かんたん動画マニュアル作成「tebiki現場教育」を展開する現場改善ラボ編集部です。
5S活動とは、整理・整頓・清掃・清潔・躾の5つで構成される取り組みで、トヨタから生まれたとされる職場環境の改善手法です。現場の効率を高め、生産性を向上させるうえで重要な役割を持っています。
本記事では5S活動の基本から具体的な実践方法、効果について詳しく解説します。
目次
5S活動とは。具体的に何をする?
5Sとは、整理/整頓/清掃/清潔/躾(しつけ)の頭文字を取った用語で、職場環境や業務を改善し、生産性を向上させるための活動です。
ここからは、以下の5Sの要素の概要などを解説します。
5Sを生産性向上などにつなげるための具体的なアクションについて知りたい方は、以下のリンクから専門家による「5Sの正しい進め方」の解説動画をご覧ください。
整理
「整理」とは、作業に必要なものと不要なものを分け、不要なものを処分することです。
整理をすることで作業の必要なものが明確になります。必要なもの整理をすることで、的確でムダのない仕事ができるようになります。「もの」というのは作業道具や作業スペースだけに限らず、作業手順や業務内容など物質として存在しないものも対象です。
整理に該当する主な取り組み例は以下の通りです。
- 作業台には作業に必要なものだけを置いておく
- 個人で物を持たず、共有化する
- 紙ベースの資料は電子データに変換して、保管スペースを減らす
- 作業手順でムダで不要な動きを取り除く
このように必要なものと不要なものを整理し、不要なものを取り除く動きを、職場の共通認識とする活動が整理です。
整頓
「整頓」とは、必要なものを使いやすくして、誰でも分かりやすい状態にすることです。
整理の段階で、必要なものを職場の共通認識としたとしても、それが使いにくい/分かりにくい状態であれば整理の効果は発揮できません。整理による効果を引き出すために、必要なものを使いやすく分かりやすい状態に整頓します。
整頓に該当する主な取り組み例は以下の通りです。
- 資料や備品の置き場所を決める
- よく使うものを近くに置き作業をする
- 道具を色分けして配置し、区別しやすくする
このように、必要なものを必要なときにすぐ使える効率的な状態にする活動が整頓です。
清掃
「清掃」とは、作業現場やデスク周りなどの掃除や点検/メンテナンスを行うことです。
清掃には「綺麗にする」という意味が先行しやすいですが、清掃と同時に点検/メンテナンスも行うことが5Sの清掃では大切です。これにより、きれいな状態維持と不具合発生を未然に防げます。
清掃に該当する主な取り組み例は以下の通りです。
- 作業が終わったあとは掃除をする
- 清掃道具を誰でも使える状態にしておく
- 点検項目も共通認識化しておく
2024年に冷凍麺世界売上No.1となった株式会社テーブルマークでは、言語や文化の違いから、外国人従業員へ「ごみの分別方法」が伝わらないという課題を抱えていました。そこで構内ルールを動画マニュアル化することで、ごみ捨てをはじめとした清掃方法が標準化でき、ルールが守られるようになりました。
このように5Sのルールを守るには、動画の活用が効果的です。テーブルマークの動画マニュアル活用事例については、以下のインタビュー記事も併せてご覧ください。
インタビュー記事:属人化業務の指導工数を83%削減!標準化教育により安心安全な食品を提供
清潔
「清潔」は整理・整頓・清掃を定期的に行い、清潔な状態を維持することです。言い換えると、整理・整頓・清掃が行き届いた状態を「標準化」するための活動が清潔です。
清潔に該当する主な取り組みは以下の通りです。
- 清潔の判断基準など共通認識を決めておく
- 清掃をルーティン化する
- 責任者や管理者などを決め、定着するまで確認する
このように、整理/整頓/清掃の3Sにあたる要素を継続させる仕組みを整える活動が清潔です。
躾(しつけ)
「躾(しつけ)」とは、整理/整頓/清掃/清潔の4Sを習慣づけ、職場環境の改善サイクルを維持する活動です。
躾ができていなければ、現場の改善サイクルが失われ、結果的に4Sの活動内容も形骸化してしまうため、最も大切な要素といえます。5S活動成功の鍵を握る躾の秘訣については、後述する『5S活動の効果を最大化させる「躾」のコツ』をご覧ください。
躾に該当する主な取り組みは以下の通りです。
- 5S活動の目的を周知させる
- ルールを定期的に見直し、改善する
- 5Sに関するルールをマニュアル化する
このように、5S活動全体で決められたルールや標準を習慣化させるための活動が躾です。
5Sの各要素ですぐに現場でマネできる実践的な活動例は、以下の専門家による解説動画でご覧いただけます。5Sを定着させるポイントも講演しているので、ぜひ記事と併せてご覧ください。
単なる片付けではない!5S活動の目的や効果
5Sの概要だけを見ると「職場の片付けができていればいいのでは?」というように感じるかもしれません。
しかし5S活動の本質的な目的は、職場を綺麗にすることではありません。
5S活動は、さまざまな職場改善を目的に実施されます。ここでは、5S活動で代表的な3つの目的と効果を詳しく解説します。
このような「現場改善効果を出す5S活動の進め方」については、以下のリンクをクリックして専門家による解説動画をご覧ください。
3Mの排除による効率化と標準化の推進
5S活動には、業務における3M(ムリ・ムダ・ムラ)を排除し、作業が効率的に行われ、ムダな動きや時間が排除されている状態が実現するという効果があります。さらに工程を見直しシンプルな手順にできると、誰でも一定の業務品質で作業ができる業務標準化も推進できます。
業務が標準化されることで、業務品質のバラつきやミス、ヒューマンエラーが起こりにくくなり、製品の品質や生産性を高める効果が期待できます。
「3Mを見つける視点」については、専門家による以下の解説動画も併せてご覧ください。
>>【視聴無料】専門家が解説する「3M(ムリムダムラ)の視点と改善」の方法を見る
生産性や品質の向上
5S活動が進むと、以下のような現場での変化が起こるため、生産性や品質向上に寄与すると考えられます。
- 作業スペースが確保される
- 動線が最適化される
- 探し物時間が短縮される
- 作業時間が効率化される
- 設備の故障予防につながる
- 不良品の発生が抑制される
一方で、生産性や効率を重視するあまり、従業員の安全が脅かされる場合があります。現場の安全に関わる部分には、過度な生産性や効率性を求めないようにバランスよく活動することが必要です。
▼関連記事▼
・製造業の生産性を向上させる4ステップとは?生産性の指標や計算式の求め方も紹介!
・【品質改善】製造業の品質向上策9選!改善事例も解説
労働災害など安全トラブルの未然防止
整理/整頓/清掃で業務に不要なものを取り除くことで、製造業で特に多い挟まれや転倒の防止といった労働災害対策につながります。
また、5Sを日常的に行うことで、作業環境や機械における異常の早期発見にもつながります。そのため、潜在的なリスクの排除も実現できるでしょう。
労働災害といった安全トラブルの予防については、専門家による「ヒヤリハット」に着目した実践的な改善方法を解説する以下の動画をご覧ください。
>>【視聴無料】専門家が解説する「労働災害を撲滅するヒヤリハット対策の心得」を見る
5S活動の効果を最大化させる進め方
いざ、実際に5S活動を進めようとすると現場主体ではなく、トップダウンで具体的な行動を指示するだけの形骸化した活動になってしまうことも珍しくありません。このような5S活動では、活動の目的や効果を引き出すことは難しいでしょう。
そこで本章では、現場改善の効果を引き出す5S活動の進め方を3ステップに分けて解説します。
① 目的やゴールを策定する
5S活動は単なる職場の整理整頓や清掃活動ではありません。「何のために5S活動を行うのか、最終的にどのような効果を期待するのか」を具体的に設定し、従業員全員と共有することが重要です。
そのため、「不良品率を〇%削減する」や「ヒヤリハット発生件数を〇%削減する」といった具体的かつ定量的な目標を設定しましょう。実際に施策を行った成果や効果を評価しやすくなる・改善を目的とした活動であることを伝えつつ進められるというメリットがあります。
5S活動の実際の成果例や目的達成のための実践フォーマットを見たい方は、以下のリンクをクリックして「実践的な5S活動」の解説動画をご覧ください。
② 5Sのルールを作る
現場に「5Sをやってください」と言っても、5S活動のレベルややり方が個人によってバラバラになり、効果が安定しません。そのため、誰が行っても同じレベルで実施できるように5Sのルールを作成しましょう。
ルールを作成する際は、現状の職場環境を観察し、問題点や課題を洗い出し、各要素(整理、整頓、清掃、清潔、躾)ごとにルールを定めることが効果的です。従業員へのヒアリングを行うと、課題を具体的に把握できます。
▼5Sルールの例▼
整理 | ・1ヶ月以上使っていないものは、廃棄または保管場所へ移動する ・机の上には、作業に必要なもの以外は置かない |
整頓 | ・工具は、種類ごとに定位置に保管する ・使用頻度の高いものは、取り出しやすい場所に置く |
清掃 | ・1日の終わりに、自分の作業場所を清掃する ・月に1回、全員で職場全体の清掃を行う |
清潔 | ・整理、整頓、清掃の状態を維持する ・汚れたら、すぐに清掃する |
躾(しつけ) | ・ルールを守らない場合は、注意喚起を行う |
5S活動は、整理⇒整頓⇒清掃⇒清潔⇒躾の順で進めましょう。順序を守ることで、無理なく自然な流れで職場環境を改善することが可能です。
③ 効果測定をして5Sサイクルを繰り返す
5S活動は「ルールを実施して終わり」ではありません。
実施による効果を測定して、現場をよりよくするための改善点を探し出しましょう。実際に取り組んでみることで分かる問題も出てきます。定例ミーティング等で進捗状況を連携し、問題が発生した場合は計画や施策を見直しすることが大切です。
策定した目標が達成したら、より高い数値目標や別の課題解決を目的に設定するのがおすすめです。そうすることで、5S活動のサイクルを継続して現場改善につなげることができます。
しかし、どれだけ筋の良い施策を講じたとしても、分かりやすく実行しやすい内容をルールとして正しく理解してもらう「躾」ができないと、期待していた効果を引き出すことは難しいでしょう。
次章では、躾による現場への定着を助ける教育方法について詳しくご紹介します。
5S活動の効果を最大化させる「躾」のコツ
5S活動が成功するか否かは、「躾(しつけ)」にかかっていると言っても過言ではありません。
躾は、他の4Sを定着させ持続可能な活動にするための要となります。たとえ整理整頓が行われていても、それを維持する意識や行動がなければ、すぐに元の状態に戻ってしまいます。
継続的な改善活動とするためにも、ルールを守る意識と習慣を育む「躾」のコツを以下でチェックしていきましょう。
躾を正しく理解する
「躾」という言葉だけを見ると、「強制的にやらせる」というようなイメージを抱かれるかもしれません。しかし、それでは自律的な行動を促せず、やがて形骸化してしまう恐れがあります。
単に指示に従わせるのではなく、「なぜルールが必要なのか、守ることでどのような効果があるのかを理解させる」ことが躾であると理解して、従業員へルールを周知させましょう。
トップ自らが率先して行い、良い行動を褒め・悪い行動は改善を促すといった、継続的な働きかけも不可欠です。
動画を活用してやり方を標準化する
5S活動を効果的に進めるためには、躾の一環として「5S活動やり方を標準化」しましょう。
しかし、口頭や文書での説明だけでは、なかなか理解が浸透しないことがあります。そこで有効なのが、動画を活用した教育です。
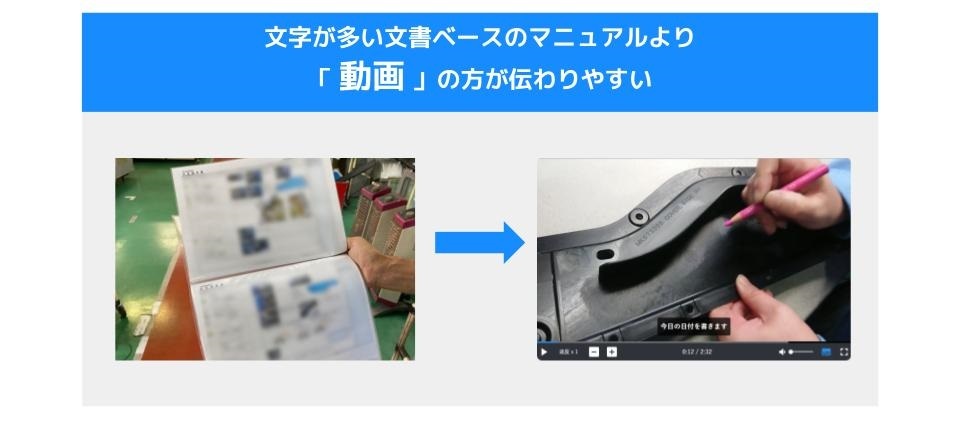
5Sの実施方法を撮影した動画で見せることで、具体的なイメージをつかみやすくなります。また、動画は繰り返し見返せるため、工数をかけずに、従業員の理解度を均一化し、個々人の解釈の違いによる誤った行動を減らす効果も期待できます。
しかし、動画形式のマニュアルを作ること自体が「時間がかかりそう」「編集が難しくて作られなさそう」とお思いではないでしょうか? そこでおすすめなのが、誰でもかんたんに動画マニュアルが作成できる「tebiki現場教育」というツールです。
かんたん動画マニュアル作成「tebiki」
現場教育システムである「tebiki」は、現場の教育に必要な機能を厳選したシンプルで使いやすい編集画面で、動画編集未経験者でもかんたんに動画マニュアルが作成できるツールです。
以下のような機能を取り揃えており、5Sルールや作業手順など、教育工数を削減しつつも分かりやすく従業員に伝えることが可能となっています。
- 動画の音声を自動で字幕化
- 日本語字幕を100ヵ国語以上に自動翻訳が可能
- テスト機能を活用した理解度の可視化
- オフライン再生機能で通信環境が悪い現場でも使用できる
- レポート機能で従業員の学習状況を可視化
一部のプランでは、スキルマップ作成機能も搭載されています。この機能により、5Sに関するトピックにおいて、自社の現場で必要な項目の理解度がどれほど進んでいるかを、従業員ごとに把握できます。
「他の機能やプランの詳細を知りたい」という方は、以下の画像をクリックしてサービス紹介資料をご覧ください。
5Sを成功させる動画による標準化事例
tebiki現場教育を使用し、動画マニュアルによる標準化を実現している2社の事例をご紹介します。5S活動の成功に欠かせない「標準化」を実現させるヒントとしてご覧ください。
より多くの企業事例と効果を知りたい方は、以下のリンクから導入事例集をぜひご覧ください。
大同工業株式会社
大同工業株式会社は、自動車/産業機械/福祉機器などさまざま領域を展開し、2022年には海外11カ国に拠点を持つグローバル企業です。言語化しにくい高度な技術が多いゆえに、業務手順が“我流化”し、品質にバラつきが発生していることを課題視していました。
この我流化を防ぐために、tebiki現場教育を導入。各メンバーが持つカンやポイントを活かしながら動画マニュアルを整備したことで、業務の効率化や最適化、最終的には部内での業務標準化を実現し、評価エラーを削減することを実現しました。
マニュアルの作成工数も50%以上削減させた大同工業株式会社のインタビュー記事をもっと読みたい方は、以下からご覧ください。
インタビュー記事:製造業の技術部門での動画マニュアル導入事例|製造業の技術部門の業務を動画で標準化。品質評価に関わるヒヤリハットを8割削減して、多能工化を実現
理研ビタミン株式会社
理研ビタミン株式会社は、1935年設立の食品および食品添加物の製造販売を行う企業です。同社では、教育をベテラン社員に依存していたため、教育の質が個人の経験や知識に左右されていました。そのため、教育内容にばらつきが生じ、新入社員のスキル習得に時間がかかっていました。
そこで教育課題を解決するために、tebiki現場教育を導入。tebikiを活用することで、ベテラン社員の技術や知識を動画で記録し、新入社員や若手社員に対して効率的に伝えられるように。これまで、特定の担当者に偏っていた教育方法から脱却し、誰もが同じレベルの教育を受けられる標準化された教育体制を実現しました。
その結果、作業手順のバラツキが減少し、製品の品質管理が向上。標準化された教育内容により、従業員間での知識共有が進み、全体のスキルレベルも底上げされました。
理研ビタミン株式会社の事例をさらに詳しく知りたい方は、以下のインタビュー記事をチェックしてみてください。
インタビュー記事:品質保証部門と製造部門がONEチームで取り組んだ業務標準化と技術伝承
より多くの企業事例を知りたい方は、以下の導入事例集も併せてご覧ください。 各社がどのような現場教育の悩みを抱えて、tebikiで解決してきたのかがわかりやすく1冊にまとまっています。
5S活動に関連する用語の意味や違い
5S活動について調べていると、以下の用語に触れる場面があるでしょう。
これらを目にしたときに『何が違うのか?』と疑問に感じるかもしれません。本章では、それぞれの用語について解説します。
5S3定
5S3定とは、先述した5Sに定位・定量・定品を表す3定(さんてい)を組み合わせた言葉で、5Sの「整頓」を細分化し、目標とする整頓された状態を示しています。
定位・定量・定品の意味は、それぞれ以下の通りです。
- 定位:モノを置く場所を定める
- 定量:置くモノは適正な数量を保つようにする
- 定品:決められた位置に決められたモノだけを置く
5S活動の「整頓にあたる5S3定」の実践的なやり方を知りたい方は、以下のリンクをクリックして正しい5S活動の進め方を解説する動画をぜひご覧ください。
>>【視聴無料】5S3定のポイントは?5S活動の進め方を見る
6S
5S活動に「作法(Saho)」を加えたものが6Sです。
作法とは「正しい行動をする」ことを意味し、従業員が礼儀正しい行動を日常的に実践することを目的としています。6S活動は、従来の整理、整頓、清掃、清潔、躾に加え、作法を取り入れることで、職場環境の改善を推進します。
日常と仕事を完全に切り替えるのは難しいため、日常生活で乱暴な態度を取る人は、仕事中にも乱暴な行動や態度が現れやすい傾向にあるといえます。仕事が乱暴であれば、5S活動も同様に乱雑になりがちです。たとえば、清掃を行っても汚れが残っているなど、活動が不十分な結果に終わることがあります。
そこで、作法を取り入れることで普段から礼儀や模範的な行動を意識させ、仕事中も丁寧な作業を心がけてもらうことが望まれます。結果として、活動が丁寧かつ正確になり、改善活動の効果も高まります。
3Q6S
「3Q6S」とは、3つの「Q:Quality(品質)」と6つの「S」からなる手法です。
3Q6Sの3つのQは人の品質、製品の品質、会社の品質を指し、6つのSは整理、整頓、清掃、清潔、躾、作法を含みます。6つのSを徹底的に実践することで、3つのQが自然と向上することを目指しています。
最初のQは「人の品質」です。
人の品質のねらいとして、6S活動を通じて従業員ひとりひとりが正しい行動を習慣化し、高い倫理観とモラルを持つことが挙げられます。従業員の質が向上することで、結果として職場全体のパフォーマンスの向上が期待できます。
次に「製品の品質」です。
整理・整頓・清掃・清潔・躾・作法を徹底することで製造プロセスが効率化され、不良品の発生が減少します。結果として、製品の品質が向上することで顧客満足度も高まります。
最後に「会社の品質」です。
高品質な製品を安定して供給できる企業は、信頼と評判を得られます。従業員が6S活動を実践して常に高い品質を維持することで会社全体のブランド価値が向上し、市場での競争力を強化できます。
7S
5S活動や6S活動をさらに改良した7S活動は、業種や企業の特性に応じて必要な要素を5Sに追加しているものです。
有名な7Sの要素としては、食品衛生で使われる「洗浄(Senjyo)」と「殺菌(Sakkin)」が挙げられます。
食品衛生における7Sや、効果的な衛生管理手法を知りたい方は、以下の記事も併せてご覧ください。
関連記事:食品衛生7S「具体例」や「進め方」は?5Sとの違いも解説
他の業界における7Sとして、「安全(Safety)」と「安心(Smile)」。「節約(Setsuyaku)」や「創意工夫(Souikufu)」も加えられることがあります。
【事例】業界別に使える5S活動のアイデア集
5S活動は多くの現場で導入されており、製造業・病院・飲食店・事務所など多くの業界で環境改善に向けた取り組みとして取り入れられています。業界別のアイデア集をまとめると以下の表の通りです。
▼製造業 / 工場
課題 | 工具をバラバラに置いていたり上に積み上げた状態のため、欲しい治工具がすぐに見つからない |
5S対策案 | 工具のサイズ別に並べ替えて定位置を決めることで、見つけやすく取り出しやすい状態にする |
▼物流業
課題 | 在庫がどこにあるかが明記されず、探すのに時間がかかる |
5S対策案 | 在庫の定位置を決めて、箱や袋や棚などにそれぞれ品名を表示する |
▼飲食業
課題 | キッチンやホールの床に汚れゴミがあり、転倒しやすい |
5S対策案 | ・掃除をして帰るように徹底する ・清掃手順や清掃箇所をマニュアル化する |
より多くの5S活動のアイディアを知りたい方は、5Sコンサルタントが解説する「5S活動の具体的な実践方法」を以下のリンクをクリックしてご覧ください。
まとめ
5S活動は、製造業の職場環境を改善する手法で、「整理・整頓・清掃・清潔・躾」の5要素で構成されます。業務効率、生産性向上、労働災害防止に効果的です。
これらの効果を5S活動によって出すには、5Sのルールを標準化させて、従業員へ周知することが欠かせません。
本記事でご紹介した、大同工業や理研ビタミンの事例のように、「tebiki現場教育」導入で教育効率化と標準化が可能です。成功事例を参考に、自社での5S活動定着を目指しましょう。
動画マニュアルを簡単に作れるだけではなく、スキル管理や教育進捗管理などを行える「tebiki現場教育」についてより詳しく知りたい方は、以下の画像をクリックしてぜひサービス資料をご覧ください。