部品が問題ないかどうか、あわせてチェックしてみてください。
Method(方法要因):作業方法・工程設計
作業のやり方や工程の設計に問題がある場合も、不良の温床となります。主な要素は以下の通りです。
- 作業標準書の不備(分かりにくい、最新でない、存在しない)
- 非効率な工程設計、無理な加工条件
- 変化点管理の不徹底(4M変更時の対応不備)
特に、作業手順が明確に定められていない、内容が古く現状の作業と合致していない、あるいは作業者にとって分かりにくい手順書では、作業の標準化が進まずバラつきが生じ、不良が発生しやすくなります。
例えば化学メーカーの児玉化学工業株式会社は、技術の言語化が難しい作業が複数あり、かつ外国人労働者が混在する現場であることから、作業手順の教育が難しくたびたび品質不良が発生していました。
そこで動画マニュアルによる教育体制を整備し、正しい作業手順の浸透を実現しています。以下は、同社で実際に作成された動画マニュアルのサンプルです。
▼「ヤスリでバリをとる」動画マニュアル▼
※現場従業員が「tebiki」で作成
このような複雑な業務作業も、動画で手順をおさめれば「誰が見ても同じ解釈」になるので、外国人労働者も含め、正しい作業方法で進められるようになります。
製造業では動画マニュアルによる教育が進んでおり、多くの事例があります。詳しくは「製造業における動画マニュアル活用事例集」でご覧いただけるので、他社の製造業が動画マニュアルを通じてどのように現場教育を改善しているのか、参考にしてみてください。
Measurement(検査・測定要因):検査方法・測定機器
製品が規格を満たしているかを確認する検査や測定のプロセスも、不良を見逃したり、誤った判断を下したりする原因となり得ます。そうすると、歩留まりの低下につながります。
主な要素は以下の通りです。
- 検査基準の曖昧さ・不統一
- 検査方法・測定方法の不備
- 測定器の精度不良・校正不備
特に、良品と不良品を判定する基準が明確でなかったり、検査員によって解釈が異なったりすると、良品を誤って不良と判定したり、逆に不良品を見逃して後工程や市場に流出させてしまう可能性があります。
製造業における品質検査は、検査基準や作業手順のバラつきによる課題が多く潜んでおり、多くの現場で問題視されています。課題解決の具体的な検査方法について学びを深めたい方は、PDF資料「製造業の品質不良を未然防止する次世代の品質検査」もあわせてご覧ください(下の画像をクリック)。
Environment(環境要因):作業環境
作業を行う環境も、間接的あるいは直接的に製品品質に影響を与え、不良の原因となることがあります。例えば温湿度、照度、清浄度、騒音、振動などが挙げられます。
こうした要素が適切に管理されていない場合、作業者の集中力低下を招いてヒューマンエラーを誘発したり、製品品質に直接悪影響を与えたりすることがあります。
「材料ロス」になりうる原因の一覧
歩留まり悪化のもう1つの大きな柱である「材料ロス」は、不良品としてカウントされる以前に、製品にならずに廃棄されてしまう材料の無駄を指します。
これらは日常的に発生しているため、「仕方のないもの」として見過ごされがちですが、意識して削減に取り組める余地があります。
設計起因のロス
製品設計そのものが、材料ロスを生みやすい構造になっている場合があります。主な要素は以下の通りです。
- 歩留まりを考慮しない製品設計
- 材料取り効率の悪い設計
こうした設計を改めて見直し、歩留まりに悪影響を及ぼすポイントがないかどうかを確認するのも手です。
例えば部品の配置(ネスティング)が悪く、抜きカスや端材が多く発生するような設計は材料ロスに直結し、歩留まり率の低下を引き起こします。
工程起因のロス
製造工程の特性や設定が原因で生じる材料の無駄です。「仕方ない」と見過ごされがちですが、改善の余地はあります。
例えば、必要以上に材料を削り取る「加工しろの過多」、プレス加工で出る「抜きカス」、樹脂成形の「ランナー」や「バリ」、塗装時に製品に付着しなかった塗料などが代表的です。
これらは、金型設計の工夫、加工条件の最適化、塗装方法の見直しなどで削減でき、歩留まり向上につながります。
作業起因のロス
作業者の行動や管理方法に起因する、比較的防ぎやすい材料ロスです。主な要素は以下の通りです。
- 材料の誤投入、過剰投入
- 段取り替え時の材料ロス
- 有効期限切れによる材料廃棄
特に、5S(整理・整頓・清掃・清潔・躾)の徹底や、適切な運搬・保管によって防げるロスは改善の余地があります。例えば仕掛品が、油やゴミで汚れ、使用できなくなるようなケースです。
5Sの各要素で具体的にどのような活動をするのか、活動内容も詳しく知りたい方は、数々の職場で5S改革を行ってきた専門家が解説する以下のセミナー動画もご覧ください。
>>>セミナー動画「生産性を高める5S活動 正しい運用に欠かせない『重要なS】とは」を見てみる
また、先入れ先出しの管理が徹底されていなかったり、需要予測の誤りから過剰な在庫を持っていたりすることで、材料が使用期限を過ぎてしまい、やむなく廃棄されるケースも、防ぐべき材料ロスです。
【改善事例あり】歩留まり改善のための具体的な対策
歩留まりの原因は「不良品削減」と「材料ロス削減」の2つの視点で分析できることを解説しました。そこでここからは、それぞれの視点における歩留まりの改善策について紹介します。
生産状況のリアルタイム可視化とKPIモニタリング
歩留まり改善を進める上で、「今、現場で何が起きているのか」を正確かつリアルタイムに把握することは不可欠です。しかし、多くの現場では、生産数、不良数、設備稼働状況などのデータが紙の日報やExcelに記録され、集計や分析に時間がかかったり、情報が古くなったりしがちです。
このような課題を解決するのが、現場帳票のデジタル化です。タブレット等を用いて現場で直接データを入力・記録し、それらが自動的に集計・グラフ化される仕組みを導入することで、以下のようなメリットが生まれます。
リアルタイムでの状況把握 | 歩留まり率、不良発生状況、設備稼働率などをダッシュボード等でいつでも確認でき、異常の早期発見に繋がります。 |
データ収集・集計工数の削減 | 手書きや転記、Excelへの入力といった手間がなくなり、現場担当者は本来の改善活動により多くの時間を割けます。 |
データに基づいた意思決定 | 客観的なデータに基づいて問題の原因を分析し、データに基づいた対策を迅速に打つことが可能になります。 |
KPIモニタリングの効率化 | 設定した歩留まり目標(KPI)に対する実績を容易に追跡でき、目標達成に向けた進捗管理が効率化します。関係者間での情報共有もスムーズになります。 |
このように、生産状況のリアルタイムな「見える化」は歩留まり改善の「基盤」と言えます。
例えば株式会社日本電気化学工業所(NACL)は、紙ベースの帳票管理ではデータ管理や記録がままならず、現場の状況をリアルタイムで把握することができていませんでした。
そこで、現場帳票をデジタル化(tebiki現場分析)し、データのリアルタイム監視を可能にしました。例えば、ダッシュボードで設備の温度データを定点観測できるようにし、通常パターンとは異なる挙動を早期発見し、品質不良の早期発見と未然防止を実現したのです。
▼同社の改善事例▼
紙やExcelによる現場帳票の運用に課題を感じ、「現場帳票のデジタル化」による改善効果や具体的な進め方について詳しく知りたい方は、以下の資料がおすすめです。現場帳票を電子化するメリットや費用対効果の考え方等がまとめられているので、あわせて参考にしてみてください。
作業標準化の徹底と改善
不良やロスの多くは、作業のバラつきや手順の不遵守から生じます。「誰が作業しても常に同じ品質・効率で作業できる」状態を目指し、作業標準書を作成・見直しすることが基本です。
手順、使用工具、品質基準、異常時処置などを具体的かつ明確に定め、曖昧な表現や個人の「カンコツ」への依存を排除しましょう。
標準化の実現には、「正しい作業手順(ロスが生まれない手順)が、一目で分かるマニュアル」の整備が鍵を握ります。そこで、製造業を中心に多く導入されているのが「動画マニュアル」です。
実際に製造業で活用されている動画マニュアルの例を以下に掲載します。こちらは「児玉化学工業株式会社」が作成した「バリの取り方」を動画マニュアル化したものです。文字や紙のマニュアルでは伝えにくい技術や手順も、動画であれば一目で理解可能です。
▼標準化を浸透する動画マニュアルの例▼
※「tebiki」で作成
不良やロスが生じないための正しい作業手順を動画におさめることで、歩留まりの改善につながります。動画マニュアル作成ツールtebikiについて少しでも気になる方はサービス資料もあわせて参考にしてみてください。動画マニュアルの導入事例や活用イメージが掲載されています。
>>>歩留まりを改善する動画マニュアル作成ツール「tebiki現場教育」のサービス資料を見る
設備・治工具の維持管理と改善
設備の安定稼働は、高品質な製品を効率的に生産するための大前提です。故障してから対応するのではなく、日常点検や定期メンテナンスを徹底し、計画的な予防保全や、センサーなどを活用した予知保全に取り組みましょう。
ただし、保全業務は実施のタイミングが比較的限られることから、保全業務スキルがなかなか現場全体で浸透せず、属人化する傾向にあります。
そこで、資料「製造業の設備トラブルによる生産性低下を解消する設備保全のDX」では、保全業務を形式知化し、標準化を進めるための具体的な方法について解説されています。下のリンクをクリックして、本資料もあわせて参考にしてみてください。
>>>資料「製造業の設備トラブルによる生産性低下を解消する設備保全のDX」を見てみる
ポカヨケ(フールプルーフ)によるヒューマンエラー防止
人間の注意力には限界があり、「うっかりミス」は誰にでも起こり得ます。こうしたヒューマンエラーを根本的に防ぐためには、注意喚起だけでなく、そもそもミスが起こらないような仕組み、あるいはミスが起きても不良に繋がらないような物理的・システム的な工夫(ポカヨケ)を導入することが重要です。
ヒューマンエラーによる不良の発生は「仕方ない」と割り切られがちで、多くの製造現場が抱える根深い課題ですが、現場の仕組みづくり次第で未然防止が可能です。ヒューマンエラーがなぜ起こるのか、そのメカニズムと具体的な未然防止策について書かれた資料があるので、下の画像をクリックしてご覧ください。
変化点管理の徹底
人・設備・材料・方法(4M)などに変更があった場合(変化点)、予期せぬ品質問題を引き起こす可能性があります。
※変化点管理の詳細は、下の関連記事でもまとめられています。
関連記事:【変化を見える化】変化点管理の4ステップと好事例。トヨタ流のポイントも解説
変更内容、理由、リスク評価、事前検証、関係者への周知、変更後の効果確認といった一連のプロセスをルール化した「変化点管理」を確立し、それを厳格に遵守することで、変更に伴うトラブルを未然に防ぎ、安定した生産を維持しましょう。
ただいま公開中のセミナー動画「トヨタ流品質管理に学ぶ!はじめての変化点管理」では、変化点管理の具体的な実践方法について解説しているので、あわせてご覧ください(下の画像をクリック)。
小集団活動による現場改善力の向上
トップダウンの指示だけでなく、現場の作業者が主体となって自分たちの職場の問題点を見つけ出し、知恵を出し合って改善に取り組む「小集団活動(QCサークル活動など)」は、歩留まり改善においても非常に有効です。
QCサークル活動の具体的な実践方法や進め方について知りたい方は、専門家が解説しているセミナー動画「QCサークル活動を成功に導く5つのポイントとは?」もあわせてご覧ください(下の画像をクリック)。品質改善に直結する実践的なヒントが得られるはずです。
歩留まり向上を目的とした業務標準化には動画マニュアルが効果あり
歩留まり改善には「作業手順や設計ルール、社内ルールを徹底的に標準化させ、業務のムリムダムラを取り除いていくアプローチ」が必要です。
ヒューマンエラーを減らしていくような業務標準化こそ、短期的に効果を出しやすく設備投資等の大きなコストもかからない改善策といえるでしょう。
一方で従来のように、作業手順書の整備やOJTによる教育を行っていても標準化が進みにくいというケースは少なくありません。
本章では業務標準化を推進するための従業員教育に「動画マニュアル」を活用する方法をご紹介します。どのような効果があるのか?実際の活用事例も交えて詳しく見ていきましょう。
動画マニュアルを使うメリットと効果
動画マニュアルのメリットは、現場作業の様子が文章よりも鮮明に伝えられることです。
文字や写真ベースの作業手順書、OJT等の口頭では、作業の流れや絶妙なカンコツは理解しにくいです。動画マニュアルであれば、動きを視覚的にわかりやすく理解することができ、作業者にとって初めての業務でも視覚的な理解が可能です。
また、視覚的に伝えることができるため、外国籍の従業員に対しても視覚的に業務標準を伝えることが期待できます。文字や口頭で課題になる言葉の壁を打破する手段としてお使いいただけます。
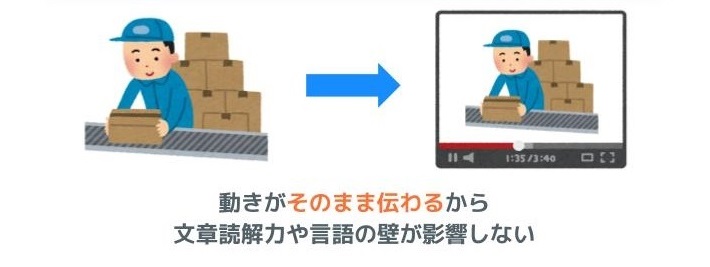
誰でもかんたんに動画マニュアルが作成できる「tebiki」とは?
動画マニュアルと聞くと『編集作業が難しいのでは?』と感じるかもしれません。
そこで動画編集未経験者でも、数多くの動画マニュアル作成を行っている実績がある現場教育システム「tebiki」をご紹介します。tebikiは製造業を中心とした現場産業において、業務ノウハウをわかりやすく伝えられない/教育担当者に負荷が集中するといった教育課題を解決するツールとして活用されています。
tebikiは、スマートフォンなど身近なデバイスで作業風景を撮影するだけで、誰でもかんたんに動画マニュアルの作成が可能です。その容易さから、従来の紙マニュアルや手順書作成と比較しても短時間で作成できている事例が多数あります。
作成した動画マニュアルの字幕は、100ヵ国語以上の言語に翻訳が可能です。そのため多国籍の従業員を抱える現場では、それぞれの従業員が母国語で作業手順や社内ルールを学べる環境を構築することができます。
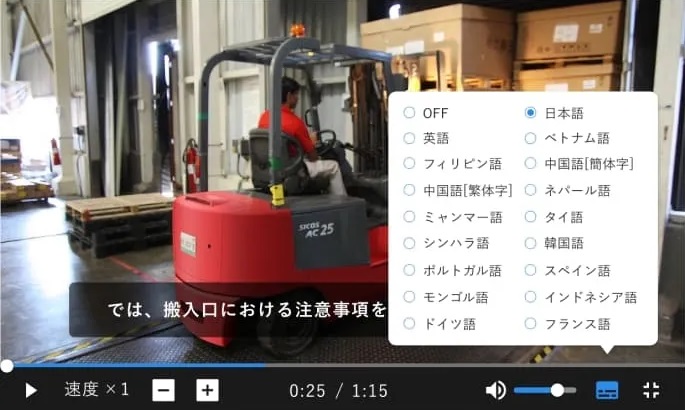
tebikiで作成した動画マニュアルで業務標準を伝えることで、歩留まりの原因となるヒューマンエラーや作業不遵守を改善することが期待できます。
現場教育システム「tebiki」に関する具体的な機能紹介やプランについては、以下の資料よりご覧いただけます。
動画マニュアルで業務標準化の推進/品質を向上させた事例
実際に動画マニュアルを活用した教育によって、製造現場の業務標準化や品質向上につながった事例を2社ご紹介します。
より多くの動画マニュアル活用事例を見たい方は、製造業における活用事例を凝縮した以下の参考資料も併せてご覧ください。
大同工業株式会社
大同工業株式会社は、バイクチェーンや自動車エンジン用チェーン、産業機械チェーン、コンベヤシステム、福祉機器を提供している企業です。
大同工業株式会社はOJT教育の際、トレーナーによって指導にバラつきがあるという問題を抱えていました。結果として我流化になっていき、試験におけるヒヤリハットが発生したり、評価結果のエラーによる再試験などの手戻りの一因になっていました。また、手順書の作成に工数がかかっていることも課題にありました。
そこで、大同工業株式会社は動画マニュアルtebikiを導入しました。導入により、試験手順の小さな違いがヒヤリハットや評価結果のエラーを引き起こしていた問題を解消し、ヒヤリハットの8割削減に成功しました。
また、マニュアル作成に2時間以上かかっていたものが1時間以下にできるよう作成時間削減にも成功しました。
大同工業株式会社がtebikiを導入し、現場改善に成功している様子は以下のインタビュー記事で詳しく解説しています。あわせてご覧ください。
インタビュー記事:製造業の技術部門の業務を動画で標準化。 教育工数を8割削減し、業務の効率化・最適化も実現。
サラヤ株式会社
サラヤ株式会社は、消毒剤や洗浄剤、医薬品、食品を製造する化学・日用品メーカーです。
サラヤ株式会社では、従来紙のマニュアルを使用して教育を行っていましたが、紙のマニュアルでは微妙なニュアンスや作業工程の詳細が伝わりにくいという課題がありました。
そこでサラヤ株式会社は動画マニュアルtebikiを導入しました。tebikiの導入により、紙のマニュアルがタブレットに置き換わり、作業者は動画を通じて具体的な作業工程や注意点を確認できるようになりました。tebikiは、作業のニュアンスや機械の動き、音など紙では伝えられない情報を効果的に伝えることが可能です。
またtebikiの導入により、サラヤは複数の拠点で400個以上のマニュアルを作成し、作業品質の改善を実現しました。作業者の力量が均一化され、安全性も向上しました。
サラヤ株式会社がtebikiを導入し、現場改善に成功している様子は以下のインタビュー記事で詳しく解説しています。あわせてご覧ください。
インタビュー記事:消毒剤のトップシェアメーカーでtebikiを活用。 半年で400動画作成!世界の「衛生・環境・健康」に貢献!
まとめ:「不良品発生」と「材料ロス」対策のうち、できることから着手
本記事では、製造業における歩留まり悪化の原因と、その具体的な改善アプローチについて解説しました。歩留まり低下は「不良品発生」と「材料ロス」が主な原因なので、これらを改善するための対策が重要になります。
具体的な対策としては、データのリアルタイム計測や作業標準化、教育訓練の質の向上、設備管理の徹底、変化点管理などが挙げられます。
そのための有効手段として、動画マニュアルによる分かりやすい手順の共有や、現場帳票のデジタル化による生産状況のリアルタイムな可視化とデータ活用が非常に有効であることもお伝えしました。もし少しでも動画マニュアルや現場帳票のデジタル化を検討される場合は、これらのサービス資料もあわせてチェックしてみてください(下の画像をクリック)。