かんたん動画マニュアル「tebiki」、かんたん現場帳票「tebiki現場分析」が運営するWEBメディア・現場改善ラボ編集部です。
「チョコ停(ちょこてい)」とは、短時間で復旧する一時的な設備停止を指します。本記事ではチョコ停の定義や計算式、ドカ停との違いについて解説します。また、チョコ停の対策に必要な、メンテナンス手順の標準化や属人化の解消方法、設備の不具合を検知する仕組みもご紹介します。
「チョコ停が定期的に発生しているが原因・対策がわからない…」とお悩みの方に向け、チョコ停ゼロを達成するヒントが詰まったハンドブックもご用意しております。以下のリンクをクリックし、是非お役立てください。
>>チョコ停ゼロ・安定稼働を達成するには?設備保全改善のヒントをみる(無料配布中)
目次
チョコ停とは?ドカ停との違いも解説
チョコ停は何分から?定義や言い換え
チョコ停とは設備が短時間で停止し、すぐに復旧する軽微なトラブルのことを指します。「日本工業規格の生産管理用語」によると、設備が規定の機能や性能を失い、産出物や作用が規定の品質レベルに達しなくなる状態とされています。
一般的にチョコ停の停止時間は数秒~数分程度で、現場では「空転ロス」「空運転」などと言い換えられることもあります。
チョコ停は製造業における7大ロスの一つであり、特に性能ロスに分類されます。以下は7大ロスの一覧です。
故障 | 設備の故障による停止 |
段取り/調整 | 生産ラインの変更や調整によるロス |
工具交換 | 工具の交換に伴うロス |
立ち上がり | 新しい設備や製品の立ち上げに伴うロス |
速度低下 | 設備の速度低下によるロス |
チョコ停/空運転 | 短時間の一時的な停止によるロス |
不良/手直し | 製品の品質不良や手直しによるロス |
これら7大ロスは、製造現場のKPI指標として見られる「設備総合効率(OEE)」を低下させる主要因として、多くの製造現場で重要な改善対象とされています。
一見するとチョコ停は軽微な問題のように見えますが、発生頻度が高いと生産性に大きな悪影響を与えます。たとえ1回あたりのロスが小さくても、積み重なることでラインの稼働率や出荷数にまで影響が出るため、見逃せない課題です。
ドカ停との違い
ドカ停とはチョコ停とは異なり、設備が長時間にわたって停止する重大な故障のことです。「日本工業規格の生産管理用語」によると、システム全体を停止させるような重大な故障を「ドカ停」といい、通常1時間以上の停止を伴います。チョコ停が数分で復旧するのに対し、ドカ停は復旧に長時間を要するため、影響が大きくなります。
つまり大まかに分けると、設備が生産ラインなどの大規模なシステムの一部として機能している場合、システム全体を停止させるような重大な故障を「ドカ停」、逆に短時間に回復できる部分的な停止や不具合を「チョコ停」といいます。
チョコ停は短時間で済むため見逃されやすいですが、頻繁に発生するとドカ停の前兆となりえます。つまり、チョコ停の積み重ねがドカ停を引き起こす可能性があるため、チョコ停の管理と対策が不可欠です。
チョコ停の計算式
チョコ停の計算式について、ここでは以下の2パターンを解説します。
- チョコ停時間
- チョコ停率
チョコ停時間
チョコ停時間とは、設備が停止してから復旧するまでの時間を指します。チョコ停時間を正味稼働時間から差し引くことで、稼働率の低下を具体的に把握できます。計算式は以下の通りです。
- チョコ停時間=全稼働時間−正味稼働時間
たとえば1日の全稼働時間が24時間で、チョコ停による停止時間が合計で2時間あった場合、チョコ停時間は以下のようになります。
- チョコ停時間=24時間−22時間=2時間
これにより、チョコ停がどのくらいの間で発生し、生産効率に影響を与えているかを明確にできます。
チョコ停率
チョコ停率とは、全稼働時間に対するチョコ停時間の割合を示す指標のことです。チョコ停率を用いることで、チョコ停の影響を相対的に評価することが可能です。計算式は以下の通りです。
- チョコ停率=チョコ停時間/全稼働時間×100
たとえば全稼働時間が24時間でチョコ停時間が2時間の場合、チョコ停率は以下のようになります。
- チョコ停率=2時間/24時間×100=8.33%
チョコ停率を計算することで、短時間の停止が全体の稼働にどれだけ影響を及ぼしているかを可視化できます。
チョコ停が現場にもたらす4つの影響
チョコ停は短時間で復旧できるため生産スケジュールへの影響も少ないと誤解されることが多く、放置されやすい傾向にありますが、頻発することで生産ライン全体に蓄積的なロスをもたらす可能性があるため、注意が必要です。
ここではチョコ停がもたらす悪影響について、4つの切り口から整理します。
チョコ停は設備総合効率(OEE)など、現場で指標とすべき数値に直接影響を与える重大な課題です。設備総合効率を下げる原因や「現場の可視化」による改善策の立て方についても知りたい方は、是非以下の無料動画をご覧ください。
稼働率や生産能力の低下
数分で復旧できる「チョコ停」ですが、それが1日に何度も繰り返されると、気づかないうちに大きな生産ロスを生み出します。現場感覚では「対応できているから問題なし」と見過ごされがちですが、積算すると確実に稼働率を押し下げ、生産能力の低下につながります。
たとえば、1回5分のチョコ停が1日に10回発生すれば、合計で50分の停止時間が発生します。これは24時間稼働の工場において、約0.83時間=3.5%の稼働ロスに相当します。
- チョコ停時間=5分 × 10回=50分(0.83時間)
- 稼働率=(24時間 − 0.83時間) ÷ 24時間 × 100=96.54%
一見小さな差に見えるかもしれませんが、これが毎日続けば月間で約25時間の停止時間となります。1日以上の操業分が失われることになり、生産計画の遅れやコスト上昇、納期遅延のリスクが現実味を帯びてきます。
こうした「小さな停止の積み重ね」が、気づいたときには大きな損失になっている――それがチョコ停の本当の怖さです。現場では見えにくい稼働ロスとして蓄積されている可能性があることを、今一度認識する必要があります。
品質問題の発生
チョコ停は単なる「停止時間のロス」にとどまらず、製品の品質にも深刻な影響を及ぼす可能性があります。設備が停止して再稼働する際、温度や圧力、タイミングなどの制御値がわずかにずれることがあり、その変化が製品の仕上がりに微妙な差を生むのです。
たとえば、射出成形の現場ではチョコ停によって金型の温度バランスが崩れ、再立ち上げ後に成形品に反りや気泡が生じることがあります。見た目にはわからないような小さな変化でも、製品基準を満たさない不良品として扱われることになり、歩留まりが悪化します。
こうした品質トラブルには、以下のような現実的な影響が伴います。
不良品率の増加 | わずかな条件変化でも、連続する製品の中で 一定の割合で不良が発生しやすくなる |
追加コストの発生 | 手直しや仕掛品の廃棄、ライン停止によるリカバリ対応など 目に見えないコストが蓄積 |
顧客からのクレームリスク | 出荷後に異常が判明した場合、 信用失墜や返品・回収といった大きなダメージに発展 |
チョコ停は「その場で復旧すれば終わり」と思われがちですが、見えにくい品質リスクが潜んでいることを忘れてはなりません。特に精密さが求められる製造現場では、チョコ停による微細な影響が顧客満足度に直結するリスクもあるため、現場全体での意識改革が必要です。
関連記事:【改善事例あり】製造業における品質不良の原因と8つの対策
納品遅延による信頼損失
チョコ停は、その場で対処しても生産スケジュール全体をじわじわと圧迫する厄介な存在です。たとえば、1回5分のチョコ停が1日に10回発生すれば、合計で50分もの生産時間が失われることになります。表面的には「少し止まっただけ」と見えるかもしれませんが、その累積が製造計画のズレを引き起こし、最終的に納期遅延につながる恐れがあります。
特にタクトタイムが厳密に管理されているラインや、部品供給と組立が連動しているような現場では、わずかなズレが他工程にも波及し、全体工程の遅延に発展するリスクが高くなります。
納期遅延が発生した場合、以下のような深刻なトラブルにつながる可能性があります。
顧客満足度の低下 | 納品遅れにより「納期が守れない会社」という印象を与え、 信頼を損なう |
追加コストの発生 | 突発的な残業・休日稼働、緊急便対応など 想定外のコストが発生 |
契約違反リスク | 納期遵守が契約条件となっている場合 違約金や取引停止といった経営上の損失に直結 |
「わずか数分の停止だから」と油断していると、その代償は生産現場だけでなく、顧客との関係や企業全体の信用にまで影響を及ぼします。チョコ停は単なる現場課題ではなく、全社的なリスクとして捉える必要があります。
労働災害など安全トラブルの増加
チョコ停が頻繁に発生すると、「すぐに直さなければ」という焦りから、作業員が普段の安全手順を省略して復旧作業に入ってしまうケースが少なくありません。繰り返し発生する軽微なトラブルほど、「慣れ」による油断が生まれやすくなります。
一見すると些細な作業に見える復旧対応ですが、安全確認を怠れば深刻な労働災害に直結するリスクをはらんでいます。例として、以下のような事故がチョコ停対応中に発生することが考えられます。
挟まれ・巻き込まれ事故 | 稼働確認中の設備に手を入れてしまい、 可動部分に指や腕を挟まれる |
火傷事故 | 加熱装置や成形機など高温部に不用意に触れ、 火傷を負う |
墜落・転倒事故 | 復旧を急ぐあまり足場のない場所に上がり、怪我をする |
これらの事故は、本来であれば手順を守っていれば防げたものです。しかし、チョコ停の頻発が作業員の「心理的な焦り」や「作業の雑さ」を引き起こし、安全意識の低下を招いてしまいます。
チョコ停がもたらすリスクは稼働率や品質だけでなく、現場の安全文化そのものを揺るがす可能性があることを認識する必要があります。繰り返し発生するチョコ停にどう向き合うかが、安全で持続可能な現場づくりの鍵となります。
関連記事:工場の安全対策10選と好事例を解説!製造業の安全宣言例も紹介
チョコ停の主な原因は?
チョコ停は一見すると偶発的なトラブルに見えますが、発生の背後には構造的な課題や日常業務の盲点が潜んでいます。ただ単に「原因を分類する」だけでなく、「なぜそれが起きるのか」を掘り下げることで、再発を防ぐための改善視点が見えてきます。
以下では、4つの主な原因に加えて、それぞれの背景にある根本的な問題を詳しく解説します。
「チョコ停ゼロ」を達成するには、設備停止の原因を正しく把握し、適切に対処する必要があります。チョコ停対策の仕組み作りや分析方法について詳しく知りたい方は、以下の画像をクリックし詳細な資料をご覧ください。
設備に関する原因
設備トラブルによるチョコ停の背景には、「予防保全が不十分であること」が多くあります。たとえば、定期点検が形骸化していたり、清掃が後回しにされていたりすることで、本来なら早期に発見できたはずの不調が見逃されるのです。
- 摩耗部品の交換時期を過ぎたまま稼働を続けた結果、動作不良で停止
- センサーの汚れにより、製品を誤検知してラインが停止
- 清掃不足で削りくずや異物が蓄積し、機構部が正常に動作しない
こうした設備の問題は、「止まるまで放置される」という現場習慣によって見過ごされがちです。「停止=発見」の受け身ではなく、未然に気づける管理体制が必要です。
予防保全を実現させるには、単に点検の頻度や内容を定めるだけでなく、誰が担当しても同じ水準で保全が実施できる仕組みづくりが欠かせません。とはいえ、現場では「保全といえばあの人」というように、特定の熟練者にノウハウが偏り、属人化してしまっているケースも少なくありません。
そうした属人化の課題を解消するには、どこから手をつければよいのでしょうか?設備保全の仕組み化に向けた3つのポイントについて、専門家がわかりやすく解説した動画をご紹介します。是非ご覧ください。
>>設備保全の属人化、どう防ぐ?作業分析による改善の実践方法を解説!(無料公開中)
材料・部品に関する原因
材料や部品に起因するチョコ停は、「前工程の乱れ」がそのまま後工程に伝播していることが大きく影響しています。つまり、「受け取った側の工程で起きた停止」であっても、その発端は別の工程にあることが少なくありません。
- 前工程で寸法にばらつきがある部品を流したことで、次工程の装置が停止
- 梱包や搬送時の管理が甘く、異物や傷が発生してラインが止まる
これは、品質情報や異常情報が工程間で共有されていないことや、工程間の“つながり”が意識されていない業務設計に起因します。ライン全体を一つの流れとして捉え、各ポイントで不良や問題を発生させない視点が必要です。
前工程での突発的なトラブルのような「意図せぬ変化=変化点」をうまく捉え、管理することで後工程でのチョコ停を未然に防ぐことが可能になります。トヨタ流の変化点管理の秘訣について解説した動画もご用意しておりますので、是非お役立てください。
>>トヨタ流品質管理に学ぶ!トラブルを未然に防ぐ変化点管理のコツをみる(無料公開中)
作業員に関する原因
作業員による操作ミスや判断ミスなどのヒューマンエラーが原因でチョコ停が発生するケースは多くありますが、その背景には単なる「不注意」では済まされない構造的な問題が潜んでいます。現場で起きる多くのヒューマンエラーは、個人の能力や意識の問題ではなく、教育・標準作業・現場設計の曖昧さに起因するものです。
たとえば以下のような状況ではミスが発生しやすくなり、結果としてラインの一時停止(チョコ停)につながります。
- OJTが担当者任せで、教える内容や順序にばらつきがある
- 標準作業手順書(SOP)が形骸化し、現場で活用されていない
- 作業員ごとに手順や段取りが異なり、設備への影響が発生する
- 慣れていない作業員が操作方法を誤り、ラインを止めてしまう
- 忙しさやプレッシャーから確認作業を省略し、ミスが発生する
特に生産に追われている現場では、「多少のミスは仕方ない」「早く復旧させることが優先」といった風土が根づいていることもあり、ヒューマンエラーを引き起こしやすい条件が常態化しています。
このように、「人が原因」とされがちなチョコ停も、実は人がミスしにくい仕組みや環境が整っていないこと自体が問題なのです。
ヒューマンエラーを防止するには、従業員に対する教育だけでなく、教育訓練を行っても一定の確率で発生する「ポカミスへの対策=ポカヨケ」も欠かせません。
ポカミス対策の重要性や取り組みへの考え方、製造現場ですぐに実践できるポカヨケ対策事例をまずは見てみたい!という方は、以下のリンクをクリックし専門家による解説動画をご覧ください。
>>ポカミスゼロへ!ヒューマンエラーを未然予防する「ポカヨケ対策」の進め方をみる(無料公開中)
作業環境に関する原因
作業環境やライン設計そのものにも、チョコ停の引き金となる要因が多く潜んでいます。たとえ作業員や設備が正常でも、現場に“ムリ・ムダ・ムラ(3M)”が放置されていると、チョコ停は繰り返されます。
例として、以下のようなケースが挙げられます。
- 製造ラインのバランスが悪く、一部工程だけに作業負荷が集中している
- 資材補充のタイミングや導線が非効率で、補充が間に合わず停止する
- 作業スペースが狭く、通行や作業のたびに人や物がぶつかる
- 照明が暗く、部品の識別ミスやセンサー誤作動のリスクがある
- 気温や湿度の変化により材料の状態が不安定になり、設備が誤作動する
これらの問題は、日常的な業務の中では「よくあること」として見過ごされやすく、一度発生しても“仕方ない”と処理されてしまう傾向があります。しかし、このような「作業しにくい環境」が蓄積されることで、結果的にチョコ停の頻発を招いているのです。
作業現場における3M(ムリ・ムダ・ムラ)は、課題視されやすいものから潜在的なものまで様々なものが現場に潜んでいます。そのため、まずはどのような3Mが潜んでいるのか?を洗い出すことから始めると良いでしょう。
現場に潜む3Mを可視化する視点やムダ取りの方法について知りたい方は、以下の専門家による詳しい解説もご覧ください。
>>3M(ムリ・ムダ・ムラ)は現場のどこにある?改善~標準化までのステップを学ぶ(無料公開中)
チョコ停への具体的な対策方法5選
チョコ停が頻発すると生産効率に重大な影響を及ぼします。ここではチョコ停を防ぐための具体的な対策方法として、以下の5つを紹介します。
- まずはチョコ停を分析し真因を特定する
- 設備の課題には「定期的な予防保全」
- 材料・部品の課題には「トヨタ生産方式による在庫管理の徹底」
- 作業員の課題には「標準作業の徹底」
- 作業環境の課題には「5S活動による3Mの排除」
まずはチョコ停を分析し真因を特定する
チョコ停を減らすための第一歩は、感覚や思い込みで対策を進めるのではなく、発生状況を正しく記録・分析し、根本原因(真因)を特定することです。目の前の現象に対して場当たり的な対応を続けていても、問題の再発を防ぐことはできません。
たとえば「センサーが誤作動した」と記録されていても、よく調べてみると「清掃されておらず汚れが原因だった」「点検基準が人によって異なっていた」など、本質的な原因は別のところにあることがよくあります。
ここでは、真因の洗い出しに有効な4つの分析手法についてわかりやすく解説します。
なぜなぜ分析
なぜなぜ分析は、表面的な「原因」ではなく、本質的な「真因」まで掘り下げるための思考法です。チョコ停のような繰り返し発生するトラブルには、目に見える要因の奥に根本的な問題が潜んでいることがよくあります。
例として、「センサーが反応せず、チョコ停が発生してしまった」というトラブルの真因について、なぜなぜ分析を行ってみましょう。
ステップ | なぜ?(問いかけ) | 原因の内容(答え) |
---|---|---|
なぜ① | なぜセンサーが反応しなかったのか? | センサーが汚れていて 正しく検知できなかった |
なぜ② | なぜセンサーが汚れていたのか? | センサーの清掃が行われていなかった |
なぜ③ | なぜ清掃が行われていなかったのか? | 清掃手順が作業標準に 記載されていなかった |
なぜ④ | なぜ作業標準に 清掃手順が記載されていなかったのか? | 現場で必要性が認識されておらず、 標準化の見直しが長らく行われていなかった |
なぜ⑤ | なぜ標準化の見直しが 行われていなかったのか? | 標準書の更新が属人化し、 「気づいた人が修正する」体制だった |
このように、「センサーの誤作動」→「清掃されていない」→「標準化の不備」→「保守体制の属人化」と現象の奥にある管理上の課題(真因)までたどることができます。
一方で、なぜなぜ分析は方法を間違えると問題が発生したこと自体に焦点を当て、問題を単にやり過ごすことや、個人を吊るし上げる責任追及/攻撃に逸れてしまう可能性もあります。
そのような事態を避けるべく、真因を正しく導き出すなぜなぜ分析の進め方や例題、すぐに使えるテンプレートがまとまったハンドブックをご用意いたしました。是非お役立てください。
>>なぜなぜ分析の生みの親!「トヨタ流」の分析手法、わかりやすい例題を参照してみる(無料公開中)
ワークサンプリング
ワークサンプリングとは、作業や設備の稼働状況を一定の間隔で観察・記録し、どれだけの時間が実際の作業に使われ、どれだけの時間がムダになっているかを統計的に分析する手法です。製造現場では「稼働分析法」とも呼ばれ、チョコ停の影響を定量的に把握し改善対象を絞り込むのに非常に有効です。
一見わずかな停止に見えるチョコ停も、ワークサンプリングによって「1日あたり何回・何分発生しているか」が明確になり、どの工程・設備でロスが大きいのかが客観的に見える化されます。
▼ワークサンプリング調査の進め方▼
調査対象の選定 | 調査する設備や工程を選定する。 |
調査の実施 | 一定期間にわたり設備の稼働状態を観察し、 稼働・停止の時間を記録する。 |
データの集計 | 収集したデータを集計し、 チョコ停の発生頻度や停止時間を算出する。 |
そして、収集したデータから稼働率を算出することで、改善インパクトの大きさが数値で把握できます。
項目 | 数値 |
---|---|
負荷時間(理論稼働時間) | 24時間 |
実稼働時間 | 22時間 |
チョコ停による停止時間 | (24-22=)2時間 |
稼働率(チョコ停除く) | (22÷24=)約91.67% |
実質稼働率(チョコ停含む) | 22 ÷(24+2)=約84.62% |
このようにワークサンプリングを通じて「どのくらいのロスが発生しているか」「どこに対策を集中すべきか」を把握することで、チョコ停の再発防止に向けた的確な対策の優先順位付けが可能になります。
「たった数分」が積み重なることで、1日単位・月単位でどれほどの損失が出ているかを“見える化”することが、改善の出発点となります。
パレート図
パレート図は、チョコ停の原因を分析し「どこから手をつけるべきか」を判断するための有効な手法です。QC七つ道具のひとつとして知られており、製造現場の課題を「数値の大きい順」に可視化することで、効果的な改善の優先順位づけが可能になります。
たとえば、チョコ停の原因が「センサー誤作動」「材料供給の遅れ」「操作ミス」など複数ある場合でも、発生頻度や影響の大きさにはバラつきがあります。パレート図を使えば、発生件数が多くインパクトの大きい要因を一目で把握できるため、限られたリソースでも効率的な改善活動が行えます。
▼パレート図の例▼
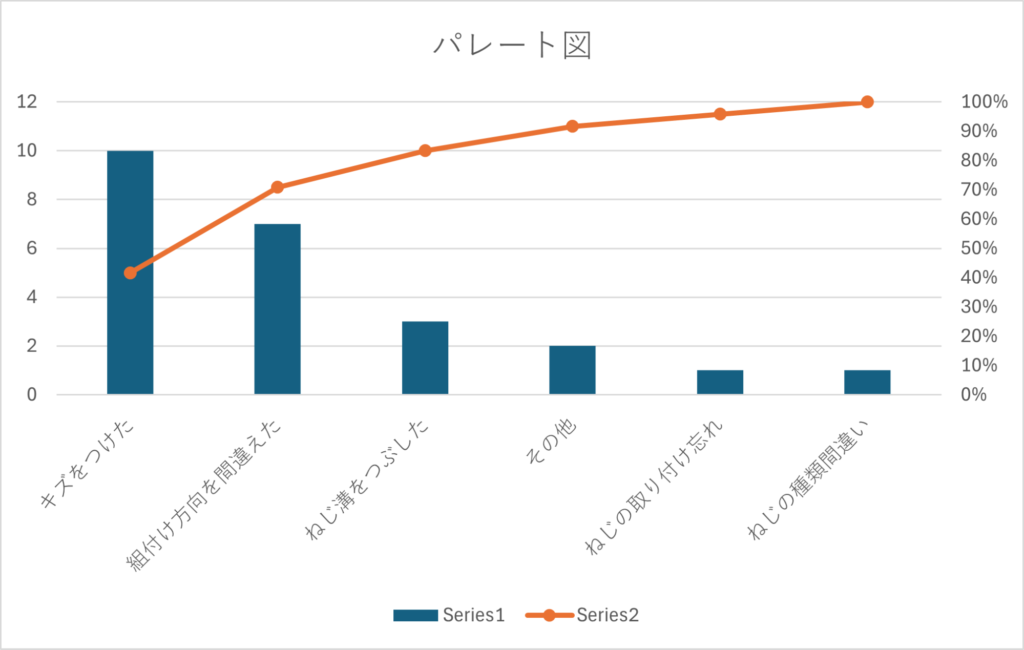
パレート図はQC7つ道具の1つとして、製造現場の改善活動で広く活用されています。具体的な使い方は以下の記事で詳しく解説していますので、併せてご覧ください。
関連記事:品質問題を可視化するQC7つ道具の使い方【事例や覚え方、テンプレートを紹介】
4M分析
4M分析は、問題の原因を「人・設備・材料・方法」の4つの視点から分類し、抜け漏れなく洗い出すフレームワークです。製造業における不具合分析の基本であり、チョコ停のように原因が多岐にわたるトラブルにも有効です。
たとえば、あるチョコ停の原因を4Mに分類すると以下のようになります。
視点 | 例 |
---|---|
Man(人) | 操作手順の誤り、確認漏れ、作業員のスキル差 |
Machine(設備) | センサー故障、摩耗部品の劣化、清掃不足による動作不良 |
Material(材料) | 部品の寸法バラつき、異物混入、不良品の混入 |
Method(方法) | 作業標準が不明確、工程設計の不備、 保全ルールが徹底されていない |
4M分析の強みは、「どのカテゴリーに原因が集中しているか」が明確になる点です。
たとえばMachine(設備)に偏りがあるなら、予防保全体制を見直す必要がありますし、Man(人)に集中していれば、教育や標準作業の再整備が優先課題となります。
4M分析にはチョコ停の真因特定だけでなく、歩留まりロスの発見といったメリットもあります。4M分析の進め方について動画でわかりやすく学んでみたい方は、是非以下のリンクをクリックしご覧ください。
>>4M分析の実践例!4Mの視点からアプローチした改善事例や、作業不順守改訂のコツをみる(無料公開中)
設備の課題には「定期的な予防保全」
機械や設備のメンテナンス不足は、チョコ停の主な原因の1つです。特に多く見られるのが、予防保全が十分に行われていないことによる突発的な停止です。事後保全にみられる「止まってから対応する」受け身の姿勢から脱却できず、「停止=気づく」という状態を改善できない限り、チョコ停は何度でも繰り返されます。
本来の予防保全とは、異常が起こる前に問題の兆候を捉え、トラブルの芽を摘んでおく活動です。「気づける」点検体制と、「気づいたときに対応できる」仕組みづくりがセットで求められます。
さらに重要なのが、保全業務の属人化を防ぐこと=保全業務のノウハウを「形式知化」することです。特定のベテランだけが対応できる状況では、休暇や異動、退職などで対応力が一気に低下するリスクをはらんでいます。
予防保全を仕組みとして根づかせるには、点検内容や頻度を明文化することに加え、誰が実施しても同じ品質で対応できるように標準化・マニュアル化を進めることが不可欠です。
予防保全のサイクル確立に向け、設備の傾向管理を「かんたん」にするノウハウをまとめた以下のハンドブックを是非ご参照ください。
>>チョコ停による生産性低下を解消する「予防保全」の実現策とは?(無料ハンドブック配布中)
材料・部品の課題には「トヨタ生産方式による在庫管理の徹底」
材料や部品が原因で発生するチョコ停には、「前工程で起きた乱れ」がそのまま次工程に持ち込まれているという構造的な課題があります。このような問題は、工程間で品質情報や異常の共有ができていないこと、そもそも「つながり」を意識した業務設計になっていないことが根本にあります。
ここで有効なのが、トヨタ生産方式(TPS)における在庫管理の考え方です。TPSでは「後工程引き取り方式」により、必要なものを必要なときに必要な量だけ供給する仕組みを重視しており、これにより過剰在庫や不良品の流出を抑えられます。
また、異常があればすぐに止めて対応する「アンドン」や「自働化」の思想を取り入れることで、チョコ停の原因となる“変化点”に即座に気づき、止める・知らせる・直すという流れが可能になります。
つまり、工程間の在庫を「情報のフィルター」として機能させ、異常を検知しやすくすることがチョコ停の未然防止につながるのです。在庫の量や品質を適切に管理し、「どの工程で、どんな異常が起きているのか」を見える化できれば、ラインの流れがスムーズになり、チョコ停の発生頻度は大きく下げられます。
トヨタ生産方式をもとにした作業改善/工程改善の着眼点についてより詳しく知りたい方は、以下のリンクをクリックし専門家による解説動画をご覧ください。
>>トヨタの改善哲学!前工程のトラブルを下流に流さない仕組みづくりについて知る(無料公開中)
作業員の課題には「標準作業の徹底」
作業員の操作ミスや判断ミスによってチョコ停が発生するケースは少なくありません。しかし、こうしたヒューマンエラーの背景には「人の不注意」では片付けられない教育や作業手順、環境面の“標準化不足”が潜んでいます。
このような現場では、作業者の能力や注意力に依存する運用が常態化しており、「誰でも、いつでも、同じ手順で、安定した結果が出せる」という状態にはなっていません。
チョコ停のような短時間停止を減らすには、作業を“人に依存させない”仕組みづくり=標準作業の徹底が不可欠です。作業のばらつきや曖昧さを取り除き、誰が行っても同じ品質・スピードで作業ができるようにすることでミスの発生を抑え、再発防止にもつながります。
標準作業を徹底させるには、マニュアルの整備などに加え「作業標準の見直し」も欠かせません。安定した稼働のために何を統一すべきか?ということを定期的に確認し共通認識を持つことで、標準作業を単なる「手順の押しつけ」にしないようにしましょう。
標準作業を見直す適正なタイミングや現場に浸透させる方法については、以下の詳細なハンドブックを是非ご参照ください。
>>トヨタ流に学ぶ!作業標準の見直しで実現する製造現場の生産性向上(無料配布中)
作業環境の課題には「5S活動による3Mの排除」
作業環境の乱れは、チョコ停を誘発する“目に見えにくい”原因のひとつです。ムリ・ムダ・ムラ(3M)が放置されたままの現場では、作業負荷の偏りや動線の非効率、ヒューマンエラーの発生リスクが高まり、設備や作業員に問題がなくてもチョコ停が頻発する状態に陥ってしまいます。
こうした「環境起因のチョコ停」を防ぐうえで有効なのが、現場を整えるための基本である5S活動(整理・整頓・清掃・清潔・しつけ)です。
5Sは単なる片付けではなく、現場に潜む3Mを可視化し、継続的に排除していくための“仕組み”です。たとえば、以下のような効果が期待できます。
ムリの排除 | 整理整頓により重たい物の持ち運びや不自然な姿勢作業が減り、 作業者への負担が軽減される |
ムダの削減 | 導線を見直し、資材や工具の“探す時間”や“取りに行く手間”をなくす |
ムラの是正 | 表示や区画の整備により作業の順番や配置が統一され、 作業ばらつきを防止 |
3Mは一度取り除いても、時間とともに再び現場に忍び込んでくるため、日常的な5Sの実践が欠かせません。チョコ停を引き起こす温床を排除するには、「見た目を整える」だけで終わらない、現場の3Mに目を向けた5S活動を組織全体で継続することが重要です。
そこでカギを握るのが、「しつけ=ルールを守る習慣づけ」です。どれだけ整理整頓や表示のルールを定めても、守る意識が現場に根づいていなければ5Sは一時的な活動にとどまり、すぐに元通りになってしまいます。
現場に5S活動を浸透させるコツや「しつけ」の実践方法については、以下の専門家による解説動画をご確認ください。
>>正しい運用に欠かせない「重要なS」とは?具体的な実践方法をみてみる(無料公開中)
ここまで、チョコ停を防ぐ具体的な対策方法についてご紹介しました。一方で、「似たことはすでに実践しているが、依然としてチョコ停が減らない…」とお悩みではないでしょうか?
次章では、チョコ停の根本にアプローチするポイントや、現場改善に役立つツールについてご紹介します。
チョコ停の再発防止には「放置・見逃し」対策から!
チョコ停は生産性の低下を招く要因です。多くの現場で先述したような対策を講じているものの、依然としてチョコ停の発生を完全には防げていません。
ここではチョコ停が減らない根本的な理由と、チョコ停を発生させない仕組み作りについて探ります。
チョコ停が減らない根本的な理由とは?
私たち現場改善ラボが製造業の方76名を対象に行った調査では、「チョコ停がどれくらいの頻度で発生していますか?」という質問に対し、以下のような回答が得られました。
毎日 | 49% |
数日に一回 | 24% |
数週間に一回 | 15% |
数カ月に一回 | 5% |
ほとんど発生しない | 7% |
約半数の方が「毎日チョコ停が発生している」と回答されており、チョコ停の発生頻度の高さが伺えます。さらに、「チョコ停の発生が生産性の低下を招いていると思いますか?」という質問に対しては、93%の方が「はい」と回答しています。
では、なぜチョコ停は頻繁に発生してしまうのでしょうか?そこには、以下のような原因が潜んでいます。
原因 | 詳細 | 例 |
---|---|---|
微細な異常が 見過ごされる | 停止時間が短く「すぐ直るから大丈夫」と軽視され、記録も対策もされず再発する | 「5分くらいの停止だし、記録まではしなくていいかなと思って放置してしまった」 |
属人的な判断に 依存している | 作業者ごとに報告基準がバラバラで、ベテランでないと異常に気づけず、対応のばらつきが生じる | 「前は●●さんなら止めずに続けていたけど、自分は止めていいのかわからなかった」 |
正確なデータが 蓄積されない | チョコ停が記録されないため、発生傾向や頻度が可視化されず、改善が後手に回る | 「毎日ちょこちょこ止まっているけど、報告しても仕方ないと思って記録していない」 |
表面化しにくい 環境要因 | センサー精度の低下や材料のわずかなバラつきを目視で発見できず、チョコ停が常態化しやすい | 「最近ちょっとずつ止まるけど、何が原因かもよく分からずにいつの間にか慣れてしまっている」 |
では、このような状況を防ぐには何が必要なのでしょうか?
放置・見逃し対策には「標準化」と「記録の可視化」
チョコ停の発生を根本から減らすには、発生頻度の低減(未然防止)と、遅延の最小化(速やかな復旧)から対策を講じる必要があります。
そのためには、「誰でも同じ作業ができる状態」=標準化と、「原因・対策をすぐに確認できる状態」=記録の可視化が欠かせません。
しかし、実際の現場では以下のような課題が障壁になっています。
項目分類 | 主な課題 | よくある課題例 |
---|---|---|
標準化 | 作業手順の整備が大変 | 手順書の作成・更新に工数がかかり、 現場変化に追従できていない。 |
手順書の伝達力に限界がある | 複雑な作業内容は文書だけで 正確に伝えるのが難しく、紙では検索性も低い。 | |
教育の徹底が困難 | 指導にかける時間や人材が不足し、 標準作業が浸透しにくい。 | |
OJTにばらつきがある | 教え方が属人化し、 作業品質や理解度に差が生まれやすい。 | |
記録の 可視化 | 記録作業が負担になりやすい | 作業中に記録する余裕がなく、 手書きではミスや記録漏れが発生しやすい。 |
記録の質にばらつきがある | 担当者ごとに記録の粒度や内容が異なり、 正確なデータが蓄積されない。 | |
データ分析のリソース不足 | 原因分析や改善策立案に必要な スキル・時間が現場に不足している。 |
これらの課題を解消するには、動画やデジタルツールを活用した標準化・記録の仕組み化が有効です。形式だけの5Sや手順書に頼らず、「現場で活用される」状態にどう落とし込むかが、チョコ停対策の鍵となります。
次章では、現場の標準化と記録の可視化をサポートする2つの「tebiki」についてご紹介します。
【事例も紹介】現場の標準化と記録の可視化を促進する2つのツール
現場改善を進めるためには、作業の標準化と記録の可視化が欠かせません。この2つの要素を効果的に実現するためのツールに、「動画マニュアルtebiki」と「デジタル帳票tebiki現場分析」があります。
以下に、2つのツールのメリットや実際の活用例などを解説します。
現場の標準化には「動画マニュアルtebiki」
「動画マニュアルtebiki」は、動画マニュアルの作成から従業員の習熟度管理まで行えるクラウド型ツールです。
従来の紙のマニュアルやテキストベースの指示書では伝えきれない細かな動作やニュアンスを、視覚的に分かりやすく伝えることで現場の標準化を促進します。
▼動画マニュアル作成ツール「tebiki」紹介動画▼
また、動画マニュアルの作成をサポートする豊富な機能が搭載されているのも大きな特徴です。
- 動画の字幕などの自動翻訳
- オフライン再生
- 文書作成機能
- 動画の音声を認識して字幕の自動生成
- タスク機能により自主学習を促す
- レポート機能
- テスト機能
実際に、tebikiを導入した新日本工機株式会社では、動画マニュアルにより作業の標準化が進みました。従来の紙のマニュアルでは情報の更新や共有が困難でしたが、動画マニュアルを導入することで作業手順の共有が迅速かつ確実に行えるようになりました。その結果、作業ミスが減少して作業品質が安定し、生産性が向上しています。
本記事でご紹介した動画マニュアルtebikiの機能や導入サポート体制、プランなどを詳しく知りたい方は、こちらの資料をご覧ください。
>>「かんたん動画マニュアル・tebikiサービス説明資料(pdf)」を見てみる
記録の可視化には「tebiki現場分析」
データの「リアルタイム収集・一元管理・効果検証」を簡単に行えるツールとしておすすめなのが、かんたんデジタル帳票「tebiki現場分析」です。
tebiki現場分析を活用すれば工程データをかんたん・効率的に管理できるため、情報が部署や担当者ごとに散在することがなくなり、迅速な原因特定が可能となります。
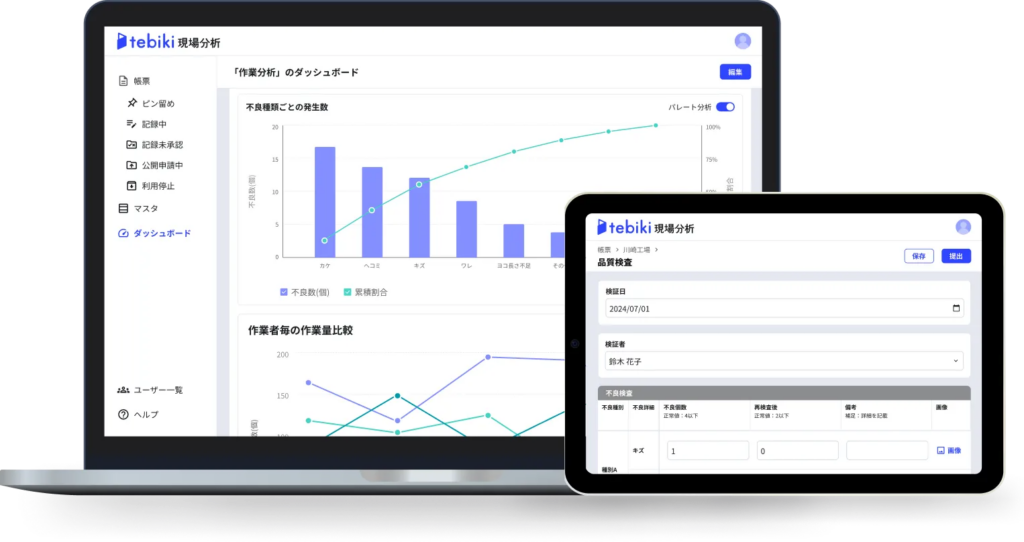
画像による記録にも対応しており、現場での記録作業もスムーズに行える点が特長です。また、収集したデータは自動で集計され、パレート図などへの展開もその場で行えるため、データの可視化や分析が非常にスピーディーです。
定量データと定性データの両方を、ひとつのシステム上でシームレスに収集・分析できるため、Excelでの手作業や複雑なデータ処理にかかる負担を大幅に削減することができます。実際に、株式会社日本電気化学工業所ではtebiki現場分析の導入によりデータの蓄積と分析が容易になり、長期的な品質改善計画の立案が可能になったと報告されています。
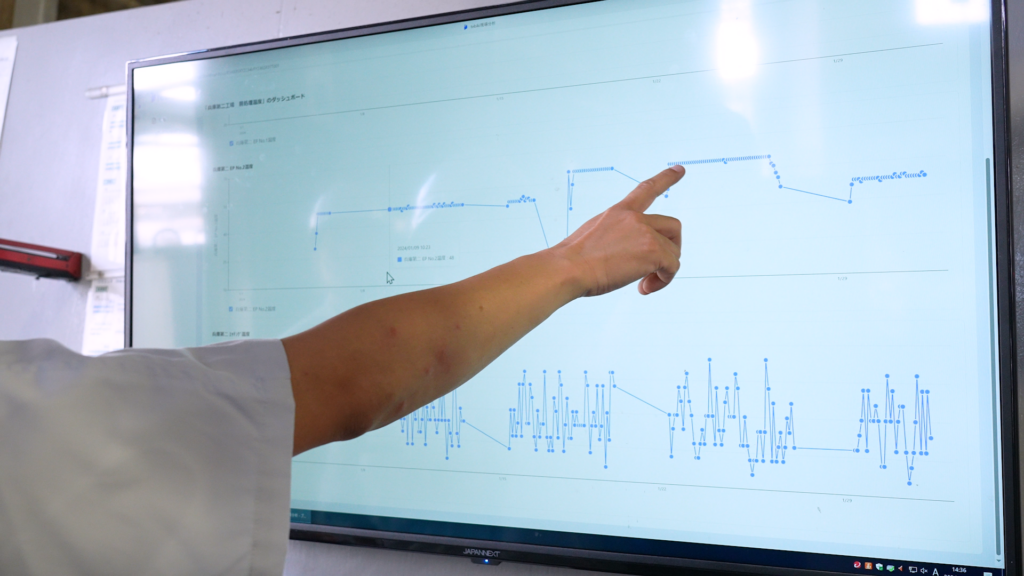
同社では現場帳票をデジタル化し、管理図をもとに設備の温度データをリアルタイムで検知しています。通常の温度パターンとは異なるデータに気づき、設備の配管に穴が開いていたというアクシデントを迅速に発見できたという事例もありました。
さらに、tebiki現場分析は対策実施後の効果検証も効率的に行えるのも大きな魅力です。
電子帳票上で不良率の推移などを継続的にモニタリングできるため、改善の効果をリアルタイムで把握し、必要に応じた追加の対策もすぐに検討できます。このように、データの蓄積から可視化、分析、効果検証までを一貫してサポートすることで、現場の改善活動を加速させる強力なツールとなっています。
tebiki現場分析の機能詳細や導入イメージ、改善事例の詳細について知りたい方は、以下のリンクをクリックし詳細な資料をご覧ください。
>>「tebiki現場分析サービス説明資料(pdf)」を見てみる
チョコ停を見逃さない・放置しない現場づくりで効果的な未然防止を【まとめ】
チョコ停は短時間で復旧できる軽微な停止として軽視されがちですが、頻発すれば生産性・品質・安全・納期といった多方面に深刻な影響を及ぼします。ドカ停の前兆にもなり得るため、見逃してはなりません。
現場ではまず、チョコ停の発生状況を記録し可視化することが第一歩です。そして原因を正しく分析した上で、誰が対応しても同じ品質で作業できるよう標準化することが、根本的な再発防止につながります。
小さなロスの蓄積こそ、現場改善の出発点。チョコ停を「見える化」し、「対策を定着させる仕組み」を持つことが、生産性向上の鍵となります。
本記事でご紹介した、現場の標準化と記録の可視化を促進するかんたんデジタル帳票「tebiki現場分析」について詳しく知りたい方は、以下の画像をクリックし詳細な資料をご覧ください。