かんたんデジタル現場帳票「tebiki現場分析」を展開する現場改善ラボ編集部です。
製造業DXやデジタル化の一環で、ペーパーレス化を検討する製造現場が増えていますが、『ペーパーレス化による改善効果がわからない』『失敗したくないので成功方法を知りたい』といった方もいらっしゃると思います。
そこで本記事では、製造業がペーパーレス化に取り組むメリットや成功事例、ペーパーレス化の進め方やポイントを、現場改善ラボ独自の調査データも交えて解説します。目次からご覧になりたいトピックスをクリックしてご覧ください。
目次
製造業でペーパーレス化を進める目的やメリット
ペーパーレスという言葉だけを見ると、ペーパーレス化=「業務で使う紙を減らすこと」と感じるかもしれません。確かにペーパーレス化によって、紙や印刷、廃棄、保管スペースなどのコスト削減はできます。
しかし本来の目的は、製造現場で紙の使用で発生しているムダな業務や、紙の運用によって生じるトラブルを解消するといった、業務効率化や業務改善がペーパーレス化の目的です。
まずは製造業がペーパーレス化に取り組むことで、どのような業務改善を実現するのか?目的やメリットを整理します。
紙を用いた業務による負担を減らす
ペーパーレス化を推進することで紙に関する付帯業務の負担を効率化し、会社の利益に直結するような生産活動や改善活動に時間を割けられる効果が期待できます。
製造業で使用する紙として、作業手順書や紙マニュアルを例にお話します。
作業手順書・紙マニュアルは製品や工程ごとに存在し、作成⇒印刷⇒配布⇒回収⇒管理のサイクルがたびたび発生します。製造日報などの現場帳票も同様のサイクルが日々発生し、現場管理者は記載内容の承認や集計、分析といった工数も発生しています。
このような業務は日々の生産活動に不可欠ですが、実際に対応している間は会社の利益に直結しない業務となってしまいます。ペーパーレス化によってこれらの工数が軽減され、現場の作業者や管理者は付加価値の高い生産活動や改善活動に注力できるようになります。
▼具体的なペーパーレス化による負担軽減の例▼
作業手順書のペーパーレス化 | 1つあたりの作成期間を0.5~1か月から1~2日に効率化 (株式会社神戸製鋼所の事例より) |
現場帳票のペーパーレス化 | 集計作業が1日2時間から約1分に効率化 (共栄工業株式会社の事例より) |
情報伝達を容易にできるようにする
ペーパーレス化によって、場所を問わずリアルタイムで必要な情報にアクセスできる点もメリットです。
紙の作業手順書を例に取ると、多品種少量生産の現場では製品別に膨大な手順書が存在します。少量生産がゆえに使用頻度が限られていることから、管理場所や方法があやふやになってしまい、必要な時にすぐ使えないというケースも珍しくありません。
また、不具合報告書のように管理者へ早急な情報伝達が必要な帳票では、手書きの工数に加えて記入ミスやクセ字によって管理者が再度記入者に確認する工数が発生するなど、必要な情報にアクセスできるまでにタイムラグが生じる場面もあります。
ペーパーレス化によって作業手順書や現場帳票など、業務に必要な文書はデジタル上に一元管理され、使用者は必要なときに正しい情報にリアルタイムでアクセスできます。
製造現場をデータとして可視化してKPI分析や改善を行う
ペーパーレス化を進めることで、製造現場の状況や動きなどがデータとして可視化できます。
従来は、紙やExcel上に蓄積された現場帳票の情報を集計する工数が必要ですが、デジタル上で一元管理することで集計の手間がなく、データとして可視化ができるようになります。結果的に、リアルタイムで不良率や設備総合効率といった現場指標(現場KPI)の可視化/分析が行えます。
さらに、情報の集計といった膨大な手間が発生していた工数が効率化されることで、より重要な製造現場にまつわる分析に注力できるようになり、品質改善や生産性向上、工場の安全対策など本質的な改善活動まで行えるようになります。
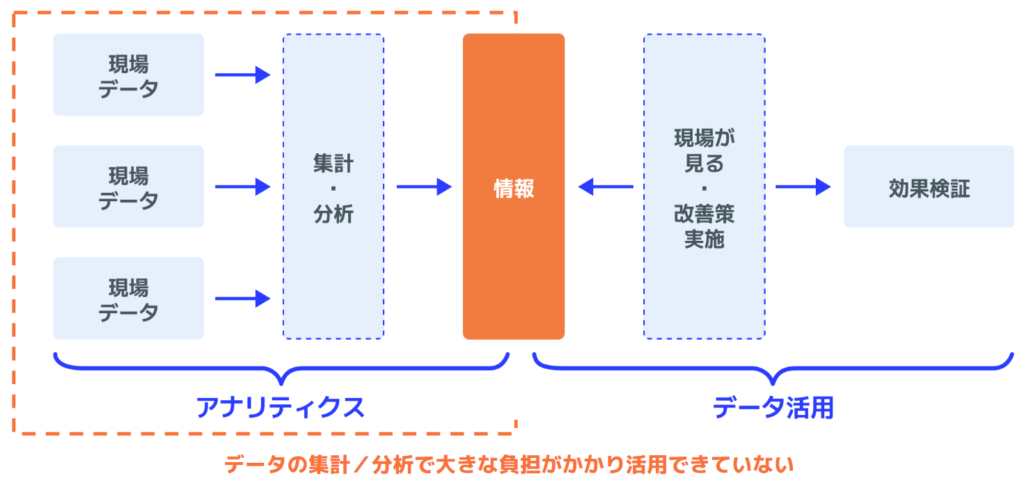
上記の図のように、ペーパーレス化を進めることで製造現場のデータ活用を推進する動きに直結します。現場の状況がデータとして可視化されることで、ボトルネックも確認しやすくなり、現場主体による改善提案のきっかけにもなります。
ここまで製造業がペーパーレス化に取り組む、主な目的やメリットをご紹介しました。このような業務上に存在するムリムダムラの改善を通じ、生産性の向上を狙うことが本質的な目的といえるでしょう。
『より詳しく目的やメリットを確認したい!』という方は、以下のリンクをクリックして製造業のペーパーレス化に関するお役立ち資料をご覧ください。
>>「製造現場の生産性を向上するペーパーレスの進め方」の参考資料も見てみる
製造業のペーパーレス化が進まない理由から紐解く「成功のヒント」
私たちが行った「ペーパーレス化推進状況の実態調査」で、取組状況について回答を集計したところ、全体の27%が「取り組んでいるが、成果が出ていない」という結果になりました。
ペーパーレス化に取り組んでいる方だけを対象とすると、推進しているうちの52%は「成果が出ていない」という結果です。
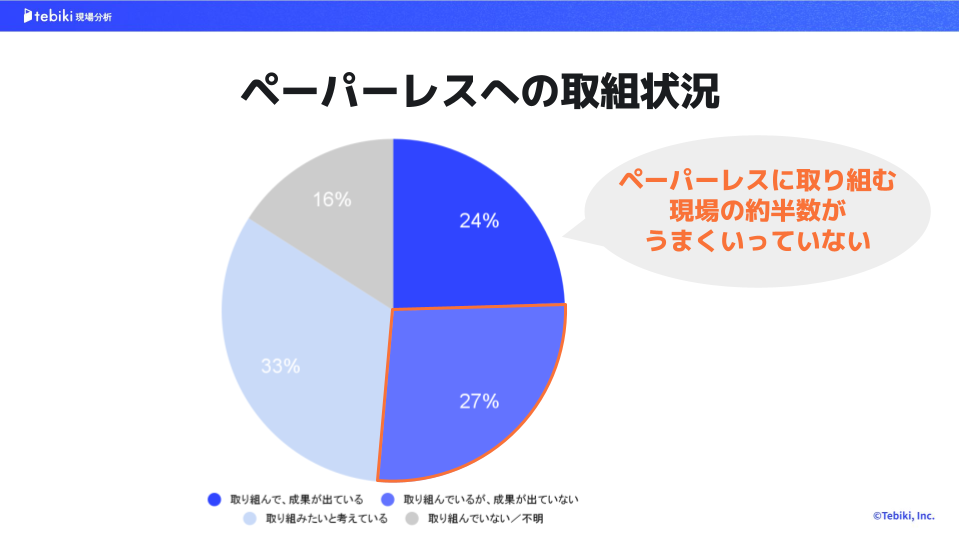
【現場改善ラボ「ペーパーレス化推進状況の実態調査」を基に作成(N=143)】
「取り組んでいるが、成果がでていない」と回答した39名の方に、成果が出ていないと考える1番の理由を伺ったところ、以下のような結果となりました。
- 製造現場など社内でペーパーレス化の必要性が認識されていない:21%
- 業務内で紙を使用する場面を減らすことができない:21%
- 慣れ親しんだ従来の方法の変化に対する抵抗がある:15%
- かえって業務フローが複雑になり手間が増えている:10%
- 可視化したデータをうまく活用できていない:3%
- 複雑なシステムで使用者に高度なスキルが求められるため:3%
- セキュリティ面で不安に感じる社員がいるため::0%
- その他:28%
その他の回答数が多く、それぞれの製造現場や環境によって上手くいかない背景はさまざまあることが伺えるものの、ペーパーレス化の必要性が浸透していない/紙の使用頻度が減らせない/慣れ親しんだ方法からの変化に対する抵抗といった、根強い紙文化をなくしにくいことが上手くいかない理由として考えられるでしょう。
製造現場で紙を使用する方にとって、日々の紙文書の処理に負担は感じてはいるものの、それ以上にゼロから新しい手法に対応する不安や負担を感じていることが予想されます。
また、ペーパーレス化の必要性が伝わっていないことで、『なぜわざわざ変える必要があるのか?』という意識に繋がっている可能性も考えられます。この背景を踏まえると、実際にペーパーレス化を推進するときには、以下のような意識やポイントが必要です。
- 従業員の業務負荷が減るなど「明確なメリットが生まれる」ことを伝える
- 最初は一部の紙文書からペーパーレス化を進める(スモールスタート)
- 誰でもかんたんに対応できるツール/フォーマットを用いる(現場の負担をかけない)
このポイントを踏まえて、次章では実際にペーパーレス化による業務改善に成功している製造業の事例を詳しくご紹介しますので、ぜひこのままご覧ください。
『他にもポイントがあれば知りたい!』という方は、以下のリンクをクリックしてペーパーレス化に関する参考資料をご覧ください。
>>「製造現場の生産性を向上するペーパーレスの進め方」の参考資料も見てみる
単なるペーパーレスで終わらせず、現場改善につなげる進め方とポイント
現場から抵抗が起きないペーパーレス化には、「業務改善や生産性改善など明確な改善が見込める」「新しい手段でも負担が少ない方法」である必要があります。
本章では、このようなペーパーレス化を推進する方法やポイントをステップ別にご紹介します。
- 解決したい問題を定義する
- 解決したい問題の優先度を整理する
- ペーパーレス化によって生じる課題を整理する
- ペーパーレス化した後の業務手順や方法を設計する
- ペーパーレス化を進めるためのスケジュールや計画を決める
今回ご紹介している内容は、別紙のガイドブックでも図解を交えて、より分かりやすく解説をしています。記事と併せてご活用いただくと、より分かりやすく進め方をご理解いただけるので、以下のリンクをクリックして、ご覧ください。
>>「製造現場の生産性を向上するペーパーレスの進め方」の資料も見てみる
解決したい問題を定義する
まずはペーパーレス化によって解消したい問題を定めます。
重ねてにはなりますが、ペーパーレス化は単に紙を減らすことではなく、生産性向上や業務効率化など業務改善を目的としています。紙文書の使用によって製造現場で発生している課題を洗い出し、解消を狙う問題を決めましょう。
紙の使用によって発生している問題例は以下のような内容です。この例を参考に、皆さまの職場で発生している課題を精査してみてください。
- 現場帳票の記録/転記ミスが頻発し、確認工数に時間が割かれている
- 現場帳票の承認や管理対応が膨大で、データ分析を通じた改善活動ができていない
- 作業手順書が形骸化し、OJTに依存した教育体制になっている
- 文字ベースの紙マニュアルでは、作業手順などの動作が理解しにくくミスが起きる
解決したい問題の優先度を整理する
解消したい問題を一度にすべて対応することは現実的ではありません。また、現場からの抵抗や混乱を抑えるためにもスモールスタートで進める必要があります。そのため、まずは解消したい問題の優先度を整理しましょう。
優先度を整理するときには、「ペーパーレス化の難易度」と「業務改善の効果が高いもの」を検討して4象限に分けることをおすすめします。
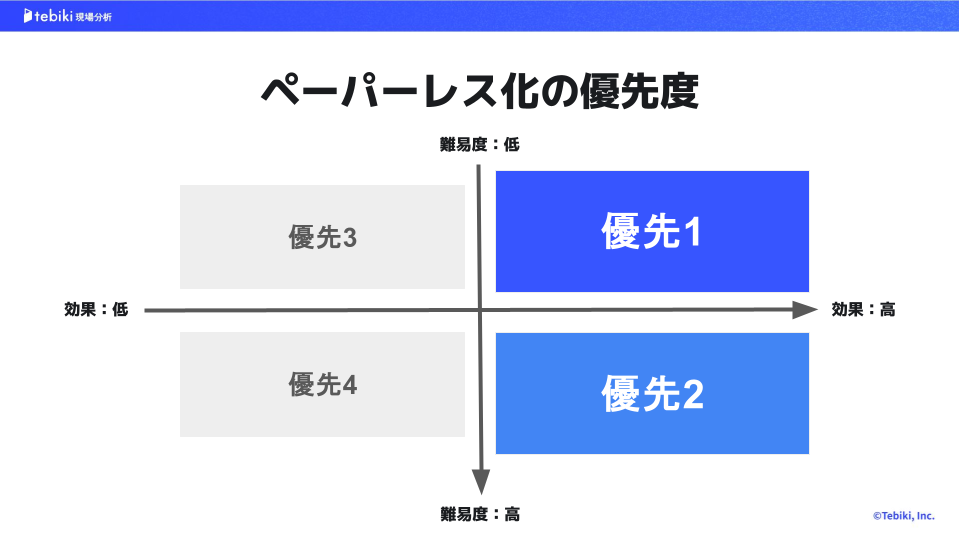
ペーパーレス化の難易度が低く改善効果が高いものから着手することで、製造現場からも『思ったよりかんたんに使えて、紙の時よりも負担が少ない!』という印象を引き出せます。
導入時に好意的な印象を残すことによって、その後のペーパーレス化もスムーズに進むため、まずは難易度が低く改善効果が高い課題から着手しましょう。
改善効果を判断するには、「費用対効果」が重要な指標の1つです。しかし、この費用対効果を算出するのは簡単ではなく、「費用対効果がよくわからないから、導入したほうがいいかどうかも結局わからない」となりペーパーレスに踏み切れずにいる現場は少なくありません。
そこで、現場帳票をペーパーレス化するコストが見合うかどうかが分かる、費用対効果を算出するシートをご用意しています。以下のページで公開中の資料内でシートを公開していますので、参考情報としてぜひご活用ください。
>>現場帳票をペーパーレス化する「費用対効果」をクリックして調べてみる
ペーパーレス化によって生じる課題を整理する
ペーパーレス化を行う場合、何らかのITツールを使用することになります。ペーパーレス化で使用するツールによって、どのような課題が発生しそうか予め整理を行いましょう。事前に課題を整理することで、その課題に対処できる作業方法や、自社にマッチしたツールの選定軸などを確認できます。
例えば、解消する課題を「手順書の内容が古く標準作業が伝わっていない」としたケースを想定します。
この場合の解決策として、手順書を動画化して作成/更新工数を効率化する、動作を映像で伝えて分かりやすく伝えるといった内容が考えられます。この解決策を実行するときに、以下のような点が懸念点になるでしょう。
- 誰が動画を編集するのか?
- 製造現場からどのように動画ファイルへアクセスし、閲覧するのか?
このとき、やってしまいがちなことが「懸念点を実行できない理由」にしてしまうことです。
できない理由として捉えてしまうと、難易度が多少あっても改善効果が見込める領域のペーパーレス化が進みません。結果的に、改善効果が薄い領域から着手してしまい、現場も効果を実感しにくく『前の形で問題なかった』と抵抗が発生してしまいます。
ペーパーレス化を進めるときに直面する懸念点は「乗り越えなくてはいけない取組課題」として捉え、取組課題を解決できる方法の検討や、使用するツールの選定基準などに盛り込んでいきましょう。
ペーパーレス化した後の業務手順や方法を設計する
従来使用していた紙媒体をペーパーレス化する場合、業務手順や方法が変わる可能性があるため、事前に整理して再設計を行いましょう。
「組付け作業の作業手順書」を動画マニュアルによってペーパーレス化したとすると、以下のような変化が考えられます。
紙の手順書 | ペーパーレス(動画)化された手順書 |
---|---|
1. 保管場所に手順書を取りに行く 2. 説明文を確認する 3. 作業を開始する 4. 終了後、元の保管場所に戻す | 1. 作業場でPC/タブレットから情報を探す 2. 動画で作業手順を確認する 3. 作業を開始する |
上記は簡易的な例ですが、手順書を取りに行く/戻す作業が大きく変わることが分かります。このように、ペーパーレス化によって作業手順や流れなど、工場内ルール(標準)が変わるため、事前に整理を行うことが必要です。
ペーパーレス化は4m変更にも該当すると想定できるため、事故やトラブルを未然防止するためにも予め整理を行いましょう。
ペーパーレス化を進めるためのスケジュールや計画を決める
前章の「成功のためのヒント」でご紹介したように、ペーパーレス化はスモールスタートで進めていく必要があります。整理した優先度を基に、どのようなスケジュールで何の紙文書からペーパーレス化していくかスケジュールを定めましょう。
計画の粒度は「12月までに製造日報をペーパーレス化する」といったものではなく、12月に製造日報のペーパーレス化を実現するという目標から逆算し、必要な作業を洗い出したうえで各作業もスケジュールに盛り込むことがおすすめです。
以下はスケジュール設定のサンプルです。
- 8月:製造日報に必要/不要な項目の精査
- 9月:マスタ(マスターデータ)の整理、デジタル製造日報のフォーマット作成
- 10月~11月:一部の工程でテスト的にペーパーレス化し検証と改善を重ねる
- 12月:製造部全体の製造日報をペーパーレス化
ご紹介したように、「業務改善や生産性改善など明確な改善」を見込んで製造現場のペーパーレス化を進めていく必要があります。一方で、「現場の負担が少ない方法」はペーパーレス化に使用するツールに依存します。
本章でご紹介したペーパーレス化を進める方法について、より詳しく・分かりやすく知りたい方は、図解も交えて解説しているガイドブックを以下の画像をクリックしてご覧ください。
ペーパーレス化が業務改善につながった製造業の成功事例4選
本章では、ペーパーレス化によって業務改善を実現した4社の成功事例をご紹介します。
株式会社日本電気化学工業所
アルミニウムの表面処理を専門に行う株式会社日本電気化学工業所では、点検表のような現場帳票をペーパーレス化し、製品の品質保証に直結する重要なデータを正確かつ効率的に管理できるようになりました。
▼インタビュー動画:株式会社日本電気化学工業所▼
紙で帳票管理を行っていた以前は記録そのものが目的化し、収集データを改善活動に活用することができなかったと語っています。また、設備の異常値検出に時間を要し、迅速な対応が難しい状況がありました。
そこで同社は、tebiki現場分析を活用した現場帳票のペーパーレス化に取り組み、設備の異常など現場の不具合をリアルタイムで計測、品質不良の早期発見と未然防止を実現できる品質管理プロセスに改善しました。実際に、温度データをリアルタイムで確認できたことでわずかな温度低下を発見し、現場で詳細な点検を行ったところ、配管の小さな穴を発見しています。
この早期発見により、大規模な故障や生産ラインの停止といった深刻な事態を未然に防ぐことができました。「もし従来の紙ベースの記録管理だったら、このような微細な変化を見逃してしまい、問題が大きくなってから気づいたかもしれません。」と、tebiki現場分析導入の効果を実感されています。
同社のより具体的なペーパーレス化推進の背景や効果は、以下のインタビュー記事をクリックしてご覧ください。
インタビュー記事:品質不良の未然防止をリアルタイムデータで実現。異常値検知を迅速にできた理由。
共栄工業株式会社
スチール製家具の生産・販売を行う共栄工業株式会社では、製品の品質管理やISO9001の運用のために、製造工程の記録を行う現場帳票をペーパーレス化しています。
▼インタビュー動画:共栄工業株式会社▼
もともと現場帳票を紙やExcelで運用していた同社では、以下のような課題を抱えていました。
- 分析や現場改善ではなく、記録することが目的に
- 紙からExcelの転記に1日2時間かけ、管理者の負担に
- 日々の生産管理/進捗管理に追われ、分析や改善が後回しに
そこでtebiki現場分析を活用し、製造日報など現場帳票のペーパーレス化に取り組んだところ、以下のような業務改善を実現しています。
- 管理者の集計作業が、1日2時間から約1分まで削減
- ダッシュボード/グラフ化機能で、分析から業務改善までを効率化
- 記録データをもとに、設備トラブルの予防措置が実行できるように
- 作業実績がリアルタイムで分かり、他部門の進捗が可視化されるように
具体的なペーパーレス化の取り組みを知りたい方は、以下のインタビュー記事をクリックしてご覧ください。
インタビュー記事:1日2時間の集計作業が約1分に。スチール製家具製造の共栄工業のデジタル改革
株式会社日ピス福島製造所
株式会社日ピス福島製造所は、リケンNPRのグループ企業として1982年に操業開始し、主に自動車のエンジン部品を製造しています。
▼インタビュー動画:株式会社日ピス福島製造所▼
同社では、”生きたデータ活用”ができていないという課題を抱えていました。例として、とある製造管理記録の数値が前月比で1.4倍になっていたにも関わらず、紙で記録していたため発見が遅れたことや、蓄積した記録をグラフ化することが現場の負担になり、進まないという状況でした。
そこで、課題解決のためにtebiki現場分析を導入。作業者がデータを記録するだけでグラフがリアルタイムに更新されるため一目で変化が見えるようになり、監督者が現場に状況を見に行く時間が大幅に短縮されました。
特に、生産実績帳票をグラフ化したことで「段取り」の停止時間に人による差があることが判明し、停止時間がかかっている作業者への標準化教育を通じて、設備稼働の効率化が可能になりました。
同社が感じるtebiki現場分析の「使い心地」や、ペーパーレス化による生産性向上に向けての取り組みを詳しく知りたい方は以下のインタビュー記事をご覧ください。
インタビュー記事:設備停止は”作業者ごとのバラつき”が要因だった。スピーディな要因分析の方法とは
株式会社アルバック
世界最高水準の真空技術による製品を多数製造/販売する株式会社アルバックは、作業手順書を動画に置き換えるペーパーレス化推進で拠点間の技術/ノウハウの共有が進み、結果的に67%の生産性向上を実現しています。
生産性向上を実現した、同社の取り組みの詳細は以下のような内容です。
- 定点カメラで作業全体の流れや動線を撮影し、移動時間や作業の切り替えなどを評価
- 細かい作業のポイントや手順を動画マニュアル化し、詳細な動作分析を実施
- 拠点間で意見交換し、「なぜそのように作業するのか」理由や背景を議論
製造現場の生産性を支える暗黙知を、動画マニュアル「tebiki現場教育」で視覚的に理解できるようにし、その動作の意義や有効性を拠点間で議論したことで、作業を客観的に見直す機会となり改善点の発見にもつながっています。
このような取り組みを半年間集中的に行った結果、ある製造工程の制作時間を78分短縮し、1日あたりの生産可能数も従来よりも67%向上しています。
同社のより具体的なペーパーレス化推進の内容は、以下のインタビュー記事をクリックしてご覧ください。
インタビュー記事:人員・労働時間を変更せずに、ボンディング工程の生産性を167%に改善
効果が見えやすいペーパーレス施策は「帳票のデジタル化」がおすすめ
ここまでご紹介したように、製造業のペーパーレス化の成功には「現場に負担をかけないこと」「明確な改善が見込めるところから始めること」がカギです。
その2つを実現し、現場の課題解決に役立つツールとして、「デジタル現場帳票」をおすすめします。ここでは、デジタル帳票導入のメリットと、実際に現場で使いやすいツール「tebiki現場分析」をご紹介します。
現場帳票を電子化する「デジタル現場帳票」
デジタル現場帳票は、紙やExcelで運用されている記録や承認、集計が一気通貫で行えるツールです。製造現場の管理者が負担となっている業務を、デジタル上で簡単に行うことが可能になります。
製造業で活用されているツールはさまざまありますが、今回は記録データの分析まで効率的に実行可能な「tebiki現場分析」の機能概要をご紹介します。
「紙からExcelへの転記」が不要になり、負担をかけずにデータを扱える
tebiki現場分析は記録から承認、分析までをツール上ですべて行うことができます。
従来の運用では、紙ベースの現場帳票で記録を行い、管理者による承認、Excelへ転記して集計、複雑な関数やマクロでデータ分析という工数が発生します。本来、データ分析を行い業務改善につなげることが現場帳票の目的である一方、記録や承認、転記で相当な手間が発生し、分析まで着手できていないという声をよく頂きます。
tebiki現場分析なら、スマートフォンやタブレットといった現場の端末上で記録された情報を、リアルタイムで管理者が確認/承認できる状態になります。また自動計算に加え、管理図やパレート図などグラフ機能があるため、確認段階で現場データを瞬時に可視化して分析を行うことが可能です。
実際にtebiki現場分析を活用する製造現場では、管理者による現場帳票の集計作業が1日2時間から約1分まで、大幅に効率化された事例もあります。
異常値をリアルタイムで計測でき、迅速な改善につなげられる
tebiki現場分析では、記録項目ごとに正常な記録値の基準を設定することで、正常値から外れた記録は異常値として検出されます。
異常値を記録した箇所が強調表示されるだけでなく、管理者へ異常値が記録されたことが通知されるため、いち早く現状把握から対策を講じることができます。
従来の運用では異常の検知までタイムラグが生じ、原因分析から対策実行まで膨大な時間を要していました。tebiki現場分析では、前述の分析機能と異常値設定を組み合わせることで、不良品の流出や設備不具合による生産ライン停止など、重大な問題に発展する前に対策が講じられるようになります。
実際にtebiki現場分析を活用する製造現場では、設備の異常を早期に捉えたことで、初期段階でトラブルに対応し不良品の発生を未然防止できた事例もあります。
自動グラフ化機能やダッシュボード機能でリアルタイムの確認が可能
tebiki現場分析は記録された現場帳票のデータを、管理図など自動でグラフ化する機能、不良率などの自動計算機能を搭載しています。
出力されたデータは、tebiki現場分析上のダッシュボードでリアルタイムで確認することができるため、製造現場のモニターなどに投影し、その場で状況を確認することが可能です。
▼製造現場でダッシュボードを確認するイメージ▼
【tebiki現場分析導入事例:株式会社日本電気化学工業所より抜粋】
今回ご紹介した機能以外にも、記録者や管理者の現場帳票運用工数を効率化する機能が多数あります。tebiki現場分析のより詳細な機能やプラン、改善事例を知りたい方は、以下のリンクをクリックして概要資料をご覧ください。
>>かんたんデジタル現場帳票「tebiki現場分析」の詳細を見てみる
【補足】製造業でペーパーレス化できる主な文書
製造業でペーパーレス化を進める場合、実行できる主な文書とペーパーレス化の方法、そのメリットについて表形式でまとめました。
文書の種類 | ペーパーレス化の手段 | 主なメリット |
---|---|---|
現場帳票 (製造日報・品質管理書類・保守点検記録・注文書など) | 「tebiki現場分析」のようなデジタル帳票ツールの導入 | ・本社や他拠点からリアルタイム閲覧が可能 ・製造管理や意思決定の効率向上 ・検索/更新/共有が容易になり、一元管理が可能 |
作業手順書・紙マニュアル | 動画マニュアル化 | ・作成/更新工数の削減(最大1/3に削減した事例あり) ・紛失や汚損リスクの軽減 ・PCやタブレットでの検索性向上 |
設計図・図面 (特に大判サイズ) | ・PDFや3D図面の電子化 ・タブレットでの閲覧 | ・印刷や保管にかかるコストの大幅削減 ・視点変更やズームなど、紙では不可能な操作が可能 |
会計帳簿 (勤怠管理・給与明細・請求書など) | ・打刻/給与/会計データのシステム導入 | ・打刻ミスや入力漏れの防止、管理コスト削減 ・個人情報のセキュリティ強化 ・電子帳簿保存法に対応(2022年改正) |
補足情報:製造業のペーパーレス化推進状況の調査結果
最後に、私たち現場改善ラボが会員の方のうち、製造業に従事する方を対象に行った実態調査の結果をご紹介します。総回答数143件です。
【調査結果】活用頻度の多い紙文書について
現場改善ラボ会員の方のうち、製造業に従事されている143名の方に伺ったアンケートでは、活用頻度が多い紙文書として製造日報や点検表といった現場帳票が43%と最も多い結果になりました。
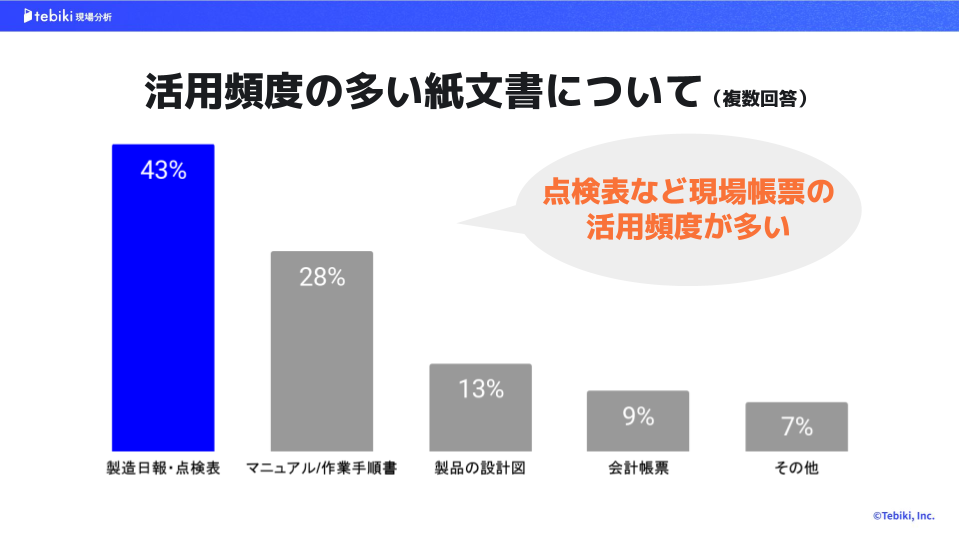
現場帳票を中心にマニュアルや作業手順書など、製造業では紙を使用する場面が多く、ペーパーレス化による業務改善の効果は高いといえるでしょう。
【調査結果】紙文書の使用で生産性の低下を感じること
前項と同じ143名の方に紙の使用で生産性の低下を感じるか伺ったところ、「よくある」「ときどきある」という回答が約80%に上りました。

生産性が下がっているような紙の運用、とくにマニュアルや作業手順書、現場帳票のペーパーレス化は生産性向上策の1つとして効果的な可能性が伺えます。
【調査結果】紙文書の処理に割いている時間
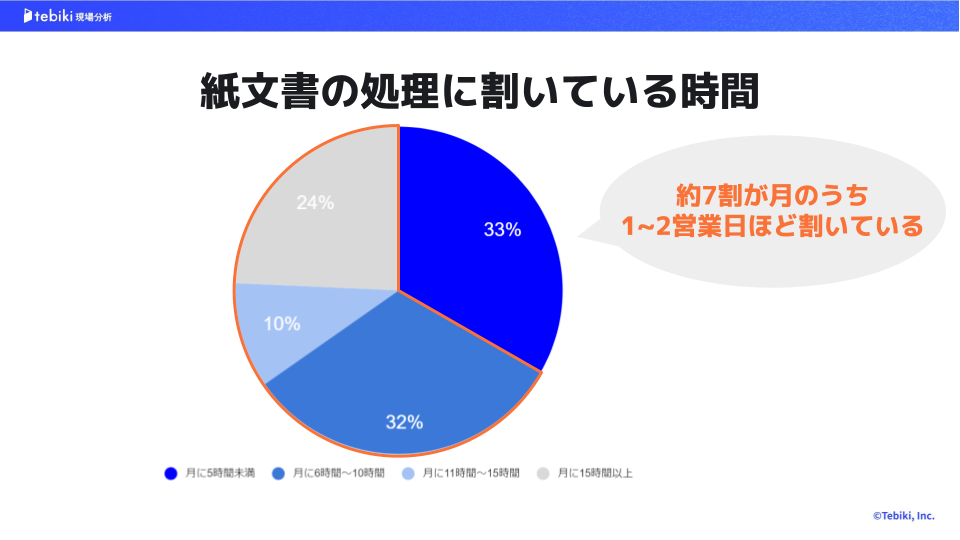
製造業に従事する143名の方に毎月、業務内で紙文書の処理に割いている時間を確認したところ、「月に5時間未満」が33%で最も多い結果となりました。一方で、「月に15時間以上」も24%と少なくない結果となっており、現場によっては紙文書の処理に膨大な業務時間が割かれている様子が伺えます。
別の設問【紙文書の使用により生産性の低下を感じること】で「よくある」を選択した53件に注目をすると、月に6時間以上割いている方が81%に上り、製造現場の生産性に紙文書が影響を及ぼしているといえます。
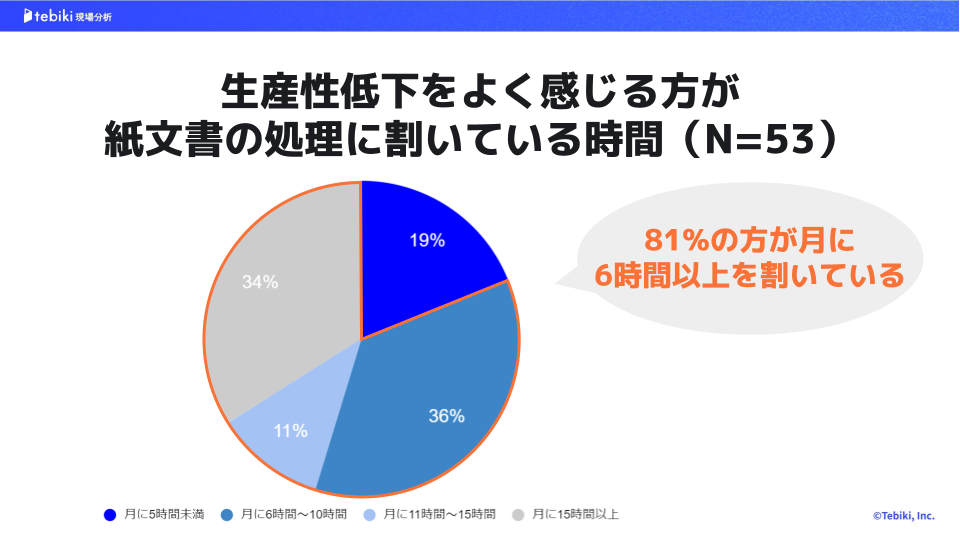
【調査結果】ペーパーレス化を進める1番の目的
【ペーパーレスの取組状況】で「取り組んでいて成果が出ている」「取り組んでいるが成果が出ていない」「取り組みたいと考えている」と回答した119件に対し、ペーパーレス化を進める1番の目的を伺ったところ、「生産性改善や業務プロセスの効率化」が41%と最も多い結果となりました。
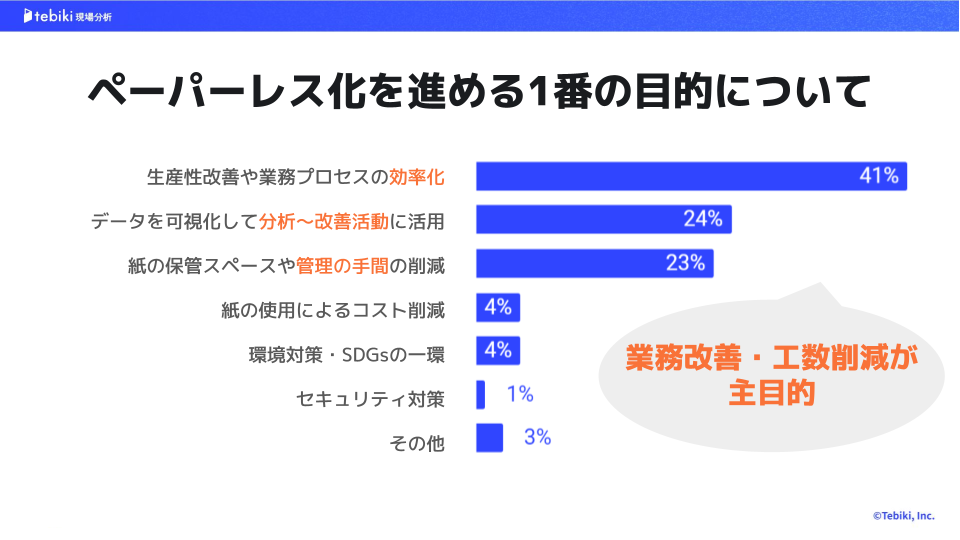
また、「データを可視化して分析~改善活動に活用」「紙の保管スペースや管理の手間の削減」も多く、製造現場で膨大な紙文書を運用し、管理の手間を抱えているだけでなく、集めた情報を改善活動などの取り組みに反映ができていない実態が伺えます。
この結果から、ペーパーレス化に取り組むことで業務プロセスや生産性、手間が効率化できるだけでなく、改善活動など前向きな取り組みに時間を割けられるようになる期待があるといえるでしょう。
【調査結果】ペーパーレス化で実感する1番の効果
【ペーパーレスの取組状況】で「取り組んでいて成果が出ている」と回答した35件に対し、ペーパーレス化によって実感している効果を伺ったところ、以下のような結果になりました。
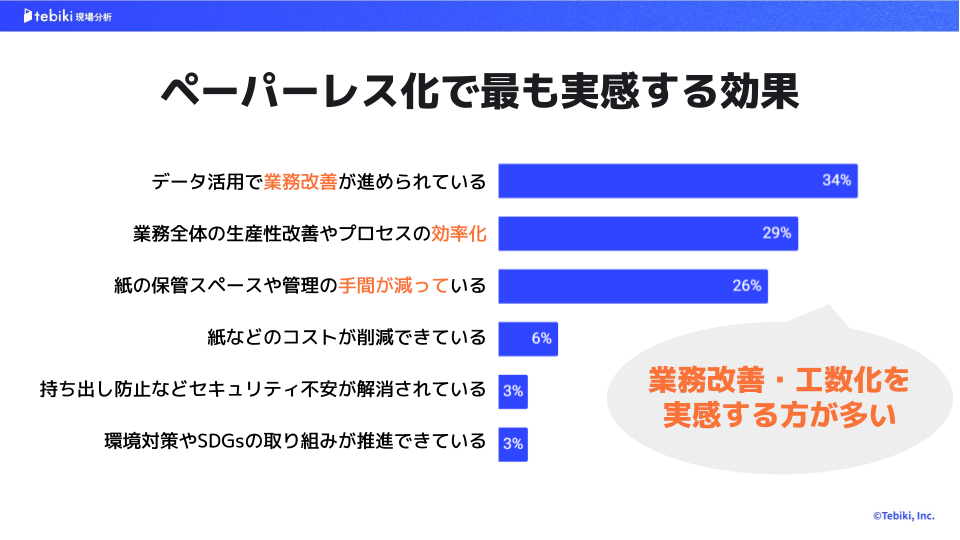
前述の【ペーパーレス化を進める1番の目的】と類似するような結果となっており、ペーパーレス化によって業務効率化や業務改善の目的も達成しやすい様子が伺えます。
【調査結果】ペーパーレス化で最も生産性や業務改善につながった文書とエピソード
【ペーパーレスの取組状況】で「取り組んでいて成果が出ている」と回答した35件に対し、最も生産性改善や業務改善につながった紙文書を伺ったところ、「現場帳票」が31%と最も多い結果となりました。
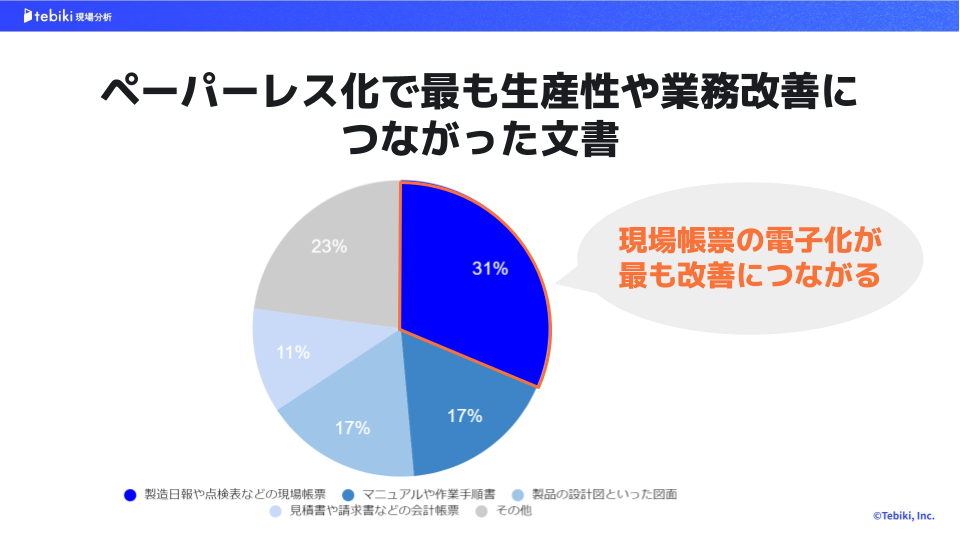
別の設問【活用頻度の多い紙文書について】でも、現場帳票が最も多い結果となっており、製造現場で使用される頻度が多い現場帳票をペーパーレス化することで現場改善の効果を引き出しやすいといえるでしょう。
実際に、現場帳票をペーパーレス化した方に伺った、業務改善につながったエピソードを一部ご紹介します。帳票管理の手間が効率化されることで、業務品質の向上や現場主体による改善提案の増加といった効果が期待できるでしょう。
▼現場帳票のペーパーレス化で業務改善につながったエピソード1 点検表の点検自体がまともに行われているのか疑わしかったが、電子点検表化で日時が記録されるようになり、点検を行っている事実が確認できるようになった。 内容の追加や削除が容易なので、ドカ停やチョコ停が発生した箇所は細かいところまで点検項目を作り込み、不具合発見時もすぐに動画に撮って送信できるようにしてを繰り返し行っていたら、ガイドに沿って点検しているせいか面倒がらず逆に集中して点検するようになり、自分たちから点検表のブラッシュアップに関しても要望を出すようになった。 ▼現場帳票のペーパーレス化で業務改善につながったエピソード2 承認書類を電子化する事で、紙媒体を持ち回って承認印をもらう必要が無くなった。 |
また、マニュアルや手順書、図面などのペーパーレス化も業務改善が期待できるといえるでしょう。現場改善ラボでは、現場帳票と手順書/マニュアルをペーパーレス化できるツールをご紹介しています。
以下のリンクをクリックして、そのツールに関する概要をご覧ください。
>>「現場帳票」をペーパーレス化できるツールを見てみる
>>「マニュアルや手順書」をペーパーレス化できるツールを見てみる
【調査結果】ペーパーレス化を考えている方が優先的に電子化したい文書と理由
【ペーパーレスの取組状況】「取り組んでみたいと考えている」と回答した47件に対し、優先的に電子化したい紙文書を伺ったところ、「現場帳票」が66%と最も多い結果となりました。
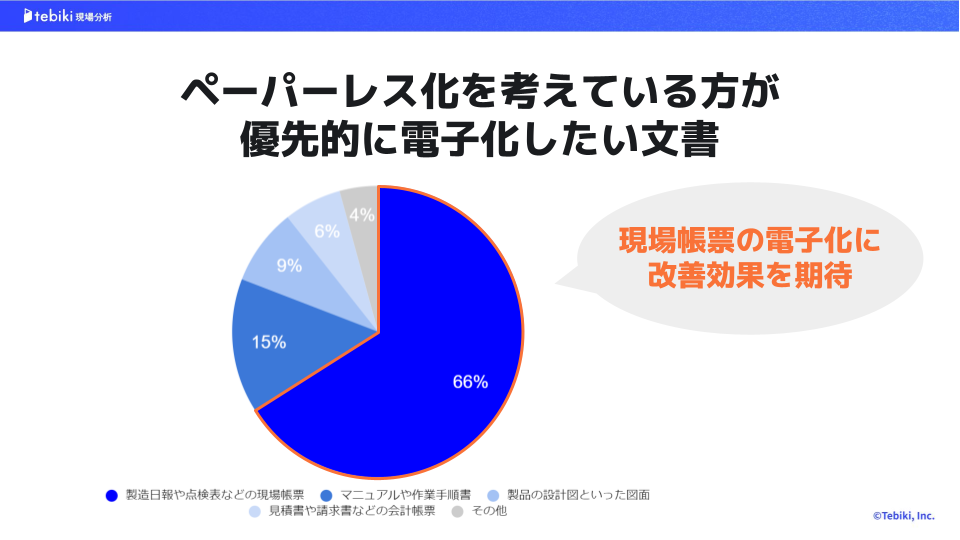
また、現場帳票を電子化したいと考える方に対し、その理由を伺った内容が以下のフリーコメントです。製造現場における現場帳票の作成/記録/承認/管理に大きな負担が発生し、本来取り組まなければいけない改善活動まで着手できていない実態が伺えます。
▼現場帳票を電子化したい理由1 現場帳票を紙で運用しており、作成/印刷/配布/承認に時間を割いている上に紙帳票の保管にもスペースと管理の工数が発生している。 ▼現場帳票を電子化したい理由2 現場帳票出力を複数人様々な時間に行ており、更に配布、記票、回収、内容確認、承認、保管に1日当たり延べ時間で1時間は必要。トレーサビリティ記録としても必要。ペーパーレスで紙代、時間削減。その分タイムリーに帳票を活用し、誰もが正しい記票を行い、ヒューマンエラー対策の効果を少しでも上がる仕組みの改善活動継続の為の時間を取れるようになるため。 ▼現場帳票を電子化したい理由3 各ライン、各シフト単位に製造日報を記入しているが、約10分の記入時間であっても10分×2シフト×25ライン×20日=10,000分=166時間/月も要している。しかも記入内容に不備も多い。 |
紙による現場帳票の運用は、記入ミスなどのヒューマンエラーを誘発しやすく管理者の確認工数を引き上げている実態があります。ペーパーレス化するツールを活用することで、記録内容によってアラートを出すこともでき、再確認などのムダを省くことができます。
製造現場の業務改善につながる期待が大きい、ペーパーレス化の進め方やポイントは以下のガイドブックでも詳しく解説しています。画像をクリックして、ぜひ本記事と併せてご活用ください。
まとめ
今回は、製造現場においてペーパーレス化するメリットや効果を独自の調査を基に解説しました。ペーパーレス化のように、新しい取り組みを推進するときには少なからず抵抗が発生しやすいです。
しかし、本記事でご紹介したように、「現場の従業員にとって明確なメリット」があり「手間なくかんたんに扱える」ような手段であることで、製造現場のペーパーレス化を成功しやすくなるといえるでしょう。
製造業で紙文書の形で使用される頻度が多い現場帳票をペーパーレス化することで、生産性改善や業務改善につながる期待が大きいです。この紙文書をかんたんにペーパーレス化できるツールが「tebiki現場分析」です。
tebiki現場分析の機能や活用事例、プランといった概要をまとめて確認できる資料もご用意しています。是非この機会に、以下の画像をクリックし内容をご覧ください。