かんたん動画マニュアル作成ツール「tebiki現場教育」や、かんたんデジタル現場帳票「tebiki現場分析」を展開する現場改善ラボ編集部です。
製造業における生産性向上とは、限られた人員や資源でも成果(事業成長)をあげることを目指す取り組みです。本記事では、生産性の定義や指標など基礎知識を解説しつつ、工場の生産性を67%向上した事例や改善方法を詳しく解説します。
目次
製造業における生産性とは?定義や計算式
生産性の定義や指標
生産性とは「コストに対する成果の比率」のことです。製造業における生産性は、労働力や設備の稼働状況、原材料などの投入によって生み出される成果や価値の効率を示す指標です。
生産性が高い企業は、競合他社と同じリソースでも高いアウトプットを生み出すことができます。生産性は市場での競争力を高め、企業の持続的な成長を促す指標といえます。製造現場で使用される指標として、以下のようなものが挙げられます。
- 全要素生産性:労働力や資本など、全ての生産要素に対する産出効率を測る指標
- 設備総合効率:設備の稼働率や性能、良品率を総合的に評価する指標
- 人時生産性:従業員の1時間あたり生産量や付加価値を示す指標
- 不良率:不良品の割合を測定し、品質の水準を把握する指標
- リードタイム:原材料の投入から製品完成/出荷までに要する時間を示す指標
製造業の場合、上記のような指標を現場KPIとして設定し、生産性を測ることが多いです。
生産性の計算式
生産性の計算式は、生産性=産出量(アウトプット)÷ 投入量(インプット)という形になります。産出量(アウトプット)は「生産活動による成果や価値」を、投入量(インプット)は「生産過程で使用されるリソースの総量」を指します。
▼例:1日100台の自動車を生産するために、1,000万円の原材料を必要とする場合
生産性 = 100台 ÷ 1,000万円 = 0.1台/万円
前述したような製造現場のKPIとなるような指標の場合、それぞれで計算式は変わるので各種指標をクリックして別記事をご覧ください。
製造業の生産性は本当に低いのか?
よく一般論として『製造業の生産性は低い』という悲観的な言論がされることがありますが、本当にそうでしょうか?
内閣府の国民経済計算(GDP統計)で日本の名目GDPで見た場合、製造業が占める割合が30%台だった1970年代と比較し、2000年代には20%台まで減少傾向にあります。また、総務省統計局による労働力調査では、製造業の就業人口も約1,800万人だった1980年代に比べ、2020年代は約1,000万人と同様に減少傾向にあります。
名目GDPの比率や就業人口はいずれも、減少の一途をたどっているため『生産性が下がっている』という印象を受けるかもしれません。しかし実際は、製造業が生み出すGDPや生産額はさほど減少しておらず、労働力が減る中で生産性を高め続けているといえます。
経済産業省の令和5年度ものづくり白書によると、製造業の1人あたり名目労働生産性が953万円だった2012年に比べ、2022年は1,031万円と伸び続けています。これは全産業よりも約1.2倍の労働生産性があることを示し、日本における製造業は生産性が高いことを示しています。
製造業が生産性向上に取り組む目的やメリット
製造業が生産性向上に取り組むことで、以下のような目的やメリットがあります。
- 人手不足対策のため
- 熟練者の技術/技能伝承につながるため
- ムリムダムラの除去で収益性改善につながるため
あくまでも一例ですが、生産性向上を通じた生産工程の改善から、結果的にQCDの最適化による「企業競争力強化」につながることが期待できます。
人手不足対策のため
前章のように、製造業の就業人口は減少し続けており、全体の労働人口が減り続けている日本では人材を採用する難易度が高いでしょう。
製造現場の人手不足をカバーする手段として、外国人労働者を受け入れるケースも多いですが、文化や言葉の壁による従業員教育の難しさから、作業のルールが伝わりにくい/トレーナーのフォローが必要といった点で、短期的には製造現場の生産性を下げる恐れがあります。
単に人手を増やす=生産性が上がるというわけではないため、以下のような取り組みを通じて人手不足の中でも生産性を高める効果が期待できます。
- 新人受け入れ時の教育工数を効率化する仕組み作り
- 製造現場の自働化による省人化の推進
「教育工数を効率化する仕組み」を実現する手段として、動画マニュアルを活用する製造現場も増えています。うどんなどの冷凍食品を製造/販売するテーブルマーク株式会社では、動画マニュアルを活用して属人的な現場作業の教育工数を83%削減し、現場の生産性を高めています。
「製造業における動画マニュアル活用事例集」では、同社のように業務の生産性を高めている製造現場の事例を多数ご紹介していますので、以下のリンクをクリックして参考資料をご覧ください。
>>製造現場の生産性向上事例が分かる!「動画マニュアル活用事例集」を見てみる
熟練者の技術/技能伝承につながるため
製造現場の生産性を支える要素の1つに、熟練者が長年の経験を通じて習得した「カンコツ」があります。熟練者の勘やコツは、業務を効果的かつ効率的に行う動作として現れています。
このような生産性の高い動作を現場で標準化することで、結果的に次世代への技術/技能伝承につながる効果がメリットとして期待できます。また生産性向上だけでなく、技術/技能伝承によって自社の魅力的品質を支える企業競争力につながる視点もあります。
オーダースーツなどの紡績から縫製、販売を行っている御幸毛織株式会社では、生地の風合いなどの付加価値が熟練者のカンコツによって支えられており、技術/技能伝承を通じた生産性向上と競争力強化に取り組んでいます。
このような技術/技能伝承を成功に導く、施策実施のポイントや事例などを解説するガイドブックを公開していますので、以下のリンクをクリックしてご活用ください。
>>「技術伝承を成功させるポイント」をまとめたガイドブックを見てみる
ムリムダムラの除去で収益性改善につながるため
ムリムダムラは、製造現場の生産性を下げる代表的な要因です。
ムリが続けば作業者や設備への負担が増大し、労働災害のような事故や品質不良のリスクを高めます。ムダは付加価値を生まない在庫や作業を指し、コストと時間を浪費します。さらにムラは需要変動や作業ばらつきなどにより、安定した生産体制を阻害します。
これらを放置すると製造現場全体の効率が落ち、本来の生産性を十分に生かせない悪循環に陥る恐れがあります。生産性を向上させるためには、現場で生じているムリムダムラを除去することが不可欠です。
除去によって生まれた余裕は、新たな改善活動の検討や立案、会社として市場に対する新たなる価値創出につながるような本質的な取り組みへ目を向けることができます。
このようなムリムダムラを取り除く手段について、専門家による解説動画を無料で公開していますので、以下の画像をクリックしてご活用ください。次章からは、生産性向上を実現した製造業の事例を定量的な情報も交えてご紹介します。
工場の生産性を67%向上した製造業の施策事例
世界最高水準の真空技術による製品を多数製造/販売する株式会社アルバックは、動画マニュアルを活用した「拠点間の技術/ノウハウの共有」や「全体的な生産効率の向上」に取り組み、結果的に67%の生産性向上を実現しています。
生産性向上を実現した、同社の取り組みの詳細は以下のような内容です。
- 定点カメラで作業全体の流れや動線を撮影し、移動時間や作業の切り替えなどを評価
- 細かい作業のポイントや手順を動画マニュアル化し、詳細な動作分析を実施
- 拠点間で意見交換し、「なぜそのように作業するのか」理由や背景を議論
製造現場の生産性を支える暗黙知を、動画マニュアルで視覚的に理解できるようにし、その動作の意義や有効性を拠点間で議論したことで、作業を客観的に見直す機会となり改善点の発見にもつながっています。
このような取り組みを半年間集中的に行った結果、ある製造工程の制作時間を78分短縮し、1日あたりの生産可能数も従来よりも67%向上しています。
同社のより具体的な取り組み内容は、インタビュー記事「人員・労働時間を変更せずに、ボンディング工程の生産性を167%に改善」をご覧ください。今回の事例のように、動画マニュアルを活用した製造業の施策事例をまとめたガイドブックもご用意していますので、以下のリンクをクリックして参考資料もご覧ください。
>>株式会社アルバックのような「製造現場の動画マニュアル活用事例集」を見てみる
製造業で生産性向上を達成する改善方法
前章でご紹介した株式会社アルバックの事例のように、製造業の生産性を向上するためには「製造現場の実態を可視化すること」「可視化によって見えた課題への対策実施」というサイクルが必要です。
ここからは、このサイクルに基づいて生産性向上を達成する改善方法を詳しく解説します。
現場の生産数や不良率などを可視化する
まずは現場の生産性を表す、1日当たりの生産状況や不良率といった指標を定量的に可視化できる状態に整えることが大切です。定量的に計測できるようにすることで、基準に対する状況を正確に捉え、ボトルネックに対する対策を早期に行えるようになります。
製造業の場合、生産性を表す定量的なデータを「紙やExcelによる現場帳票」で収集することが多いですが、記録や承認/集計/分析業務など、可視化する工数が管理者に重くのしかかり、生産性を阻害している側面もあります。そこで「現場帳票の電子化」に取り組むことで、帳票付帯業務を大幅に効率化することが可能です。
スチール製家具の生産・販売をしている共栄工業株式会社では、紙/Excelで運用していた現場帳票を電子化したことで、1日2時間発生していた帳票集計作業を1分まで削減し、管理者の生産性を高めたような事例もあります。
現場帳票の電子化(デジタル化)に取り組む有効性は、以下のガイドブックでも詳しく解説していますので、画像をクリックしてご活用ください。
現場で顕在化している課題から改善の優先順位を設定する
可視化した情報をもとに、不良率が高い工程や稼働率が低い設備など、改善すべきポイントを洗い出します。「生産性向上」という目的の場合、現場課題が1つということはなく、複数の問題が複雑に入り混じっているはずです。
そのため洗い出した課題は、それぞれの問題が与える影響度と緊急性を評価し、優先順位を明確にすることが重要です。たとえば、高頻度で発生する不良の削減や、費用対効果が大きい工程改善などは優先度が高いといえます。
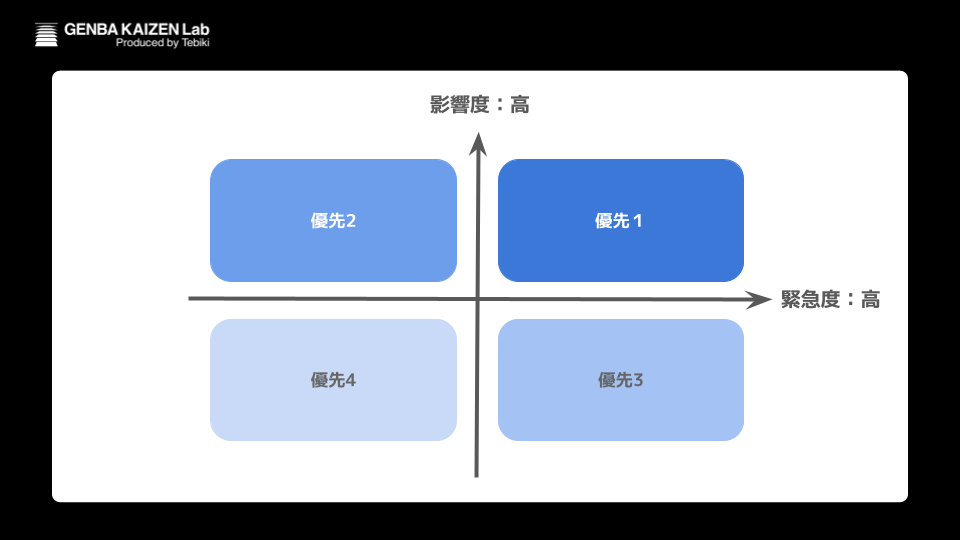
上記のような「影響度」「緊急度」を掛け合わせた4象限に課題を分類することで、生産性向上を早期に実現すべきところから適切に改善策を進めることが判断できます。
設定した課題の改善策を検証する
生産性に影響を及ぼしていると判断した課題によって、明確な改善策は変わってきます。もしも『対策内容がまだ抽象的で実行できない』という場合は、課題の真因を明らかにできていない恐れがあるので、なぜなぜ分析で深掘りを行うことも手段の1つです。
対策内容が明確になったのち、いきなり職場全体に適応するのではなく、まずは一部の部門や工程で試験的に検証を行いましょう。改善策の効果は不確定要素が少なく、実際に検証してその有効性が明らかになります。一定の成果が見込めると検証できた場合、他の部門でも改善策を実行していきましょう。
今回ご紹介した「なぜなぜ分析」について、現場改善ラボではトヨタ社内でなぜなぜ分析の講師を務めていた専門家による解説資料を無料で公開しています。分析方法だけでなく、解説動画やテンプレートもセットでご活用いただけますので、以下のリンクをクリックしてご活用ください。
>>トヨタ流「なぜなぜ分析」の実践方法とポイントを資料で見てみる
現場のルールとして対策内容を標準化する
一定の効果が見込めると分かった改善策は、他の製造現場でも取り入れていくことで、全社的な生産性向上を本格的に進めていきます。このような新しい取り組みは「現場のルール」として浸透させていくことが欠かせません。
ルール(標準)が守られないと想定していた効果を最大限引き出せず、現場の従業員も生産性の向上を実感できず、『守っても意味がない』と対策内容そのものが形骸化してしまう恐れがあります。
製造現場全体で実行する段階では、関係する従業員に対する説明や狙いを徹底することは勿論、改善策の内容や対策によって生じる4M変更の内容を周知し、新たなルール(標準)として守られるようにすることが大切です。
作業内容の変更が伴う場合、作業手順書のような文字で「動作」を理解することは難しいため、視覚的に理解できる動画を活用することも効果的です。ルールを守らせる効果的な方法は、別紙のガイドブックでも詳しく解説していますので、以下のリンクをクリックして資料をご活用ください。
>>「“手順書通りにできない”から卒業!作業ルールを守らせる効果的な方法」を見てみる
対策実施後の変化をモニタリングする
対策実施後は、想定していた効果を引き出しているか計測するためのモニタリングが必要です。「現場の生産数や不良率などを可視化する」でご紹介したような、現場帳票の電子化で可視化を行っている場合、容易にモニタリングを行うことが可能です。
かんたんデジタル現場帳票「tebiki現場分析」であれば、集計した現場帳票の記録を自動でグラフ化し、複雑な関数も不要でダッシュボードの整備ができます。製造現場のディスプレイにダッシュボードを投影することで、リアルタイムでモニタリングすることができます。
▼製造現場でダッシュボードをモニタリングするイメージ▼
【株式会社日本電気化学工業所:現場帳票の電子化事例インタビューより抜粋】
このように、対策実施後のモニタリングも行うことで、新たな改善に気づくきっかけにもなります。改善点に対する打ち手を繰り返していくことで、最終的に製造現場の生産性向上という大きな効果を引き出します。
次章では、このような生産性向上のサイクル実行を助けるツールを2つご紹介します。
製造業の生産性向上を実現する2つのツール
製造現場を効率的に可視化する「デジタル現場帳票」
デジタル現場帳票は、紙やExcelで運用されている製造業の帳票を電子化することで、内容の記録/承認/集計/分析を効率的に行える効果が期待できます。結果的に、作業者や管理者の帳票付帯業務の負担を軽減できるため、製造現場の生産性向上に有効なツールです。
デジタル現場帳票を活用する製造現場では、以下のような導入効果を実感しています。
このような効果を実感できるツールが、かんたんデジタル現場帳票「tebiki現場分析」です。帳票付帯業務を効率化する機能が揃っているのは勿論のこと、自動分析機能やグラフ化機能によって、生産ラインの異常を早期に捉えることができる点が特徴です。
- 申請から承認までの流れがスムーズ
- 正常値を設定することで、異常値アラートを出せる
- 画像記録機能
- 入力の手間を省く定時記録機能
- 記録した数値を自動で管理図等のグラフにできる
tebiki現場分析の具体的な機能やプランは、サービス概要資料で詳しく解説していますので、以下のリンクをクリックしてご確認ください。
>>かんたんデジタル現場帳票「tebiki現場分析」の詳細を見てみる
業務標準化を効果的に推進する「動画マニュアル」
動画マニュアルは、製造現場の作業内容を共有している作業手順書やOJTではなく、文字や口頭でイメージしにくい「作業動作」を視覚的に分かりやすく伝えられる効果が期待できます。結果的に、作業者が業務ルール(標準)を正確に捉え、品質/安全トラブルにつながるような手順不遵守を防止できるツールです。
また、新人や外国人教育で製造現場に負担が発生しているOJTも、大部分を動画に置き換える使い方をすることで、トレーナーの負担を軽減し、生産活動への影響を最小限に抑えることも可能です。動画マニュアルを活用する製造現場では、以下のような導入効果を実感しています。
- 手順不遵守が9割削減され、作業ミスによる品質不良が大きく減った
- 作業手順書の作成は0.5~1ヶ月から1~2日ほど、OJTの時間は3割程度効率化できた
- 人員や労働時間を変更せずに、製造工程の生産性を67%改善できた
このような効果を実感できるツールが、かんたん動画マニュアル作成ツール「tebiki現場教育」です。作業手順など「現場の動き」を視覚的に分かりやすく伝え、製造現場の業務標準化を推進することができます。
業務標準化を助ける機能として、主に以下の機能をご用意しています。
- 100カ国語以上への自動翻訳
- 字幕の読み上げ(多言語にも対応)
- アクセス履歴等がわかるレポート機能
- オリジナルのテストを作成できるテスト機能
- 従業員のスキルを評価・可視化できる機能 など
今回ご紹介していない具体的な機能のご紹介、プランなどの情報は以下のリンクをクリックして概要資料をご確認ください。
>>かんたん動画マニュアル作成ツール「tebiki現場教育」の概要資料を見てみる
まとめ
製造業の生産性は、投入量(人員・設備・資源など)に対する産出量(成果・価値)の比率を示す指標です。名目GDPや就業人口が減少傾向にある一方で、製造業自体は少人数で高い生産性を維持している実態があります。
人手不足や熟練技術の伝承、ムリムダムラの除去などが重要課題となるなか、現場帳票の電子化や動画マニュアルを用いた標準化による作業効率の向上が注目されています。実際に、アルバックでは動画マニュアル化により生産性を67%も改善し、省人化や教育工数削減の成果を得ています。こうした取り組みは、企業競争力を高めるうえで有効な手段といえるでしょう。
今回ご紹介した「tebiki現場教育」と「tebiki現場分析」は、製造現場の生産性向上の達成に役立つ2つのツールとなり得ます。両者のサービス概要資料は、以下のフォームを入力いただくとご覧いただけますので、生産性向上策の1つとしてご検討ください。