「動画教育システムtebiki」と「帳票ペーパーレス化システムtebiki」が運営しているメディア、現場改善ラボです。
7つのムダは、製造業における現場作業を行う方にとってはもちろん、事務系の業務を行う方にとっても、生産性を向上させるために有効な概念です。
本記事では、「7つのムダとは何か」「7つのムダを改善するにはどうしたらいいか」を主なテーマとし、7つのムダを詳しく解説していきます。
目次
7つのムダとは?提唱者はトヨタ?
7つのムダを具体的に解説する前に、まずは「7つのムダ」という概念がそもそも何なのか?また、なぜこの考え方が誕生したのかについて確認していきましょう。
7つのムダとはそもそも
「7つのムダ」とは、仕事や作業の中で発生する非効率な要素=無駄(ムダ)を整理した考え方・フレームワークです。
これらのムダは、無駄な時間や労力、資源を生む原因となるものであり、削減することで効率的に目標を達成できるようになります。
ビジネスや製造業だけでなく、日常の仕事や生活の中でも、ムダを意識して見直すことで、よりスムーズな進行や成果を得ることができる指針となります。
7つのムダの起源はトヨタ生産方式
今でこそ製造業以外の業界にも広く浸透した「7つのムダ」ですが、初めて提唱したのはトヨタだと言われています。
トヨタ生産方式(TPS)の中心にある「カイゼン」の思想から7つのムダが誕生しました。カイゼンとは、日々の業務やプロセスを見直し、小さな改善を積み重ねて効率化や品質向上を図る考え方です。このアプローチの中で、効率的な生産を妨げる要因として「ムダ」に注目が集まりました。
生産現場では、従業員が問題を発見しやすくし、具体的に改善する対象を明確にする必要があります。そのために、ムダを体系化し、「7つのムダ」として分類したのです。これにより、現場で誰もが以下の問いを考える指針が得られました。
- 価値を生まない活動は何か?
- 不要な動きや手間がどこにあるのか?
- どのように削減すれば効率化できるのか?
「7つのムダ」は、単なる非効率の分類ではなく、カイゼン活動を具体化し、生産現場の全員が主体的に取り組む文化を育むための道具として誕生しました。この考え方は、日常的な改善を促進し、トヨタの競争力を支える重要な柱となっています。
現場改善ラボでは、トヨタ自動車元理事でいらっしゃる小森 治氏による、トヨタ生産方式に基づく現場改善について解説した無料動画を公開しています。製造業においてはもちろん、それ以外の業界に共通して活用できる「カイゼンの視点」を得ることができます。以下のリンクをクリックしてご覧ください。
>>トヨタ元理事が語る「トヨタ生産方式と改善の着眼点」を見てみる(視聴無料)
製造現場における「7つのムダ」を詳しく解説
それでは、7つのムダの詳細を解説していきます。ここでは、製造業における以下の7つのムダを紹介していきます。
製造業”以外”における7つのムダに関しては、記事後半の「事務系職場における7つのムダ」で解説しているので、現場作業ではなくデスクワークをメインに行っているという方は、ぜひそちらをご覧ください。
まずは7つのムダを覚える語呂合わせを確認しましょう。
7つのムダの覚え方:「かざふてつどう」
一般的な覚え方は、「かざふてつどう」と「かざつでどうふ」の2種類があります。どっちが正しいということはないので、自分にとってしっくり来るほうで覚えると良いでしょう。
ここでは、「かざふてつどう」を紹介します。
- 「か」:加工のムダ
- 「ざ」:在庫のムダ
- 「ふ」:不良・手直しのムダ
- 「て」:手待ちのムダ
- 「つ」:作り過ぎのムダ
- 「ど」:動作のムダ
- 「う」:運搬のムダ
加工のムダ
加工のムダとは、必要のない加工を行うことで生じるムダのことを指します。製造現場の場合、主に「必要のない作業」と「必要のない検査」の2つがあるでしょう。
「必要のない作業」の例
「作業効率向上のために、メックネジ(ネジ部に接着剤があらかじめ付着されているネジ)が導入されたにも関わらず、現場にメックネジについての説明がなされずに、接着剤を用いていた」という事例は、わかりやすい加工のムダです。
振動等によって緩みやすい箇所は、ネジ締めを行う際に接着剤を用いることがあります。しかし手作業での接着剤塗布は、塗りむらや作業者によるバラツキが出てしまいやすい傾向です。
そこで開発部署は、使用するネジをメックネジという、ネジ部にあらかじめ接着剤を塗布する仕様に変更して、生産管理者はメックネジを発注しました。ところがその変更が現場には伝わっておらず、現場ではメックネジを締める際に接着剤を塗布し続けていたのです。
「必要のない検査」の例
必要のない検査を行っていた事例を2つピックアップしました。いずれも、本来であれば必要のない作業であり、加工のムダといえます。
- 良品率、直行率ともに高いにも関わらず、品質保証部が外注企業に全数検査を依頼
- 検査不正を防止する監視員を配置したが、業務がまともに遂行されず監視員を監視する人員も配置
在庫のムダ
在庫のムダとは、以下の4つの在庫を持ちすぎることをいいます。
- 原材料
- 部品
- 仕掛品
- 完成品
「なぜここにあるのか」を説明できない在庫はすべてムダと定義されています。ここでは、原材料と完成品のムダを例に、さらに詳細を見ていきます。
「原材料のムダ」の例
たとえば「原材料の投入ミスが発生したときのために多めに原材料在庫を用意しておく」という在庫の持ち方は、一見合理的に思えます。しかし、原材料を多く在庫しておくことで「倉庫の維持・管理コストのムダ」「在庫管理のムダ」を生み出します。
さらに「失敗したら予備の原材料を使う」というスキームが恒常化することで、「原材料の投入ミスが頻繁に生じる異常な状態」が隠れてしまいます。本来は「原材料の投入ミスが発生しないような作業工程を考えること」が正しい対処法といえるでしょう。
「完成品のムダ」の例
短納期への対応として完成品を多めに在庫すると、仕様変更によるデッドストックや不良品発生時の検査・手直しの手間が増え、倉庫保管や棚卸の負担も膨らみます。
こうした過剰在庫は営業努力の一環ではあっても、経営を圧迫するリスクを伴うことを認識すべきでしょう。
不良や手直しのムダ
不良や手直しのムダには多数のムダが内包されています。ここではその代表的なものをピックアップしました。
- 不良品の発生による「ライン停止のムダ」
- 不良品の選別や回収、原因究明によって生じる「人件費のムダ」
- 不良品の手直し・作り直しによって生じる「人件費・材料費のムダ」
- 不良品の再発防止策を講じるためにかかる「コストのムダ」
- 不良品の廃棄によって生じる「原材料・廃棄コストのムダ」
製造している製品の用途や材料、単品なのかアッセンブリーなのかによっても不良によって生じるムダは異なりますが、いずれにしても不良によって生じるムダは他のムダと比較しても、損失が計り知れません。
「不良のムダ」の例
不良が発生すると、営業担当者は顧客先での選別や原因究明、不良品の回収を迅速に行い、生産現場や品質保証部も在庫の選別や再発防止対策、全数検査等に追われます。
外注費や残業代が増え、新規活動も停滞し、社内のモチベーションにも悪影響を及ぼすなど、大きなムダが発生します。さらに顧客からの信頼回復に時間を要し、対応が長期化すれば1年以上も全数検査が続く場合があるなど、企業全体に大きな負担をもたらします。
関連記事:【改善事例あり】製造業における品質不良の原因と8つの対策
手待ちのムダ
手待ちのムダとは、作業者がやるべき仕事がない遊んでいる状態で生じるムダです。
「前工程の遅延」や「おおざっぱな生産計画による不均一な作業量」「機械の故障による作業のストップ」「原材料の配送遅延」といった原因で発生します。
手待ちのムダは、人件費のムダや生産効率の低下に直結するムダです。ときには手待ちのムダによって、「忙しく働いている作業者」が「手待ちの多い作業者」への不満を募らせて、現場の人間関係が悪化することもあります。
「手待ちのムダ」の例
手待ちのムダは、前工程の不良や原材料の遅延などが原因で作業が滞り、後工程の人員が手持ち無沙汰になる状況を指します。
生産計画の不均一や機械故障も同様の事態を引き起こし、その間の人件費や残業代が無駄に増大するのです。さらに納期や納品数を変えにくい場合、手待ちが解消されても法定外労働が必要となり、企業全体のコストとスタッフ負担が膨らみます。
作りすぎのムダ
作りすぎのムダとは、製品を作りすぎることによって生じるムダです。
作りすぎのムダは在庫のムダや手待ちのムダに繋がります。作りすぎて在庫が増えれば在庫管理の手間がかかりますし、過剰在庫状態になれば、手待ちのムダが生じてしまいます。
また作りすぎの状態が常態化すると、さまざまなミスや異常状態が見過ごされやすくなるリスクもあります。
「作りすぎのムダ」の例
作りすぎのムダとして、ベテラン作業者が機械トラブルに備えて指示以上に製品を製造し、隠し在庫を抱えていたという例をご紹介します。
急な注文に対応できる利点はありましたが、仕様変更で余剰在庫はすべてデッドストック化しました。本来なら他の製品を製造できた作業時間も失われ、生産管理のミスが隠し在庫に頼って改善されないまま繰り返されるなど、多面的にムダを生み出しています。
動作のムダ
動作のムダとは、製造の進捗に関係しないすべての動作です。製造するために欠かせない動作であっても、その動作によって製品が完成に近づかなければ動作のムダと判断されてしまいます。
たとえば、「作業手順をを忘れたから事務所に戻って調べる」「治具が見当たらないから探す」「棚の下にある材料や工具を取るためにしゃがむ」「作業を進めるために、何度も工具を持ち替える」といった動作は、動作のムダです。
「動作のムダ」の例
動作のムダに該当する複数の事例を紹介します。
- 作業員の数に工具の数が見合わず、工具を使うために工場内をくまなく探す
- 冶工具が工場内のあちこちに保管されており、作業者の移動距離が長い
- 作業標準が現場に掲示されておらず、不慣れな作業者は事務所へ確認しに行く必要がある
- 作業標準がテキストベースで、作業者が動きを理解できず読み込む時間が長い
- 必要な工具・材料等の保管場所が、地面に近く何度もしゃがまなければならない
運搬のムダ
運搬のムダとは、必要のない運搬のことです。
仕掛品や原材料、部品等を取りに行く作業や、仮置き場所への運搬、余剰在庫の倉庫への運搬、在庫の管理などが運搬のムダといえます。運搬のムダは、原材料や仕掛品、完成品などの過剰在庫によって生じることもあれば、作業場のレイアウトの悪さによって生じることもあります。
運搬のムダの事例
以下のような事例は運搬のムダです。
- 原材料の「仮置き場」「保管場所」が存在し、在庫状況を確認し保管場所を決める手間がある
- 前工程と後工程の作業場が工場内で離れており、仕掛品を後工程に運ぶ時間がかかる
- 完成品の在庫が多く、完成のたびに箱詰め・フォークリフトで立体倉庫に運ぶ必要がある
- 原材料や部品置き場と作業場が離れており、運搬に時間がかかる
7つのムダの中で一番ダメなのはズバリ、不良や手直しのムダ!
さて、ここまで7つのムダをそれぞれ詳しく紹介してきましたが、結局どれが一番悪いのでしょうか?
人によって意見が割れるとは思いますが、私たちとしては「不良や手直しのムダ」が優先的に解消すべきムダだと考えています。本章では、そのように考える理由を解説します。
不良や手直しのムダは一番最後の工程で発生する
不良や手直しのムダの「不良」は、客先に流出してから発覚するものもあります。この「不良のムダ」が発生してしまうと、たとえどんなに前工程でムダを改善したとしても、不良を検知できていなければすべてが水の泡になります。
最後に発生するムダだからこそ、最優先で改善を行うべきなのです。
他のムダに波及し、カバーするのに大きなコストを伴う
「動作のムダ」や「加工のムダ」などは、たとえ発生したとしてもその行程の中だけで事態が収まります。
ですが「不良や手直しのムダ」は、発生すると修理や再加工をしないといけないので、「動作のムダ」や「加工のムダ」、「運搬のムダ」が追加で発生します。
1つ発生してしまうと他のあらゆるムダも誘発してしまう、それが「不要や手直しのムダ」なのです。
企業のブランド価値低下を招いてしまう
他の6つのムダは自社の中だけで完結するムダですが、「不良や手直しのムダ」だけは外部に影響を及ぼすムダです。不良品が外部に流出することによって「あの会社の作る製品は品質が良くない」と、ブランド価値を低下させてしまう危険性があります。
たとえどんなに「加工のムダ」や「動作のムダ」を省いて生産効率を向上させたとしても、ブランド価値の低下によって取引先を失ってしまえば意味がありません。
このような3つの理由から、私たちは「不良や手直しのムダ」が最も優先的に改善すべきムダだと考えています。そして、2019年版ものづくり白書でも言及されているように、品質トラブルが生じる原因として従業員教育の不足といった「人」に起因するものが挙げられます。
現場改善ラボでは、人に起因する品質不良の改善策について、専門家による解説動画を無料で公開しています。以下の画像をクリックしてご活用ください。
不良や手直しのムダを改善するカギは”標準化”にあり
7つのムダにはそれぞれ改善の方法がありますが、ここでは「不良や手直しのムダ」にフォーカスして、改善方法を紹介していきます。
結論から述べると、「不良や手直しのムダ」を改善するために最も重要なことは”業務標準化”です。
業務標準化とは、すべての人が同じ手順で作業を行えるようにすることです。標準化がされていない現場では、作業員それぞれのやり方が異なるため、業務品質にバラツキが生じます。ですが標準化がされていると、皆が同様の手順で作業を行うので、必然的に業務品質のバラツキも一定の範囲に抑えられるのです。
業務標準化を徹底的に推進している現場こそ、7つのムダを考案したトヨタ自動車です。現場改善ラボでは、トヨタの現場を知る専門家による「トヨタ式標準化の推進方法」の解説動画を無料で公開しているので、リンクをクリックしてご覧ください。
また製造現場において、作業手順のような「動き」を標準として伝える手段として、動画マニュアルを活用して視覚的に理解できる取り組みを推進しているケースが増えています。次章では、標準化を推進する手段として「動画」が有効な理由を整理しましょう。
標準化を効果的に進めるには動画マニュアルがおすすめ
標準化の具体的な方法については、さきほどご紹介した記事や動画で詳しく説明しているので、ここでは標準化を効果的に進める方法の1つとして、動画マニュアルをご紹介します。
動画マニュアルとは、実際の作業風景を動画として撮影し、そこにさらに編集を加えたものです。
▼動画マニュアルのサンプル▼
動画マニュアルが標準化におすすめな理由
標準化を進める上で、従来の紙マニュアルより動画マニュアルを活用したほうが効果的である理由は、主に以下の2つです。
- 作業の”標準”が映像で直観的に理解できる
- 自習教材として使いやすい
作業の”標準”が映像で直観的に理解できる
紙のマニュアルだと、書かれてある文章から動作をイメージしないといけませんが、動画マニュアルは、動作をそのまま映像で伝えることができるので、より直観的です。
この”わかりやすさ”があることによって作業者は、マニュアルの手順通りに業務を行うことができます。結果的に作業手順のばらつきが抑えられ、標準化が促進されるのです。
自習教材として使いやすい
標準化は、作業者が自ら学習することによっても促進されます。動画マニュアルは、作業者が自ら学習する自習教材としても適切なのです。
運用方法のイメージとしては、eラーニングを思い浮かべるとわかりやすいでしょうか。たとえば、新人が入ってきたときOJT教育を行うと思われますが、その復習として動画マニュアルを視聴し、反復学習してもらう活用が考えられます。
動画マニュアルのその他のメリット
動画マニュアルは、標準化以外の観点でもメリットがあります。
マニュアル作成の工数が大幅に削減できる
動画でマニュアルを作成すると、紙で作成するよりも大幅に時間を短縮できます。紙のマニュアルだと、動作を表現するための文章を考える必要があり、そこにかなりの時間を要してしまいます。
ですが動画マニュアルなら、撮影とかんたんな編集を行うだけで済みます。実際、動画マニュアルを活用することによって、手順書の作成工数を1/3に軽減した事例も存在します。
インタビュー記事:OJTや手順書作成工数を大幅に削減!熟練者の暗黙知も動画で形式知化
加工のムダ・動作のムダも併せて改善できる
動画マニュアルを活用して、普段行っている作業手順を映像として可視化してみると、思わぬところで発生している加工のムダや動作のムダを発見できます。
世界最高水準の真空技術を活用した製品を幅広く展開している株式会社アルバックでは、動画マニュアルを活用して2拠点間の作業手順を比較し、より効率的な手法に統一する試みを行っています。
この取り組みによって、1日あたりの生産数が改善以前の167%となり、67%もの生産性向上を実現しています。具体的な取り組み内容は、インタビュー記事「人員・労働時間を変更せずに、ボンディング工程の生産性を167%に改善」をご覧ください。
このように製造業において、動画マニュアルを活用して改善を実現している事例が増えています。今回ご紹介したような、製造現場の動画マニュアル活用事例をまとめた資料をご用意しているので、以下の画像をクリックして内容をご覧ください。
動画マニュアルの活用で7つのムダが改善された事例
ここからは、動画マニュアルを活用して7つのムダを改善した実際の事例を観ていきましょう。「不良や手直しのムダ」と「それ以外のムダ」に分けて、それぞれの改善事例を紹介していきます。
不良や手直しのムダが改善された事例
手順不遵守による品質不良を9割削減!児玉化学工業株式会社
住宅設備や自動車向けの樹脂製品を製造/販売する児玉化学工業株式会社では、動画マニュアル活用による業務標準化に取り組み、手順不遵守による品質不良を9割削減しています。
▼インタビュー動画:児玉化学工業株式会社▼
新人の従業員や外国人従業員を抱え、紙の作業手順書/マニュアルでは作業の手順やコツを伝えきれなかった同社は、動画マニュアルを活用したことで作業内容を視覚的にわかりやすく伝えることができました。
従業員が理解しやすくなかったことで作業手順の標準化が進み、結果的に手順不遵守による品質不良を9割削減しています。この品質改善は、かんたん動画マニュアル作成ツール「tebiki現場教育」の活用によって実現した事例です。
より具体的な、動画マニュアルを活用した品質向上の取り組み事例は、以下のリンクをクリックしてインタビュー記事をご覧ください。
インタビュー記事:手順書作成の工数は紙の1/3になったと思います。動画で作るのはかんたんだし、学ぶ側にもわかりやすいですよね。
溶断・サンダー工程での不良が月4.3件→月2.4件に!クマガイ特殊鋼株式会社
クマガイ特殊鋼は、鋼板と呼ばれる大きな鉄板をガス溶断機やレーザー切断機などで切断・加工し販売している鋼板の専門商社です。
同社が動画マニュアルの活用を検討した当初の理由は、作業手順書が形骸化していたり、文字や画像だけで作業のカンコツを伝えることに限界を感じていたからでした。
動画マニュアルの導入によってまず現れた効果としては、教育の質向上と、教育者の負担軽減でした。
期待していなかった効果として現れたのが、品質不良の改善です。動画マニュアルで教育をするようになってから作業手順が遵守されるようになり、結果として溶断・サンダー工程での社内不良が月4.3件から、月2.4件へと減少しました。
インタビュー記事:人材危機に立ち向かう創業100年以上の中小企業。tebikiの活用で教育体制の改革と多能工化を推進!
不良や手直しのムダ”以外の”ムダが改善された事例
加工/動作のムダを改善し生産性67%UP!株式会社アルバック
株式会社アルバックは、世界最高水準の真空技術を有し、様々な製品やサービスを提供する企業グループです。
同社は当初、作業品質の安定化や人材育成の効率化などを目的として動画マニュアルの導入を進めていました。ですが、別の課題として存在していた、「拠点間ごとでの生産量の開き」を解消することにも、動画マニュアルの活用を検討したのです。
具体的な取り組みとしては、定点カメラで作業動作を動画として記録し、加工のムダや動作のムダを発見していくというものでした。
この動画マニュアルを活用した取り組みによって、ムダのない最適な作業手順を全ての拠点で標準化し、結果として、月の生産性を67%向上させたのです。
インタビュー記事:人員・労働時間を変更せずに、ボンディング工程の生産性を167%に改善
新人の手待ちのムダを改善!日本クロージャー株式会社
日本クロージャーは、各種金属キャップ、樹脂キャップ及び樹脂製品の製造販売を行っている企業です。
同社では、ベテラン作業者が日々の業務に忙しく、新入社員の教育になかなか時間をさけないことが課題でした。新入社員から業務に関する質問が来た時、「ちょっと待ってね」と20~30分待たせてしまうこともざらにあり、新人の手待ちのムダが多い状態でした。
そこで導入したのが動画マニュアルでした。今まで口頭で指導していた内容を動画にすることで、新入社員はベテラン作業者に聞かなくても動画を観て自力で解決できるように。結果、教育の7割程度は動画による自習に置き換わり、新人の手待ちのムダは解消されました。
インタビュー記事:新人OJTの7割を動画に置き換え。組み込み/分解/金型作業など、製造現場の動画マニュアルを作成。教育の手間を大幅に削減しました。
誰でもかんたんに始められる動画マニュアル「tebiki」
動画マニュアルは様々なムダを改善するのに大きな効果を発揮しますが、やはり難しさが懸念として残るでしょう。
さきほどの事例でご紹介した事業者が共通して使っている動画マニュアルは「tebiki」です。「tebiki」は、初めて動画マニュアルに取り組む人でもすぐ使いこなすことができます。
ここでは、「tebiki」の魅力について解説します。
▼動画マニュアル作成ツール「tebiki」紹介動画▼
マニュアル作成に必要な機能だけを厳選しているから「かんたん」
tebikiは、とにかく「操作のかんたんさ」にこだわって作られたツールです。マニュアル作成にほんとうに必要な機能だけを残し、不要な機能はそぎ落とした設計になっています。
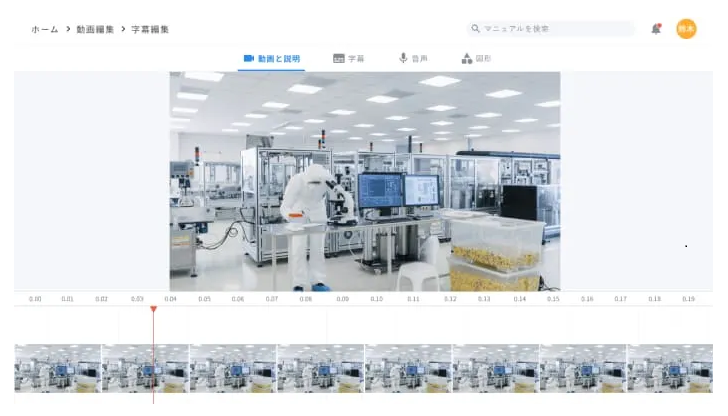
操作画面はシンプルで使いやすく、編集スキルがない方やパソコン操作に不慣れな方でも直感的に動画マニュアルが作成できます。
実際にtebikiを活用することによって、1本の動画マニュアルを作るのに1時間かかっていたのが、たったの15分ほどに短縮された事例も。
また、操作が簡単だからこそtebikiを活用できる人が増え、動画マニュアルの作成スピードが加速度的にアップします。
以下の事例記事では、tebikiがどれくらい簡単にマニュアルを作成できるのかをご確認いただけます。
インタビュー記事:動画マニュアル作成時間が75%削減!教育体制を強化し、お客様に喜ばれる商品を提供したい
テスト機能やレポート機能で、理解度や学習進捗度を把握できる
tebikiには従業員の理解度をチェックするための「テスト機能」が搭載されています。動画視聴後や研修後にテストを実施することで、従業員一人ひとりがどの程度業務を理解しているかを把握したうえで、教育内容や頻度を調整することが可能です。
また、テストの自動採点機能もついているため、教育担当者は手間をかけずに従業員のスキルを確認できます。
▼tebikiで作成したオリジナルテスト▼
(株式会社大商金山牧場の導入事例より)
.jpg)
100ヶ国語以上の言語に自動翻訳
tebikiの動画マニュアルは、100ヶ国語以上の言語に自動翻訳できる機能が付いています。外国人労働者が使うためのマニュアルをわざわざ翻訳して作る必要がなくなります。さらに、英語やベトナム語などの計15言語で字幕を読み上げられるため、母国語で説明を聞きながら理解を深めてもらうことが可能です。
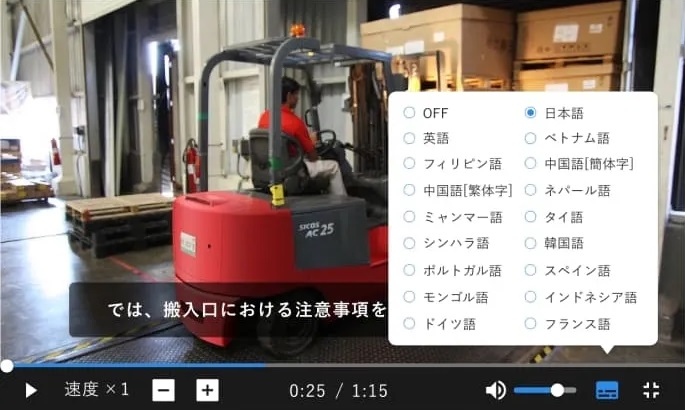
気になる「精度」ですが、日本語の日常会話程度であれば、問題なく伝わるレベルです。もし自動翻訳で伝わらないということであれば、後から修正することも可能です。
以下の記事では、実際にtebikiを活用して外国人教育が効率化された事例をご紹介しています。外国人労働者の教育工数を課題に感じていらっしゃる方はぜひご覧ください。
インタビュー記事:新人研修の手間が1/10に!自動字幕翻訳で、外国⼈スタッフの理解度テスト正答率が100%になりました。
本記事でご紹介できたtebikiの機能はほんの一部です。さらに詳細な内容は、資料にまとめています。ぜひ、tebikiの活用にご興味を持たれた方は、以下をクリックして資料を無料ダウンロードしてみてください。
事務系職場における7つのムダ
では、最後の「まとめ」に入る前に事務系職場における7つのムダについても解説します。事務系職場における7つのムダは以下の内容です。
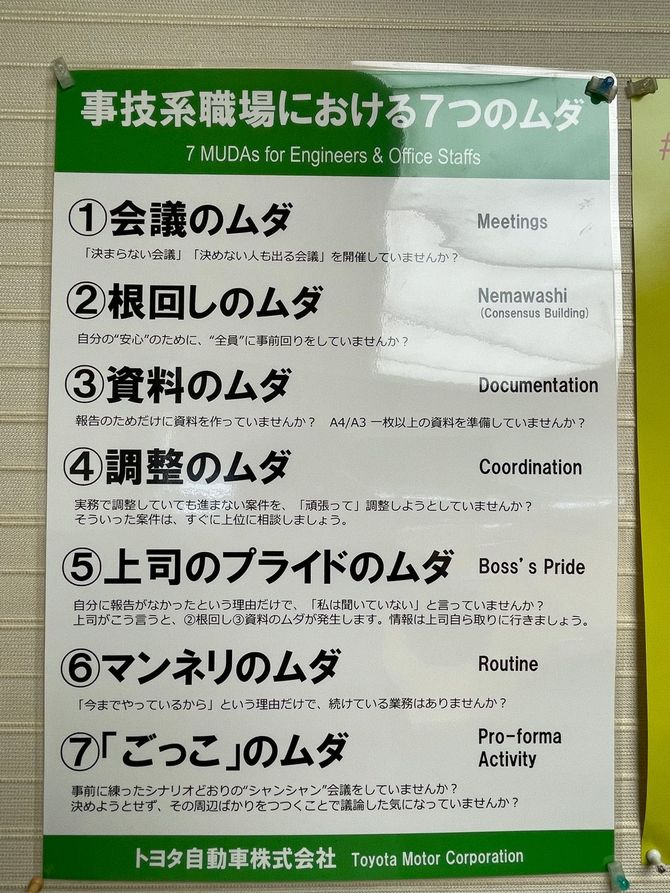
会議のムダ
会議のムダとは、目的や効果が曖昧なまま行われる無駄な集まりを指します。
例えば、特に意思決定が行われず、単なる情報共有に終始する会議や、参加者全員が発言する必要がないのに全員出席が求められる場合が典型です。
根回しのムダ
根回しのムダとは、必要以上に多くの人を巻き込む事前調整が業務効率を低下させることを指します。
具体的には、全員の了承を得るために繰り返される個別の打ち合わせや、実務に影響しない人への形式的な説明などが含まれます。
資料のムダ
資料のムダとは、過剰に作成される資料が時間や労力を浪費することを指します。
例えば、毎回ほとんど読まれない詳細なレポートを作成したり、使い道が不明確な資料を大量にコピーする行為がこれに該当します。
調整のムダ
調整のムダとは、過剰な調整作業によって実務のスピードが低下することを指します。
例として、関係者のスケジュール調整に時間をかけすぎたり、不必要に多くの人の意見を求めて手戻りが発生する場合があります。
上司のプライドのムダ
上司のプライドのムダとは、上司の自己満足が業務効率を妨げる行動を指します。
具体例として、上司の意見を無理に尊重するために無意味な手直しを繰り返したり、上司の承認が必須とされることで決裁が遅れる場合があります。
マンネリのムダ
マンネリのムダとは、古い習慣や慣例に縛られることで業務効率が低下することを指します。
例えば、既に不要となった定例業務や、目的が失われたルーチン作業を続けている場合が典型です。
「ごっこ」のムダ
「ごっこ」のムダとは、実態のない形式的な取り組みが時間やリソースを浪費することを指します。
例えば、実効性のない形だけの改革活動や、成果を出すよりも「やっている感」を重視したイベントや施策がこれに該当します。
7つのムダを把握して、現場の生産性を向上させよう【まとめ】
ここまで7つのムダについて解説してきました。
7つのムダとは、仕事や作業の中で発生する非効率な要素=無駄(ムダ)を整理した考え方・フレームワークのことで、それぞれ「加工のムダ」「在庫のムダ」「不良や手直しのムダ」「手待ちのムダ」「作りすぎのムダ」「動作のムダ」「運搬のムダ」です。
全てのムダを一気に改善するのは大変なので、最も効果のあるところから徐々に着手していくべきでしょう。現場改善ラボがおすすめするのは、「不良や手直しのムダ」です。
そして、「不良や手直しのムダ」を改善するための方法は”標準化”です。作業者の作業手順を統一することによって、作業品質にばらつきがなくなり、結果として「不良や直しのムダ」がなくなります。
標準化を効率的に進めたいなら、動画マニュアルを活用すると良いです。今までの”紙の”手順書では、そのわかりづらさのために、読み手が誤った解釈をしてしまうなどがありましたが、”動画の”手順書は、映像で直観的に理解できます。
「tebiki」なら、動画マニュアルをかんたんに始めることができます。以下の資料には、「tebiki」の詳細な機能やメリット、活用事例などをわかりやすくまとめています。無料でダウンロードできるので、ぜひご覧ください。