かんたんデジタル現場帳票「tebiki現場分析」を展開する、現場改善ラボ編集部です。
変化点とは、製造工程における意図的な変化・意図的ではない変化を指します。変化点管理を行うことで、品質や安全、生産性といった重要指標のトラブルに発展することを未然に防ぐことができます。
本記事では、製造現場の変化点を見える化し、変化点管理を行う4ステップを詳しく解説します。適切な変化点管理で重大トラブルを未然防止した事例、トヨタ流の変化点管理のポイントもご紹介しているので、ぜひご覧ください。
目次
変化点管理とは?製造現場が行うべき重要性
変化点管理は、製造工程における変化を正確に捉え、コントロールすることで品質不具合や異常の発生を未然に防ぐ手法です。
製造現場では日々変化が起こり、変化が品質不具合の原因となりえます。このような変化を早期に検知し、適切な改善策を講じることが変化点管理の狙いです。
変化点とは
変化点とは、何かが変わる瞬間や場所、または状況が変わる具体的な点を指します。製造業では、小さな変化が大きな品質問題を引き起こす可能性があるため、変化点を正確に把握することが重要です
たとえば、以下のようなケースが変化点として該当します。
- 生産ラインで設備が前触れもなく故障した
- 設計変更の適用に伴い、使用部品や材料の仕様変更
- 作業効率や品質改善を目的とした、作業手順の計画的な変更
- 仕掛品から前工程で発見されなかった品質不具合の発見
- 担当作業員の欠勤で、代理作業者が急遽その作業を担当する など
例に挙げた変化は、製品の品質に直接影響を及ぼす可能性があるため、変化点を正確に把握し管理することが品質維持の肝といえます。
変化点の例として5つご紹介しましたが、さらに細分化すると、これらは「計画的変化点」と「突発的変化点」の2つに分けられます。本記事では、後者の突発的変化点に焦点を当てて、管理方法 / 見える化について解説していきます。
前者の計画的変化点は意図的な変更であり、特徴や取り組むべき対策が異なるため、以下の記事で詳しく解説しています。
関連記事:4M変更とは?通知義務の有無や管理しやすくする方法も解説!
変化点管理の目的は?品質・安全・生産性に与える重大な影響
変化点管理の目的として、製品品質の担保や従業員の安全性確保、現場の生産性といった重要指標の改善が挙げられます。
ここからは、変化点を見過ごすことによる品質・安全・生産性への影響を整理し、管理を行う重要性について解説します。
品質への影響:積み重なる不良と失われる信頼
『いつもと材料の粘度が違う気がするけど、まあ、いいか』『機械の動きが少しおかしいけど、とりあえず動いているから大丈夫だろう』といった変化を見過ごすことで、品質不良につながることがあります。
たとえば、材料の変化点を軽視して稼働しつづけた結果、製品に予期せぬ強度不足や色ムラが発生し、市場への不良流失やクレームに繋がるケースが挙げられます。また、機械の異音や振動といった変化を無視した結果、加工精度が徐々に狂い、気づいた時には大量の寸法不良品が後工程に流出してしまった、などのケースがあります。
このような変化を見過ごすことで、重大な品質問題につながるリスクがあり、問題の程度によっては顧客信頼の失墜といった形で、ブランドイメージの低下や取引停止となる恐れもあります。
関連記事:【品質改善】製造業の品質向上策9選!改善事例も解説
安全への影響:一瞬の油断が生む取り返しのつかない事故
『安全装置のエラー表示が出ているけど、後で確認しよう』『化学薬品の容器に少しヒビが入っているけど、漏れてはいないから大丈夫だろう』など、危険な兆候を示す変化を見過ごすことで、従業員の安全を脅かす重大な労働災害に直結します。
たとえば、設備メンテナンス後に安全囲いのボルトが1本締め忘れた結果、振動で囲いが外れ、作業員が回転部に巻き込まれる事故につながったといったケースです。また、作業者自身の「慣れ」による安全作業の省略も突発的な変化とも言え、安全意識の低下が重大事故につながりかねません。
関連記事:工場の安全対策10選と好事例を解説!製造業の安全宣言例も紹介
生産性への影響:止まるライン、膨らむコスト
『機械から変な音がするけど、納期が近づいているから生産を続けよう』など、設備異常のような変化への対応の遅れがライン上のトラブルを引き起こし、結果的に製造現場の生産性低下や工場の収益性へ悪影響を及ぼします。
設備の不具合を見過ごすことで、チョコ停の頻発による稼働率の低下や、長時間のライン停止(ドカ停)による生産性悪化が起こり得るでしょう。また、前述の品質トラブルによって、原因究明~手直しといった追加作業とコストが発生します。最悪の場合、製品回収(リコール)に至れば、その費用は莫大です。
関連記事:製造現場の生産性が67%向上した事例や改善方法【指標や計算式も解説】
管理すべき「4M3H」「5M+1E」の変化
前章では変化点管理の基礎知識、重要性を解説しました。製造現場の変化を適切に捉え、問題の初期段階で対策を講じることが、製品品質の担保につながります。
ここからは、製造現場で管理すべき具体的な変化について、「4M3H」と「5M+1E」の2つの視点に分けて解説します。
4M3H
4M3Hとは、4M(Man、Machine、Materia、Method)と3H(初めて、変更、久しぶり)の頭文字を取った言葉です。
▼4Mに関する変化の例▼
Man(人) | 担当作業員の急病による突然の欠勤、それに伴う未熟練者の緊急投入、作業中の集中力低下によるヒューマンエラー(指示の聞き間違い、手順の飛ばし)、慣れた作業における「うっかりミス」。 |
Machine(機械・設備) | 稼働中の機械の予期せぬ故障・停止、センサーの突然の誤作動、点検では見つからなかった内部部品の破損、使用中の治工具の突発的な破損やズレ。 |
Material(材料) | 納入された材料ロット内での予期せぬ品質ばらつき(成分、物性値)、輸送・保管中に発生した材料の変質・汚損、仕掛品への予期せぬ異物混入。 |
Method(方法) | 緊急対応やイレギュラー処理による通常とは異なる作業手順の適用、指示系統の混乱による誤った指示の伝達、災害時など緊急時の作業手順の不備。 |
このような突発的な変化を見過ごすことによって、品質・安全・生産性に関わるトラブルにつながるリスクがあります。また、3H(初めて、変更、久しぶり)の状況は、それ自体がヒューマンエラーのリスクを高めますが、これらの状況下でさらに「突発的な変化」が発生した場合、リスクはさらに増幅します。
▼3Hに関する突発的な事態の例▼
初めて | 新人作業員が初めての作業中に予期せぬ設備アラームに遭遇し、パニックになって誤った処置をしてしまう。 |
変更 | 作業手順が変更された直後に、材料に予期せぬ異常が見つかり、古い手順の知識と新しい手順の知識が混同してしまい、対応を誤る。 |
久しぶり | 久しぶりに操作する機械で、勘が鈍っているところに突発的な停電が発生し、復旧手順を誤って設備を破損させてしまう。 |
4Mの変化を捉えるだけでなく、3Hの状況も重点管理することで、トラブルを未然に防ぐ効果が期待できます。
5M+1E
5M+1Eは、4M(Man、Machine、Material、Method)に加えて、Measurement(計測)とEnvironment(環境)を含む言葉です。この視点で変化点を管理することで、4Mだけでは捉えきれない突発的変化のリスクへの気づきを促します。
▼計測や環境に関する変化の例▼
Measurement(計測) | 使用中の測定器が突然故障したり、精度が狂ったりする、検査員が体調不良などで集中力を欠き、不良品を見逃してしまう(誤判定)、停電等で検査記録データが消失する。 |
Environment(環境) | 突然の停電や瞬時電圧低下、空調設備の突発的な故障による急激な温度・湿度変化、近隣の解体工事による予期せぬ粉塵の飛来や振動の発生、ゲリラ豪雨による工場内への浸水。 |
4M3Hや5M+1Eなど、本章でご紹介したような変化点は予測することが困難です。だからこそ、製造現場の変化を初期段階で捉えられるように見える化を図りつつ、重大なトラブルにつながる変化への感度を高めることが大切です。
次章では、製品品質を担保するための変化点管理の方法や、変化点を見える化するコツを解説します。
変化を見つけて対策する変化点管理の4ステップ
変化点管理を効果的に機能させるためには、場当たり的な対応ではなく、一連のプロセスとして体系的に進めることが不可欠です。
ここからは、製品品質を担保する変化点管理の方法、変化を見える化するコツを詳しく解説します。本記事では突発的変化点に焦点をあてて解説します。計画的変化点(意図的な変更)の管理方法を知りたい方は、変更管理に関する別記事をご覧ください。
現場改善ラボでは、元デンソーの原嶋 茂氏による「トヨタ流の変化点管理」に関する解説動画を無料で公開しています。以下のリンクをクリックして、解説動画もご活用ください。
>>専門家による「トヨタ流品質管理に学ぶ!はじめての変化点管理」の動画を見てみる
ステップ1:製造現場の変化を「見える化する仕組み」を整える
変化点管理を行うためには、平常状態からの逸脱、すなわち「変化」またはその「兆候」を、可能な限り網羅的に、かつ早期に検知できる仕組みを整えなくてはいけません。
変化を捉える手段の1つとして、製造日報や点検表のような現場帳票の集計や分析をまずはオススメします。設備にIoTセンサーを取り付けて自動計測する方法もありますが、仕組みの整備に人やコストなどリソースを多く必要とするため、ハードルが低い手法として「現場帳票」の活用がよいでしょう。
そして、現場帳票で集めた記録を、QC7つ道具のパレート図や管理図などを用いて分析することで、4Mや5M+1Eのあらゆる現場の変化を視覚的に見える化することができます。
一方で、紙やExcelによる現場帳票の運用の場合、集計作業や分析で『膨大な工数が発生する』『分析できる人が属人化している』といったお悩みを伺うことがあります。そこで、かんたんデジタル現場帳票「tebiki現場分析」のような、記録の自動分析(グラフ化)機能も備わった帳票電子化ツールを用いることで、手間なく変化をリアルタイムで見える化することが可能です。
▼デジタル現場帳票で変化点を見える化するイメージ▼
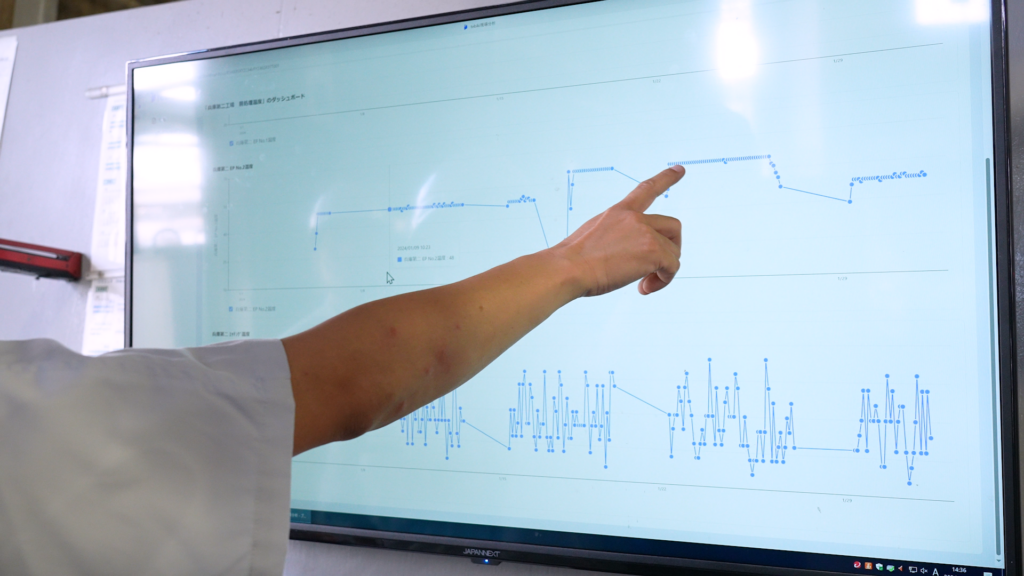
「現場帳票デジタル化事例:株式会社日本電気化学工業所」より抜粋
現場帳票をデジタル化することで、変化点の記録が即座に管理者に届き、変化度合いもリアルタイムで計測することができるため、見える化の仕組みとして効果的な手段の1つです。
現場帳票をデジタル化する効果や方法、具体的な改善事例をまとめた資料もあるので、以下のリンクをクリックして資料もご活用ください。
>>PDF資料「はじめての現場帳票デジタル化ガイド」を見てみる
ステップ2:変化が起きた原因を特定する
変化という事実を捉えたら、すぐ対策に入るのではなく、まず「なぜその変化が起きたのか?」という原因を特定することが重要です。
なぜなら、表面的な事実だけを見て対策を講じても、真の原因が別にあれば問題が再発するからです。 例えば、製品に傷が多発したという「事実」に対し、作業者が原因として注意や再教育を行ったものの、実は製品を搬送する際の治具の一部が摩耗していたことが真の原因であり、結局どの作業者が担当しても傷が再発してしまった、というようなケースは製造現場では往々にして起こり得ます。
初期段階で原因の当たりをつけることが、的外れな再発防止策を防ぎ、効果的な打ち手へ繋げる第一歩となるのです。
そこで、まずは変化を示す記録を行った作業者に、「いつもと違った点は?」「何か心当たりは?」といった質問で事実情報を引き出します。そして必ず現場・現物・現実を直接確認し、客観的な情報を集めます。
収集した事実に基づき、4Mの観点から原因仮説を複数考えます。それぞれの観点を深掘りするときには、なぜなぜ分析を通じて、客観的に最も可能性の高い真の原因を推定します。
このステップでの注意点は、あくまで初期判断に留め、深追いしすぎないこと(迅速性重視)、思い込みを排し客観的事実に基づき判断すること、そして推定した原因と根拠も明確にすることです。
現場改善ラボでは、なぜなぜ分析が考案されたトヨタ自動車流に基づく、正しい実践方法を解説した資料を公開しています。以下の画像をクリックして、参考資料として併せてご活用ください。
ステップ3:変化が製造現場にもたらす影響評価と対策計画
ステップ2で変化の原因を明確にしたら、その変化がもたらすリスクを評価(リスクアセスメント)し、具体的な対策を計画します。原因の性質を踏まえることで、的確なリスク評価と対策立案が可能です。
まず、特定された原因に基づき、その変化が品質・安全・生産性・コストなど、現場の重要な指標や管理点に及ぼす具体的な影響を予測して評価します。その際、発生の可能性と影響度など、リスクの大きさを考慮して対応の優先順位を判断することが重要です。
そして、優先順位が高いリスクから順に、原因除去や影響緩和のための具体的な対策を計画します。必要に応じ、応急的な「暫定対策」と根本解決を目指す「恒久対策」を区別します。
計画は「何を」「誰が」「いつまでに」「どのように」行うか(5W1H)を明確にし、担当者や期限、効果検証の方法も定めます。
When(いつ) | 対策をいつ開始し、いつまでに完了させるのか? |
Where(どこで) | 対策を実施する具体的な場所、対象となる工程や設備はどこか? |
Who(誰が) | 対策実施の担当者や責任者、関連部署は誰か? |
What(何を) | 対策の具体的な内容は何か? |
Why(なぜ) | 対策実施の目的、どのリスクに対応するものなのか? |
How(どのように) | 対策をどのような手順やツール、方法(条件)で実施するのか? |
ステップ4:対策効果の評価と標準化の徹底
対策を実施したら、それが狙い通りの効果を発揮したかを客観的に評価し、有効性が確認された場合は組織の標準として定着させる、変化点管理サイクルの最終段階です。
まず、効果測定・評価では計画に基づき、一定期間データを収集します。品質データ(不良率、測定値)、生産性指標(サイクルタイム、設備総合効率)、安全に関する記録などを対策実施前と比較し、対策の有効性を定量的に評価します。同時に、対策によって新たな問題(副作用)が発生していないかも確認することが重要です。
データ収集については、ステップ1で示したように製造現場を見える化する方法を、先んじて明確にしておくことで手間なく効率的に行うことができます。評価結果を関係者で確認し、もし効果が不十分、あるいは新たな問題が見つかった場合は、ステップ2やステップ3に戻り、PDCAサイクルを回します。
対策が有効であると判断されれば、新たな現場の作業ルールとして標準化の徹底を図ります。
標準化を行う際には、作業の基準となる作業手順書やQC工程表など標準文書を改訂することが基本です。改訂された標準を関係者全員に確実に周知徹底し、必要であれば現場教育を実施して理解と遵守を促します。
この手順書に盛り込まれている内容は「正しい動作」が中心です。作業者へ理解を促す周知徹底ももちろん重要ですが、内容を分かりやすく伝えられているか?という視点も同時に重要です。正しい動作を分かりやすく伝える手段として、視覚的に学べる「動画マニュアル」を活用する製造現場も増えています。
▼動画マニュアルによる標準化推進事例▼
【インタビュー記事:新日本工機株式会社より抜粋】
同社の標準化推進のような、動画マニュアル活用による業務改善事例をまとめた資料も用意していますので、以下のリンクをクリックして、参考情報としてご覧ください。次章では、実際に現場の変化を即座に捉え、品質不良の発生を未然に防いだ管理事例を詳しくご紹介します。
>>PDF資料「製造業における動画マニュアル活用事例集」を見てみる
変化点を見過ごさず、品質不良を未然に防いだ管理事例と手段
ここまでご紹介したように、変化点管理では製造現場の不具合傾向を早期に捉え、大きなトラブルに発展する前に対策を講じることが重要です。
本章では、設備の変化点を早期に捉え、設備異常による不良品発生を未然防止した製造業の管理事例をご紹介します。
変化点を早期に捉え、トラブルを未然に防いだ製造業の好事例
株式会社 日本電気化学工業所は、アルミニウムの表面処理を専門に行う会社で、製品品質を担保するために「処理槽の温度記録」や、完成品のアルマイト皮膜の品質を検査する機器の精度維持を目的とした「計測機器日常点検記録」のデータを現場帳票で収集していました。
しかし、紙ベースで帳票管理を行っていたことで、異常値のような現場の変化の検出に時間を要し、迅速な対応が難しい状況がありました。そこで、現場帳票のデジタル化をに取り組み、製造工程における重要なパラメーターをリアルタイムで確認、異常傾向の早期発見と迅速な対応が可能になりました。
▼インタビュー動画:株式会社 日本電気化学工業所▼
実際のエピソードとして、ツール上で普段とは少し異なる温度データの変化に気づき、わずかな温度変化に注目して、設備点検を行ったところ、配管に小さな穴が開いていることが判明したという声も挙がっています。
同社の具体的な変化点管理の取り組み内容を知りたい方は、以下のリンクをクリックしてインタビュー動画をご覧ください。
インタビュー記事:品質不良の未然防止をリアルタイムデータで実現。異常値検知を迅速にできた理由。
製造現場の変化点をかんたんに見える化できる手段
株式会社日本電気化学工業所の事例のように、変化点管理を行う方法として「現場帳票のデジタル化」は効果的な手法の1つです。一方で、現場帳票はあくまでも現場データの収集に過ぎず、変化点を見える化するためにはQC7つ道具のような分析が必要なデジタルツールが多いです。
その中でも、自動分析機能を搭載し、効率的にリアルタイムの変化点管理を行える手段が、かんたんデジタル現場帳票「tebiki現場分析」です。一般的な帳票デジタルツールとは異なり、記録データの自動計算機能や自動分析(グラフ化)機能を搭載し、ダッシュボード上で製造現場の変化をリアルタイムで可視化できる点が特徴的です。
- 項目ごとに正常値設定が可能:正常値以外の記録は異常値として管理者にアラートが届く
- 使いやすいインターフェース:デジタル端末に不慣れでもかんたんに操作可能
- 正しい現場データを蓄積:マスタの登録、バーコード読取による情報入力、画像記録も可能
- データ分析の専門知識は不要:パレート図や管理図、テーブル形式の表示が自動で更新
帳票の検索機能やCSV出力など、管理面の機能も取り揃えています。導入後は専任のサポート担当者が伴走し、現場帳票の電子化を通じた品質向上/生産性向上をご支援しています。
tebiki現場分析のより詳細な機能やプラン、改善事例を知りたい方は、以下の画像をクリックして概要資料をご覧ください。
>>かんたんデジタル現場帳票「tebiki現場分析」の詳細をPDF資料で見てみる
【補足】トヨタ流変化点管理のポイント
トヨタ流の変化点管理のポイントについて、本章では現場改善ラボで公開している、元デンソーの専門家による解説動画から抜粋して概要をご紹介します。
トヨタ生産方式(TPS)で知られるトヨタグループでは、変化点管理において特に「異常(意図しない変化、想定外のこと)」への対応が重視されます。
これは、設計段階で品質を作り込む源流管理に加え、製造現場で発生する予期せぬ変化を見逃さず、不良を作り続けない、流さないという思想に基づいています 。
その根幹には、TPSの柱の1つである「自働化」の考え方があります。
これは、機械や人が異常を検知したら、すぐにラインを止めて問題を顕在化させ、即座に対応するというものです 。これにより、異常が大きなトラブルに発展する前に対処します。
トヨタ流の実践では、異常を早期に発見するための「見える化」が徹底されます。5S活動や工具・部品の定位置管理(三定)に加え、「三現主義(現場・現物・現実)」に基づき、管理監督者が現場をよく観察すること(三三活動など)も重視されます 。
また、ヒューマンエラーが起こりやすい「3H(初めて・変更・久しぶり)」の状況や、作業者の僅かな様子の違い(顔色、姿勢など)にも注意を払い、人の変化に対する感度を高めることもポイントです。
過去のトラブル事例(過去トラ)を共有・活用し、再発防止に繋げることや、誰もが異常を指摘できる「何でも言える職場風土」づくりも欠かせません 。
ここでご紹介したのはトヨタ流変化点管理の要点です。デンソーで長年品質管理に携わった専門家による、より詳細な考え方や具体的な取り組みについては、以下の解説動画で深く学ぶことができます。
【補足】変化点管理でよくあるQ&A
変化点は主に何種類ある?
変化点には「計画的変化点」と「突発的変化点」の大きく2種類があります。それぞれの違いは以下の通りです。
- 計画的変化点:特定の目的や目標を達成するために、意図的に設定された変化
- 突発的変化点:予期せぬ状況や事故によって生じる、意図しない変化
両者ともに、製造ラインの変化が安全や品質、生産性などの重要指標にネガティブな影響をもたらす影響があるので、変化を可視化して管理する取り組みが大切です。
変化点管理と変更管理の違いは?
変化点管理と変更管理の違いとしては、変化点管理は予期せぬ変化による影響に対応する一方で、変更管理は意図的な変更を効果的に実施するという点が異なります。
変化点管理は、製造プロセス内で発生する予期せぬまたは計画的な変化を識別し、変化が製品品質に与える影響を管理・制御することに重点を置いています。製造業では、小さな変化が製品の品質に大きな影響を及ぼす可能性があるため、変化を迅速に識別し、適切に対応することが重要です。例えば、材料の微妙な変更や環境条件の変化などが変化点に該当します。
一方、変更管理は、製品やプロセスに対する計画的な変更を管理する工程です。新しい材料の導入、製造プロセスの改善、設備のアップグレードなどが含まれます。変更管理の目的は、変更が製品の品質や生産効率に与える影響を評価し、変更をスムーズに実施することにあります。
関連記事:4M変更とは?通知義務の有無や管理しやすくする方法も解説!
変化点と異常の違いは?
変化点と異常の違いは、変化点が製造工程における任意または不可避の変更を指すのに対し、異常は製造工程が正常な状態から逸脱した状態を指す点にあります。
変化点は製造工程の変更や調整の一環として発生するものであり、必ずしも品質問題を引き起こすわけではありません。一方で、異常は通常の製造プロセスからの逸脱を意味し、品質問題や生産遅延の原因となりえます。
例えば、計画的に行われる設備のアップグレードは変化点ですが、機械の突然の故障は異常と考えられます。変化点は管理の対象であり、異常は問題解決の対象となります。
【まとめ】変化点管理をかんたんに行うために
変化点管理は、製造工程における変化を正確に捉え、コントロールすることで品質不具合や異常の発生を未然に防ぐ手法です。変化点には計画的変化点と突発的変化点があり、それぞれ異なるアプローチが必要です。
製造現場の変化点として管理すべき要素として、4M(Man、Machine、Material、Method)や5M+1E(Measurement、Environmentを加えた6M)、そして3H(初めて、変更、久しぶり)といった内容を見える化する仕組みづくりが重要です。
変化を早期に捉え、問題の初期段階で対策を講じる手段として、製造日報や点検表などの現場帳票のデジタル化が挙げられます。tebiki現場分析のような、記録の自動計算・自動分析(グラフ化)機能を搭載するツールを活用することで、ダッシュボート上からリアルタイムで変化点を見極めることが可能です。
株式会社日本電気化学工業所のような、わずかな変化傾向を捉え、設備異常を早期に対策できるような変化点管理を行いたい方にはオススメの手段です。tebiki現場分析の詳しい機能やプラン、その他の改善事例を知りたい方は、以下の画像をクリックして、概要資料をご覧ください。