かんたん動画マニュアル作成ツール「tebiki現場教育」を展開する、現場改善ラボ編集部です。
現場の品質意識を高めるには、品質教育が欠かせません。しかし「何を教えるべきか分からない」「現場で活かされていない」と悩む企業も多くあります。
本記事では、品質教育のテーマや手法を12項目に整理し、実践事例やよくある課題、見直しのポイントを解説。動画を使った効果的な教育方法にも触れています。現場で「伝わる品質教育」を実現したい方は、是非ご参照ください。
目次
品質教育とは?目的や品質管理・品質保証との違い
品質トラブルを防ぎ安定したものづくりを実現するには、社員一人ひとりが「品質を守る」意識と行動を身につけることが欠かせません。そこで重要となるのが、現場作業者から管理職までを対象とした「品質教育」です。
ここでは、品質教育の目的と役割を明らかにするとともに、品質管理・品質保証との違いについても整理して解説します。
品質教育を実施する目的は?
品質教育とは、社員が「品質の大切さ」を理解し、品質を守るために必要な知識・技術・意識を身につけるための教育活動のことです。製品をつくる現場の作業者から、品質を管理・改善する管理職まで、すべての社員が対象になります。
品質教育を実施する目的は、社員一人ひとりが品質に対する意識を高め、日々の業務の中で「不良を出さない」「品質を守る」行動をとれるようになることです。現場任せの対応ではなく、全員が共通の基準や考え方を持つことで、品質トラブルの未然防止や継続的な改善が実現します。
製品や工程のルールだけでなく、「なぜそれを守るのか」という背景まで教育を通じて伝えることが、品質文化の定着につながります。
品質管理・品質保証との違い
品質教育とよく比較される取り組みが、品質管理・品質保証です。違いについて以下の表にまとめました。
品質教育 | 品質管理 | 品質保証 | |
---|---|---|---|
概要 | 品質を高める人材を育てる取り組み。全社員が対象で、意識やスキル向上を目的とする。 | 製品や工程の品質を保つための活動。主に現場での検査や管理が中心。 | 顧客に満足される品質を保証する活動。第三者視点で信頼性を確保する。 |
視点や 対象 | 人 (意識・行動) | モノ・工程 (仕様・数値) | 顧客 (満足・信頼) |
例 | ・不良の原因を考える研修 ・品質意識向上の動画教育 | ・寸法検査や不良率の管理 ・工程内のチェックリスト運用 | ・出荷前に保証書を添付 ・クレームへの是正対応 |
品質管理と品質保証の違いを正しく理解することで、現場での不良防止と顧客への品質保証という役割分担が明確になり、的確な品質活動とトラブル対応が可能になります。より詳しく知りたい方は、以下の関連記事をご覧ください。
関連記事:品質管理とは?品質保証との違いは?管理手法や品質改善のポイントを解説
【12選】品質教育では何を教える?テーマや具体的な手法
品質教育では、単にルールや手順を伝えるだけでは不十分です。現場で品質を守り改善を継続するためには、考え方や分析手法を理解し、実践できる力が求められます。
この章では、5Sや4M分析、QC手法など、品質教育で取り入れたい代表的な12のテーマや手法を紹介します。それぞれの特徴や活用シーンを知ることで、自社の教育に役立てるヒントが見つかるはずです。
品質教育は、若手社員からベテラン層、さらにはマネジメント層まで幅広く対象に行うべき教育です。対象者別に何を教えるべきか知りたい方は、以下のリンクをクリックしカリキュラム資料集をご覧ください。
>>品質教育で教えるべき内容を対象者別に解説!品質意識を高める実践的な教育手法のヒントをみる(無料配布中)
- 5S活動
- 4M
- 3H(初めて・変更・久しぶり)
- 5ゲン主義
- 5つの「化」
- PDCAサイクル
- シックスシグマ
- QCストーリー
- 3Mの削減
- インダストリアルエンジニアリング
- QC7つ道具 / 新QC7つ道具
- なぜなぜ分析
5S活動の徹底
5S活動とは、環境改善を行う取り組みのことです。以下の言葉の頭文字をとって、5Sと呼ばれています。
- 整理
- 整頓
- 清潔
- 清掃
- 躾(しつけ)
現場のムダを発見・改善することで、品質の向上だけでなく職場の環境改善や、怪我・事故の防止につながります。これらを現場で習慣化することで、作業ミスやムダを減らし、品質トラブルの防止につながります。
例として、工具が決まった場所に整頓されていれば探す時間が減り、異常にもすぐ気づけます。5S活動は品質の土台ともいえる基本であり、全員で継続して取り組むことが重要です。
一方で、5S活動に取り組んでいるのにも関わらず、失敗に終わってしまう企業も多いです。5S活動で生産性を向上させるには、正しい手順で取り組む必要があります。
現場改善ラボでは数々の企業で5S改革を行ってきたコンサルタントによる、現場で実践できる「正しい5S活動」の実践方法の動画を無料で公開しています。具体的にとるべきアクションを知りたい方は、是非本記事と併せてご覧ください(下のリンクをクリック)。
>>5S活動の基本から「定着」までを徹底解説!現場でマネできる5S事例をみてみる(無料公開中)
4Mの変化点や変更点の共有
4Mとは、製造現場の品質に大きく影響する4要素の頭文字を取った言葉です。以下の言葉の頭文字をとって、4Mと呼ばれています。
- Man(人)
- Machine(機械)
- Material(材料)
- Method(方法)
製造現場では、この4Mのいずれかに変更や変化が起こると品質不良が発生するリスクが高まります。たとえば、作業手順の変更や設備・材料の切り替えといった「意図的な変更」は、しっかりと関係者に情報を共有しなければ、ミスの温床になりかねません。
一方で明確な変更がない場合でも、「何か様子が違う」と感じるような変化点を、現場の経験や勘どころから察知することがあります。こうした気づきは言語化が難しく属人化しやすいため、教育によって共有・伝承していくことが重要です。
4Mの変化点・変更点を整理し、現場全体で共有する仕組みを持つことは、不良の未然防止に直結します。品質教育では、「何を」「どのように」共有するのかまで教えることが、不良ゼロに向けた土台づくりとなります。
4M変化点を管理し教育する方法については、デンソーの製造現場で品質管理を担っていた専門家による以下の解説動画でご覧ください。
>>元デンソーの専門家による「トヨタ式4M変化点管理の方法」を見てみる(視聴無料)
3H(初めて / 変更 / 久しぶり)に該当する作業の教育
3Hとは、ミスや不良が発生しやすい3つの要因のことです。以下の言葉の頭文字をとって、3Hと呼ばれています。
- 初めて
- 変更
- 久しぶり
「初めてやる作業」「手順が変更された作業」「久しぶりに行う作業」は、いずれも慣れや経験の不足、注意力の低下によってミスや不具合=ヒューマンエラーが発生しやすくなります。
品質教育ではこの3Hの考え方を理解させたうえで、対象となる作業に対して事前の教育や再確認を徹底することが重要です。また、現場で3Hに該当する場面を見逃さず、声かけやチェックを行う習慣も併せて教えることで、不良を未然に防ぐ力が育ちます。
品質不良につながるヒューマンエラーの対策方法については、別記事か、「エラーの検知と抑制」に着目した以下のハンドブックをご参照ください。
>>再発するヒューマンエラーを防ぐには?適切なヒューマンエラー対策に必要な視点を学ぶ(無料配布中)
5ゲン主義に沿った不良原因の追求と対策
5ゲン主義は、現場/現物/現実にあたる「三現主義」の視点で現状を捉え、原理や原則といった本来目指すべき状態に向けて改善を行っていくことを指します。現場/現物/現実/原理/原則の頭文字をとって、5ゲン主義と呼ばれています。
下記のような視点で品質問題を捉える考え方を品質教育で教えることで、現場主体による品質改善活動の推進や徹底といった効果が期待できるでしょう。
5ゲンの要素 | 見るべき点 |
---|---|
「現場」に足を運ぶ | ・作業環境 ・作業の流れ ・従業員の動き ・設備や機械の状態 |
「現物」を手に取る | ・製品や部品の品質 ・原材料の状態 ・不良品や問題の発生物 |
「現実」を自分の目で見る | ・問題や課題の具体的事例 ・現場での実際の状況 |
「原理」から外れていないかを確認する | ・品質管理の基本原則 ・標準作業手順 |
「原則」と異なることが 行われていないかを確認する | ・品質管理の基本原則 ・遵守すべきルールや規範 |
しかし、品質の考え方や重要性だけでなく、改善のための考え方やプロセスを伝えることが品質教育には必要です。品質の改善ステップやプロセスを伝えることで、具体的な行動ベースの改善提案が現場主体で挙げられることが期待されます。
品質改善に求められる5つの「化」
品質改善を効果的に行うには、以下のような品質改善のステップやプロセスを教えることも重要です。「品質向上のためにどのような施策を行うべきか、洗い出すための視点」として教えるとよいでしょう。
可視化 | 製造に関わる情報を可視化(目に見えない情報をデータ化)すると、改善策が実際に効果をもたらしているかを明確に確認できるようになります。 製造に関する情報を数値化してデータ管理ツールで整理すると、効率的に品質改善を行えるようになるでしょう。 |
定量化 | 製造に関わる可視化した情報をより細かく数値化することで、効率よく製造工程を改善できます。 統計ソフトを使って製造データの傾向を分析することで、数字に基づいた具体的な改善案を提案できるようになります。 |
課題化 | 目標と現状の数値を比較して問題点を明確にすることで、効率的に業務改善できるようになります。業務管理と製造を行っているメンバーが一緒に行うことで、効率的に問題点を発見できるでしょう。 |
実践化 | 実践化とは、設定した目標に沿って品質改善を行うことです。課題化を行って目標を明確にした後、実践を繰り返していくことで短時間で品質を向上させられます。 ただ、計画通りに進むことは少ないため、定期的に目標と現状の差分を計測して、計画を修正していく必要があります。 |
定着化 | 人事異動や原材料の質によって品質が変わってしまうため、実践化で目標の品質に達した後に品質が悪くなることがあります。 そのため、定期的に業務マニュアルの更新や再教育を行い、品質を安定させるための施策を行いましょう。 |
「可視化」は品質改善に特に重要であり、有効手段として例えば製造日報や不具合報告書などの「現場帳票」を活用するケースが多いでしょう。しかし、紙やExcelベースで運用される場合が多い現場帳票は、記録や集計に膨大な工数が発生して改善に向けた分析が着手できないというケースも少なくありません。
そこで、「現場帳票のデジタル化」も行うことで、記録や承認工数の削減/記録データの自動グラフ化ができるため、品質教育で改善意識を標準化させた現場主体で、不良の分析から改善活動まで取り組めます。
▼デジタル帳票上で作成した記録のグラフ▼
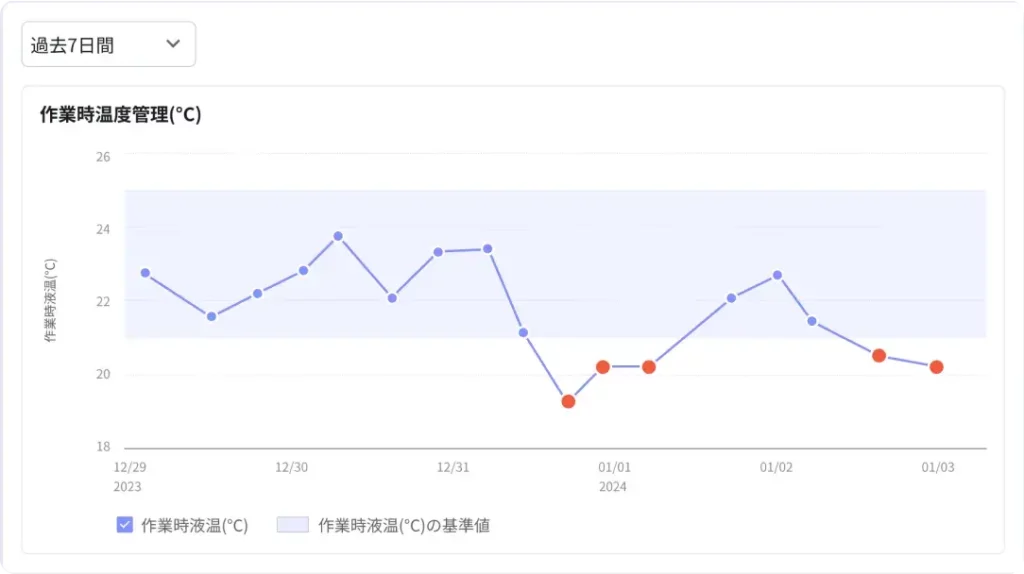
デジタル帳票の活用による品質向上の効果や導入方法、デジタル化ツールの選び方については以下のガイドブックもご覧ください。
>>記録のデジタル化で品質問題をカイゼン!デジタル帳票導入による品質向上のアプローチをみる(無料公開中)
改善につながるPDCAサイクル
PDCAサイクルとは、仮説・検証を繰り返して品質を高める手法のことです。Plan(計画)、Do(実行)、Check(評価)、Action(改善)の頭文字をとってPDCAサイクルと呼ばれています。
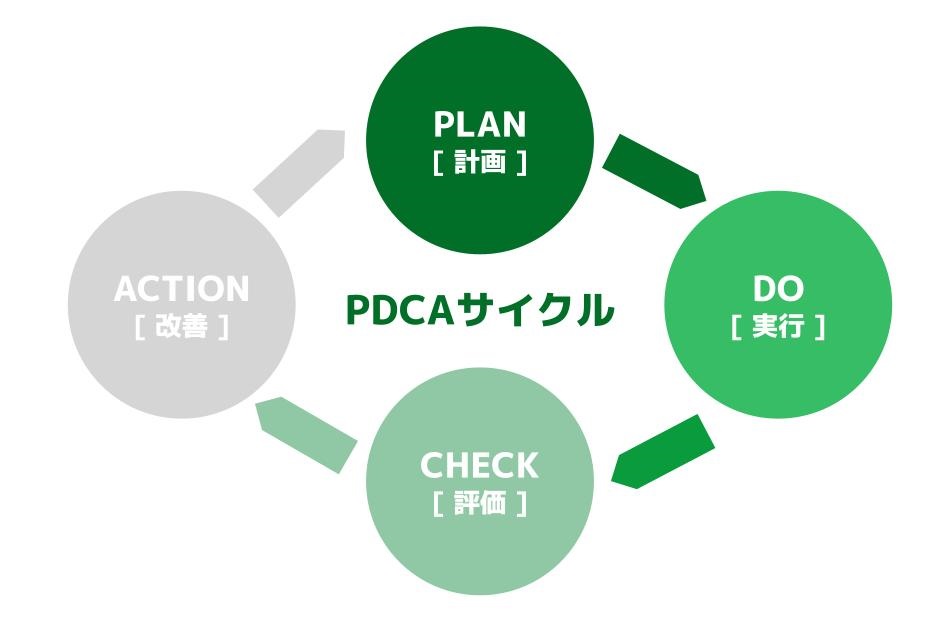
製造現場で発生している品質問題の対策を計画し、実際に検証と効果を計測したうえで、効果が見込める改善サイクルを繰り返すことで、品質改善の効果が期待できます。
製造業の場合、Plan(計画)ではなくStandardize(標準化)を指す「SDCAサイクル」の手法でも良いでしょう。
改善が見込める手法や施策を現場の標準として落とし込むことで、品質改善を期待することができます。一方で実際に標準化を進めようとする場合、暗黙知化している「カンコツ」の技術継承が大きな壁となり、難易度が高いことも事実です。
“伝わらない”“属人化している”カンコツ作業を標準化するコツについてまとめた以下の資料がヒントとなっておりますので、本記事と併せ是非ご覧ください。
>>作業品質のばらつきを改善!属人化の大敵「カンコツ」を標準化するポイントをみる(無料配布中)
品質のばらつきを解消させるシックスシグマ
シックスシグマ(6σ)とは、品質のばらつきを小さくするための改善手法のことです。
データのばらつきを表す「標準偏差」の単位であるシグマが名前の由来で、6σ(不具合が100万回あたり3.4回以内)が最も厳しい基準です。プロセス改善手法「DMAIC(ディーマイク)」やプロセス開発手法「DMADV(ドマドブ)」を使うことで、個人のスキルや発想力に左右されずに改善を行えます。
シックスシグマの具体的な手法である「DMAIC(ディーマイク)」や「DMADV(ドマドブ)」の詳細や、シックスシグマを行うメリットについて知りたい方は、是非以下の記事も併せてご覧ください。
関連記事:シックスシグマ(6σ)とは?経営/品質管理で必要な概念をわかりやすく解説!
品質問題を解決するQCストーリー
QCストーリーとは、品質改善(Quality Control)を行うための考え方や手順のことです。QCストーリーを実践することで、問題解決までのステップが明確になり、順序に沿って効率よく改善を行えるようになります。
「問題解決型」「施策実行型」「課題達成型」という3つの型があり、業務や問題によってアプローチを変えて改善を行えるという特徴があります。
QCストーリーの正しい進め方を知りたい方は、以下から元トヨタ自動車九州の主幹が解説する「トヨタ式QCストーリーの進め方」の解説動画をご覧ください。NG事例もわかりやすく解説します。
>>品質問題の正しい問題解決プロセスはこう進める!QCストーリーの模範例を学ぶ(無料公開中)
3Mの削減
3Mとは「ムリ・ムダ・ムラ」の3つの頭文字を取った言葉で、現場のムダや不安定さをなくすための基本的な考え方です。品質教育では、これら3つを見つけて改善する視点を持つことが重要です。
特に、ムリ(無理な作業)はヒューマンエラーや故障の原因となり、ムダ(不要な動き)は生産性を下げ、ムラ(ばらつき)は品質の不安定さにつながります。3Mを正しく理解し、日常の業務の中で意識的に見つけ、改善につなげる姿勢を教育で定着させることが大切です。
製造現場の3Mに気づくための視点や改善方法を知りたい方は、以下の専門家の解説動画も併せてご覧ください。3Mの削減活動の実施後の標準化のポイントまでしっかり解説しています。
>>現場に潜む3Mはどう見つけるべき?3M発見~実施後の標準化のポイントまでをみてみる(無料公開中)
インダストリアルエンジニアリングによる3M改善
IE(インダストリアルエンジニアリング)とは、現場に潜む「ムリ・ムダ・ムラ(3M)」を見つけ出し、作業や工程を効率化・標準化するための体系的な手法です。
品質教育においては、単に作業をこなすだけでなく、「なぜそのやり方なのか」「もっと良くする方法はないか」といった改善の視点を育てることが求められます。IEの基本を理解することで作業者自身が問題に気づき、改善提案につなげられるようになります。
IEには大きく分けて以下の2つの分析手法があり、改善の目的に応じて使い分けます。
分類 | 内容・目的 | 主な対象 | 教育のポイント |
---|---|---|---|
方法研究 | 作業方法や手順、動作を見直し ムダを省いて効率化する | 人の動作 作業手順 運搬・配置 | 「なぜその作業が必要か」「もっと良いやり方はないか」を考える視点を持たせる |
作業測定 | 作業時間や機械の稼働率などを 数値化し、基準や標準を作る | 作業時間 稼働率 作業ばらつき | 作業にかかる時間を測って “基準”をつくる大切さを理解させる |
関連記事:【生産管理】IE(インダストリアルエンジニアリング)とは?分析手法や改善のコツを紹介
QC7つ道具 / 新QC7つ道具を使った分析手法
QC7つ道具と新QC7つ道具はいずれも、製造現場の品質問題を改善するために使う分析ツールです。
▼QC7つ道具と新QC7つ道具の比較表▼
含まれる分析手法 | 特徴やメリット | |
---|---|---|
QC7つ道具 | ・パレート図 ・特性要因図 ・グラフ ・ヒストグラム ・散布図 ・管理図 ・チェックシート | 数値データ(定量データ)を扱う。現場データを視覚化して現象の傾向を把握しやすい |
新QC7つ道具 | ・系統図法 ・連関図図法 ・親和図法 ・マトリックスデータ解析法 ・アローダイアグラム ・PDPC法 ・マトリックス図法 | 言語データ(定性データ)を扱う。抽象的・複雑な課題でも因果関係を整理しやすい |
品質教育では、QC7つ道具で現象を把握し、新QC7つ道具で対策を立てるといったように、目的に応じた使い分けを教えることが重要です。現場改善ラボでは、実務で使える「QC7つ道具/新QC7つ道具の使い方」を専門家が解説している動画を無料公開しています。基本的なことから応用的・実践的なことまで解説していますので、併せてご覧ください。
>>QC7つ道具と新QC7つ道具を組み合わせた問題分析の方法は?わかりやすい使用例で実践してみる(無料公開中)
なぜなぜ分析による真因の特定
なぜなぜ分析とは、問題が発生した原因を「なぜ?」と何度も質問をしながら深掘りすることで、根本的な問題を明確にする手法です。品質教育では、単に5回繰り返すだけで終わらせず、因果関係を論理的にたどる力を身につけることが重要です。現象に対して安易に結論を出さず、「本当の原因か」「なぜそうなったのか」を事実に基づいて考える姿勢が求められます。
また、なぜなぜ分析はチームで検証し、再発防止策に結びつけることが大切です。結果を記録し、他部署へ水平展開する視点も教育の中で伝えるべき要素です。
なぜなぜ分析の教材として、すぐに使えるテンプレートや分析の手法を示したわかりやすいハンドブックも以下にご用意しておりますので、是非お役立て下さい。
>>トヨタで実践されているなぜなぜ分析の進め方!便利なテンプレートですぐに実践してみる(無料配布
ここまで、品質教育で教えるコンテンツ例について詳しく解説しました。次章からは、実際に品質教育を通じて品質向上や品質改善を推進している企業事例をご紹介します。
品質教育で品質向上を推進している事例
実際に品質教育を行っている企業事例を4社分ご紹介します。具体的な事例を通じて、各社がどのように品質教育を行っているかを学ぶことで、自社の取り組みに役立ててください。
さらに多くの教育事例を知りたい方は、以下のハンドブックもご覧ください。
>>品質意識を向上させる教育事例!教えるべきカリキュラム資料もこれ1つで確認できます(無料配布中)
児玉化学工業株式会社
児玉化学工業株式会社は、住宅設備や自動車向けの合成樹脂加工を行っている化学メーカーです。
同社は、新人に加えて社内異動など職種が変わる人に向けて、品質と現場の基礎を勉強し直す「品質道場」という独自の取り組みを行っています。品質管理の基礎知識を学んでから現場に配属することで、品質道場の取り組み開始から8年で60〜65%の品質向上に成功しました。
品質不良を削減する取り組みの一環として、動画マニュアルの活用も行っています。簡単に動画マニュアルが作成でき、自動翻訳機能などを有している「動画教育システムtebiki」を導入したことで、手順書作成の工数は紙の1/3にまで削減。動画だからこそ、学ぶ側もわかりやすくなり、社内の作業も標準化されているとのことです。
▼インタビュー動画:児玉化学工業株式会社▼
児玉化学工業株式会社における品質改善に向けた取り組みの詳細は、以下のインタビュー記事もぜひご覧ください。
▼インタビュー記事▼
・品質とは”人の質”『不良ゼロ』を目指す児玉化学工業の現場改善
・工場の作業手順や異常処置、安全指導を動画で作成。手順書作成の工数は紙の1/3に。自動翻訳で外国人教育にも活用。
トヨタ自動車株式会社
トヨタ自動車は、従業員数7万人以上(連結37万人以上)の国内最大手の自動車メーカーです。「お客様第一」「品質第一」のクルマづくりを行っていて、毎月11日を「品質教育の日」と定め、全工程の作業者が品質知識を学んでいます。
顧客の生の声を聞いて品質意識の向上を図る「品質講話会」や、品質向上活動事例を社内で共有するための「品質事例展示会」も実施。品質管理の意識を高めています。
現場改善ラボにて、トヨタ自動車株式会社元副社長が講演した「品質経営の歴史と課題」の内容を知りたい方は、以下のレポート記事も併せてご覧ください。トヨタにおける品質経営の歴史をお届けしています。
関連記事:自工程完結を発案したトヨタ元副社長が語る『品質経営の歴史と課題』【IMPROVE開催レポート】
沖電気工業株式会社
沖電気工業株式会社は、通信機器を製造する電機メーカーです。同社は、社員全員がQC(Quality Control)を実務に活用することが大切だと考え、入社後の早いタイミングで品質教育を実施しています。
具体的には、以下のような技能教育を行い、品質への意識を高めているそうです。
- QC7つ道具・統計的品質管理などを学ぶ新入社員教育
- 製造物責任(PL)法および消費生活用製品安全法・製品安全規格などの教育
- はんだ付け技能・ソフトウェアテスト技法などの教育
(参照元:沖電気工業株式会社「品質への取り組み」)
沖電気工業株式会社にて品質管理課長を務めた濱田氏による「品質改善活動・QCサークルのポイント」を聞きたい方は、以下から講演動画をご覧ください。QCサークル活動の現状と問題点なども解説していますので、品質教育のネタとしてもご活用いただけるでしょう。
>>>【無料】成功に導くQCサークル活動のポイントを動画で見る
新日本工機株式会社
工作機械などの製造販売を行う新日本工機株式会社では、「人が育つ環境づくり」が最も大切であると考えて、現場作業のプロフェッショナルな作業はもちろんのこと、仕事に対する向き合う姿勢など作業以外のことも直接伝える教育を行っています。
具体的には、「教育道場」と銘打って、社内で認定されたマイスターがものづくりに必要な基本作業を何度も繰り返して教育しているとのこと。教育道場の対象は、主に現場で作業をする若年者や新入社員向けですが、設計技術者にも現場作業を体験してもらうことも行っているそうです。
教育道場では、一気に全ての基本作業をマイスターが全て教えています。そのため、教え漏れがなく、教育内容を標準化できているという効果を得られているそう。その結果、新人の即戦力化を実現しています。
同社では、作業を標準化させるための手段として他にも「動画教育システムtebiki」を活用しています。文字ベースのマニュアルから動画に置き換えて、作業品質が安定するようになりました。品質の面だけではなく、ベテラン従業員に依存していた作業の技術伝承も推進できているとのことです。
▼インタビュー動画:新日本工機株式会社▼
「人材育成の領域が形になってきた」と語る新日本工機株式会社の詳しい取り組み内容については、以下のインタビュー記事でぜひご覧ください。
インタビュー記事:人が育つ環境づくりとして動画マニュアルtebikiを活用。技術の蓄積と作業品質の安定を実現。
品質教育がうまくいっていない現場が抱えがちな課題
「教育しているのに不良が減らない」「教えても現場で活かされていない気がする」。そんな悩みを感じたことはありませんか?
多くの現場で品質教育は行われていますが、その効果が現場の成果につながっていないケースも少なくありません。ここでは、品質教育がうまくいかない現場でよく見られる課題を整理し、次の改善につなげるヒントを探ります。
現場教育が上手く機能していない原因についてさらに詳しく知りたい方は、以下のハンドブックもご覧ください。根本に潜む原因や、抜本的に改善する教育方法のヒントがまとまっています。
>>教育が失敗してしまう原因は?3つの根本的要因、教育の改善事例3選をみてみる(無料配布中)
教育の目的が現場に伝わらず形骸化している
品質教育を実施していても、「何のためにやっているのか分からない」「この作業は本当に意味があるのか?」といった声が現場から聞こえてくることはありませんか?これは、教育の目的が現場まで浸透していないことが原因です。
たとえば「不良を減らすため」とは伝えていても、具体的にどんな品質リスクを避けるのか、どのように仕事の質が変わるのかが曖昧なままでは、受け手にとっては“意味のない作業”に映ってしまいます。
その結果、朝礼での読み合わせや形式的なOJTだけが繰り返され、教育の本質が見失われてしまう事態に。現場としても「どうせいつも通りやればいい」と受け流すようになり、教育が“儀式化”してしまうのです。目的が腹落ちしていない教育は「やらされ感」だけが残り、かえって現場のモチベーションを下げてしまう要因にもなります。
内容が実務と結びつかず現場で活かされていない
教育資料やスライド、マニュアルが整っていても、それが現場作業と噛み合っていなければ意味がありません。実際には、「あの講義で言ってたこと、現場では使えない」「ウチのラインでは通用しない」といったギャップがよく発生します。これは、教育内容が現場の実務を踏まえて設計されていないことが原因です。
たとえば、ラインごとの作業条件や検査基準に触れていなかったり、製品や工程の実情を反映していないと、現場は「机上の空論」と受け止めてしまいます。現場にとってリアリティのない教育は、せっかくの時間を浪費するだけになり、結果的に現物を前に直接教える“属人的なOJT”に頼らざるを得ない状況に戻ってしまうのです。
「製造Aラインのこの製品は、なぜ不良が出るのか?」「そのとき作業者はどんな判断に迷っていたか?」といった、実務に根ざした内容がなければ、現場は「現物見て教わった方が早い」と属人的な教育に戻ってしまいます。
教える内容や基準にムラがあり現場で混乱が生じている
同一の作業であっても、教育を担当する人によって伝え方や基準が微妙に異なるケースは現場でよく見られます。しかし、「〇〇さんからはこう教わったけど、△△さんは違うやり方を言っていた」という声が現場で頻発すると、現場の不安や混乱が生じ、品質のばらつきにつながります。
これは、教える内容が統一されておらず、教育の基準が個人任せになっていることが原因です。教育担当者の経験や感覚によって伝える内容が変わってしまうため、組織としての“標準”が守られず、作業者の判断に委ねられてしまう場面が増えます。属人化した教育は現場のスピードや柔軟性を損なうだけでなく、品質リスクそのものになりかねません。
同様に、標準作業書があっても現場で共有されておらず、現場教育がベテランの勘や経験に依存している状態も現場の混乱を招きます。現場では、「昔からこうやってるから」「こっちのほうが早い」と独自の教え方が広まりやすく、それが結果として品質のばらつきやクレームの温床になります。教える人によって指導内容が変わる環境は、現場の安定にとって大きなリスクです。
教育の効果測定がされず改善につながらない
品質教育を実施しても、その後の定着状況や効果を確認していない現場は意外と多いものです。「とりあえず教えたからOK」となり、理解度の確認やフォローアップが行われないまま時間だけが過ぎていく。この状態では、教育が現場の成果につながっているのか分からず、当然改善にも結びつきません。
この背景には、教育後の評価方法や仕組みが用意されていない、あるいは現場の忙しさから検証の時間が確保できないといった実情があります。しかし、教育と実務が分断されたままでは「やったつもり」「分かったつもり」が残り続け、現場も管理者も「本当に伝わったのか分からない」という不安を抱えたままとなってしまいます。
このような状態では、「同じミスの繰り返し」や「何度教えても変わらない」といった悪循環が引き起こされやすく、加えて教育に対する現場の信頼が低下し、「どうせまた形だけで終わる」といった諦めにもつながります。
製造現場で「教育があっても現場の品質は変わらない」と感じる背景には、このような具体的な課題があります。これらを放置してしまえば、いくら教育の時間を確保しても成果にはつながりません。まずは現場の実態に即した課題を見つめ直すことが、改善の第一歩です。
次章では、品質教育の効果を引き出す「教育手法の改善」の実践方法について解説します。
品質教育を改善するには、教育手法の見直しがカギ
前章で述べたような課題を解決し、品質教育を適切に現場で実施するには、教育の「中身」だけでなく「手法」そのものを見直す必要があります。
ここでは、従来の紙マニュアルや形式的なOJTの課題を踏まえ、より効果的に現場に浸透しやすい教育手法のポイントについて解説します。
紙マニュアルやOJTだけでは限界がある
多くの製造現場では、これまで通りのOJTや紙ベースのマニュアルに教育の大部分を依存しています。しかし、現場で発生している問題の多くは、これらの手法では十分に対応しきれていないのが実情です。
たとえば、紙の手順書を配布しても「文字ばかりで分かりづらい」「現場で見る余裕がない」といった声が上がりやすく、実際の作業中に参照されることは少なくなっています。
また、OJTもベテラン作業者の経験や感覚に頼った指導が中心となりやすく、教える内容に一貫性がないまま属人化が進行する傾向があります。例として、担当者が変わるたびに教え方や基準が微妙に異なると現場では混乱が生じ、品質のばらつきを招くリスクが高まります。さらに教育内容の可視化も難しいため、「何をどこまで教えたか」「誰が何を理解しているか」が把握しづらく、教育の振り返りや改善も困難になります。
こうした状況を踏まえると、従来の教育手法を踏襲するだけでは限界があり、より再現性・共有性の高い方法へと転換していく必要があります。
現場に伝わる教育には「伝え方」の工夫も必要
品質教育を現場に定着させるには、伝える内容だけでなく「どう伝えるか」も重要です。多くの教育資料があっても、現場の環境や理解レベルに合わなければ「使えない」と感じられます。
例えば、文字中心のマニュアルや座学だけでは複雑な手順や品質リスクの細かなニュアンスを伝えにくいため、動画や実践的なデモを取り入れることが効果的です。これにより作業者は具体的な動きを理解しやすくなり、教育のムラや伝達ミスを減らせます。
また、受け手が「自分ごと」として理解できるよう、実際の不良事例やトラブルを盛り込む工夫も効果的です。具体的な失敗や判断ミスを示すことで学びが実務に直結しやすくなり、記憶にも残りやすくなります。
さらに、現場でコミュニケーションを積極的に行うことも重要です。実際に、自動車部品を製造している「上松電子株式会社」では、品質不良の約4割がコミュニケーションミス、特に教育不足に起因していることが、過去半年間の調査で判明しています。コミュニケーション不足は作業手順の誤解や情報伝達漏れを招き、不良の見逃しやミスの繰り返しにつながります。言語や文化の違いによる指示の理解不足も品質トラブルを増やし、現場の混乱や生産性低下の原因となるでしょう。
同社が取り組んだ教育改善について詳しく知りたい方は、後述するインタビュー事例をご覧ください。次章では、これらのポイントを踏まえた「おすすめの教育手法」についてご紹介します。
効果のある品質教育には「動画」の活用がおすすめ
先述したような教育のポイントを満たした教育手法として、「動画」が注目されています。言葉では伝えにくい動作や作業のコツも、動画なら視覚的に共有でき、理解が深まります。
ここでは、動画による教育効果や、複雑そうに見える動画マニュアルがかんたんに作成できるツールをご紹介します。実際の動画マニュアルもお見せしますので、「動画マニュアルってどんなもの?」と気になっている方にもイメージしやすくなっています。教育の効率化や品質の安定化に役立つ動画活用の具体的なイメージを、是非ご覧ください。
【サンプルあり】動画で教育が改善される理由
動画で教育が改善される理由は、視覚と聴覚を同時に使って情報を伝えられる点にあります。文章や口頭説明では伝わりにくい細かな動作や作業のコツも、動画なら一目で理解できます。
例として、油圧ジャッキの操作方法を動画化したマニュアルをご紹介します。
※tebiki現場教育で撮影・編集しています
文章では表しにくい複雑な内容も、動画であれば見たままに伝わります。さらに、「ゆっくり回す」という感覚的な操作についても、動画であれば「どの程度の速度で回すべきか」という模範例を示すことができ、教育のばらつきを抑えることができます。
また、視線の動かし方や手の位置、タイミングなど、紙の手順書では伝えきれなかった微妙な動作も再現でき、何度も繰り返し視聴できるため現場での理解度が飛躍的に向上します。これにより教育にかかる時間を短縮しつつ、ミスの発生も抑えることが可能になります。
動画マニュアルが教育のばらつきや教育負担を削減できる理由や実際の活用事例についてより詳しく知りたい方は、以下のハンドブックもご覧ください。「OJT」と「動画マニュアル」を組みあわせ、さらに質の高い教育を実施している事例もございますので、自社の教育に取り入れる際の参考としてお役立てください。
>>現場教育の課題を解決する手段がわからない方は必見!動画を活用した教育改善事例をみてみる(無料配布中)
動画マニュアルを簡単に作れる「tebiki現場教育」で教育の質を向上
動画マニュアルのメリットはわかっても、「編集スキルがないから、動画マニュアルの導入に踏み切れない」とお思いの方もいらっしゃるでしょう。しかし、「tebiki」という動画マニュアル作成ツールを使用すれば、誰もが簡単に動画マニュアルの作成から教育管理が可能になります。
▼動画マニュアル作成ツール「tebiki」紹介動画▼
tebikiには、主に「動画を簡単に作成できる機能」と「教育管理ができる機能」があります。
- 音声認識による自動字幕生成
- 100カ国語以上への自動翻訳
- 字幕の読み上げ(多言語にも対応)
- アクセス履歴等がわかるレポート機能
- オリジナルのテストを作成できるテスト機能
- 従業員のスキルを評価・可視化できる機能 など
実際に導入いただいている企業からは、「tebikiは単なる動画作成ソフトではなく“社員教育ツール”」という声もいただくほど現場教育に特化したツールです。そのため、品質意識を定着させる教育体制の整備が可能になるでしょう。
tebikiには、まだまだ現場教育に便利な機能が搭載されています。より詳細な情報や無料サポート体制については、以下のサービス紹介資料からぜひご確認ください。
tebiki現場教育を品質教育の場で活用している事例
動画マニュアル「tebiki」を活用し、品質教育を効果的に進めている事例についても解説します。
その他の事例についても知りたいという方は、以下のリンクをクリックし詳細な資料をご覧ください。
>>かんたん動画マニュアル「tebiki」活用の実例をもっとみる
理研ビタミン株式会社
理研ビタミン株式会社は、調味料や加工食品の製造を行う食品・化学メーカーです。同社では、紙マニュアルでは業務手順が伝えきれず、業務にばらつきが生じ品質に問題が発生するという課題を抱えていました。
そこで、課題解決のために動画マニュアル「tebiki」を導入。一部の部門で従来の紙マニュアルの40%を動画マニュアルに変更した結果、紙マニュアルではわかりにくい部分の理解が進んだだけでなく、OJT教育にかかる時間を20%削減できました。現在は、品質管理・生産技術・安全教育・研修・点検業務・メンテナンス業務など、幅広い業務の人材教育で活用しています。
tebiki導入前の課題 | tebiki導入の効果 |
---|---|
・業務手順が文字や静止画だけでは伝わりにくく、品質にばらつきがあった ・特定社員に依存した作業が多く、属人化が進んでいた ・多様な勤務体系のため教育機会やタイミングにムラがあった | ・動画で動作を視覚的に示せるため業務品質のばらつきが減少 ・動画化で作業の標準化を進め、属人化の解消に向けた取り組みを推進 ・多様な勤務体系に対応し、いつでも視聴可能な動画研修で教育機会を拡大 |
理研ビタミン株式会社のより詳しい導入経緯や効果は、以下のインタビュー記事よりご覧ください。
インタビュー記事:品質保証部門と製造部門がONEチームで取り組んだ業務標準化と技術伝承
上松電子株式会社
上松電子株式会社は、電子部品や金属部品を含む様々な自動車部品を製造している企業です。同社では、高い品質基準が求められる中、コミュニケーションミスや教育不足に起因した品質不良を課題視していました。具体的には、現場には多くの外国人派遣社員がおり言語の壁があることや、紙のマニュアルでは検査作業の細かな動きやニュアンスが伝わらず、標準作業が浸透しないことが課題でした。
これらの課題を解決するため、同社は動画マニュアル「tebiki」を導入。動画によって視覚的に動作や手順を示すことで、言葉の壁を越えた教育が可能になり、特に外国人派遣社員への指導がスムーズになりました。実際に、塗装工程と組立工程の班長が連携して動画マニュアルを活用した教育を繰り返し実施した結果、塗装工程での不良見逃し率は5週間で撲滅されました。
また、tebiki導入により現場のコミュニケーションが活発になり、職場の雰囲気も明るく改善。班長は「教えたつもり」にならず、内容が正しく理解され実践されているかを確認する重要性を実感しています。
tebiki導入前の課題 | tebiki導入の効果 |
---|---|
・外国人派遣社員への指導が言葉の壁により困難で、現場のコミュニケーション不足があった ・作業者の「見落とし」問題が作業者個人の責任とされがちで、管理者側の教育体制の改善が必要だった | ・動画マニュアルにより視覚的に動作を伝え、自動翻訳機能も活用したことで言葉の壁を超えた効果的な教育が可能に ・動画マニュアルと「教えた内容の確認」を徹底し、手順通りの作業が行われているか管理者も確認する文化づくりを推進 |
上松電子株式会社のより詳しい導入経緯や効果は、以下のインタビュー記事よりご覧ください。
インタビュー記事:「教えたつもり」をなくし、塗装工程の不良見逃し率を大幅に削減
まとめ
品質教育は、製造業において品質を確保し、顧客満足を向上させるための重要な取り組みです。本記事でご紹介した、品質教育のテーマ例から具体的な手法などを参考にお取組みいただけますと幸いです。
「教育を行う時間やコストがない」「教育を行える人が少ない」といった各企業が直面する課題に対しては、動画マニュアルの活用が有効です。正しい手順だけではなくNG例もわかりやすく動画化すれば、より効果的に知識をインプットでき、品質への意識醸成につながるでしょう。
動画マニュアルの作成には、「tebiki現場教育」がおすすめです。tebikiならば誰でもかんたんに動画マニュアルを作成できるだけではなく、自動翻訳による外国人教育のサポート・テスト機能などによる教育管理も行えます。tebikiの詳細な情報やプランについては、以下の資料から是非ご覧ください。