かんたん動画マニュアル作成「tebiki現場教育」や、かんたんデジタル現場帳票「tebiki現場分析」を展開する現場改善ラボ編集部です。
不良率とは、製造過程で生じる不良品の割合を示す指標です。不良率をより精密化した指標であるPPMの定義と計算方法もあわせて、本記事で紹介します。不良率を改善するための分析手法や改善案もあわせて解説しているので、製造現場の生産率向上のヒントにしてみてください。
目次
不良率とは?計算方法や歩留まりとの違い
不良率とは、生産された製品の総数に対する不良品の数の割合を示します。不良率が高いと生産コストの増加、顧客満足度の低下、さらにはブランドイメージにも悪影響を及ぼす可能性があります。
自動車の製造業を例として挙げると、1,000台の車を生産した場合、10台が不良品であれば不良率は1%となります。例に示した通り、不良率は生産効率や品質管理の水準を測る基準となります。
【計算式】不良率(%)=(不良品の総数 / 総生産数)× 100
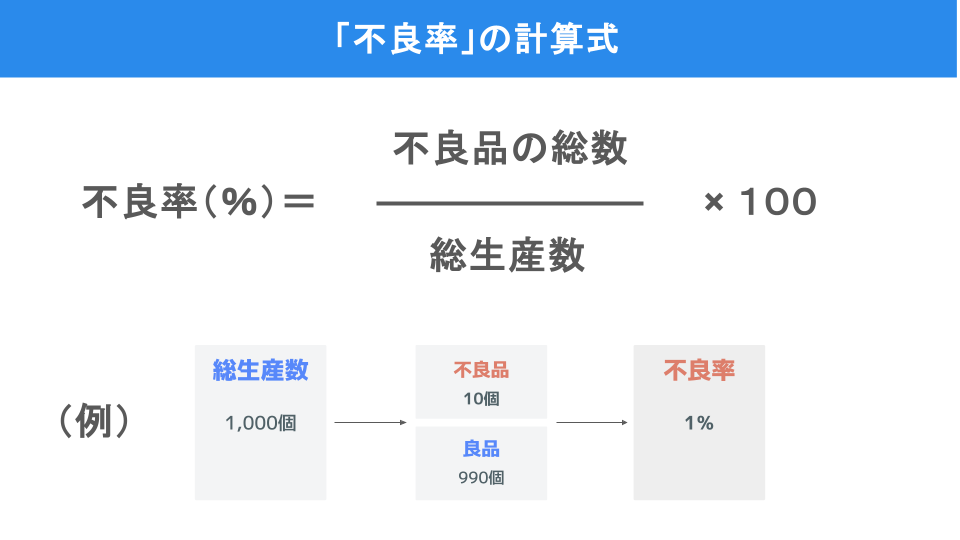
※かんたんデジタル現場帳票「tebiki現場分析」を活用すると、製造日報などで記録された生産数や不良数のデジタルデータを自動集計し、記録者・部門ごとの不良率が自動で計算されます。
不良率が高ければ生産された製品の中で不良品が多いということです。不良品は通常、修理または廃棄が必要となってしまうため、生産コストの増加につながります。
また、不良品が市場に出回ると顧客満足度の低下につながり、リピート購入や口コミによる新規顧客獲得が減少する可能性もあります。
さらに不良品が多く品質が低いことを認知されると、消費者はそのブランドの製品を避けるようになり、ブランドイメージに影響を与えることもあります。特にSNSやレビューサイトでの悪評が拡散すると、その影響は一気に広がる可能性があるため注意が必要です。
不良率と歩留まりの違い
不良率と似た概念である「歩留まり」との違いも解説します。
歩留まりは「投入した原料から実際に得られた生産量」を指すのに対して、不良率は「生産量に対する不良品の割合」を指します。
▼不良率と歩留まりの違い▼
比較項目 | 不良率 | 歩留まり |
---|---|---|
定義 | 生産総数に対する不良品の割合 | 投入原材料から得られた良品の割合 |
計算式 | (不良品数 ÷ 生産総数) × 100% | (良品数 ÷ 理論生産可能数) × 100% |
望ましい値 | 低いほど良い | 高いほど良い |
主な用途 | 品質管理の指標 | 生産効率の指標 |
測定タイミング | 製品完成後の検査時 | 製造プロセス全体 |
改善の焦点 | 検査基準、品質管理 | 製造プロセス、材料効率 |
コスト関連 | 不良品の廃棄、手直しコスト | 材料ロス、工程効率のコスト |
たとえば、スマートフォンの製造業で100個の部品を使って90個の製品が完成した場合、歩留まりは90%です。しかし、その90個の製品のうち5個が不良品であれば、不良率は5/90、すなわち約5.6%となります。
歩留まりが重要指標になる業界として「半導体製造業」が挙げられます。製造プロセスは微細な工程が多く、1つの小さな不具合が製品全体の品質に大きく影響するからです。
「食品業界」では不良率がより重要な指標であり、品質基準の維持に直結します(もちろん歩留まりも重要です)。包装ミスや重量不足は消費者の信頼を損なう要因となり、クレームやリコールのリスクを引き起こすからです。
つまり、歩留まりは生産効率に関わる数値であり、不良率は品質に関わる数値です。不良率と歩留まりはそれぞれ異なる改善策や管理手法が求められ、製造業では両方をバランスよく管理することが求められます。
歩留まりが低下する原因や改善事例を知りたい方は、無料動画「4Mの視点から実践する歩留まり改善」もあわせて参考にしてみてください。以下の画像をクリックすると、視聴用ページのフォームに遷移します。
不良率を精密に把握する指標「PPM」とは?計算方法も解説
PPMとは「Parts Per Million」の略称であり、製品100万個あたりの不良品の数を表す単位を指します。すなわち不良率に100万をかけ合わせた数式で計算でき、細かな不良率の把握を可能にします。
【計算方法】PPM= ( 不良品の数 / 製品の総数 )×1,000,000
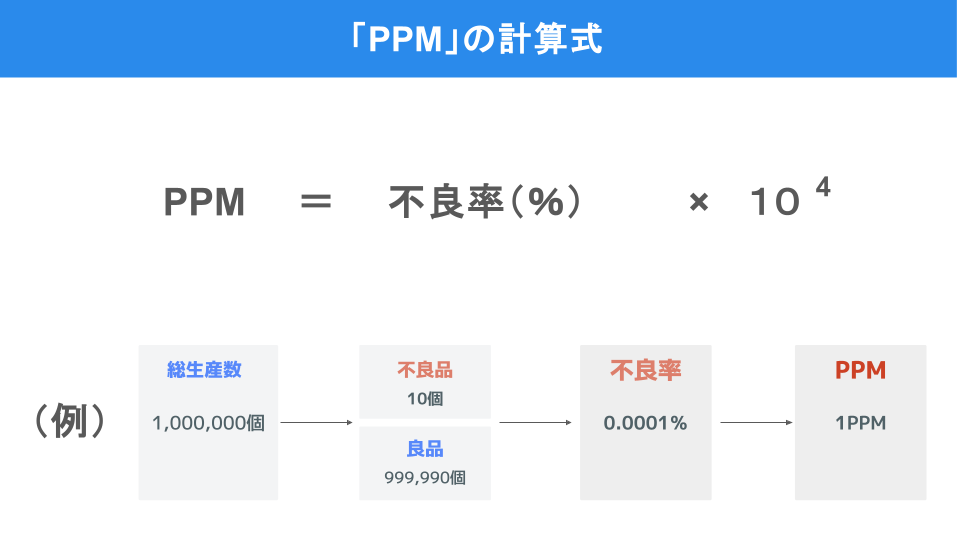
たとえば、1,000,000個の製品を生産し、20個が不良品だった場合、不良率(PPM)は以下のように計算されます。
不良率(PPM)=( 20 / 1,000,000 ) × 1,000,000 = 20PPM
PPMは、大量生産が行われる現場で特に重要になる指標であり、微細な不良率の把握によって品質管理の精度を高める役割を果たします。
PPMが重要指標とされる理由や存在意義
不良率をさらに精密化した指標「PPM」は、以下のような理由で重要視されています。
高精度が求められる製品に対応するため
自動車業界や航空宇宙業界のように、安全性が最優先される分野では、1個の不良品でも重大なリスクを伴うことがあります。PPMを用いることで、非常に小さな不良率も管理することが可能です。
サプライチェーン全体で基準を統一するため
サプライヤーや外注先と品質基準を共有する際、PPMは世界的に標準化された単位として役立ちます。これにより、品質基準のばらつきを抑え、一貫性のある製品供給を実現できます。
継続的な改善活動を促進するため
PPMを活用することで、不良率削減の進捗を定量的に評価できるため、品質改善活動を効率的に進めることができます。
たとえば、自動車業界では一般的に10PPM以下の品質基準が求められることが多く、航空宇宙業界ではさらに厳しい基準が適用されます。このような基準をクリアすることで、製品の信頼性と市場競争力を高めることが可能です。
製造業における不良率の目安と現実的な目標設定
製造業において不良率は非常に重要な指標ですが、業種や製品、生産規模によって許容される不良率は異なります。そこでここからは、一般的な不良率の「目安」について紹介します。
製造業における不良率の目安は「3σ(スリーシグマ)」「6σ(シックスシグマ)」で定義されることが多いです。
不良率の目安として用いられる「3σ(スリーシグマ)」「6σ(シックスシグマ)」とは
3σ(スリーシグマ)とは、製品1000個中3個以下の不良品を目指す水準であり、品質のばらつきが比較的小さなプロセスに適用されます。
一方で6σ(シックスシグマ)は、製品100万個中3.4個以下の不良品を目指す水準という極めて厳格な基準であり、安全性や精密さが特に求められる分野で使用されることが多いです。
それぞれPPMに換算すると以下のとおりです。
- 3σ = 2700PPM
- 6σ = 3.4PPM
業種によりますが、製造業における一般的な不良率の目安は3σとされています。ただし、生命や命の危機にかかわる製造分野での不良率は6σが目標値として定められていることもあります。例えば自動車業界や医療機器製造、航空機製造など。
一方で、プラスチック製の玩具のような人名にあまり影響のない業種では、6σまで求められることは少なく、3σ程度が一般的です。
関連記事:シックスシグマ(6σ)とは?経営/品質管理で必要な概念をわかりやすく解説!
不良率0%は現実的か?目標設定のポイント
「不良率0%を目指す」というのは理想ですが、現実的には難しいです。前述の3シグマや6シグマのように、厳格な指標であっても一定の不良品が発生することが考慮されています。
経済産業省による「2019年度ものづくり白書」では、品質トラブルの原因として多く当てはまっているのが、従業員教育の不足・従来慣行への依存や馴れ合いといった、いわゆるヒューマンエラーであるという調査結果が提示されています。
ヒューマンエラーもまた、発生をゼロにできないトラブル原因であるため、ヒューマンエラーのような作業ミスによる品質不良は起きるものとして現実的な目標設定を行いましょう。設定を行う際は、以下のようなポイントを踏まえながら、目標設定を考慮すると良いでしょう。
- 現状把握:過去の不良率や不良要因を分析し、実態を正確に把握する
- 基準との比較:業界の不良率目安や顧客の要求品質を調査し、ギャップを明らかにする
- 改善投資とリスク評価:不良率低減に必要なコストやリスクを総合的に検討する
- 段階的な目標設定:達成可能性を考慮し、期限を切って少しずつ目標を引き下げる
- 継続的な改善:不良率の推移を定点観測し、PDCAサイクルで定期的にレビューと改善を行う
不良品の発生原因を分析する方法
製造現場で発生する不良品の原因を特定し、適切な対策を講じることは品質改善の基本です。そこでここからは、不良品の原因を体系的に把握するための分析手法を3つ紹介します。
それぞれの手法を活用することで、問題の可視化、根本原因の特定、データの効果的な活用が可能となります。
「5M+1E」と「特性要因図(フィッシュボーン)」の活用【可視化と整理】
不良率の原因を分析する1つ目の方法として「5M+1E」に基づいた「特性要因図(フィッシュボーン)」の活用が挙げられます。
「5M+1E」とは、製造業における問題の発生要因を体系的に整理するためのフレームワークです。
5Mとは人(Man)、機械・設備(Machine)、方法(Method)、原料、材料(Material)、測定、検査(Measurement)で、1Eとは環境(Environment)です。
- 人:作業員のスキル不足、注意力低下、教育体制の欠如など
- 機械:設備の老朽化、故障、メンテナンス不足
- 方法:作業手順の不備、標準化の欠如、無駄な工程
- 材料:原材料の品質のばらつき、不適切な選定
- 測定:測定器の精度不足、誤差が大きい計測
- 環境:作業環境の温度・湿度、騒音、照明の影響
これらの製造プロセスが不適切であれば不良品が発生しやすくなります。ゆえに、プロセスをひとつひとつ見直すことで原因を洗い出せます。
また、特性要因図とは、5M+1Eの各要素を可視化するツールです。魚の骨のような構造を持つため「フィッシュボーン」とも呼ばれます。5M+1Eそれぞれのプロセスにおける、不良品の複雑な発生原因をシンプルに整理でき、対策を検討するための出発点を明確にします。
▼特性要因図(フィッシュボーン)の例▼
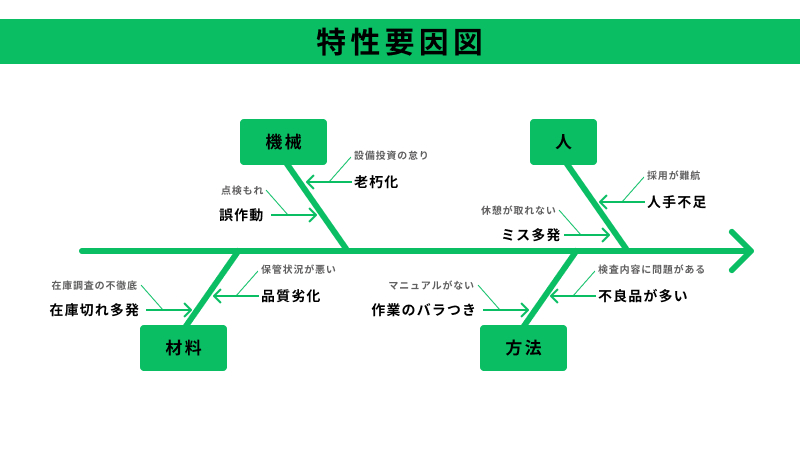
特性要因図の分析のやり方や書き方について、詳細を知りたい方は以下の記事もあわせて参考にしてみてください。
関連記事:【図解あり】4M分析とは?問題整理や変更管理での分析方法を解説!
「なぜなぜ分析(5Why)」の活用【根本原因の特定】
なぜなぜ分析は、不良品発生の根本原因を深堀りするのに有効な分析手法です。特定された要因に対して、「なぜ?」を5回程度繰り返して問いかけることで、根本原因にたどり着きます。
例えば、「製品に傷がある」→「なぜ?」→「作業員が工具を落とした」→「なぜ?」→「工具の置き場所が不安定だった」→「なぜ?」→「工具置き場が整理整頓されていなかった」といった具合に深掘りしていきます。
より実践的ななぜなぜ分析の具体的手法が知りたい方は、無料動画『ヒューマンエラーに対する「トヨタの考え方」ートヨタで学んだなぜなぜ分析ー』もあわせてご覧ください。本動画では、トヨタ社内にてトヨタの正社員に対して「なぜなぜ分析」を教えていた訓練指導者「伊藤 正光氏」をお招きし、トヨタ社内にて実際に教えられていた「なぜなぜ分析」のエッセンスをお届けしています。
なぜなぜ分析の演習から標準作業を確立させる教育アプローチの解説まで、多岐にわたるコンテンツが収録された無料動画になります。以下の画像をクリックしてご視聴ください。
「QC7つ道具」の活用【データの収集、整理、分析】
不良品の発生原因を特定する方法として「QC7つ道具」も有効です。QC7つ道具は、品質管理の分野で広く用いられる7つの基本的な分析ツールです。
QC7つ道具は、品質の問題を特定、分析、解決するために設計されており、製造業をはじめとする多くの業界で活用されています。
具体的には、以下のツールが含まれます。
チェックシート
目的: データ収集と整理。
作成手順: 調査項目を明確にし、チェックする形式(例:正の字、○×)を決めてシートを作成。
解釈方法: 集計結果からデータの傾向や分布を把握。
活用例: 不良の種類別発生回数、作業工程ごとの作業時間などを記録。
パレート図
目的: 問題の優先順位付け。「80/20の法則」を活用し、重要な要因を特定。
作成手順: データを集計し、棒グラフで表示。累積構成比を折れ線グラフで表示。
解釈方法: 棒グラフの高い順に要因を並べ、累積構成比が高い要因に注目。
活用例: 不良原因別の発生件数を集計し、最も多く発生している原因を特定。
特性要因図(フィッシュボーン図)
目的: 問題の原因を体系的に整理し、根本原因を特定。
作成手順: 問題を「結果」として右側に記述。主要因(例:4M)を大骨として左側に記述。各要因に関連する原因を中骨、小骨として追加。
解釈方法: 骨の繋がりを辿ることで、問題と原因の因果関係を把握。
活用例: 製品の不良発生原因を4Mの視点から分析。
ヒストグラム
目的: データの分布状況を把握。
作成手順: データを適切な階級に分け、各階級の度数を棒グラフで表示。
解釈方法: データの中心、ばらつき、偏りなどを確認。
活用例: 製品の寸法データをヒストグラムで表し、寸法ばらつきの程度を確認。
散布図
目的: 2つのデータの相関関係を分析。
作成手順: 2つのデータをそれぞれX軸、Y軸にプロット。
解釈方法: 点の分布から相関の有無や強さを判断。
活用例: 作業時間と不良品発生数の相関を分析。
管理図
目的: 工程の状態を監視し、異常を発見。
作成手順: データを時系列順にプロットし、管理限界線(上限値と下限値)を設定。
解釈方法: プロットされた点が管理限界線を逸脱した場合、工程に異常が発生していると判断。
活用例: 製品の寸法を定期的に測定し、管理図で監視。
グラフ
目的: データの変化や比較を視覚的に表現。
作成手順: データの種類や目的に合わせて適切なグラフ(折れ線グラフ、棒グラフ、円グラフなど)を選択し作成。
解釈方法: グラフの形状からデータの傾向や変化を把握。
活用例: 月ごとの不良品発生数の推移を折れ線グラフで表示。
これらQC7つの道具は、目的や状況によって使い分ける必要があります。不良品を改善するにはQC7つ道具を正しく用いて問題を見える化することが求められますが、「改善を行う際にQC7つ道具を使いたくても使い方が分からない」や、「実務でどう活かせばいいか分からない」とお悩みの方も多くいるでしょう。
そこで、QC7つ道具の実践的な活用法をさらに知りたいという方は、無料動画「品質問題の原因を見つける『正しいQC7道具の使い方』と『改善の考え方』」を参考にすると良いでしょう。
株式会社エイシン・エスティー・ラボの代表取締役である山本 諭氏に品質問題が起きる原因やQC7つ道具と新QC7つ道具の違い、実務で実践できる品質問題を見える化させるQC7つ道具の使い方、品質改善の重要なカギを握る「業務標準化」について解説しています。
不良品が発生するよくある原因と改善例
前述した3つの分析手法を用いると、不良品の発生には一定の頻度で見られる共通の要因があることがわかります。そこでここからは、「よくある不良品発生の原因」を4つに分類し、それぞれの対策方法について解説します。
不良品発生の背景を理解し、具体的な改善の方向性をイメージしやすくなるでしょう。
ヒューマンエラー
ヒューマンエラーは、不良品発生の中でも特に頻度が高い要因です。手作業が多い工程では、作業者のミスが直接的に品質に影響を及ぼすことがよくあります。具体的には以下のような状況が挙げられます。
- 作業手順の理解不足
- 慣れや疲労による注意力の低下
- 教育不足や不適切な訓練
これらの要因により、手順漏れや誤操作、不適切な判断が発生し、不良品の増加を招きます。こうしたヒューマンエラーを抑えるには、以下のような対策が挙げられます。
改善策 | 内容 |
---|---|
教育基盤の構築 | 作業者のスキル向上がなされる教育基盤を作る。 |
作業手順の標準化 | 誰が作業しても一定の品質が保たれるよう仕組み化する。 |
作業環境の最適化 | 作業場の照明、温湿度、配置を見直し、作業者が集中できる環境を整える。 |
特に重要なのが「教育基盤の構築」「作業手順の標準化」です。多くの製造業はこれら2つの課題を根本的に解消できず、不良率を改善し切れていないのが実情です。
不良率を改善している製造業、すなわち作業者の教育や作業品質の向上が徹底できている多くの製造業では「動画マニュアル」を導入しています。
動画マニュアルは、「文字では伝えきれない複雑な作業手順」を「一目でわかりやすく伝えられる」教育手段であり、不良率を根本的に改善する有効策のひとつです。実際に動画マニュアルを活用したことで、手順不遵守による作業ミスが9割削減され、この原因による不良品発生が相当数削減された事例もあります。
動画マニュアルを活用し、品質不良や生産性、安全トラブルなどの現場課題を解決している製造業の事例集をご用意していますので、以下の画像をクリックしてご覧ください。
設備の老朽化や整備不良
設備の老朽化や整備不良も、不良品発生の大きな要因となります。設備保全が適切に行われていない場合、以下のような問題が発生しやすくなります。
- 部品の摩耗による精度低下
- 突発的な機械故障
- 生産ライン全体の停止
これらの状況は、製品の規格外や品質のばらつきを引き起こし、生産効率にも悪影響を与えます。したがって対策としては以下の項目を検討し、予防保全/予知保全を行うことを徹底しましょう。
改善策 | 内容 |
---|---|
定期点検の徹底 | 設備の寿命を延ばし、不良品の発生を防ぐため、定期的な点検スケジュールを策定・遵守する。 |
現場帳票のデジタル化 | 温度、振動、電流などをデジタル現場帳票に記録することで、それらの数値や情報をリアルタイムで監視し、異常が発生した際に早期対応を可能にする。 |
こうした設備トラブル防止策は不良率改善に不可欠であるにもかかわらず、多くの製造現場では設備の整備業務が属人化しており、不良率をなかなか改善できずにいます。ゆえに、あらゆる製造現場で予防保全/予知保全の「DX化」が検討されています。
DXによって設備保全業務の属人化を解消し、不良率を改善する方法や、実際に不良率を改善できた製造現場事例を知りたい方は、以下のPDF資料もあわせてご覧ください。
>>「製造業の設備トラブルによる生産性低下を解消する設備保全のDX」を見てみる
不十分な技術・技能伝承や人材育成
技術・技能伝承や人材育成が不十分な場合、熟練した技術やノウハウが次世代に引き継がれず、不良品の発生リスクが高まります。具体的には以下のような問題が生じます。
- 作業精度の低下
- 問題発生時の即時対応力の欠如
- 多能工化の遅れ
これにより、製品の品質にムラが生じたり、迅速な対応ができずに不良品が拡大することがあります。
対策としては、「カンコツや技能の見える化」が重要です。多くの製造業では「ベテラン社員への依存」がまだまだ根強く残っており、若手世代への技能継承が喫緊の課題となっています。
そこで多くの製造業では、紙ベースの作業手順書もしくはOJTで技術伝承に取り組んでいます。しかしこれらの方法では複雑な技術や微妙な技能は伝わりにくく、さらには手順書の編集や更新の手間、各教育担当者の教える力のばらつきなど、さまざまな問題が伝承を阻害しています。
そんな従来の技能伝承手法を使わずとも、品質を作りこめる人材を育てる技能伝承の進め方について「元トヨタのトップ技能者である伊藤正光氏」が以下の動画(無料)で解説しています。人材育成や技能伝承に課題を抱え、突破口を見つけたい方は必見の動画なので、ぜひご覧ください。
原材料や部品の不良
原材料や部品の品質が不安定な場合、不良品の発生リスクが著しく高まります。特に外部から調達する材料に依存している場合、以下の要因が問題となります。
- 原材料の品質ばらつき
- サプライヤーの管理不足
- 受け入れ時の検品体制の不備
これらは、製品全体の品質低下を引き起こし、顧客の信頼を損なうリスクを伴います。上記要因を改善するには、以下のような対策が挙げられます。
改善策 | 内容 |
---|---|
サプライヤーの選定基準の明確化 | 信頼性の高いサプライヤーを選定する基準を設定し、契約前に適切な審査を行う。 |
品質管理プロセスの強化 | 受入検品を徹底し、品質基準を満たさない材料を排除する。 |
長期的な協力体制の構築 | サプライヤーと連携して品質改善活動を推進し、継続的な信頼関係を築く。 |
製造現場の不良率を改善した企業事例
不良率を実際に改善している製造現場では、いったいどのような対策が行われているのでしょうか?そこでここからは不良率改善の実例を紹介します。
他社の取り組みを参考にして、不良率改善を実現するためのネクストステップをイメージしてみてください。
児玉化学工業株式会社:新入社員や外国人労働者の作業のばらつきを解消
1946年創業の化学メーカーである「児玉化学工業株式会社」の製造現場では、部品を製造するための要領書が500ほど存在していたために、作業手順の伝達に煩雑さが生じていました。かつ、外国人労働者が多い現場でもあり、紙マニュアルの限界を感じていたのです。
以上の課題から品質不良の問題として挙がっていましたが、これらの課題を「動画マニュアルの導入」によって解消しました。
複雑な作業手順がすべて動画で見える化されただけでなく、非言語マニュアルによって外国人労働者の作業品質も向上。さらに、現場従業員が動画マニュアルの撮影や編集を手掛けていることもあり、それによりルールや手順を遵守する・遵守させるような文化が醸成されています。
品質不良を改善した動画マニュアルの例として、児玉化学工業株式会社で実際に使われている動画を以下に掲載します。
▼バリの取り方を解説する動画マニュアル(音量にご注意ください)▼
※現場従業員が「tebiki」で作成
こうした動画マニュアルを通じて、同社は不良率改善を実現しています。
児玉化学工業株式会社の本事例に関する詳細は、以下の記事からご覧いただけます。あわせて参考にしてみてください。
関連記事:手順書作成の工数は紙の1/3になったと思います。動画で作るのはかんたんだし、学ぶ側にもわかりやすいですよね。
サラヤ株式会社:作業手順の標準化を徹底し、製品の不良数を削減
消毒剤や医薬品・食品等を製造する化学・日用品メーカーである「サラヤ株式会社」では、作業品質のばらつきが課題でした。細かい作業が品質維持・向上には人材育成が生命線であると掲げている同社では、従来から運用していた紙の作業手順書が作業品質ばらつきの原因であると判断しました。
たとえば「製造機器の整備方法」のような、紙では伝わりにくい業務は作業者によって品質がばらつきやすく、複雑な作業でも標準化できる対策を模索していたのです。
そこで、同社が抱える紙のマニュアルを動画マニュアルに置き換え、教育基盤を構築することを決意。結果的に品質のばらつきや属人化が改善され、動画マニュアルの効果を実感した同社は複数拠点にて400以上の動画マニュアルを作成しました。
同社が実際に作成した動画マニュアルの一部を、参考として以下に掲載します。
▼ラベルの貼り方を解説する動画マニュアル(音量にご注意ください)▼
※現場従業員が「tebiki」で作成
サラヤ株式会社の本事例に関する詳細は、以下の記事からご覧いただけます。あわせて参考にしてみてください。
関連記事:消毒剤のトップシェアメーカーでtebikiを活用。半年で400動画作成!世界の「衛生・環境・健康」に貢献!
テーブルマーク株式会社:作業手順の標準化を徹底し、製品の不良数を削減
冷凍食品や業務用食品等の製造を手掛ける「テーブルマーク株式会社」では、「教育品質が担当指導者によってばらつく」という課題がありました。結果的に新入社員間で作業品質に差が生じ、標準化されていないことが問題視されていたのです。
また、製品の出来栄えを見極める方法も「カンコツ」に依存することが多く、技能伝承という面でも課題を抱えていました。こうした課題は製品不良につながる要因でもあります。
そこで同社は「わかりやすくて、とっつきやすい手順書」が解決の糸口であることを考え、「動画マニュアル」の導入に舵を切りました。数ある動画マニュアルの作成ツールの中でも、「通常業務を行いながらでも問題なく動画マニュアルを作成できる”手軽さ”」がコンセプトである「tebiki」を導入。
動画マニュアルによって品質向上を実現しているだけでなく、「安全な作業手順」も周知できるようになっており、従業員の安全性にも寄与しています。
テーブルマーク株式会社の本事例に関する詳細は、以下の記事からご覧いただけます。あわせて参考にしてみてください。
関連記事:属人化業務の指導工数を83%削減!標準化教育により安心安全な食品を提供
【結論】不良率改善の鍵は「現場データをリアルタイムで把握すること」と「教育基盤の体制整備」
不良率は「生産された製品の総数における不良数の割合」であり、PPMは不良率をより精密に把握するための指標です。
不良率が改善されないよくある要因は以下のとおりです。
- ヒューマンエラー
- 設備の老朽化や整備不足
- 不十分な技能伝承や人材育成
- 原材料や部品の不良
上記の課題解消には「現場データをリアルタイムで把握すること」と「現場教育の体制整備」が有効手段であり、あらゆる製造現場で取り組まれています。
現場データのリアルタイム把握には「現場帳票のデジタル化」が、現場教育の体制整備には「動画マニュアルの導入」が主な選択肢となっており、これら二つを活用した製造現場における不良率の改善事例を本記事でいくつか取り上げました。
現場帳票のデジタル化を実現するのによく使われるサービスはかんたんデジタル現場帳票「tebiki現場分析」であり、現場教育の体制整備にはかんたん動画マニュアル作成「tebiki現場教育」が活用されています。
いずれのtebikiサービスも、以下のフォームから機能詳細や活用事例がまとまったPDF資料をご覧いただけますので、ぜひ参考にしてみてください。