かんたん動画マニュアル作成ツール「tebiki」を展開する現場改善ラボ編集部です。
現場で対策したり気を付けていても「ヒューマンエラーがなくならない…」と思った経験はございませんか?本記事では、ヒューマンエラーの発生確率やその根本的な原因、ヒューマンエラーを防ぐうえで有効な対策や手法について紹介します。
本記事の他、以下の専門家による解説動画でも「効果のあるヒューマンエラーへの再発防止策」について詳しくご紹介しています。繰り返す品質不良や安全トラブルを課題視している方は是非ご覧ください。
目次
ヒューマンエラーが発生する確率は?
ヒューマンエラーとは、人間が意図しない行動や判断ミスを行うことで発生するトラブルを指します。ミスは日常業務から製造工程、医療現場など、あらゆる場面で避けられないものです。
ここでは、ヒューマンエラーの発生頻度や重大事故に至る確率といった観点から解説します。
- ヒューマンエラーが発生する確率は「0.3%」
- ヒューマンエラーが重大な事故に発展する確率は?
ヒューマンエラーの確率は「0.3%」
ヒューマンエラーの発生確率は多くの専門家によって研究されており、その中でも高崎ものづくり技術研究所の代表である濱田金男氏が提唱している「1000回に3回=0.3%」という確率が有名です。
濱田氏の考えによれば、どれだけ注意深く作業を行っていても、1000回の作業や行動のうち3回はミスが発生するとされています。さらに、この3回のミスのうち実際に気づかれずに流出してしまう「見落としミス」も「1000回に3回=0.3%」の確率で発生するとされています。
つまり、現場でヒューマンエラーが発生する確率が0.3%であることに加え、どれだけ対策をしていてもヒューマンエラーを見逃してしまう確率は「0.3%×0.3%=100万回に9回」であり、ヒューマンエラーの対策の限界が予想できます。
現場改善ラボでは、濱田金男氏による「ヒューマンエラーを未然予防する対策」の講演動画をご用意しております。本記事と併せ是非ご覧ください。
>>>ヒューマンエラーによる作業ミスを撲滅する「仕組み作り」とは?(視聴無料)
ヒューマンエラーが重大な事故に発展する確率は?
ヒューマンエラーが発生する確率だけではなく、重大な事故に発展する可能性についても考える必要があります。アメリカの損害保険会社の安全技師であったハインリッヒが提唱した「1:29:300の法則」は、この点について非常に示唆に富んでいます。
ハインリッヒの法則では、330件の災害のうち1件が重大事故であり、その背後には29件の軽微な事故、さらにその背景には300件のヒヤリハット(傷害や物損が発生していないが、潜在的に危険な状態)があることが示されています。このことから、ヒューマンエラーが軽微なミスであっても、それが積み重なれば重大事故に至る可能性が高いことがわかります。
特に「1:29:300」の法則が示唆しているのは、重大な事故を防ぐためには、軽微な事故や無傷害事故の段階でエラーを発見し、対策を講じることが重要だという点です。約0.3%という割合でヒューマンエラーが重大な事故に発展するリスクがあることを考えると、日常的なエラーやヒヤリハットの報告や対応の徹底が、重大な事故防止に必要となります。日常的なミスを軽視せず、ヒューマンエラーの発生を根本から減らす取り組みが必要です。
ヒューマンエラーの確率は「ゼロ」にできる?
ヒューマンエラーを完全に防ぐことは、多くの専門家が指摘するように限りなく難しいといえます。人間は複雑な判断や操作を日々行っており、その中には予期せぬ状況や疲労、注意散漫などが関わるため、ヒューマンエラーが発生するということです。そのため、エラーを前提にシステムやプロセスを改善し、エラーが発生した際に大きな影響を与えない仕組み作りが重要です。
ヒューマンエラーを「ゼロ」にすることは不可能
「ヒューマンエラーをなくすことは可能か?」という問いに対して、答えは明確に「不可能」です。これは、正常で明晰な状態にあり、積極的に活動している人であってもエラーが発生するためです。
人間の注意力や集中力は、一定の時間が経つと低下し、ミスが発生するリスクが高まります。例えば、過度な緊張状態や疲労感、逆にリラックスしすぎた状態では、意識が散漫となりエラーが発生しやすくなります。以下の表は、意識のモードとエラー発生率の関係を示しています。
フェーズ | 意識モード | 生理的状況 | エラー発生率 |
---|---|---|---|
フェーズ0 | 無意識・失神 | 睡眠 | 1.0 |
フェーズ1 | 意識ぼけ | 疲労・居眠り | 0.1以上 |
フェーズ2 | 正常・リラックスした状態 | 休息時、定例作業時 | 0.01~0.00001 |
フェーズ3 | 正常・明晰な状態 | 積極的な活動時 | 0.000001以下 |
フェーズ4 | 興奮状態 | 慌てている時、パニック時 | 0.1以上 |
「正常・明晰で積極的に活動している状態(フェーズ3)」では、エラー発生率が非常に低くなりますが、ゼロにはなりません。どれだけ集中して作業を行っても、わずかな判断ミスや認識のズレが生じる可能性が残っているからです。特に人間は多くの情報を処理し続ける中で、見落としや誤解が発生することがあります。
一方で、ヒューマンエラーが発生しやすいのは、疲労や居眠りなどによって意識がぼんやりしている「フェーズ1」、慌てたりパニックになったりしている「フェーズ4」の時です。「フェーズ1」と「フェーズ4」の状態では判断力や集中力が低下し、ミスの確率が一気に上がるため、特に注意が必要です。
参考元:中條 武志著「人間信頼性工学:エラー防止への工学的アプローチ」
ヒューマンエラーが防げない原因は?3つの「誤解」
ヒューマンエラーを完全に防ぐことは難しく、多くの人が「誤解」している原因がいくつか存在します。誤解は、現場でのエラー対策がうまくいかない理由にもつながっています。以下では、ヒューマンエラーが防げない主な3つの誤解について説明し、それらが現場でどのように影響しているのかを見ていきます。
注意力によって防げる
1つ目の誤解は「ヒューマンエラーは注意力を高めることで防げる」というものです。確かに、注意力を高めればエラーの発生率は低下しますが、それでも完全に防ぐことはできません。先述の表を参考にすると、人間の意識状態は常に変動し、最も集中した「正常・明晰な状態(フェーズⅢ)」であっても、エラーが発生する可能性は0にはなりません。理想的な状態でのエラー発生率は0.000001以下ですが、この状態を維持できる時間は短く、すぐにリラックスしたフェーズⅡや過度な緊張状態であるフェーズⅣに移行します。
人間は一時的に高い集中力を発揮できても、長時間その状態を保つことは生理的に不可能です。たとえば外科手術のような高度な集中力が求められる場面では、術者が一時的に高い集中力を維持できますが、長時間の作業や複雑な手術においてはミスのリスクが増加します。そのため「最高の状態であればエラーは防げる」という考えは、現実には適用しにくいものとなります。注意力に頼りすぎず、システムや作業工程を見直すことが重要です。
教育・訓練・動機付けによって防げる
2つ目の誤解は「ヒューマンエラーは教育・訓練・動機付けによって防げる」というものです。
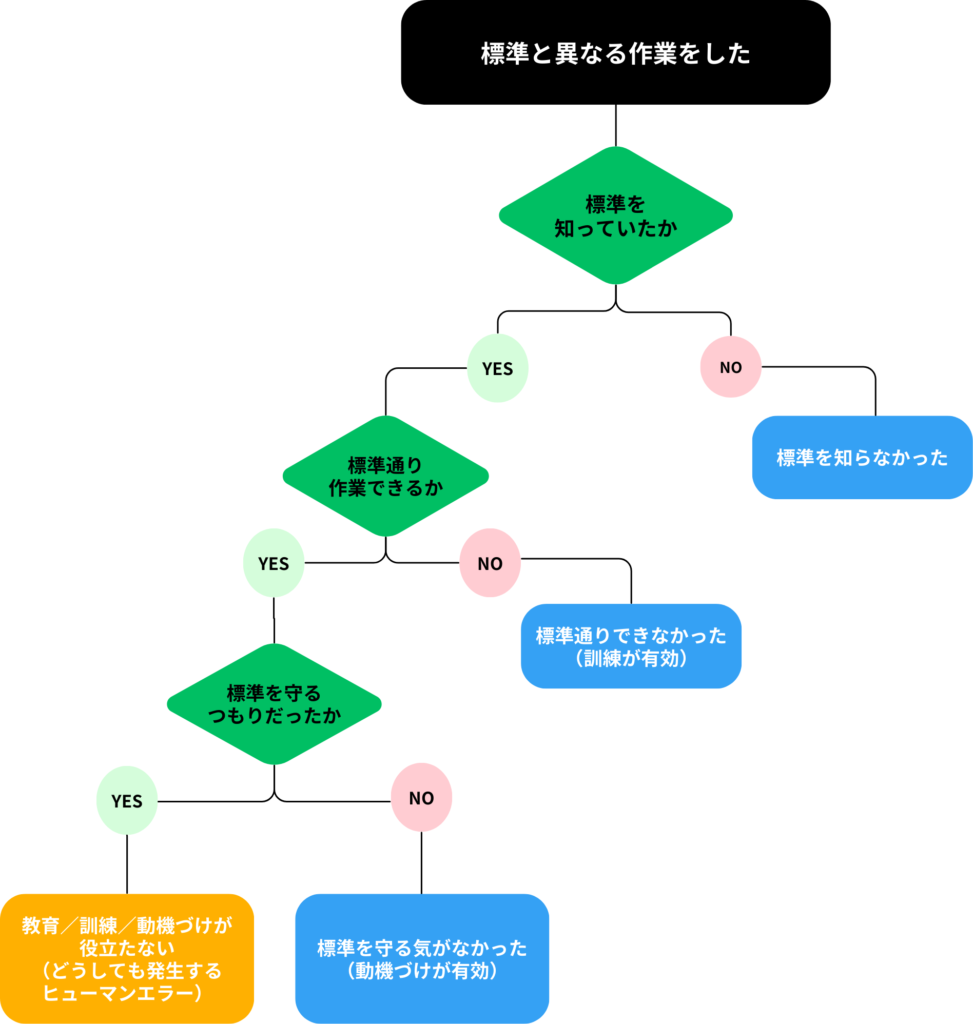
この考え方には一定の効果があるものの、すべてのエラーを防ぐことはできません。たとえ十分に教育や訓練を受け、標準作業手順を理解している従業員であっても、人間の意識は常に変動するため、熟練者でもエラーを犯すことがあります。例えば、医療現場で経験豊富な看護師や医師が、疲労やストレスにより標準手順を守らず、誤って患者に違う薬を投与してしまうケースがあります。これは、人間の限界からくるエラーで、避けることが難しいものです。
一方で、「標準作業を知らない」「正しく実行できない」「標準作業を守る意識が低い」という理由で発生するエラーには、教育・訓練、動機付けは効果的です。新しい機器の操作方法や標準手順をきちんと教えることで、こうしたエラーは減少します。また、適切な動機付けを行うことで、従業員が標準作業を遵守しやすくなり、エラーのリスクが低減されます。しかし、標準を守るだけではエラーを完全に防ぐことはできず、システム全体の改善やプロセスの見直しが必要です。
人による確認・チェックで防げる
3つ目の誤解は「ヒューマンエラーは人による確認・チェックで防げる」というものです。人間が作業ミスをチェックすることで、エラーを未然に防ごうとするのはよく行われる手法ですが、この方法も限界があります。確認・チェックの多重化によってエラーを防ぐという考えは、一見効果的に思えますが、実際にはチェックが増えるごとに「他の人が確認しているから大丈夫だろう」という油断が生まれ、全体の検出力が下がるという逆効果が生じます。
たとえば製造業における品質管理で、複数の作業者が同じ工程を確認しても、ミスが見逃されることがあります。これは、一人一人の確認者が自分の責任を他の確認者に転嫁し、結果としてミスが見逃されやすくなるためです。さらに長時間にわたる確認作業は集中力を必要とするため、次第にエラーの見逃しが増える可能性もあります。このように、単に人によるチェックを多重化するだけでは、根本的な解決にはなりません。
なぜヒューマンエラーが発生する?
ヒューマンエラーが発生する理由は多岐にわたります。人間は完璧ではなく、意識の集中や注意力が一時的に低下することがあり、エラーの原因となることもあります。また経験不足や慣れからくる油断、コミュニケーション不足など、さまざまな要因がエラーを引き起こします。厚生労働省が示す12の分類を通じて、どのような状況がミスを引き起こすのかを理解することで、効果的なエラー防止策を講じることが可能です。
ヒューマンエラーの発生原因12分類
ヒューマンエラーの発生要因は大きく12の分類に分けられ、それぞれが特有の条件や状況下で発生します。以下に、ヒューマンエラーの12分類について、ミスの内容・原因・例・発生しやすい環境を含んだ表を作成しましたのでぜひ参考にしてみてください。
ミスの内容 | ミスの例 | 発生しやすい環境 |
---|---|---|
不注意 | 作業手順を確認せず誤った部品を取り付けてしまう | 単調な作業や長時間労働で集中力が低下しているとき |
錯覚 | 記憶違いで部品の位置を誤り、間違った場所に設置する | 慣れた作業で細部を確認せず進めてしまうとき |
無知・未経験・不慣れ | 新しい機械を誤操作してラインを止めてしまう | 新人や新しい業務に取り組む際に発生しやすい |
危険軽視・慣れ | 長年の経験で保護具を使用せず作業し、事故を起こす | 熟練者やベテランが「慣れ」から作業を簡略化する場面 |
疲労 | 長時間の作業で集中力が切れ、間違った操作をする | 長時間労働や過度な疲労が溜まっているとき |
近道・省略行動 | 安全帯をつけずに高所作業を行い事故を起こす | 納期に追われ、手順を省略しようとする場合 |
場面行動本能 | 落下物を本能的に手で受け止めて怪我をする | 突然の事態に遭遇し、冷静な判断ができないとき |
高齢者の心身機能低下 | 高齢作業者が重い荷物を持とうとして筋力不足で怪我をする | 高齢者が若い作業者と同じような負荷をかけられたとき |
パニック | 故障時に焦って修理を試み、さらに故障を悪化させる | 機械の異常など、通常と異なる状況に直面したとき |
単調作業による意識低下 | 食品工場で袋詰め作業中、量を間違えて詰めてしまう | 単純作業を長時間続けているとき |
連絡不足 | 材料変更の情報が伝わらず、誤った作業手順を行う | 組織内でのコミュニケーションが不足しているとき |
集団欠陥 | 工場全体で目視検査のみ行い、精密検査を怠る | ピリピリした環境で「仕方ない」と集団で間違いを放置する |
現場改善ラボではヒューマンエラーの原因や具体例、対策を紹介した記事を用意していますので、ぜひ下記のリンクからチェックしてみてください。
関連記事:ヒューマンエラーとは?対策11選!原因12分類と具体的な事例も解説
ヒューマンエラーが多いと感じたら?有効な5つの対策
ヒューマンエラーは、無意識に発生するミスが多く、完全にゼロにすることは難しいですが、対策を講じることで大幅に削減することが可能です。ここでは、ヒューマンエラーを防ぐための以下の5つの有効な対策を紹介します。
ポカヨケを行う
ポカヨケとは、「人間はミスをするもの」という前提にもとづいて、ミスが起こっても重大な問題にならないような仕組みを導入することを指します。
具体的には、作業工程での誤操作を防ぐための仕組みを設けたり、間違いが起こりやすいポイントを自動化するなどが有効です。たとえば部品の逆付けを防止するための形状変更や、異なるサイズの部品が同じ場所に取り付けられないような設計を行うといった対策が挙げられます。
現場改善ラボではポカヨケについて詳しく解説した記事を用意しましたので、ぜひチェックしてみてください。
関連記事:ポカヨケとは?ポカミスの原因は?製造業の対策手法や事例を解説
フールプルーフの導入
フールプルーフとは、操作ミスや不注意によるエラーを未然に防ぐ仕組みです。ポカヨケと似ていますが、より「ミスをしても安全に戻れる」設計を目指します。
たとえば電動工具のスイッチを押さないと作動しないようにすることや、車のドアが開いている状態ではエンジンがかからないようにすることなどがフールプルーフの例です。フールプルーフは、作業者がどんなに慣れていてもミスを防ぐことができるため、安全性を確保しやすいです。
現場改善ラボでは、フールプルーフについて具体的に解説した記事を用意しましたので、ぜひこの機会にチェックしてみてください。
関連記事:フェイルセーフとは?フールプルーフとの違い、安全性を確保するための考え方を解説!
5S活動を定着させる
5S活動は、整理・整頓・清掃・清潔・躾(しつけ)の5つの要素を徹底することで、作業環境を整え、ミスや事故を防ぐための活動です。5S活動を徹底することで、職場の作業環境が整い、作業ミスや見落としが発生する可能性が減ります。
特に、工具や部品の整理整頓がしっかりと行われていると、誤った道具を使用することがなくなり、無駄な動きも減らせます。結果的に効率の向上とともにエラーも削減されます。
ヒヤリハットを共有する
ヒヤリハットとは、事故には至らなかったものの、危険を感じた瞬間や出来事を指します。ヒヤリハットを共有することで、同様の状況が再発しないよう、対策を講じることが可能です。
職場全体でヒヤリハットを共有する文化を作ることは、ヒューマンエラーの未然防止に役立ちます。また、他者の体験を共有することで、誰もが潜在的なリスクを意識するようになり、日常の業務において注意力が向上します。
危険予知トレーニング(KYT)を定期的に実施する
KYTは、危険な状況を事前に予測し、対策を考えるためのトレーニングです。作業現場で発生しうる危険をチームで話し合い、そのリスクを洗い出していきます。
特にヒューマンエラーが発生しやすい業務や工程において、この訓練を定期的に行うことで、潜在的なリスクを認識しやすくなり、日常業務でも注意を払う習慣がつきます。結果として、事故やミスの発生を予防する効果が期待されます。
初めて/変更/久しぶり(3H)に該当する作業前にマニュアルを確認する
3Hとは「初めて」「変更」「久しぶり」の頭文字を取ったものです。このような条件に該当する作業は、ヒューマンエラーが発生しやすいとされています。
特に新しい作業や長期間行っていなかった作業に関しては、事前にマニュアルを確認することで、作業手順のミスを防ぐことができます。定期的な見直しや研修を行い、全ての作業者が正しい手順を理解しているかを確認することが重要です。
ヒューマンエラー対策には「教育から」
ヒューマンエラー対策を5つ紹介しましたが、そのうち下記の4つは「教育」に関係する対策です。つまり、『教育を徹底させること』が、ヒューマンエラー対策の大きなカギであることがわかります。
- 5S活動を定着させる
- ヒヤリハットを共有する
- 危険予知トレーニング(KYT)を定期的に実施する
- 初めて/変更/久しぶり(3H)に該当する作業前にマニュアルを確認する
既に、ヒューマンエラー対策の一環で人材育成を行っている職場は多いと思いますが、教育の負担が多くかかる一方で『なかなかミスなどのヒューマンエラーが減らない…』という場合も少なくないでしょう。
そのような方に向け、次章ではヒューマンエラー対策に有効なツールである「動画マニュアル」をご紹介します。
ヒューマンエラーを削減する教育手法は「動画マニュアル」が有効
「教育」によってヒューマンエラーを削減している事例を通じ、動画マニュアルという手法を初めて知った方に向けて、ここからは動画マニュアルの有効性について詳しくご紹介します。
後ほど詳細をご紹介しますが、ヒューマンエラー対策を目的とした教育に動画マニュアルを活用することで、理解度向上につながるだけでなく、教育工数や負担の効率化も期待できます。
文章マニュアルよりも直観的に理解できる
文章で「これをこうして~」と伝えるよりも、動画で見せた方が直観的に理解しやすいです。
特に作業手順のような動作を伝える場合、コツやポイント、NG例を文章で伝えることは難しいでしょう。動画マニュアルを活用することで、正しい手順に加えてNG例も盛り込むことで理解度向上につながります。
▼動画マニュアルのサンプル(音量にご注意ください)▼
(【業界別26社】動画マニュアルの事例とサンプルを多数ご紹介!より抜粋)
作業内容やコツ、ポイントを動画マニュアルで伝えることで、動作を視覚的にわかりやすく理解することができます。作業の危険性などを盛り込んだ内容にすることで、ヒューマンエラーの未然防止にもつながります。
解釈の違い・齟齬が生まれにくい
動画マニュアルでは、見る人ごとによる解釈の違いや齟齬が生まれにくいです。
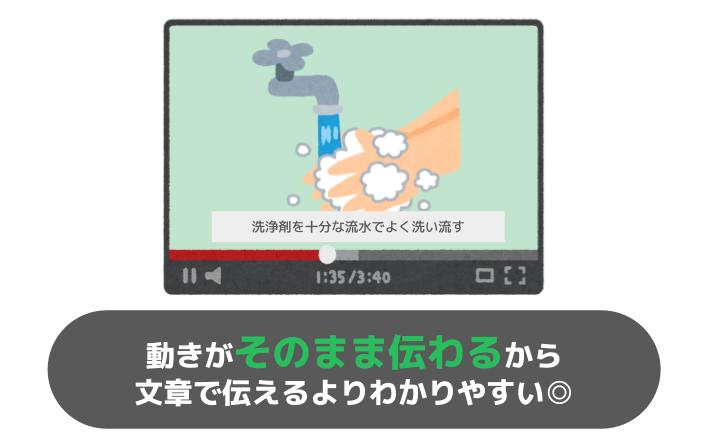
文章だと解釈が読み手の読解力に依存するため、マニュアルの意図通りに解釈されないケースが発生します。ですが、動画マニュアルだと視聴者の理解力に依存しないので、均一な解釈になりやすいです。
例として、解釈の違いによって異なる手順で作業を行ってしまった結果、ヒューマンエラーが発生し品質不良を起こしてしまうといったケースの場合、動画マニュアルで「標準」を伝えることで対策が期待できます。
実際に動画マニュアルの活用によって、品質不良を削減したケースもあります。詳しくは以下のインタビュー記事をご覧ください。
インタビュー記事:動画マニュアルの活用で教育の効率化、不良数の削減、学習意欲の向上。
マニュアル作成にかかる工数を削減できる
動画マニュアルなら、動画を撮影するだけでマニュアルが作成できます。
文章や図だと、わかりやすい説明をしようとするとかなりの工数がかかってしまいます。とくに文章の作成は、動作情報を言語化する際の難しさがあるため、苦労されている方も多いはずです。
しかし動画マニュアルなら、動作の言語化や図の作成に時間をかけることなく、素早くマニュアルを作成できます。実際に動画マニュアルを活用することで、マニュアル作成の工数を1/3に削減した事例もあります。詳しくは以下のインタビュー記事をご覧ください。
インタビュー記事:手順書作成の工数は紙の1/3に。自動翻訳で外国人教育にも活用。
OJTにかかる工数を削減できる
従来のOJTでは現場の担当者が直接指導を行うため、多くの時間と労力がかかります。
動画マニュアルを活用すれば、各自で自学自習できるようになるため、OJTの回数を大幅に減らせます。
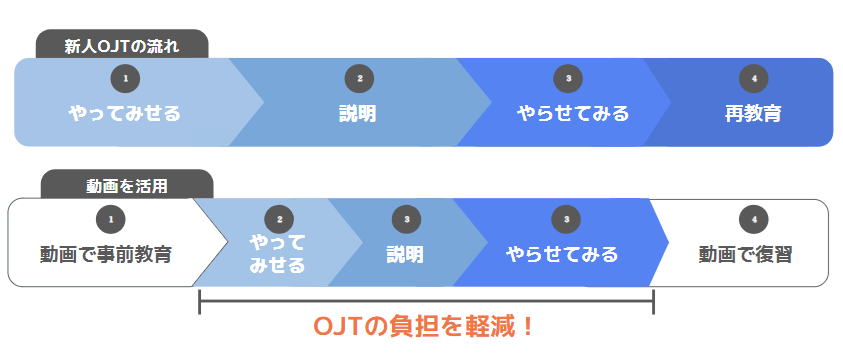
また、動画マニュアルで一度予習してからのOJTは、いきなり始めるOJTよりも理解度が高くなりやすいです。OJT後の復習として、もう一度動画を見ればさらに理解度は高まるでしょう。
ヒューマンエラーを抑止するためには、反復的な学習を繰り返して、ゆくゆくは意識/体に沁み込ませるということが必要です。動画マニュアルを活用することで、管理者などの教育負担を軽減しつつ反復学習することが可能です。
動画マニュアルを活用して、OJTの7割を動画マニュアルに置き換えたという事例もあります。詳しくは以下のインタビュー記事をご覧ください。
インタビュー記事:年間の新人教育時間を3,700時間削減。トレーナーの教育時間が大幅に減り営業成績も向上!
動画マニュアルのより詳細な効果などは、以下のガイドブックからご覧になれます。ヒューマンエラーだけでなく、教育の工数などにも課題感を感じていらっしゃる方は、ぜひ動画マニュアルの活用をご検討ください。
動画と聞くと『編集が難しそう…』と感じるかもしれませんが、編集未経験者でもかんたんに動画マニュアルを作成できるツールが動画マニュアル「tebiki」です。次章では、本ツールの機能概要をご紹介します。
動画マニュアルをかんたんに作成できる「現場教育システムtebiki」とは
動画マニュアル「tebiki」は、誰でもかんたんに動画マニュアルが作成ができるツールです。
動画作成だけではなく、動画マニュアルの閲覧状況や習熟度管理、スキルマップ機能によるスキル管理など、人材教育を効率化する機能が揃っています。
▼動画マニュアル作成ツール「tebiki」紹介動画▼
誰でも簡単に動画マニュアルを作成できる
tebikiは、とにかく「操作のかんたんさ」にこだわって作られたツールです。
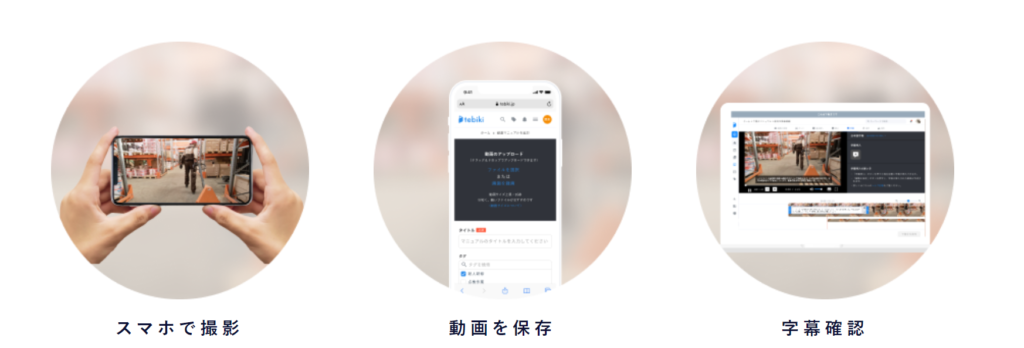
操作画面はシンプルで使いやすく、編集スキルがない方やパソコン操作に不慣れな方でも直感的に動画マニュアルが作成できます。tebikiを活用することによって、一般的な動画編集ソフトで1時間かかっていた作成時間が、15分ほどに短縮された事例もあります。
また、操作が簡単だからこそtebikiを活用できる人が増え、動画マニュアルの作成スピードが加速度的にアップします。以下の事例記事では、tebikiがどれくらい簡単にマニュアルを作成できるのかをご確認いただけます。
インタビュー記事:動画マニュアル作成時間が75%削減!教育体制を強化し、お客様に喜ばれる商品を提供したい
テスト機能やレポート機能で、理解度や学習進捗度を把握できる
tebikiには、従業員の理解度をチェックするための「テスト機能」が搭載されています。
動画視聴後や研修後にテストを実施することで、従業員がどの程度業務を理解しているかを把握したうえで、教育内容や頻度を調整することが可能です。また、テストの自動採点機能もついているため、教育担当者は手間をかけずに従業員のスキルを確認できます。
ヒューマンエラー対策の場合、動画マニュアルで学んだ内容をテストで確認し、合格に達した従業員から該当作業に着手できるといった運用も可能です。作業前に一定の理解を求める仕組みにすることで、ヒューマンエラーを未然に防ぐことができます。
▼tebikiで作成したオリジナルテスト▼
(株式会社大商金山牧場の導入事例より)
.jpg)
100ヶ国語以上の言語に自動翻訳
tebikiの動画マニュアルは、字幕を100ヶ国語以上の言語に自動翻訳できる機能が付いています。
この機能により、外国人労働者が使うためのマニュアルをわざわざ翻訳して作る必要がなくなります。さらに、英語やベトナム語などの計15言語で字幕を読み上げられるため、母国語で説明を聞きながら理解を深めてもらうことが可能です。
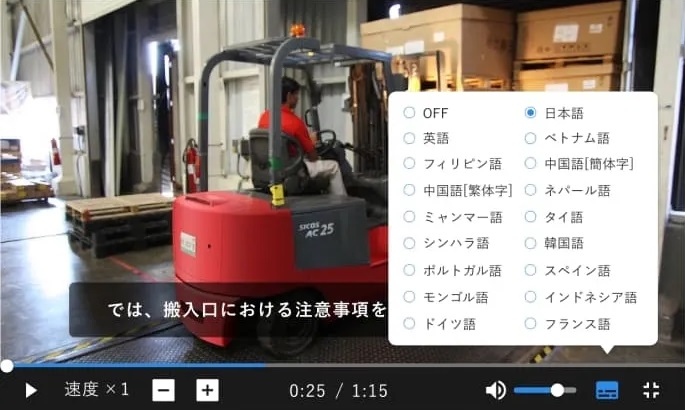
tebikiなら100ヶ国語以上に対応した自動翻訳機能が搭載されていることが分かる編集画面
気になる「精度」ですが、日本語の日常会話程度であれば、問題なく伝わるレベルです。もし自動翻訳で伝わらないということであれば、後から修正することも可能です。
製造業や建設業のように、職場で多国籍の従業員を抱えているケースもあります。このような現場では、言葉や文化の違いがヒューマンエラー対策を難しくしているといえます。このような職場でtebikiを活用することで、それぞれが母国語で学べる仕組みを整えて、業務理解度を向上させることができます。
以下の記事では、実際にtebikiを活用して外国人教育が効率化された事例をご紹介しています。外国人労働者の教育工数を課題に感じていらっしゃる方はぜひご覧ください。
インタビュー記事:新人研修の手間が1/10に!自動字幕翻訳で、外国⼈スタッフの理解度テスト正答率が100%になりました。
半永久的に続く手厚いサポート
tebikiでは、導入してからきちんと運用されるまでのサポートとして、導入支援プログラムをご用意しています。また、ある程度運用が軌道に乗った後も、半永久的なフォローアップを行っています。
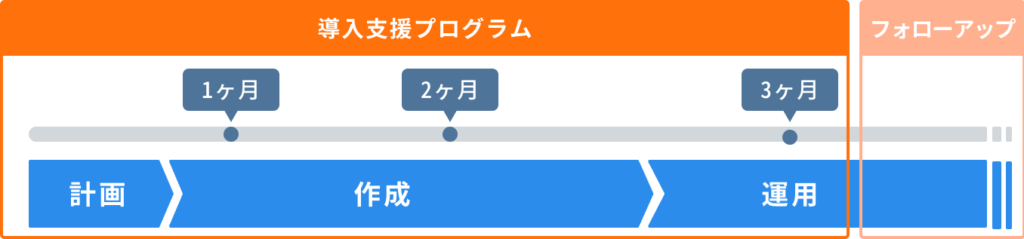
動画マニュアルは、あくまでも業務改善のための手段です。
ヒューマンエラーを動画マニュアルで減らしていく場合、作成して終わりではなく、分かりにくい部分など改善できるところは修正し、PDCAサイクルを重ねていくことが必要です。また、動画マニュアルを現場で運用する仕組みも必要です。
tebikiでは、動画マニュアルの品質向上と、運用による業務改善を実現するための伴走支援を行っています。今回ご紹介しきれていないtebikiの機能概要やプランなど、より詳細な情報を知りたい方は以下のバナーをクリックして資料をご覧ください。
tebikiを利用してヒューマンエラーの確率を下げよう【まとめ】
製造業におけるヒューマンエラーは、日常的な課題の一つであり、およそ1000回に3回(0.3%)の確率で発生します。注意や教育だけで防ぐのは難しく、特に小さなミスが積み重なることで重大事故につながるリスクが高まります。
ヒューマンエラーをゼロにすることは不可能ですが、効果的な対策を講じることでその確率を大幅に減らせます。
ポカヨケやフールプルーフの仕組みを導入してミスを防ぎ、5S活動で作業環境を整えることが重要です。また、ヒヤリハットの共有や危険予知トレーニング(KYT)も、全員で危険を意識するために有効です。
さらに、マニュアルの徹底確認や、動画マニュアル「tebiki」を使った教育によって、より理解を深め、ミスを予防できます。
tebikiの資料は以下の画像から無料でダウンロード可能です。有効なヒューマンエラー対策や現場に負担をかけない教育方法をお探しの方は、是非ご覧ください。