かんたん動画マニュアル作成ツール「tebiki現場教育」を展開する、現場改善ラボ編集部です。
ヒューマンエラーとは、人の行動や選択によって生じるミスを指します。ヒューマンエラーは企業活動に悪影響を及ぼす事故など、大きなトラブルにつながる恐れがあるため、発生そのものを減らす対策が必要です。
本記事では、ヒューマンエラーの発生原因を12部類で整理し、ヒューマンエラー対策の具体例を全業界向け/製造業向けの計13選ご紹介します。
ヒューマンエラーの種類や多い人の特徴など、基礎知識も解説しているのでぜひご覧ください。
目次
ヒューマンエラーとは何か?種類やタイプなど簡単に解説
ヒューマンエラーとは、人の行動を起因として発生するミスのことです。
ヒューマンエラーは、注意不足や疲労から発生するケアレスミスやポカミスなどの小さい事故から、製品の品質不良発生や情報流出、交通事故、労働災害など企業に深刻な影響を及ぼすような大きい事故にもつながります。
まずは基礎知識として、ヒューマンエラーの意味や種類/タイプを解説します。
ヒューマンエラーとは「意図しない結果を生じる人間の行為」
ヒューマンエラーとは、人間による行動を起因として発生した失敗や事故のことを指します。
日本産業規格(JIS Z 8115:2000)では「意図しない結果を生じる人間の行為」と表現されています。
これまでの生活や仕事の中で、大小の違いはあれ、ミスをしたことがない人はいないでしょう。このようなミスは意図的ではないケースが大半のため、ヒューマンエラーの発生をゼロにすることはほぼ不可能です。
しかし、発生した事故が企業活動に重大な損害を与える可能性もあるため、発生をゼロに近づけるための再発防止策や未然防止策を検討し実施することが求められます。
ヒューマンエラーの種類やタイプ
ヒューマンエラーは、「ついつい・うっかり起きる」意図的ではないものと「あえて起こす」意図的なものの2種類に大別されます。
意図的ではないヒューマンエラー
ついつい・うっかり起きてしまうヒューマンエラーには、主に以下の4タイプがあります。
- 記憶エラー:覚えにくい情報や記憶の薄れによるミス。
- 認知エラー:誤った情報認識による行動ミス。
- 判断エラー:思い込みや曖昧な状況判断の誤り。
- 行動エラー:不適切な手順や操作性の問題で発生。
このようなヒューマンエラーがなぜ起きるのか?その原因は、後述の『ヒューマンエラーの原因は?12分類を解説』で詳しく解説しています。
意図的なヒューマンエラー
「あえて」によるヒューマンエラーは、主に業務に慣れている中堅社員や熟練者が、慢心や効率化を求めた結果、手順を意図的に省略することを引き金に発生します。
背景には、業務手順を遵守する意識不足や決まり事を守る納得感の欠如があるでしょう。このような手順不遵守を減らすためには、後述の『ヒューマンエラーに対するトヨタの考え方は?』が参考になります。
ヒューマンエラーの原因は?12分類を解説
ヒューマンエラーの原因について、高木 元也氏による「建設業におけるヒューマンエラー防止策」で報告されている12分類が分かりやすいのでご紹介します。
▼ヒューマンエラーの12分類▼

【参照元:建設業におけるヒューマンエラー防止対策】
この原因は建設業だけでなく、製造業や物流業、医療現場、一般的なビジネスの現場などにも通じる内容です。ここからは、ヒューマンエラーの原因を12分類ごとにご紹介します。
『ヒューマンエラー対策の具体例をまずは知りたい!』という方は、以下のリンクをクリックしてご覧ください。
不注意
不注意は、無意識に発生するミスで、スケジュールの見落としや業務マニュアルの確認不足が主な原因です。とくに定常業務では、同じ作業の繰り返しによる集中力低下が注意力不足を招き、ミスを誘発する傾向があります。
ミスを防ぐには、確認作業の習慣化や集中力を保つ環境整備が重要です。
錯覚(思い込み)
錯覚は、最初に理解した内容が先入観や思い込みによって誤認されることで生じるミスです。たとえば、業務進行中にプロジェクトの指示内容を誤って解釈し、不要な作業を進めてしまう場合が挙げられます。
このようなミスは原因を特定しづらいため、進捗確認の場を設けたり、業務内容をルール化(業務標準化)することで防ぐことができます。
危険軽視・慣れ
慣れや軽視によるミスは、業務に慣れてきたタイミングで発生しやすいです。最初は慎重だった作業も、『慣れて大丈夫』と感じて確認や手順を省略することでミスにつながります。
たとえば、慣れた業務で重要な確認を怠り、誤った結果を報告してしまうケースが挙げられます。とくに配属から数カ月~半年経過した新人に注意が必要で、定期的な確認作業の推奨や安全教育の実施が有効です。
集団欠陥
「みんながやっているから大丈夫」という同調圧力によって、間違いが放置され、ヒューマンエラーが発生することがあります。
たとえば、職場全体で非公式な手順を暗黙的に許容し、効率重視で重要な確認作業を省略してしまうケースが挙げられます。問題を指摘しやすい職場環境の構築や、業務のルール(標準)を守る重要性の意識醸成が重要です。
ここまで、ヒューマンエラーの原因について12分類に分けて概要をご紹介しました。このような原因が複雑に絡み合うことで、事故/トラブル発生につながるため、特効薬となるようなヒューマンエラー対策はありません。
近道・省略行動
時間や労力を節約するために、決められた手順や規則を無視して作業を行うことで、ヒューマンエラーを誘発してしまいます。たとえば高所作業を行うときに、『安全帯を付けるのはめんどくさいな…』と、必要な保護具を装着せずに作業を行ってしまうケースなどがあります。
なぜこの手順を守る必要があるのか?地道ではありますが、その理由を丁寧に伝えることが大切です。
単調作業による意識低下
単調な作業を長時間続けると集中力が低下し、ミスが発生しやすくなります。たとえば、データ入力業務で最初は正確に進めていたのに、同じ形式の作業が続く中で数字を入力し間違えるケースなどが挙げられます。
このようなミスを防ぐには定期的に休憩はもちろん、そもそも単調作業自体を減らせないか?自動化できないか検討することが重要です。
無知・未経験・不慣れ
初めて行う業務や経験不足により、業務内容の全容やポイントを理解できず、ミスにつながることがあります。たとえば、新しい作業内容を十分に習得していない新人が、手順を誤り修正対応の工数が発生してしまう場合などです。
このミスは、新人に限らず誰にでも起こり得るため、教育体制やマニュアルの整備が重要です。このような職場では、「いつでも正しい内容を学べる」ように動画マニュアルを活用している事例も増えています。
特に製造業においては、新人教育の改善があらゆる現場で課題となっています。製造現場の業務構造上、どうしても「OJT」に頼らざるを得ない場面が多く、教育担当者によって教育品質にバラつきが生じ、新入社員のスキルにバラつきが生まれるという構造が問題視されています。
製造現場における新人教育に潜む構造的な要因や、その改善策について知りたい方は、以下の画像をクリックしてPDF資料「新人教育に失敗する製造現場に潜む3つの構造的要因と新しい教育アプローチ」もあわせてご覧ください。
疲労
疲労が蓄積すると注意力や判断力が低下し、ヒューマンエラーを引き起こす可能性があります。たとえば、締切直前の長時間労働や休憩なしの作業が続く状況では、細かなミスが発生しやすくなります。
同じ作業の繰り返しやストレスの増加も要因となるため、適度な休憩を促し、作業環境を整備することがミス防止の鍵となります。
場面行動本能
突発的な状況に直面したときに、本能的な反応をとってしまうことでヒューマンエラーが発生します。
たとえば、そのまま見過ごせばよかった落下物を本能的にキャッチしようとして、ケガをしてしまうケースなどがあります。
高齢者の心身機能低下
加齢による視力や反応速度の低下は、ヒューマンエラーの原因となることがあります。若い頃は問題なくできた作業でも、加齢に伴う体力や感覚の衰えによりミスや事故を招くことがあります。
たとえば、重い荷物を過信して持ち上げようとして怪我をするケースが挙げられます。高齢者の負担を軽減するための作業支援や環境整備が重要です。とくに、製造業のような人手不足の産業では対応が急務でしょう。
パニック
異常事態が発生すると冷静さを失い、誤った判断や対応をしてしまうことがあります。とくに経験の浅い若手に多く見られ、慌てて解決を試みた結果、状況を悪化させる場合があります。
たとえば、機械故障時に無理な修理を行い、さらに故障を深刻化させるケースが典型です。緊急時の対応手順を明確にし、冷静な判断を促す教育が重要です。
連絡不足
作業者間や部署間での情報共有が不十分だと、ヒューマンエラーにつながります。「伝えたつもり」が原因となり、重要な変更が適切に伝わらない場合もあります。
たとえば、プロジェクトの仕様変更が共有されず、旧仕様で進行してしまうケースが挙げられます。このようなミスを防ぐには、明確な共有手段や定期的な確認ミーティングの実施が有効です。
共有手段として、「言った言わない」が起こらない動画マニュアルを活用している事例もあります。
次章からは、エラーの発生数をゼロに近づけるために「少なくとも実施しておきたい」ものを、全業界向け/製造業向けに計12例ご紹介します。
ヒューマンエラーの原因についてより詳しい解説を見たいという方は、専門家による以下の解説動画もご活用ください。
ヒューマンエラーを防ぐ7つの対策【ソフト面とハード面】
さまざまな業界や業種で適応可能な、ヒューマンエラー対策の具体例として以下の6つが挙げられます。
- 確認不足/思い込み/慣れがあってもエラーが起きない仕組みに(フールプルーフ化)
- エラーが起きた作業自体を無くす/自動化する
- 教育や研修で理解度が深まるような工夫をする
- なぜなぜ分析で根本的な原因を特定して対策を検討する
- 5S活動の定着でエラーの原因を日頃から排除する
- ヒヤリハット事例を社内で展開する
ヒューマンエラー対策は、ソフト面(人間の行動や意識を改善する対策)とハード面(装置や技術、仕組みによる対策)の両軸から対応していきます。
「製造業に特化した対策例を知りたい」「他業界の対策内容も参考にしたい」という方は、後述の『製造現場で実施したいヒューマンエラー対策6例』もご覧ください。
確認不足/思い込み/慣れがあってもエラーが起きない仕組みに(フールプルーフ化)
重ねてにはなりますが、ヒューマンエラーの発生をゼロにすることは現実的ではありません。そのため、ヒューマンエラーが起きても問題として顕在化しない仕組みにすることが有効的です。
このような仕組みは「フールプルーフ」と呼ばれ、ヒューマンエラーによるミスが労働災害や品質不良の流失といった重大トラブルにつながりやすい製造業を中心に用いられている考え方です。例えば、刃物を用いる設備では両手で掴んで作動する機構を採用し、挟み込みによる事故を防いでいます。
このように作業内容の確認不足や思い込み、慣れのようなヒューマンエラーは必ず起こるものという前提で、ミスが起きても重大な問題に発展しない仕組みを検討/導入するような対策も有効です。
関連記事:フールプルーフとはどういう設計?品質不良/ヒューマンエラーを未然防止する考え方、使用例を解説
エラーが起きた作業自体を無くす/自動化する
ヒューマンエラーの再発防止策として最も効果的なのは、問題が起きた作業自体を無くしてしまうことです。人の手が介在しなくても、業務が進むような状態にすることが理想的です。
単純業務だとしても減らせない作業の場合、ITツールや設備のようなハード面で自動化できないか情報収集することがオススメです。
作業を無くす、もしくは自動化することによってヒューマンエラーの再発防止につながることはもちろん、業務のムリムダムラを無くすことにも繋がります。
関連記事:3M(ムリ・ムダ・ムラ)を無くし業務効率化を図る!実施方法や改善事例も紹介
教育や研修で理解度が深まるような工夫をする
ヒューマンエラー対策として、従業員に対する再教育は不可欠です。
正しい作業手順を伝えるだけでなく、異なるやり方/意図的な省略によって起こりうるトラブルも伝えることで理解定着を助けます。一方で、1回の教育だけでは100%理解することはできません。
エビングハウスの忘却曲線をご覧いただくと分かるように、人は復習を重ねていくことで徐々に記憶として定着していきます。そのため、従業員自身が繰り返し自分で学べる仕組みがあると望ましいでしょう。
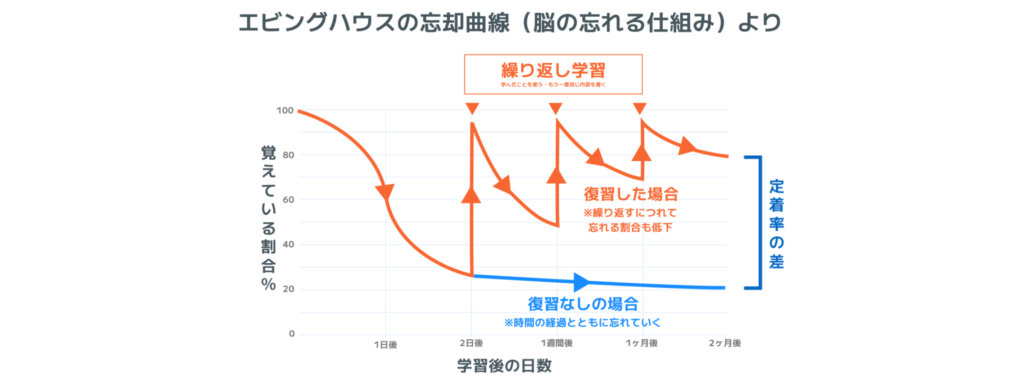
この仕組みに適切なのが「動画マニュアル」です。動画マニュアルであれば、一度正しい内容で整備することで、従業員自身が見たいときにすぐ確認できる状態になります。
人材育成における動画マニュアルの有効性について、詳しい解説は以下のリンクをクリックして参考資料をご覧ください。
>>「動画マニュアルで現場の教育をかんたんにする方法」を見てみる
なぜなぜ分析で根本的な原因を特定して対策を検討する
さまざまな対策を講じたものの『ヒューマンエラーが減らない…』という時には、なぜなぜ分析によって一度根本的な原因を深掘りすることをオススメします。
ひとえに「作業手順を誤った」という内容でも、その原因は多岐に考えられます。
- 作業者が理解が浅い状態で業務を進めてしまった
- 業務マニュアルが改訂されておらず、最新の手順と異なっていた
- OJTトレーナーによって伝達内容が異なっていた
- 先輩社員が忙しく質問しにくかった
上記はあくまでも一例ですが、トラブルによって顕在化した現象には複数の原因が考えられ、適切な対策も異なります。ヒューマンエラー対策には、根本的な原因(真因)を捉えて検討することが重要です。
根本的な原因を特定するためには、なぜなぜ分析によって「なぜ起きた?」を繰り返して真因を探ります。なぜなぜ分析の具体的な手法は、以下のリンクよりご覧ください。
関連記事:【テンプレ付】なぜなぜ分析のやり方は?トヨタ式のコツや事例、例題を解説
5S活動の定着でエラーの原因を日頃から排除する
ヒューマンエラー対策として、5S活動の定着も対策となります。5Sとは、「整理/整頓/清掃/清潔/躾(しつけ)」を総称した言葉です。
業務環境の整理や整頓がされていれば、作業に必要な材料探しで焦りや不注意、誤認識は起きにくいです。この状態を維持するためには、清掃や清潔に取り組む必要があります。
この一連のサイクルを躾として、ルール化していくことが職場のヒューマンエラー対策につながります。
業務改善につなげる5S活動の進め方は、以下のリンクをクリックしてご覧ください。
関連記事:「5S活動」とは何をする?進め方や目的、アイデアも解説
ヒヤリハット事例を社内で展開する
ヒヤリハットとは、業務中に危険と感じた出来事を指し、重大な事故につながりかねない状況を表します。
このようなヒヤッと・ハッとした出来事を社内で共有することで、似た場面に遭遇する従業員が危険性を意識するようになり、ヒューマンエラーの予防につながります。
また、そのヒヤリハットがなぜ起きたのか?原因を深堀することで、将来的な事故発生を未然に防ぐことにつながります。
ヒヤリハットを用いて職場の労働災害発生を予防する対策方法は、以下の記事で詳しく解説しています。
関連記事:ヒヤリハットとは?報告書の例文・書き方や対策方法、語源について
ミスを報告しやすい職場環境にする
上記のヒヤリハット報告共有にも通じますが、ミスを報告しやすい職場環境であることも大切です。
「怒られるのが怖い」「業務を止めてしまうのが申し訳ない」のように、心理的安全性が確保されていない職場環境だとミスが報告されにくいです。
結果的にトラブルの芽を隠してしまい、後々ヒューマンエラーによる大きな事故につながってしまうこともあるのです。
もちろん業務改善のために、ミスに対する注意は必要です。ただ、注意するときには個人を攻めるのではなく、トヨタ自動車のような「人を責めるな、仕組みを責めろ」という考え方のもと行うのが望ましいです。
ここまで多くの業界や業種で通じる、汎用的なヒューマンエラー対策を7つご紹介しました。ヒューマンエラーはさまざまな場面で起こり得るものの、発生時に大きなトラブルにつながりやすいのが製造業です。
そこで次章では、製造業に焦点を当てたヒューマンエラー対策の具体例を6つご紹介します。他業界で対策を講じるときのヒントにもなるので、ぜひこのままご覧ください。
【他業界でもヒントに】製造業で実施したいヒューマンエラー対策6例
製造業のヒューマンエラーは労働災害のような安全トラブル、不良品の市場流出といった品質トラブルなど、重大な企業問題につながりやすく対策の重要度が高いといえます。
製造業であれば実施したいヒューマンエラー対策例としては、主に以下の6つが挙げられます。
- ポカヨケでミスを発生させない
- 初めて/変更/久しぶり(3H)に該当する作業前にマニュアルを確認する
- 組立部品の種類を減らせないか検討する
- フェイルセーフの考えに沿った生産ラインを確立する
- 4Mに変化や変更がないか管理をする
- 危険予知訓練(KYT)を定期的に実施する
『他にオススメの対策例を知りたい!』『対策検討時の視点や考え方を把握したい』という方には、製造業のヒューマンエラー対策に焦点を当てたガイドブックを別途ご用意しています。
以下のリンクをクリックして、ガイドブックもご活用ください。
>>「製造業におけるヒューマンエラーの未然防止と具体的な対策方法」
ポカヨケでミスを発生させない
ポカヨケとは、主に製造現場で人による作業ミスを防ぐ仕組み/装置のことです。
作業ミス(ポカミス)の発生を防ぐ仕組みを整えることで、工程内不良の発生や労災のような事故発生につながります。結果的に生産ラインの停止頻度も減るため、生産性向上の効果も期待することができます。
ポカヨケによるポカミス対策の進め方は、以下の画像をクリックして専門家による無料の解説動画をご覧ください。
初めて/変更/久しぶり(3H)に該当する作業前にマニュアルを確認する
ヒューマンエラーのようなミスは、初めて行う作業や従来の手順に変更があった作業、久しぶりに行う作業で発生しやすいです。
これらは総称して3Hと呼ばれ、ヒューマンエラーを未然に防ぐ対策として焦点を当てると有効です。製造現場の3H対策には、動画マニュアルを用いられるケースがあります。3Hに対する動画マニュアルの有効性は以下の通りです。
- 初めて :作業内容や動さを視覚的に分かりやすく理解できる
- 変更 :変更された工程だけ内容調整でき、マニュアル/手順書の改訂工数が効率的
- 久しぶり:作業前に注意点やポイントを視覚的に再確認できる
とくに3Hの場面が発生しやすい、多品種少量生産の製造現場でオススメの対策です。多品種少量生産の現場における動画マニュアル活用事例は、以下のインタビュー記事をご覧ください。
>>「多品種少量生産の現場における動画マニュアル活用事例」を見てみる
組立部品の種類を減らせないか検討する
ヒューマンエラーを減らすためには、発生機会となる作業自体を減らす動きが有効です。
とくに組付け作業時におけるヒューマンエラーは、製品特性にもよって変わるものの品質/安全トラブルが起きやすい工程といえるでしょう。作業時に必要な部品数を減らすためには、製品開発時のDR(デザインレビュー)がカギを握ります。
DRを行う段階で関連部署の意見を募り、製品の設計開発に反映させることで、人の手が介在する部分を減らす効果が期待できます。
フェイルセーフの考えに沿った生産ラインを確立する
フェイルセーフとは、設備やシステムに異常が発生しても安全に停止する仕組みのことです。
どれだけ教育に力を入れて手順遵守の意識が醸成されていたとしても、設備の異常傾向などが保全活動で見過ごされていると、ヒューマンエラーの発生につながってしまう恐れがあります。このような製造現場のリスクを最小限に抑える仕組みがフェイルセーフです。
関連記事:フェイルセーフとは?フールプルーフとの違い、安全性を確保するための考え方を解説!
4Mに変化や変更がないか管理をする
4Mとは、Man(人)・Material(材料)・Machine(機械)・Method(方法)の頭文字で、製造現場を構成する主要要素を指します。
この4Mにおいて、何らかの意図しない変化や意図的な変更が加わった場合、トラブルが起きやすいため注意が必要です。4Mに何らかの異常が発生を防ぐためには、変化点管理や4M変更を通知する手順書の改訂や再教育が必要です。
4M変化と4M変更の違い、効果的な変化点管理の手法は専門家による解説動画で詳しく解説しています。無料でご覧いただけますので、以下のクリックをしてご覧ください。
>>「トヨタ流品質管理に学ぶ!はじめての変化点管理」の解説動画を見てみる
危険予知訓練(KYT)を定期的に実施する
ミスやヒューマンエラーを対策するには、「どのような場面でミスやヒューマンエラーが発生するのか」といった潜在的な要因を予測する力をつけることも効果的です。このような予測する力を養う方法が、危険予知訓練(KYT)と呼ばれる手法です。
危険が潜む現場の写真やイラスト、動画を提示し、どのようなリスクがあるのかを複数名で洗い出し、対策案を見極めるトレーニングです。
「あいまい」「マンネリ化しない」実践的なKYTの方法は、専門家による解説動画【効果のあるKYTとは:KYTの実情、3つの課題とその解決策】をご覧ください。
ここまで、製造業であれば実施しておきたいヒューマンエラー対策を6つご紹介しました。製造業に焦点を当てたものの、考え方としては他業界にも転用できる内容です。
『他にも具体的な対策例を知りたい!』『ヒューマンエラー対策の考え方や視点を把握したい!』という方は、より詳しく解説しているガイドブックを以下の画像をクリックしてご覧ください。次章以降では、効果的なヒューマンエラー対策を講じている企業事例、ヒューマンエラー対策で活用されているツールを解説します。
ヒューマンエラーに対するトヨタの考え方は?
ヒューマンエラーを減らすためにできることは何か?考え抜いている会社がトヨタ自動車です。トヨタ自動車では、製造現場の効率的と生産性を高めるため「トヨタ生産方式」を確立しています。
生産性を担保するため、ヒューマンエラーとどのように向き合ってきたのか、トヨタ自働車でトップ技能者と認定され、社内研修の講師としての経歴がある伊藤 正光氏によるセミナー講演の内容を抜粋してご紹介します。
トヨタ流のヒューマンエラーに対する考え方は以下の2つです。
1.ヒューマンエラーをゼロにすることは困難。極力少なくするしかない。
2.ヒューマンエラーを抑えるためには、標準作業を確立し、守る以外に道なし。
今の世の中では数多くの電車が動いていますが、ミスはほとんど出ていません。それは運転手の手順が標準として確立されひたすら遵守しているからです。
数値が誤入力のようなミスがなぜ起きるのか?なぜなぜ分析で洗い出すと以下の4つが挙げられ、この中に必ず原因があります。
・標準作業を守らなかった
・標準作業を守れなかった
・標準作業が確立されていない
・標準作業はあるが定着していない
原因の原因、真因を特定するためのなぜなぜ分析は「標準作業」がスタートとなります。
このように、トヨタ自動車におけるヒューマンエラー対策の軸は「業務の標準(ルール)を守ること」であることがお分かりいただけると思います。
次章では、ヒューマンエラー対策を目的に業務標準化を推進している企業事例と取り組み内容を詳しく解説します。
効果的なヒューマンエラー対策を講じている企業事例
本章では、ヒューマンエラー対策を講じている好事例を2社ご紹介します。どちらも「動画マニュアルによる業務標準化」によって、ヒューマンエラーのような作業ミスを減らしたケースです。
どのようにして業務標準化を推進しているのか具体的に解説します。動画マニュアルの有効性や、その他の活用事例については以下のガイドブックもご活用ください。
- 「現場教育に動画マニュアルを活用する有効性」を見てみる
- 「業界別の動画マニュアル活用事例」を見てみる
【製造業】児玉化学工業株式会社
住宅設備や自動車向けの樹脂製品を製造/販売する児玉化学工業株式会社では、動画マニュアル活用による業務標準化に取り組み、手順不遵守による品質不良を9割削減しています。
▼インタビュー動画:児玉化学工業株式会社▼
新人の従業員や外国人従業員を抱え、紙の作業手順書/マニュアルでは作業の手順やコツを伝えきれなかった同社は、動画マニュアルを活用したことで作業内容を視覚的にわかりやすく伝えることができました。
従業員が理解しやすくなかったことで作業手順の標準化が進み、結果的に手順不遵守による品質不良を9割削減しています。より具体的な、動画マニュアルによる手順不遵守の改善事例は、以下のリンクをクリックしてインタビュー記事をご覧ください。
インタビュー記事:手順書作成の工数は紙の1/3になったと思います。動画で作るのはかんたんだし、学ぶ側にもわかりやすいですよね。
【物流業】株式会社ジェイ・メイト
株式会社ジェイ・メイトはスーパーの店舗配送を行う物流センターで、メーカーから届いた商品を受け入れて、配送店舗別に各商品を仕分ける作業を行っています。現場は24時間365日稼働しており、ベトナム人を中心とした多くの外国人も働いています。
24時間稼働の物流センターであるため、トレーナーと新人のシフトがあわない、外国人スタッフに言葉が通じない、教える人によって内容が違うなどの理由で、人的な仕分けミスを減らすための教育が十分にできていないことが課題でした。
そこで同社は、仕分けミスをしてしまう間違った手順と正しい手順を動画に残すことにしました。スタッフ全員に動画を見せた後に、仕分けミスが起きる都度、ミスした人に現場でタブレット端末で動画を見せて再教育する、ということをやったところ、1ヶ月目あたりから大きくミス発生率が下がり、半減させること成功しています。
インタビュー記事:効率よく再教育することで、倉庫内作業の仕分けミスが半減!
ヒューマンエラーの根本原因「標準化の形骸化」は動画マニュアルで解決できる理由
これまで様々なヒューマンエラー対策をご紹介しましたが、その多くが失敗に終わる現場には共通点があります。それは、ヒューマンエラーの根本原因である「標準作業が浸透していない、守られていない」という課題です。
トヨタ生産方式が示すように、エラー対策の根幹は「確立された標準作業を守ること」。しかし、従来の紙マニュアルやOJT頼みの教育では、この「標準化」がどうしても形骸化してしまいます。
そこで、現場教育に特化した動画マニュアル作成ツール「tebiki現場教育」は、この「標準化の壁」を乗り越え、ヒューマンエラー対策を本質的なレベルで実現します。その理由は、動画が持つ3つの圧倒的な力にあります。
1.【指導のバラつき撲滅】 全員が「1つの正しい手順」を共有できる
「A先輩とB先輩で教え方が違う…」これは、標準化を阻む最大の要因です。OJTに依存する限り、指導品質のバラつきは避けられず、人によって手順の解釈が異なってしまいます。
動画マニュアル(tebiki)なら、「人によって教え方が異なる」は一切発生しません。 熟練者の正しい動きをそのまま全社で共有できるため、指導のバラつきがゼロになり、誰もが同じ正しい手順で作業できるようになります。
2.【解釈のブレを追放】 作業を「見たまま」正しく理解できる
文字だけのマニュアルでは、「ゆっくり」「しっかり」といった表現の解釈が個人の感覚に委ねられ、ミスを誘発します。 動画(tebiki)なら、作業を「見たまま」直感的に理解できます。
正しい動きとNGな動きを映像で見比べれば、なぜその手順が必要なのか、どこに危険が潜んでいるのかが一目瞭然です。教育やマニュアルの解釈のブレが生じないため、全員が迷いなく正しい作業を実践できます。
3.【学習の定着促進】 「繰り返し見る」ことで、手順が体に染み付く
正しい手順も、1度教えただけでは身につきません。しかし、分厚い紙のマニュアルを何度も読み返すのは、誰にとっても負担です。
動画(tebiki)は、紙媒体よりも学習ハードルが圧倒的に低く、反復学習に最適です。 スマートフォンでいつでも・どこでも・何度でも簡単に見返せる手軽さが、学習の継続を促します。
この「繰り返しの学習」こそが、作業手順を頭だけでなく体に染み込ませ、ヒューマンエラーの起きにくい状態を作り上げるのです。
例えばとある製造現場では、操作する機械の前にタブレットを設置し、機械の操作方法が動画で常に流れるような環境を作り、誰が担当しても作業手順のミスが発生しないよう徹底している、というようなケースがあります。
このように動画マニュアルは、「指導のバラつき」と「解釈のブレ」をなくし、「学習の定着」を促すことで、ヒューマンエラーの根本原因である「標準化の未浸透」を解消します。
「人を責める対策」ではなく、「仕組みで標準化を浸透させる仕組み」を作るために動画マニュアルを少しでも検討している方は、現場作業員でもカンタンに作れる動画マニュアル作成ツール「tebiki現場教育」のサービス資料をご覧ください(下の画像をクリック)。動画マニュアル導入のメリットや詳細な機能がまとめられています。
【補足】ヒューマンエラーによって引き起こされた有名な事故/具体例
ヒューマンエラーはときに企業にとって深刻な影響を及ぼします。ここではヒューマンエラーによる有名な事故や具体例をご紹介します。
- みずほ証券のジェイコム株大量誤発注事件(2005年)
- 年金記録5,000万件の不備問題(2007年)
- 新幹線のぞみ34号台車亀裂事件(2017年)
みずほ証券のジェイコム株大量誤発注事件(2005年)
2005年に起きたみずほ証券のジェイコム株大量誤発注事件は、データ入力ミスによるものです。
みずほ証券のスタッフが本来の注文として「1株を610,000円で売る」と入力すべき個所に対し、「610,000株を1円で売る」と誤って入力したのが原因です。このミスは、コンピューターシステムの警告を無視してデータを入力したため発生し、注文が完了した後で発見されました。
キャンセルを試みたものの失敗し、この誤発注はみずほ証券に約30億円の損失をもたらしました。本事件は株式市場に大きな影響を与え、みずほ証券自身にも財務的な大きなダメージを与えました。
年金記録5,000万件の不備問題(2007年)
2007年に起きた年金記録5,000万件の不備問題は、日本の社会保険庁でのデータ管理のミスにより発生しました。
当時、マイナンバーのような国民1人1番号という制度がなく、国民年金や厚生年金保険、共済組合などの年金制度によって年金記録番号が異なっていたため、1人の個人に複数の異なる番号を使用する必要があり手続きが煩雑でした。
そこで、行政はこれらの年金記録を10桁の番号に統一させようとしていました。しかし、コンピュータに年金番号があるものの、基礎年金番号に統合・整理されていない記録が約5000万件あることが判明しました。また、過去の紙台帳からコンピュータへの記録の転載が不正確だったことが原因だと指摘されています。
この不備は、年金記録が基礎年金番号に正しく統合されず、多くの記録が持ち主不明となる結果を招きました。この問題は、公的年金制度への信頼を大きく損ない、国民からの批判を集めると同時に行政の情報管理能力に疑問を投げかけることとなりました。
新幹線のぞみ34号台車亀裂事件(2017年)
2017年に起きた新幹線のぞみ34号台車亀裂事件は、博多〜東京行きのJR西日本の新幹線車両の台車で亀裂が発見された事件です。台車の亀裂は14cmにも達しており、あと3cmで台車が破断するという深刻な状態でした。
この不備は走行中の異音・異臭が確認されたにもかかわらず、運行を継続したことが原因となっています。この事件は名古屋駅での床下点検により油漏れが発見され、運転が中止されました。幸い被害者は出ませんでしたが、脱線事故につながる危険性があったと判断され鉄道安全管理の重要性を浮き彫りにしました。
【補足】ヒューマンエラーに関するQ&A
ヒューマンエラーが多い人の特徴は?
ヒューマンエラーが多い人の特徴と原因として、以下の内容が挙げられます。
- 注意力が散漫な人:身体的、精神的不調を抱えている可能性
- 知識や経験が不足している人:業務未熟や相談不足が原因
- 自分の能力を過大評価している人:慢心や自己過信による誤判断
- コミュニケーションが足りていない人:情報共有不足で認識のずれが発生
これらの特徴に共通するのは、適切なサポート体制や情報共有の不足、自己認識の欠如です。環境整備やコミュニケーション強化、冷静な状況判断がミス防止の鍵となります。
ヒューマンエラーは教育だけで防げる?
ヒューマンエラーの対策は教育だけで完全には防げませんが、適切な教育を行うことで作業手順や安全対策への理解を深め、発生を効果的に減らすことが可能です。
研修を通じて意識を高め、ミスの要因を理解して対策を講じることで、未然予防と迅速な対応が実現します。
また、動画マニュアルを活用することで教育のムラをなくし、正確な手順を伝える効果が期待できます。教育はヒューマンエラーの軽減に重要な役割を果たします。
ヒューマンエラーはゼロにできる?
ヒューマンエラーを完全に無くすことは不可能ですが、そのリスクを最小限に抑えることは可能です。
エラーは人間の特性や環境変化が要因で常に発生し得るため、未然予防策を講じるとともに、ミス発生時の対処法を確立することが重要です。
ヒューマンエラー対策は個人だけでなく組織全体で取り組むべき課題であり、リスク管理を徹底することで安全性を高めることができます。
機械のトラブルはヒューマンエラーに含まれる?
機械トラブルは、老朽化や消耗など人間の行動に起因しない場合、ヒューマンエラーには含まれません。
一方、社内で作成したマニュアルに記載漏れや検討不足があり、それが原因でミスが発生した場合はヒューマンエラーに該当します。原因の明確化と適切な対応が重要です。
ヒューマンエラーに近い言葉は?言い換え
ヒューマンエラーに近い言葉には「人為的ミス」と「人災」があります。
人為的ミスは個々の誤判断や行動による小規模なミスを指し、操作ミスや情報の誤解が該当します。一方、人災は人間の過ちによる大規模な災害や事故を指し、工業事故や環境汚染などが含まれます。
ヒューマンエラーに含まれないミス
ヒューマンエラーとは人間の行動によるミスを指し、機械の老朽化や消耗によるトラブルは含まれません。
ただし、社内で作成したマニュアルの記載漏れや不備が原因の場合はヒューマンエラーに該当します。また誤った行動だけでなく、やるべきことを怠った場合はヒューマンエラーに含まれます。
【まとめ】動画マニュアルを活用してヒューマンエラー対策を推進
ヒューマンエラーは不注意や疲労といった人間による行動を起因として発生した失敗や事故のことです。作業工程ごとにヒューマンエラーが発生するメカニズム・要因を明確にしてから適切な対策を取ることで、後工程や自社に大きな影響を与えるようなトラブルを避けることが期待できます。
本記事では、ヒューマンエラーの分類や発生のメカニズム、ヒューマンエラーを解消するための具体的な対策について解説しました。
ヒューマンエラーを効果的に防ぐためには、発生の原因となる人への教育が重要です。教育には様々な方法がありますが、ヒューマンエラー対策には動画マニュアルによる教育が有効です。動画マニュアルを活用することによって従業員は作業手順を正しく理解することができるため、ヒューマンエラーを効果的に防止することができるでしょう。
現場教育システム「tebiki」の機能やプランなど、詳細は以下のバナーをクリックするとご覧いただけます。ヒューマンエラーを削減する手段として、動画マニュアルをご検討ください。